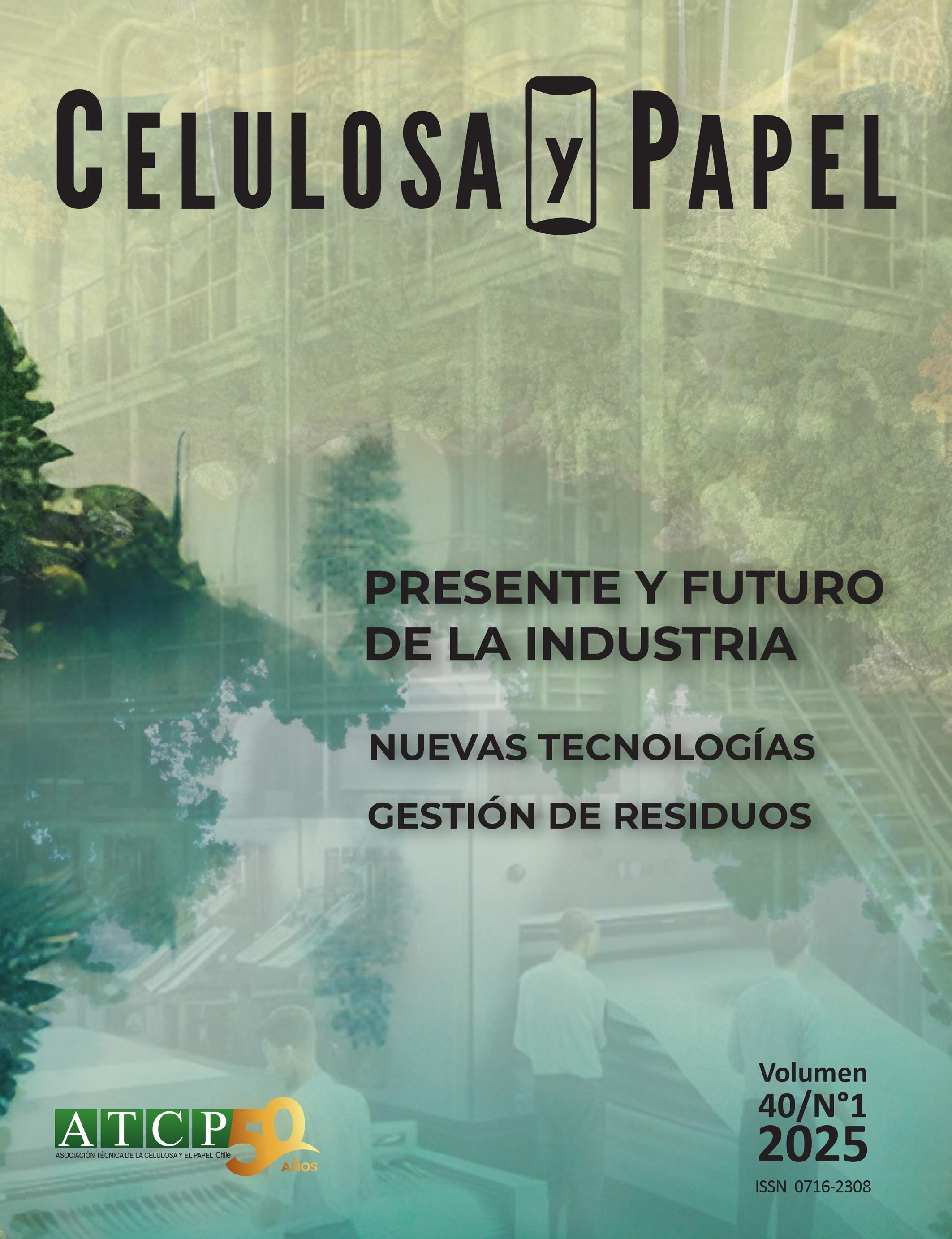
Presidente
02 01 03 Álvaro Oñat
Héctor Godoy 1er VicePresidente
Presidente
02 01 03 Álvaro Oñat
Héctor Godoy 1er VicePresidente
Secretario General
Miguel Pereira Director Financiero
María Graciela
Aguayo Directora
Marco Rodríguez 2do VicePresidente 08 07 09 Miguel Salinas Director Miguel Osses Director José Soza Director 05 04 06 Víctor Otárola
GRUPO EDITORIAL ATCP CHILE
Comité Editorial
Álvaro Oñat, Marco Rodríguez, Víctor Otárola
Periodista Natalia Sáez
Diseño y Diagramación Alejandra Cerda
Síguenos
El reciente Congreso de Olores, celebrado en la UNAB en Santiago los días 9 y 10 de abril, organizado por la Asociación AMIGO, resultó ser una instancia de gran valor. La calidad de las presentaciones y la excelente organización nos permitieron actualizar nuestros conocimientos en esta materia crucial, entre ellos el uso de la ciencia ciudadana, las mejoras en sensorización y actualización de cambios normativos y metodológicos, entre otros. Este evento me motivó a escribir sobre la evolución y los desafíos en la gestión de olores, especialmente en la industria forestal.
Históricamente, las emisiones de olor han sido un foco de atención en el ámbito medioambiental. La industria ha trabajado continuamente para minimizar las externalidades hacia las comunidades aledañas. Esta evolución ha sido impulsada tanto por cambios regulatorios como por una transformación en la visión de la propia industria. La industria forestal, en particular, ha enfrentado desafíos significativos debido a sus procesos de producción de celulosa. Los diseños originales de las plantas no siempre consideraban la captura de todas las fuentes de emisión, lo que ha llevado a la ejecución de diversos proyectos de inversión para asegurar la captura de fuentes fijas y emisiones difusas a fin de tener el menor impacto nivel posible en términos de percepción olor.
En el pasado, las exigencias regulatorias en cuanto a emisiones de olor eran laxas o inexistentes. La atención se centraba principalmente en otros contaminantes atmosféricos, dejando en segundo plano el impacto de los olores en la calidad de vida. Sin embargo, la creciente conciencia ambiental y las demandas de las comunidades han traído como resultado en mejoras en los procesos y en regulaciones más estrictas y específicas. Hoy en día, se reconoce el impacto de los olores en el bienestar de la población, y las normativas buscan controlar y minimizar estas emisiones.
La nueva mirada de la industria se basa en la adopción de tecnologías más robustas, la implementación de mejores prácticas operacionales y la transparencia en la comunicación con las comunidades. Se ha invertido en sistemas de control de emisiones de última generación, respaldos de quemadores y otras tecnologías , y además se han fortalecido los mecanismos de monitoreo y seguimiento para detectar y abordar rápidamente cualquier incidente. A todo lo anterior se suma que: Se han implementado espacios de trabajo conjunto y participación, involucrando a las comunidades en la identificación de problemáticas y alertas tempranas.
En conclusión, la gestión de olores en la industria forestal ha avanzado significativamente. Si bien persisten desafíos, los avances logrados son un claro indicio de que es posible construir una industria forestal más sostenible y respetuosa con su entorno.
p c
Artículo Técnico
Evaluación de Gas Solution para la Neutralización de Gases Odoríferos en Entornos Industriales
Entrevista Destacada
Juan Carlos Carrasco
Liderando la innovación desde la UDT
Opinión
Candelaria Briceño
Conectando puentes hacia un Chile que Transforma
Nuevos Socios
Noemí Alvarado y Diego Loncomilla
Artículo Técnico
Editorial
Reportaje
De la celulosa al tissue: el compromiso ambiental detrás de cada hoja
Opinión
Pamela Castillo
Sinergia entre Normativa Ambiental y Tecnología para el Manejo de la Calidad del Aire
Entrevista
Marianne Hermanns
Gestión ambiental con visión de futuro
Opinión
Raúl Arias
¿Y si Buscamos en la Naturaleza?
18 06 27 10 22 12 26 16 28
Control del bulking filamentoso en lodos activados de cinco industrias de celulosa y papel en Brasil 03
Opinión
Alejandra Hernández
El Futuro del Control de Olores: Tecnologías y Regulaciones en Evolución
Nuevos Socios
Romina Márquez y Víctor Parra
Actualidad
XIII Congreso nacional de estudiantes Ingeniería Química
Artículo Técnico
Innovación y Tecnología en la Gestión Preventiva Ambiental para las Operaciones Impecables
Visión Universitaria
Teresita Marzialetti
Nuevos Directores
Actualidad
Propuesta de gestión residuos impulsa economía circular.
Jóvenes Construyendo Futuro
Breves
En un contexto global donde la sostenibilidad dejó de ser una tendencia para convertirse en una exigencia transversal, la industria de la celulosa y el papel ha debido repensar sus procesos productivos, especialmente en la conversión de celulosa en productos tissue, como papel higiénico, servilletas y toallas. Este segmento, que tiene un contacto directo y cotidiano con las personas, enfrenta el desafío de satisfacer una demanda creciente sin comprometer los recursos naturales ni el equilibrio ambiental. En 2024, el mercado mundial de papel tissue fue valorado en aproximadamente USD 90.99 mil millones, con proyecciones que indican un crecimiento hasta USD 154.54 mil millones para 2032, impulsado por una tasa de crecimiento anual compuesta (CAGR) del 6.95%. (Fuente: Fortunebusinessinsigths.com).
A nivel mundial, las compañías del rubro han adoptado tecnologías de última generación para reducir el consumo de agua, energía y materias primas, impulsando modelos de producción circular que permiten reutilizar subproductos y minimizar residuos. En países como Suecia, Finlandia o Canadá, líderes en manejo forestal sustentable, la trazabilidad del origen de la fibra, la eficiencia en el uso de agua en las plantas de conversión y la valorización de residuos industriales forman parte de una gestión integral orientada a la neutralidad ambiental.
Chile no se ha quedado atrás. Con una industria forestal consolidada y estándares ambientales cada vez más exigentes, algunas empresas han implementado estrategias concretas para reducir la huella ambiental en todas las etapas del proceso. Esto incluye el uso de energía autogenerada a partir de biomasa renovable, programas de eficiencia hídrica, recirculación de aguas industriales y compromisos de valorización del 100% de los residuos sólidos no peligrosos hacia 2030.
El desafío actual no solo radica en producir más y mejor, sino en hacerlo con respeto por el entorno, promoviendo una industria del papel que, desde la celulosa, avance con firmeza hacia una economía baja en carbono y alineada con los principios de la economía circular.
EJEMPLO EN INDUSTRIA NACIONAL
En el complejo proceso que convierte la celulosa en papel y productos derivados, la sostenibilidad ya no es una opción, sino una necesidad. Y en esa transición, profesionales como Francisco Albornoz, Ingeniero Civil Químico de la Universidad de Concepción y actual Jefe de Desempeño Ambiental en Celulosa ARAUCO, cumplen un rol clave.
“Comencé mi carrera profesional en el área comercial de COPEC, como Jefe de Zona del canal de lubricantes en Copiapó. Más adelante, llegué a ARAUCO, inicialmente a Celulosa Planta Valdivia”, comenta el profesional. Desde entonces, su trayectoria ha estado marcada por una diversidad de roles: desde Ingeniero de Procesos, pasando por áreas de Personas y Seguridad, hasta especializarse en procesos ambientales.
Hoy, desde su posición en la Gerencia de Medio Ambiente, su objetivo es claro: “Mi foco está en monitorear, controlar y optimizar las emisiones gaseosas, líquidas y sólidas de las plantas. Esto implica implementar estrategias para reducir el impacto ambiental, promoviendo prácticas sostenibles dentro de los procesos productivos que dan origen a la celulosa y, con ello, a los productos que llegan a las personas”.
CELULOSA: UN PROCESO CON BASE RENOVABLE
En el corazón de este proceso se encuentra la celulosa, base esencial para papeles, cartones y múltiples soluciones que forman parte de la vida cotidiana. Pero, ¿cómo se
asegura que esta producción sea sustentable?
“Desde su origen, la producción de celulosa es un proceso sustentable, porque utiliza un recurso renovable como la madera y opera con ciclos cerrados para la recuperación de químicos. Además, las plantas generan su propia energía a través de la combustión de biomasa, lo que incluso permite inyectar excedentes al Sistema Eléctrico Nacional”, explica Albornoz.
Esta autogeneración energética no solo reduce costos, sino que disminuye significativamente el uso de combustibles fósiles. En ARAUCO, este enfoque va acompañado de una gestión ambiental rigurosa en cada etapa del proceso.
USO EFICIENTE DEL AGUA Y REDUCCIÓN DE EMISIONES
Uno de los grandes desafíos del sector es el uso del agua. Al respecto, Albornoz destaca: “Todas las plantas cuentan con programas de reducción de consumo de agua, enfocados en mejorar la eficiencia hídrica y minimizar impactos ambientales. Se han implementado medidas como la recirculación interna, recuperación de condensados y reutilización de aguas en diferentes etapas del proceso”.
En cuanto a las emisiones de gases de efecto invernadero, ARAUCO ha dado pasos relevantes mediante proyectos de cogeneración con biomasa residual. “Nuestros sistemas utilizan subproductos forestales, incluido el licor negro, como combustible renovable y carbono neutro. Estos proyectos están registrados bajo estándares internacionales como el Mecanismo de Desarrollo Limpio (MDL)”, precisa.
