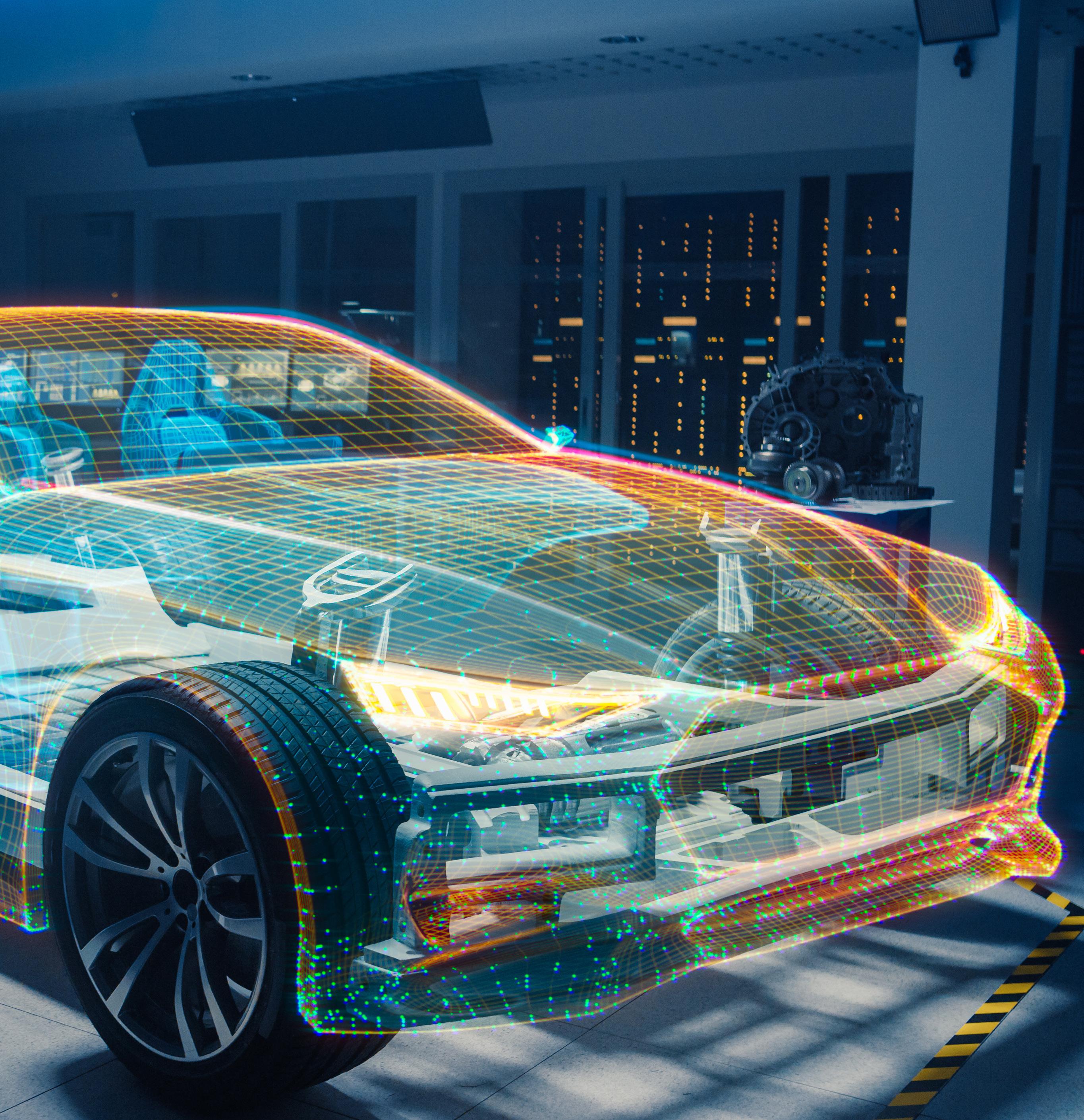
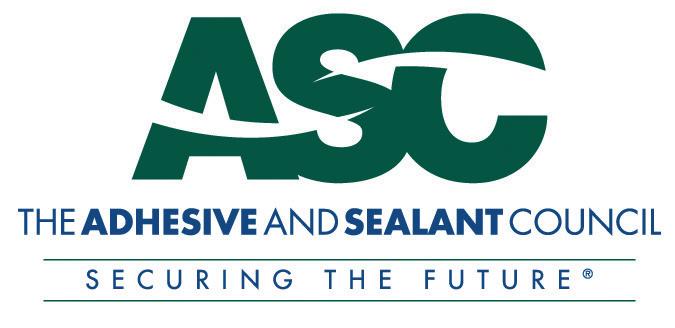
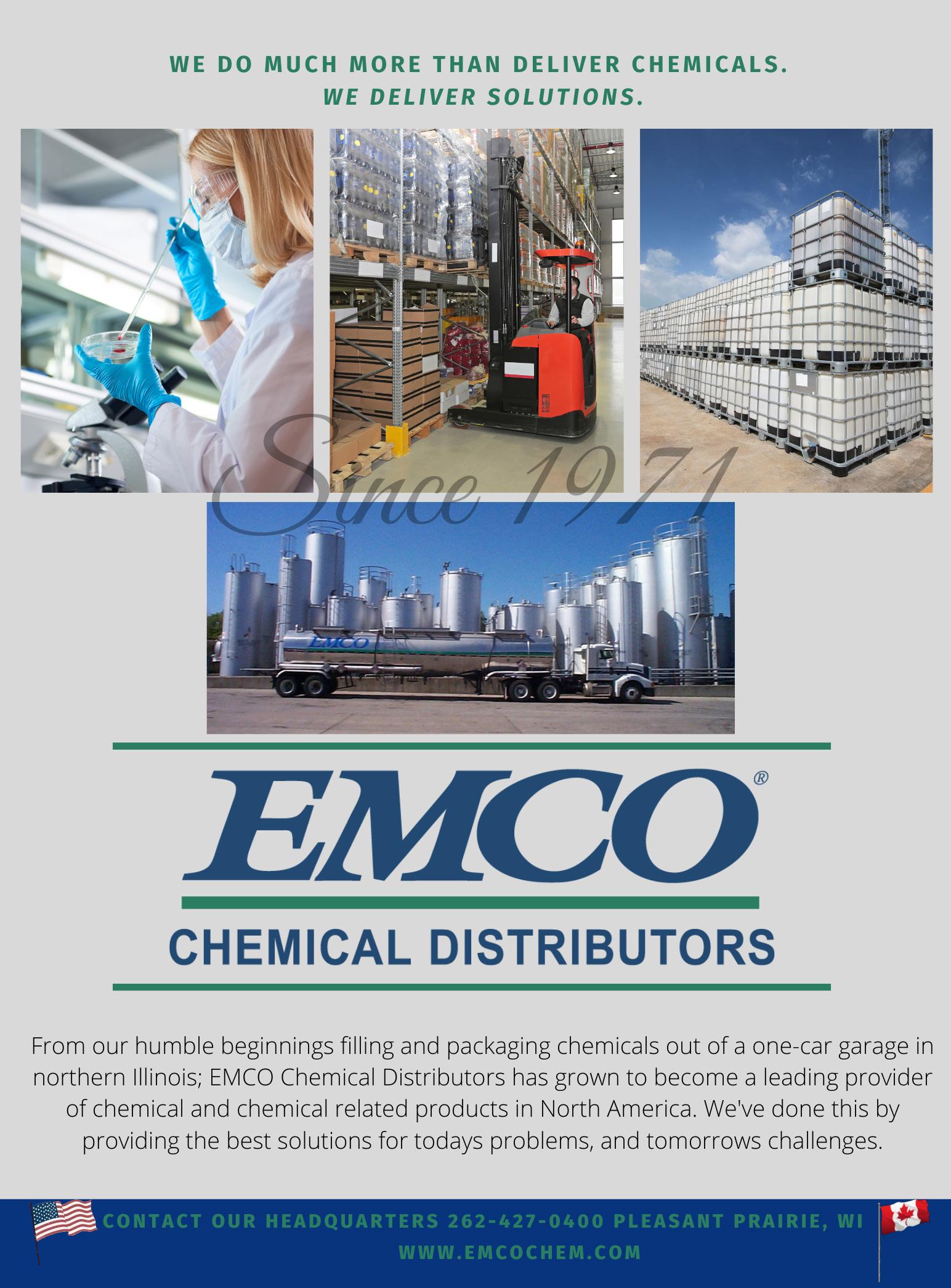
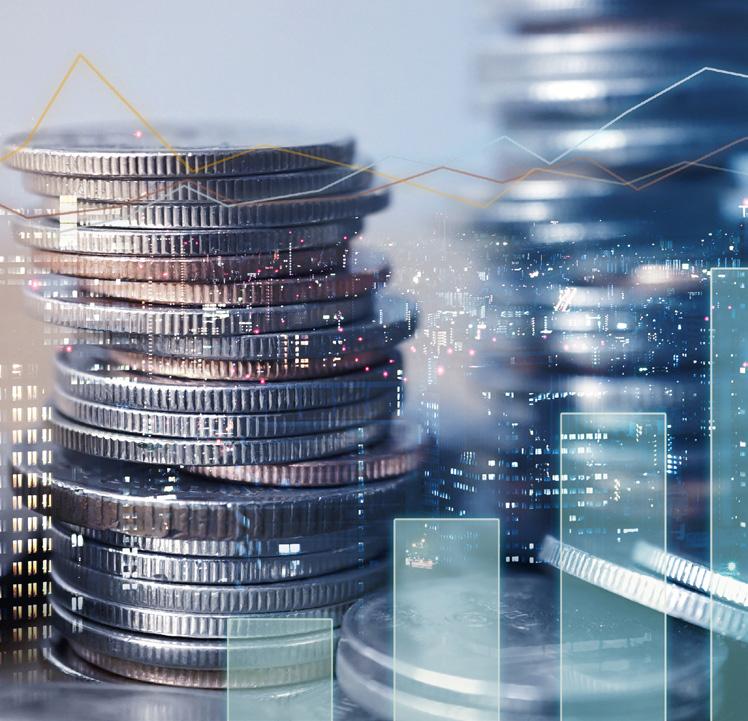
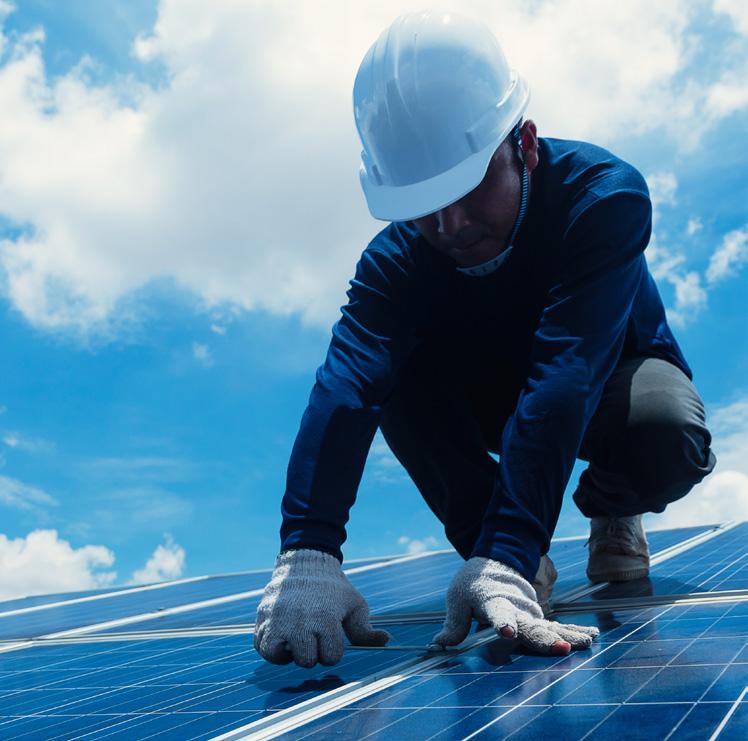

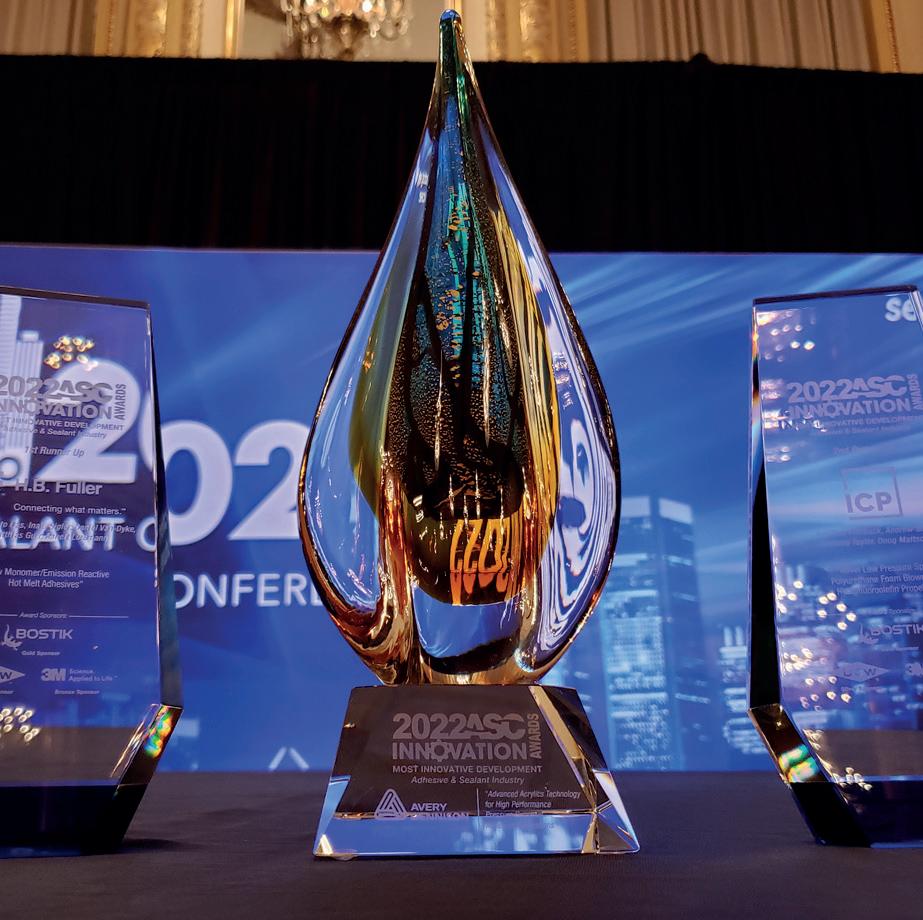
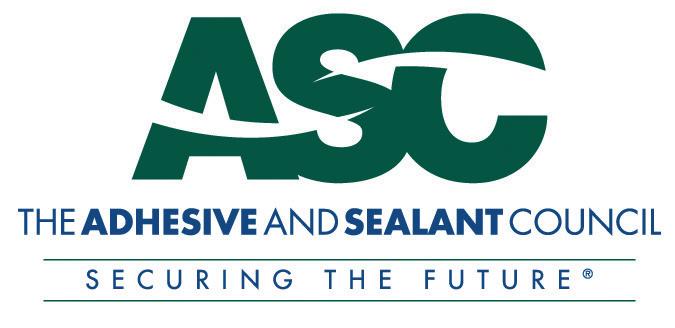
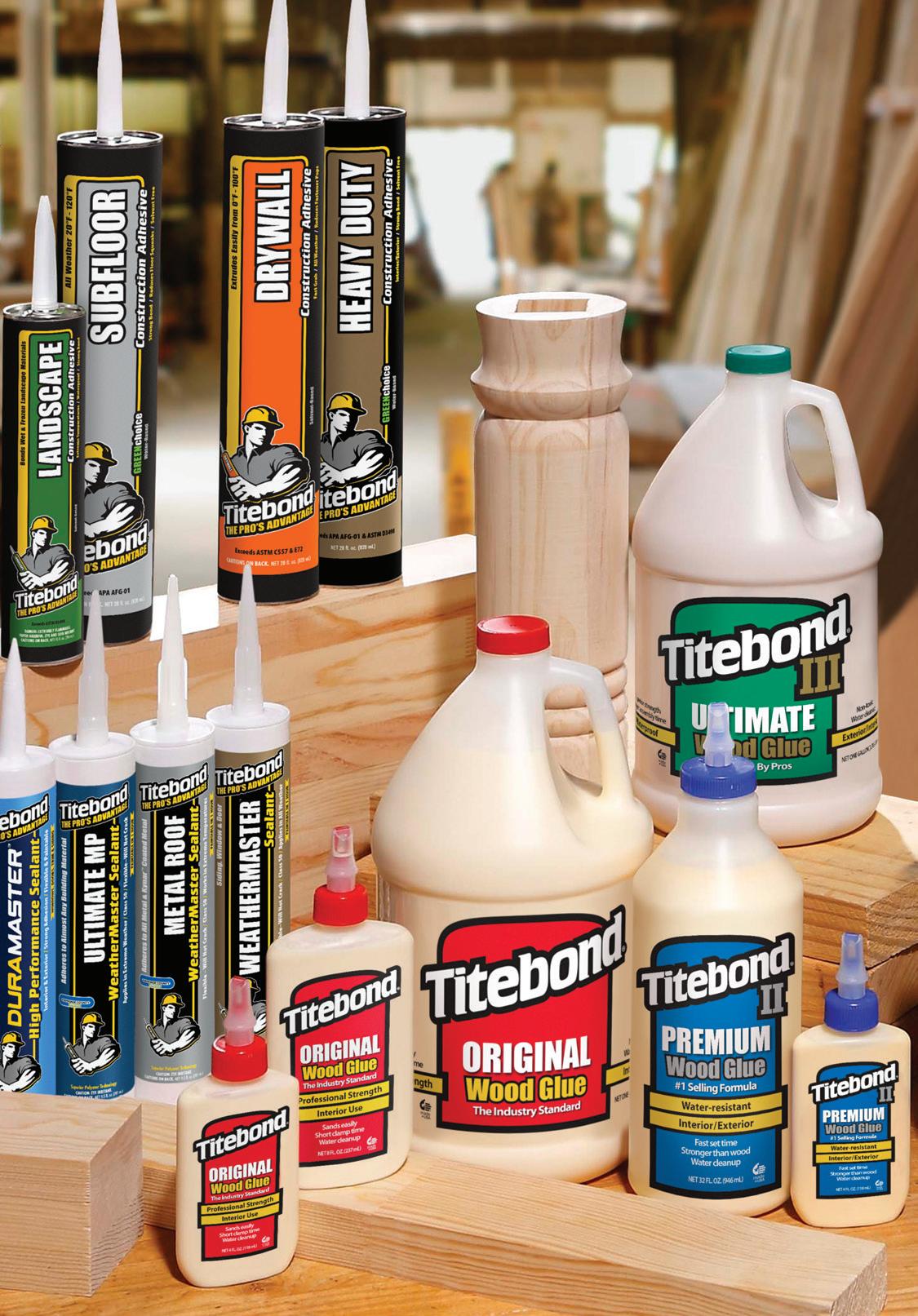
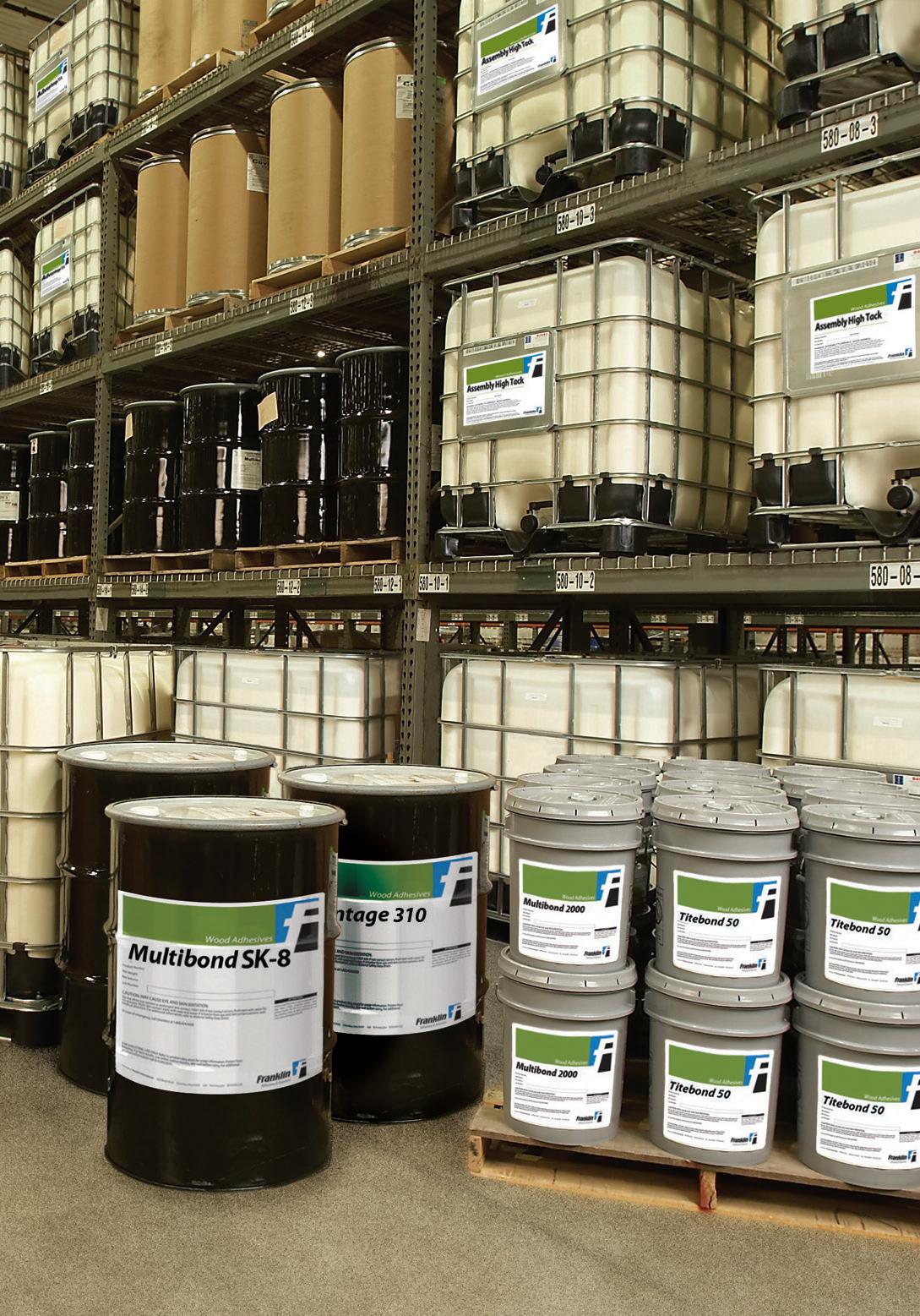
Welcome to the inaugural edition of ASC’s newest publication debuting with ASC’s Annual Convention and EXPO in New Orleans.
The featured articles cover hot topics on the minds of attendees as well as the broader adhesive and sealant industry such as automotive — with a particular focus on EVs — and building and construction. Thought leaders and industry experts discuss current and future trends as well as challenges and new, advanced adhesive and bonding technologies.
Also, I hope you enjoy reading about Avery Dennison’s award-winning technology that won top recognition from ASC at last year’s Innovation Award ceremony in Chicago, IL. Avery Dennison’s Mark Gower and Chuck Williams explain what the recognition means to the company and why the award matters.
In addition to rolling out our new publication, we are busy engaged in new and exciting activities that advance our industry forward. For example, we have formed strategic partnerships with downstream end user shows, such as the ASSEMBLY Show, PACK EXPO, and Fastener Fair, to promote the benefits of adhesives and sealants and ASC’s members that make them possible.
