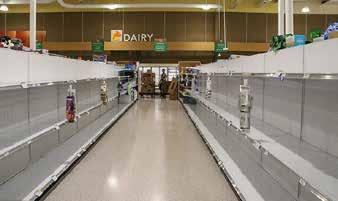
18 minute read
AMTIL FORUMS
from AMT DEC/JAN 2021
by AMTIL
How to set up your business for success in export markets
Philip Smith outlines five top tips to set up your manufacturing business for exporting success.
Are you a manufacturing business looking to export, but unsure about where to begin? As the Government’s export credit agency, we provide financial solutions to help Australian businesses take on the world. Working across a range of industries for more than 60 years – such as manufacturing – we understand the domestic and global markets. Here are our five top tips to give your manufacturing business the best chance for export success. 1. Ensure you have enough cashflow For many manufacturers who export, there is often a long lead time from the point of delivery until the receipt of payment. This could greatly impact your cashflow. To address this, try to arrange more favourable payment terms with your long-term customers. Another solution may be arranging external finance to maintain cashflow and your operations moving. Understanding how to manage your export cashflow will be a big help. 2. Get ahead of customer demand Winning a major contract or experiencing high customer demand is a positive outcome for any business. While this may boost your profits, it may also mean you need to ramp up your operations quickly to meet a sudden spike in demand. This could involve ordering more inventory or hiring more employees and you may need additional finance. To help, Export Finance Australia offers a range of financial solutions that could support your business to take on these new opportunities.
Case study: Nature’s Dairy Australia One of our customers, Nature’s Dairy Australia, is a business which locally sources, manufactures and packages milk from across Victoria. Approximately 65% of what they produce is exported to Asia. But as a relatively new business, they needed financial support to help them meet the growing international demand. “Nature’s Dairy Australia being only a few years old, we have a huge amount of growth ahead of us,” said their Chief Executive Officer, Bevan Tippett. “But all of that comes with cashflow implications, and so we needed some assistance to fund that continued growth of the business. That’s how we came to talk to Export Finance Australia.” Our $2.6m Export Line of Credit facility is helping Nature’s Dairy Australia finance the working capital funding requirements of their business operations, particularly as sales volumes increase. This enabled them to develop new products and fund equipment specifically for exports – while meeting international demand.
3. Develop your export strategy If your business is in expansion mode, you may be looking to branch into new markets. But remember, each market has its own challenges and risks. When targeting a new export jurisdiction, it’s important to do your research. Understand the trade laws, banking systems and the reliability of their shipping and delivery schedules. This should all form part of developing your export strategy. 4. Seize international opportunities To export successfully, your business needs to be open to international markets and seize those growth opportunities. This will require you to build strong business relationships in your overseas markets or in your supply chain. You may even need to set up physical offices or shops in key markets, or import your materials. Making sure you have access to the finance you need is crucial in expanding your business internationally.
Case study: BirdDog Australia BirdDog Australia designs and builds high-grade cameras and livestream software for homes, offices, education institutions, stadiums and houses of worship around the world. As the demand for video capability dramatically increased during COVID-19, BirdDog Australia absorbed the pressure on their supply chain and manufacturing business operations. Having identified the need to fund growth with additional cashflow, BirdDog Australia was recommended the support of Export Finance Australia. Our Victorian Business Development team worked with BirdDog Australia to understand their business and helped them secure the right financial solution. We provided a working capital facility to assist BirdDog Australia increase its manufacturing output, maintain large orders and keep up with growing demand. Our support also meant that they could win business opportunities for international growth. “Without Export Finance Australia, we would have merely grown at a moderate rate, and missed out on export opportunities across the globe, thereby stifling the business and our trajectory,” said their Chief Financial Officer and Finance Director, Barry Calnon. “We’re going to keep growing and enjoying the support that Export Finance Australia have given us.”
5. Protect against risks Working in overseas markets could expose your business to a range of risks. Researching on country profiles could help you understand the different risks of doing business around the world. Particularly with financing, it’s important to negotiate payment terms that work for you – for example, securing a deposit up front. You should also choose a robust payment method to protect yourself from any payment risks. Our range of financial solutions, including loans, bonds and guarantees, cold help your business offset such risks. Talk to us. We’re helping manufacturing businesses take on the world, and we could help you. Talk to us about our range of financial solutions. Call our experienced team on 1800 093 724 or visit our website
Philip Smith is Business Development Director, VIC & TAS, Export Finance Australia. www.exportfinance.gov.au
Calculating ‘safety stock’: the key to minimising supply chain risk
Panic-buying earlier this year and the resultant empty supermarket shelves have highlighted the importance of determining appropriate inventory levels. Levi Martins explains.