Mirando hacia el futuro, ARAUCO ha asumido un compromiso ambicioso: valorizar el 100% de los residuos sólidos no peligrosos para 2030. “Nuestro propósito es eliminar completamente el envío de estos residuos a rellenos sanitarios, avanzando hacia una operación más limpia y eficiente”, afirma Albornoz.
Este desafío es abordado desde una perspectiva tanto ambiental como económica. “La valorización de residuos implica desarrollar soluciones competitivas, que integren innovación, eficiencia y generación de valor. En ese sentido, trabajamos en alianzas estratégicas con terceros, centros internos de valorización y mejoras continuas en los procesos productivos”, explica.
Este enfoque se enmarca en la Hoja de Ruta de Economía Circular promovida por el gobierno, pero va más allá: busca transformar residuos en recursos útiles, cerrando el ciclo productivo de forma coherente con los principios de sostenibilidad.
Cada hoja de papel, cada producto que llega al consumidor final, tiene detrás un proceso industrial que puede —y debe— ser responsable con el entorno. Desde la elección de materias primas renovables, pasando por el uso eficiente del agua y la energía, hasta la valorización de residuos, ARAUCO está configurando una cadena de valor donde el respeto por el medio ambiente es parte esencial.
“En nuestra labor diaria, entendemos que el desempeño ambiental no es un objetivo aislado. Es parte integral de cómo hacemos las cosas, de cómo transformamos la celulosa en productos que llegan a miles de hogares y empresas, con la convicción de que se puede producir de manera eficiente, rentable y respetuosa con el entorno”, concluye Francisco Albornoz.
Su mirada técnica, su experiencia transversal en distintas áreas de la compañía y su compromiso con el desarrollo sostenible reflejan cómo la industria forestal y de celulosa puede liderar la transición hacia una economía más circular y baja en carbono.
p c
Históricamente, la industria de celulosa y papel ha sido percibida como un sector de alto impacto ambiental, especialmente en lo que respecta a la contaminación atmosférica y la emisión de olores. No obstante, impulsada tanto por el fortalecimiento de la normativa ambiental como por la creciente conciencia social respecto a la sostenibilidad, en las últimas décadas esta industria ha experimentado un cambio significativo hacia prácticas más responsables.
En 2021 comenzó la segunda revisión de la Norma de Emisión de Compuestos TRS, un proceso que incorpora análisis comparativos con normativas internacionales, informes de cumplimiento y avances tecnológicos. Esta revisión busca proponer alternativas efectivas para minimizar la percepción de olores, mediante un mayor control de los procesos en las fuentes de emisión. Es en este contexto donde la tecnología se convierte en un aliado fundamental.
En las últimas décadas, las soluciones tecnológicas han evolucionado de forma notable, pasando de ins-
trumentos voluminosos y de uso exclusivo en laboratorio a dispositivos cada vez más compactos, portátiles y precisos. Un claro ejemplo de esta evolución es el uso de técnicas cromatográficas que hoy permiten realizar mediciones en terreno de compuestos azufrados como H2 S, SO2 , MM, EM, DMS, DMDS y DES, entre otros. Asimismo, en el caso de los hidrocarburos, se dis-
pone de analizadores capaces de detectar cadenas livianas y pesa -
das (C 2–C6; C6 –C12), COVs, BTEX, etc.
Nuestra representada, Chromatotec, ofrece soluciones que optimizan el control operacional asociado a estas emisiones, posibilitando una identificación más precisa de las fuentes de emisión por área.
El avance tecnológico no se detiene. Hoy, soluciones como los nodos Bettair, que integran inteligencia artificial, representan una alternativa económica para la cuantificación de gases, con un nivel de correlación óptimo (r = 0,9) respecto a métodos de referencia. Esto permite no sólo medir, sino también optimizar procesos de manera continua y eficaz.
El futuro de esta industria dependerá de su capacidad para adaptarse y evolucionar en un entorno regulatorio que exige un compromiso real con la sostenibilidad. Si bien la tecnología es una herramienta imprescindible, su verdadero impacto radica en una implementación acompañada por una genuina responsabilidad ambiental por parte de las empresas.
p c
Marianne Hermanns
Gerente Medio Ambiente
La actual Gerente de Medio Ambiente de ARAUCO repasa su trayectoria en el sector público y privado, abordando los principales desafíos ambientales en la industria de la celulosa y el papel. Con una mirada estratégica, destaca la importancia de anticiparse a las regulaciones, mejorar continuamente el desempeño ambiental y fortalecer la colaboración con el Estado, las comunidades y el entorno científico-técnico.
“Después de egresar del Colegio Alemán de Concepción, decidí estudiar Ingeniería Química en la Universidad de Concepción”, recuerda Marianne Hermanns. Durante su formación universitaria, combinó los tradicionales cursos del sector celulosa y papel con asignaturas emergentes de medio ambiente, una decisión que marcó el enfoque de su carrera. “Fue una manera de prepararme para un mundo productivo más exigente, que ya demandaba procesos más responsables y sostenibles”, comenta.
Aunque no ha cursado postgrados formales por razones familiares, ha complementado su formación con diversos cursos de especialización técnica, un desafío que espera retomar en el mediano plazo.
“El aprendizaje continuo es clave para aportar valor en una industria que evoluciona constantemente”, sostiene.
En 2014 asumió el desafío de convertirse en Seremi de Medio Ambiente en la Región del Biobío. “Recibí la invitación con sorpresa, pero también como un reconocimiento a mi trayectoria profesional y a la credibilidad construida con años de trabajo técnico”, explica. A pesar de lo desafiante del contexto político y familiar, Hermanns lideró importantes avances en calidad del aire, planes de descontaminación por material particulado, recambio de calefactores, y restauración de áreas afectadas por incendios forestales con especies nativas. “Implementamos programas inéditos en esa época, que lograron vincular la gestión pública con la participación ciudadana y la innovación ambiental”, señala. Su gestión también coincidió con la entrada en operación de la Superintendencia del Medio Ambiente, marcando un cambio profundo en la institucionalidad ambiental chilena. “Fue un periodo intenso, pero enriquecedor, donde aprendimos a navegar entre la política, la técnica y la gestión de territorio en una región industrializada y diversa”.
Desde su actual vereda en ARAUCO, Hermanns, impulsa
una agenda ambiental centrada en la mejora continua del desempeño de las plantas de celulosa. “No basta con cumplir la norma, el verdadero desafío es superarla, anticiparse a los cambios regulatorios y generar valor desde la sostenibilidad”, afirma. Su labor abarca desde la verificación de cumplimiento legal hasta la implementación de proyectos estratégicos como la valorización total de residuos industriales no peligrosos al año 2030. “Hemos desarrollado productos como mejoradores de suelo, que devuelven nutrientes al ecosistema forestal, cerrando ciclos bajo principios de economía circular”, explica. En paralelo, ARAUCO trabaja en la optimización de recursos hídricos, reducción de emisiones, control de olores y monitoreo ambiental constante. “Uno de los focos ha sido reducir el impacto por olores en las plantas de celulosa, a través de mejoras tecnológicas, ajustes operacionales y, sobre todo, un cambio cultural dentro de la operación”, sostiene.
La empresa también ha implementado un modelo de prevención de delitos ambientales, junto con robustecer los procesos de evaluación ambiental de nuevos proyectos. “Buscamos evaluar tempranamente los impactos, generar instancias de diálogo técnico con el Estado y actuar con transparencia ante las comunidades”, comenta.
Mirando al futuro, Hermanns identifica desafíos estructurales para el sector: “Debemos avanzar en replantación, prevención de incendios forestales, investigación de su origen y fortalecimiento de la seguridad rural”. También destaca la importancia del rol del sector en la mitigación del cambio climático, mediante la captura de CO2, generación de energía renovable y sustitución de materiales fósiles. “La celulosa y los productos derivados de la madera son, por su carácter renovable, los materiales del futuro”, afirma.
Sobre el vínculo con organismos públicos, resalta el valor del trabajo colaborativo. “Participamos activamente en procesos de elaboración normativa, entregando antecedentes técnicos y abriendo nuestras operaciones a la autoridad”, indica. La experiencia conjunta en la delimitación del Santuario de la Naturaleza en la desembocadura del río Carampangue, la comuna de Arauco, es un ejemplo concreto: “Junto a autoridades, academia y comunidad, entregamos información científica para definir su polígono de protección y avanzar en un plan de manejo sustentable”, concluye.
p c
El desarrollo industrial enfrenta enormes y múltiples desafíos, como la competitividad global, la vertiginosa renovación y obsolescencia de las tecnologías informáticas, la escasez de personal calificado, normativas cada vez más estrictas, reducción de costos, crecimiento sostenible, y por supuesto el cuidado del medio ambiente y de la salud de las personas. Todo lo anterior en un ecosistema social con comunidades más informadas y empoderadas, además de la instantaneidad y masividad de las redes sociales.
Por supuesto que la industria de la celulosa y el papel no es ajena a estos desafíos y menos aún en nuestro país, en donde las exigencias de las normativas de olor, ruido, eficiencia energética, el uso del agua, la gestión y reducción de residuos, la huella de carbono, y las buenas relaciones con las comunidades vecinas; todas condiciones que, en conjunto, demandan un alto nivel de excelencia en la operación de las plantas industriales, acuñándose el término “Operaciones Impecables”.
¿Cómo hacer para lograr Operaciones Impecables y no morir en el intento?
Evidentemente no existe una receta infalible para lograrlo, pero sí hay herramientas que ayudaban mucho en el pasado y que tal vez en la vorágine de estos tiempos, han ido quedando en el olvido, me refiero a la sociabilización del
conocimiento, de las mejores prácticas y las experiencias entre profesionales afines.
Aristóteles decía que la naturaleza humana se caracteriza por la capacidad de razonar y la necesidad de sociabilizar. Así el hombre busca vivir en sociedad principalmente por la necesidad de cooperación y protección, transmisión de conocimientos y la búsqueda de bienestar.
Raúl Arias
Gerente General Neo inert
rentes a la naturaleza humana, al ámbito profesional y en particular al quehacer de la industria de la celulosa y el papel, aparece como una herramienta muy útil y también muy al alcance, el revivir los comités de trabajo transversales de áreas a fines, por ejemplo, el Comité de Hornos y Caustificación y el Comité de Calderas Recuperadoras de Chile, que marcaron el inicio de varias generaciones de profesionales de esta industria. En ellos se intercambiaban experiencias de eventos recientes, se discutían con profundidad aspectos de la operación y el mantenimiento para poder optimizar los procesos, hacerlos más eficientes y reducir la ocurrencia de incidentes. Para profesionales nuevos era una instancia tremendamente enriquecedora en su desarrollo profesional y para los más experimentados, era una buena forma de transmitir sus conocimientos a las nuevas generaciones.
Es importante que estos comités sean transversales, mientras más experiencias distintas haya, más enriquecedor y útil será para la industria, esfuerzos individuales no han sido y no serán suficientes, se requiere el compromiso de todos los actores involucrados, tanto de las empresas como de sus profesionales.
En tiempos en donde es imperiosa la necesidad de realizar operaciones impecables, tal vez sea una buena idea volver a buscar en la naturaleza humana. p c
Al llevar estos conceptos filosóficos inhe-
es que con la celulosa reemplazamos toneladas de plástico que terminarían en el océano. ¡Esos son muchos vasos de café!
Bruno Arias 1, Edwin García 2 y Bernardita Muñoz 3
1. Centro de Investigación y Desarrollo, DUX ; bruno.arias@duxgrupo.com.br
2. Centro de Investigación y Desarrollo, Innovaquímica; egarcia@innovaquímica.cl
3. Gerencia de Ventas, Banff Chemical; bernardita.munoz@banffchem.cl
Resumen
La creciente preocupación por la calidad del aire ha impulsado el desarrollo de Gas Solution, una tecnología innovadora creada y patentada por Dux en colaboración con Innovaquímica y Banffchem para el control de olores industriales. Esta solución avanzada emplea una combinación de aceites esenciales y nanotecnología para neutralizar eficientemente gases odoríferos como sulfuro de hidrógeno (H2 S), amoníaco (NH3), compuestos orgánicos volátiles (COV), compuestos reducidos de azufre (TRS), comunes en instalaciones de tratamiento de aguas residuales.
Los resultados de estudios recientes demuestran que Gas Solution logra una reducción de hasta el 99% en las concentraciones de olores, destacándose por no generar subproductos tóxicos y por su composición biodegradable que garantiza seguridad para el medio ambiente. A diferencia de métodos convencionales, esta tecnología patentada ofrece una solución más eficiente y sostenible, aunque se recomiendan ajustes en la dosificación para optimizar aún más su rendimiento. Gas Solution se posiciona como una alternativa innovadora y respetuosa con el entorno para la gestión de olores industriales, respondiendo a los actuales desafíos de calidad del aire con un enfoque técnico y ambientalmente responsable.
Palabras Clave: control de olor; gas solution; medio ambiente.
La creciente conciencia ambiental ha incrementado la
demanda de soluciones efectivas para gestionar las emisiones odoríferas en plantas de tratamiento, fábricas y vertederos. A diferencia de los métodos convencionales que simplemente enmascaran los olores, nuestra tecnología patentada ofrece una neutralización real mediante un sistema avanzado de atomización molecular. Desarrollada a partir de una combinación científica de más de 350 aceites esenciales y principios activos, cuenta con 50 formulaciones específicas para abordar diversos tipos de olores industriales. La solución destaca por su capacidad de eliminación efectiva, sin recurrir a enmascaramientos temporales.
