
9 minute read
IMI/IMTEF
Meet BAC Members Committed to Lifelong Learning & Career Growth
At the BAC/IMI International Training Center (ITC), BAC members from across the country are working to expand their career opportunities. From apprentices just getting their start to experienced journeyworkers; meet some of the dedicated members taking advantage of IMTEF’s lifelong learning programs.
Advertisement
LEAISURES EXPAND FAMILY LEGACY IN THE TRADES AS FUTURE COMPANY OWNERS
(L–R) Charles and Billy Leaisure
Charles and Billy Leaisure are a dynamic father-son duo from BAC ADC Ohio/Kentucky with experience in bricklaying and masonry restoration. They recently earned both their welding and JAHN certifications together at the ITC.
Charles already has quite a few advanced trainings under his belt, with half a dozen certificates from the ITC and over 70 certificates of completion from IMI’s webinar series. “I’m just a blue-collar guy,” he said. “When I was in school, I didn’t enjoy it much, but as I’ve gotten older, that’s changed. I want to learn until I can’t anymore. I’d like to one day be the smartest person in the room.”
Charles instilled an appreciation for education in his son, Billy. “The welding certification will help me expand my opportunities, so that when work slows down, I can stay busy,” Billy explained.
As Charles continues to enhance his skillsets, the opportunity to become a business owner became a reality for him and his family. “I work for a restoration company and the current owner would like to pass the baton to me, so we are in the process of finalizing the transfer,” expressed Charles. “Never in my life would I have imagined that I would own a business that I get to pass on to my children one day.”
SEGURA WEST, RESTORATION APPRENTICE, BUILDS HIS AMERICAN DREAM
Before coming across a job advertisement online for apprenticeship opportunities with BAC Local 2 New York/Vermont, Nathaniel Segura West was working as an Uber driver. “I was looking for a stable, long-term career,” he explained. “I applied but had no idea they’d hire me, because I didn’t have any prior experience in the construction industry. It ended up being a really good choice.”
West recently completed his pre-job training in restoration at the ITC, where he learned all the basics of his trade, along with important safety skills to prepare him for the jobsite.
“This is a great opportunity for me. It’s a chance to live the American dream,” said Segura West, a Panamanian immigrant. “It’s not just a job. You’re learning a skill and improving your life. I look forward to growing professionally and becoming a journeyworker.” He is excited to return to the ITC for more advanced specialty training in future.
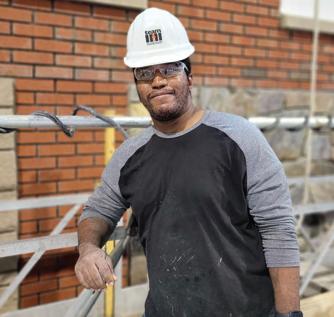
Nathaniel Segura West
ANSELL, BRICKLAYING INSTRUCTOR, WALKS THE TALK FOR HIS STUDENTS
As a bricklaying instructor for BAC ADC Ohio/Kentucky, Scott Ansell knows how critical continuing education is to mastering the craft and keeping up with the ever-changing construction industry. That’s why he decided to pursue his welding certification at the ITC.
“There’s always going to be another certification you can get. What we do is probably the hardest form of art there is,” Ansell said. “As an instructor, I want my students to know that there will always be room to grow.”
Ansell encourages his fellow brothers and sisters to become teachers and mentors on the job. “I make it a point to give back to the next generation of craftworkers by teaching them skills on the jobsite and purposely moving slowly and providing instruction so they can learn. They’re the future of our union. Times have changed. We all need to be a little patient and encouraging to our apprentices, or else they’ll leave for other opportunities,” he advised.
Instructors like Ansell also visit the ITC for train-the-trainer programs, where they learn to teach IMTEF’s national standardized curriculum to members in their home local or ADC.
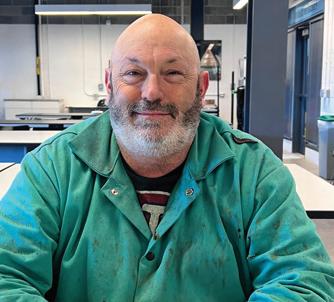
Scott Ansell
GRAJEDA READIES TO TAKE ON REFRACTORY WORK
Alex Grajeda is a proud restoration apprentice with BAC ADC 1 Illinois, who enjoys restoring and maintaining Chicago’s skyscrapers. He visited the ITC this winter to learn more about another side of the trade he’s interested in: refractory.
