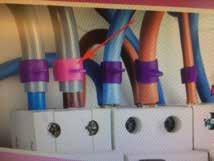
25 minute read
VOICEBOX Opinions from across the manufacturing industry
from AMT DEC/JAN 2021
by AMTIL
Yes, we need to make things in Australia, but not like in the past
Calls for a revival of Australian manufacturing have surged in 2020 as the COVID-19 pandemic showed our vulnerability as global supply chains broke down. However, we should be strategic in targeting areas of manufacturing where Australia can enjoy a comparative advantage, writes Richard Holden.
Much of the focus of Opposition Leader Anthony Albanese’s budget reply speech was around Labor’s proposal to expand childcare subsidies – a policy with some flaws but which moves in the right direction. Labor’s plan to modernise the electricity grid by setting up a “Rewiring the Nation Corporation” with $20bn in government support was also met with general approval. What got less attention was the third pillar of Labor’s budget strategy – a big push toward more local manufacturing jobs. Albanese wasn’t shy about what he meant. He lamented the loss of Australia’s car-making industry: “Australians will never forget that it was this government that drove Holden, Ford and other car makers out of Australia, taking tens of thousands of jobs in auto manufacturing, servicing and the supply chain with them.” He then announced Labor would create a National Rail Manufacturing Plan to expand Australia’s boutique train-building industry: “We will provide leadership to the states and work with industry to identify and optimise the opportunities to build trains here in Australia – for freight and for public transport.” The economics of pillars 1 and 2 make sense. Pillar 3 involves trying to turn back the clock on the irrepressible, tectonic forces of globalisation and automation to pretend we should make things here we shouldn’t. Understanding comparative advantage Countries benefit from trade rather than seeking to produce everything they need locally. This is due to the idea of ‘comparative advantage’, originated by David Ricardo in his 1817 book On the Principles of Political Economy and Taxation. One country (call it country A) might be more efficient than another (country B) in absolute terms at producing, for example, T-shirts and wine. It is tempting to think, then, that country A should produce both T-shirts and wine. But what if country B is really inefficient at producing T-shirts but reasonable at producing wine? If country A specialises in producing T-shirts and country B specialises in producing wine, they can trade and both be better off. Why? Because country A produces T-shirts much more efficiently than country B, and country B is only a little less efficient at producing wine. Overall, both economies get more efficient, raising living standards. Making cars and trains in Australia Does Australia have any comparative advantage at producing cars or trains? With cars the evidence speaks for itself. Local manufacturing only survived for decades because of huge government subsidies. Without them Australian-made cars couldn’t compete. Only part of that was to do with labour costs – and we should be rightly proud of our comparatively high wages and good working conditions. Germany – home of BMW, Mercedes Benz and Volkswagen – also has high wages and conditions. What about trains? Some trains are made in Australia – by Downer EDI and Canadian multinational Bombardier. That’s good for a few thousand jobs. But the market is domestic, with the customers being state governments who buy with an eye on local jobs. There’s not a lot to suggest it can become an export industry, competing for example with Japan, which has been making bullet trains since the early 1960s. Or France, whose train builders have sold hydrogen trains to Germany and high-speed freight trains to Italy. With these competitors having such an edge, and the well-known phenomenon of “learning-by-doing”, are we really going to catch up? There are many other sectors in which Australian producers are internationally competitive, such as agriculture, services and areas of high-tech manufacturing. Building on and expanding comparative advantage in these areas makes a lot more sense. The case for strategic manufacturing That said, the COVID-19 pandemic has taught us how fragile certain parts of our economy are. The same logic of comparative advantage that has done so much to improve living standards has also made us vulnerable in some areas. Having little or no manufacturing capacity in personal protective equipment (PPE) or pharmaceuticals like insulin, EpiPens and antibiotics is potentially very dangerous. Importing more than 90% of our pharmaceuticals puts us in a vulnerable position if a state actor that controls important parts of the global supply chain decides to cut supply. This is what economists call the “hold-up problem”. So it makes sense for Australia to have more presence in strategic manufacturing like pharmaceuticals and personal protective equipment, even if producing these goods locally is not as efficient as buying them from overseas. From just-in-time to just-in-case The pandemic has taught us that we have, as a nation, moved a little too far towards the efficiencies of “just-in-time” supply chains. We need to move back somewhat, but certainly not completely, in the direction of “just-in-case” – to a little less efficiency but a little more insurance. That should involve a push for strategic manufacturing. We should at all times be looking to build on and expand our comparative advantage. But trying to go “Back to the Future” and build an Australian De Lorean makes no sense.
