
33 minute read
INDUSTRY NEWS: Current news from the Industry
from AMT OCT/NOV 2021
by AMTIL
AMTIL announces changes to Australian Manufacturing Week 2022 exhibition
AMTIL on 10 September announced changes to the schedule for next year’s Australian Manufacturing Week (AMW) exhibition, relocating and rescheduling the event from Melbourne in March to Sydney in June.
Amid uncertainty over the latest COVID-19 outbreak, the AMTIL Board decided in early September not to proceed with the AMW 2022 exhibition that had been scheduled to take place at the Melbourne Convention & Exhibition Centre (MCEC) from 8-11 March. With the Melbourne event not going ahead, AMTIL has instead confirmed that AMW 2022 will take place at the International Convention Centre Sydney (ICC Sydney), running from 7-10 June 2022. AMW 2022 in Sydney has drawn an encouraging show of support from the industry. Bookings for the show have been very strong, with 85% of the floorspace already sold. The decision not to proceed with the AMW exhibition in Melbourne in March was taken in response to the ongoing COVID-19 outbreak in Victoria and the resultant uncertainty over the viability of large public events so early in 2022. “The AMTIL Board made the very difficult decision not to proceed with the show in its current March 2022 timeslot,” said Shane Infanti, Chief Executive Officer of AMTIL. “Despite the great support we have for the exhibition from all our exhibitors, recent developments relating to the COVID-19 Delta strain have created an unpredictable environment that we felt had the potential to seriously jeopardise the event given that it is so early in the New Year.” Following the decision, AMTIL began moving forward in exploring plans for a rescheduled event to take place later in the year in a different location. The ICC Sydney was secured as a venue for AMW from 7-10 June. AMTIL is confident that by June the current COVID-19 outbreak will have been contained, and high vaccination levels will allow the staging of large public events. Infanti explained: “The AMTIL Board felt that the return of exhibitions is an important step in our COVID recovery plan and that there remains a very strong appetite for a show at some stage in 2022. We explored a number of options in regard to shows over the coming two years. “Running AMW in June at the ICC Darling Harbour would represent a return to Sydney since we last ran Austech there in 2012, and reflects strong local demand for a significant manufacturing event. We are confident that the COVID-19 implications for an event mid next year will be minimal.” Looking further ahead, AMW 2023 will also take place in its usual May timeslot in Melbourne, running from 9-12 May 2023 at the MCEC. Infanti added: “This is planned to be one of the largest exhibitions of its type in the Southern Hemisphere. We are truly excited to be bringing this to the Australian manufacturing sector. For both of these events, the industry can be confident of receiving the same great support and service that manufacturers have come to expect from AMTIL over 20-plus years of running trade shows.” Owned and operated by AMTIL, AMW is Australia’s premier manufacturing solutions event, an industry exhibition encompassing all aspects of manufacturing in Australia. Since 2000, AMTIL has operated Austech, Australia’s premier advanced manufacturing and machine tool exhibition, which going forward has now been incorporated into the AMW exhibition.
www.australianmanufacturingweek.com.au
Boeing, RMIT partner on space manufacturing capability
RMIT University and Boeing have entered a partnership at developing and growing Australia’s space manufacturing.
The partnership announced on 15 September involves projects on product design strategy, materials research and process innovation. These collaborations will harness global networks and expertise to develop local solutions for the manufacturing of space equipment. RMIT’s Advanced Manufacturing Precinct is a leader in the advanced manufacturing techniques required. RMIT Deputy Vice Chancellor for Research and Innovation, Professor Calum Drummond AO, said the research & development will be undertaken at RMIT’s Space Industry Hub. Launched this year, the Hub is a launch pad and industrial solutions incubator dedicated to growing Australia’s space sector. “Our ultimate goal is to maximise opportunities for commercialisation of the products that we co-develop with Boeing,” Drummond said. “This is a pioneering project which provides a tangible pathway for Australian businesses to upskill, innovate and export globally as manufacturers of products for space applications. Leveraging Boeing and RMIT’s joint expertise and facilities, we believe we can unlock boundless future opportunities for Australian industry.” Paul Watson, Director of Aerospace Engineering and Production at Boeing Defence Australia, said Australia’s burgeoning space sector required the production of complex, low volume, bespoke components not suited to conventional manufacturing techniques. “This partnership will develop new knowledge in advanced manufacturing technologies which will not only stimulate the development of a local fabrication capability but will also expose Australian industry to space export markets as part of Boeing’s global supply chain,” he said. Boeing’s longstanding relationship with RMIT has contributed significantly to Australia’s aerospace manufacturing capability through innovation in undergraduate education, postgraduate research and collaborative research projects.
