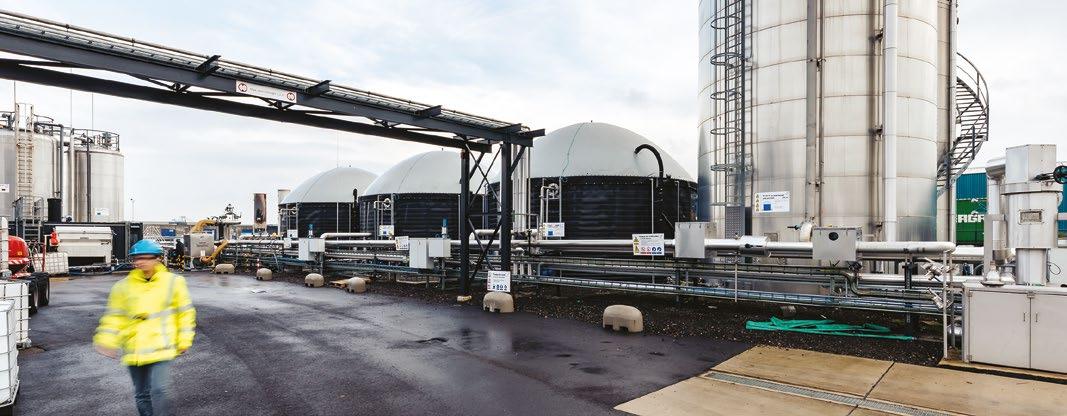
6 minute read
How to make supply chains more robust and sustainable?
NEW THINKING ON BIG QUESTIONS | FEED INGREDIENTS & ADDITIVES
Replacing production processes based on petrochemicals or oleochemicals with fermentation to make feed additives – ChainCraft
Advertisement
As the industry has moved away from the use of antimicrobials, many have turned to short- and medium-chain fatty acids as an alternative to help regulate the microbiome and maintain good gut health. However, these feed additives are currently made from either petrochemicals or palm oil. Now, a spin-off from Wageningen University in the Netherlands has found a way to ferment organic residues into a feed-grade product containing C6 caproic acid and C4 butyric acid.
According to Niels Van Stralen, Director and Co-founder of ChainCraft, this move to fermentation-based production has various environmental advantages. First, it has a lower carbon footprint and less energy-intensive production process; second, it provides a higher-value application for a low-grade waste stream.
Beyond that, it also has the advantage of being less dependent on the same volatile feedstocks as the traditional production process, meaning that events such as a ban on palm oil exports would not cause a supply chain shock. Moreover, a fermentationbased process also makes small-scale production of these products economically feasible, and makes it possible to locate production outside of large, centralized chemical production complexes, which is a win for both sustainability and supply chain robustness. “We can produce these chemicals locally. We are producing them in Amsterdam instead of in Malaysia or Indonesia.”
Finally, and perhaps most excitingly, the company claims it can offer this more sustainable product at a competitive price to traditionally-manufactured feed grade fatty acids, meaning that this will not be an innovation limited to niche applications, but should be accessible to all.
ChainCraft has already begun marketing its product, made in its 2,000 tonne per year facility in Amsterdam. The company is looking to begin construction on a facility about 10 times larger in 2024, and expects to bring this online in late 2025.
A BROADER VIEW:
The advantages that fermentation-based production processes can provide are being explored in other feed additive categories as well. DSM has recently announced a breakthrough in fermenting vitamin A, although the initial application for this technology will be in cosmetics rather than in animal nutrition. Meanwhile, CJ Cheiljedang has been making bio-methionine since 2015, the only producer of this amino acid to use a fermentation-based production process.
Bringing circular economy principles to the phosphates market – EasyMining
Mineral phosphates are essential for both crop production and animal nutrition, and they are a finite resource. Swedish firm EasyMining has a process for closing the nutrient cycle, recycling these precious materials from municipal waste and making them available for agriculture once more.
According to Dr. Sara Stiernström, Product and Market Developer for EasyMining, this involves incinerating municipal waste biosolids to produce a mineral concentrate free of microbiological or other organic contaminants, and then applying a proprietary “Ash2Phos” process to recover precipitated calcium phosphate with a lower heavy metal content than that of phosphates derived from mineral deposits.
Beyond being “cleaner” in the sense of contaminants, recycling phosphates from waste in this way has many virtues. Phosphates emissions into the environment can cause eutrophication, disrupting the natural ecological balance; EasyMining’s concept thus extracts a valuable product from an ecologically problematic waste stream. Moreover, not only are Earth’s mineral phosphate resources finite, but they are also unevenly distributed. Recycling phosphates from waste locally would mean that places without natural endowments of rock phosphate could become less dependent on imports from the few countries which produce and export these products. It would also reduce the greenhouse gasses emitted in the long-distance transport of these ingredients.
EasyMining is planning plants in Germany and Sweden, which are expected to start up in 2024 and 2025. Both will process some 30,000 tonnes of ash per year into 15,000 tonnes per year of dry precipitated calcium phosphate. Longer term, Stiernström believes the company may look to license the process.
