
3 minute read
How we used biosynthesis to produce the world’s strongest antioxidant
Maxim Mikheev, BIOMEDICAN
A B
Advertisement
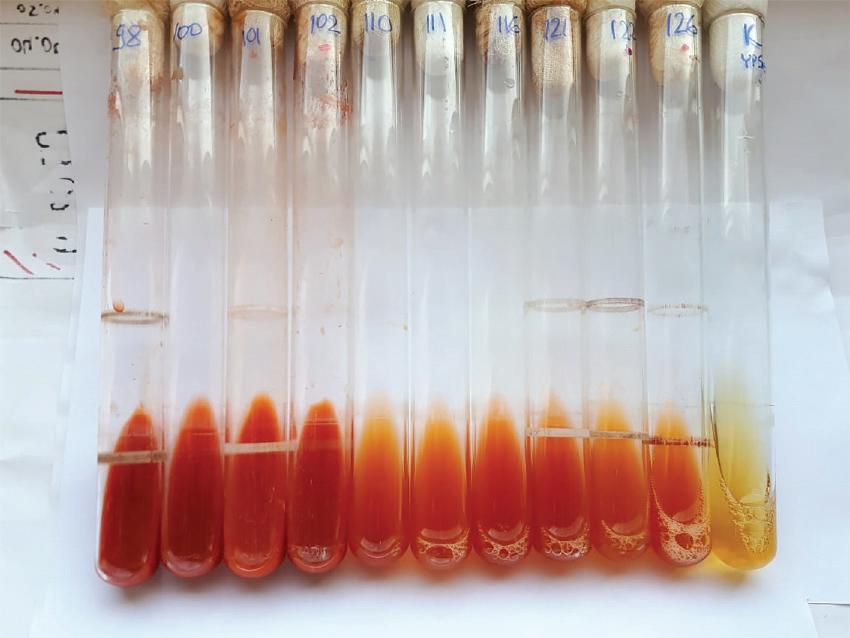
D E
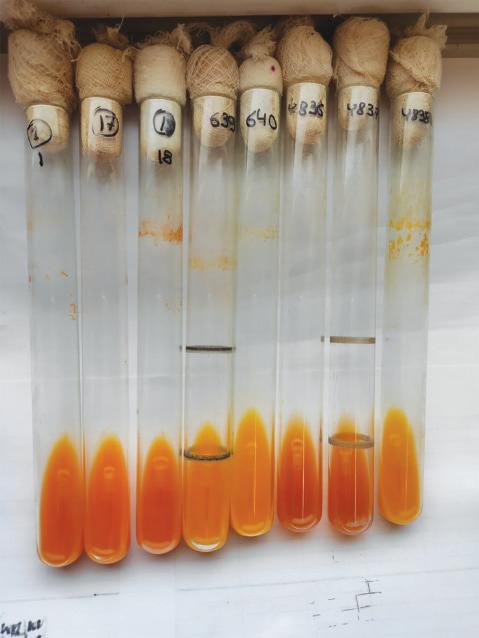
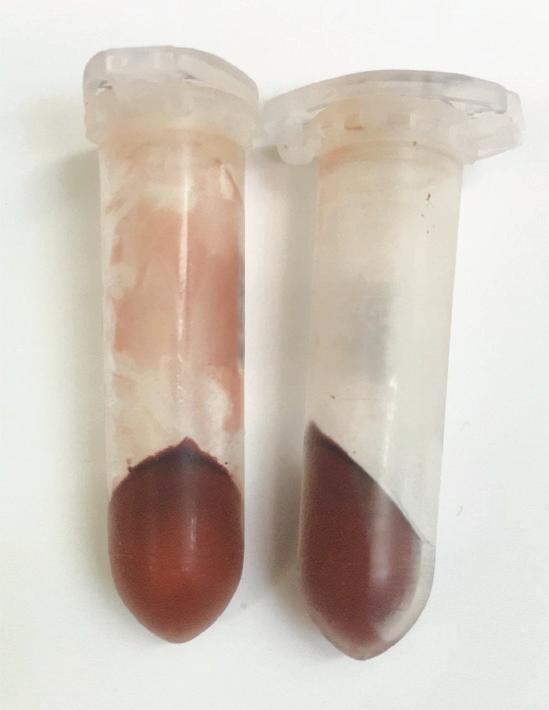
Figure 1. Summary of product development, from the beginning to production-ready strain. A) Initial red colonies. B) Improving carotenoids production. C) Scaling up production. D) Crystals inside cells contain 70% astaxanthin, 17% beta-carotene and 10% of canthaxanthin. D) Final biomass.