The retail surge of March 2020 saw a rise of 8.5% in retail trade according to the ABS, the strongest rise since it began tracking retail trade. Whilst the panic buying saw empty shelves in supermarkets, what often goes unseen are the Australian manufacturers behind the scenes struggling to fill this unprecedented demand. Determining appropriate inventory levels is one of the most important and most challenging tasks faced by supply chain managers. If you carry too much inventory, you tie up money in working capital and risk writing off perishable goods; if you don’t carry enough inventory, you face stockouts. What Is Safety Stock? In any supply chain planning, safety stock (sometimes known as ‘buffer stock') is extra stock to cover demand or supply variability and to avoid stockouts. Think of safety stock as serving as a type of insurance against unplanned supply chain events. For example, a supplier may deliver their product late, the warehouse may be understaffed or items may be received that are below the usual level of quality. There’s also the chance that a competitor may be sold out on a product line, which leads to increasing demand for your own product. The cycle stock portion of the inventory equation might be straightforward. But what really keeps people up at night is safety stock, and how to determine the appropriate level. Safety stock enables organisations to satisfy customer demand in the event of these variables. Panic buying during March and April of 2020 saw many manufacturers facing high levels of variables, forcing rapid changes to the planning process to meet increased demand. Some operations managers rely on gut feelings or hunches to set safety stock levels, while others base them on a portion of cycle stock levels — such as 15 or 25%. While they are easy to execute, these techniques generally result in poor performance or leave you with other stock management issues. Perishable products make the game even more challenging because they are particularly susceptible to spoilage, especially if there are improper storage conditions. Safety stock determinations are not intended to eliminate all stockouts—but they can reduce many of them. While designing for a higher service level would result in fewer stockouts, this requires significantly more safety stock. There must be a balance between inventory costs and customer service. By using different methods and equations, you can still find safety stock levels that help you achieve your desired customer service levels. Safety days of supply Being profitable in these scenarios is reliant on the proper management of inventory, and this is where supply chain planners are the behind-the-scenes rock stars. Using a formulaic approach to safety stock helps rationalise the required levels of inventory to the business, while balancing the need to deliver on customer service and minimising costs of higher stock on hand levels. Inventory issues are one of the biggest problems impacting profitability in manufacturing. Developing production plans by simply dividing annual demand by the number of forecast periods has been the approach for many food and beverage companies, but this doesn’t take seasonality, trends, cost of production and carrying costs into account. Other companies will base their figures on "safety days of supply” (or safety coverage). The days of supply refers to the number of days of demand that your safety stock can service. The days of supply may include the inventory held to satisfy certain and uncertain demands. To calculate how much you should produce or purchase against safety days of supply, you need to sum the projected demand for the next “safety days” number of days. Once you’ve set a safety days coverage, you should also calculate your number of days of supply. This is calculated against your current holdings, asking the question “If I didn’t receive any other supply, how many days would I have before running out of stock?” Sadly, Excel (which is the number one tool used by supply chain planners) doesn’t have the simplest formulas to calculate Safety Days or Days’ Supply. This means planners tend to use static approximate safety stock calculations, since this is what they can produce in a spreadsheet. Supply chain planners need an easy-to-use system that can perform the calculations quickly and generate credible results. Improving the supply chain planning process One way to simplify the process around safety stock and general stock planning is to use the right tools. That way, you can not only stay on top of planning, but take advantage of other features to fine-tune your forecasting. The biggest benefit of having a tool for supply chain planning, among other features, is being able to clearly see the stock levels and quickly calculating safety days in one application, such as the customisable TilliT Planner designed to address production planning challenges.
SAGE Group company Nukon specialises in delivering digital transformation for companies and has a number of clients who already use their advanced planning solution - TilliT Planner - to address production planning challenges. When developing this part of software suite, the team at Nukon made sure safety days of supply was one of the features. TilliT Planner can draw on the real-time existing stock levels and customer demand to calculate the correct stock you will need to be covered. All calculations are made for you, instead of having to refer to multiple spreadsheets and formulas. Levi Martins is a Senior Consultant at Nukon. www.nukon.com
Return to work – Managing COVID-19 risks What COVID-safe practices should a business implement if their workers cannot work from home? Rob Jackson explains.
