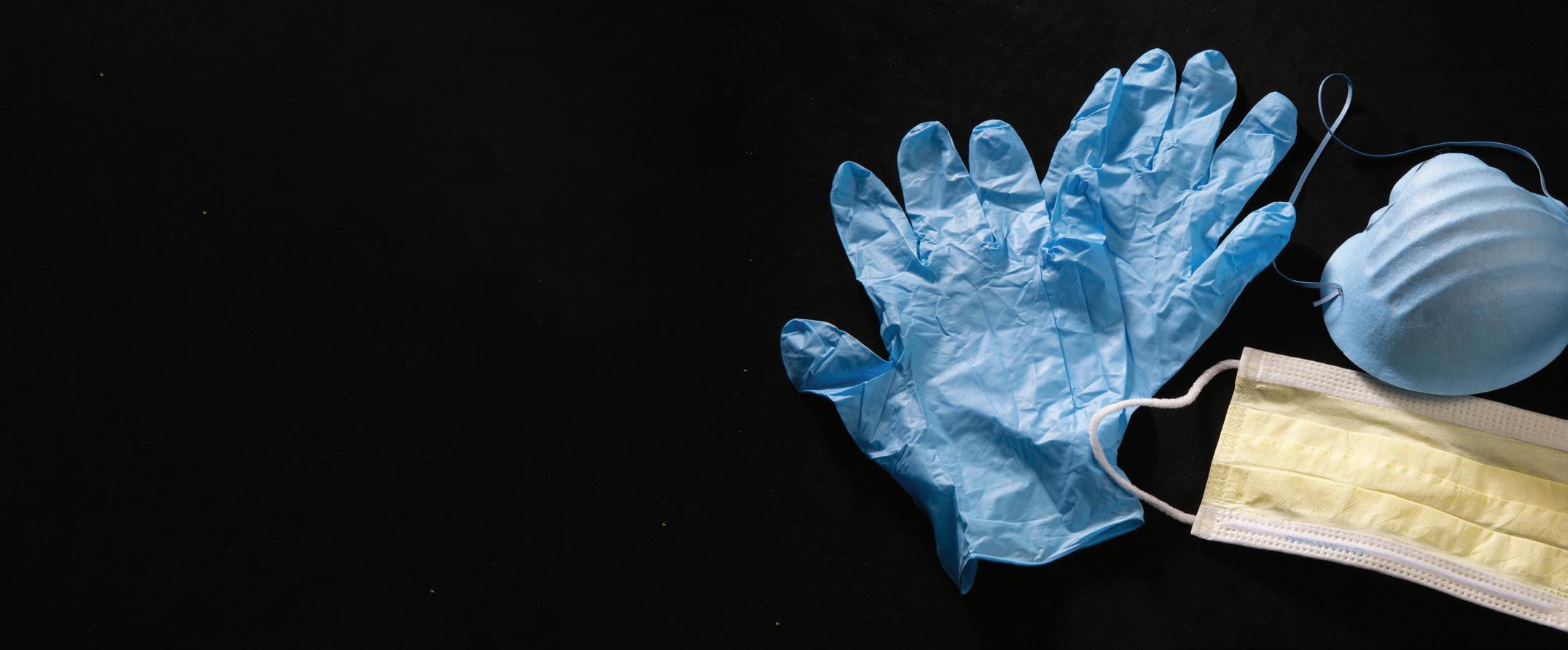
3 minute read
KEEP PROTECTION ON THE SHELVES

from NOLN - May 2023
by EndeavorBusinessMedia-VehicleRepairGroup
PPE precautions are
a holdover from COVID 19 to keep on hand for contingencies
BY ENID BURNS
THE COVID-19 PANDEMIC IS PAST THE extreme days of high infection rates and lockdowns. At the start of this year, four states (Hawaii, Illinois, Oregon, and Washington) still had indoor mask mandates in place. Small businesses that deal with the public such as quick oil chain shops continue to face challenges to keep up with changing regulations while staying up to speed on day-to-day business operations.
A good standard to live up to is set by the Occupational Safety and Health Administration (OSHA). Businesses nationwide are required to keep certain standards and have regular review. If a business sees a need to go further than OSHA standards, the model set by the organization can be used to implement any additional measures.
Changing Standards
Precautions such as cleaning standards and protective gear have both national and local regulations, which has been difficult for many businesses to keep up with. In a prolonged pandemic rules have evolved over time, and while some Personal Protective Equipment (PPE) standards have lightened, it is advisable to keep gear on hand to use as situations arise.
One effect of the pandemic was to bring cleaning and protective standards to attention, and create better best practices.
“It is best to have a formal safety program which includes the PPE Hazard Assessment required by OSHA,” explains Colette Bruce, owner of Team Safety LLC. “This assessment specifies each task performed by the employees, the hazards associated with those tasks, and PPE required to perform that task safely. This assessment is required to be updated when new assignments/tasks are created, and annually thereafter.”
While some pandemic-related precautions are now relaxed, it is important to keep up with current safety standards and have a plan when it is necessary to increase those measures. Practicing regular safety within a shop or business is always necessary.