Todos los componentes empleados son completamente atóxicos y biodegradables, garantizando la máxima seguridad para las personas, animales y el medio ambiente. Esta aproximación tecnológica representa un avance significativo en el manejo sostenible de emisiones odoríferas, ofreciendo resultados permanentes sin comprometer la calidad del entorno.
2. ANTECEDENTES
Existen muchos métodos efectivos para aplicar la línea
Gas Solution de Dux. El método más adecuado se determinará por varios factores, como:
• El tipo de olor a controlar.
• La fuente de emisión de olores.
• El tamaño del área a controlar.
• La posible presencia de un sistema de hardware de control de olores existente.
• Las condiciones del gas ambiente o de proceso.
• La ubicación del objetivo que necesita ser protegido de los olores (generalmente personas).
• La flexibilidad de las instalaciones de ingeniería.
La aplicación óptima de productos líquidos para neutralización de olores requiere su nebulización directa en el aire donde se originan los compuestos odoríferos o en proximidad a la fuente del mal olor. El principal reto técnico radica en asegurar la correcta atomización del producto en el ambiente gaseoso para permitir la interacción molecular efectiva, más que en el mecanismo de neutralización en sí mismo.
Las moléculas con mal olor y las gotículas del producto deben entrar en contacto entre sí o estar lo suficientemente cerca para que la atracción molecular tome el control. En última instancia, el mal olor debe ser adsorbido en la superficie de la gota y/o absorbido por el mecanismo de solubilidad del proceso de control de olores. Si las moléculas de mal olor permanecen libres en el aire, por encima del umbral de olor del gas, el olor no será controlado.
La "nebulización" es clave para la efectividad del producto, ya que genera gotas menores de 25 micrones (óptimo <10μ). Esto aumenta su eficacia, reduce el consumo y mejora la distribución en el aire. Los equipos básicos de pulverización producen gotas más grandes con menor tiempo de residencia y cobertura irregular, requiriendo mayor cantidad de producto para resultados inferiores.
Para entender por qué las gotas pequeñas son tan importantes, pensemos en la diferencia de área entre gotas de 10 micrones y 1000 micrones. Si comparamos estas gotas, vemos que, al aumentar el tamaño, la superficie de contacto se reduce mucho. De hecho, las gotas de 10 micrones tienen hasta 100 veces más área de contacto que las de 1000 micrones. Esto significa que, al usar gotas más pequeñas, el sistema para controlar olores funcionará mucho mejor.
En Dux, hemos desarrollado un modelo que considera las variables primarias de la tecnología de control de olores. La solubilidad es el primer mecanismo de control de olores. Debido a la forma en que funciona el producto, el gas odorífero debe ser solubilizado en las gotículas atomizadas del producto para que ocurra una reacción. La eficiencia en la eliminación de malos olores es proporcional a la solubilidad del mal olor. Dicho de otra manera, podemos mejorar la eficiencia de eliminación aumentando la solubilidad de la gota atomizada. La solubilidad está relacionada con qué aceite esencial se aplicará, considerando las siguientes variables:
• Aumente la concentración del producto (concentrar la
tasa de dosificación) – [CONC].
• Reduzca el tamaño de la gota atomizada – [TAMAÑO].
• Aumente el contacto (tiempo de residencia entre el producto odorífero y la gota de producto) – [TIEMPO].
• Aumente la velocidad de las gotas y, por lo tanto, la velocidad de impacto entre ambas, ayudando a la atracción molecular de la reacción – [VELOCIDAD].
• Cambie la polaridad de la gota – [POL].
Estas relaciones pueden resumirse de la siguiente manera:
SOLUBILIDAD = [CONC] * [TIEMPO] * [VEL] * [POL] = (EFICIENCIA) / TAMAÑO
Idealmente, queremos una baja concentración de producto, un largo tiempo de contacto y una gota pequeña con alta velocidad. Desafortunadamente, no siempre es el caso, y es necesario optimizar las variables controlables para compensar aquellas que no se pueden controlar.
Los tipos de equipos de entrega pueden variar desde una máquina de nebulización simple, transportada de un lugar a otro, hasta sistemas complejos de medición, inyección y recuperación, usados en sistemas de tratamiento de aire a gran escala. Estos sistemas se pueden aplicar de diversas maneras en distintos ambientes, incluyendo refinerías de petróleo, estaciones de tratamiento de aguas residuales, fábricas de procesamiento, vertederos y fábricas industriales de todo tipo. Debido a la flexibilidad de aplicación y adaptabilidad del producto en diversos entornos, esta adaptabilidad reduce aún más los costos de capital.
El producto puede ser diluido y aplicado directamente en el sistema de nebulización atomizada para eliminar malos olores en áreas de compostaje confinadas, tratamiento de agua, tratamiento de lodo, manejo de residuos sólidos y procesos industriales.
Al aire libre, el producto controla olores en tanques de aireación, lagunas, pozos de lodo, vertederos, sitios de remediación y lugares industriales. Los sistemas son altamente efectivos en la descomposición de olores y en la eliminación de vapores nocivos que pueden extenderse a las áreas circundantes.
2.1 Boquillas de Nebulización
Las boquillas atomizadoras son el método más utilizado para dispersar productos en la atmósfera. Aunque varios fabricantes ofrecen estas boquillas, los sistemas Dux destacan por su ingeniería especializada y knowhow, garantizando máxima eficiencia. La selección de la boquilla óptima varía según cada proyecto específico, ya que cada caso tiene requerimientos únicos de rendimiento
Las boquillas pueden utilizarse en ambientes interiores, fijadas en paredes, tuberías, soportes o estructuras, y también pueden montarse en un sistema de lavado, sistema de tratamiento de aire o pila de emisión, utilizando una serie de boquillas o un sistema de agrupamiento. Las boquillas pueden fijarse en perímetros de edificios, aberturas de edificios, áreas de transferencia de carga o colgarse libremente alrededor de áreas de procesos que generan olores.
Los sistemas de boquillas también se utilizan en cercas de perímetro como último recurso para controlar olores que están escapando de un lugar cerrado.
Los sistemas de boquillas simples se adaptan a la mayoría de las aplicaciones industriales donde se necesita una fuente fija/continua de control de olores. Con frecuencia, se puede instalar un mayor número de boquillas con una tasa de entrega mayor (mayor caudal) para ampliar el tratamiento del área con olor.
2.2 Nebulizadores Portátiles (Manuales y eléctricos)
Los nebulizadores con sistema de bombeo manual, usados en agricultura y control de plagas, pueden utilizarse para nebulizar los productos en áreas donde no es necesario un control constante de olores, para aplicaciones tópicas simples y donde no haya disponibilidad de energía eléctrica.
Pequeños atomizadores eléctricos portátiles de capacidad variable pueden emplearse para descontaminar áreas pequeñas y grandes.
El uso de máquinas de nebulización portátiles ofrece al consumidor máxima portabilidad y cobertura con un mínimo de gastos.
3. OBJETIVOS
Dux desarrolló el “Odor Box”, un equipo de prueba de laboratorio para evaluar la eficiencia en el control de gases y probar productos neutralizadores.
El estudio tiene como objetivo evaluar la acción de neutralización y reducción de olores sobre los malos olores. Para obtener los tratamientos odoríferos, se utilizan patrones naturales de malos olores. Se utilizan dos tipos de tratamientos (Sustancia de Prueba y Control) con varias repeticiones. A continuación, se describe su principio de funcionamiento.
4. METODOLOGÍA
Seguimos la metodología internacional como referencia para realizar los estudios.
ASTM E 1593-13 (2013): Práctica Estándar para Evaluar la Eficacia de los Productos Ambientadores en la Reducción de la Intensidad del Mal Olor Perceptible Sensorialmente en Interiores.
Metodología de prueba en 5 pasos:
La caja de pruebas de laboratorio está diseñada para evaluar la neutralización de gases y olores, opera con alta precisión y control estricto, siguiendo un protocolo bien establecido que garantiza resultados confiables y reproducibles. A continuación, se detallan los pasos detallados, con explicaciones técnicas y pasos adicionales para garantizar la calidad del proceso:
a. Introducción de gases olorosos
Los gases olorosos para neutralizar se introducen en la cámara de reacción mediante un sistema de nebulización con boquillas atomizadoras, basado en el principio Venturi. Este sistema permite una eficiente atomización del gas y su dispersión homogénea en la cámara. Este proceso inicial es monitoreado por sensores que aseguran una concentración uniforme para la prueba.
b. Lectura inicial de gas
Luego de introducir el gas, un medidor de precisión realiza la lectura inicial de parámetros, como concentración en ppm (partes por millón), composición química y otras características específicas, dependiendo del tipo de gas evaluado. Este paso establece una línea de base para una comparación posterior.
c. Aplicación del producto neutralizante
El producto neutralizante se nebuliza hacia el interior de la cámara a través del sistema de atomización. La aplicación está controlada por válvulas dosificadoras automáticas, que garantizan la precisión en la cantidad de producto introducido. Los sensores internos monitorean el flujo y la cobertura del producto en tiempo real.
d. Monitoreo en tiempo real
Durante la aplicación, el medidor de precisión lee continuamente la concentración de gas en la cámara. Este monitoreo en tiempo real es esencial para evaluar la dinámica de reducción de ppm e identificar la eficiencia del producto en diferentes intervalos de tiempo.
En fracciones de segundos se observa la reducción de gases olorosos en el medidor. Los datos cuantitativos, como la tasa de reducción, el tiempo de respuesta y el porcentaje de eficiencia, se registran automáticamente
e. Verificación de eficiencia cuantitativa
en un sistema integrado de recopilación de datos.
5. RESULTADOS
La Figura 5.2 muestra el historial de neutralización de un gas odorante específico, representado por la variación de la concentración (en partes por millónppm) a lo largo del tiempo (en segundos). El gráfico se obtuvo a partir de los datos registrados por un sensor de detección continua, ubicado en un punto estratégico para la lectura.
Se observa una marcada disminución de la concentración de gas en los primeros segundos tras la aplicación de la solución neutralizante por nebulización, con una reducción de aproximadamente 100 ppm a valores inferiores a 5 ppm en menos de 5 segundos. Este comportamiento sugiere una alta eficiencia de la formulación neutralizante, asociada a una rápida cinética de reacción entre los compuestos odorantes y los principios activos presentes en el agente aplicado.
Desde un punto de vista técnico, esta reducción exponencial concuerda con los modelos de primer orden, frecuentemente descritos en la literatura para procesos de neutralización mediante reacciones químicas o físico-químicas, en los que la tasa de eliminación es proporcional a la concentración inicial del contaminante. Este resultado destaca la eficacia del sistema nebulizador adoptado, cuya distribución fina y homogénea del agente neutralizante mejora el contacto superficie-volumen con la columna de gas.
Además, la gráfica demuestra la estabilidad de la neutralización a lo largo del tiempo, manteniéndose la concentración residual prácticamente constante en los momentos posteriores, lo que sugiere no sólo una acción rápida, sino también la persistencia del efecto neutralizante en el ambiente monitoreado.
En síntesis, a lo largo de este documento, hemos presentado de manera integral la metodología y las tecnologías innovadoras implementadas en la aplicación, especialmente en la línea Gas Solution de Dux, con el objetivo de neutralizar gases y controlar olores en entornos industriales. Este estudio exhaustivo refleja no solo nuestro compromiso con la excelencia técnica, sino también nuestra dedicación a la continua búsqueda de soluciones eficaces y sostenibles.
El análisis de los procesos implementados evidencia nuestra capacidad para abordar los desafíos más complejos de neutralización de gases mediante tecnologías avanzadas y metodologías probadas. Los resultados obtenidos en aplicaciones reales demuestran la eficacia de Gas Solution, que se consolida como referente del sector por su enfoque proactivo y preventivo.
Nuestra solución destaca por integrar innovación tecnológica con responsabilidad ambiental, garantizando entornos industriales más seguros y sostenibles. La combinación de experiencia técnica, desarrollo continuo y compromiso ecológico nos permite ofrecer respuestas personalizadas y de alto impacto.
Al optar por Dux, las empresas no solo resuelven sus retos inmediatos de calidad del aire, sino que avanzan hacia operaciones industriales más limpias y responsables con el medio ambiente, asegurando un futuro sostenible para sus actividades productivas. p c
Director UDT
Con más de 20 años de experiencia en investigación aplicada y desarrollo tecnológico, el destacado profesional lidera actualmente la Unidad de Desarrollo Tecnológico (UDT) de la Universidad de Concepción, una institución reconocida por su capacidad de generar soluciones concretas para sectores productivos como la celulosa, el papel, la bioenergía y los materiales sostenibles. Doctor en Ingeniería Química por la Universidad de West Virginia e Ingeniero Civil Químico por la Universidad de Concepción, su trayectoria ha estado profundamente ligada al desarrollo tecnológico del país y, en particular, al sector forestal.
Carrasco conoce la UDT desde sus cimientos: fue parte del equipo fundacional del centro en 1996, en un contexto en que la vinculación entre universidad e industria comenzaba a consolidarse como un eje estratégico para el desarrollo regional. Durante 14 años lideró el área de Medioambiente, enfocándose en soluciones tecnológicas para el tratamiento de residuos, eficiencia energética y reducción de emisiones. “La UDT nació con una vocación aplicada. Su esencia es hacer investigación con sentido práctico y con impacto directo en el entorno productivo”, comenta.