UniSA to develop cutting-edge lasers for manufacturing, defence
The University of South Australia (UniSA) has been awarded a $1.8m Federal Government contract to develop technology that underpins the next generation of high-powered lasers in Australia for the defence and manufacturing sectors.
UniSA Professor of Laser Engineering, David Lancaster, will lead the three-year project, funded by the Defence Science and Technology Group (DSTG), in collaboration with the University of Adelaide. Lancaster, who heads one of the country’s leading laser and photonics manufacturing research laboratories at UniSA, will use the funding to help build sovereign manufacturing capability, bringing Australia up to speed with other developed nations. “High-powered lasers are increasingly being used in defence and manufacturing, but despite a long history of developing lasers in Australia, our technology is still relatively immature compared to other countries,” says Professor Lancaster. “There is a substantial gap between the research outputs and the needs of our defence industry, so Australia has had to buy this technology from other countries, which is quite restrictive because most nations severely limit their exports of lasers.” Over the next three years, Professor Lancaster aims to build a new type of high-powered laser that combines multiple smaller lasers, finetuning the manufacturing process so it is cheaper and more efficient. “In the past, I have worked on lasers that take years to build and cost millions of dollars,” he adds. “I think it’s more important to put years of effort to develop the technology and manufacturing processes to build many miniature and safer lasers which cost hundreds of dollars each. That is our aim.” UniSA’s Laser Physics and Photonics Devices Lab will manufacture the lasers and the University of Adelaide’s Institute for Photonics and Advanced Sensors will develop the specialist laser glass. Professor Lancaster says Australia’s universities and defence sector need to be more closely integrated to build sovereign independence in laser technology. “The reason that UniSA and the University of Adelaide have been selected for this project is that our miniature laser technology and manufacturing processes are world-leading and will supercharge the DSTG’s laser system program,” he says. High-powered lasers are also the preferred tools for the manufacturing sector as they can cut, shape and weld most industrial materials with high precision. Their ability to manipulate and transform materials makes them ideal for the automotive, computer and clothing industries as they can create extremely fine features that are near impossible to make using traditional machining equipment.
www.unisa.edu.au www.adelaide.edu.au www.dst.defence.gov.au
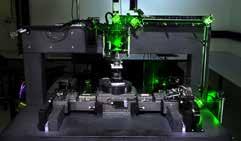
The state-ofthe-art laserbased device manufacturing facility developed at UniSA.
A proud Australian manufacturer of diverse bespoke metal products for 68 years.
EXTENSION TORSION COMPRESSION



Get in touch today…
T +61 7 3271 3500 E sales@marshalliance.com.au W marshalliance.com.au
Northern Territory, AMGC launch Advanced Manufacturing Ecosystem Fund
The Northern Territory (NT) Government has opened applications to the $7.5m Advanced Manufacturing Ecosystem Fund (AMEF) in partnership with the Advanced Manufacturing Growth Centre (AMGC).
The Fund delivers on the recommendations from the Territory Economic Reconstruction Report, and will leverage AMGC’s experience in successfully increasing Australia’s manufacturing capability. With a focus on expanding manufacturing in the NT, coinvestments will target local projects that seek to: • Grow an advanced manufacturing ecosystem and capability in the NT across the Territory’s priority sectors. • Increase investment in advanced manufacturing activity in NT, and secure a greater number of advanced manufacturing jobs located in the NT. • Commercialise new products and processes, including transitioning a new product or process from pilot/prototype stage to full commercial operations. • Support early-stage small-scale and pilot research projects in advanced manufacturing, allowing them to more quickly move to larger-scale commercialisation. Funding will range from $25,000 up to $500,000 (or more based on scale and impact), and must be matched by industry. Projects should include collaboration with a research partner and a minimum of one industry partner. “We are Australia’s comeback capital, but we also want to be Australia’s innovation capital,” said Michael Gunner, Chief Minister of the Northern Territory. “Advanced manufacturing will be a major jobs driver of the future, and this new partnership will provide local manufacturers with the ability to turn their dreams into realities. “By building up the Territory capabilities in advanced manufacturing, we are expanding industries and export opportunities, and creating new and exciting job opportunities for Territorians and investors.” AMGC’s Northern Territory Director, Charmaine Barrett added: “The NT has a significant opportunity to leverage its vast natural resources, research talent, and manufacturing base to grow its impact both locally and abroad. The launch of the Advanced Manufacturing Ecosystem Fund arrives at a time when public sentiment is high and the NT Government focus on the critical
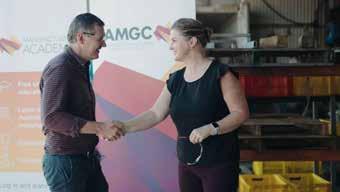
NT Chief Minister Michael Gunner with AMGC NT Director Charmaine Barrett at the launch of the Fund.
