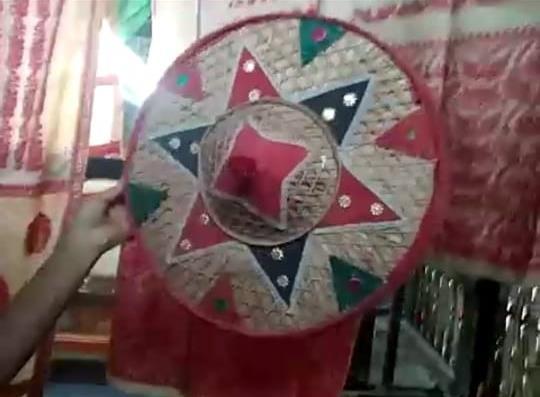
25 minute read
References
Figure 48 japi cap
Figure 49 joonbiri motif and joonbiri necklace
Advertisement
Figure 50 collection of mekhela chador
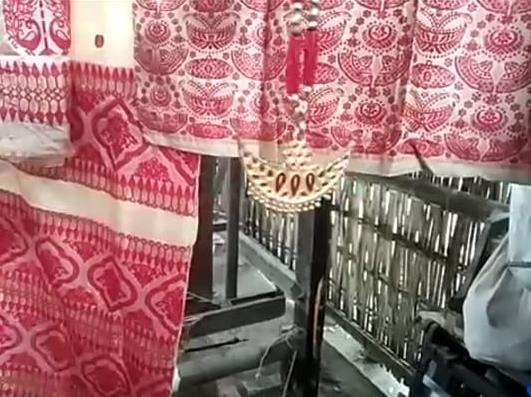


Figure 51 combination of phool buta and contemporary design


Figure 52 mourah motif
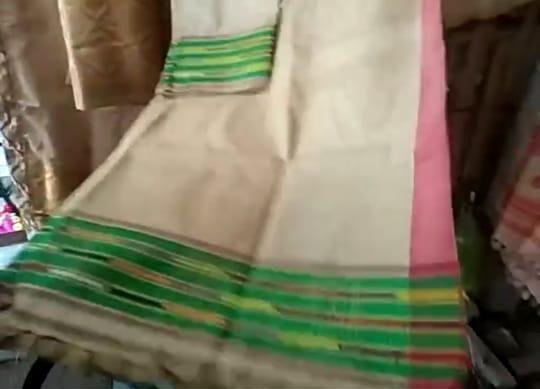
Figure 55 riha chador Figure 53 mourah motif and arnal bodo motif
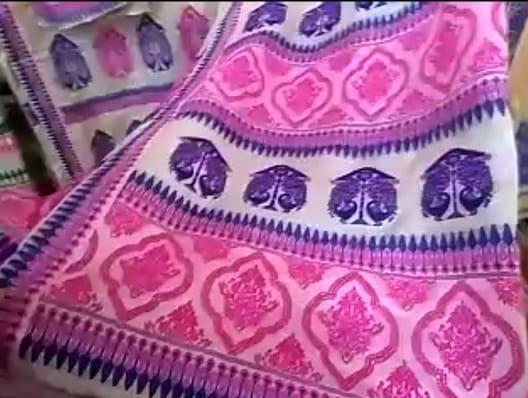
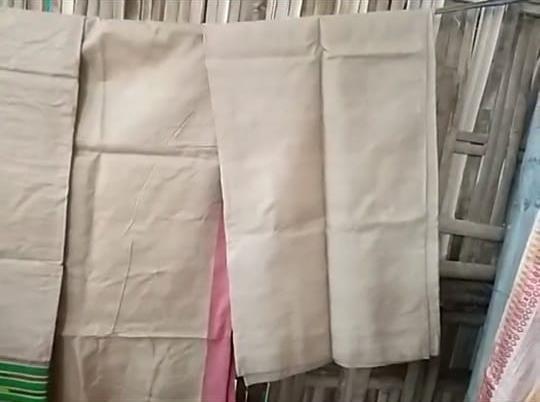
Figure 56 single mekhela (to be worn with riha) 23
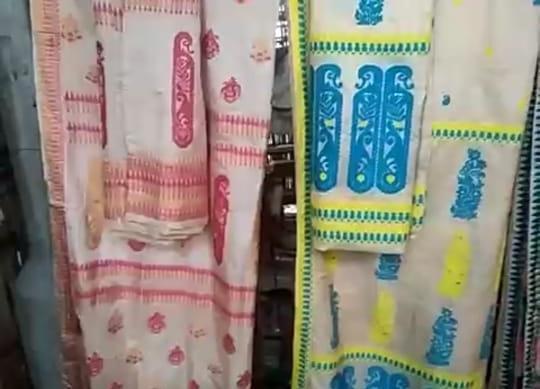
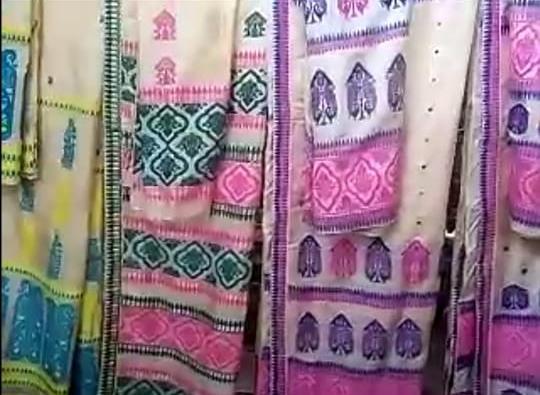
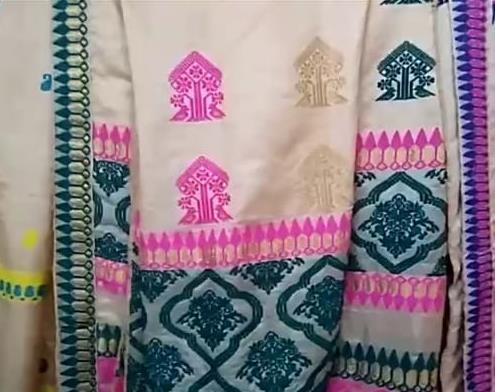
Figure 57 kalki motif and phool buta motif Figure 58 collection of contemporary mekhela chador
Figure 60 gach motif Figure 59 gach motif
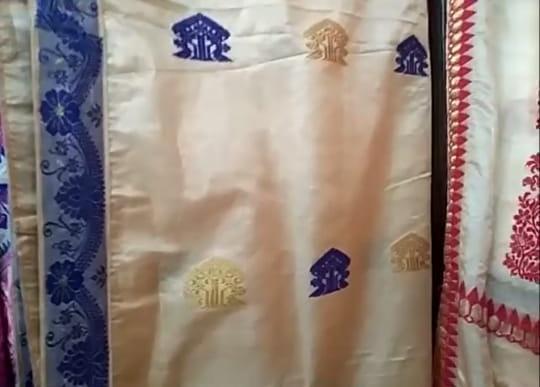