Posteriormente, su formación académica continuó en Estados Unidos, donde obtuvo su doctorado y se desempeñó profesionalmente en la instalación y operación de plantas para densificación energética de biomasa. Esta experiencia internacional, según señala, fue clave para consolidar una visión sistémica e innovadora del desarrollo tecnológico. “En Estados Unidos entendí la importancia de escalar procesos desde el laboratorio a niveles industriales, un desafío que requiere no solo conocimiento técnico, sino también capacidades de gestión y colaboración interinstitucional”.
A su regreso a Chile, Carrasco asumió labores académicas en la Universidad de Concepción y poco después fue
elegido como director ejecutivo de la UDT. “Conozco las raíces de esta institución. Regresé por el compromiso con su esencia: la investigación y desarrollo aplicado con impacto real en la industria”, señala.
Desde sus inicios, la UDT ha cultivado una relación virtuosa con el sector productivo, fortalecida por su modelo de autofinanciamiento, que ha exigido pertinencia, oportunidad y efectividad en cada proyecto. “Eso nos obliga a generar propuestas relevantes, con impacto real y utilidad para las empresas. Nuestra colaboración con compañías del ámbito forestal, así como con programas públicos como CORFO, FONDEF o FIA, ha sido esencial para mantenernos vigentes y competitivos”, explica Carrasco.
El centro fue pionero en abordar desafíos ambientales en los años 90, mucho antes de que conceptos como economía circular, sostenibilidad o huella de carbono se convirtieran en tendencia. “Fuimos de las primeras instituciones en Chile que desarrollaron tecnologías para
valorización de residuos, bioproductos y eficiencia energética en procesos industriales. En ese tiempo, hablar de bioeconomía era casi visionario”, destaca el director UDT.
En el rubro de celulosa y papel, la institución ha sido un actor clave para la modernización del sector. Ha promovido activamente la adopción de tecnologías limpias, procesos innovadores y soluciones de bajo impacto ambiental. “Chile cuenta con una industria forestal altamente tecnificada y competitiva. Nuestro rol es aportar con conocimiento y tecnologías que estén a la altura de los estándares internacionales”, afirma. A lo largo de su historia, la UDT ha licenciado diversas tecnologías, ha colaborado en la implementación de plantas piloto y ha generado patentes que han sido reconocidas a nivel internacional.
Uno de los pilares estratégicos de la actual administración es consolidar el vínculo entre la academia, la industria y los centros de investigación internacionales. “La clave está en conocer lo que ocurre a nivel mundial, anticipar tendencias, proponer soluciones novedosas y mantener redes sólidas. Colaboramos con centros de excelencia como VTT de Finlandia o Fraunhofer de Alemania, que tienen estructuras similares y una fuerte articulación con sus industrias”, señala Carrasco.
NUEVAS LÍNEAS ESTRATÉGICAS PARA EL DESARROLLO TECNOLÓGICO
Entre las principales líneas de trabajo de esta nueva etapa, destaca el fortalecimiento de los servicios tecnológicos con foco industrial, profundizando alianzas con empresas estratégicas. “Queremos escalar tecnologías que ya han sido validadas a nivel laboratorio y que están listas para su implementación en procesos industriales reales. Hay una ventana de oportunidad para transferir innovación de manera efectiva y rápida”.
Otro de los focos emergentes es la incorporación de inteligencia artificial en el funcionamiento de las plantas piloto, lo que representa un desafío técnico de alto nivel. “El reto es integrar IA en procesos que no son continuos ni estables, como es el caso de los ensayos a escala piloto. No hay muchas experiencias a nivel global, pero creemos que este es un paso necesario para aumentar la eficiencia y generar aprendizaje automático que optimice la toma de decisiones”.
HACIA UNA COLABORACIÓN INTERSECTORIAL
CON ENFOQUE SOSTENIBLE
Una tercera línea estratégica apunta a la transferencia de conocimientos desde el sector forestal a otras indus-
trias como la minería, en el contexto de los compromisos de descarbonización y adaptación al cambio climático. “La bioeconomía —basada en el uso de materias primas renovables como la biomasa forestal— es esencial para avanzar hacia modelos industriales sostenibles. La minería chilena enfrenta una presión creciente para reducir su huella ambiental, y ahí vemos una gran oportunidad para aplicar soluciones tecnológicas probadas en otros sectores”.
Juan Carlos Carrasco enfatiza que el compromiso de la Unidad de Desarrollo Tecnológico (UDT) no se limita únicamente a lo tecnológico, sino que existe también una clara vocación por el desarrollo territorial, la formación de capital humano avanzado y la generación de impactos sociales positivos. “Hoy en día somos más de 70 profesionales de diversas disciplinas, enfocados en resolver desafíos reales. Uno de nuestros principales propósitos es contribuir al desarrollo sostenible del país, aportando desde la ciencia y la tecnología a una economía más limpia, eficiente y respetuosa con el medio ambiente”, finaliza el profesional.
Chile ha sido históricamente reconocido por su fuerte vínculo con los commodities. Desde el siglo XIX, con el salitre y luego el cobre, nuestra economía ha dependido de la exportación de materias primas. Hoy, las principales exportaciones provienen del sector minero. A ello se suma la industria forestal, que ha ganado protagonismo con la producción de celulosa y papel.
Fibras como la celulosa kraft de eucalipto y pino radiata nos posicionan entre los principales exportadores globales. A pesar de los desafíos, la industria forestal ha comenzado a dar pasos importantes hacia la incorporación de productos de mayor valor agregado. Este impulso representa una valiosa oportunidad para seguir avanzando en la diversificación de la matriz productiva, con miras a reducir la dependencia de productos de bajo valor y mitigar la exposición a los ciclos internacionales.
Frente a este escenario, Chile destaca en el ámbito académico. Según el QS Latin America 2024, 16 universidades chilenas están entre las 100 mejores de la región, incluyendo la Pontificia Universidad Católica, la Universidad de Chile y la Universidad de Concepción. Esto nos posiciona como líderes en formación
e investigación en Latinoamérica. Contamos con instituciones capaces de generar conocimiento útil para transformar sectores estratégicos, si logramos vincular sus capacidades con los desafíos productivos del país.
El potencial de colaboración con la
Candelaria Briceño
Ingeniera Innovación Senior CMPC
pueden liderar procesos de innovación en áreas como bioeconomía, automatización, biotecnología o industria 4.0. En Chile, aunque contamos con instituciones públicas como CORFO, ANID y el Ministerio de Ciencia que promueven la vinculación academia-industria, aún falta una estrategia articulada de largo plazo que transforme esta colaboración en un eje estructural del desarrollo nacional.
¿CÓMO CREAMOS ESPACIOS DE COLABORACIÓN PERMANENTE ENTRE INDUSTRIA, ACADEMIA Y ESTADO?
industria es enorme. Países como Canadá, Suecia y Finlandia ya han demostrado cómo universidades alineadas con sectores productivos
La pregunta es cómo avanzar. ¿Cómo creamos espacios de colaboración permanente entre industria, academia y Estado? ¿Cómo comprometemos a las universidades con la formación de talentos estratégicos y a las empresas con la adopción de innovación nacional? Chile tiene los recursos, el capital humano y la oportunidad histórica para dejar de ser solo un país que extrae y empezar a construir un país que transforma. Para esto,debemos trabajar juntos, crear instancias concretas de conexión e intercambio entre industria y academia, guiadas por entidades públicas que dirijan la bajada de los focos, impulsando la construcción de puentes para romper las barreras tradicionales y apostar por una agenda compartida que mire más allá de la próxima exportación y piense en los próximos 50 años. p c
Noemí Alvarado
Ingeniero Químico
Cursó sus estudios superiores en la Pontificia Universidad Católica de Chile, donde obtuvo el título de Licenciada en Química. Fueron seis años de formación intensa, tanto académica como valórica, experiencia que marcó profundamente su camino profesional. Recuerda con especial cariño a sus profesores, quienes le entregaron no solo conocimientos, sino también una visión ética y rigurosa del quehacer profesional.
Su carrera comenzó con una práctica en CMPC Papeles Puente Alto, cuna de la industria papelera en Chile, donde trabajó durante 14 años. Allí se desempeñó en distintas áreas y laboratorios, adquiriendo una visión integral de los procesos papeleros, desde el laboratorio hasta su aplicación industrial. “El 80% de mis conocimientos en papelería los adquirí allí”, comenta, destacando la influencia de colegas que la formaron como especialista.
Más adelante, asumió el rol de Gerente de Producción en una empresa de colorantes para las industrias textil y papelera. Esta etapa, en un entorno familiar, fue clave para consolidar conocimientos técnicos y sumar experiencia. Posteriormente, se integró al área comercial, lo que le permitió fortalecer la relación con clientes del rubro, comprendiendo en profundidad cómo aportar valor desde ambos frentes.
Hoy en día es Gerente Técnico en Khemnova, lugar donde transmite su experiencia y busca dejar un legado para las nuevas generaciones. Conoció la ATCP gracias a su trayectoria profesional y decidió hacerse socia porque “el conocimiento debe ser compartido” y ve en la Asociación un espacio clave para la colaboración y desarrollo de la industria.
Diego Loncomilla
Ingeniero Civil Químico
Algunos aspectos relevantes de su vida profesional fueron su paso por CMPC de 7 años, donde realiza su práctica y memoria de título junto a Fernando Valdebenito y Miguel Pereira, desarrollando un modelo de simulación Wingems de planta Santa Fe. Luego trabaja con José Soza y Daniel Aracena en el área de procesos de misma planta. Posteriormente, trabajé con Rodrigo Caro en área de excelencia operacional e inversiones de CMPC. “En 2021, por compatibilidad con proyectos personales, me cambié de trabajo a Nalco Water junto a Felipe Marnich y Alvaro Oñat, con quiénes sigo aprendiendo y desarrollando mi carrera, todos ellos excelentes tutores y personas de destacadas carreras en el rubro de celulosa”.
Conoció la ATCP desde que era alumno en la UdeC, participé de los cursos de industria de celulosa junto al profesor y director ATCP Miguel Pereira, “donde escuché de los seminarios y pude leer la revista, que despertaron gran interés en mí acerca de esta industria”.
En sus palabras, Diego decidió convertirse en socio debido a la constante oportunidad de aprendizaje que brinda la ATCP, junto a la posibilidad de participar de las Jornadas Técnicas que se realizan en la zona. Además, de la referencia de varios de mis colegas en la industria, con los que intentamos aportar un granito de arena a esta Asociación y el crecimiento de la industria en la región.
Ana Luiza Fávaro Piedade1 y Raquel Tommasi1*
1. Acqua Expert Engenharia Ambiental, Santos, Brasil; contato@acquaexpert.com.br
* Contacto del autor: ana.luiza@acquaexpert.com.br; Telefono contacto: +55-11-95552-2576 (A.L)
El estudio evaluó la reducción del bulking filamentoso en sistemas de lodo activado de cinco industrias de celulosa y papel en Brasil, enfocándose en ajustar la dosificación de nitrógeno y fósforo. Cuatro de las cinco plantas de tratamiento de efluentes (PTEs) tenían problemas crónicos de separación de sólidos debido al alto índice volumétrico de lodo (IVL) causado por el bulking filamentoso, siendo el Tipo 021 N la bacteria predominante, especialmente bajo condiciones de deficiencia de nitrógeno, alta septicidad y altos niveles de sulfuro. Se confirmó que todas las PTEs sufrían de esta deficiencia nutricional. El aumento en la dosificación de macronutrientes se recomendó, con el objetivo de mantener el nitrógeno inorgánico soluble residual entre 1,0 mg/L y 3,0 mg/L, más allá de la relación estándar DBO:N:P de 100:5:1. Las variaciones de carga llevaron a deficiencias en alta carga y excesos en baja carga. Cuatro PTEs controlaron el bulking manteniendo NH4 y P sobre 1,0 mg/L, pero una PTE no logró estos niveles, resultando en una mejora limitada de los flóculos y persistencia del bulking y problemas de separación.
PALABRAS CLAVE: Lodos activados, Bulking filamentoso, Deficiencia nutricional.
1. INTRODUCCIÓN
El bulking filamentoso es uno de los problemas más comunes en plantas que tratan efluentes mediante sistemas de lodos
activados, causado por el crecimiento excesivo de bacterias filamentosas [6]. Este fenómeno ocurre cuando hay un desequilibrio entre las poblaciones de bacterias formadoras de flóculos y bacterias filamentosas [11]. Las poblaciones microbianas influyen en la dinámica comunitaria con estrategias de reproducción y crecimiento que dependen de fuentes de carbono y disponibilidad de nutrientes [3]. Si estos compuestos se disponen en niveles mínimos, limitan el crecimiento de especies [7]. En entornos competitivos, la habilidad para asimilar sustancias a bajas concentraciones favorece a algunas especies sobre otras. Andreasen [2] afirma que las bacterias filamentosas superan a las formadoras de flóculos en sustratos de bajas concentraciones, mientras que las formadoras alcanzan tasas máximas en concentraciones elevadas. Además de la deficiencia nutricional, otros problemas operacionales como bajos niveles de oxígeno disuelto, sulfuro y septicidad pueden estimular a las bacterias filamentosas. Dependiendo de las condiciones del proceso, distintos tipos se desarrollan [5].