industry is strong, we look forward to getting to work and to helping build prosperity for Territorians.” The launch of the Fund coincides with the latest AMGC research finding that appreciation of local manufacturing in the Northern Territory has risen the quickest of any Australian region. Comparing data collected in early 2019, before the COVID-19 pandemic, with today, AMGC contrasted the awareness and attitudes toward local manufacturing, revealing that pubic support is higher compared to pre-pandemic times. Territorians' support for, and knowledge of, manufacturing is the highest of anywhere in mainland Australia, rising by 33% to 83% over the pre-pandemic survey. Dr Jens Goennemann, Managing Director for AMGC, said: “The Northern Territory is certainly ahead of other jurisdictions, both in public perception and policy direction when it comes to investing in the potential of manufacturing. AMGC’s partnership with the Territory Government to grow the NT’s manufacturing ecosystem is a sound investment that will deliver secure jobs and higher growth to the Territory, helping to transform the local economy from a lucky one into a smart one,”
Further information regarding the Fund, the application process and grant guidelines are available at: www.amgc.org.au/projects
Lithoz, Objective3D deliver ceramics 3D printer to UoW
Despite ongoing COVID-19 travel restrictions, Lithoz and Objective3D have successfully completed the remote installation of a Lithoz CeraFab 3D printer at the University of Wollongong (UoW).
A partnership between UoW, Lithoz and Objective3D allowed the remote installation of the high-resolution ceramic printer to occur, which will be used for a broad range of applications in the development of bioprinting hardware. The printer was purchased by the Australian National Fabrication Facility (ANFF) Materials Node, which is based at UoW, for use at the Translational Research Initiative for Cellular Engineering and Printing (TRICEP). TRICEP works with research institutions and industry to develop innovative technologies using 3D bioprinting. Dr Johannes Homa, CEO of Lithoz, said the project highlighted the importance of agile working: “We are world and industry technology providers for ceramic 3D printing systems and materials, and have been working in research and industry for more than 10 years. After the past year, it has become clear to us just how critical flexibility in the manufacturing world is, and we are very happy that this remote installation has been a success.” The investment from ANFF will give TRICEP a highly flexible means of customising and producing devices to support material development research worldwide. Associate Professor Stephen Beirne, Associate Director at TRICEP, said the team was thrilled to have access to this exciting new technology. “The CeraFab 3D printer provides us with access to new families of materials with properties and printing characteristics that greatly expand our service and research capabilities,” said Beirne. “The system will be immediately put to use in the development of next generation biofabrication hardware and implantable structures.”
www.lithoz.com www.objective3d.com.au www.uow.edu.au
High-growth businesses reveal new technology plans
Technology use is a major determinant of business success and is set to become more influential, according to a survey by CPA Australia.
“High-growth businesses spend more time and resources on technology,” said Gavan Ord, Senior Manager – Business Policy at CPA Australia. “Their choice of technology puts them even further ahead of their competitors. Our survey results suggest other businesses may improve their growth prospects by investing in the technologies used by high growth businesses.” One of the world’s largest professional accounting bodies, CPA Australia surveyed 725 professionals in different industries in Australia, mainland China, Hong Kong, Macau, Malaysia and Singapore. Respondents were asked about their businesses’ past and expected technology use and past and expected financial performance. “COVID-19 accelerated technology adoption by businesses, but not all businesses were equally placed when the pandemic hit,” Ord added. “High-growth businesses had already embraced technology enthusiastically. This helped them manage the disruption caused by COVID-19.” In 2020, high-growth businesses were significantly more likely to develop a long-term technology strategy, work with technology companies and increase their recruitment of technology staff than businesses whose growth was stagnant or shrank. “High growth businesses have been focusing on technologies that deliver greater value to customers, such as data analytics and visualisation software, business intelligence software and artificial intelligence,” Ord said. Differences in future technology plans also sets higher and lowergrowth businesses apart. High-growth businesses are much more likely to expect to increase their use of or investment in data analytics and visualisation software, business intelligence software, customer relationship management software and artificial intelligence than their lower growing counterparts. The top technologies Australian businesses are most likely to increase investment in over the next 12 months are cloud technology and data analytics and visualisation software. Highgrowth businesses in Australia are also planning to invest in business intelligence software. The key drivers of technology adoption by Australian businesses are improving operational efficiency and the customer experience, while the main challenges are financial constraints and complex legacy systems. “If you want to do well in business, look at what others are doing well,” Ord remarked. “The clear lesson from our survey is that technology adoption, and making the right choices, leads to better business performance.” Over the next 12 months, large businesses (more than 1,000 employees) are planning to use or invest in data analytics and visualisation software, cloud technology, robotic process automation and artificial intelligence. Small businesses (fewer than 50 employees) are more likely to focus on cloud technology, video conferencing and group collaboration tools, and data analytics and visualisation software. “When it comes to technology adoption, it’s not a level playing field, and many small businesses struggle,” Ord concluded. “We support government programs to build small businesses’ digital capability. It’s a great way for governments to future-proof the economy.”