Figure 61 mourah motif
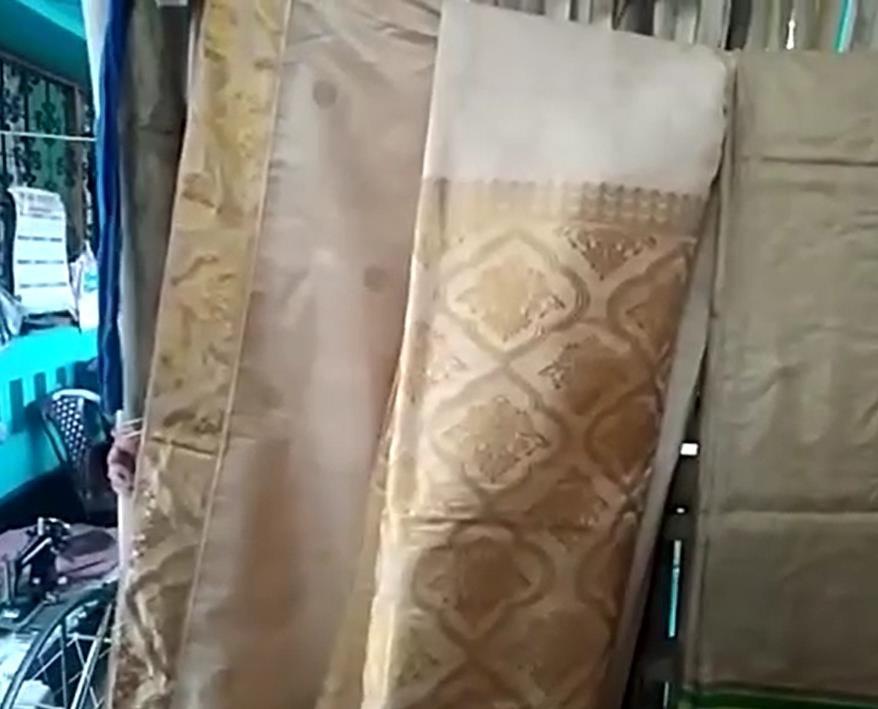
Figure 62 bridal mekhela chador Figure 63 bridal mekhela chador
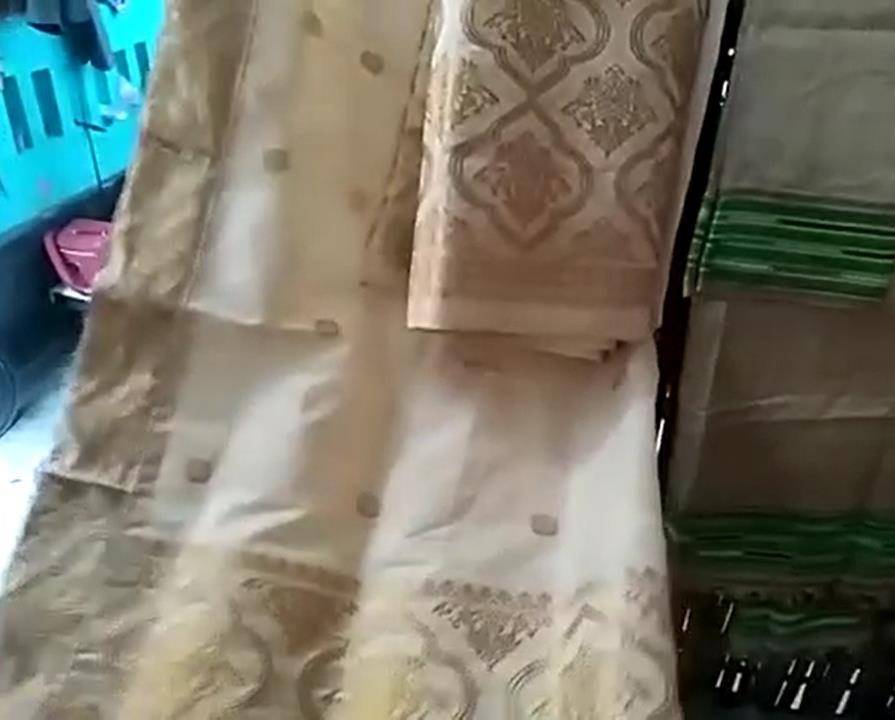
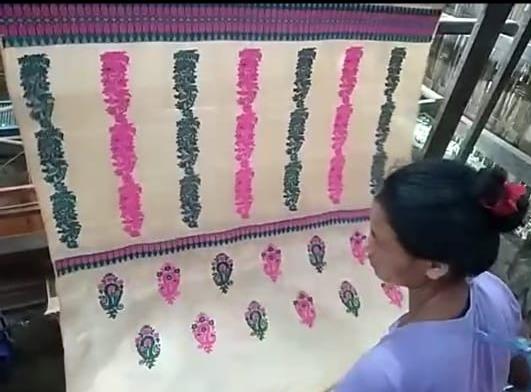


Figure 64 Figure 65 Figure 66
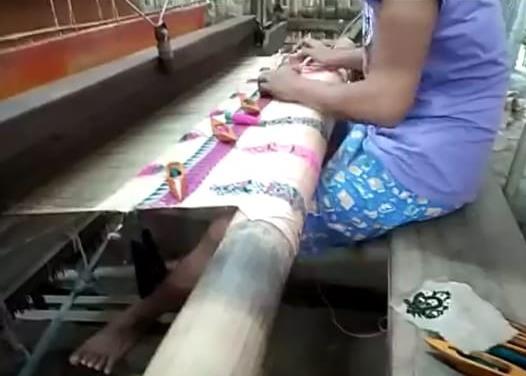
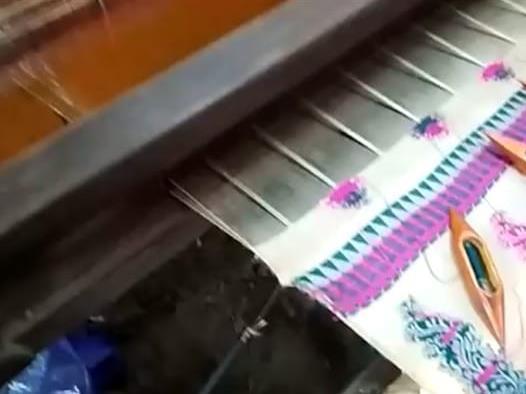

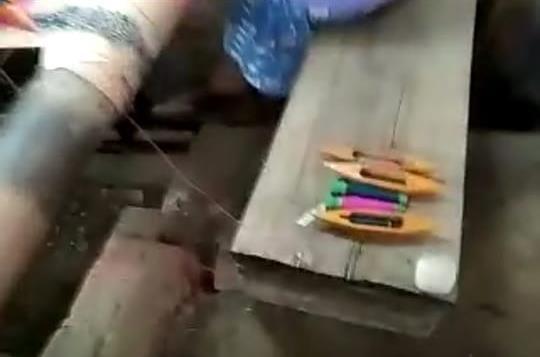
Figure 70 mouharah Figure 71 silk loom Figure 72 silk loom

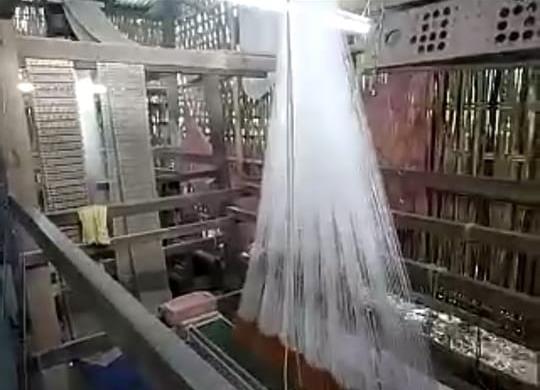
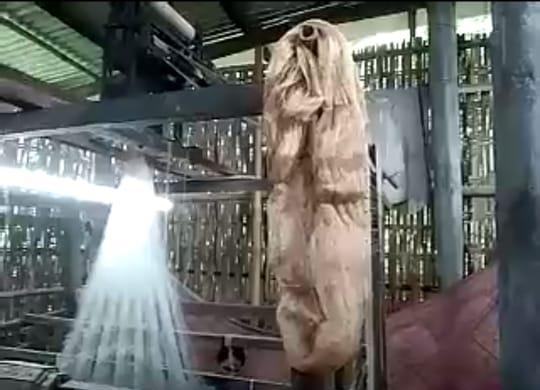
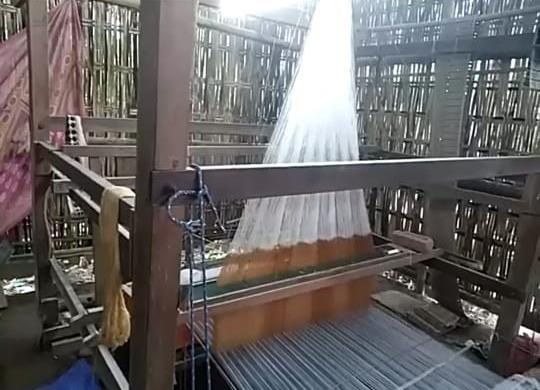
Figure 75 Design cards mounted on the loom for creating motifs
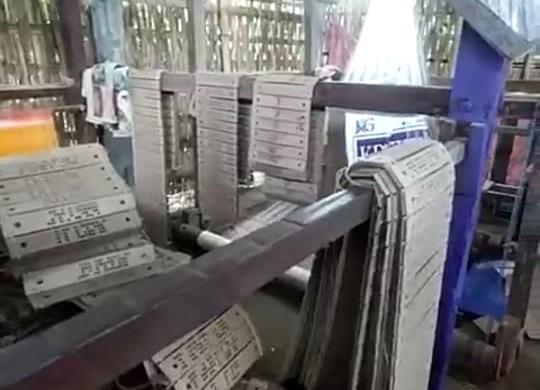