En Brasil, el sector de celulosa y papel abarca más de 200 industrias, siendo uno de los mayores fabricantes en volumen [1]. La mayoría trata sus efluentes mediante lodos activados con alta eficiencia en la remoción de DBO. Sin embargo, problemas en la separación de fases del lodo biológico y efluente en el decantador secundario resultan en arrastre de sólidos, causados principalmente por bulking filamentoso.
2. MATERIALES Y MÉTODOS
Cinco industrias de papel y celulosa monitorizaron su sistema de tratamiento durante 2021 a 2023 en Brasil. Los detalles sobre cada industria se pueden encontrar en la Tabla 1.
Este trabajo investigó las causas del bulking filamentoso en cinco industrias entre 2021 y 2023, estableciendo acciones correctivas para equilibrar las poblaciones de bacterias filamentosas y formadoras de flóculos.
Para análisis microbiológicos del lodo activado, las muestras fueron recolectadas del tanque de aireación y enviadas a Acqua Expert en Santos/SP, manteniéndolas refrigeradas de 4 a 10°C hasta 48 horas. Usamos microscopios ZEISS AXIOLAB 5 con aumentos de 100x, 400x y 1000x y técnicas de fase para caracterizar flóculos y cuantificar filamentosas mediante coloraciones de Gram y Neisser. Filamentosas se cuantificaron según [6] y [4].
2.3 Parámetros de control de proceso
Los parámetros operacionales incluyeron la carga orgánica (DBO, DQO), Índice Volumétrico del Lodo (IVL) y concentraciones de nitrógeno amoniacal y ortofosfato, tras filtrar el efluente en 0,45 µm; datos proporcionados por las industrias.
3. RESULTADOS Y
El análisis mostró un persistente bulking filamentoso en las cinco industrias estudiadas.
Industria 1: Clasificada densidad de filamentosas como “e” (Figura 1), con IVL promedio de 280 mL/g. Dominantes Nostocoida limicola y Tipo 0675, relacionadas con carencia de fósforo. La relación DBO:N:P fue 100:3.5:0.5, indicando carencia. Inicialmente, nitrógeno residual era 0.91 mg/L y fósforo 0.2 mg/L. Al aumentar fósforo a más de 1 mg/L, el IVL bajó a 134 mL/g (Figura 2), disminuyendo bulking y aumentando flóculos.
Como muestra la Figura 3 y según [3], los microorganismos filamentosos son K-estrategas y los formadores de flóculos son r-estrategas. Los filamentosos tienen ventaja competitiva a bajas concentraciones, típicas en configuraciones de tanques de mezcla completa [2]. Condiciones con bajo oxígeno o nutrientes insuficientes favorecen a los filamentosos, que utilizan estos compuestos eficientemente incluso en bajas concentraciones, por lo que deben
evitarse estas limitaciones para controlar su crecimiento [2].
de P monitorizados por la industria.
La industria 3 no presentó ningún problema con el arrastre de sólidos durante el período evaluado. Sin embargo, es un caso interesante, ya que, a pesar de trabajar con un valor de IVL bajo (promedio de 106 mL/g), como se observa en la Figura 7, los flóculos biológicos presentaban bulking filamentoso de la especie Tipo 021N. A pesar del exceso de bacterias filamentosas, los flóculos biológicos son muy compactos y firmes, lo que mantiene el IVL más bajo (Figura 5). Observando los resultados de IVL y NH4 residual en la Figura 4, se nota que, a diferencia de los casos anteriores, esta planta operó con un NH4 residual entre 1,0 mg/L y 3,0 mg/L la mayor parte del período evaluado, lo que explica esta excelente floculación de la biomasa. También se observa que el período en que el
Figura 3: Diferencia en la cinética de crecimiento de bacterias formadoras de flóculos y bacterias filamentosas.Fuente: [2].
4: Resultados de IVL (mL/g) y Residual de Nitrógeno Amoniacal monitorizados por la industria 3.
Figura 5: (a) Flóculos biológicos observados en el lodo activado de la Industria 3 durante el período en que el IVL estaba alrededor de 130 mL/g y (b) flóculos durante el período en que el IVL estaba alrededor de 80 mL/g y con mayor residual de NH4. In vivo. 100x. Contraste de fase.
IVL fue más bajo (cerca de 80 mL/g) coincidió con el período en que el NH4 residual se mantuvo más alto, lo que redujo, incluso, la cantidad de bacterias filamentosas (Figura 5b).
En la industria 4, cuando se inició el trabajo, las bacterias filamentosas de la especie Tipo 021N estaban causando un bulking de categoría “f” (Figura 6 y Figura 7a y b). Tras evaluar todas las posibilidades que podrían estar favoreciendo su crecimiento, se detectó que la causa era también la carencia de nitrógeno. Entonces, se incrementó la dosificación de urea para mantener el NH4 residual por encima de 1,0 mg/L en el efluente tratado. Observando la Figura 8a, se nota que en el período inicial del estudio en esta industria, el IVL era en promedio de 265 mL/g, lo que en varias ocasiones conducía a la fuga de sólidos en el efluente tratado. Aproximadamente 20 días después de aumentar la dosificación de urea y mantener el NH4 residual por encima de 1,0 mg/L, el ambiente se volvió incómodo para las filamentosas Tipo 021N, que comenzaron a reducirse, hasta el punto de que el IVL disminuyó a valores cercanos a 50 mL/g, gracias a las excelentes características de los flóculos biológicos, que se volvieron grandes, firmes, compactos y con una densidad "c" de bacterias filamentosas (Figura 9).
En la industria 5, los flóculos biológicos de la primera muestra eran grandes y difusos con bulking filamentoso (Figura 10a) de la especie Thiothrix sp ( Figura 10b). El IVL inicial fue de 400 mL/g y los niveles de nitrógeno amoniacal promediaban 0,7 mg/L. La dosificación de nitrógeno se incrementó según la
recomendación para mantener el residual entre 1,0 mg/L y 3,0 mg/L, pero la empresa no logró mantener consistentemente estos niveles. Como se ve en la Figura 13a, el residual promedio se mantuvo bajo 0,9 mg/L con grandes oscilaciones. En julio/22, el residual subió a entre 2,0 mg/L y 4,0 mg/L, reduciendo el IVL de 500 mL/g a 300 mL/g, pero volvió a subir cuando el residual bajó nuevamente. En octubre/22, se incrementó la dosificación de N, pero siguieron las oscilaciones entre 0,1 mg/L y 5,0 mg/L. Estudios indican que incluso breves periodos de deficiencia de N pueden inducir desequilibrios y dar ventaja a Tipo 021N [10]. Aunque hubo un aumento en la biomasa y el IVL se redujo, no se logró eliminar totalmente el bulking filamentoso (Figura 11). Constantemente mantener N por encima de 1,0 mg/L probablemente habría controlado el bulking y reducido más el IV L.
7:
Figura 8: Resultados de IVL (mL/g) y Residual de Nitrógeno Amoniacal monitorizados por la industria 4.
Figura 9: Cambio en las características de los flóculos biológicos de la Industria 4 durante el período en que se trabajó con mayor N residual. In vivo. 100x. Contraste de fase.
Figura 10: Bulking filamentoso observado en la Industria 5. In vivo. 100x. Contraste de fase. (b) Especie Thiothrix sp. In vivo. 1000x. Contraste de fase.
Figura 11: Cambio en el lodo activado de la Industria 5 30 días después del aumento en la adición de nutrientes. In vivo. 100x. Contraste de fase.
4. CONCLUSIONES
Este estudio analizó las causas de los elevados Índices Volumétricos de Lodo (IVL) en las plantas de tratamiento de efluentes (PTEs) de cinco industrias de celulosa y papel en Brasil. Todas presentaban problemas de arrastre de sólidos debido al bulking filamentoso de especies como Tipo 021N, Thiothrix sp. y Nostocoida limicola. Estas bacterias proliferan en condiciones de baja disponibilidad de nitrógeno y fósforo. Aunque el efluente tratado presentaba residuos de macronutrientes, estos niveles no eran suficientes. El análisis microscópico del lodo reveló la importancia de identificar organismos indicativos de carencia de nutrientes.
De las cinco industrias, cuatro lograron controlar el bulking y reducir el IVL manteniendo el nitrógeno y/o fósforo soluble por encima de 1,0 mg/L de manera continua, eliminando así el arrastre de sólidos en 20-30 días. La industria que no tuvo éxito fue la que no pudo mantener consistentemente los niveles de nitrógeno adecuados debido a dosificaciones intermitentes. Para lograr resultados constantes, se debe ajustar la dosificación de macronutrientes según las variaciones de la carga orgánica.
AGRADECIMIENTOS
Los autores agradecen a las cinco industrias por proporcionar muestras de lodo biológico y datos de control, y al equipo de Acqua Expert por su experiencia en la identificación de bacterias filamentosas. Su colaboración fue esencial para este trabajo.
5.
1. ABTCP - Associação Brasileira técnica de celulose e papel. (2023). O setor. Disponível em: https://www.abtcp.org. br/o-setor#:~:text=Contatos-,O%20setor,e%20640%20 mil%20empregos%20indiretos Acesso em 12 fev. 2023.
2. Andreasen, K., Agertved, J., Petersen, J., Skaarup, H. (1999). Improvement of sludge settleability in activated sludge plants treating effluent from pulp and paper industries. Water Science and Technology, 40 (11-12), 215-221.
3. Chudoba, J., Dohányos, M., Grau, P. (1982). Control of Activated Sludge Filamentous Bulking – IV. Effect of Sludge Regeneration. Water Science and Technology, 14(1-2), 73–93.
4. Eikelboom, D.H. and Geurkink, B. (2002). Filamentous microorganism observed in industrial activated sludge plants. Water Science and Technology, 46(1–2), 535–542.
5. Fourest, E., Craperi, D., Deschamps-Roupert, C., Pisicchio J.-L., Lenon, G. (2004). Occurrence and control of filamentous bulking in aerated wastewater treatment plants of the French paper industry. Water Science and Technology, 50(3), 29–37.
6. Jenkins, D., Richard, M. G., Daigger, G. T. (2003). Manual on the causes and control of activated sludge bulking, foaming, and other solids separation problems. 3rd edition.
7. Odum, E.P. (1988). Ecologia. Editora Guanabara Koogan.
8. Richard, M. G., Shimizu. G. P., Jenkins, D. (1985). The Growth Physiology of the Filamentous Organism Type 021N and Its Significance to Activated Sludge Bulking. Journal (Water Pollution Control Federation), 57(12), 1152-1162.
9. Reid, J.R. (1991), Phosphorus and Filaments. TAPPI Environ. Conf. Proc., 1, 99.
10. Richard, M.G. (1991), Filamentous and Polysaccharide Bulking Problems and Their Control in Paper Mill Activated Sludge, TAPPI Environ. Conf. Proc., 1, 95.
11. Von Sperling, M. (2002). Lodos ativados. Princípios do tratamento biológico de águas residuárias. Imprensa Universitária da UFMG. 2 ed. Vol.4E.
p c
Alejandra Hernández
Key Account Manager Ecolife
En los últimos años, nuestro país ha generado un cambio importante impulsado por el Ministerio de Medio Ambiente, esto queda reflejando con la creación del departamento de Olores, Ruido y Lumínica. No solo es el olor si no que existe ocupación por todas aquellas áreas que involucra un efecto directo a la población. Esto ha generado también que tanto el sector público como privado han tenido que adaptar su funcionamiento y producción a esta nueva realidad, que incluye tanto la educación ambiental como la participación activa de la ciudadanía.
En el área de olores, que es en la que nos desenvolvemos, quedo claramente reflejando en el reciente Congreso Internacional de Olores desarrollado en nuestro país, el pasado 9 y 10 de abril, donde la alta y exitosa participación de diferentes agentes del mercado, reflejaron la necesidad por participar, investigar y sobre todo indagar nuevas tecnologías que permitan estar en línea con el desarrollo de las normativas que se están instaurando en Chile.
El enfoque actual se centra en la
prevención y la eliminación de los olores en su origen, buscando soluciones que no solo neutralicen, sino que también transformen los gases responsables en sustancias no odoríferas. Esto implica un enfoque
EL ENFOQUE ACTUAL SE
más holístico que considera la causa raíz de la contaminación odorífera y busca soluciones integrales para su control.
La industria ha evolucionado más allá de simplemente neutralizar
olores, buscando tecnologías que eliminen los gases responsables de los olores desagradables en el origen, antes de que sean liberados, y que incluso los transformen en sustancias no odoríferas. Esto incluye tecnologías como la biofiltración y el uso de filtros de carbón activado, incorporación de químicos y nutrientes en los RILes, además de sistemas de alerta temprana en emisiones difusas.
Queda claro, entonces que los profesionales del rubro y las empresas que se dedican a atender este mercado deben, estar preparando y complementando su oferta a los nuevos desafíos y a la vez implementando las nuevas tecnologías disponibles, siendo nuestro país un agente importantísimo para el desarrollo a nivel internacional en el rubro de control de olores.
