
4 minute read
The Laser Cutting Company: For laser-precision
Based in the heart of Sheffield, The Laser Cutting Co is a Made in Sheffield® trademark company offering industry leading cutting services. These services include tube laser cutting (3D cutting), large and open section cutting, 2D flatbed laser cutting and 4 metre profile bending, smart design service, flow drilling, waterjet cutting, flame cutting and weld preps.
The customer base ranges across diverse industries such as automation, architecture, construction, manufacturing and fabrication, from the medical sector right through to nuclear.
Cutting-edge Tube Lasers
Established in 1981, the company has grown exponentially and provides access to the latest cutting technology through continuous investment in the latest machinery. This includes multi-axis tube lasers with the arrival of the TruLaser Tube 7000 Fibre Machine, which allows unprecedented tube laser cutting quality and productivity. This machine provides laser power of up to 6kW cutting material thickness up to 15mm, rapid processing of section parts up to 254mm outside diameter and with Bevel Cut and RapidCut technology, handling material like mild and stainless steel, through to aluminium, brass, and copper.
Tube laser cutting (3D cutting) offers meticulous accuracy and precision, with tight tolerances to +-0.25mm and a smooth finish quality across a wide range of materials. The five-axis cutting mechanism is engineered to cut intricate configurations, leaving minimal heat distortion or warping.
Seamless chamfer and countersink production
“Our flatbed laser cutting machines offer industry leading capacity and lead time. With five lasers handling sheet metal sizes up to 2.5m x 6m on material up to 50mm thick, we’re able to provide customers with the most reliable service available on projects of all shapes and sizes.” explained Charlie Day, Sales Director. Notably the latest addition of the flatbed fleet includes a Trumpf 5030 with BevelEdge, allowing for the laser cutting of bevelled edges and countersunk holes performed by the laser, on sheet sizes up to 4m x 2m. Customer receive finished parts from raw material in one efficient process.
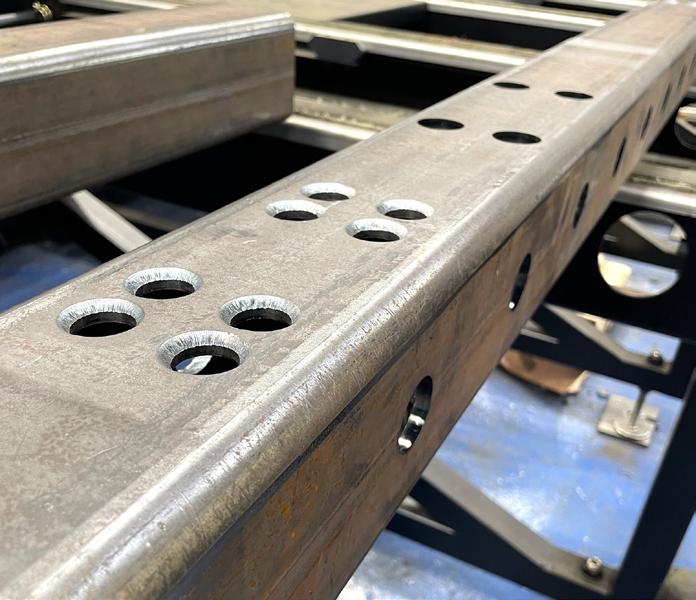
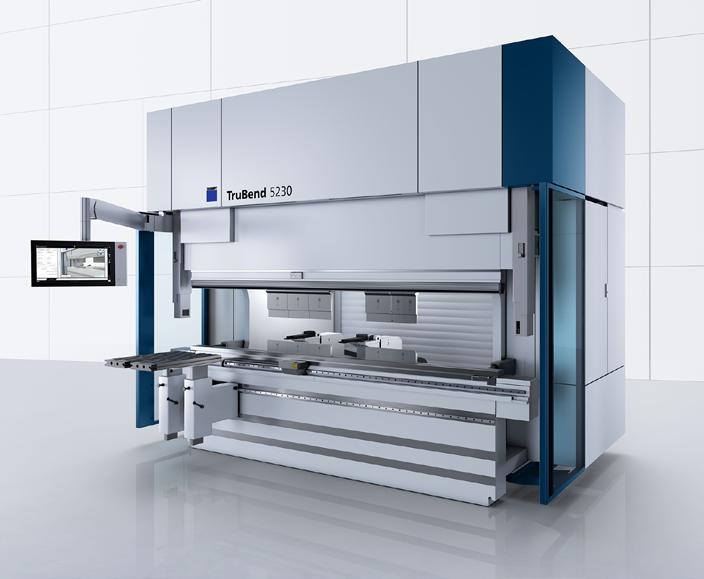
Smart design production
Design is the key to refining the manufacturing process and the in-house design team at The Laser Cutting Company use a methodical approach to design production.
The in-house design team at The Laser Cutting Co. take a holistic approach to part optimisation, considering everything from material waste to reduced handling and assembly processes, to realise downstream efficiencies.
The more complex a design is, the higher the risk. The aim of The Laser Cutting Co.’s CAD design service is to reduce component volume, reduce material waste, and reduce overall complexity. The results are an average 50% time and cost saving for customers on downstream processes such as fabrication.
One-stop profiling shop
It is paramount that customers receive parts correct and on time to the highest quality, so offering a reliable service is key, otherwise knock on delays for customers and their production plans can be very costly.
“Our services stretch much further than just flat and tube laser cutting. The machines we have in-house give us the capability to offer a complete profiling solution all designed to simplify the manufacturing process. From Plasma Cutting, to Waterjet Cutting, Flame Cutting, Shot Blasting, Deburring and Vibro-Deburring, Laser Engraving and Etching, we are keen to continue investing in only the very best machinery that will enhance our service experience for our clients.
The Laser Cutting Company can greatly increase customer’s downstream efficiencies, providing them with the competitive edge in their market sector.
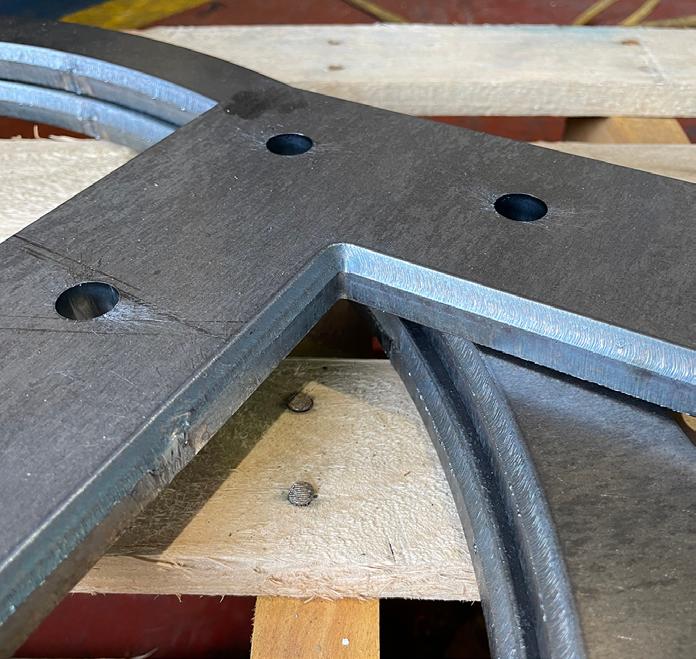
For more information on The Laser Cutting Company, please see the details below:
T 0114 242 0101
sales@lasercutting.co.uk
https://www.lasercutting.co.uk