Figure 76 saraity loom
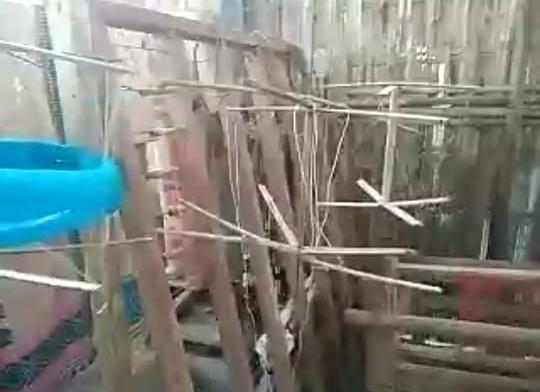
Figure 78 saraity loom
Figure 77 saraity loom
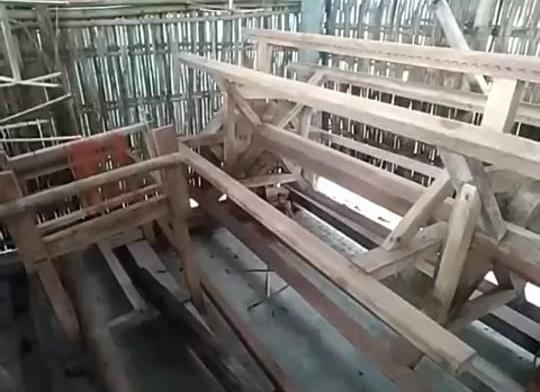
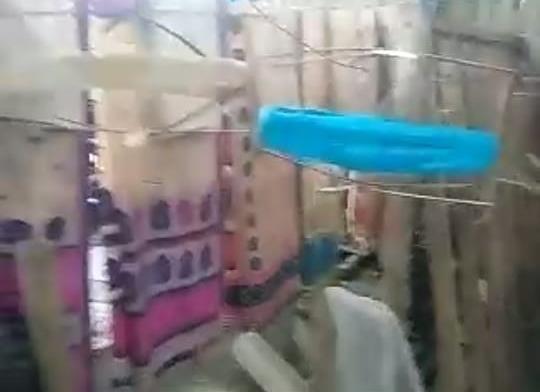
Figure 79 saraity loom
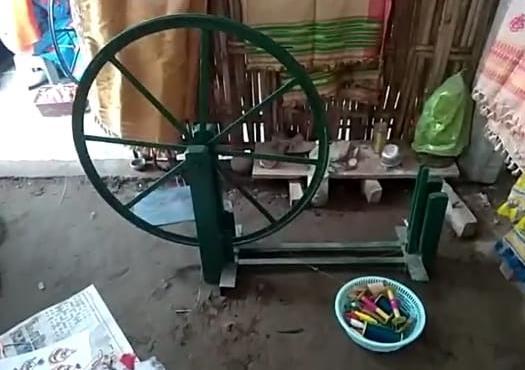
Figure 80 Jatar
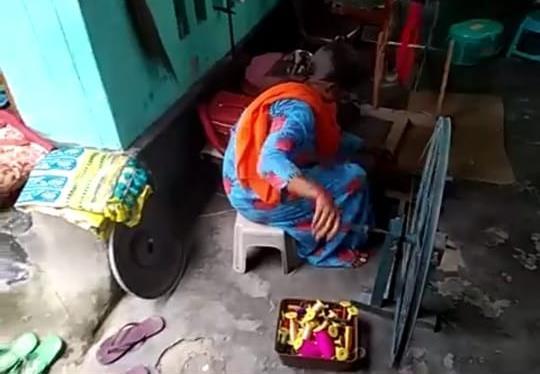
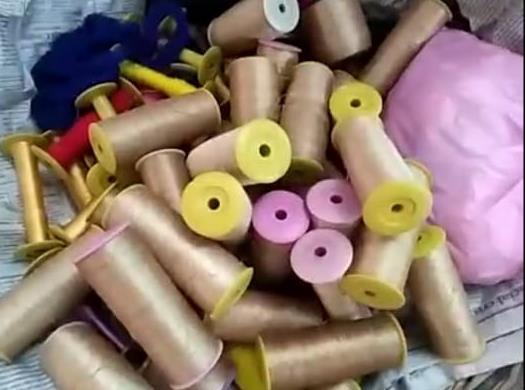
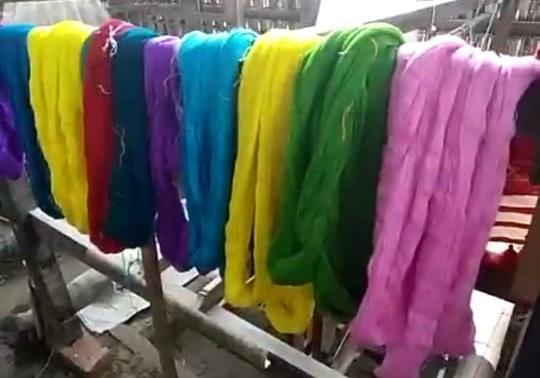
Figure 82 Muga bobbin Figure 81 artisan working on jatar
Figure 83 silk threads
Glossary
1. Bani - silk used to weave the horizontal patterns 2. Bao - frame to which the thread is inserted one by one after placing in noarah. 3. Chador – shawls 4. Deregi – the tool used for spinning 5. Dhangori – traditional bamboo tool is used in the boiling process 6. Dhi - vertically woven silk threads that forms the base of the garment 7. Dholbiri - Assamese jewellery 8. Gacha – a tree motif
9. Gomkharu – Assamese jewellery 10. Golap – the rose (motif) 11. Japi - traditional headgear which was used by females of noble and rich families 12. Joonbiri - Assamese neck piece like crescent moon 13. Kalaktine – the smaller bamboo frame into which the thread is again spun 14. Karbi – a motif 15. Kalki – a motif in the shape of mango 16. Kaziranga – name of a motif which is most commonly used 17. Kesh Bosa - very simple and basic motif like stripes 18. Kinkhap - motif style which is inspired from the Ahom dynasty 19. Loka paro - Assamese jewellery
Glossary
20. Makoups - bigger frame used for weaving designs and motifs 21. Mekhela - long piece which is draped from the waist downwards 22. Mekhala chador – traditional assamese costume
23. Moaharah - small spool inside a small wooden frame 24. Noarah - wooden bar of the loom 25. Padum – the lotus (motif) 26. Phool buta – motif that represent nature or flower 27. Pokhila - butterfly pattern which is often woven in different shape 28. Rashk - comb like a frame
29. Riha – female upper garment worn by married women 30. Saraity – bamboo around which the silk thread is spun 31. Sokori – the moths used in rearing of Mugha silk 32. Ughasereya - huge frame in which bobbins are placed 33. Zator - spinning wheel
Origin
Assamese tradition traces the origin of its famed silk back to the 3rd century BC, to a political literary work called Arthashastra by Kautilya. It talks highly and is full of praises for the sophisticated silk cloths from Assam and goes on to describe its fibres as 'the colour of butter', 'as red as the sun', and 'of supreme quality'.
Historical records such as those by Huen Sang and Banabhatta spoke in detail about the silk route that passed through China, Tibet and Burma to reach Assam, and brought the knowledge of sericulture and silk trading along with it. The major centre for this silk trade continues to be the weaving town of Sualkuchi located in the Kamrup district of western Assam.
Ruled by the Pala Dynasty's King Dharma Pala from 900 to 110 AD, legend has it he about 26 silk weaving families and created a weaving village here, close to current day Guwahati. Although this weaving village rose to fame during the Ahom rule.
History:
Legend gives credit for developing silk yarn to a Chinese empress, Leizu (Hsi-LingShih, Lei-Tzu).Those silks were originally reserved for the Emperors of China for their own use and gifts to others, but spread gradually through Chinese culture and trade both geographically and socially, and then to many regions of Asia.
The Ahom reign (1226 AD-1828 AD) was the golden period of Muga culture in Assam though the origin of world famous muga silk fabric is not so clear yet it was produced only in the handloom weaving industries of Assam, India. The first official record of muga silk worm relates to 1662.
In the epic Mahabharata, Assam is called Suvarnakanakanan, meaning the silk producing province. It is known from the History that king Bhagadutta of Assam had took part in the bottle of Kurukhetra wearing a muga dhoti.
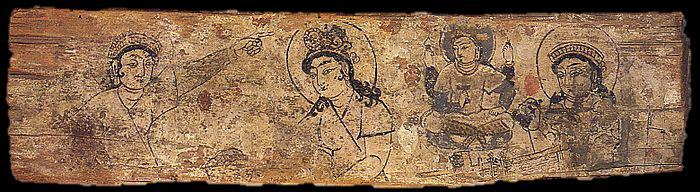
Location
Assam is well known for the production of high quality silk since ancient times .
In Assam, the craft of weaving goes along with the production of silk.
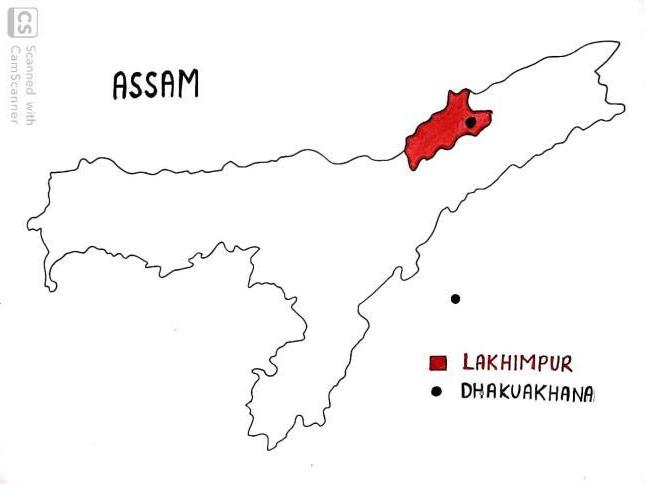
Assamese silk can be categorised into 3 types based on its production, being Muga Silk, Eri
Silk and Pat Silk.
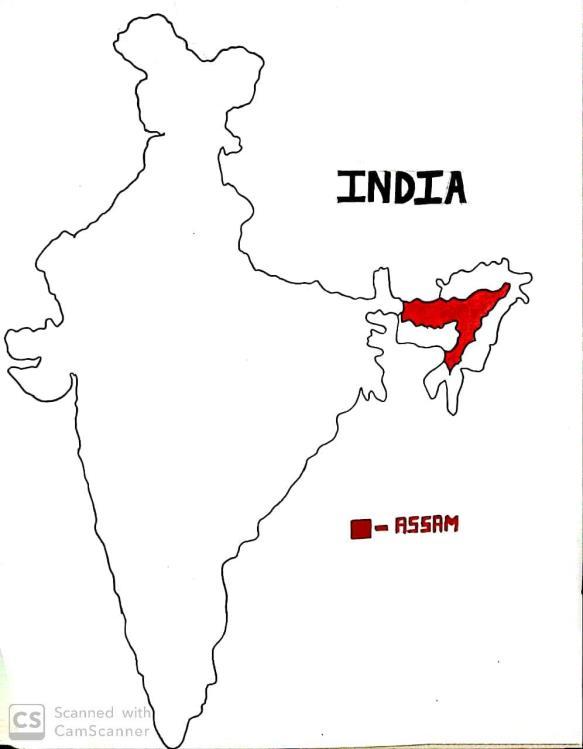
Assam Contributes 95% and 65% of country’s total Muga and Eri production respectively.
Assam
LAKHIMPUR DHOKUWAKHANA
India
ASSAM
Muga, revered in Assam is globally famous as ‘Assam silk’ .Sericulture and silk weaving is an ancient agro-based industry of Assam .Rearers have been rearing muga silkworm traditionally since time in memorial .Lakhimpur district has a leading position in production of muga silk. Dhakuwakhana sub-division of Lakhimpur district, a flood affected area of the state, is known as the land of Muga culture of Assam.
Muga silkworm rearers of this area have been conserving this culture traditionally in generations and it has the biggest share of their annual income.
Muga silkworm is reared in the host plant called Som found abundantly in this region of Assam. It is estimated that one hector Som plantation could produce a harvest of two lakhs Muga cocoon in a year
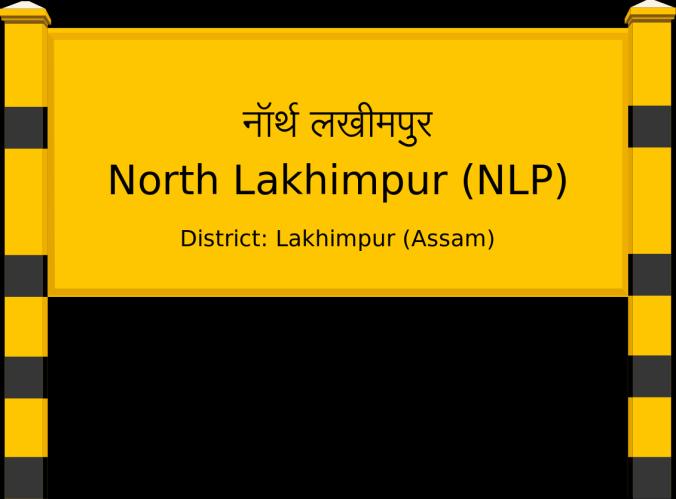
Climatic requirement for Muga rearing
The uniqueness of Muga from Assam is because it can only grow in a certain temperature that is only favorable in Assam.
The muga silkworm performs best in the temperature range of 25-27 °C and humidity of 75-85 percent.
Generally a temperature range minimum of 15 °C and a maximum of 33 °C is considered as the range of temperature suitable for muga silkworm rearing.
The Karha-Charikaria-Champara river basin area of Dhakuwakhana subdivision of Lakhimpur district is a traditional Muga silkworm rearing zone that has the potentiality of transforming the livelihood condition of thousands of rural population while contributing considerably towards preserving the biodiversity of the state.
Dhakuwakhana sub-division of Lakhimpur district is also one of the worst affected areas of Assam’s annual flood havoc. Muga culture is suitable for flood affected areas as it provide smooth livelihood for the affected people.
It also checks land erosion and proper exploitation of barren and wasteland. The host plants of Muga silkworm are integral part of rainforest vegetation. Thus Muga culture is unique for sustainable conservation of environment and biodiversity.
Products
Mekhela Chador , a type of Saree comprising two pieces of cloth, draped on the top and bottom, which is the traditional attire worn by the women of Assam .
Riha is part of a three piece Assamese traditional garment worn with the Mekhela chador. It forms a part of the bridal trousseau for most Assamese brides these days
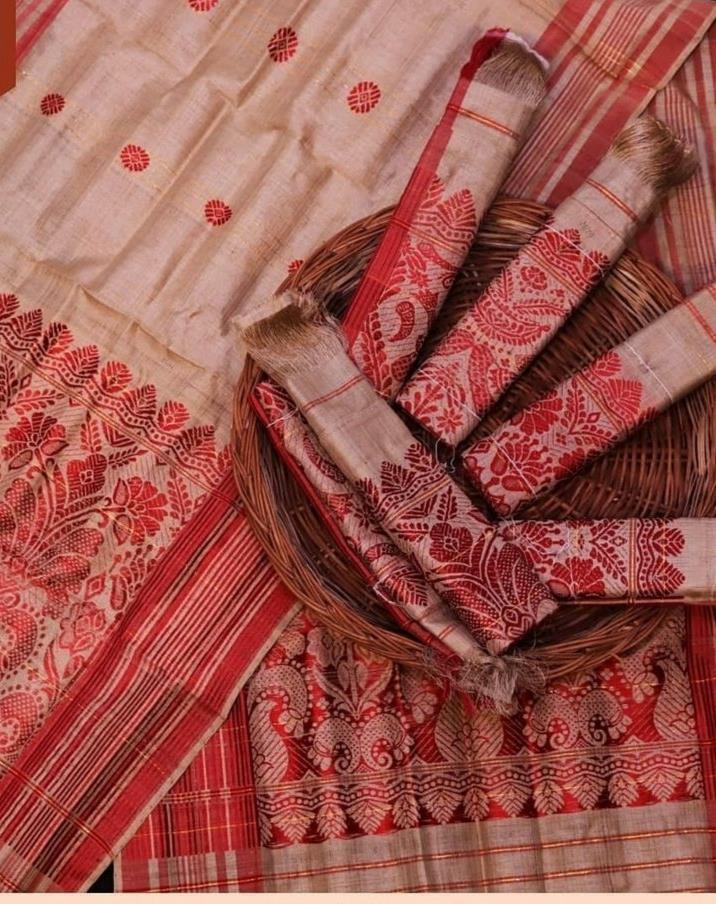
Muga silk stoles known as Gicha are also worn by the people of Assam
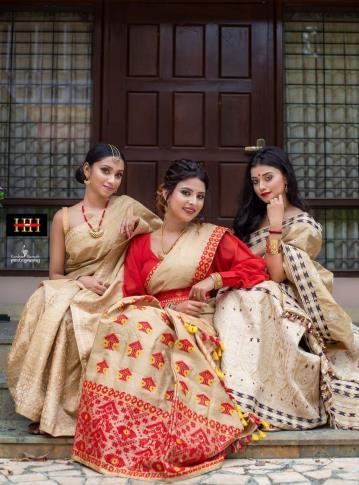
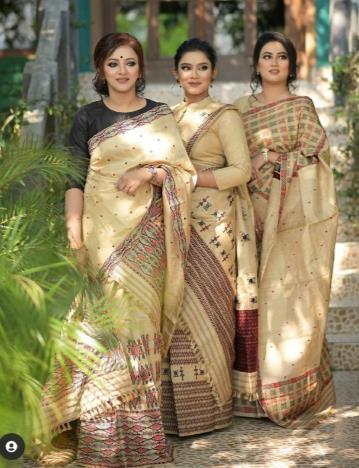
Costumes
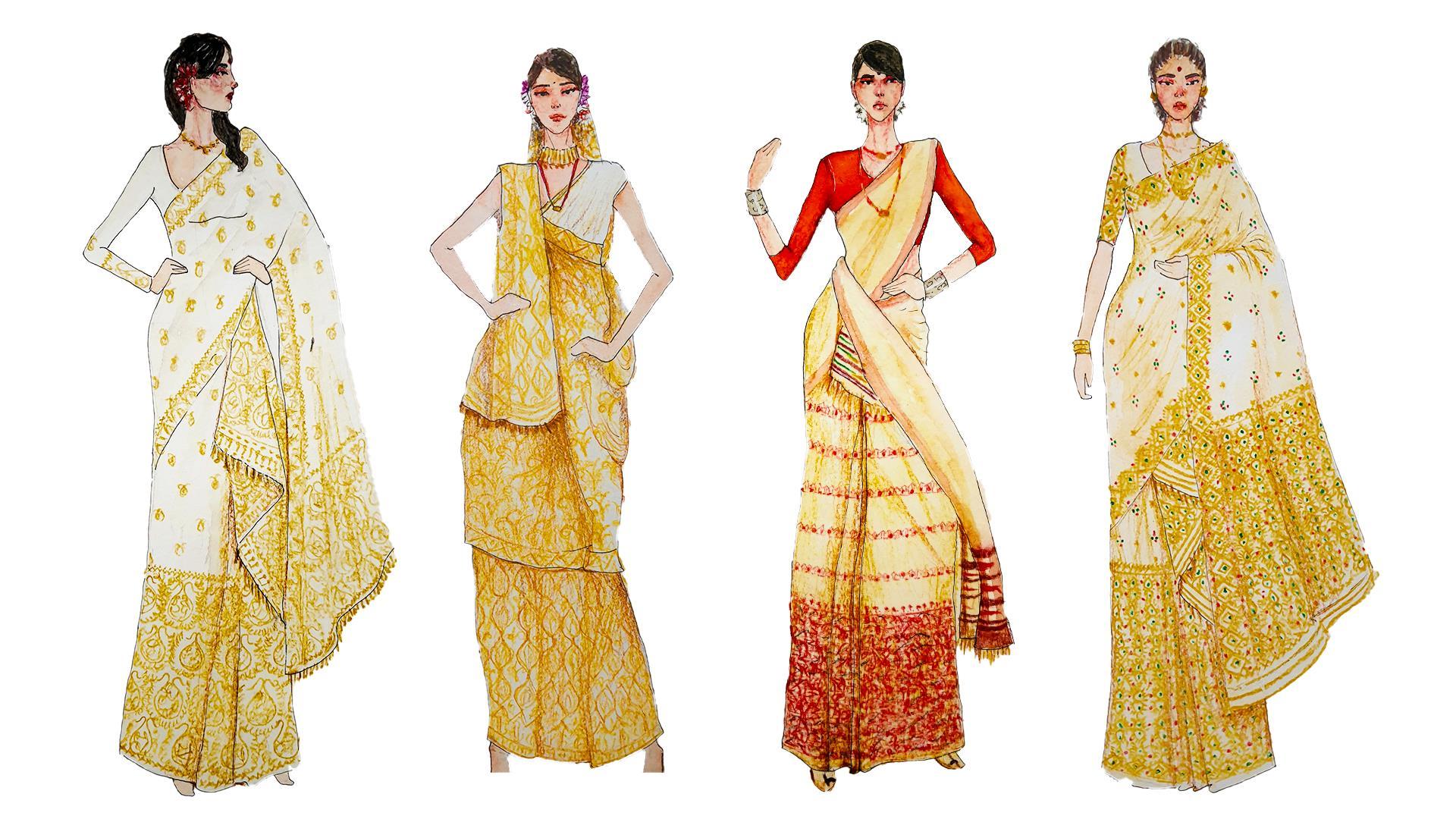
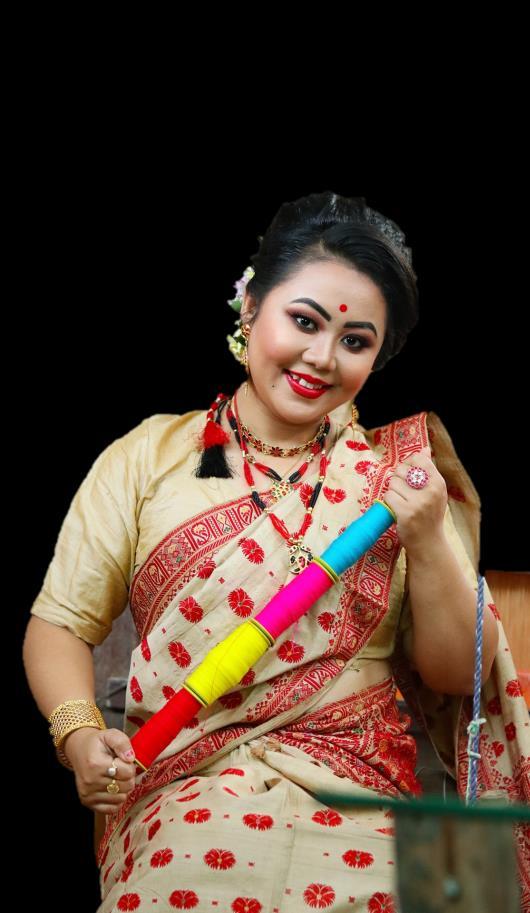
Muga the most expensive silk known as golden silk
This Muga silk is used to make different kinds of chador( shawls), Sarees, scarves and many other garments
Mekhela Chador is worn by women of all ages, Chaddor is a drape, mekhela is stitched(garment)
It has a long piece which is draped from the waist downwards and then folded into pleats and tucked in. This part is called Mekhela
The Upper part of the dress is the chador, that is also a long piece of fabric which is draped on one side, pleated and kept over the shoulder while the other end is tucked into the waist after being draped around the body.
A tool called Deregi is used for the spinning
Riha is another important female upper garment and only worn by married women. Also known as kachali, it was mainly used for breast coverage before blouses were introduced. It was made of silk, muga and endi.
Wearing of riha along with mekhela and chador is associated with decency and modesty in Assamese culture.
Riha with its distinctive mode of wearing, makes the dress of an Assamese women graceful. It is an important item of bridal attire. It is also much valued as an item of dress of married women on ceremonial occasions and also used in Bihu dance attire.
It was worn around the waist and reached till the ankle joints. It was worn in combination with a chador. Generally, mekhelas were woven from cotton, muga, eri and silk yarn. When it was wrapped around the breast and reached down to the knee
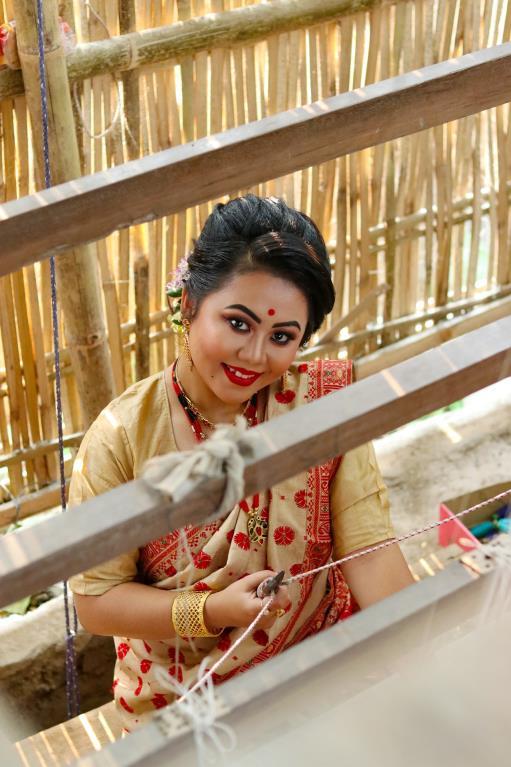
Life Cycle “ Larva/ Muga polu: Period of 8-12 days, it goes on top of the gauze and start eating leaves and its growth is dependent on the climate For 20-50days they mature into cocoons, the mature worms are Process collected into a bamboo basket and then layed out on a jaali. The rearers have their hands full all the time. Like other larvae, muga silkworms eat voraciously, 1000 silkworms need one big tree or two medium-sized trees during their entire larval period. Once they mature, they crawl down to the foot of the tree and start spinning their cocoons. Rearers then collect them and place them in baskets of dry leaves allowing them to complete their cocoon spinning process. Takes 18 days during summers and 30 days in winters for a cocoon to transfer to a moth The moths are known as sokori The body of a male moth is 3cm and female moth is 3.5cm in length
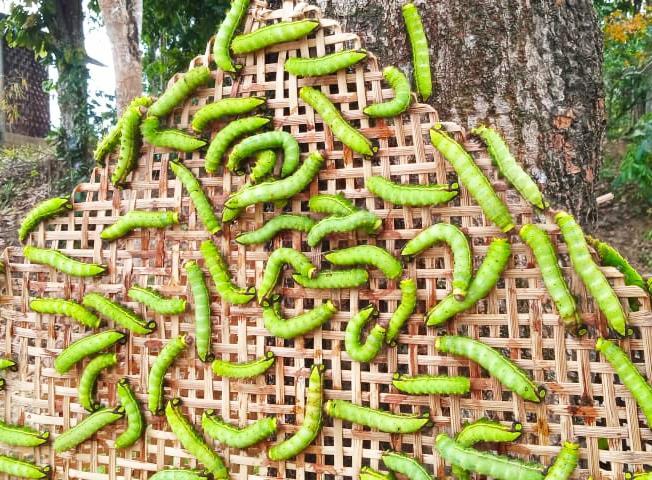
9. The process of metamorphosis occurs
10. Before the pupae emerge out of the cocoon and metamorphose into a silk moth, they are stifled by boiling or heating to prevent them from cutting the cocoons. In mulberry silk, this makes it possible to reel in the threads, otherwise, filaments from cut cocoons cannot be reeled.
11. The Degumming process starts, here the cocoons are boiled in water for 15 – 20mins, where the filament is separated from the cocoon.
12. They are also sun-dried
13. The bamboo traditional tool is used in the boiling process is called
Dhangori
Once the filament is separated from pupa after Degumming, we get the fine muga filament.