Es por esto que Ecolife se ha preparado para estar a la vanguardia del mercado y ha incorporado a su gama de productos, biofiltros, agentes para el control de olores acuosos, sistemas de telemetría, olfatometría de campo entre otros. p c
Romina Márquez
Ingeniera Civil Química
Formada en la Universidad del Bío-Bío, dio sus primeros pasos en la industria papelera durante su práctica profesional en CMPC. “Fue una experiencia clave, que me permitió descubrir el enorme potencial de este sector”, comenta. Más tarde, durante su habilitación profesional, su interés por el rubro se consolidó con el apoyo de una profesora que la guió en esta etapa.
Actualmente, se desempeña como Ingeniera de Aplicación en CHT, donde enfrenta nuevos desafíos tecnológicos a diario. “Valoro mucho esta oportunidad, porque me impulsa a desarrollarme continuamente y a seguir aprendiendo”, afirma.
Su acercamiento a la ATCP Chile ocurrió en la universidad, cuando su mentora le presentó el trabajo de la Asociación. “Desde ese momento supe que quería ser parte”, dice. Hoy, como socia, destaca el valor de pertenecer a una comunidad técnica activa y en constante actualización. “Ser parte de la ATCP me permite estar al día con las nuevas tecnologías e innovaciones que están transformando nuestra industria”, concluye.
Víctor Parra
Ingeniero Civil Químico
Con casi tres décadas de experiencia dedicadas al rubro de la celulosa y el papel, el actual Gerente de Ventas Papel de INGER ha construido una sólida trayectoria al servicio del desarrollo técnico y comercial de especialidades químicas para esta industria. Formado en la Universidad de Concepción, reconoce la influencia clave de sus años universitarios en su vocación. “Mi interés por el área se fortaleció gracias a profesores como Roberto Melo y José Paz, quienes marcaron profundamente mi formación”, señala.
Desde sus años de estudiante, la ATCP Chile fue parte de su entorno técnico-académico. “Era imposible no conocer la ATCP: sus seminarios, publicaciones y actividades estaban siempre presentes en nuestro quehacer universitario”, recuerda.
Hoy, como nuevo socio, valora profundamente el rol de la Asociación en el fortalecimiento del conocimiento técnico y la colaboración entre profesionales del sector. “Ser parte de esta red es una forma de seguir contribuyendo y aprendiendo, incluso después de tantos años en la industria”, afirma.
p c p c
Atoda marcha se encuentra trabajando el equipo organizador para la nueva versión de este evento, a realizarse entre el 03 al 07 de noviembre en la Universidad del BíoBío, sede Concepción.
ATCP Chile es oficialmente su Media Partner, por ello, conversamos con Joaquín Roble, uno de los 3 coordinadores de la actividad, para que nos entregue mayores detalles sobre este esperado encuentro, que se presenta como una oportunidad única para compartir conocimientos, conectar con futuros colegas y estar al tanto de los avances de la Industria de Procesos y específicamente en una de las disciplinas clave, como es la Industria de la Celulosa y Papel.
¿CÓMO NACE LA NECESIDAD DE CREAR ESTE CONGRESO?
Responde a la necesidad de generar un espacio que promueva el intercambio de conocimientos y experiencias entre estudiantes y profesionales de la ingeniería química. A través de ponencias, charlas y talleres, busca -
mos fomentar la colaboración entre instituciones, fortalecer redes de contacto y proyectar el rol de la ingeniería química tanto a nivel nacional como internacional. El congreso de estudiantes llevaba un tiempo sin realizarse, por lo mismo decidimos como comité organizador afrontar este desafío y mostrar también el potencial que nuestra casa de estudios (UBB) tiene en el campo de la ingeniería química.
¿CUÁLES SON SUS OBJETIVOS PRINCIPALES?
Como principal objetivo se tiene fortalecer los lazos entre estudiantes de distintas universidades del país, generando un espacio de encuentro para compartir experiencias, conocimientos y distintas miradas sobre nuestra formación profesional. A través de ponencias, charlas y talleres, se busca fomentar el intercambio académico, la creación de redes de contacto y la divulgación científica. Además, se abordan desafíos actuales de la ingeniería química, como el cambio climático, la innovación en procesos, la investigación y la revalorización de residuos, todo basado en los principios de la sostenibilidad y la economía circular, temas clave para el futuro.
¿CÓMO PROYECTAN, EN CUANTO A NÚMEROS, LA PARTICIPACIÓN DE ESTUDIANTES DE INGENIERÍA QUÍMICA?
Esperamos una alta convocatoria, considerando el largo período en que Chile no contó con un CoNEIQ. Además, hemos realizado encuestas de interés que evidencian el entusiasmo de estudiantes de distintas universidades por participar. Esta información ha sido recopilada desde el año pasado, con el objetivo de asegurar el éxito del congreso. Nuestra meta es completar los cupos disponibles, estimados en aproximadamente 200 personas, y que todo se desarrolle según lo planificado.
AL 7 DE NOVIEMBRE EN
El CoNEIQ se enfoca en tres ejes clave: sostenibilidad, economía circular y revalorización de residuos. Los ejes tratan del rol de la ingeniería química con los desafíos ambientales actuales. Como futuros ingenieros, buscamos aportar con soluciones innovadoras y sostenibles a través del desarrollo de procesos más eficientes y responsables.
Economía Circular: Chile enfrenta el reto de avanzar desde un modelo lineal hacia una economía circular, que promueva el uso eficiente de recursos y la valorización de subproductos. La Ley REP es un ejemplo de este impulso hacia una gestión más sostenible.
Revalorización de residuos: La ingeniería química permite transformar residuos mediante procesos fisicoquímicos, termoquímicos y biotecnológicos, generando productos de valor agregado y reduciendo el impacto ambiental.
Sostenibilidad: Buscamos equilibrar el desarrollo industrial con la protección del medio ambiente y el bienestar social. En este eje abordamos temáticas como la gestión de recursos, procesos sustentables y la normativa ambiental chilena.
MENCIONAR LOS PRINCIPALES APOYOS RECIBIDOS PARA PODER LLEVAR A CABO ESTE EVENTO
Actualmente contamos con el patrocinio de la ATCP como media partner y el apoyo de la Escuela de Ingeniería Civil Química así como la Facultad de Ingeniería de la Universidad del Bío-Bío. Estamos abiertos a colaborar con empresas del rubro y esperamos prontamente conectar con ellas. p c
José Soza 1, Rafael Ayala 2 y Nicole Reyes 3
1. CMPC, Los Ángeles, Chile, jsoza@celulosa.cmpc.cl
2. CMPC ; rayalap@celulosa.cmpc.cl
3. Siamec ; nreyes@siamec.cl
*jsoza@celulosa.cmpc.cl; +569-8158-0147
El manejo de olores en la industria de la celulosa es un desafío crucial, especialmente en instalaciones como la Planta Santa Fe de CMPC, situadas cerca de comunidades. Ubicada en Nacimiento y con las fuentes potenciales de emisiones odoríferas situadas a 780 mts, la planta enfrenta la tarea de gestionar los olores derivados de las operaciones en un tiempo de reacción de 4 a 8 minutos.
Los operadores de la planta controlan múltiples variables de procesos y ambientales en simultáneo, lo que tiene incidencia en la detección temprana de desviaciones. Para fortalecer la gestión ambiental preventiva, se implementó un modelo de soporte humano a la operación 24/7, que integra monitoreo en tiempo real de sensores y variables críticas del proceso. Este enfoque se complementa con la aplicación de técnicas de aprendizaje automático para anticipar y mitigar la emisión de olores antes de que impacten a la comunidad. La implementación de este modelo ha permitido mitigar más de 450 incidentes con connotaciones ambientales y ha reducido significativamente la percepción de olores en la comunidad, mejorando la eficiencia operativa e inci -
diendo en la optimización del uso de odorizantes en un 34% el 2024.
PALABRAS CLAVE: Gestión de olores, Monitoreo ambiental, Prevención de emisiones.
1. INTRODUCCIÓN:
La producción de celulosa enfrenta un desafío ambiental clave: la gestión de olores. Durante la fabricación de pulpa mediante el proceso Kraft, se generan compuestos odoríferos, como el metil mercaptano (CH3SCH3), el sulfuro de dimetilo (CH3SSCH3) y otros compuestos de azufre reducidos, conocidos como TRS (Total Reduced Sulfur), formados en reacciones de sustitución nucleofílica con grupos predominantes de lignina (Sixta et al., 2006). Este problema es especialmente relevante en Chile, donde, después del ruido, los olores constituyen el segundo mayor motivo de reclamos ambientales, con un promedio de 200 denuncias anuales entre 2019 y 2023, impactando significativamente a la Región del Biobío (SMA, 2012), lo que impulsó en 2024 nuevas regulaciones que exigen mayor control y monitoreo de emisiones.
La normativa nacional, específicamente el Decreto Supremo N° 37, establece límites para la emisión de compuestos TRS en plantas de celulosa Kraft (SMA, 2012). Sin embargo, no es solo la normativa lo que impulsa el desarrollo de un plan de gestión de olores, sino también el bienestar de la comunidad circundante y el compromiso de ser “buenos vecinos”. Frente a este escenario, y a pesar de las inversiones en infraestructura y optimización de procesos, la variabilidad operativa continúa siendo un desafío persistente.
Según la guía EEMUA 191 de buenas prácticas de los sistemas de alarmas, un operador debería gestionar un máximo de 6 alarmas por hora en condiciones estables y un máximo de 60 alarmas por hora en un escenario inestable (EEMUA, 2024), asumiendo una sobrecarga de la capacidad de control.
En el contexto anterior, CMPC implementó un modelo de soporte a la operación, que integra herramientas digitales y personal altamente capacitado, que priorizan la estabilidad ambiental sobre la maximización de la producción, asegurando que ninguna decisión comprometa el control de emisiones odorantes.
2. MATERIALES Y MÉTODOS
En un entorno industrial donde la estabilidad operativa y la gestión ambiental deben convivir, surge una pregunta clave: ¿Cómo genera valor el soporte humano en la mitigación de incidentes que pueden impactar en el
olor a la comunidad?.
Para responder, se analizaron tanto factores cuantitativos (datos de monitoreo en tiempo real, análisis estadísticos y alarmas operativas) como factores cualitativos (interacción con operadores, toma de decisiones y estrategias de respuesta), cuya metodología se detalla a continuación.
2.1. Foco en el proceso, entender qué sucede en la operación a través de datos
El primer paso fue comprender qué sucede en el proceso a través de datos. Se identifican 526 variables críticas de distintas áreas del proceso, como vacío de los sistemas de gases, temperaturas, pH, conductividades y variables con límites de cumplimiento normativo. Con esta información, se establecen límites operativos basados en análisis históricos.
2.2. Foco en las personas, entendiendo por qué actúan como lo hacen y asegurar que tomen acción
El segundo paso fue comprender por qué los operadores actúan como lo hacen y cómo asegurar que las alertas sean atendidas de manera efectiva. Para ello, se establecen estándares de comunicación que garantizan que la información llegue de forma inmediata, permitiendo acciones correctivas oportunas y minimizando la exposición a incidentes odorantes. Esto permite generar el vínculo de alianza estratégica para la operación ambientalmente impecable.
Figura 2: Evolución de las alertas reactivas a preventivas.
Figura 3: Serie temporal de concentración H2S de nariz electrónica clarificador primario vs pH área Blanqueo.
2.3. Generación de valor, aplicando tecnología y herramientas digitales que permitan capturar y potenciar el impacto del modelo
El tercer paso fue consolidar el valor generado a partir del conocimiento del proceso y la interacción con los operadores, integrando herramientas digitales que optimizan la toma de decisiones y fortalecen la gestión ambiental.
• Plataforma de Gestión y Análisis de Métricas Medioambientales (GAMMA) desarrollada por CMPC: Unifica la información de 526 variables críticas, permitiendo conocer el estado de riesgo de la Planta en materia ambiental y en tiempo real, analizando tendencias e identificando correlaciones entre las variables.
• Sistema de alarmas sonoras en la sala de control: Notificaciones en tiempo real sobre 39 variables clave, asegurando una respuesta inmediata de los operadores ante incidentes odorantes.
• Protocolos de respuesta operativa: Estándares y guías que estructuran la toma de decisiones, minimizando la incertidumbre y permitiendo una actuación eficiente ante desviaciones ambientales.
2.4. Mejora continua y expansión
El cuarto paso fue la evolución del modelo, asegurando su adaptación y escalabilidad para consolidar su impacto en el tiempo y extenderlo a otras operaciones de CMPC.
• Ajuste dinámico de Indicadores Claves de Rendimiento (KPI) ambientales: Se revisan y optimizan los límites operacionales, asegurando que los parámetros se mantengan alineados con la realidad de la operación. Evaluación del desempeño del modelo: Se registra y analiza la cantidad de alertas emitidas, midiendo la eficacia en la proporción de alertas preventivas y reactivas.
• Cultura preventiva en la operación: La adopción inicial presentó desafíos en un entorno acostumbrado a operaciones tradicionales, pero el enfoque proactivo ha permitido la integración del modelo sin afectar la continuidad ni la eficiencia productive.
