
10 minute read
Another Way to Optimize RAP Efficiency on Site
ABOVE & RIGHT: Slabs of asphalt at your site can wait for a contract crusher to arrive and process them or can be processed right away if you have your own horizontal impactor crushing plant and screen ready to do the job. The crushed and screened material on the facing page is 0.75-inch minus. Photos courtesy of Rubble Master
Consider adding contract recycle preparation to your operation to increase RAP use, increase profits
ABY SANDY LENDER Asphalt producers and contractors don’t need a primer on how dumping rates or tipping fees are rising or how piles of reclaimed asphalt pavement (RAP) are building in some counties versus others. With the cost of recycled material often priced at half the cost of virgin material, professionals are interested in finding the best way to get their hands on this product. With the growing interest in increasing RAP use to further the industry’s good standing in the march toward net-zero, professionals are also interested in finding the best way to use this material.
Stockpiling RAP requires planning ahead and proper management, as discussed in our February 2016 edition and others, but building the on-spec stockpile starts with crushing and screening if you’re doing it right.
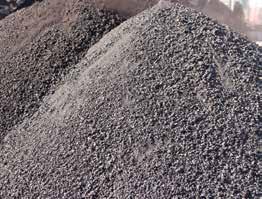
If you intend to fractionate your RAP to perfect it for mix designs, you have options. You could rent a crusher and scalping screen on a weekly or monthly basis to separate the existing “mountains” at your site into prepared stockpiles of on-spec material. You could have a company come in with portable equipment and crush your material into piles for you on a per-job basis or predetermined schedule. Depending on the amount of material you’re moving through your operation, you could invest in the equipment to do your own crushing of recycle material at your leisure. This third option opens the door to another revenue stream, which we’ll touch on below.
ROI TIME
When is the right time to hire a contract crusher versus investing in your own equipment? The team at Eagle Crusher shared that there’s no cut-and-dry answer to that one. Each company will need to do the math to determine when equipment purchases will offer a quick enough return-on-investment to pull the trigger. Without flinging more clichés at you, let’s look at some basics.
René Wagner of Rubble Master Americas Corp., St. Ennis, Texas, reminded readers that your time is worth money. He suggested asking yourself how easily you can get a contract crusher to process your materials in a timely manner. Look at how often you’ve been placed on a waiting list behind other customers waiting for crushed product. “Can your crushing contractor process all your desired materials and specs?” Wagner asked. “What does it mean for your business to have a contract crusher in your yard processing your materials? In many cases, this imposes a major interruption of your day-to-day operation.”
If you elect to rent a crusher from a dealer to process material yourself, you must have enough work/enough material to keep the machine working for the whole week of the rental. A crusher sitting idle in the yard is a crusher that’s costing you money.
If you’re renting a crusher multiple times a year or hiring a contract crusher to set up on your site frequently, it’s time to run the numbers on starting the operation on your own. Chris Worley is the product sales specialist for mobile crushing/screening at Astec Industries, Chattanooga, and he also shared some wisdom with readers. “I would say, if a customer is paying a contractor or renting the equipment to crush and screen their RAP 40% of the time or more in a given year,
Rejuvenate Reclaimed Asphalt with ReLIXER® Rejuvenator
An Elixir of Bio-Based Oils
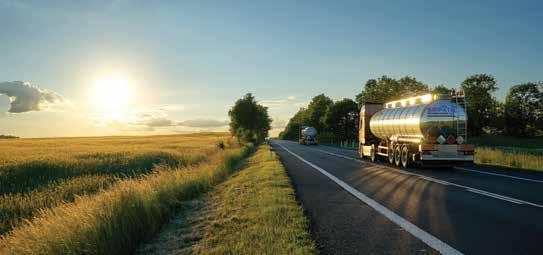
Tested.
Proven.
Trusted by users woldwide.
ReLIXER® • PGXpand® • NuMIXER®• ReNUBIT® • SriCote®
1-800-562-6276 1-201-721-7562
Learn More At Sripath.com/pro
then they should look at doing it themselves. If the contractor owns the equipment, they can better control when and where the equipment needs to be if they have multiple locations, versus having a contractor come in and crush.
“Also, owning the equipment—versus having a contractor come in and process the RAP—will give the contractor better control of the products being made if specs change for the RAP or if they need to increase the percentage of RAP in their mixes. Lastly, if the contractor chooses to rent the equipment versus owning it, then their cost per ton will be much higher. Owning the equipment will give them a better advantage when they are bidding new work due to the lower cost per ton to process the material.”
“I WOULD SAY, IF A CUSTOMER IS PAYING A CONTRACTOR OR RENTING THE EQUIPMENT TO CRUSH AND SCREEN THEIR RAP 40% OF THE TIME OR MORE IN A GIVEN YEAR, THEN THEY SHOULD LOOK AT DOING IT THEMSELVES.”—CHRIS WORLEY
START SMARTLY
While there are multiple stages of crushing and multiple pieces of equipment you could add to the recycling crushing process, you can start out with just the crusher and the machine that feeds it, according to the experts at Rubble Master.