Tools and equipments
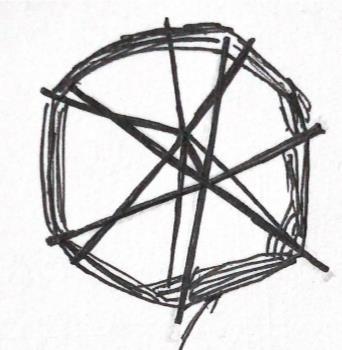
Spindle Saraity
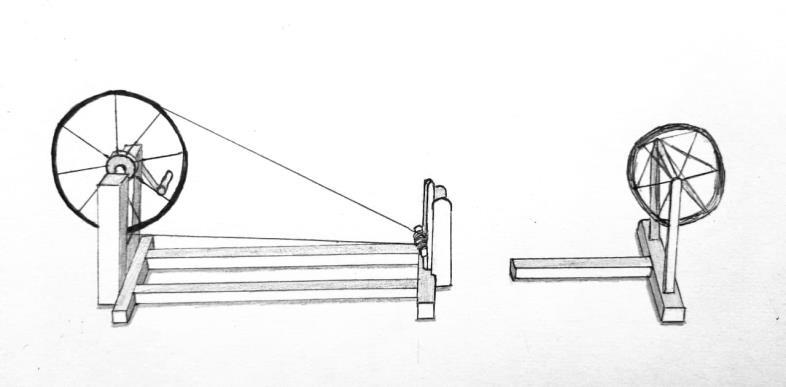
The loom is basically classified into two – the vertically woven silk threads that forms the base of the garment is called
Dhi and the silk used to weave the horizontal patterns are called Bani The woolen threads are used to weave patterns and motifs . The muga silk thread is spun around the bamboo instruction called Saraity The saraity has small bamboo sticks attached on its side and one bamboo stick coming at the centre The process is done to remove the knots or uneven fibres of the thread The thread is again spun into a smaller bamboo frame called Kalaktine in local language . Later , the thread is again spun into a smaller bamboo frame then transferred to a spool called bobbin frame . It is performed using a spinning wheel called zator . Zatoring is once single handed by a person who spins the thread into the wheel with one hand while warping the thread into the spools with the other hand
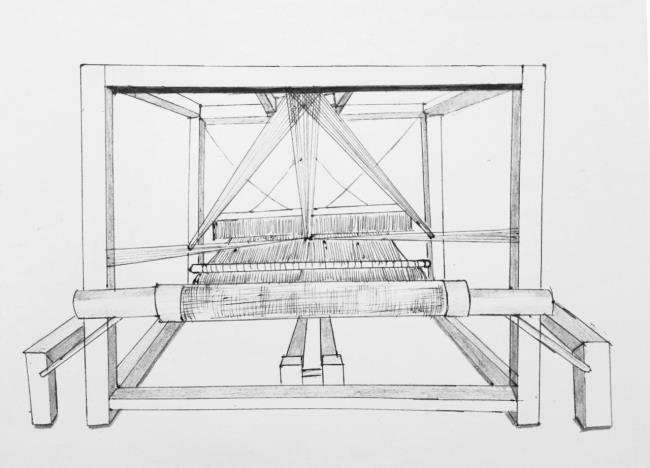
Loom Warping Drum