Un caso destacado fue la rápida intervención en el incinerador 1, punto de quemado dedicado a gases diluidos no condensables (DNCG) y gases concentrados condensables (CNCG), donde el modelo de soporte detectó en el mapa de riesgo la elevación anormal de temperatura
Un caso destacado fue la rápida intervención en el incinerador 1, punto de quemado dedicado a gases diluidos no condensables (DNCG) y gases concentrados condensables (CNCG), donde el modelo de soporte detectó en el mapa de riesgo la elevación anormal de temperatura a 1027°C. El operador, alertado de inmediato, ajustó los controles operacionales, evitando que la temperatura alcanzara los 1100°C, lo cual habría apagado el equipo y causado la emisión de gases olorosos (venteos) de DNCG al ambiente y la presurización de CNCG en el circuito.
El sistema ha evitado 452 escenarios de riesgo durante el último año, del cual el 84,6% es atribuido a olor, contribuyendo significativamente a la reducción de desviaciones e impactos ambientales negativos.
El avance de la monitorización de reactiva a preventiva, junto con la integración de técnicas de machine learning, ha fortalecido la base para futuras mejoras en la gestión ambiental y los procesos operativos. Un ejemplo clave fue el análisis con modelos predictivos del compuesto H2S en los clarificadores primarios de planta de tratamiento de efluentes, donde se identificó que el pH del área de blanqueo influía significativamente en las concentraciones de H2S. La optimización del rango operacional de pH de 3 a 8 llevó a una notable disminución de H2S de 500 ppb a 100 ppb, mejorando la percepción de olores y demostrando la efectividad de aplicar ciencia de datos para una gestión operacional más eficiente y sostenible.
4. CONCLUSIONES
El modelo de soporte ambiental implementado en la Planta Santa Fe de CMPC, ha demostrado su eficacia en la operación de una gestión ambiental operativa anticipativa, abordando de manera efectiva tanto la preven -
ción como la respuesta ágil ante incidentes con impacto de olor. El establecimiento de 526 KPI con monitoreo 24/7 ha facilitado la prevención de percepción de olores mediante el análisis detallado del proceso y alertas tempranas sobre potenciales riesgos que ha permitido detectar en promedio 1,2 alertas críticas diarias, equivalente a más de 438 escenarios al año, e incidir en la reducción de los venteos, que es consecuencia del actuar ágil de los operadores al accionar cambios en el proceso que nacen de visualizar variaciones en estos KPI en el proceso y reducir emisiones. Adicionalmente el uso de herramientas digitales y aprendizaje automático junto al adecuado mapeo de los KPI ha permitido identificar las causas raíz, generar aprendizaje y por ende mejoras que permiten minimizar su nueva ocurrencia.
Como complemento la reducción de escenarios de riesgos ha contribuido a una optimización relevante en el uso de odorizantes, lo que ha permitido disminuir costos asociados y reforzar la relación con la comunidad. La adaptabilidad y eficacia del modelo se reflejan en su implementación exitosa tanto en Santa Fe como en Planta Laja, consolidándose como un estándar en la gestión ambiental de CMPC.
El impulso para mejorar nuestras operaciones diarias nos llevó a desarrollar e implementar el sistema actual. Agradecemos a las gerencias por su apoyo y visión al adoptar soluciones innovadoras en materia medioambiental y de sostenibilidad. También queremos expresar nuestra gratitud a los operadores por su dedicación y esfuerzo constante en la gestión operativa, ya que su colaboración ha sido vital para potenciar una cultura preventiva y lograr operaciones impecables.
1. Ministerio de Medio Ambiente. (2012, Octubre 29). Biblioteca del Congreso Nacional de Chile. Obtenido de https://www.bcn.cl/leychile/navegar?i=1049596&f=2013-03-22.
2. H.Sixta, A. Potthast, W. Krotschek. (2006). Chemical Pulping Processes. In H. Sixta, Handbook of Pulp (pp. 3-14). Weinheim: Wiley-VCH GmbH.
3. EEMUA. (2024). A guide to design management and procurement (4.ª ed.). EEMUA Publications.
p c
Los días 21 - 23 y 28 - 30 de abril se realizó este curso, dirigido a supervisores, técnicos y profesionales del área forestal o afines, ideal para quienes buscan entender cómo la estructura de la madera influye en la producción de celulosa y papel.
Contó con la participación de experimentados relatores en sus campos de investigación, como los profesores de la Universidad de Concepción Juan Elissetche, Regis Texeira y Miguel Pereira, quienes compartieron sus conocimientos en esta capacitación única, que mezcla ciencia, tecnología y aplicación industrial.
Teresita Marzialetti
Jefa Carrera Ingeniería Civil Química UdeC
Con una sólida trayectoria en docencia, investigación aplicada y gestión académica, la actual Jefa de Carrera de Ingeniería Civil Química de la Universidad de Concepción (UdeC) lidera procesos clave de modernización curricular, reacreditación internacional y fortalecimiento del vínculo con industrias estratégicas como la celulosa y el papel.
Doctora en Ciencias con mención en Química por la Universidad de Concepción y formada como Ingeniera Civil Química en la Universidad Nacional del Sur (Argentina), la académica ha consolidado una carrera orientada a la excelencia. Su formación incluye también un Magíster en Ingeniería Química y una especialización en Gestión de la Calidad, antecedentes que hoy sustentan su liderazgo dentro del Departamento de Ingeniería Química (DIQ) de la UdeC.
“Ingresé al Departamento motivada por el prestigio de esta carrera, su alto nivel de exigencia y por formar parte de una institución con más de un siglo de trayectoria”, explica. Al momento de integrarse como docente, la carrera ya contaba con acreditación nacional por el máximo número de años, y desde 2018 posee acreditación internacional ABET, también en el rango más alto posible. “Es una hermosa carrera, en una universidad con reconocimiento internacional y emplazada en un campus privilegiado”, agrega.
Desde su rol como Jefa de Carrera, su gestión ha estado enfocada en la mejora continua y en la adaptación del plan formativo a las exigencias actuales del entorno productivo. Uno de los principales desafíos que enfrenta hoy es el proceso de reacreditación ABET, cuya evaluación final está prevista para el segundo semestre del próximo año.
“Este proceso implica una fiscalización internacional rigurosa, que requiere coordinación entre académicos, estudiantes, egresados y empleadores”, señala. Junto con ello, el DIQ trabaja en una modernización del plan de estudios, que reducirá su duración de 11 a 10 semes-
tres, sin comprometer estándares de calidad. “Estamos enfocados en asegurar una formación técnica sólida y una ética profesional robusta, manteniendo el sello de excelencia que caracteriza a nuestros ingenieros químicos”, subraya.
VÍNCULO HISTÓRICO CON LA INDUSTRIA DE LA CELULOSA Y EL PAPEL
La relación entre la carrera y el sector forestal y celulósico no es reciente. “Nuestra carrera nace hace más de 100 años por una necesidad concreta de la industria forestal y minera de la región”, recuerda la académica. Ese vínculo se ha sostenido en el tiempo, y hoy constituye una alianza estratégica que beneficia tanto a la formación de los estudiantes como al desarrollo tecnológico de las empresas.
El sector celulósico, en particular, ha sido un espacio de inserción laboral clave para los egresados del DIQ, quienes también realizan en estas empresas sus prácticas profesionales y proyectos de titulación. La presencia de exalumnos en empresas como CMPC o ARAUCO ha facilitado, además, la colaboración en proyectos de I+D aplicada.
“La industria de la celulosa y el papel representa un espacio privilegiado para la aplicación de conocimientos en procesos químicos complejos, control ambiental y eficiencia energética”, afirma. “Nuestros egresados aportan valor en ámbitos como optimización de procesos, gestión de calidad, economía circular y desarrollo de productos sustentables”.
Uno de los ejemplos más recientes de colaboración efectiva con la industria es el proyecto FONDEF ID23I10101, adjudicado en 2023 y actualmente en ejecución junto a CMPC. “Estamos trabajando en el desarrollo de un producto que reduce el consumo de agua en el proceso de producción de especies”, explica. Esta innovación tiene impacto directo en el proceso de obtención de pulpa y papel, dado el alto estándar que exige tanto el mercado nacional como internacional.
“Se trata de una solución con impacto ambiental positivo, que responde a las demandas globales por procesos más sostenibles y al mismo tiempo fortalece la competitividad de nuestras industrias locales”, añade. Este tipo de proyectos, señala, también abre oportunidades para la participación de estudiantes y jóvenes investigadores, fomentando la transferencia tecnológica y el aprendizaje en contextos reales de producción.
Además del proyecto FONDEF, el DIQ mantiene una presencia activa en líneas de financiamiento como FONDECYT y CORFO, desarrollando soluciones técnicas en conjunto con actores del rubro celulósico, así como con empresas del área de tratamiento de aguas, bioprocesos y valorización de residuos industriales.
FORMACIÓN CON IMPACTO INDUSTRIAL
Con una mirada de largo plazo, la académica destaca la importancia de una formación profesional que combine rigor científico, competencias técnicas y capacidad de innovación. En este contexto, el DIQ ha fortalecido la participación de la industria en su quehacer académico, mediante comités consultivos, encuestas de empleadores y mesas técnicas.
“La formación de ingenieros químicos hoy no puede estar desvinculada de los desafíos industriales del país. Debemos formar profesionales que no solo se inserten, sino que lideren procesos de transformación tecnológica en sectores estratégicos como el forestal y el celulósico”, concluye.
El Departamento de Ingeniería Química de la Universidad de Concepción sigue consolidando su posición
como un referente nacional en la formación de capital humano avanzado, con un fuerte compromiso hacia la excelencia académica, la innovación y el desarrollo tecnológico. Su estrecha colaboración con sectores productivos estratégicos, como la industria de la celulosa y el papel, ha permitido fortalecer el vínculo universidad-industria, impulsando soluciones sustentables y proyectos de alto impacto. Esta sinergia ha convertido al Departamento no solo en un espacio formativo de primer nivel, sino también en un socio clave para una industria que enfrenta crecientes desafíos en productividad, sostenibilidad y adaptación tecnológica. Con una mirada de futuro, el DIQ reafirma su misión de formar profesionales capaces de liderar los procesos de transformación que demanda el país, aportando desde la ingeniería química al desarrollo sostenible y competitivo de Chile.
p c
E ste año, la Asociación Técnica de Celulosa y Papel recibe a nuevos integrantes a su Directorio 2024 - 2026. En esta sección, conoceremos más en detalle su valiosa experiencia profesional y sus expectativas sobre este nuevo desafío que asumen.
Miguel Salinas
Ingeniero Senior Aguas y Efluentes ARAUCO
Con una sólida base en investigación y docencia universitaria en el área medioambiental, Miguel Salinas ha desarrollado una destacada trayectoria en la industria. Desde 2005 trabaja en Celulosa ARAUCO en el área de Aguas y Efluentes, donde ha liderado procesos vinculados a tratamiento de aguas, residuos, olores, evaluación de proyectos y gestión ambiental. “He podido integrar conocimientos previos y adquirir otros nuevos, consolidando una visión integral en torno a los desafíos ambientales del sector”, comenta.
Su vínculo con ATCP comenzó con la Mesa Técnica de Aguas y Efluentes. “Fue un espacio enriquecedor donde
distintas miradas —académica, industrial y de proveedores— generaron contenidos que aún hoy son relevantes”, recuerda. Desde hace tres años, además, lidera un exitoso curso de capacitación en tratamientos de efluentes.
Hoy, como nuevo miembro del Directorio, busca fortalecer la propuesta técnica y formativa de la Asociación. “Quiero aportar desde el Comité de Seminarios con nuevas iniciativas, y reactivar la Mesa Técnica con un enfoque actualizado e integral”, señala. Su meta es clara: “Engrandecer a la ATCP, darle más relevancia como referente técnico y apoyar a las nuevas generaciones de profesionales del rubro”, puntualiza. p c
Héctor Godoy
Ingeniero Químico CHT
Ingeniero Químico de la Universidad de Concepción, con estudios en Alemania y una trayectoria en empresas como ARAUCO Valmet y EQUANS, Héctor Godoy lidera hoy la gerencia comercial de CHT para la región Andina. Su carrera ha estado siempre ligada a la industria de celulosa y papel. “He encontrado no solo un espacio de desarrollo profesional, sino también una comunidad comprometida y en constante evolución”, destaca.
Su incorporación al Directorio de ATCP responde a un compromiso profundo con la colaboración sectorial. “Siempre he valorado los espacios que permiten compartir experiencias y avanzar como industria. Ser parte
de la Asociación me ha conectado con colegas de distintas generaciones”, comenta.
Desde esta nueva posición, Godoy buscará fortalecer el vínculo con el mundo académico y fomentar la participación de jóvenes profesionales. “El recambio generacional y la diversidad de miradas son fundamentales”, afirma.
Entre sus prioridades, menciona impulsar la sostenibilidad, la innovación tecnológica y nuevas redes de colaboración. “Queremos que la ATCP siga siendo un espacio donde proyectar juntos un mejor futuro para nuestra industria”, concluye.
p c
Con una mirada innovadora y una fuerte convicción por el desarrollo sostenible, Catalina Manquilepi, egresada y titulada como Ingeniera Ambiental de la Universidad de Los Lagos, desarrolló un proyecto de alto impacto para la industria papelera. Este trabajo de título fue ejecutado en la fase de desarrollo durante el desarrollo de una pasantía, en el marco de un programa de intercambio nacional, en la carrera de Ingeniería en Recursos Naturales de la Universidad del Bío-Bío (sede Chillán) durante su último año de formación académica.
