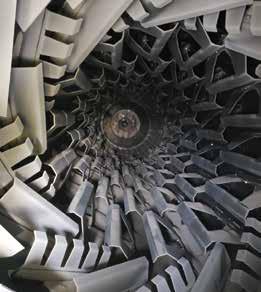
12 minute read
Optimize Your Production Veil
BY ASPHALTPRO STAFF
To kick off this month’s production-related product gallery, let’s take a look at the dryer drum. While producers will peruse the following pages for aggregate and asphalt production services and products, they can get a drum tip right here from BROCK, headquartered in Chattanooga. That tip focuses on flighting to optimize the veil of material in the drum.
Working with consulting engineer Malcolm Swanson, BROCK offers the FlexFlight™, which Swanson designed and for which he has applied for a patent through his company, e5 Engineers LLC, Chickamauga, Georgia. The FlexFlight is designed to address the fundamental challenge of executing a proper shower of material within the rotating drum.
By controlling the shower—or veil—of material in the drum as you change mix designs and/or production rates, you can also control temperatures leaving the drum. Swanson explained: “When you need a good complete veil most, as with open graded mixes and high RAP mixes, the veil is thin or nonexistent on the uplift side of the drum. So, hot gas bypasses material by taking the path of least resistance through the gap in the veil.” To get a more even veil of material for hot gas to spread evenly across, you want flights to “spill” material properly, evenly, and in a reliable fashion even when there isn’t much material in the flight.
“Conventional flights shower differently depending on fullness,” Swanson said. “When very full, they tend to allow material to cascade out early, making the uplift side of the veil too heavy. When they contain little material, as is the case with high RAP mixes, they tend to shower little or nothing on the uplift side and dump what they do have as they start back down. FlexFlight is designed to restrict flooding when full and yet allow showering even when nearly empty.”
Producers and manufacturers alike have long known the benefits of good showering in the dryer. Some of these benefits are higher production capacity, better fuel efficiency, more uniform and thorough drying of aggregates, better control of baghouse temperature, the ability to make higher RAP mixes that could not be made without excellent showering, and lower emissions. Swanson explained that manufacturers have, for many years, made flights that incorporate gaps to address the fill percentage or to prevent flooding of the flight with material, but the gaps have not always been good at allowing material to build and spill efficiently. Instead, the gaps have often allowed aggregate to dribble out.
The FlexFlight design doesn’t incorporate a gap but has a completely surrounded opening with several inches width at its bottom to prevent dribbling. “The opening is centered lengthwise, so you get a good veil at all parts of the circuit,” Swanson said. You can see the design in the photo on this page.
To configure the flights in the drum, they are placed in the drying zone according to the needs of the producer. See the photo on this page for an example of how Ranger Construction has theirs configured. “Going forward, we probably will use a number of flights per row that is a multiple of the drum diameter in feet,” Swanson said. “For example: if a 9-foot drum needs 54 new flights, it could get two rows of nine and two rows of 18 flights. That makes it a bit more rational for direct replacement in existing drums, since this is a pattern of flighting often used by dryer manufacturers.”
For more information, contact e5 Engineers at malcolm@ e5engineers.com.
Ranger Construction uses the FlexFlights in the drying zone of their 9-foot Double Barrel drum. Also called the showering zone, this is where the heavy lifting of drying and heating is done. There were four rows with 14 flights per row. Swanson explained the number of flights per row will vary according to the producer’s needs. Photo courtesy of Malcolm Swanson, e5 Engineers
The FlexFlight, designed and currently in patent-pending status by Swanson’s e5 Engineers, is available through BROCK (www.brock.llc).

AMMANN
Ammann Group offers the Ammann RAH50 drying drum retrofit to improve fuel efficiency and recycling capabilities over old drying drums.
Ammann drying drum retrofits are designed to be compatible with equipment from Ammann or other manufacturers. Ammann dryers heat and dry raw materials of different compositions, material properties and moisture contents. They have exceptional wear resistance, are easy to maintain and highly efficient, according to the manufacturer. The Ammann RAH50 is a popular retrofit because it allows customers to work with recycled asphalt.
Christian Westphal, head of machine technology MTA Mischwerke SAW Schleswiger Asphaltsplitt-Werke GmbH & Co. KG, retrofitted a plant with an Ammann RAH50 drum. He explained how his new middle dryer ring works compared to a conventional new mineral drum.