“The PPE Hazard Assessment will set out the requirements and best practices for all the tasks performed,” Bruce tells NOLN. “This should be developed with the PPE Written Program that OSHA mandates and posted throughout the shop. Additional signage is a very good way to remind employees of the policies. It is recommended to seek professional assistance with this so it is comprehensive and aligns with OSHA’s requirements.”
Bruce says there are 22 states in the U.S. that have their own OSHA program, which typically exceed Federal OSHA requirements.
Compliance Concerns
Once the guidelines are set, whether they are imposed by OSHA, the state, or simply by the shop or parent company, it can be a challenge to comply. Standards on cleaning procedures, use of PPE and other practices are only as good as the employees who follow them. Managers may have to instruct employees, but also find individual ways to get employees to follow procedure.
“Behavior-based education is the best way to eliminate resistance from employees and establish a safety culture in the shop. Management leading by example is very important,” Bruce says.
During the pandemic, it was necessary to add more PPE and additional precautions to daily operation.
“We were all over it when COVID first hit,” Bill Floyd, owner of Lucas Oil Center in Evansville, Indiana, tells NOLN. Lucas Oil Center spent time developing policies and adapting to the situation in order to stay in operation.
The OSHA PPE Hazard Assessment is a good place to start for setting best practices for the shop. From there, bringing in new hires is a good time to refresh the staff if best practices are not being met.
“OSHA requires that all employees are trained when a new hire on multiple topics of which PPE is one of them,” Bruce says. “Then annually the shops are required to conduct training.
“Supporting signage is effective and employers must enforce their policies and lead by example. If there is a sign on the door ‘Safety Glasses Required,’ then that means anyone who enters is to wear the PPE. Employees will lose respect for the PPE if they see others not wearing it.”
Keeping PPE and Supplies in Stock
During the quarantine period of the pandemic, it was nearly impossible to find basic cleaning supplies, masks, gloves, and other PPE materials. While those supplies are more readily available, keeping stock on hand is helpful to keep up with need as it arises.
Just as important as keeping an
“Establishing a PPE distribution system that is a written document similar to the PPE Hazard Assessment that outlines what has been distributed to the employee and when.”


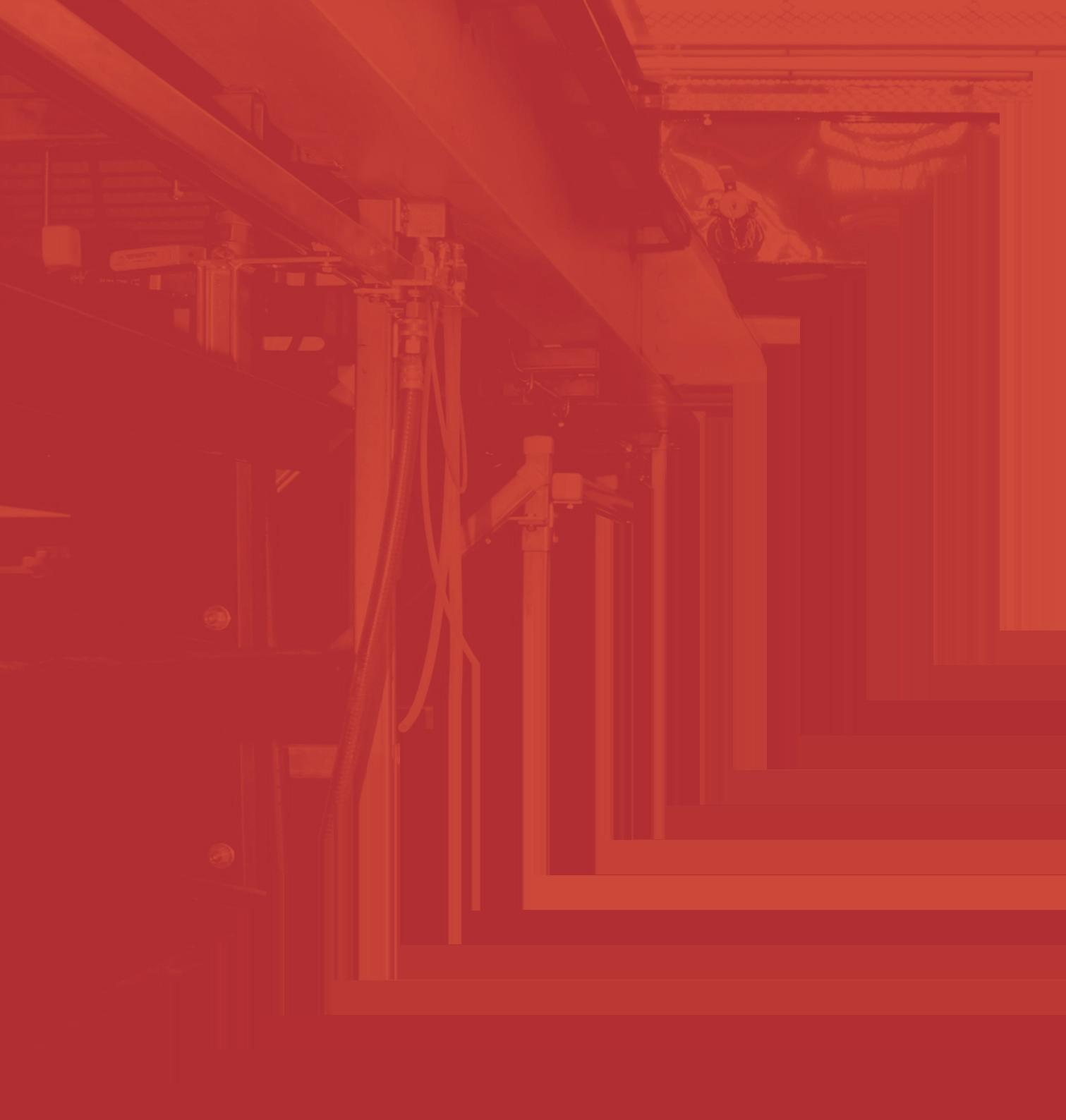
Bruce says. “A policy can also be put in place for lost or negligently damaged equipment that must be paid for by the employee. This tends to encourage proper care of the equipment.”