Su trabajo de tesis, titulado “Elaboración de propuesta para la gestión de residuos en ANDRITZ Fabrics and Rolls Chile”, se enfocó en la valorización de la goma vulcanizada generada como residuo por la empresa.
El objetivo principal de su investigación fue diseñar un plan de gestión de residuos sólidos, integrando los principios de la economía circular y los lineamientos de la norma ISO 14001 sobre sistemas de gestión ambiental. A diferencia de enfoques tradicionales, que se centran principalmente en la reducción o eliminación de residuos a través de su disposición en rellenos sanitarios, la propuesta de Catalina apuesta por su reincorporación
al ciclo productivo mediante reutilización y reciclaje.
La motivación surgió durante su práctica profesional en la empresa, realizada entre enero y marzo del año 2024. Inicialmente, su trabajo se enfocaba en la gestión del material particulado, pero tras observar el proceso productivo y la generación de residuos asociados al recubrimiento de rodillos industriales, detectó una oportunidad de mejora. Así nació la idea de revalorizar la goma vulcanizada, un residuo con potencial no explotado dentro de la empresa.
La goma vulcanizada proviene de dos fuentes principales: la producción propia de rodillos y el mantenimiento de rodillos que llegan desde otras empresas del rubro papelero. Este material, altamente resistente, se utiliza como recubrimiento externo de rodillos que forman parte esencial de los procesos de fabricación de papel. Sin embargo, tras cumplir su vida útil, el material era considerado un desecho sin valor, siendo su destino habitual la disposición final en rellenos sanitarios.
Frente a esta realidad, Catalina formuló una propuesta técnica que no solo evalúa la situación actual de los residuos generados por la empresa, sino que también identifica oportunidades concretas de valorización. Sus
Foto 1: Prototipo desarrollado como resultado del proceso de valorización de residuos elastoméricos. El material fue transformado en una superficie funcional con propiedades físicas adecuadas para su uso en aplicaciones industriales o urbanas.
objetivos específicos incluyeron: proponer alternativas de reutilización y reciclaje bajo el enfoque de economía circular, estimar los costos y beneficios asociados al plan, y generar un modelo que pueda ser replicable y escalable en la industria.
Uno de los hitos más importantes del proyecto fue el desarrollo de un prototipo funcional: un piso fabricado a partir de goma vulcanizada reciclada. Para llevarlo a cabo, Catalina trabajó en conjunto con el Centro de Valorización de Polímeros (CIPA), institución con experiencia en investigación aplicada a la reutilización de polímeros industriales. El proceso incluyó la recolección de muestras del residuo, análisis físico-químicos del material, pruebas de factibilidad y la creación de un prototipo que demuestra la viabilidad técnica de la propuesta.
“Este material puede volver a la cadena productiva en forma de nuevos productos. Dejar de verlo como desecho y empezar a reconocerlo como un recurso es clave para avanzar hacia una industria más sostenible”, señala Catalina. El piso elaborado no solo tiene potencial para ser utilizado en instalaciones industriales, sino que también abre posibilidades en mercados como la construcción o la fabricación de superficies deportivas. El trabajo contó con el respaldo de la empresa estudiada, especialmente del director de la división, Luis Navarrete, quien aprobó el proyecto y facilitó el acceso a información clave.
A través de reuniones técnicas con el CIPA, y con el apoyo de su director ejecutivo, Claudio Toro, quien en la primera visita lleva a Catalina a presentar la propuesta
a Hello Castellón, Encargado de Gestión Tecnológica y Asistencia Técnica en Polímeros (GT-ATP), empresa anexa al mismo CIPA. Concluida la presentación de la propuesta, se desarrolló la caracterización y pruebas mecánicas para la formulación de un producto viable, con la colaboración del ingeniero a cargo, Jesús Serrano, ingeniero de desarrollo y coordinador de planta piloto, gestión tecnológica y asistencia técnica en polímeros (GT-ATP).
Además del impacto ambiental positivo al reducir la cantidad de residuos destinados a relleno sanitario —una de las opciones menos sostenibles según la jerarquía de residuos—, el plan propuesto contempla beneficios económicos, tanto por ahorro en costos de disposición como por la posibilidad de generar nuevos productos y líneas de negocio.
Según el análisis económico incluido en el trabajo, la implementación del plan podría contribuir significativamente a mejorar los indicadores de sostenibilidad corporativa de la empresa, a la vez que fortalecería su imagen frente a clientes, comunidades y reguladores.
“Esta propuesta demuestra que es posible implementar acciones concretas de economía circular en la industria papelera, transformando desafíos ambientales en oportunidades de innovación”, concluye la investigadora, quien recalca que la viabilidad del plan dependerá en gran medida del compromiso de la empresa para seguir desarrollando el proyecto, destinando recursos y promoviendo una cultura organizacional orientada a la sostenibilidad.
p c
Mauricio Macaya es el fundador de varias empresas pioneras en la economía circular en Chile, destacando por su visión de transformar residuos en recursos valiosos y útiles para la industria y la sociedad. Con más de 18 años de experiencia en el ámbito textil, Macaya es el creador de SVES Soluciones Vestuario Integral Ltda., una fábrica textil de ropa técnica que mantiene contratos con diversas empresas de distintos rubros.
Más tarde, en 2020, surge Natural Plas, una empresa recicladora especializada en la transformación de plásticos, calzado, equipos de protección personal (EPP) y otros residuos voluminosos no peligrosos, que anteriormente eran considerados desechos difíciles de procesar. Posteriormente, en 2023, dio vida a Cirkla, empresa dedicada a la economía circular textil, integrando sus conocimientos de fabricación y reciclaje para ofrecer soluciones sostenibles a la industria.
¿CÓMO NACE LA IDEA DE CREAR ESTA EMPRESA?
La industria necesitaba soluciones innovadoras y eficientes para reciclar ropa y fibras textiles de forma sostenible. En 2023, decidimos dar un paso más allá y fundamos Cirkla, con el fin de ofrecer una solución integral de reciclaje, transformando residuos en productos reutilizables para diversas aplicaciones industriales. La respuesta positiva de nuestros clientes nos motivó a expandir nuestros servicios, comenzando con la gestión de calzado, EPP y otros residuos voluminosos, los cuales también transformamos en nuevos materiales. Cabe destacar que participé activamente en la redacción de las normas chilenas de reciclaje textil, lo que nos ha permitido estar a la vanguardia de las regulaciones.
¿QUIÉNES CONFORMAN EL EQUIPO?
Somos un grupo multidisciplinario de profesionales apasionados por la sostenibilidad y la innovación. Contamos con expertos en reciclaje, ingeniería, diseño de productos y logística, todos unidos por el objetivo común de transformar residuos en recursos valiosos. Además, hemos integrado a personas con experiencia en la industria textil, lo que nos permite combinar conocimientos técnicos y prácticos tanto de la fabrica -
ción como del reciclaje de textiles.
¿CUÁL ES EL SELLO O IDENTIDAD DE CIRKLA?
Nuestro sello se basa en la innovación constante, la adaptabilidad a las necesidades del mercado y el compromiso con el impacto social y ambiental. No solo transformamos residuos, sino que generamos nuevos productos con valor añadido, como placas aglomeradas, productos para la construcción, mantas y artículos corporativos. Cirkla es un proyecto que busca generar un ciclo positivo: lo que antes era un desecho, ahora es un recurso útil para otras industrias.
¿EN QUÉ ETAPA SE ENCUENTRAN ACTUALMENTE?
Estamos en una etapa de consolidación y expansión. Hemos establecido una sólida base de clientes y estamos ampliando nuestras operaciones para incluir más tipos de residuos y aumentar nuestra capacidad de procesamiento. A nivel de mercado, hemos ganado reconocimiento como un actor clave en la economía circular textil y estamos trabajando en nuevas líneas de productos.
¿CON QUÉ ACTORES SE HAN VINCULADO PARA POTENCIAR ESTE PROYECTO?
Hemos logrado vincularnos con diversas empresas y organizaciones que comparten nuestra visión de la sostenibilidad y la economía circular. Nos hemos asociado con instituciones que nos proveen residuos para el reciclaje y que, a su vez, se benefician de nuestros productos reciclados. Colaboramos, además, con instituciones académicas y centros de investigación , trabajando igualmente con gobiernos locales y entidades reguladoras que promueven políticas de reciclaje y sostenibilidad.
¿CUÁLES SON SUS PROYECCIONES A FUTURO?
Queremos continuar expandiendo nuestra capacidad de reciclaje y aumentar el número de tipos de residuos que podemos procesar. Estamos en constante búsqueda de nuevas tecnologías que nos permitan ser más eficientes y sostenibles. También planeamos ampliar nuestra presencia en el mercado, no solo a nivel local, sino también internacional.
JÓVENES CONSTRUYENDO FUTURO p c
SIEMENS ENERGY PROPORCIONARÁ ENERGÍA
A NUEVA PLANTA ARAUCO EN BRASIL
La empresa de tecnología en energías fue seleccionada por Arauco para suministrar turbogeneradores de vapor y el sistema de distribución eléctrica de su primera planta de celulosa en Brasil, ubicada en Mato Grosso do Sul. El proyecto, con una capacidad de 3,5 millones de toneladas anuales, contempla tres turbinas de vapor que permitirán generar más de 400 MW, de los cuales 200 MW serán para consumo interno. El contrato, valorado en más de 500 millones de reales, incluye la entrega de equipos en 2027. El excedente energético podría abastecer una ciudad de 800 mil habitantes. “Este proyecto refuerza nuestro rol como socio clave en soluciones energéticas sostenibles”, afirmó André Clark, de Siemens Energy.
En Temuco se lanzó un proyecto Bien Público que busca empoderar al sector agroforestal y productivo de la Araucanía mediante el uso de hidrógeno verde como motor de desarrollo sostenible. La iniciativa es cofinanciada por Corfo, ejecutada por Codesser y coejecutada por la Universidad de Talca. El objetivo es promover el crecimiento regional mediante tecnologías limpias, fortalecimiento del capital humano y estrategias de financiamiento. Eduardo Figueroa, director de Corfo Araucanía, destacó que el proyecto se alinea con el trabajo desarrollado en la Mesa de Hidrógeno Verde, avanzando en una hoja de ruta para la transición energética del territorio, con foco en el fomento productivo y una articulación público-privada que permita superar brechas y generar soluciones aplicables en el corto y mediano plazo.
Fuente: El Mostrador
El Ministerio del Medio Ambiente anunció que en junio se presentará la versión final del Decreto Supremo para la gestión de Residuos de Aparatos Eléctricos y Electrónicos (RAEE), como parte de la implementación de la Ley REP. En una ceremonia organizada por la Cámara de Comercio de Santiago (CCS), se destacó el trabajo de TRAEE, iniciativa que desde hace nueve años prepara al sector privado para estas nuevas obligaciones. En Chile se generan más de 230 mil toneladas de RAEE al año, pero solo el 5% se gestiona correctamente. TRAEE, impulsado por más de 10 empresas, busca articular un sistema colectivo de gestión que promueva el reciclaje, la recolección y la infraestructura necesaria, reforzando la colaboración públicoprivada para avanzar en sostenibilidad.
Fuente: País circular
"Precios de importación de celulosa kraft blanqueada de madera blanda del norte a China en descenso tras alza a inicios de este año. Período Sep 2022 – Sep 2024".
Entre septiembre de 2022 y septiembre de 2024, los precios de importación de celulosa kraft blanqueada de madera blanda del norte (NBSK) en China experimentaron una evolución volátil. En septiembre de 2022 alcanzaron un máximo cercano a 8.660 CNY por tonelada, impulsados por una fuerte demanda internacional y restricciones en la oferta global. Sin embargo, a partir de 2023 se inició una tendencia a la baja. En enero de ese año, los precios promediaron 820 USD/t y continuaron descendiendo hasta ubicarse cerca de 750 USD/t en agosto de 2024.
Este retroceso responde a diversos factores. Por un lado, China aumentó significativamente su capacidad de producción de celulosa integrada, incrementando la oferta local y reduciendo la necesidad de importaciones. A esto se sumó la debilidad de sectores consumidores clave, como la construcción, lo que disminuyó la presión sobre la demanda. Además, durante el verano de 2024 se observaron altos niveles de inven -
"Precios de importación de celulosa kraft blanqueada de madera dura a China muestran señales de una caída significativa. Período Sep 2022 – Sep 2024".
Durante el período comprendido entre septiembre de 2022 y septiembre de 2024, los precios de importación a China de celulosa kraft blanqueada de madera dura (BHK o BHKP) han comenzado a mostrar señales claras de una caída significativa.
Esto implica que, aunque puede haber habido cierta estabilidad o incluso aumentos puntuales en el pasado reciente, la tendencia general es bajista, y los indicadores del mercado (como menor demanda, mayor oferta, inventarios altos o baja actividad industrial) apuntan a que los precios están cayendo de manera marcada.
Fuente: Fastmarkets
tarios en los productores, lo que derivó en ajustes a la baja de los precios y generó preocupación por eventuales cierres temporales de plantas.
En el corto plazo, se proyecta que los precios de la NBSK se mantendrán bajos, salvo que ocurra una recuperación clara en la demanda o se registren disrupciones relevantes en la oferta global, que podrían revertir la actual dinámica del mercado.