We are also engaging end users at other events, such as the Battery Show, the International Roofing EXPO, and World of Concrete to better understand their needs and serve as a bridge to ASC’s membership.
Additionally, ASC’s Sustainability Initiative is bringing the adhesive and sealant value chain together to discuss this important topic. We are identifying opportunities to improve our industry’s environmental impact. We are providing educational and networking opportunities to learn from one another. We are delivering valuable resources to help speak the same language and recognize those who rise above and achieve notable milestones.
At ASC, we continually strive to be the most valuable resource for manufacturers, suppliers, and distributors of adhesives and sealants in North America.
Our members — large and small — are the leading companies creating a better world through the products they make. It is a privilege to represent them and to provide valuable opportunities for them to grow their businesses through their membership.
Bill Allmond President, The Adhesive and Sealant CouncilASC is delighted to welcome these new members to the association so far in 2023:
• Clariant
• R. E. Carroll
• Trinseo
• Exponent
• CDF Corporation
• Cremer North America
• Helmitin
• Ravago Chemicals
• Lentus
• Palmer Holland
• LANXESS
They join the following 20 who became members last year:
• Adfast Canada, Inc.
• Airable Research Lab
• BEHR Paint Company
• Braskem America, Inc.
• ExxonMobil Chemical
• FasTech Adhesives, Inc.
• gluECO ADHESIVES LLC