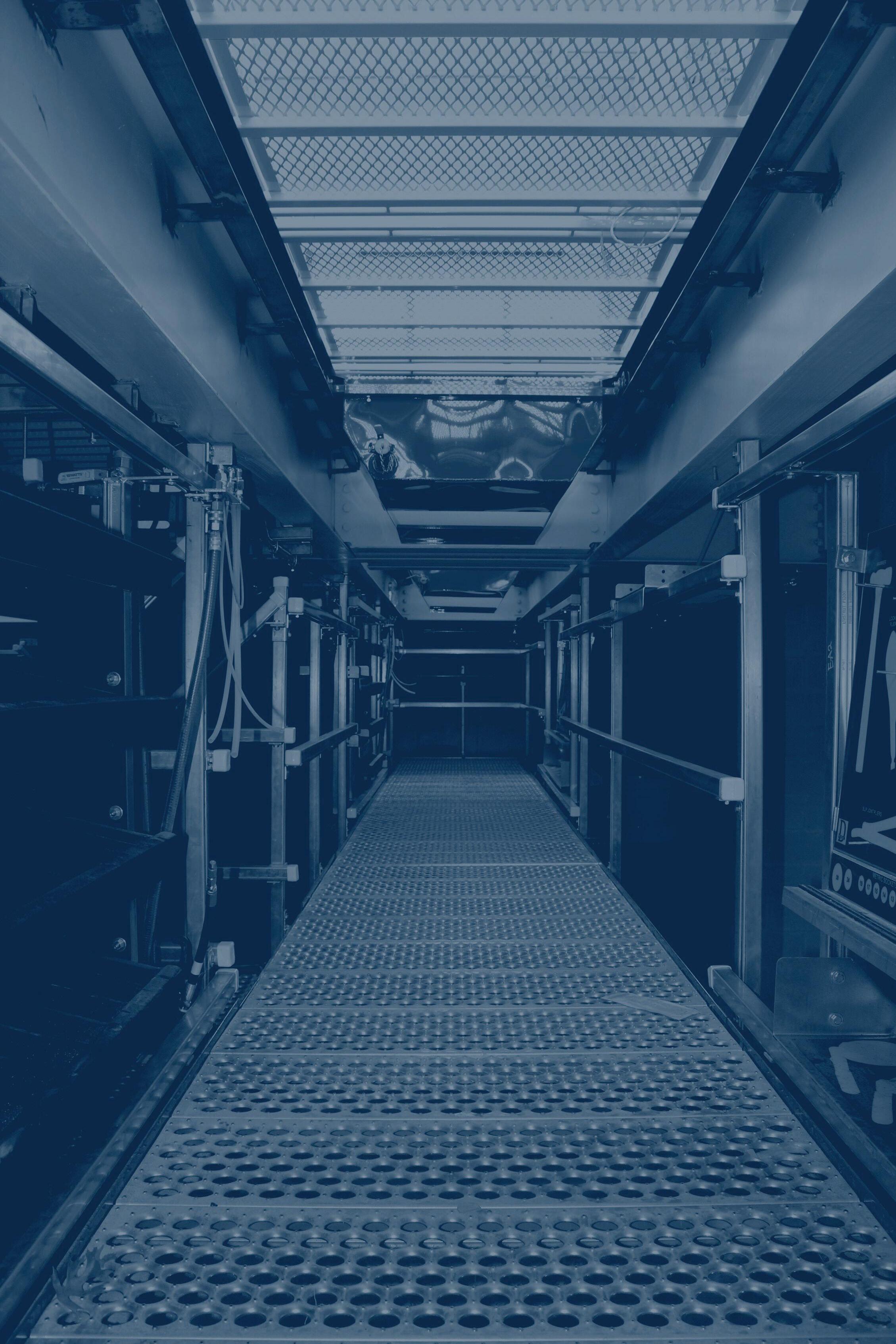