“Impact crushers are the tool of choice for processing asphalt,” Wagner reminded us. “Many contractors start out with a mobile closed-circuit impact crushing plant to turn their peeled or milled asphalt into a base or subbase product. The smaller the infeed or the finished products get, the more screening capacity you need. A mobile scalping or incline screen in combination with your mobile impactor provides the screening capacity you need to achieve high outputs and low wear with small materials.”
You could start with the impactor (and excavator or loader) and add support equipment a year or even two years later. 1. start with the impact crusher 2. add the scalping screen in front of the impactor 3. add a stacker later, maybe when you make the decision to start contract crushing
“The customer would want to look at getting a horizontal impactor crushing plant, a screen plant and conveyors, all of which could be track, portable or stationary, depending on how many sites they have and how often they would need to move the equipment,” Worley said. “If the customer is fractionating their RAP, we would recommend using the multi-frequency screen.”
You don’t need a 10-person crew for this new operation, but you do want the personnel to be mechanically inclined and well trained. These workers need to be listening to the machine(s) and be able to identify if something is starting to go wrong.
CONTRACT-CRUSH RECYCLE
When you make the decision to crush other producers’ material for them, portability is paramount. Next up is preparation. You’ll want your customers to be fully aware of your requirements for material going through your crusher. The material they have on their site could be full of rebar, crossbeams or other surprises if you’re willing to crush more than RAP. If you’re willing to have your operator pick through “blended” demolition material prior to crushing, then you can set your prices accordingly, but that’s a concern to work out ahead of time. The last thing you want is to send your operator and ground man to a site where the material is full of detritus when you thought it was ready for crushing. Demo material full of detritus is not ready to go through your crusher.
You want the foreman to set up the site in the most efficient manner to feed the crusher from the excavator in a manner that keeps dust down, keeps the crusher flowing properly and keeps extra fines—or surprises—from damaging your equipment. Wagner suggested, “Have only your own factory-trained operator run your crusher. An inexperienced operator can’t achieve your quota and can cause substantial damage to your equipment.
“Walk away from jobs that your machine is not made for or get the equipment that is right for a certain job,” Wagner continued. “Sometimes a crushing job might look too good to let go, but a mobile impact crusher has its limits.” He explained that using the machine for the wrong application causes friction that can result in premature

The RM 90GO! compact crusher is a closed-circuit impact crusher. This model has been in production since 2000 and is popular among paving, site-work and crushing contractors for high performance and mobility. Its top capacity is rated at 200 TPH. Photo courtesy of Rubble Master
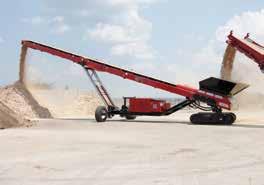
When the time comes, adding stackers will open more opportunity for the contract crusher. Photo courtesy of Rotochopper
wear and damage. “Consult your local crushing and screening specialist to get a second opinion and get the right equipment.”
“If the contractor is going to other sites to crush and screen material, they need to make sure they have a fully trained crew that knows how to operate and service the equipment properly in these applications,” Worley said. “This is very important to keep the cost per ton down. Also, before they move the equipment to different locations, they need to take a look at these sites beforehand to ensure the equipment will be set up properly. This includes taking a look at the pile—or piles—that need to be processed so they can have the right settings on the crusher and screen and to have it properly laid out on the site. This will minimize any ‘surprises’ that could drive your cost per ton up.”
Those surprises are something Wagner alluded to when discussing challenges for which contract crushers can plan. “The challenge is that you process material piles that you have no control over nor know very well,” Wagner said. “If you don’t process your own materials, you need to be prepared for everything. And performing proper due diligence before accepting a job is a must. Often, the big surprise is inside a material pile. Everything might look good on the outside but becomes a nightmare as soon as you start digging into the pile. To protect yourself from damages, you need to be very clear with your customer as to what you can and cannot process and what it means if you can’t process something.”
If you’ve determined that your site could support its own crushing and screening operation for recycle material with room to add contract recycle processing on the side, consider the ideas experts have suggested here to make your plans go more smoothly.
LOWER WEAR COSTS
Rubble Master’s René Wagner shared: “When you process large amounts of asphalt millings with a lot of fines, a mobile screen helps to reduce wear costs and increase total production. If you can’t remove fines prior to the crushing process, your wear parts get chewed up quickly, which affects your bottom line. In this case, the additional investment of a scalping screen pays for itself quickly.
“Recently, a client of ours installed a large 22-foot by 5-foot mobile incline screen to process asphalt millings with very little oversize. He screens -inch minus, and he uses a compact RM70GO! mobile impact crusher to process the little oversize that was left from the screening process.
“The same logic applies if you need large amounts of small, finished products such as ½-inch minus material. The onboard screen of a closed-circuit impact crusher might not have enough capacity and becomes your bottleneck. If you can’t screen what comes out of the impact crusher, you lose production and face higher wear costs. In this case, a screening plant after your impact crusher helps again to increase production and lower wear costs.”
Make It Last.

Protect your investment with Kenco wear parts.
Proudly manufactured in the USA since 1957, Kenco offers innovative products for the aggregate, asphalt and road building industries. Our products are designed to increase wearlife and reduce downtime on your plants and equipment.
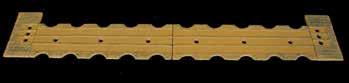