• Magnekon S.A. de C.V.
• Matrix Adhesives Group,
• Meritool LLC
• Mitsubishi Chemical America Inc.
• Momentive Performance Materials
• National Adhesive Inc.
• Omya Inc.
• Petro-Canada Lubricants Inc.
• RH Adhesives
• Specified Technologies Inc.
• Stabond Corporation
• Univar Solutions
• Valtris Specialty Chemicals
The full ASC Membership Directory can be accessed via the website (https://www. ascouncil.org/memberdirectory), complete with company overviews and contact information.
After the resounding success of last year’s Sustainability Summit — which made its long-awaited return after eight years — ASC is delighted to announce Louisville, KY, will be welcoming attendees to our next two-day Sustainability Summit later this fall. More details will be announced shortly.
The event provides the perfect opportunity to learn about the
challenges and opportunities surrounding sustainability, and to hear from a fantastic lineup of industry experts. Presentations will look at the latest industry trends, market drivers, and innovations that will help to shape the industry in the years to come.
Sustainability is one of the three pillars of ASC’s Long Range Plan, which aims to help
member companies reduce their environmental impact and to develop and promote new products and technologies. Read more about the current Long Range Plan at https:// www.ascouncil.org/memberbenefits
Stay tuned to the ASC website (https://www.ascouncil.org/) for more information about the event in the months ahead.
January 2023 saw the release of ASC’s updated website, https://www.ascouncil.org/, offering a new-look portal where you can discover the latest news affecting the adhesive and sealant industry and access various resources.
Visitors can find out more about the association and the work we do, access information about member benefits, as well as upcoming events. There is also a section on our education offering,
with details about the ASC Training Academy Certificate Program (TAC), the technical short courses held at our events, and live and on-demand webinars.
“When designing the new ASC homepage, improving our members’ experience visiting the site was the highest priority,” said Bill Allmond, ASC President. “The new site is interactive, easier to locate the information our members most need, and more visually appealing.”
The ASC is pleased to announce that Forest Driggs (pictured), Senior Vice President & CFO at Franklin International, is our new Chairman, effective January 1, 2023.
With over 25 years’ experience in the adhesive and sealant industry, Driggs has seen firsthand the important role ASC plays in representing the sector and its membership.
He succeeds outgoing Chair Heather Campe and starts his two-year tenure hoping to help the association grow and support its members.
"I'm really excited to be working with our Board and Bill
and his team. I think we've got a diverse and dynamic group of leaders in our industry who are really engaged and committed to building and enhancing the value of ASC membership," said Driggs.