Richard Holden is Professor of Economics at the Australia Business School of the University of New South Wales (UNSW). This article was originally published by The Conversation. www.theconversation.com www.unsw.edu.au
Observation – The key to inspiring amazing, disruptive innovations
The key to real innovation is in observing and identifying problems worth solving. Unfortunately many innovators are driven by the teaching that commitment and persistence will lead to success, even with ideas and products that may have little merit, writes Roger La Salle.
Persist and you will succeed, we are told. But how true is this? Does persistence really win in the end? I have always lived by a saying I coined many years ago: “Persistence is an important element of success; Persistence is an essential element of failure.” The underlying thinking here is that if the idea is fundamentally bad, no amount of persistence will make it good. Worse still, many are so enamoured with their ideas that they invest heavily in patents only to then fail and go broke at the same time. Persistence needs to be moderated with a high degree of common sense and objectivity, and the ability to let go and know when to stop. It’s not a failure if you stop before it’s too late. It is a failure if you persist beyond the point of sensibility. Having said that, capturing and holding the nub of a good idea is another matter as maybe it’s just a matter of time until the technology is achievable. A good example may be the concept of a wristwatch phone – conceived 50 years ago and a marvellous idea, but only recently possible. With that in mind let us explore the ways we can identify ideas or problems worth solving in the first place, before applying the tools of innovation and engineering to find a solution. Quite remarkably, the suggestion that you should explore your customers’ needs in search of a problem is somewhat new in the pursuit of innovation. This simple notion –of asking what the customer wants – is embodied in so-called “Design Thinking”, a movement that only swept the world during the past decade. The idea of exploring customer needs is of course excellent; the problem is that the means of exploring such needs was lacking. The secret to identifying possible good ideas lies in the art of not asking, but observing people’s behaviour. This is best done using the tools of “Opportunity Capture”, where there are only five things one needs to observe: • Predictable activities. • Widespread activities. • Repetitious activities. • Emerging trends in activities. • Comparison between groups. These are the seeds of opportunity capture, with the entire opportunity scan process being embedded in a five-by-eight matrix that gives some 40 ways to explore the opportunity horizon. However, the above seeds alone will suffice if we just use these to observe behaviour. Properly used, the approach of observation makes it easy to identify opportunities for innovation – in fact, disruptive innovation, since it focuses on common behaviours. This brings to mind a problem we observed many years ago, but have only recently resolved and brought to market. To put this into context, fires in electrical switchboards almost always occur at terminations as joints become loose and corrode and resistance rises, resulting in thermal runaway or hot spots. For years the approach to identifying hot spots has included all of the ingredients that may qualify for an opportunity scan. Activities that were predictable, widespread and repetitious, with thermographers virtually worldwide annually taking single-shot thermal images inside electrical switchboards in an endeavour to find hot spots. Unfortunately, as good as this may sound, a thermography can never be sure that when the picture is taken the load actually causing the hot spot is even operating. Who really knows what’s happening when the thermal image is captured? In fact the suggestion that a one-shot thermal picture of an electrical switchboard, with unknown loads operating, can give you peace of mind that a building is safe from fire until the next annual picture is questionable. Alternatives such as real-time radio I0T alert devices are available. So too are fibre-optic monitors that span many connections, or fixed thermal cameras or wired thermocouples, but these are simply not cost-effective for use across the myriad of switchboards and wires that populate every building in the country. It was the opportunity scan and observation of hot spots and the sheer population of switchboards that resulted in the development of a newly released technology. Costing only a few cents each, permanent colour change clips that change colour from purple to bright pink are now available and can be attached to every cable to indicate the presence of a hot spot, no matter when it occurred. Faults are now obvious the moment you open the switchboard. This is one simple example of what an opportunity scan can achieve on just one level. How many other safety-related events do we see only periodically monitored that could be monitored in a more thorough fashion and thus lead to breakthrough innovations? Examples might include: • “Tag testing” of trade power tools, only for the tool to become damaged and dangerous the very day after is passes all tests. • Vehicle tyre pressure. • Smoke detectors. • Life jackets in boats. • Electrical appliance connections. • Gas leaks. • CO monitors for domestic heaters. • Water leaks and dripping taps. The list is endless if we simply employ this opportunity scan approach of observing the way people work. Indeed, safety-related activities are a most fertile ground for identifying problems worth solving.