After the thread is woven into such number of bobbins , these bobbins are then placed on huge frame called Ughasereya The thread from each of these bobbins placed on the Ugha is spun around a huge wooden quill called wrapping drum The spinning enables the weavers to get the exact size and length of the Muga silk garment that is to be woven on the loom The thread is very systematically taken out from the wheel and placed on the wooden bar of the loom called Noarah The rethread from the wrapping drum is slowly taken out systemically and slowly encircled around the noarah . This is done with the edge of a sharp by loom tool is inserted at the end of the knots Once the thread are placed around the noarah system of the deli the loose thread will be inserted one by one into a frame called the bao . This system is done with a lot of precision and these threads are then inserted into a comb like a frame called the Rashk These threads are then again taken by the weavers to weave the garment
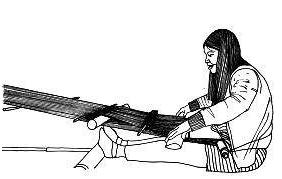
Loin Loom
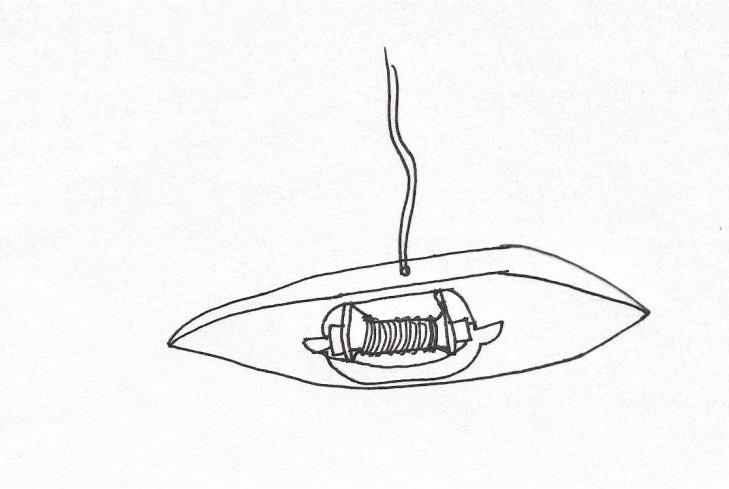
Manual Shuttle
• As the rethread is placed on the noarahs and the bani thread is placed on the small spool inside a small wooden frame called moaharah
• The small makoups are used for weaving designs and motifs . The mouharah is again placed on a bigger frame called the makoups at the side of the loom .
• The colourful threads from the mouharah is then woven into flowers , motifs , patterns on the rethread and which forms the entire base of the garment
• This weaving process is the process of interlacement of warp and weft – vertical and horizontal set of yarns
• The fabrics which are weaved on handloom are known as handloom crafts .
• Handloom is a loom that is used to weave fabrics using hands
• The foot paddle is pressed to lift the respective feeter according to the weave planned and is said to be times which throwing the vertical or weft yarns across those sections of weft yarns
• Weavers continue to weave for long hours in a day from morning 7 o’clock till 8’o clock
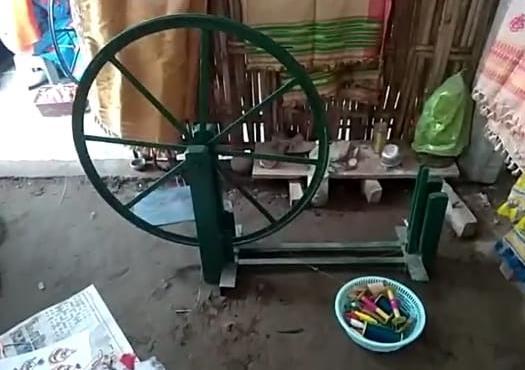
Jatar
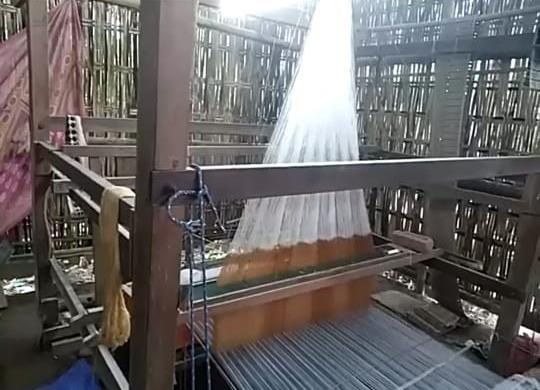
Jewellery and ornaments
Assamese traditional ornaments . The gomkharu is a major part of traditional Assamese attire . Assamese ornaments are one of the most important part of the Assamese culture . It is generally made from gold termed as Kesha xoon or raw gold and it is very beautiful and prestigious part of Assamese culture .
Some of the popular tradition Assamese ornaments or Asomiya Gohona include earrings with exquisite
Lokaparo , Keru , Thuriya , janghpai long keru , makori , golpata , satsori , joon biri , dhol biri , doog doogi , biri moni , mukuta moni .