"I want to continue to look at ways to add value for our members and help them grow their businesses," he added.
"We've been really blessed with a lot of talented and dedicated leaders over the history of the organization, so I want to carry that legacy of stewardship and leadership forward. I'm committed to growth and enhancing the member experience and engagement."
After a challenging period for the industry, Driggs is confident market fundamentals are improving and that ASC members are well positioned to seize the opportunities that lie ahead.
Among his priorities, Driggs wants to showcase the many benefits of ASC membership and the resources available. "Coming out of COVID-19, I think we all now have a renewed appreciation for opportunities for members to assemble, network, learn, and grow together."
"Much of my time in this industry has been in sales, so I hope to be able to sell the value of what we offer at ASC. Hopefully that leads to membership growth, retention, and higher engagement — which will help us continue to be a strong organization moving forward."
ASC’s Annual Convention & EXPO will be held April 17-19, 2023, at the Hyatt Regency New Orleans. This three-day event will include sessions focusing on business development and market trends, regulatory, market segments, and new technology/applications
October 23-25, 2023
ASC 2023 Executive Leadership Conference
Join us at the ASC 2023 Executive Leadership Conference this October, where senior management will gather for three days of thought-provoking presentations and networking opportunities. Set at the fantastic Ponte Vedra Inn & Club resort in Florida, this will be a truly unmissable event.
September 13-15, 2023
FEICA European Adhesive & Sealant Conference and EXPO 2023
The FEICA 2023 European Adhesive & Sealant Conference and EXPO is the most important event for the adhesive and sealant industry in Europe. This year’s event is set at the PortAventura Convention Centre in Tarragona, Spain. Find out more at www.feica.eu.
Brittany Onslow, Head of Events for the Americas at Smithers, discusses the Sustainability in Packaging US conference and growing demand for adhesive and sealants in packaging.
Greenwashing
Sustainability is top of the agenda for ASC member companies and of increasing importance to customers and consumers. Tanya C. Nesbitt, Partner at Thompson Hine, highlights the implications of greenwashing and how to avoid it.
May 17, 2023
Design of Polymer Synthesis for Adhesives & Sealants
Jeremy Pasatta of Advanced Polymer Coatings provides an overview of the major polymer synthesis techniques, including free radical, emulsion, condensation and living polymerization.
June 21, 2023
Quality Considerations for 2C Adhesives from Cartridges
Ideal for users and suppliers of adhesives filled in 2C cartridges, this session — hosted by Dr. Hartwig Lohse — looks at the different technologies available, the requirements, and applications.
July 19, 2023
Silicones for Electronic Assembly: Principles & Applications
Sandrine Teixeira de Carvalho of Stammer Chemie GmbH examines the advantages and limitations of silicones in electronics and best practice.
August 2, 2023
Sustainable Product Innovation for Adhesives and Sealants
Tad Radzinski, President — Sustainable Solutions Corporation, considers the market drivers and sustainability requirements for adhesive and sealant products within the construction, transportation, and packaging sectors.
Inflation is at record highs, energy and gas prices are volatile, supply chains have been suffering severe disruption — all of which have been compounded by geopolitical tensions that are continuing to add to the uncertainty. There are still lingering fears of a recession and key end-use markets for adhesives and sealants — namely construction and automotive — will inevitably be affected.
For Dr. Bill Conerly, economist and consultant of Conerly Consulting LLC, current conditions have improved, but there are still concerns about the outlook later in 2023 and into 2024.
“For most businesses, it’s actually not been a particularly rough period,” he says. “Yes, inflation is high but revenues have, in any cases, been higher. Sales have been good in most sectors. People are facing much the same challenges as last year but lesser.”
“There are some sectors that haven't been great and they're the most interest sensitive sectors such as single family housing. But overall, things have been pretty good.”
The dollar has recently rebounded and energy costs are starting to ease. Even the supply chain issues seem to be improving, adds Conerly.
“Some of the statistical measures suggest it's about in line with long run averages, but I think people are perhaps more attuned to supply chain problems and pay more attention to them than they did five years ago.”
Port congestion, shipping issues, rail disputes, and driver shortages have beset orders and deliveries over the past few years, resulting in lengthy lead times and soaring costs. The supply chain woes have touched every business and presented significant challenges, which has required careful
planning and a willingness to adapt to new ways of working.
“The supply chain is looking better, without a doubt, but we have more and more businesses that are still nervous about its fragility,” notes Conerly.
“I'm seeing companies holding more inventory. It's unclear whether these are finished goods or raw materials, but the inventory-to-sales ratios are higher. Sometimes that happens early in a recession because companies make product they cannot sell, but I think this time round the companies are moving from ‘just in time’ to ‘just in case’ deliveries. For decades now, we've been seeing companies run their inventories leaner and leaner, and now they’re changing their mentality.”
Hiring has also become more problematic, he says. During the pandemic, the labor force bore the brunt of multiple lockdowns, social distancing restrictions, and the enormous financial pressures placed on businesses.
Some people were unable to work, some were too afraid to. Others seized the opportunity to leave the workforce entirely and retire.
At the start of this year, U.S. job market figures showed a 50-plus year low in terms of unemployment levels. The labor market remains tight and some employers are struggling to find suitable candidates for empty roles, says Conerly.
“Right now, if you’re the person looking for a job, things are pretty rosy — but if you’re looking to hire people, it’s not so good,” he says. “Hiring is easier; it’s still tougher than what we’re used to, but it’s not as tight a labor market as it had been.”
“I am seeing more and more companies saying they’ve been able to find the people they need but, of course, it’s harder for those looking for the more technical, specialist positions. Things will continue to get easier but looking through to 2030, we’re in a very long term tight labor market with baby boomers retiring and the next generation being smaller.”
Market conditions these past few years have been challenging, to say the least. So, what’s on the horizon for the U.S. economy — and the adhesive and sealants sector?
“The supply chain is looking better, without a doubt, but we have more and more businesses that are still nervous about its fragility”
Dr. Bill Conerly Economist and consultant, Conerly Consulting LLC
Building and construction remains one of the major markets served by adhesive and sealants. However, the combination of rising home prices and high mortgage rates have dented demand for house purchases, with the home improvement segment also suffering because of tightening household budgets and the ongoing cost of living crisis, says Conerly.
“We’re now starting to see the effects of the Federal Reserve tightening and after a while, six months or so, you start to see ripple effects where people may be trimming their spending — and then you have sectors that are not particularly interest sensitive cutting back. Those ripple effects would affect DIY and home improvement projects.”
“Home construction will continue to be soft this year,” he suggests. “Mortgage interest rates are not as high as they have been, but house prices are still very high. They've come down a little in the last few months, but by
my calculation they're still running about 25% above trend. The bright spark here though is remodeling and renovation.”
“I think multi family, including multiple units and duplexes, will decline as well, but it will be on a longer lead time and move more
sluggishly. Net, I think we’re going to see reduced demand for construction related products.”