“For me, it was important to come and get better training, because I’ve been doing refractory work here and there and want to have more chances to land jobs,” Grajeda said. “This training alone shows how much our union takes pride in preparing us and teaching the craft. It’s not like the non-union [companies], where they throw you to the wolves. I know what it’s like because I came from that side. I was tired of having no benefits. Being in the union to me means a better future.”
Grajeda learned about that chance at a better future through a friend. Even as locals try new recruitment strategies – from online job ads, to targeted social media, and more — referrals from friends and family are still a powerful way to connect more people with middle-class careers in the union trowel trades. //
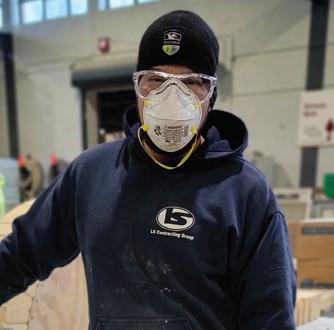
Alex Grajeda
GROW YOUR OWN SKILL BASE
The BAC/IMI International Training Center offers a unique opportunity for members to learn from top-tier instructors and network with fellow craftworkers from coast to coast. From the 61,000 square foot, 2-story open bay training floor to the well-equipped dorms with dining hall and recreation spaces, the campus is designed to facilitate immersive, enriching learning. Look out for IMTEF’s fall training calendar at imtef.org/calendar and contact your local training center or JATC to learn more about training programs that can help you advance your career.
Masonry Materials & BAC Artisanship Make Loyola’s New Performing Arts Center Sing
At Loyola Academy in Wilmette, Ill., BAC members and signatory contractors are showcasing their skills building a vibrant new center for the performing arts. The star of the $25 million facility is the Leemputte Family Theater, a 550-seat auditorium with an arched stage. BAC ADC 1 Illinois members with signatory contractor Midwest Masonry just finished building the theatre’s exposed concrete masonry unit ground faced block walls. The complex installation involved rotated units and compound curvature that give the space great acoustics.
This undertaking required close collaboration between the project team — enter the International Masonry Institute (IMI). Director of Industry Development and Technical Services Jeff Diqui saw a unique opportunity to bring together key project players for a hands-on day to address concerns related to aesthetics, constructibility, structure, sequencing, and cost. During the event, the team built a large-scale mock-up of the curved block wall at the District Council Training Center. Representatives from Midwest Masonry attended, along with architecture firm Krueck Sexton Partners, structural engineering firm Thornton Tomasetti, and general contractor Valenti Builders.
Krueck Sexton Partners called it an “amazing opportunity” to ensure “everyone is on the same page and shares the same goals.”
REMOVED REDUNDANCY
One of those goals was to make the masonry as efficient and aesthetically pleasing as possible. Prior to the hands-on event, IMI and the Illinois Structural Masonry Coalition engaged Thornton Tomasetti early in the project to optimize the structural design for the auditorium. It was over budget, putting the block at risk of being value engineered out.
Diqui and the coalition supporting the engineer successfully eliminated the redundant steel columns, making the masonry loadbearing and avoiding construction tolerance challenges where steel interfaced with block. They also reduced the size of the block units from 12 inch to 8 inch to better accommodate the curvature, improve aesthetics, and minimize potential shrinkage cracking caused by overly wide head joints.