www.innovationtraining.com.au www.safeconnectaustralia.com.au
Collaborative automation key to Australia’s manufacturing revival As 2020 draws to an end, Australian manufacturing must face the challenges of operating in a new, post-COVID landscape. Collaborative robotic applications can help manufacturers emerge more competitive with greater production flexibility, higher output, and better output quality, writes James Taylor of OnRobot.
In the midst of the COVID-19 pandemic, many of us have had to face once-in-a-lifetime challenges, perhaps both personally and economically. At the same time, geopolitical tensions have created uncertainty for some manufacturers with exposure to international markets. However, once-in-a-lifetime challenges also present significant opportunities for those who are willing to learn and adapt. With that in mind, new innovations in manufacturing technology are a key development for manufacturers seeking sustainable growth in this changing climate. For many years manufacturing played a significant role in Australia’s economic success and was one of the country’s biggest employment providers. In the 1980s, for instance, it accounted for roughly 16% of the country’s workforce—more than any other industry. So although Australia currently ranks last among Organisation for Economic Cooperation and Development (OECD) countries for manufacturing self-sufficiency, there is a history of success. The COVID-19 pandemic has impacted economies around the world, but Australian manufacturing can adapt, capitalising on international supply chain disruptions to meet growing domestic business demands. Driven by new technologies and capabilities, including modern collaborative applications and automation, now could be the time for manufacturing to make its welcomed comeback. The rise and advantage of collaborative applications Collaborative applications – created when lightweight industrial robots and collaborative robots (cobots) are equipped with intelligent tools such as grippers, sensors, vision and the software that drives them – are the future of automation. These advanced technologies enable simple, rapid deployment and new processes while working safely alongside workers. In the past, automation was viable only for large manufacturers who had the space, cash, and technical resources for large investments in traditional industrial robots. Companies needed large runs of the same products and processes over long periods of time. Investments took years to pay for themselves. Collaborative applications provide a quick and easy entry-point to automation, particularly for smaller manufacturers whose businesses have lower-volume, high-mix production lines. These small-and-medium-sized enterprises (SMEs) can emerge more competitive with greater production flexibility, higher output, and better quality. Since SMEs are more vulnerable to supply chain disruptions and “black swan” events such as COVID-19, versatility and the capacity to quickly adjust manufacturing processes are hugely important. One such Australian company that improved its manufacturing processes is Designed Mouldings, primarily serving the pharmaceutical industry with plastic injection-moulded components. The company integrated OnRobot’s VGC10 vacuum gripper with a cobot at its factory in Caringbah, New South Wales, to automate the delicate, time-consuming task of picking and placing plastic moulded caps.
Japanese contract manufacturer Sanmatsu used a collaborative robot to automate a machine tending application, eliminating the need to have a worker continuously stationed at the machine, reducing overtime and lowering production costs by 10%.