As COVID-19 infection rates drop dramatically, Victorians welcome back normality. Or something close to it. Since 11.59pm, 8 November, metropolitan Melbourne entered the third stage of reopening, in line with regional Victoria. Manufacturers, like all employers, must be vigilant in managing COVID risks before re-opening the doors. Manufacturing workers cannot work from home, and the layout of a factory may make physical distancing difficult to achieve. So, what should a business do? Get a COVIDSafe plan Every Victorian workplace must have a COVIDSafe Plan based on six key principles: 1. Physical distancing, where work is performed 1.5m apart, and the 4sqm rule is applied. Continue to work from home, if possible. 2. Wear face masks with the provision of face masks and other personal protective equipment (PPE). An employee must wear face masks. 3. Good hygiene practices by supplying effective sanitiser, ensuring frequent surface cleaning. 4. Keep records of all people (workers, visitors, customers, suppliers) who enter the workplace. 5. Avoid interaction in enclosed spaces, and where possible enhance air flow. 6. Create workforce bubbles to minimise cross-infection between the workforce, staggering work start and finish times, and lunch breaks. A manufacturer within metropolitan Melbourne must also keep cleaning logs, provide PPE training, ensure daily cleaning for all areas accessed by workers and clean between shifts. A worker must declare they are free of COVID symptoms before starting work. Further, manufacturing is one of seven designated ‘high risk’ industry sectors. The other five are closely related to manufacturing: warehousing, supermarket and chilled distribution, postal, and wholesale. The remaining sector is the care industry. All sectors, apart from manufacturing, must have a High Risk COVIDSafe Plan, unless involved in meat and seafood processing. Construction, pharmaceutical and medical suppliers are no longer considered high risk industries. A new initiative is the COVID Marshal to ensure somebody has specific responsibility for complying with a COVIDSafe Plan. Marshals must be appointed to all Victorian abattoirs and meat processing facilities, and to all Melbourne-based supermarket and chilled distribution centres. Also, public gyms, casino and gaming facilities must have COVID Marshals. For all other sectors, such as manufacturing, a COVID Marshal is recommended. A COVID Marshal must do what any safety-conscious business should already be doing - proactively managing workplace safety. To support manufacturers in their return to work preparation, in addition to information on numerous websites and telephone support lines, free accredited infection control training has been made available to employers in a high risk industry. (1) Day one A business should induct returning workers as if they are new starters and this includes all employees: casuals, part-timers, volunteers, labour hire employees, and also contractors. The return presents a valuable opportunity to consult and discuss safety. Keep attendance records; ensure individual responsibilities are clearly allocated in writing concerning for example hygiene practices and face masks, distancing in the lunchroom, visitor protocol, keeping a register. Workers will be distressed by lengthy absences from workplace due to social isolation, family responsibilities, childcare, elderly parents, family discord and many other factors. An employer must anticipate these risks, and have counselling services available. Psychological risks are as important as the physical risks, and form an important part of a business’ risk management strategy. Poor management practices will increase legal risks such as bullying or WorkCover claims. It is important supervisors and managers are supported to look after their own health, before they try and deal with an employee’s distress displayed in the workplace. Working from home has benefits: no commuting, no interruptions, no risk of infection. Or, carer or family responsibilities may dictate staying at home, prompting a request for flexible working arrangements under the National Employment Standards. Or a business may restructure its business model to rely on home-based working. This may give rise to an obligation to consult under an award or enterprise agreement. Checking and updating the employment contract is also wise. A sick employee, however minor the symptoms, must stay away from workplace, and obtain medical advice. An employer may provide financial support, or seek government assistance. An employer has an obligation under section 22 Occupational Health and Safety Act to monitor the health of employees and workplace conditions, and provide information in appropriate languages. An employer must not turn a blind eye. And if there is a positive case, an employer since 28 July 2020 must notify WorkSafe of a ‘confirmed COVID-19 diagnosis’ by calling WorkSafe immediately on 13 23 60, and submitting a written notification within two days. Fines can be imposed for a failure to notify. Future trends There is no going back to the pre-COVID normal workplace! Employers and workers have learnt what can be achieved away from the workplace, leading to a questioning of what the postCOVID workplace will look like. The Australian Council of Trade Unions is calling for a right to Work From Home, relying on a recently published survey of 10,000 employees. Enterprise bargaining is likely to see such clauses negotiated. A manufacturer will need to stay a step or two ahead on safety, and not just perform the minimum required by law. What will your business do? Think now, and consider not only the risk of infection in its own right, but also of the human effect, on workers holistically as part of a risk management system.