MHI Australia, Primetals Technologies join Heavy Industry Low-Carbon Transition CRC
Mitsubishi Heavy Industries (MHI) Australia and Primetals Technologies have joined the Heavy Industry Low-Carbon Transition Cooperative Research Centre (HILT CRC) as key partners.
The HILT CRC aims to develop technologies to decarbonise Australia’s heavy industrial sector, leverage the country’s natural endowments in mineral and clean energy resources and seize the opportunity of growing export markets for certified low-carbon products. Over the next 10 years, MHI Australia and Primetals, a member of MHI Group, will contribute financially to the CRC as well as with their experience in iron and steel production to this effort. The companies will focus on research & development of hydrogenbased direct reduction of iron ore. This includes the novel HYFOR (hydrogen-based fine-ore reduction) technology currently being piloted by Primetals in Europe. Australia has the world’s largest iron ore deposits and is the leading exporter of iron ore. Since the iron and steel sector is responsible for 7%-10% of greenhouse gas emissions globally, Australia has a key role to play in the decarbonisation of the industry. Switching from traditional coal and coke-based ironmaking processes to hydrogen-based production methods is the only way for the industry to fully decarbonise. Deploying these technologies at scale in Australia could move producers up the value chain and turn the country into a major exporter of low-carbon, direct-reduced iron. This would help Australia meet its obligations under the Paris Agreement and make it easier for the global iron and steel industry to reach net-zero by 2050. MHI Australia is an active partner in Australia’s sustainable development efforts with a focus on energy and decarbonisation. Primetals brings an extensive portfolio of iron ore beneficiation, pelletising, sintering and iron ore reduction technologies. Earlier this year, Primetals commissioned a pilot plant for its HYFOR technology at a site of Austrian steelmaker voestalpine. The next step — building an industrial-scale HYFOR prototype — will be decided by the end of the year. Dr Alexander Fleischanderl, Technology Officer – Upstream and Head of Eco Technologies at Primetals, said: “Australia has large deposits of iron ore, great potential for green energy, and boasts a dynamic academic and business environment. This puts the country in a unique position in the quest for net-zero by 2050 as a supplier of clean metallics. The HILT-CRC, with its wide range of partners from across the energy, hydrogen, mining, and cement industries, will form a great ecosystem for innovation.”
www.mhi.com www.primetals.com www.hiltcrc.com.au
Research collaboration to strengthen welding wire composition
New high-strength aluminium-scandium welding wire for Wire Additive Manufacturing (WAM) applications will be developed in a $600,000 research partnership between AML3D Limited and Deakin University, supported through the Innovative Manufacturing Cooperative Research Centre (IMCRC).
AML3D, a pioneer in Wire Arc Additive Manufacturing (WAAM), has teamed up with Deakin's Institute for Frontier Materials (IFM) to investigate scandium as a strengthening element for existing aluminium wire feedstock for 3D printing and welding, with the potential to commercialise. The 12-month collaboration will see IFM researchers create and road-test new alloy compositions that deliver high-strength, corrosion-resistant WAAM structures, using AML3D’s WAM technology. Dr Thomas Dorin, who leads the research at IFM, says most aluminium alloys obtain their strength via additional heat treatments, which can be costly and impractical when using WAM technology. “When you add scandium to aluminium, it acts as an ‘excellent strengthener’,” says Dr Dorin. “Our preliminary research has shown that aluminium-scandium forms strengthening AI3Sc particles during WAM and create as-printed high-strength structures with limited need for subsequent heat treatment. Also, scandium is electrochemically neutral with aluminium. The new WAM structures are thus expected to be more corrosion resistant compared to the ones created with existing welding wires.” AML3D is trialling aluminium-scandium compositions for various industry use cases. Successful trials will enable many new applications for WAM, with the automotive, resources and transport industries (such as shipbuilding) showing strong interest in highstrength aluminium products. Encouraged by the success of initial industry-scale welding trials, Andrew Sales, Managing Director of AML3D, describes the research progress as promising. “The uniqueness of our WAM technology lies in its ability to 3D print large metallic structures,” says Sales. “The welding wire compositions created through this research project will enable us and our customers to manufacture components with stronger and better mechanical properties. This will help us to position high-strength aluminium products produced by WAM as a viable alternative to existing processes.” With the potential of generating new Australian-owned intellectual property, the project also provides AML3D with new revenue prospects not only through high-strength aluminium WAM parts but also wire feedstock sales for 3D printing and welding applications. Australia is one of the largest producers of aluminium, and with scandium being declared a critical commodity for Australia, the US and Europe. Dr Matthew Young, Manufacturing Innovation Manager at IMCRC, sees the collaboration also as a significant opportunity to value add to Australian resources. “The project is a great example of creating new, higher value products using Australian resources,” says Dr Young. “By enhancing the properties of aluminium by adding scandium, and thus its value, the research demonstrates that Australia is capable of manufacturing and delivering high-quality products.” Deakin University and AML3D are looking to expand their partnership to develop a range of purpose specific alloys for WAM applications and provide unique facilities and capabilities to assist in their growth.