A BROADER VIEW:
Unfortunately, animal nutrition products obtained from wastewater cannot be used in the EU, regardless of the processing they have undergone to ensure the safety and quality of the final product. Therefore, barring any change to this regulation, EasyMining’s home market (and a key livestock producing region without natural phosphate resources of its own) is currently off limits. Stiernström calls for animal feed companies to add their voices to the call to authorise recycled phosphates use as the EU pushes forward on other circular economy plans for the agriculture industry. “We cannot do this alone…this is not something one company can change,” she says.
Single-cell proteins from fossil-fuel-free carbon – Gas2Feed
Demands for feed proteins such as soy and fishmeal have put strains on the world’s oceans and forests. Norway’s Gas2Feed seeks to replace those with a single-cell protein made from exotic microbes naturally found in geothermal hot springs, microbes which produce their biomass from hydrogen, oxygen, and CO2. According to Dr. Vukasin Draganovic, Business Development Director, the resulting ingredient has a lower CO2 footprint than other aqua feed proteins such as soy protein concentrate or fishmeal. While the concept of using single-cell protein in animal feed is not new, Gas2Feed’s process is distinctive in terms of where it sources its inputs. First, the CO2. The company has novel plans to capture some of this from the biological emissions of the RAS fish farms it is partnered with. “Fish exhale CO2 as we do. We’re working together with an institute in Trondheim in Norway called SINTEF, and looking at ways to extract the CO2 and use it in the protein production.”
If that does not cover the process’s requirements, Draganovic says Gas2Feed will source CO2 using a direct air capture concept, rather than using emissions captured from an industrial source and purified. “You could get the CO2 from industrial waste gasses…that would be the easy target, relatively easy to get, and these bacteria can also tolerate a certain level of impurities. But this is not our intention; we would like to get a kind of biogenic CO2.” he asserts. Beyond the CO2, the other two inputs, hydrogen and oxygen, will be derived from splitting water, using electrolysis technology from Gas2Feed sister company HydrogenPro.
Founded in 2020, the Norwegian startup is in the process of extending its small pilot plant in Risavika to reach 1,500l of production capacity in 2023. Beyond that, Gas2Feed has its eyes on a demo plant, followed by a 20,000-tonne commercial-scale plant planned tentatively for 2026.
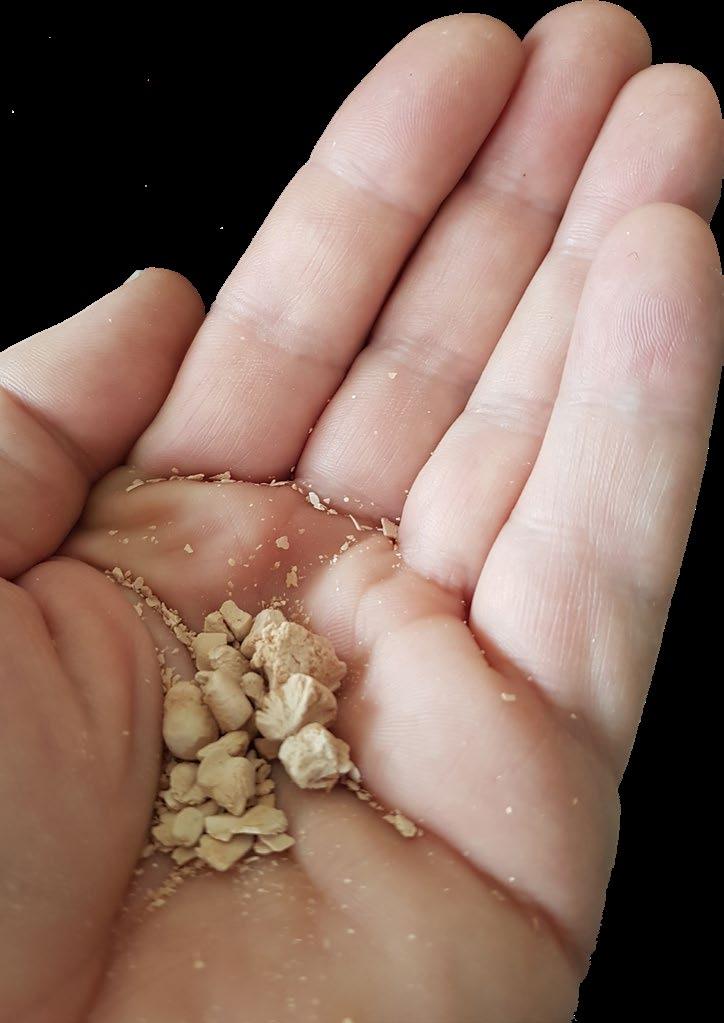
A BROADER VIEW:
While Gas2Feed is pre-commercial at this point, other single-cell protein concepts are being manufactured and sold into the feed industry. To cite just two examples: Calysseo, a joint venture between Adisseo and Calysta, announced this June that commissioning and start-up activities have commenced at its first industrial-scale facility in Chongqing, China; meanwhile, Unibio began supplying commercial customers with its single-cell protein late last year.
By Shannon Behary, senior editor
AUTUMN 2022 | 9