Rob Jackson is a Partner in Rigby Cooke’s Workplace Relations, International Business and Manufacturing groups. Rob has extensive experience in employment and industrial relations, occupational health & safety, workplace investigations and employment related migration. Ph: + 61 3 9321 7808; E: RJackson@rigbycooke.com.au www.rigbycooke.com.au
(1) See generally www.coronavirus.vic.gov.au
How COVID-19 lockdowns are affecting communities mentally Brendan Torazzi takes a closer look at the mental impact of COVID-19 lockdowns, the signs to look out for, and the advice and resources available.
The first case of coronavirus in Australia was reported on January 25, 2020. By the end of October, the country had over 27,000 confirmed cases, many in Victoria. As the biggest city in Victoria, Melbourne was hit by the coronavirus particularly hard. Officials even imposed a curfew between 8 pm and 5 am to help contain the virus. The lockdowns may have helped slow the virus, but they also took a toll on people’s mental health. The signs to look out for while adapting to the “new normal” Coronavirus restrictions were first nationwide in March and April. Victoria introduced additional lockdown conditions at the beginning of July as the daily case count rose. Metropolitan Melbourne endured a long period in stage four. Fortunately, the government has now eased some restrictions, but many remain in place. When Melbourne entered stage four of the lockdown in September, the government also had a curfew in place and heavy restrictions on travel. These restrictions are designed to slow the spread of the coronavirus. Unfortunately, dealing with these restrictions can lead to a wide range of physical and mental health issues. Understanding the psychological impact of lockdowns Social isolation and the anxieties related to the coronavirus have taken their toll on people from all walks of life. Staying indoors and isolating from others is known to create a wide range of negative effects, such as an increased risk of: • Depression • Anxiety • Stress • Cognitive decline One study found that about 35% of people experienced some form of mental distress at the start of the pandemic. The pandemic enhances people’s anxieties. However, lockdowns may add to the problem. When people are forced to stay home, the limited socialisation they receive may not be adequate. People are more likely to become withdrawn and despondent, which leads to depression. Limited social contact and confined spaces are also known to increase the risk of cognitive decline. How to detect mental health issues in yourself and others People are generally good at hiding their feelings, which can make it difficult to detect mental health issues. You may even lie to yourself about your own mental health. Here are some of the signs that you should look out for in yourself and others: • Loss of appetite • Restlessness • Lack of interest • Muscle tension • Fatigue • Anger • Reckless behaviour • Lack of concentration Some signs may be subtle while others are more obvious. The main thing to watch for is changes to a person’s overall demeanour. When people suddenly change their attitude or behaviour, there is likely an underlying cause, which may be related to a mental health issue brought about by the lockdowns. What can you do to help protect against mental health problems? If someone is experiencing suicidal thoughts, do not hesitate to contact medical professionals or a suicide hotline. However, some situations are less urgent, such as helping someone through their depression or anxiety. To help yourself or others cope with the negative aspects of social isolation and coronavirus restrictions, find distractions. Taking up a new hobby which interests you can help keep the mind busy, which is one of the challenges of isolation. Maintaining a routine is also helpful for dealing with lockdowns. Following a routine provides structure and gives you more control over your daily life. This leads to a greater sense of self-reliance, which may ease anxiety. Exercise is also a top recommendation for protecting against mental health. Getting your blood pumping provides oxygen to the brain and promotes better cognitive function. With a healthy body, you are more likely to have a healthy mind. Do the benefits of lockdowns outweigh the costs? The lockdowns have led to a spike in depression, anxiety, and other mental health issues. However, the alternative to the lockdown is allowing the virus to spread uncontrollably. The coronavirus has already cost the lives of over 900 Australian citizens. Without social distancing, masks, and the closing of nonessential services, there would likely be far more deaths and hospitalisations from the virus. Mental illness is a serious issue, but the loss of life is also significant. There are resources available to help those who are suffering from depression and anxiety due to social isolation and the fear of the virus. However, there are no resources for bringing people back from the dead. What can we learn from this whole situation? The coronavirus was a wake-up call for many, as it showed the strengths and weaknesses of the way that governments responded to a pandemic. If anything, the situation has taught the public that limiting the spread of a virus requires sacrifices. For the greater good of the country, people may need to deal with continued restrictions on travel, work, and socialisation. However, there should also be help available for those who are suffering from mental health issues brought about by the restrictions. If the country continues to stay locked down, continue to pay attention to the signs of mental health in yourself and others. Do not hesitate to receive help when necessary, even for symptoms that may appear minor, such as depression. Suggested websites of companies specialising in mental health are listed below.