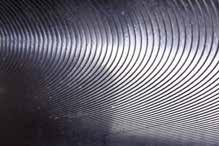
Smart manufacturing, R&D commercialisation get $16.12m boost at Monash
Smart manufacturing and research & development (R&D) commercialisation at Monash will be enhanced by a $16.12m investment through the Victorian Higher Education State Investment Fund (VHESIF).
The investment aims to enhance research commercialisation, support the creation of future industries and jobs, accelerate the attraction of international investment, and build access to global supply chains. The funding will support investment integration to maximise impact in three core areas across the Monash Technology Precinct by June 2022, including: • Medicines Manufacturing Innovation Centre (MMIC):
Expansion of MMIC’s presence to a new node at Clayton, allowing the scale-up of medicine manufacturing capability, and support for clinical trials and growth of exports and jobs.
• UP-LINK university partner collaboration space:
A platform at the heart of Clayton campus that will drive manufacturing innovation and modernisation. This will provide industry with early access to Monash research and talent pipelines. In addition, incubator and start-up facilities will support commercialisation and spinouts, enabling entrepreneurial activity across the precinct, and creating new businesses. • oNKo-innate Headquarters: A biotechnology research and development facility to accelerate the development of cancer therapies, enabling target identification, validation, and subsequent development, manufacturing and commercialisation of cancer treatments. President and Vice-Chancellor Professor Margaret Gardner AC said: “Monash University is pleased to receive $16.12m through the VHESIF to drive commercial and entrepreneurial activity across the Monash Technology Precinct. This funding will enable the MMIC to greatly enhance process optimisation and product development, and advance medicine manufacturing and clinical trials through the establishment of a new node at Clayton campus. UP-LINK is an excellent example of university, government and private-sector collaboration to realise the significant innovation towards Australia’s advanced manufacturing industry, and to enable job-ready graduates to secure a prosperous future for our communities.”
Bosch opens new Manufacturing Automation Centre
Bosch has opened its new $17m Manufacturing Automation Centre in Clayton, Victoria, a purpose-built facility that houses Bosch Australia Manufacturing Solutions (BAMS) and the Rexroth Drives and Controls businesses.
The establishment of the new centre completes the consolidation of all Bosch’s businesses in Victoria at its Clayton campus, boosting strategic collaboration and innovation. Gavin Smith, President of Bosch Oceania, said: “Manufacturing automation is now the fastest growing part of our business. We are leveraging our more than 50 years of manufacturing experience and factory automation know-how and drawing on the global expertise within the Bosch group, to help Australian manufacturers become fit for the future.” BAMS has become one of the country’s leading factory automation companies, working with a diverse array of blue-chip, mid-tier and start-up manufacturers to automate their manufacturing. Most recently, BAMS was engaged by digital diagnostics company Ellume to automate the high-volume production of its rapid COVID-19 tests. BAMS is highly regarded in the biotech sector, currently working with CSL to create a high-tech automatic materials handling line for their manufacturing facility in Broadmeadows. BAMS was also part of the industry consortium led by Grey Innovation that built ventilators in the fight against COVID-19. Also occupying the new centre is the Victorian arm of Bosch Rexroth Australia. With significant investment in new equipment, the business has increased its support to customers in Victoria and offers advancements in repair and testing technologies, including industry 4.0 solutions. Bosch Rexroth Australia is focused on meeting its customers’ needs into the future. Its team of expert hydraulics and application engineers continually develop new technologies, working closely with local customers to develop state-of-the-art solutions. This support provides technical solutions to design challenges in a changing global market. With a complete portfolio of drive and control technologies, Bosch Rexroth represents a one-stop source for controls, electric drives, hydraulics, mechanics, and system solutions. Martin Pakula, Victorian Minister for Industry Support and Recovery, said: “Victoria is the place for innovators like Bosch Australia to grow and thrive, due to our skilled workforce, established supply chains, engineering expertise, education excellence, and research and development capability. We will continue to support businesses to capitalise on the opportunities and talent available in Victoria, ensuring we remain at the forefront of advanced manufacturing, innovation and technology.” www.bosch.com.au
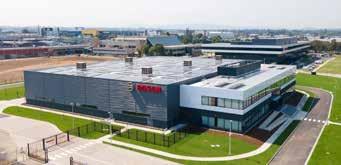
Clearly the best Clearly the best
Industrial Door Solutions
NEW 36pp brochure now available. Contact us to get your FREE copy.