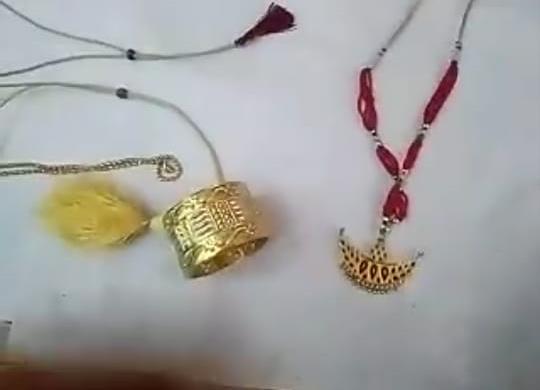
▫Qualities of muga silk yarn: Muga is a natural protein fibre possessing many of the unique qualities such as strength, sheen, high resilience, drap ability, anti- flammable, anti bacterial above all UV protection property (85.08%) useful for human being.
▫Longevity : Longevity is one of the major highlights of Muga Silk. It is said that generally a
Muga silk fabric outlives the wearer. ▫ Tensile strength and elongation ▫ : The presence of alanine and serine makes the fibres strong and resistant to breaking. The breaking strength of Muga silk is 4g/denier and its elongation is about 20%. Its tensile strength is due to the many interceded hydrogen bonds, and when stretched the force is applied to these numerous bonds and they do not break.
Properties of muga silk yarn :
▫Luster: It has got a natural golden luster and the intensity of luster of muga silk increases with age. Most importantly, it does not need any dyeing to be done, it is still quite compatible with most dyes. ▫ Resilience: Muga Silk is known for its resilience. It can be given a fine texture by ironing it in a damp state. Moisture absorbance: Silk can absorb moisture that is why it is comfortable to wear in warm weather also. ▫ Eco-friendliness: It is organically produced and the strongest natural fibre with natural golden colour. Effect of Acid/alkali : Silk is resistant to most mineral acids, except sulfuric acid (H2SO4), which dissolves it. It becomes yellow with the contact of perspiration. ▫ Sheen of muga silk: Slight colour variation of Muga silk depend, on the time of the year of its production
Design
Karbi
Pokhila
Phool buta
Motifs
Motifs in a general way is divided into five broad categories, viz, naturalistic, stylized, geometric, abstract and structural. Naturalistic designs are those that are drawn from flowers, leaves, plants, animals, landscapes etc. The motifs are kept realistic to provide an authentic image of nature. Geometric designs are based on the true forms of circle, square, triangle, rectangle, diamond shaped etc. Endless variations and combinations of these basic geometric forms are used Flowers from the simplest and smallest configuration to those with welldefined petals are found in the textiles of Assam. The simplest floral motif found is a small circle or dot with short radiating lines on all sides. Padum (lotus) and golap (rose) are two flowers commonly found in the textiles produced traditionally in the region A variety of animal motifs like butterfly, peacocks, elephant, tiger, fish etc. cleverly adopted in stylized form with a minimum of lines occupy an important place in the textile design Loka paro, jon-biri, Dholbiri, Golpata, Japi, Pepa, Kerumoni, Dugdugi, etc are some of the traditional assamese jewelleries which influence the designs of the motifs used Some of the common designs, patterns and motifs are Kaziranga style, King khap style, Joon biri style, Karbi, Bodo, Mourah, Gach, Phool Buta, Bhagavat Sarai, Japi, Kalki,
and Pokhila
Kinkhap

