
5 minute read
INNOVATION IN HARMONY: The AdventHealth Innovation Tower and the Collaboration Behind Its Creation
PHOTOS COURTESY OF BATSON-COOK CONSTRUCTION
The Batson-Cook tradition of building a strong relationship with their clients is well expressed in their relationship with AdventHealth. Over the past few years, the two companies have completed nearly a dozen projects throughout the Central Florida region, including several offsite emergency rooms. One of the larger projects they’ve collaborated on is the AdventHealth Innovation Tower in Orlando, Florida.
This new, 12-story, 330,000 SF medical office building on a fiveacre site next to I-4 in downtown Orlando will provide several health services to the community. The facility hosts a brain health institute, AdventHealth Innovation imaging center, ancillary specialists, Orlando specialties, research administration, rehab center, conference center, retail pharmacy, and shell space for future tenant development.
The Innovation Tower exterior can be split into three sections, a concrete center in between two concrete shells. The concrete center has gray metal panels with vertical glass windows in a checkered pattern that runs up the middle of the building. If the concrete trucks used for the building were lined up end-to-end, they would stretch 11 miles. Approximately 95,000 SF of glass was installed in the building. The site is also in a tight space, surrounded by I-4, an occupied apartment complex, and an 11-story parking garage constructed at the same time as the tower. The team took precautions to minimize the impact on their neighbors during the construction phase of the project. Additionally, HuntonBrady designed the exterior façades to evoke the feeling of movement with the shift and flex of the building’s appearance, inspired by the orthopedic services inside the building. Those unique angles made installation of exterior finishes on the façade challenging. The east and west sides of the façade are angled two degrees in opposite directions, creating an approximately seven-foot difference between the bottom and top of the building’s precast. This required using a special counterweight sled to place the material during installation.
As with most large-scale construction projects, there were several logistical challenges the team had to consider and overcome. One was the large parking deck. The Batson-Cook team provided the building pad for the parking garage, then turned that portion of the site over to the parking garage general contractor. Trey Miller, assistant project manager, said, “A parking garage was being built by another general contractor directly adjacent to our site and they were sharing a common access road with them for deliveries. The field staff coordinated with the other contractor daily and held weekly project meetings to ensure we were fully utilizing the site.”
Communication was key to having two independent companies working on two structures simultaneously on a small site. The Batson-Cook project staff had coordination meetings with the parking garage general contractor every few days to schedule deliveries and other logistics to help facilitate both projects.
The team also found ways to innovate and enhance safety measures on the project. Some include multiple cameras on each tower crane for their operators to better see the objects they are pulling, full deployment of the EPS edge guard system for edge of slab and shaft protection, and cast-in-place tie-off anchors throughout the building.
The project scope included a structural steel pedestrian bridge connecting the tower’s second floor to the parking garage. The pedestrian bridge provides visitors with safer and easier access to the Innovation Tower building. Batson-Cook created a thorough safety plan for the pedestrian bridge and held proactive safety meetings throughout the process, which included the foreman from the steel erection companies, safety heads, project managers, and relevant executives. The Batson-Cook team also ensured that the area around the building and under the bridge was blocked off to pedestrians. Any road shutdowns were coordinated with trade partners in advance so that they could move materials and adjust their workflow accordingly. The Batson-Cook safety philosophy discusses work methods, assesses risk, and agrees on controls and procedures. They could focus on anything that could happen unexpectedly.
Any large-scale construction project can be disruptive, so BatsonCook’s approach is to consider themselves as a member of the surrounding community and neighborhoods they work in. The goal is to minimize the impact construction has on their daily life. Continuous coordination was required with the surrounding businesses and services, primarily medical and residential. The goal is to minimize the impact construction has on their daily life. Throughout the project, they constantly ensured they did everything possible to be good neighbors to the surrounding community.
This project was a private and public partnership for AdventHealth’s Health Village and its community development district. A portion of the project site was located on historic Orlando brick streets. To assist the city’s future restoration efforts, the Batson-Cook team completed selective demolition of the original brick streets. They removed all pavers from the city streets by hand and then cleaned, stacked, and returned them to the city for future use.
At the end of the day, Batson-Cook safely completed a $101 million quality project on schedule. The team found it rewarding to have worked on Innovation Tower and AdventHealth and contributed to the larger vision of their Health Village campus. The landmark tower project is a beautiful job that will serve the community well into the future.
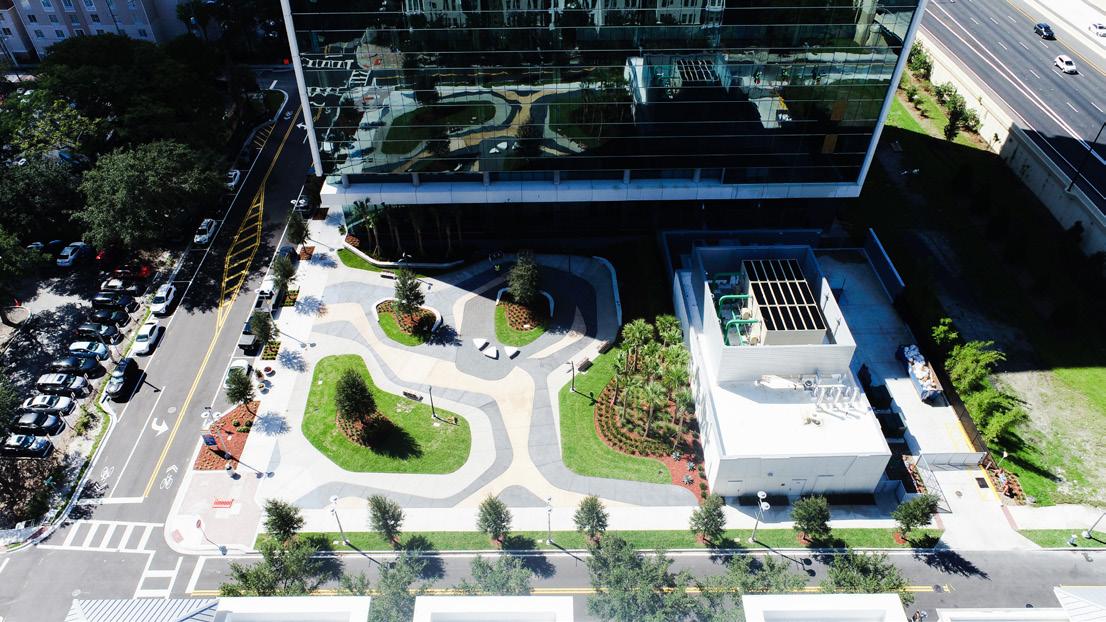
Central Florida Chapter MEMBERS
Acousti Engineering Company of Florida
Boys Electrical Contractors, LLC
BrightView Landscape Development, Inc.
Century Fire Protection
Coastal Mechanical Services, LLC
Collins Construction and Company, LLC
David Allen Company, Inc.
Fabco Metal Products LLC
Gate Precast Company
Hartford South, LLC
Hudson-Everly Commercial Flooring, Inc.
Interior Specialties, Inc.
Mills & Nebraska
Percopo Coatings Company, LLC
SMI Cabinetry, Inc.
Smith Fence Company
Spectra Contract Flooring
The Stowell Company, Incorporated
Tri-City Electrical Contractors, Inc.