The automotive industry — and specifically electric vehicles (EVs) — provides many potential applications for adhesives and sealants producers, but activity is also being dampened somewhat because of the prevailing market conditions.
“There’s talk that dealers are worried consumers are looking at higher interest rates for financing their purchase. Car prices have gotten really high, but I think there’s some pent up demand for new car sales and that prices will come down to get them moved,” says Conerly.
“The car market has suffered in terms of units sold because of the supply chain problems. With less supply, people have been paying over list price for popular models, which is really unheard of. As supply problems diminish, car volumes will at least stay level and probably rise. More volume will help those selling adhesives and sealants into the car market.”
Although EVs still represent only a relatively small portion of the total car sales, demand is slowly accelerating — opening up many new applications for adhesive and sealants suppliers in the future.
Market fundamentals may be improving but consumers are still spending less in these tough times. For now, uncertainty remains. Business leaders would do well to now start putting contingency plans in place so they can weather the storm and capitalize on any opportunities that arise, says Conerly.
“I do believe we’re headed for a recession, starting maybe late 2023 or early 2024. That’s what I said last fall at the ASC Leadership Conference and it still seems right in line,” he says. “We had a good second half of 2022 despite the higher interest rates, but I do think the chickens are going to come home to roost and we’ll soon have a recession lasting maybe 6-9 months.”
“As we go into a recession, I always advise my clients to start planning on how to take advantage of it,” adds Conerly. “The early stages of a recession are probably a little too early to be expanding, but it’s the right time to identify what you want to do. That could be buying another company, expanding facilities, entering new markets, or hiring people.”
Andy BriceHalf the cars sold in the U.S. will be electric by 2030, according to goals set by President Joe Biden.
Various incentives and initiatives are already in place to facilitate the move of electric cars from high-end market to mass production — although limited charging infrastructure and high battery prices could slow that transition.
But whether this ambitious target is met or not, the burgeoning electric vehicle (EV) market will certainly enjoy substantial growth this decade. And that’s great news for the adhesive and sealant sector because of their many and varied applications in vehicle bodies, interior components, and the battery packs themselves.
The automotive sector is already one of the biggest end markets for adhesives and sealants. Applications vary from joining components and holding together body panels to providing sound and vibration attenuation and protecting car circuits.
The value of adhesives used in light vehicle components amounted to over $2 billion in 2020, according to data provided by strategy and research consultancy ChemQuest.
This figure has likely increased in 2021 and 2022 as demand for new vehicles continues to grow after the slowdown seen during the COVID-19 pandemic.
“Adhesives and sealants play a critical role for the safety, appearance and performance of every vehicle on the road,” says Marc Benevento, President of Industrial Market Insight. “It goes even further for EVs because they have been so important in the development of the electric powertrain technology.”
Adhesives and sealants are used in the battery packs, as well as the electric motors that power EVs. Thermally conductive adhesives, for example, help the cooling
process of the different battery components — improving efficiency, extending their lifespan, and preventing electrical shorts and fire risk.
Structural adhesives provide additional support and protection of battery cells within a battery pack, protecting them from mechanical shock and vibration while the vehicle is in motion. They also ensure the electrically charged cells do not touch, which could cause a fire and significant damage to the vehicle.
“Inside the battery pack, you need electrical isolation, thermal management, and structural strength — all of these things are performed by adhesives,” says Dr. Pradyumna Goli, eMobility Business Development Manager at Henkel.
Sealants also play an equally vital role in ensuring a battery’s safety by completely sealing it from environmental debris or moisture, while also preventing fumes from spreading in the event of a thermal runaway.
The construction of the body and interior of a modern vehicle is completely reliant on adhesives and sealants.
Lightweighting is a key advantage over other bonding methods such as mechanical fasteners. A lighter vehicle improves efficiency and extends the life of the engine — whether electric or a traditional internal combustion engine. This is particularly pronounced in EVs though as they prove much heavier than traditional cars, says Goli.
“An electric car is at least three times heavier than the traditional car because of all the metal going into the battery pack,” he says. “Adhesives really help balance that weight out and improve the car’s efficiency.”
Structural adhesives tend to be preferred to welding when constructing the body of the car given their ability to bond dissimilar materials — something that cannot be achieved by any other method.
Separately, adhesive automation through robot dispensing helps speed up production, an advantage valued by any mass car manufacturer.
Adhesives are also a much safer alternative than welding, especially in an electronically
The electric vehicle market is expected to grow significantly over the next few years — and adhesives and sealants will play a vital role
sensitive environment.
Noise, vibration and harshness characteristics are also an important consideration. In a conventional vehicle, they limit engine noise entering the passenger compartment. And even though EVs lack such noisy engines, drivers are still subject to excessive road and wind noise. Manufacturers are therefore looking at various ways to block that noise, which presents new opportunities for the adhesive and sealant market.
“Adhesives and sealants will remain key components of modern vehicles as you just can’t beat the tons of benefits they bring, whether they are used together with other joining methods or alone,” adds Benevento.
Adhesives and sealants will undoubtfully be a key contributor to the projected growth of EV consumption in the years to come. There are, however, some doubts as to the speed at which that growth will materialize.
Just under 6% of new U.S. cars sold in 2022 were electric, according to public market data. The number is relatively low compared to the ambitious 2030 target, although it still represents a steep 65% year-on-year improvement.
This positive trend contrasted to a decline in the overall year-on-year number of cars bought in the U.S. in 2022. It also came at a time when the auto sector has been tackling inflation, a stretched labor market, and a
supply chain crisis — all of which contributed to a shortage of new vehicles.
The EV sector has been somewhat shielded from these challenges. With electric cars still considered a premium product, their demand was not high enough to be significantly impacted by these logistical challenges. However, the sector has still had its own set of obstacles to overcome.
Among these is their high price point, which keep them at the top end of the market.
“The perception that future demand will be there is driving the specification work around EVs, but for that demand to really materialize cost reduction is necessary,” says James Swope, Chief Commercial Officer at ChemQuest.
While there are a number of tax credits and rebates aimed at U.S. households, there is skepticism over how quickly and easily they will turn to electric cars.
“The key thing is, are consumers in the U.S. ready for EVs? Making the change from early adopter to mass market is typically not that smooth a transition,” says Benevento.
Goli is much more optimistic about the speed at which EVs will penetrate the U.S. market.
“I can safely say electric cars should be a dominant player on the road compared to traditional cars in the next 10 years,” he says, adding that the overall perception of electric cars as a premium product is somewhat misleading as they vary considerably in their model and price range.
“When talking about EVs, the base model to look at is a semi premium model [Tesla Model 3]. We should get out of that mindset and see other EVs like Leaf, Bolt, ID4, etc. that also are available in the market,” he notes.
The current lack of sufficient EV charging stations is another major factor to consider when looking at near future electric car consumption in the U.S.
While there are government rebates aimed at supporting charging network manufacturers, there is some doubt as to how quickly these stations could be up and running.
