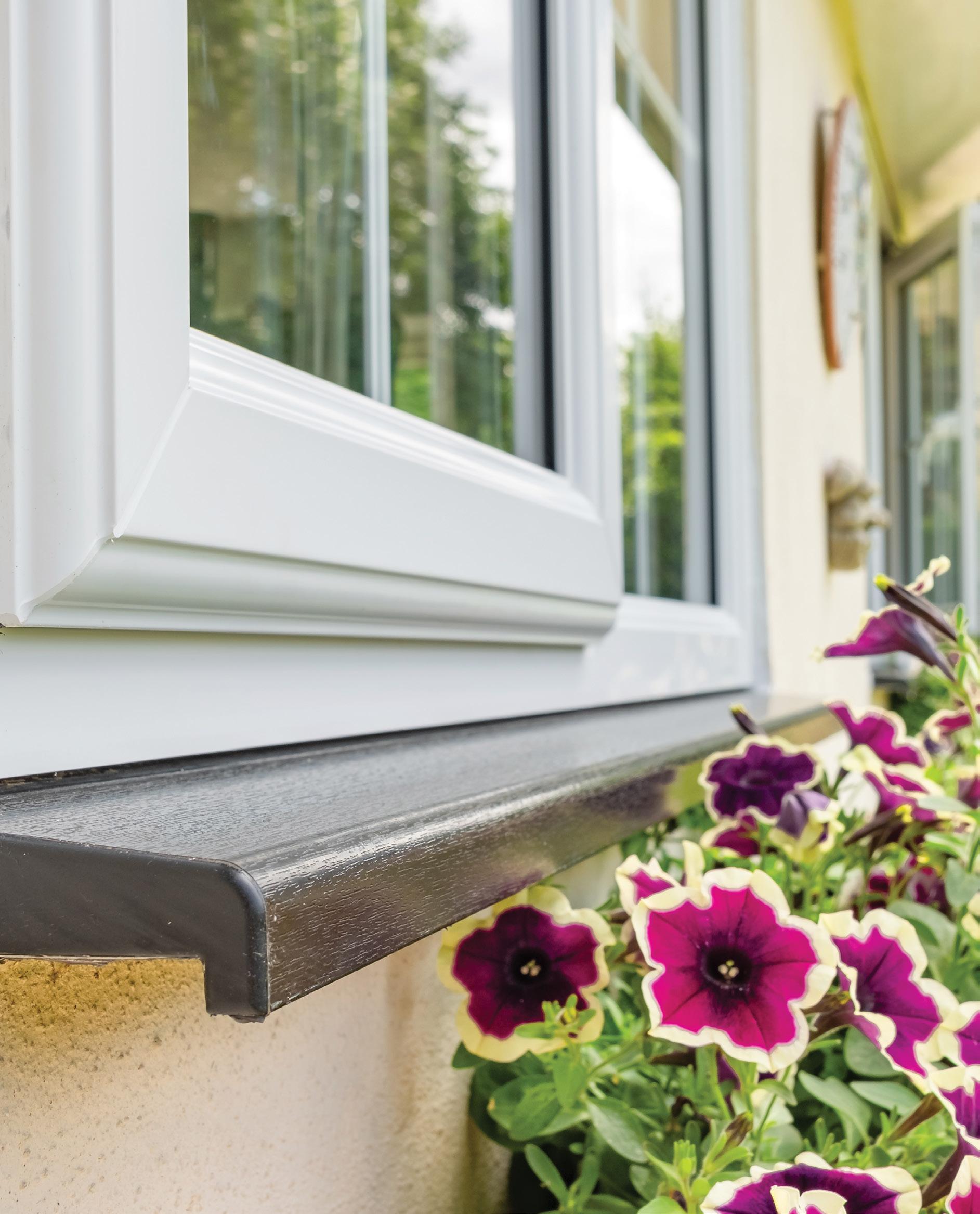
4 minute read
TECHNICAL
TECHNICAL
WHAT’S CAUSING THE PANE
– IGU FAILURES
Adam Davies and Dr Pouya Abtahi AGWA
With the ever-increasing push for higher performing and energy-efficient homes, the role and uptake of Insulated Glass Units (IGUs) is on an upward trajectory. This is obviously positive for our industry, but with the greater production and installation of IGUs comes more risk of non-conformance leading to failures.
