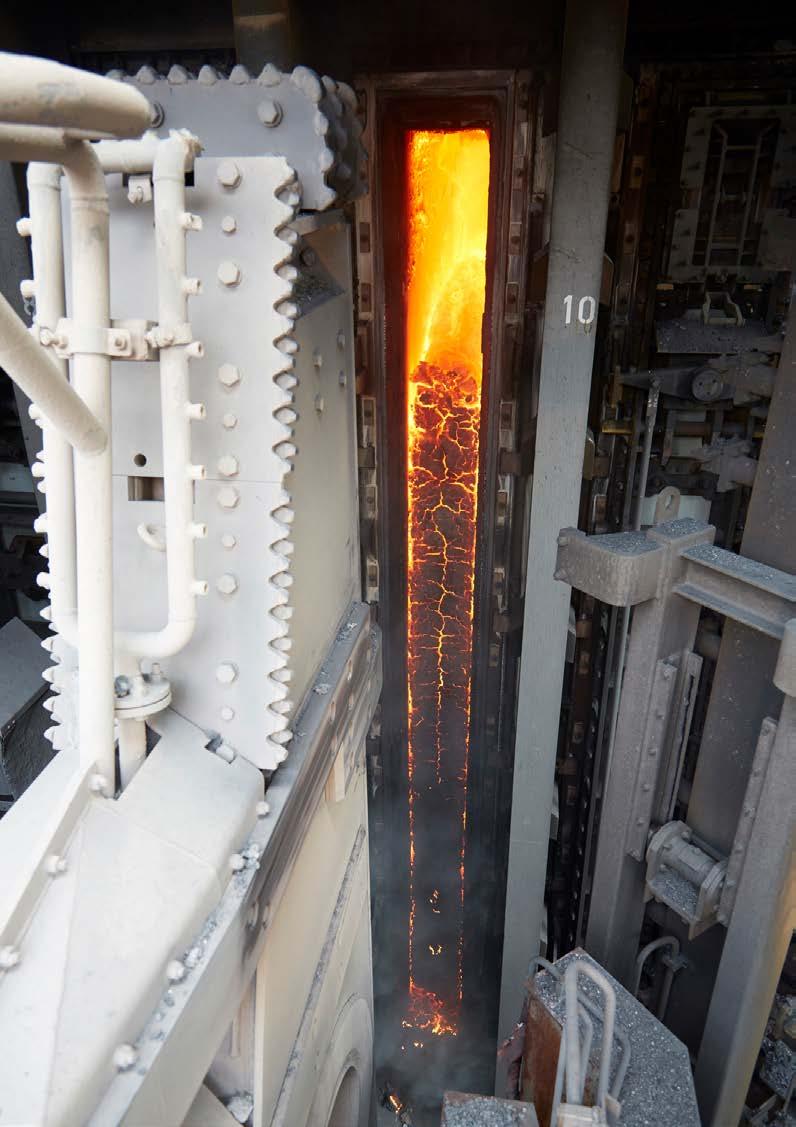
6 minute read
Klimaatneutrale productie begint bij ‘groene’ materialen
De weg naar klimaatneutrale productie begint bij ‘groene’ materialen
Om de CO2-footprint in de hele keten van de metaalverwerkende industrie te verlagen, is het essentieel om hoogovens ‘groener’ te maken. (foto: worldsteel thyssenkrupp steel)
De opwarming van de aarde is een van de belangrijkste milieuproblemen waarmee de wereld vandaag de dag wordt geconfronteerd. De internationale industrie heeft een grote invloed op de uitstoot van broeikasgassen en zal dus een sterke bijdrage moeten leveren aan de klimaatdoelstellingen. Aangespoord door het Klimaatakkoord, waarvan het belangrijkste doel is om de CO2-uitstoot in 2030 met 49% te verminderen, staat de industrie aan de vooravond van grote veranderingen.
Veel maakbedrijven zijn eigenlijk al op de goede weg om het energie- en materiaalverbruik te reduceren. Indirect wordt hiermee ook de CO2-footprint verkleind. Deels komt dit omdat bedrijven zelf de noodzaak zien voor het terugdringen van het verbruik. Daarnaast, en dat is een heel actueel thema, dwingen de hoge energie- en materiaalprijzen producenten om kritisch naar het verbruik te kijken. Er zijn inmiddels veel praktische oplossingen die producenten kunnen helpen. Denk aan zonnepanelen, efficiënte machines, lichtsnijdende gereedschappen met een hoge standtijd en energie-efficiënte bewerkingsstrategieën. Echter, omdat bedrijven sterk van elkaar verschillen op het gebied van bedrijfsprocessen en bedrijfsvoering en in sommige gevallen nog geen strategie hebben ontwikkeld om het verbruik te reduceren, zijn er grotere stappen nodig om de doelstellingen te behalen. Om de CO2-footprint in de hele keten van de metaalverwerkende industrie te verlagen, is het verduurzamen van het productieproces van juist datgene wat elk metaalbedrijf nodig heeft en gebruikt het meest efficiënt: Namelijk de productie van staal in hoogovens.