“My personal opinion is that the headwinds are still quite strong for EVs. There is little charging infrastructure ready to support the projected Battery Electric Vehicles (BEV) growth,” says Swope, adding that current infrastructure is better equipped to support alternatives, such as hybrid electric vehicles (HEVs) and Plug-in Hybrid Electric Vehicles (PHEVs).
Other technologies such as hydrogen
generated electric (fuel cell) and hydrogen powered internal combustion engines are still nascent and yet to be fully commercialized, but have enormous potential for the future. Again, adhesive and sealants will be required to enable their deployment.
Suitable infrastructure is particularly important in the U.S. where people rely heavily on long-distance driving.
Benevento believes insufficient charging infrastructure is likely to keep the number of new EVs on the road low despite the fuel economy standards introduced by the U.S. government.
“I think there is still going to be a significant bridge, where in order to meet the fuel economy standards more people are going to go for a hybrid, which is much less expensive than a long-range EV,” he says.
Most of the initial EV offerings have been very expensive due, in part, to the long range capabilities and the batteries they require.
Goli, however, remains doubtful about the future of hybrids as maintenance costs are comparatively high owing to their dual engine architecture.
“If you look at the total ownership cost for five years, EVs will be cheaper than the hybrids. Hybrids are running out of their course and in the next few years we will be seeing either traditional or pure electric cars on the road,” he says, adding that all major U.S. manufacturers are now moving away from hybrid production.
While there is still uncertainty as to how and when consumers will embrace EVs, the market will inevitably enjoy significant growth in the coming years. Adhesive and sealant manufacturers will play an increasingly important role on that journey.
Acouple of years of strong growth in the U.S. residential construction sector looks set to reverse as rising inflation and high interest rates have put a dampener on the housing market, which will undoubtedly impact the adhesives and sealants business.
“We’ve just come off the highest growth in the value of construction that we’ve seen in years within U.S. industry, primarily driven by the residential segment,” says Chris Fisher, Managing Principal at global consulting and M&A company Ducker Carlisle, where he leads the firm’s building and construction industry practice.
“COVID-19 spurred significant growth in residential construction and remodeling, although the non-residential sector did not enjoy the same opportunity. Now we’ve entered into a period of high interest rates that will slow all new construction and major projects, equating to a more challenging time for the construction industry after a few very solid years,” he says.
According to Ducker Carlisle estimates, spending on new homes grew at an average annual rate of 13-15% for the period 2019 to 2021, and residential remodeling expenditures also grew at a near record 9-11%.
And given the increased building activity and economic environment, it is likely that most adhesives and sealants manufacturers have enjoyed some pricing power and been able to achieve higher revenues with lower volumes. In the long run, construction practices continue to evolve which support using more adhesive and sealant content, particularly with panelized construction — and this looks set to continue.
Looking ahead through 2027, Ducker Carlisle is predicting slower growth for new residential construction at an annual average
of 2-4%, with remodeling a tad lower at 1-3%. Spending on non-residential i.e commercial buildings, will also see annual average growth of 1-3% during the next five years. Should interest rates and inflationary conditions improve, so will construction activity through the forecast period.
Fisher says construction demand will favor remodeling, improvement, and upgrades to facilities — both homes and buildings — as skilled labor limitations, financing costs, and the time taken for local permitting/ regulatory approvals reduce new construction momentum.
There are two major trends in construction right now. One of these is the growth of offsite construction, where building panels, walls, and structures are fabricated in a factory and then transported to the job site. This system requires a lot more lamination — and a lot more adhesive — and is, says Fisher, one of the biggest areas of innovation in the building products area in recent years.
“Offsite construction, panelization, and prefabricated/finished product suites will continue to grow at faster rates than traditional construction and offer a long-term opportunity to innovate product/system solutions that
further expand advantages within the segment, for example, making it easier to install the building envelope,” Fisher says.
He adds that building envelope performance, including moisture management, air exchange, and fire performance, as well as new technology in construction, will drive more panelization and systems thinking for both non-residential and multi-family buildings.
The second trend relates to environmental, social and governance (ESG), in other words using more sustainable materials in building products. Certainly, the ESG movement is creating new ways of thinking about chemicals and formulations, and toxicity levels. But, cautions Fisher, the industry needs to be careful not to confuse “bad chemical” concerns with adhesives and sealants that can bring multiple benefits to fabrication processes, as well as making high-weight structures lighter, delivering ESG benefits in an indirect manner.
And, adds Consultant and former Scientist Emeritus with Dow Corning, Jerome (Jerry) Klosowski, there is inevitably a trade-off between products that are environmentally durable and biodegradable. “Are customers willing to sacrifice durability for biodegradability?” he asks, noting that bio-
Slower economic conditions in the months ahead will undoubtedly impact manufacturers of adhesives and sealants — but growth opportunities abound in the longer term
degradable adhesives would be more suited to the weather-related market rather than structural applications.
Chris White, Senior Managing Scientist with engineering and scientific consulting firm Exponent, hypothesizes about the potential of using solar energy to degrade adhesives, citing banana skin as the perfect example. “There are a lot of adhesives that will not be exposed to UV light until after use, or can be designed for solar energy to degrade them post use,” he says. “Maybe adhesive manufacturers should look at changing formulations to benefit from photocatalytic degradation and degrade over time, like a banana peel. Possibly using destabilizers, rather than stabilizers, as a trigger.”
One opportunity for his suggestion could be the solar panel market, which is looking as though it may be a very attractive segment for adhesives. No different to any other structural panel, solar panels are generally fixed to frames by mechanical fasteners, which requires skilled labor.
But the mechanical fasteners suffer from thermal ratcheting, where the bolts get hot then cool and loosen over time. A peel and stick adhesive — or a structural glazing sealant
— could do the job and be durable for 30 years or so. “This area is a tremendous opportunity as there is an immense amount of solar panels being installed every year, so market growth would be significant,” says White.
Adhesives are already increasingly replacing mechanical fasteners in the transportation industry, the ASC says, where the benefits include reduced cost in terms of the material used for bonding and the labor required, plus less damage to surfaces during assembly, faster assembly time, and lighter weight of the structure.
Looking at the different types of adhesives, Klosowski sees ongoing growth for silicon products, as well as hybrids. He also notes there are some new and better-performing acrylics on the market that are now acceptable for use in high-rise buildings. Previously, acrylicbased adhesives were not used on commercial buildings because of their lack of durability, but Klosowski sees some acrylic products moving into that area going forward.
Another trend in the market centers on the supply chain challenges that reared their head during COVID-19, when several ports around the world were either closed or running at very significantly reduced rates and freight rates soared.
Because global supply chains have become more fragile — not to say more expensive — Fisher says companies have created new ways of developing formulas and formulations, with components that can be sourced locally, or certainly much closer and faster than having to wait a minimum of 12 weeks for a particular specialty chemical or additive.
An additional change — also related to
the supply chain — is the way in that the construction industry and its suppliers are working on their channel to market. Fisher says new business models and practices are finding momentum such as direct to contractor or consumer, the use of valueadded distribution services, and digital tools to solve labor constraints and create greater efficiencies throughout the value chain.