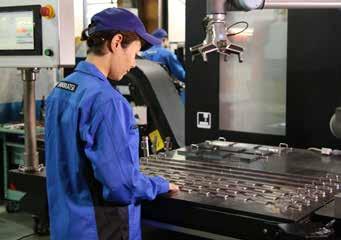
Equipped with a collaborative vacuum gripper, the cobot autonomously executes the task, reducing operational costs, increasing productivity, and delivering an expected return on investment (RoI) of just six months. Employees work safely in close proximity, feeding raw materials to the robot and removing completed products from the line. Opportunity within disruption Supply chain disruptions caused by the COVID-19 pandemic have increased demand for domestic products and spurred policymakers to consider more manufacturing investments. Increasing Australia’s manufacturing self-sufficiency to 100% could add $180bn in new manufacturing output, boost GDP by $50bn a year, and create more than 650,000 jobs. Adoption of new manufacturing methods using collaborative automation will be a key enabler. Strategic consulting firm AlphaBeta estimates that automation could boost Australia’s productivity and national income by $2.2 trillion by 2030, while leading to the development of new products, services and business models . Collaborative automation can also help reduce manufacturing costs, which remain a roadblock in Australia. It can also relieve workers of dangerous, cumbersome, and otherwise boring tasks, freeing employees to take on higher-value jobs. This advantage is evident at Sanmatsu, a Japanese contract manufacturer. The company paired OnRobot’s RG6 Dual grippers with a cobot to automate a machine tending application. The RG6 extracts and sets parts simultaneously with its dual grippers, speeding up cycle time and lowering machine idle time roughly by half. This eliminates the need to have a worker continuously stationed at the machine, reducing overtime and lowering production costs by 10%. By offering greater flexibility and value, enabling onshoring capabilities, and helping produce higher quality results, I believe collaborative automation will help drive a resurgence of Australia’s once-potent manufacturing industry.
James Taylor is the General Manager – APAC for OnRobot. www.onrobot.com
Putting out fires with gasoline – Navigating changing supply chain dynamics amid COVID-19
The disruption to supply chains has been a business casualty throughout the crisis caused by the COVID-19 pandemic. Louise Bayliss, CEO of Setec, discusses the ways her manufacturing business has navigated the changing dynamics over the past six months.
As a CEO in a manufacturing business with a history that spans more than 50 years, I know the balancing act that goes into guiding and leading a company. A successful enterprise always stands ready to redesign systems and operations in accordance with the current environment, and Setec is no exception. Our history proves a deft ability to remain competitive and strong. In the time now known as pre-COVID, it’s reasonable to say that most industries were cognisant of potential risks and how to mitigate against them. The risk of a natural disaster and its impact to business was well understood. Mitigating the risk of a misplaced shipment was equally recognised. Such potential risks were written into a business plan, ready for action in the event of such risks unfolding. It is, however, a fairly safe assumption that no business plan included a risk mitigation strategy arising from a once-in-100-year pandemic. No one saw this coming. And when we did see the virus creep across the seas in the early days, many believed it to be an isolated incident. Customers called for stock in substantial quantities, stockpiling materials to get through what was considered a small blip to trading. It was hard to gauge the full impact. There is no doubt that COVID-19 has left businesses scrambling. It’s increasingly difficult for CEOs and business owners to brainstorm the next risk point. There is a constant element of second-guessing, an ever-present need to be vigilant and agile against the next wave of coronavirus; its insidious threat vastly affects the supply chain across the globe, largely due to individual countries and their respective governments reacting with varied tactics. At a business level this takes decision-making out of our hands, held instead at the whim of governments, often with little transparency exhibited to industry and communities alike. And the ripple effect caused by these government edicts brings significant pressure to business owners as we struggle with a vagueness to supply chains. Routes that were previously known and reliable are now unknown and unreliable. Materials that might previously arrive within three or five business days can now take two weeks, sometimes three, as carriers are forced to alter routes to cross borders and enter countries in severe lockdown. The challenge this presents to CEOs demands a persistence to attempt to keep one step ahead; a resistance to accepting the status quo. This might take the form of asking the ‘What ifs’ regarding supply chain routes, and ensuring the leadership teams ask them too. It might be as simple as safeguarding multiple sources for your own suppliers or recognising alterations to the movement of your goods. Additionally, CEOs are placed under pressure just to “keep the shingle above the door”. We are left with little choice but to make more conservative decisions regarding investments, raw materials, and supply chains – all with a reduced revenue. Strategic planning and forward-thinking initiatives, seeking growth opportunities, have been paused to focus on something that is wholly unpredictable. It’s like we’re putting out fires with gasoline.