Finally, the team cut the expensive, custom horizontal joint reinforcement, designed to be installed every 16 inches. Instead, they introduced an alternate engineered method, using reinforcing
Project team at IMI’s “hands on” day for the project
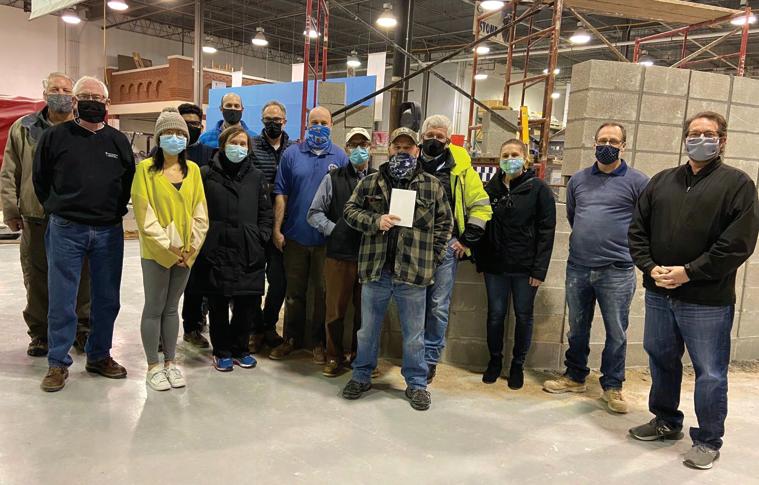
steel bent to the curvature of the wall that was placed in bond beams every four feet on center — a simpler, more cost-effective solution that also mitigates control joints.
Mark Ligas, the project’s foreperson at Midwest Masonry, said the project was challenging, but nothing his talented crew of eight BAC craftworkers could not handle. “The geometry of the wall was really unique. We had projections that stepped out in certain places at both 1/16 inch and 1/8 inch intervals, so counting every course was critical to avoid making mistakes. I had to make special tools to rake the joints,” he explained. That’s because the wall had varying mortar joint profiles, with both raked vertical joints and weathered horizontal joints.
With specially cut block and multi-faced block ranging from one-sided to three-sided, every unit had a specific place. Plus, all the receptacles for electric had to be carefully cut in the middle of the block without sacrificing the integrity of the material, and in coordination with other trades. When the walls were ready for grouting, the crew had to be especially careful to avoid staining, since all the block is exposed.
MASONRY PERFECT MATERIALS FOR PROJECT
The block Ligas and his crew worked so hard to install provides an ideal palette for acoustics, according to Scott D. Pfeiffer — FASA, Partner at Threshold Acoustics — who provided sound consulting on the project.
“For a project that’s intended to be affordable to build, block allowed us to use one layer, rather than having to build up structure and finish separately,” said Pfeiffer. “Block is a massive material, and that makes it great for reflecting full frequency sound. Its porosity helps to keep a room’s sound warm and pleasant, rather than harsh.”
As for the curvature, Pfeiffer explains: “The broad curves are meant to distribute the energy relatively evenly across the broad space, which allows you to hear more of what’s coming from the stage.”
Ligas said the team noticed the space’s incredible acoustics as they were building. “The crew was laughing at me, because they could hear me really well from the floor when they were up on the scaffolding.”
The performance sound wasn’t the only acoustical consideration; the project team also had to address traffic noise from the nearby Edens Expressway. The precast concrete exterior, installed by signatory contractor Continental Erectors, was selected to block sound on the outside from coming in.
The precast also played a role in meeting the university’s sustainability goals. The panels and poured-in-place concrete were made with fly ash, providing a 25% cement replacement. A C02 mineralization process further reduced the cement makeup of the poured-in-place. Together, these efforts helped reduce the building’s carbon footprint.
Precast was also used on the interior staircases, installed by signatory contractor Cleveland Marble Mosaic Company. According to Jim Small, Regional Manager, the material was manufactured less than 500 miles from the site, another sustainable attribute. Masonry’s local availability reduces carbon emissions associated with shipping long distances.
When the center opens this fall, it will be not only the heart of the arts on campus, but a shining example of sustainable, unionbuilt construction.
“It’s rewarding to work on a project like this that will be seen by generations to come. These types of buildings are made to last,” Ligas concluded. //
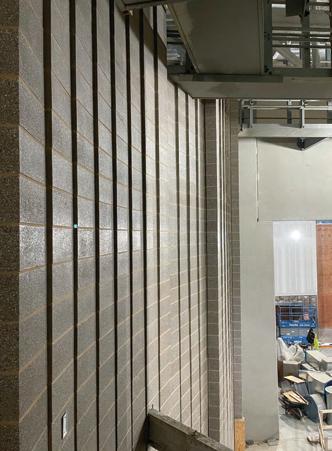
Curved block walls installed at the Leemputte Family Theatre