“Go-to-market technology will be disruptive,” he says, pointing out that the resurgence in big-box stores seen during COVID-19, coupled with strong digital platforms, and new investments toward bulk/ pro-dealer services with “professional” type offerings are creating an important customer segment to build greater alignment.
Pricing and value management competency will also be a differentiating factor in the building products industry due to channel power dynamics, slowing demand conditions, and undisciplined trade professionals, according to Fisher.
Furthermore, he adds that optimizing portfolios and rationalizing inventory levels will be important for players in the building products industry in order to maximize their resource efficiency and direct investments toward a different future state of construction materials and practices.
These factors could become increasingly important as 2023 progresses, given the fears of recession. Ducker Carlisle is predicting “a delayed recession but one that bounces back”. A shallow, soup bowl experience, probably in the second quarter,” is how Fisher describes it.
“We had anticipated that in the first quarter of this year, but it has been deferred because of the strength of the consumer,” he says. New residential construction is already down and high interest rates will keep both it and the non-residential segment very slow in the first half of this year, with potential to begin recovering in the second half. “Flat to no growth would be a win for 2023 and hopefully a slower recovery coming into 2024.”
Despite the more challenging outlook for construction in the months ahead, the longer-term outlook for adhesive and sealant manufacturers continues to burn brightly, driven by the environmental benefits they can bring to the sustainability table, particularly in replacing metal components.
Nevertheless, manufacturers must keep pace with shifting business models and digital platforms, or risk getting left behind in a rapidly evolving marketplace.
Elaine BurridgeASC has partnered with Venture Business to publish and circulate a magazine among attendees at the Executive Leadership Conference, Florida, 23-25 October 2023.
If you’re planning to sponsor or attend the conference or simply wish to reach those who are, then advertise here to showcase your products and services!
In advance of ASC announcing who will receive the 2023 Innovation Award, Avery Dennison discusses its winning entry last year
Innovation drives progress in the adhesive and sealant industry and ASC recognizes the importance that companies put on keeping their competitive edges sharp with its annual Innovation Awards.
Inaugurated in 2017, the awards will next be presented at ASC’s Annual Convention & EXPO in New Orleans from April 17-19, 2023.
Last year, Avery Dennison was selected from a record number of entries and received the accolade for its ground-breaking, solventfree acrylic pressure sensitive adhesive.
Mark Gower, Technical Principal, who led the development team, says it was “a really big deal to win a global award” and it had a hugely positive impact on the product, technology, and team behind the development.
The winning submission was centered around Avery Dennison’s Advanced
Acrylics Technology, which delivers high performance pressure sensitive adhesives. It was developed at the company’s Polymers, Adhesives and Coatings Center of Excellence (PACE) research facilities at Mill Hall, PA.
As well as providing Avery Dennison with a strong external marketing opportunity,
winning the award helped the team “to market our department internally. It helped to get the word out about the technology outside and inside the company,” says Gower.
Chuck Williams Senior Director, R&D, Global Platform at Avery Dennison adds that the award “validates the last seven years’ work and it is important that the ASC recognizes this development for the sake of the industry. It is a fledgling product, but the award recognizes that it is a game-changing technology.”
A year on from winning and the technology is being commercialized. “The award is helping,” he says. “More people are approaching us with more confidence about using the product and we are extracting value from the technology.”
Water-based adhesives evaporate water
“The award recognizes that it is a game-changing technology”
Chuck Williams Senior Director, R&D, Global Platform, Avery DennisonMark Gower, Technical Principal at Avery Dennison (pictured left) with the award alongside Chuck Williams Senior Director, R&D, Global Platform Mike Soche, KDG Advertising & Marketing
during the manufacture of self-adhesive articles whereas solvent-based systems evaporate large quantities of flammable and toxic solvents. The Advanced Acrylics technology can match, and often exceed, the performance requirements placed on traditional solvent-based systems.
Solvents-based systems (whether water or hydrocarbon-based) have solvents removed during self-adhesive article manufacture to provide a tape or label with a dried PSA layer ready for application/end-use. For legacy emulsions, surfactant accumulates at the adhesive/air interface during the adhesive drying step, lowering the overall performance of the ready-to-use self-adhesive article.
Williams explains that the technology was developed because of demand pull from the market and technology push from within Avery Dennison. “There is a need to get away from solvent-based systems. Solvents are hazardous and are only used as a carrier,” he says.
Moving away from solvents has a number of benefits. The water-based systems are typically 65% solids, and solvent-based adhesive systems are around 35-40% solids.
Avery
Watch the video by visiting https://www.averydennison. com/en/home/newsroom/ avery-dennison-blog/ Graphics-Solutions-Blog/ avery-dennison-recognizedfor-another-industry-first.html
This means that much less carrier is shipped with each delivery, so the amount of carbon generated for each pound of useful adhesive is reduced.
Water is also much less expensive than solvent. Moving to these systems in 2022 resulted in Avery Dennison reducing fossil fuel use by 67% and energy use by 49% compared to solvent-based products.
There are also benefits from water being non-flammable. Water-based systems are easier and safer to process than a flammable solvent mixture and, as water-based emulsions contain no solvents, empty drums of emulsion are also much less hazardous in terms of waste disposal than empty containers of solvent-based systems.
But emulsion-based systems are complex. Emulsions are designed to keep two incompatible liquids as a mixture, by adding a third: a surfactant.
Surfactants have two different properties in their molecular design. One part of the molecule is attracted to one liquid, the other end is attracted to the other. Soap is a good example. One end of soap molecules is attracted to greasy hydrocarbons, the other is attracted to more polar water. That is why washing works — dirt in the grease is floated off into water by the soap.
With adhesives, however, emulsions can pose a challenge. The surfactant can get between the active adhesive and the substrate, which can reduce the strength of adhesive bonds or prevent bonds forming at
all. Avery Dennison’s PACE team found a way around this.
“We had some history with controlled polymerization in solvent-based systems and decided it would be interesting to try something similar with our adhesives based on emulsion coatings,” says Gower. “We had some initial success, but it was complex.”
He says work published by the University of Minnesota gave his team encouragement. This suggested that if it were possible to keep the surfactant away from the interface between the substrate and the adhesive there would be a good chance of forming a strong bond.
The PACE team designed molecules to gain adhesion, which Gower says “is bridging the gap between polymer chemistry and fine chemistry”.
“A unique outcome of our work is that there is no surfactant at the bond,” he notes. The solution is to polymerize the surfactant as part of the bonding process.
For Williams, ASC’s Innovation Award helps to highlight the benefits of designing molecules to gain adhesion as well as the molecular architecture which drives adhesion. It also demonstrates the strength of the Avery Dennison team — and shows that it is possible to produce high-performance, sustainable adhesives that are not solvent based.
To find out more about the Innovation Awards, visit ASC’s website at https://www. ascouncil.org/innovation-awards
“It’s a really big deal to win a global award”The annual Innovation Awards celebrate the achievements of ASC members Mike Soche, KDG Advertising & Marketing
"Serving customers for over 100 years"