M.T.I. Qualos Pty. Ltd. are leaders in the manufacturing and service of Industrial Transparent Flexible Doors, Insulated Traffic Doors, and Roll-Fast Doors. We produce to the highest quality standard within a full range of industrial doors to suit any door application.
Contact our team today to find a solution for you.
M.T.I. Qualos Pty. Ltd. 55 Northern Road, West Heidelberg, Vic. 3081 Tel: 1300 135 539 E: sales@mtiqualos.com.au W: www.mtiqualos.com.au
Advanced recycling technologies could turn problematic plastic waste destined for landfill into valuable resources, according to a new report by CSIRO.
The report, Advanced Recycling Technologies to Address Australia’s Plastic Waste, evaluates the ways to convert plastic waste that can’t be recycled with existing methods, into new resources to build Australia’s circular economy. It is estimated that 130,000 tonnes of plastic leaks into the Australian marine environment each year. Less than 12% of plastic waste is recycled and about 85% ends up in landfill. Advanced recycling of plastic waste, also referred to as feedstock, molecular, or chemical recycling, converts plastic waste into its chemical building blocks and back into plastic, or other useful resources such as fuel. CSIRO researcher Sarah King said with new waste plastic export rules in place, new technologies were critical to support the increased recovery and recycling of plastics. “Advanced recycling technologies could turn hard-to-recycle plastics, such as mixed, multi-layer, flexible or contaminated plastics back into food-grade recycled plastics or other products through chemical, thermal or biological processes,” King said. “It is suitable for flexible or soft ‘scrunchable’ plastics used for food packaging, such as food pouches and chocolate wrappers. When collected, these types of plastics may be contaminated with food, or mixed with other materials so currently can’t be recycled. “Advanced recycling could process this plastic waste to increase opportunities for the polymer manufacturing and waste sectors by supporting new industries. The North American market is estimated at $120bn, demonstrating there is economic potential for adopting advanced recycling in Australia.” Australia has set a national target of 70% of plastic packaging recycled or composted by 2025, and 80% average recovery rate from all waste streams by 2030. Chemistry Australia’s Director for Strategy, Energy and Research Peter Bury, who collaborated with CSIRO on the report, said advanced recycling is an important and complementary technology able to progress an Australian plastics circular economy. “Mechanical recycling methods are our foundation technologies and very effective for a range of well-sorted plastics used for food and other packaging,” Bury said. “Advanced recycling can sit alongside these to further strengthen Australia’s recycling capabilities for plastics that can’t be processed through existing channels. “Australia already has the critical industrial capability in polymer manufacturing, steam crackers, and refineries, to integrate advanced recycling outputs to produce new polymers. Importantly, we have the talented and skilled people in place to introduce and develop this additional technology.” The report was produced in consultation with Chemistry Australia, LyondellBasell and Qenos. The report and opportunities to adopt advanced recycling technologies are key parts of CSIRO’s developing Ending Plastic Waste Mission to achieve an 80% reduction of plastic pollution entering the Australian environment by 2030. “Our report aims to build awareness of advanced recycling technologies, how they apply to different plastic types, and the key factors to enable adoption and scale up of these technologies in Australia,” King added. “Plastic pollution and waste are challenges we need to solve. Advanced recycling will improve the recovery, recycling and reuse of materials, consistent with a circular economy.”
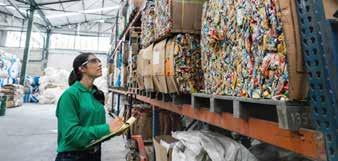
Call for local procurement on infrastructure projects like windfarms
Weld Australia has called on the Federal Government to mandate local content in the construction of critical national infrastructure projects after it introduced legislation on 2 September that will pave the way for construction of Australia’s first offshore wind farms.
