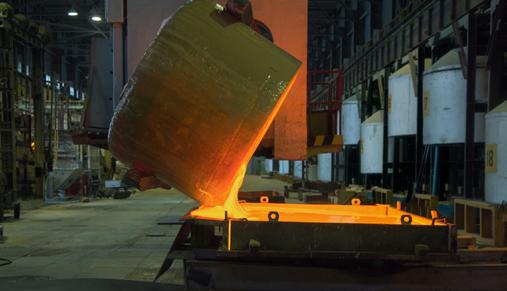
2 minute read
Optimising energy in electric boosting and melting systems
Like all industries, pressure to decarbonise is imminent. And glass manufacturing is no exception, with the objective to attain carbon neutrality by 2050. Not only does decarbonisation benefit wider industry and society, but when done correctly, also provides efficiency and cost benefits. In this article, Mikael Le Guern, Global Glass Business Development Manager at Eurotherm, a company acquired by industrial technology company Watlow, explains how installing power boxes close to furnace electrodes can help glassmakers improve energy efficiency and reduce costs, compared to traditional power system designs.
As a result of pressure to decarbonise, we are seeing more requirements to significantly increase electrical boosting for facilities all over the world. Certainly, for large glass production companies, their total CO2 emissions are the aggregate emissions of all their plants and facilities globally.
With furnace campaigns lasting between 10 and 18 years before the next rebuild or cold repair and with only a few upcoming greenfield projects, the opportunities for these companies to implement carbonreducing solutions are limited. Currently, whenever a repair is due, many glass companies are already considering their options to reduce greenhouse gas (GHG) emissions, particularly by increasing electrical boosting.
The other movement happening in the marketplace is that all types of glass producers are looking into these issues. Years ago, the size of the furnaces and type of glass made it possible to implement small to medium size electrical boosting, on average between two and five megawatts (MW). Now, not only has the required size of electrical boosting systems grown from a few megawatts (MW) to over ten MW and beyond, but this trend is happening across most types of glass production, including float glass furnaces.
To learn more about Eurotherm and its solutions for glass manufacturing, please visit: www.eurotherm.com
To learn more about Watlow’s thermal solutions, please head to: www.watlow.com