Biomedican entered into the astaxanthin market to diversify its products and show that its biosynthesis platform can target any high-value compound that has a significant market. There was a need to do something new so that we weren't overly concentrated on just the cannabinoid market.
After several days of intense research, we found a strain producing beta-carotene with a very high yield. After a not-too-long analysis, we found that by adding just a few genes, we could convert betacarotene into astaxanthin. Now, we’re able to produce a biosynthesized, non-GMO, organic astaxanthin molecule that is identical to what is found in nature.
Astaxanthin is a high-value compound. It is the strongest natural antioxidant in the world. It is 6,000 times stronger than vitamin C and 550 times stronger than vitamin E. Astaxanthin’s estimated market was $1 billion in 2019.
The astaxanthin market consists of fish feed, animal feed and human consumption. Astaxanthin is heavily used for salmon farming. Wild salmon has a pink color due to the presence of astaxanthin inside. Astaxanthin is naturally produced by some alga, yeasts and bacteria. Then zooplankton, krill and shrimp consume the initial astaxanthin producers. Later, salmon eat krill and shrimp, accumulate astaxanthin, and get their pink color in the natural environment. Astaxanthin is necessary to maintain the natural color of farmed salmon. In order for farmed salmon to have the same pink color as salmon found in the wild, they must be fed astaxanthin. This compound also serves as a chicken food supplement, adding a deep yellow color to egg yolks.
Salmon farms are currently using chemically synthetic astaxanthin. Synthetic astaxanthin is not identical to natural astaxanthin. Synthetic astaxanthin has a different molecular shape (stereoisomers) than its natural counterpart. The natural astaxanthin contains the only all-trans form. There are three main forms (3S, 3’S), (3R, 3’R), (3R, 3’S), with the most dominant being (3S, 3’S). Synthetic astaxanthin contains more than 500 stereoisomers.
The current regulations have forbidden direct consumption of synthetic astaxanthin by humans, but it is permitted to use as animal/fish feed. It was shown that synthetic astaxanthin has no health benefits and significantly weaker antioxidant properties.
Developing a natural form of astaxanthin
We decided to produce a natural form of astaxanthin using biosynthesis. Biosynthesis of astaxanthin eliminates the production of undesirable stereoisomers, allowing for the specific creation of astaxanthin found in nature. The process works through proprietary yeasts that undergo fermentation to consistently produce large quantities of high-quality biosynthetic astaxanthin, identical to its natural counterpart, at the same economical price as chemical synthesis.
We made an analysis of genes and some standard genetic designs last March. We ordered a gene synthesis by Twist Bioscience. One month later, we received a set of constructed genes optimal for biosynthesized astaxanthin. In summary, from the beginning (Apr 2020) to a production-ready strain (Sep 2020) took six months (Fig. 1).
Conclusion
BIOMEDICAN can produce a biosynthesized astaxanthin product that is non-GMO, organic, and identical to what is found in nature. We can do this at 90% less cost than the current chemically synthetic product. The chemically synthetic product is less than ideal because it produces byproducts, toxins, and contaminants. Thus, there is great interest in biosynthesized astaxanthin. The largest buyers of astaxanthin are looking to change from chemically synthetic products to non-GMO and organic products that are significantly more bioavailable for humans and animal feed.
C
More information: Maxim Mikheev
CEO and Founder BIOMEDICAN E: max@biomedican.com
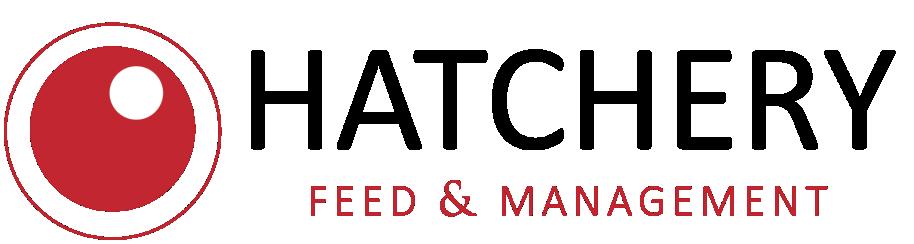
Expert international coverage of all the topics important to hatchery managers: systems, feeders, genetics, eggs, feed and nutrition, health and hygiene ... and more.
