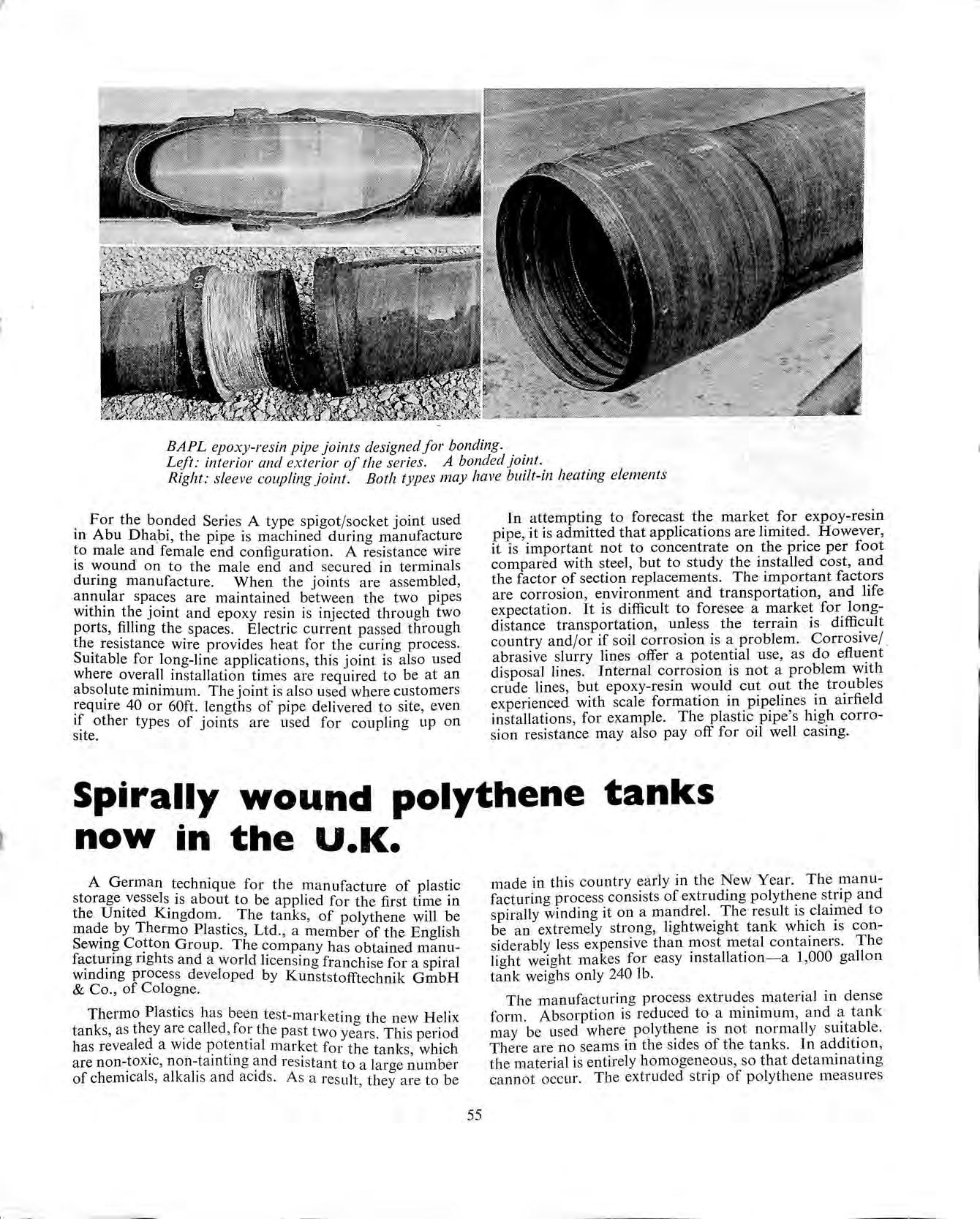
2 minute read
SPIRALLY WOUND POLYTHENE TANKS NOW IN THE U.K
by apeauk
BAPL epoxy-resin pipe joints designed for bonding. Left: interior and exterior of the series. A bonded joint. Right: sleeve coupling joint. Both types may have built-in heating elements
. For the bonded Series A type spigot/socket joint used m Abu Dha,bi, the pipe is machined during manufacture ~o male and female end configuration. A resistance wire is wound on to the male end and secured in terminals during manufacture. When the joints are assembled, a~m~lar sp~c.es are maintained between the two pipes w1thm th~ JOmt ports, ~lhng the and epoxy resin spaces. Electric is injected through two current passed through th~ resistance wire provides heat for the curing process. Smtable for long-line applications, this joint is also used where ove~al_I installation times are required to be at an abso!ute mrn1mum. ~equ1re 40 or 60ft. The joint is also used where customers lengths of pipe delivered to site, even if other Site. types of joints are used for coupling up on In attempting to forecast the market for expoy-resin pipe, it is admitted that applications are limited. However, it is important not to concentrate on the price per foot compared with steel, but to study the installed cost, and the factor of section replacements. The important factors are corrosion, environment and transportation, and life expectation. It is difficult to foresee a market for longdistance transportation, unless the terrain is difficult country and/or if soil corrosion is a problem. Corrosive/ . abrasive slurry lines offer a potential use, as do eftuent disposal lines. Internal corrosion is not a problem with crude lines, but epoxy-resin would cut out the troubles experienced with scale formation in pipelines in airfield installations, for example. The plastic pipe's high corrosion resistance may also pay off for oil well casing.
Advertisement
A German t _echnique for storage _vessels_ rs about to be the manufacture of plastic applied for the first time in the Umted Kingdom . . The tanks, of polythene will be mad_e by Thermo Plastics, Ltd., a member of the English Sewm~ Co~ton Group. The company has obtained manufa_ctu~·mg nghts and a world licensing franchise for a spiral wmdmg process developed by Kunststofftechnik GmbH & Co., of Cologne.
Thermo Plastics has been test-marketing the new Helix tanks, as they ar~ called, fo~ the past two years. This period has reveale~ a wide pot~ntial m ar~et for the tanks, which are non-_tox1c, non-_ta111t111g ~nd resistant of chemicals, alkalis and acids. As a res to a large number ult, they are to be made in this country early in the New Year. The manufacturing process consists of extruding spirally winding it on a mandrel. The polythene strip and result is claimed to be an extremely strong, lightweight tank which is considerably less expensive than most metal containers. The light weight makes for easy installation- a 1,000 gallon tank weighs only 240 lb.
The manufacturing process extrudes material in dense form. Absorption is reduced to a minimum, and a tank may be used where polythene is not normally suitable. There are no seams in the sides of the tanks. In addjtion, the material is entirely homogeneous, so that detaminating cannot occur. The extruded strip of polythene measures
55