“At first, I was rather skeptical because of the promised high RAP addition rates (up to 45%),” Westphal shared. “The promises have been kept regarding flexibility and RAP addition. The maintenance effort is, of course, slightly higher than with a pure new mineral drum, but it is lower than previously expected. Surprisingly, RAP caking is not a problem at all.”
Westphal spoke of the drum’s different applications. “In addition to the standard cold feed, the RAH50 drum gives us the flexibility to switch to hot recycling. It is already worthwhile for us to use the RAH50 middle ring addition from batch sizes of 50 tonnes. Switching to hot recycling is problem-free, taking into account the overrun from the dryer drum to the hot mineral silo. For permissible construction measures, RAP percentages of up to 45% are possible for base layers via the middle ring addition. This enables us, in consultation with the client, to recycle large quantities, which of course offers enormous advantages in terms of costs.”
Westphal also spoke of temperatures. “The addition of RAP to the RAH50 drum enables gentler heating compared to cold addition. When mixing the raw material with the RAP, we can run drum outlet temperatures of 160 to 170 degrees C. This is gentle on all plant components and also saves fuel. The frequency converter installed in the drive motors also allows us to vary the dwell time of the new minerals and the RAP, which means that all types of aggregate are dried very effectively.”
The Ammann dryer drums also offer wall thicknesses up to 15 mm and a frequency converter for energy-efficient operation. The drums are available with Amdurit wear protection and high-temperature steel.
For more information, visit www.ammann.com
ASTEC
Quick setup of durable equipment makes the Astec M-Pack™ relocatable facility an excellent value, according to manufacturer Astec Industries, Chattanooga. The plant has the capacity and size of a permanent facility with reduced setup costs. It is engineered as a set of modules that are transported by truck. Each Astec M-Pack plant ships in ready to set up loads when it leaves the manufacturing facility. Level and pave your site, then lift the pre-piped, pre-wired modules off the trailer and bolt them up. The M-Pack foundations are heavy-duty and designed to provide plenty of load-bearing surface to support the facility components. If you ever have to move to another site, most loads fit on lowboy type trailers, and the built-in foundations go with them.
High production, large storage capacity, full-size control rooms, high-quality components, and excellent maintenance access make the modular Astec M-Pack asphalt mixing plant highly functional, according to the manufacturer. This asphalt mixing plant is outfitted with the latest technology and proven Astec performance. There are a wide range of options on these plants: • Astec offers four exclusive mixing systems: Double Barrel, Double
Barrel X, Double Barrel XHR or UniDrum • Astec offers two full-size silo options: Long-Term or Short-Term • Astec offers two baghouse options: Pulse Jet or Reverse Pulse
With a team of experienced engineers and in-house technicians, Astec has the knowledge and the expertise to help you make the appropriate selections to meet your requirements.
For more information, visit https://www.astecindustries.com/ products/details/m-pack-asphalt-plant.
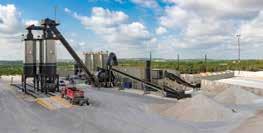
The Astec M-Pack asphalt mixing plant is engineered as a set of modules that ship in ready-to-set-up loads when it leaves the manufacturing facility.
BROCK
BROCK, Chattanooga, has signed an agreement to have booth 1976 at the World of Asphalt/AGG1 Show to be held in Nashville, March 29-31, 2022. This will be the first trade show for BROCK as a company. Ben Brock, president and CEO, said, “Our average years of successful experience in hot-mix asphalt equipment per employee is now among the highest in the United States, if not the highest, so it is only natural that our first trade show is this show. We are excited to see all attendees at the show. In the meantime, we welcome our current and potential customers to visit our facility in Chattanooga over the winter—or, since Chattanooga is just two hours from the show site, visit us either before or after the show dates.”
For more information, contact Travis Sneed at (423) 476-9900.
CLARENCE RICHARD
Steve Klein of Clarence Richard Company shares how to make aggregate stockpiles drain faster. Adding a tile drainage system under the pile area will help. Klein shows the math on why moisture is important to track—and drain. He wrote: “With the change from 6% to 5% the fuel 2.11-1.88 or a 0.23 gallon per ton difference. That’s 23.27 gallons in a hundred tons of production. Example: A plant is making 200 tph of hot mix with a fuel cost of $6.34 per ton at $3.00 gal. Reduce the stockpile from 6% to 5%. Now the cost per ton is $5.64 a ton. This is a $139.62 savings per hour from just the moisture reduction.”

The bolt-on batcher from CWMF features a heavy-duty material splitter and outward opening gates. Watch animated video demonstrating the unitized asphalt tank heater from PHCo at booth #3119 at World of Asphalt.