Setec shipped Australian-made BMPRO smart RV systems to a customer in the US in time in spite of supply chain disruptions during the COVID-19 crisis.
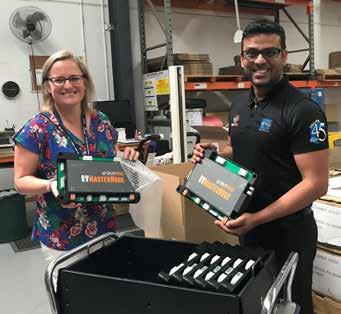
However, even during this insecurity Setec has been proud to be able to serve our customers. Throughout the pandemic, we have navigated blindly, in uncharted circumstances. We’ve split shipments to customers: one section by plane, one by truck, determined to get across the border and into our customers’ warehouses. We are privileged to maintain long-standing relationships with multiple suppliers of particular raw materials, leaving us the option of being able to use different sources as needed. We have invested heavily in building stock so we are equipped and ready to supply our customers consistently and at their need. There will always be gaps, particularly in the current climate, where plans slip and fall. But agility in leadership demands a necessity to rebalance the business. At Setec, we focus on building a rapport with our suppliers, customers and people. I believe it is through the channel of connections that we’ve weathered the most unpredictable and volatile risk in our time.
Louise Bayliss is the CEO of Setec Pty Ltd, a designer and manufacturer of custom-made power supplies for automotive, medical, communications and gaming industries based in Knoxfield, Victoria. www.setec.com.au
Germany: Leaner, greener fire-resistant glass
Although fire-resistant windows already exist, they contain a carcinogenic gel, and their production generates a lot of waste. A new technology is much safer and less wasteful. By rights, this glazing should not work. However, it does - in a way that exceeds expectations. During a fire-test, the glass withstood flames and heat of over 1,000°C for up to 120 minutes. The panes do not contain the carcinogenic acrylamide and it generates just 20kg of process waste a day – far less than the 150kg produced in the past. The glazing contains a transparent gel rich in water and electrolytes between two glass panes. If a fire breaks out, the pane facing the flames does not withstand the heat for long and shatters. This actuates two mechanisms: For one, the water in the gel evaporates and cools the intact second pane. For the other, a heat-insulating salt layer forms.
Fraunhofer/New Atlas Australia: Translating thoughts to actions
World-first and Australian-developed; a human trial has been conducted of a paper-clip-sized device (Stentrode™) which was inserted into a vein in the skull of a paralysed person. This picks up infrared brain signals and wirelessly transmits them so that the person can operate computers and phones with their minds (directed by eye-tracking software). Reading brain signals to operate devices isn’t new (ie EEG head caps). But the Stentrode is placed in a blood vessel. Unlike electrode brain-implants, which produce an immune response that leads to scar tissue around the recording electrodes, the Stentrode™ is biocompatible and is incorporated in the wall of the blood vessel and isn’t in direct contact with the brain, meaning it can keep operating permanently. Synchron Australia was founded as the vehicle to translate the technology from research to commercial product.