Joonbiri • The tradtional assamese , Kaziranga motif is one of the most commonly used motif . The motif design is inspired from the wildlife of Kaziranga . As a part of the motif a rhino and deer are woven onto the garments . • The other style is the Kinkhap motif style , which is inspired from the Ahom dynasty and signifies the royalty and magnanimity of the erstwhile kingdom . • As the Ahom originally came from Thailand , the designs are largely inspired from the region . The design consists of two lions facing each other and it is believed that the traditional design consisted of rhinos and was later replaced by the lions by Ahoms in order to signify the royalty and power of the kingdom • In the Mekhala chador set , we can see the motif Joonbiri . This pattern woven on the garments is inspired from the Assamese neck piece called
Joonbiri
• Some other traditional ornaments of Assamese people are Joonbiri , Dugdugi , Maduli , Golpaka inspires various motifs in the garments • The shape of the Joonbiri is like a crescent moon and is engraved with a lot of patterns

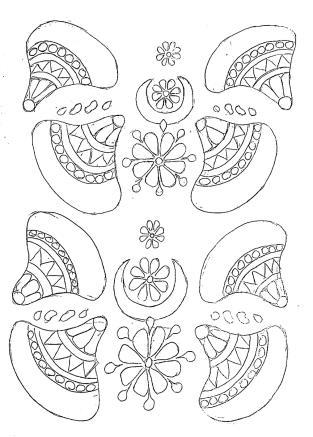
Japi
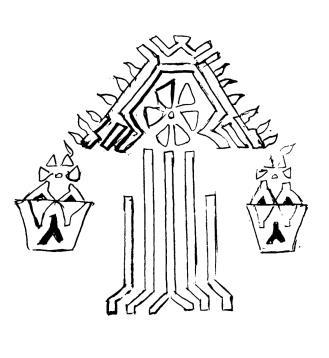
Gach • The japi is a traditional headgear which was used by females of noble and rich families but now serves as a headgear for farmers to protect them from rain and sun . • The japi motif is often found woven on traditional Assamese garments • Another motif patterns woven on mekhala chador , which is inspired by nature . The pattern of butterfly known as Pokhila in the local language is often woven in different shapes depending on the expertise of the weavers . • The motif is Phool buta , the pattern is a representation of nature . Flower or bunch of flowers are one of the most common motifs found in traditional Assamese garments • The weavers can weave the motif design combining 2-3 motifs with the combination of
Phool buta , pokhila and japi altogether . • Some of the motifs are in geometrical shapes .

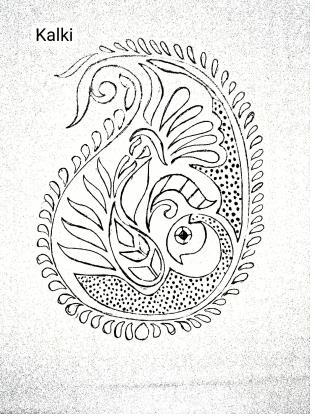
Assamese women wear Riha when they do Bihu dance . The motif seen is very simple and basic called kesh bosa , and is very commonly used in the textile and often used at the borders of the horizontal lines it also signifies the parallel line in order or women's brain The border line is in geometrical shapes and small phool buta with mourah . Mourah is the local language name for a peacock . The symbol of the peacock is very commonly woven into garments . The motif is called the Gacha in Assamese term . The gacha motif of the tree is one of the most common patterns found in Assamese traditional garments . The shape is often represented in a geometrical manner and the shape and design varies according to the expertise of the weavers . This pattern , called kalki is very popular in Assamese garments . It is in the shape of a mango .
Significance
Muga silk (Muga Paat) or the golden silk is not only a nature's gift to Assam, but also a symbol of rich Assamese culture. It represents the brilliance of traditional attire of the region. The most significant characteristic of 'Muga silk' is its golden bright hue.
Its name is derived from Assamese word 'Muga', which means yellow. The fabric is superior in every respect in comparison to the normal white silk that available all over the world. The silk is known for its extreme durability and has a natural yellowishgolden tint with a shimmering, glossy texture. It was previously reserved for the use of royalty .
Traditional rearers believe that muga silkworms are holy and that the rearing depends on the blessings of the gods. With regard to sericulture in Upper Assam, a number of proverbs exist, of which this may serve as an example: “Ahu kheti ahu kal muga kheti kopal val hali kheti korilei pai” . In English this means that ‘cultivation of rice depends on the season, but the rearing of muga depends on the fate of the rearer”
Market Channels of distribution
Muga rearer Reelers and dyers
Handloom weavers
PRIMARY PRODUCERS