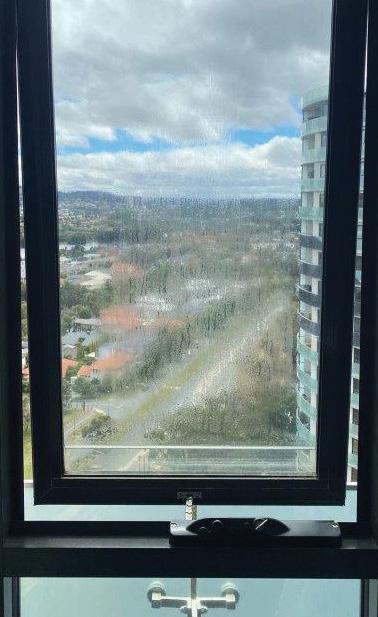
Unlike conventional monolithic glazing, an IGU is a complex system relying on multiple parts, all performing in concert, to achieve the required performance and life expectancy. AGWA is seeing an increasing number of disputes and technical enquiries relating to the failure of IGUs. Many of these disputes relate to non-conformance in either their manufacture or installation. This is of concern as the market for IGUs will increase as people choose higher performing windows and glass units. More concerning is that these failures generally do not happen soon after manufacture/installation but can take several years to eventuate. These failures could not only leave you with an issue that you are obligated to address but will come with higher cost. With the delay of the failure occurring the industry needs to be aware of these issues and address them proactively. Based on what we have seen and as a result of the feedback we have received, the failures are split roughly 60% due to installation and 40% due to incorrect manufacture.
COMMON MANUFACTURING FAILURE MODES
These are the most common manufacturing issues we are seeing. • Poor application of the primary seal where 100% coverage is not achieved
It is important that the primary seal is applied evenly to the entire perimeter of the unit. The primary seal is the main part of the IGU that prevents moisture ingress, while the secondary seal mainly provides the structural strength of the unit.
• Cold joints
This is when the primary or secondary seal has skinned over (hardened) where the bead starts before the full application of the seal to the unit is complete. This causes the seal to be interrupted and not continuous.
• Spontaneous Glass Breakage (for toughened IGUs)
During the service life of the IGU, one or more of the glass panels may spontaneously explode. There are many factors that can make this happen with most of the blame often unfairly focusing on Nickel Sulphide.
Nickel Sulphide can be present and indeed cause failure, but this is actually quite rare with other factors such as other inclusions leading to failure and possibly external factors, such as unwitnessed impact. Generally spontaneous failure is outside the control of the manufacturer and can be considered an inherent aspect of toughened glass and not a fault thus generally not covered by warranty.
COMMON INSTALLATION FAILURE MODES
These are the most common installation issues we are seeing.
• Insufficient or lack of water drainage in the framing system used.
This allows water/moisture to stay in contact with the unit for prolonged periods leading to failure. The perimeter of an IGU must not remain wet as this will degrade the secondary seal and place increased structural loads on the primary seal, for which it is not designed. This will then allow moisture vapour to migrate into the unit, consume the desiccant and lead to internal fogging.
• Lack of, or inappropriate, setting blocks
The correct application and material for setting blocks is critically important for the long-term performance of an IGU.
Setting blocks that only support the IGU on the seal result in excessive loads and will eventually lead to failure of the IGU.
The setting blocks must be a minimum of 3 mm wider than the unit thickness and of the correct size and location as stated in in AS 4666: 2012. Also important, is that the setting blocks are resilient, load bearing, non-absorbent, rot-proof materials that are constructed of a material that is compatible with the secondary seal of the unit. Some poorquality setting blocks contain chemicals that can migrate into the IGU seals and cause failure.
• Exposed Secondary Seal
If the IGU installation allows the secondary seal to be exposed to sunlight (UV) then it should not be manufactured with a Polysulfide secondary seal as this has poor UV stability and can eventually break down and lead to failure of the unit. For cases where IGUs are installed with the edges exposed, an alternate secondary seal, such as Silicone, should be selected. It is important to talk to your IGU supplier to determine the correct IGU make up for the desired application.
It is also important that if units are being stored prior to installation, regardless of secondary seal type, they should be always protected from sunlight and moisture exposure.
As stated previously an IGU is a complex system that requires both manufacturers and installers to be vigilant to ensure that an IGU meets the desired performance and has a long life. Failures of IGUs can cause significant financial and reputational consequences. The best way to avoid any issues is to ensure you are purchasing your IGUs from a reputable and compliant AS 4666: 2012 supplier, such as an IGMA member, and that the installer follows the correct installation methods as described in that standard. Both manufacture and installation are equally important to ensure the longevity of IGUs.
If you have any questions or would like any further information, please reach out to our technical team and we would be happy to assist.