The Offshore Energy Infrastructure Bill could permit the construction of the 2.2-gigawatt Star of the South wind farm off the Gippsland coast in Victoria’s south-east. The Bill could also enable construction of the Marinus Link interconnector between Victoria and Tasmania, as well as windfarms in areas like Gladstone, Newcastle and Wollongong. “The only way to ensure that these massive wind turbines meet Australian Standards for reliability, quality and safety is to award the fabrication contracts to local Australian companies,” said Geoff Crittenden, Chief Executive Officer of Weld Australia. “Local fabricators comply with internationally recognised Australian Standards and are certified by the relevant Australian authority. The Star of the South and Marinus Link interconnector projects alone are worth $10bn combined and are expected to create 10,000 jobs. According to Crittenden, a procurement policy that mandated local content would see that $10bn reinvested back into the Australian economy. It would also create thousands of jobs in regional areas like Gippsland, Gladstone and Newcastle, supporting Australia’s post-COVID-19 recovery. “The importance of our local manufacturing industry cannot be underestimated when it comes to Australia’s post-COVID recovery,” said Crittenden. “Australia’s jobs-driven COVID-19 recovery must be manufacturing-led. Now is the time to make manufacturing a national priority. Government, at all levels, must support and invest in the manufacturing sector to aid its growth. “Mandating local content in national infrastructure projects is the only way to ensure product quality and public safety, create new jobs, and strengthen Australia’s economy.”
Beep Cricket – Enabling active, inclusive lifestyles for the blind and vision impaired
At a time when sport has been curtailed and confined to restricted environments, a team of innovators including GoProto have been working on developing a new improved cricket ball for blind and visually impaired players.
Blind cricket has been played as a competitive sport in Australia since 1922. It uses a ball slightly larger than a standard cricket ball that is traditionally filled with ball bearings or bells to provide audible cues. Listening to the sound of the ball is how the players can bowl and catch. The biggest challenge is when the ball stops moving and no longer makes a sound. Supported by legendary wicketkeeper Ian Healy, non-profit organisation Blind Bats Inc and its newest venture in Beep Cricket promote increased sporting accessibility for the blind and vision impaired. Paul Szep, president of Blind Bats Inc, is an avid supporter of blind cricket. After becoming aware of the Kookaburra Smartball and its technology, he came up with the idea of a continuous beeping cricket ball controlled remotely by a phone app. For the beeping ball, the design has to withstand the punishment of a cricket bat without damaging the internal electronics, while keeping the ball at a reasonable weight and size. With the assistance of local community and government grants, Szep presented his idea to Kookaburra Sport and Sportcor, the developers of the Kookaburra SmartBall, which features an embedded micro-chip to provide cricketers with real-time feedback. Using this same technology and with the support of Kookaburra, development moved forward in designing a new audible ball that would meet the game’s regulatory requirements. To test and validate the design, 3D printing has long been a popular medium for producing presentation and functional prototypes, and more recently for volume manufacturing. With a long-standing history in 3D printing and contract manufacturing, GoProto helped Kookaburra achieve the desired results using a combination of stereolithography (SLA) and traditional moulding technologies. James Sanders, General Manager for GoProto, has worked with Kookaburra Sport on a number of projects over the years. “Professional 3D printing and moulding technologies have enabled sporting goods manufacturers, like Kookaburra, to develop sports equipment that’s lighter and better suited to the needs of the athlete,” says Sanders. “The technology and materials used in creating the beeping cricket ball has the ability to cement social cohesion and greater participation”.
www.goproto.com.au www.blindbats.org
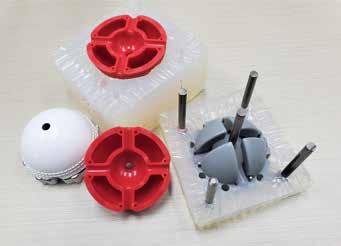
Supporting sport with 3D scanning tech
The Australian Institute of Sport (AIS) made innovative use of the latest 3D scanning technology from Hi-Tech Metrology in its work supporting Australian sporting development.
The AIS was established under the Australian Sports Commission Act 1989, to build sustainable winning systems for Australian athletes that are measured through consistently producing podium success over multiple cycles, inspiring the next generation. The AIS’ investment philosophy is to target multiple medallists over multiple cycles, and support their partners through their resources, research and facilities. They know that success will be driven by innovation, athlete wellbeing, targeted investment and a commitment to being “ahead of the game internationally”. These core values instigated an exhaustive search into the latest 3D scanning technology capable of meeting the stringent guidelines that the AIS is renowned for. As a result, Hi-Tech Metrology were approached to present the extensive range of Creaform Scanners, and after much research and investigation AIS acquired the HandySCAN BLACK|Elite. Essential to the decision was the availability of professional, nationwide training and support personnel both initially and ongoing for the project. Hi-Tech Metrology has a number of engineers located throughout Australia, which provided the reassurance that AIS needed to proceed with the purchase. Since acquiring the BLACK|Elite, AIS mechanical and manufacturing engineer Callum McNamara says: “We can undertake tasks such as reverse engineering in field measurement and data referencing for complex CAD modelling, which in the past were either done manually or not at all. The ability to capture high-resolution data at a rapid rate including highly reflective surfaces translates to delivering projects on time in a high-performance environment.” The investment in this leading-edge, dynamic scanning technology ensures the AIS maintains its commitment to providing innovative solutions and giving Australian athletes their best chance at achieving international sporting success.
www.hitechmetrology.com.au www.sportaus.gov.au
GOVERNMENT NEWS $47m in grants to boost research collaboration in manufacturing
A bionic “eye” that could restore visual and spatial perception for the blind is one of 22 industry-led collaborative research & development projects to share in $47.1m in funding from the Morrison Government.