University of Melbourne USA: 3D printable, self-healing, recyclable polymers
By tweaking the chemistry of a single polymer, researchers have created a family of synthetic materials that range from ultra-soft to extremely rigid. The materials are 3D printable, self-healing within seconds, recyclable, have shape memory and naturally adhere to each other in air or underwater. Researchers focused on the molecules involved in “crosslinking”. First, they chose a prepolymer, and then chemically studded these prepolymer chains with two types of small crosslinking molecules — furan and maleimide. By increasing the number of these molecules, they found that they could create materials stiffer. Crosslinks are reversible: furan and maleimide pairs can “click” and “unclick” depending on temperature. By modifying the hardware and processing parameters in a standard 3D printer, complex 3D objects were printed, with the layers of vastly different stiffness.
Australia: Cement-free concrete beats corrosion and fatbergs
Researchers have developed an eco-friendly cement-free concrete, which all but eliminates corrosion. Concrete corrosion and fatbergs plague sewage systems around the world. However this zerocement concrete can withstand the corrosive acidic environment found in sewage pipes, while greatly reducing residual lime that leaches out, contributing to fatbergs. The concrete eliminates free lime – a chemical compound that promotes corrosion and fatbergs. Portland cement is widely used in the fast-paced construction industry, but it poses long term durability issues in some of its applications. Making concrete out of this composite blend – rather than cement – significantly improved longevity. The zero-cement concrete achieves multiple benefits: it’s environmentally friendly, reduces concrete corrosion by 96% and totally eliminates residual lime (instrumental in the formation of fatbergs).
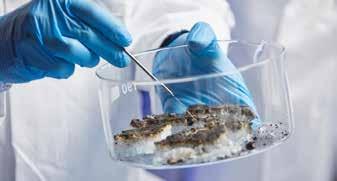
RMIT
Texas A&M University College of Engineering
Left: highly-corroded Portland cement concrete. Right: Zero-cement concrete
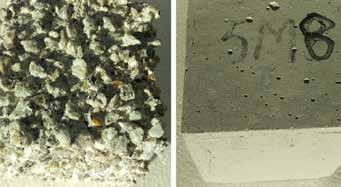
Japan: Metal–plastic 3D printing
Scientists have developed a novel and surprisingly simple method to print 3D structures made of metal and plastic, paving the way for 3D electronics. It a major improvement over the conventional metallization process, in which the plastic object is 3D-printed and then submerged in a solution containing palladium (Pd) and then submerged in an electroless plating bath which produces a metallic coating that is non-uniform and adheres poorly. In contrast, in the new hybrid method, a printer with a dual nozzle is used; one nozzle extrudes ABS whereas the other extrudes ABS loaded with PdCl2. By selectively printing layers using one nozzle or the other, specific areas of the 3D object are loaded with Pd. Then, through electroless plating, one finally obtains a plastic structure with a metallic coating over selected areas only. The technique does not require any roughening or etching of the ABS structure to promote the deposition of the catalyst, unlike the conventional method.
Waseda University
Australia: Affordable solar cells using copper
Sydney startup SunDrive is aiming to produce affordable solar cells in Australia from common materials by replacing silver (which is in limited supply) with copper, which is 1,000 times more abundant and 100 times cheaper per kg than silver. The company, securing $8m in funding, is commercialising its technology and to improve the efficiency beyond the levels attainable with silver. SunDrive is not the first to tackle the problem, but its unique copper processes put it at the forefront. Late last year, the team produced the most efficient commercial-size solar cell ever made in Australia. The business originated from co-founder Vince Allen's PhD at the UNSW, where he was developing a way for copper to stick to the surface of solar cells; creating a method of electroplating the copper, in which it is deposited using an electric current instead of a paste.