PlantDemand allows the user to create a custom dashboard with data you find most valuable.
CWMF
CWMF, Waite Park, Minnesota, has introduced its patented innovative batcher design that allows you to service your gates without removing the batcher. The bolt-on batcher is standard at 4 tons with optional extensions for increased capacity and large access doors on two sides. All components are external and gates are removable.
With a heavy-duty material splitter and outward opening gates, the batcher is designed to minimize segregation by dropping material to the center of the silo, preventing cone/can wear.
For more information, visit www.cwmfcorp.com.
MAJOR
MAJOR, a Haver & Boecker company, headquartered in Candiac, Quebec, introduced in October its FLEX-MAT ID Enabled. The RFID technology tracks and stores screen media data such as panel dimensions and customer-defined details to offer users information at their fingertips for simple reorders. Operations scan the FLEXMAT panel with the MAJOR app to access product information, simplifying re-ordering and inventory management. MAJOR can also program the chip during production with some customer-defined information to improve convenience. Unlike some systems, users just need their smartphone to view the data and don’t need to use a separate RFID reader.
For more information, visit the MAJOR website.
PHCO
Visitors at World of Asphalt in Nashville will have an insider’s view when they visit Process Heating Company (PHCo), headquartered in Seattle, at Nashville Music City Center, booth #3119. Unique animated videos show how PHCo’s products work, effectively illustrating what sets the company’s Lo-Density® drywell-style electric heat apart from fossil-fuel burners. From PHCo’s unitized asphalt and industrial tank heaters, hot oil circulation heaters, and all-in-one heaters, to its unique distributor truck tank heaters, visitors will discover how PHCo’s simple, clean heat source can positively affect their operations.
Process Heating Company has almost 75 years of experience in manufacturing Lo-Density low-watt-density electric heating systems. Common products that benefit from electric heat include asphalt, light and heavy fuel oils, diesel, bio-diesel, glycerin, lube oils, hydraulic fluids, resins/epoxies, animal fats, molasses, and other materials that are sensitive to high temperatures.
For more information, call (866) 682-1582 or visit www. processheating.com.

PLANTDEMAND
PlantDemand, Bay Area, California, gives your team a live, cloudbased, shared calendar to organize sales scheduling and improve visibility of what is coming up at your plant. This allows you to plan material needs with your suppliers, organize your crew shifts, identify potential issues with production and strategize with customers.
PlantDemand reports are available to gather information quickly to create material need and cost forecasts, sales and revenue forecasts, or send out daily dispatches for all of your plants at once. Because PlantDemand is available in the Apple App Store and the Google Play Store, you can check and update your plant schedules while on-the-go.

With the new addition of an API, one can integrate documentation to create custom dashboards with other important company data or software. While there are many options when it comes to integration, a simple approach is to give people the ability to query their data and let them configure it in a way that works best for their goal.
User experience design and user interviews have helped guide improvements from the beginning and continue to be a reason plant people find the upgrades so useful. PlantDemand launched their new redesign in 2021. Based on the user feedback, some of the implemented powerful new features are these. • A highly optimized order calendar view with search and filtering functionality • The ability to move and copy orders between plants • Settings page and user management updates • Customize required fields when entering an order • Invite multiple users at once • Enter detailed plant settings • Simplified notes.
Also, a pilot demo for paving teams to schedule paving projects is now available on the web version of PlantDemand.
For more information, visit www.plantdemand.com.
WEM
Identify opportunities to fine tune your asphalt plant production, mix quality and overall operational efficiency with WEM Analytics, a web-based software platform that can be accessed and utilized remotely via a smartphone, a tablet, or a computer, from WEM Automation.
WEM Analytics employs a drag n’ drop interface that lets you create additional customized dashboards to monitor functional areas of your plant, across various time spans (year, quarter, month, week, day, shift, and hour). Use it to compare multitiered data, with the ability to dive deeper into additional details on items such as mix production, AC usage, aggregate consumption, waste, plant alarms, and overall plant output.
The data that populates WEM Analytics’ dashboards is accessed from your WEM Automation Control System and comes with the ability to be exported in various file formats.
For more information, call (262) 782-2340 or visit WEM@ WEMAutomation.com.
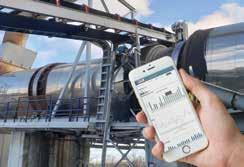
WEM Analytics data can be accessed remotely from your smartphone, tablet or computer.