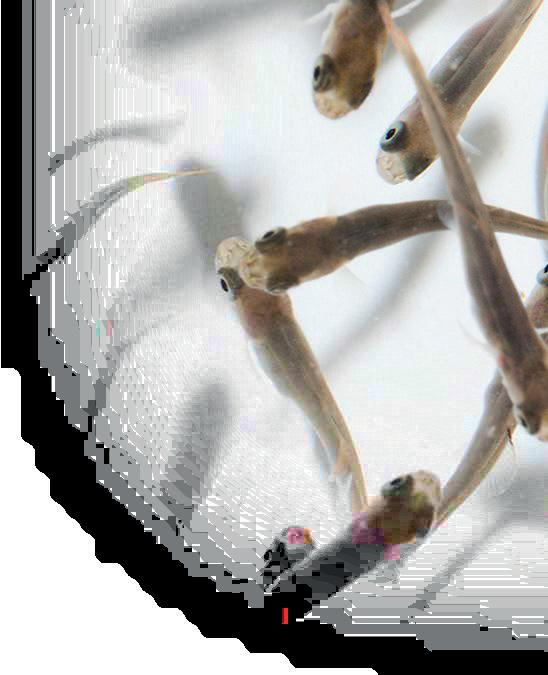
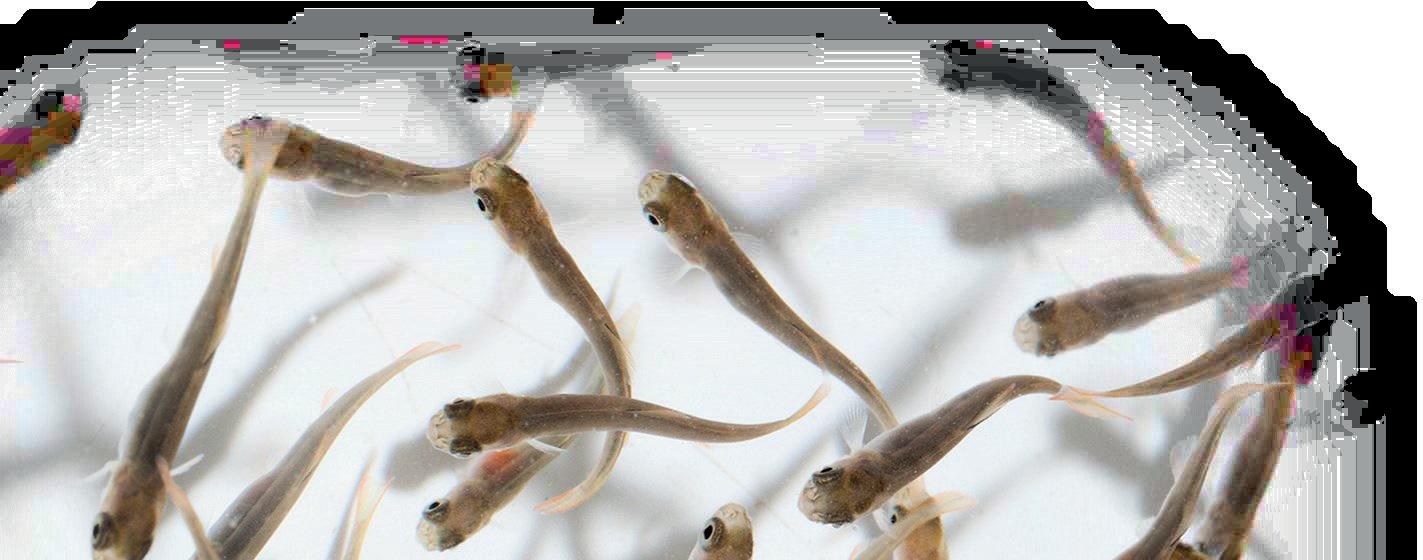
Subscribe to Newsletters & Magazines for free at HatcheryFM.com