Successful projects under round 11 of the Cooperative Research Centre Projects (CRC-P) initiative will deliver a range of innovative technologies and create job opportunities in key manufacturing sectors, including in regional Australia. These projects will leverage a further $86m of cash and in-kind contributions from 95 project partners. Aria Research Pty Ltd will partner with the University of Sydney and World Access for the Blind to undertake clinical trials of its bionic prosthesis, which could provide new levels of independence and autonomy for Australia’s 600,000 vision impaired citizens. The successful projects this round include: • SunPork Pty Ltd (QLD) with a grant of $2,892,374 to eliminate the removal of pig’s tails, improving pig welfare and the sustainability of the pork industry. • Rux Energy Pty Ltd (NSW) with a grant of $2,770,000 to develop an efficient hydrogen storage system, a key barrier to the uptake as a new zero-carbon fuel. • iOrthotics Pty Ltd (QLD) with a grant of $2,044, 034 to advance the manufacturing of smart orthotics to reduce diabetes-related amputations. • Seer Medical Pty Ltd (VIC) with a grant of $465,183 to develop its long-term brain monitoring electrodes for an improved patient experience in the diagnosis of epilepsy. The two regional projects are: • DefendTex Research Labs Pty Ltd (VIC) with a grant of $3,000,000 will establish a research centre in Gippsland for additive manufacturing of energetic materials to advance manufacturing capability for its rocket fuel additive for space launch. • Nourish Ingredients Pty Ltd (NSW) with a grant of $2,829,073 will establish a commercial pilot-scale fermentation facility in Goulburn to develop lipid fermentation for the local manufacture of future foods. Since the first round of CRC Projects in 2016, the Government has awarded over $376m in funding under the CRC-P Program to support 176 projects. These projects include over 900 collaborating partners from industry, research, government and community organisations, and are leveraging $853m in partner contributions. CRC-Ps can run for up to three years and must have at least two Australian industry partners, including one small or medium-sized business, and one Australian research organisation partner.
www.business.gov.au/grants-and-programs
Siemens backs Victoria’s Digital Jobs program
Siemens will support the Victorian Government’s $64m Digital Jobs program, a first of its kind in Australia that will help 5,000 mid-career Victorians reskill and upskill on much-needed digital skills.
Joining other companies committed to the program, Siemens will train an intake of mid-career workers on key digital technologies used by some of the most well-known companies worldwide, making them more digital job-ready. The program follows the success of Siemens’ previous award-winning Industry 4.0 Apprentice program that was launched along with Swinburne University and Australian Industry Group (Ai Group), as well as the significant grants of the company’s hi-tech industrial software to a national network of universities. Speaking on the announcement, Jeff Connolly, CEO and Chairman of Siemens Australia said that digital readiness plays a critical role in Australia’s ability to innovate and create new pathways for growth. “Digital preparedness is a constant process and happens throughout a person’s career,” said Connolly. “Gone are the days when you get a qualification early in your career and that sets you up for life. Society expectations and technology developments are driving constant change, which means everyone needs to continually learn and adapt to stay relevant.” Connolly is an advocate of on-the-job training being an important part of the learning mix: “A mix of academic learning and on the job application and training is a powerful combination and digital skills are critical. This not only makes you more employable, but it also opens up possibilities for business and society to look at ways to accelerate improved outcomes. We’re delighted to support and participate in the Victorian Government Digital Jobs program.” Siemens will host a selection from the first cohort of 450 participants scheduled to start industry placements in October. Jaala Pulford, Minister for Innovation, said the Victorian Government was committed to growing the state’s pipeline of tech talent: “We know the demand for digital talent is increasing rapidly, and the Digital Jobs program has been designed to build our tech workforce and create new opportunities for Victorians. It’s fantastic to see Siemens jumping on board. Not only will the participants benefit from learning in such a fantastic environment, but Siemens will get access to passionate and driven workers who could become long-term assets to the business.” Participants will complete 12 weeks of skills training at a leading Victorian training provider in fields such as data analytics, web development, digital marketing, cloud computing and cyber security. Following the training, participants will undertake a 12week paid internship with organisations such as Siemens to further develop their new skills.
www.vic.gov.au/digitaljobs
Jeff Connolly, CEO and Chairman of Siemens Australia.