Primary producers consists of the rearer to weavers
Home textile producers
Wholesalers Retailers
DOMESTIC MIDDLEMEN
Marketing channel is dominated by middlemen wholesalers and retailers in the domestic market
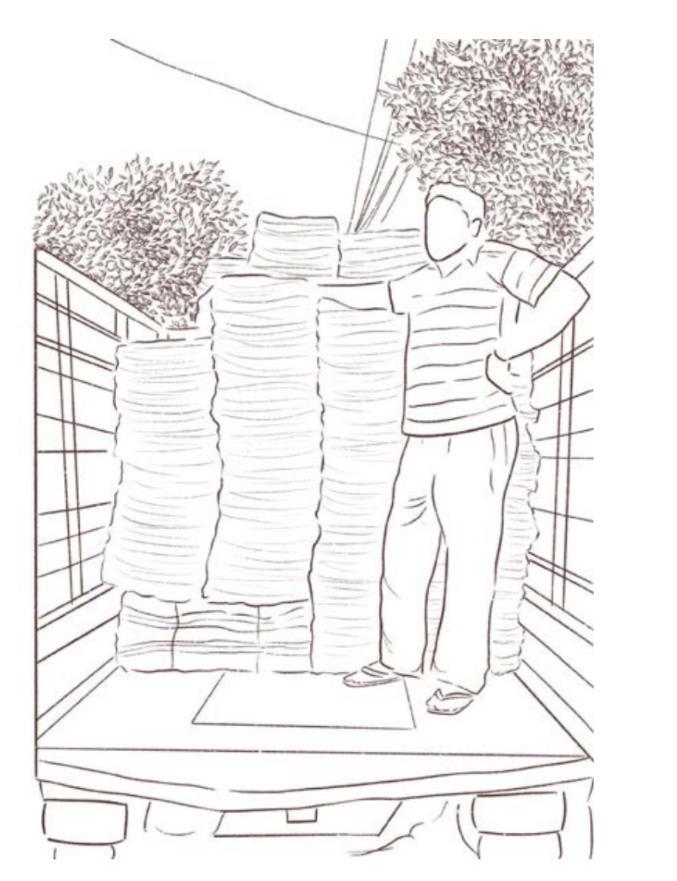
Market
For the sale of the products the weavers use all the possible options available to them –
▫ selling through wholesalers and retailers ▫ setting up stalls in exhibitions and fairs ▫ artisans even do door-to-door sales
CHALLENGES faced by artisans
• It is found that most of weavers are unaware of the latest designs. • The weavers are producing fabrics of obsolete design, no link to seasonal fashion forecasts, the looms has hardly changed leading to low productivity and overpriced fabrics, no change in product profile, low value addition resulting in subsisting wages, weavers are dependents on master weavers and there is no rewards for innovations and little opportunity to develop entrepreneurship. • Therefore there is always remaining a gap between the design preference of the consumer and the designs produced by the weavers. • Moreover, in traditional non-commercial areas it was observed that the weavers preferred throw shuttle looms having low productivity which is easier to operate and also cheap. • The weavers due to their poor economic condition cannot convert their looms to fly-shuttle one. • Quality raw materials aren’t available to the weavers to participate in an evolving market economy and to break out of the subsistence production cycle. • The loom owners of Assam are getting a readymade domestic market for their products. • But there is no proper marketing channel for displaying and selling the products outside the state, particularly ‘Sarees’, which could get a good market in the national arena.
STRENGTHS SWOT Analysis
WEAKNESSES

1) Availability of raw materials. 2) Availability of artistic, well trained and skilled weavers. 3) Muga Silk is found only in Assam, nowhere else.

S W
1) Hand woven so it becomes time consuming.
2) Less people are interested to learn and engage in the craft
OPPORTUNITIES
1) High demand for good looking products, can be sold outside through online medium.
2) Introduction of internet portals for selling silk products.
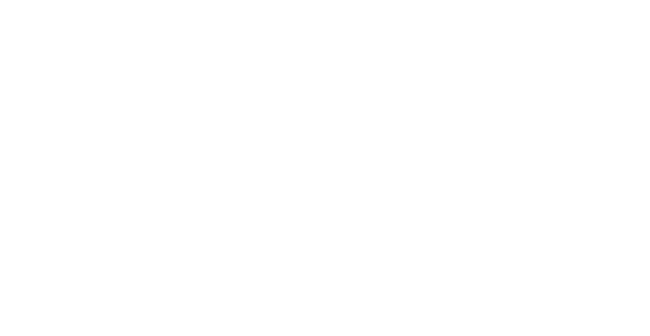
O T
THREATS
1) Global warming, natural calamities and climate change is becoming unsuitable for silkworms farming.
2) Tough competition from cheaper alternatives counterfeiting
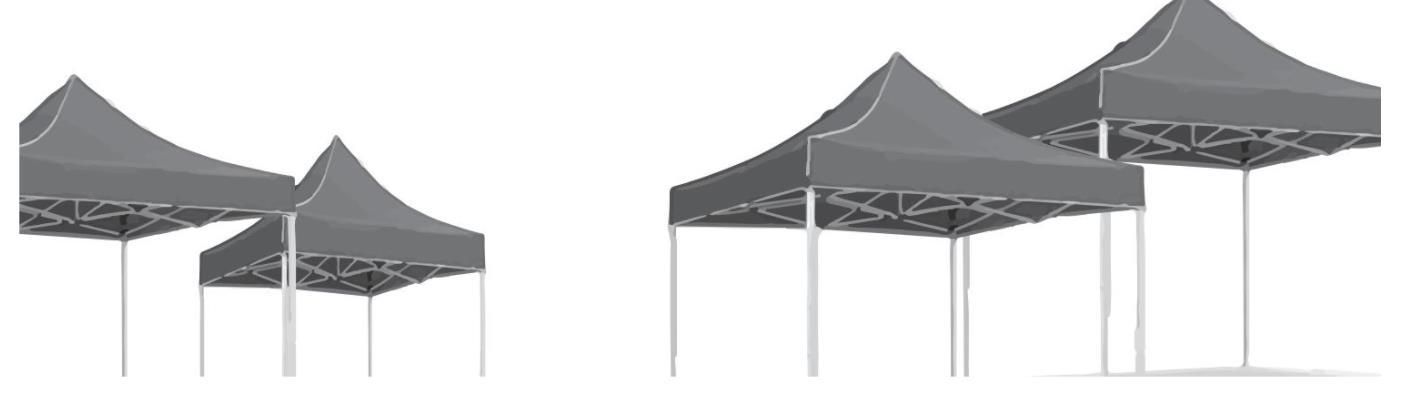
Suggestions:
There should be an equal focus on sarees and other apparels that are popular in the markets outside Assam.
Use of modern technology in the handloom units.
More awareness for technology and government policies should be spread among weavers and retailers.
Government should set up the price regulation mechanism
More fashion Institutes and brands could be set up in the region so that the weavers and traders get the national exposure and necessary platform.
Conclusion
It is popularly believed that the identity of Assamese culture is solely stands on three pillars—Assamese language, the Bihu and Muga Silk. A loss of any one of these would endanger the very essence of the Assamese culture. Therefore Muga culture is inter-related to the cultural identity, livelihood and ecology. The state government should seriously consider in declaring the Dhakuwakhana region as traditional Muga rich zone of Assam.
Although the Assamese handloom silk industry has its demand in local, national and international markets but there are certain factors which are responsible for the non-fulfillment of the demands of Assamese silk in the market. These may include the lack of diversification of the products, non-acceptance of technology, dwindling laborers‟ and the lack of modern financial practices among many others. It appears that the GI tag given to the uniqueness of the silk is able to give the Muga silk its identity of being different. But most of the people associated with the industry i.e. weavers; retailers and consumers had already good idea about this type of silk and its characteristics, advantages. Further, competition can take many forms in the form of Benarsi silk producers making better quality products at a lower price is hurting the local producers and no specific law is in support since it is a fair competitive market. Hence, it can be concluded that mere GI certification does not reap into to direct benefits to any one individual or community, one needs to constantly focus on innovative techniques and business practices in order to flourish the centuries old tradition.
REFRENCES
https://india.mongabay.com/2018/02/assams-muga-silkworm-battles-climate-change/ https://www.sundarisilks.com/blogs/article/silk-stories-from-assam
http://www.ijstr.org/final-print/apr2020/Muga-Silk-Rearers-A-Field-Study-Of-Lakhimpur-District-Of-Assam.pdf
https://nenow.in/north-east-news/dhakuwakhana-muga-rich-zone-north-east.html
https://vikaspedia.in/agriculture/farm-based-enterprises/sericulture/sericulture-in-india
http://inserco.org/en/types_of_silk
https://i.pinimg.com/originals/b2/03/db/b203db5f437d5e87048e1fe387670149.jpg
https://www.dsource.in/gallery/motifs-silks-assam
https://globaljournals.org/GJHSS_Volume12/2-Handloom-Weaving-in-Assam-Problems.pdf
https://hrdc.gujaratuniversity.ac.in/Uploads/EJournalDetail/29/1044/9.pd
https://www.magicalassam.com/2019/01/mekhela-chador.html
https://en.wikipedia.org/wiki/Muga_silk
• https://www.utsavpedia.com/attires/simplicity-and-beauty-at-its-best-mekhela-chador/
• https://hts.assam.gov.in/frontimpotentdata/uses-of-silk
• https://www.eje.cz/pdfs/eje/2013/02/26.pdf
• https://www.sundarisilks.com/blogs/article/silk-stories-from-assam
• https://link.springer.com/chapter/10.1007/978-981-10-0620-3_17
• https://nenow.in/north-east-news/dhakuwakhana-muga-rich-zone-north-east.html