Arena/ABC/Fin Review/Smart Company
UK: Wind turbine repair “blade-walker”
BladeBUG and the Offshore Renewable Energy Catapult have announced the UK’s first blade walk by a robot on an offshore wind turbine. The six-legged inspect-and-repair robot repeatedly scaled blades at a demonstration turbine off the coast of Fife. The robot is said to represent a 30% cost reduction based on lifetime blade maintenance and is predicted to reach up to 50% for next generation turbines. These costs have been a primary concern for offshore operators, as sea conditions and faster tip speeds can lead to significant blade damage. During the demonstration, the robot walked 50 metres on a vertically positioned blade (a length of 84 metres with the tip reaching 195 metres above the sea when upright). Capabilities demonstrated were the ‘perfect’ adherence of its vacuum-packed feet to blade surfaces in offshore conditions, the ability to navigate the varying curvature of blade surfaces in a variety of scenarios, and transmission of data from blade scans and live video feed to technicians.
The Engineer Australia: Loyal Wingman drone completes taxi test
Partnering with Boeing Australia, Queensland will be the production home for unmanned defence aircraft – the first military aircraft to be designed, engineered and manufactured in Australia in more than 50 years. The first aircraft prototype, the Loyal Wingman drone, unveiled last May, has completed its milestone low-speed taxi test in October where it successfully demonstrated the ability to stop and manoeuvre on command. This is part of preparations for the first flight, which is expected by the end of the year. This aircraft and the other prototypes will be unmanned with fighter-like performance and the ability to fly 3,700 nautical kms.
Mirage News/mixed UK: New technique for producing biocompatible glass
Researchers have applied a new low temperature (<250°C) processing technique to bioactive glasses which could be used to repair human tissues in a safe, sustainable way. The idea came from the concept of the cold sintering of ceramics. In addition to densifying a range of specialist glasses, cold sintering is of particular interest for bioactive glasses such as Bioglass®, which are biocompatible and widely used in the medical sector. The advantages of using this process to densify Bioglass® are many - including the potential for drugs to be embedded in the Bioglass® before densification. Cold sintered glasses can be used to coat surfaces and stick together a wide range of materials, including other glasses, ceramics, composites and metals. The potential of this technology will hopefully allow the exploration of new functional glass and polymer composites hitherto thought impossible to manufacture.
Italy: World's first 3D-printed fibreglass boat
Moi Composites has unveiled the MAMBO (Motor AM Boat), which is reportedly the world’s first genuine boat 3D-printed in continuous fiberglass thermoset material. It is 6.5 metres long by 2.5 metres wide; includes a navigation system and 113-horsepower engine. The various sections were printed using two Kuka Quantec robots at Moi Composites’ headquarters in Milan, and in Autodesk's Advanced Manufacturing Facility in the U.K. The boat was digitally crafted with patented CFM. This allows the creation of fibrereinforced products with mechanical characteristics comparable to those of unidirectional fibreglass, without the aid of models and moulds. It is thereby possible to obtain real products in small lots or unique pieces, efficiently and cost-effectively with customisation and high mechanical performance not available through traditional manufacturing. The material makes products durable and lightweight, and the robotic system allows for scalability in print size.

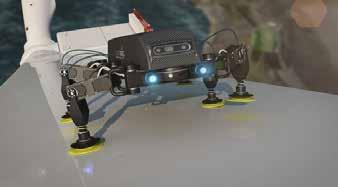
The Fabricator
University of Sheffield Redirecting lightning
“We have an invisible thread, a pen with which we can write light and control the electrical discharge to within about one tenth the width of a human hair" Prof. Andrey Miroshnichenko, UNSW, speaking about new laser tractor beam technology developed by an international team including the UNSW and ANU. The team used a laser beam that mirrors the same process as lightning and creates a path that directs electrical discharges to specific targets. It works by trapping and heating graphene microparticles in the ambient air and heating those particles trapped in the beam; thereby creating the necessary conditions for electric breakdown and transmission along the laser's path. The team used a laser intensity a thousand times less than that in any previous attempts, meaning any potential technology to control lightning could be much cheaper, safer and more precise. The discovery also has potential for the micro-scale control of electrical discharge in medicine and manufacturing.