Recycling van CO2 in hoogovens
Hoogovens behoren tot de grootste uitstoters van broeikasgassen. In Duitsland, de grootste staalproducent in de EU, is ongeveer een derde van de CO2 die door de gehele industrie wordt uitgestoten, afkomstig van hoogovens. De Universiteit van Duisburg-Essen (UDE) heeft een alternatief proces ontwikkeld dat de CO2 recycled. In de komende decennia zullen de grote staalbedrijven overschakelen op duurzamere installaties, waarbij het omzetten van ijzererts in ijzer niet meer zal worden gedaan met aardgas, maar met behulp van waterstof. Het daaropvolgende smelten zal met regeneratief geproduceerde elektriciteit worden verricht. De verwachting is dat de daaruit voortvloeiende CO2-emissie ongeveer 30 kg per ton ruwstaal zal bedragen en daardoor verwaarloosbaar is te noemen. Echter kan het tientallen jaren duren voordat de bijbehorende infrastructuur - van waterstofproductie tot overwegend CO2-vrije elektriciteitsopwekking - volledig aanwezig is. Om in die overgangsfase toch de CO2-uitstoot te reduceren, hebben Ingenieurs van de UDE samen met thyssenkrupp Steel Europe en de Technische Universiteit van Clausthal een concept ontwikkeld om hoogzuivere CO2 op korte termijn rechtstreeks in het proces te recyclen. Het zogenaamde "NuCOWin"-project zal drie jaar in beslag nemen. "De grote uitdaging is het ontwikkelen van economische processen binnen de transformatie in de staalindustrie, waarbij geen CO2 meer vrijkomt in de atmosfeer," legt projectleider Prof. Dr.-Ing. Rüdiger Deike van het UDE Institute for Technologies of Metals uit. "Koolstofverbindingen zullen onmisbaar blijven, maar de CO2 zal in de cyclus blijven."

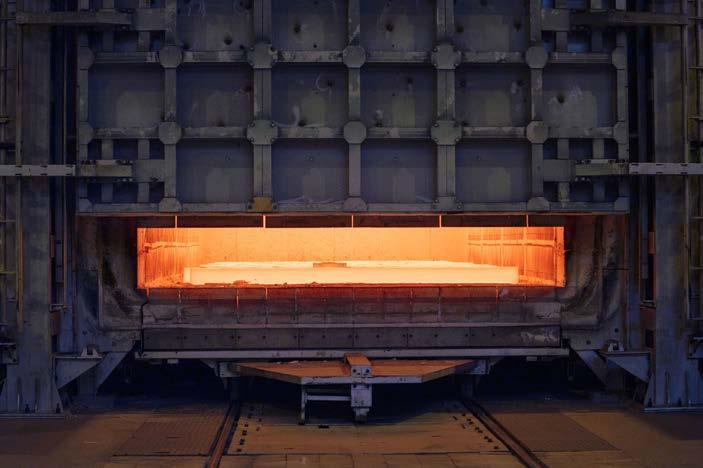
Elektrische oven voor het verwarmen van staven vóór het warmwalsen. Een voorbeeld van verwarmingsprocessen in de staalproductie die geëlektrificeerd kunnen worden om de klimaatdoelstellingen te bereiken.
Duurzaam roestvast staal
Waar de Universiteit van Duisburg-Essen vooral nog bezig is met onderzoek en ontwikkeling, heeft roestvast staal producent Outokumpu inmiddels een productieproces ontwikkeld voor een roestvast staal met een 64% lagere koolstofvoetafdruk ten opzichte van het bestaande proces. De nieuwe emissiebeperkte productlijn wordt op de markt gebracht onder de naam Circle Green. "We zien wereldwijd een toenemende vraag van klanten naar roestvast staal met een lage CO2-footprint. Met Outokumpu Circle Green kunnen we deze vraag beantwoorden en bijdragen aan de klimaatambities van onze klanten”, zegt Niklas Wass, Executive Vice President, Operations, bij Outokumpu. Outokumpu bereikte de emissiereductie dankzij verbeteringen in de hele productieketen van roestvast staal. Vermindering van de uitstoot van grondstoffen was de sleutel tot dit succes, aangezien deze het grootste deel van de totale uitstoot uitmaken. Een nauwgezette optimalisatie van de productie en de kwaliteit leidde tot een hogere energie-efficiëntie. Biogas, biodiesel, biocokes en groene energie zijn bij de productie gebruikt om 95% van alle scope 1- en scope 2-CO2-emissies te elimineren. Hoewel deze biogebaseerde materialen allemaal al eerder in de productie zijn getest, werden ze voor het eerst samen gebruikt om Outokumpu Circle Green te produceren.
Om de Nederlandse industrie te verduurzamen en de CO2uitstoot volgens de doelstellingen van het Klimaatakkoord terug te brengen, zijn flinke stappen nodig. Een belangrijke oplossingsroute voor CO2-reductie is de energietransitie waarbij het gebruik van fossiele brandstoffen wordt uitgefaseerd. Hierin ligt er naast de inzet van duurzame/ hernieuwbare energie, geothermie, hergebruik van gassen, reststromen en restwarmte enorm veel potentieel in elektrificatie van industriële processen. Industriële eindgebruikers die technologie willen ontwikkelen voor de elektrificatie van productieprocessen, kunnen zich aansluiten bij het Fieldlab Industrial Electrification (FLIE). Het FLIE is een initiatief van Deltalinqs, Havenbedrijf Rotterdam, InnovationQuarter, aangestuurd door TNO en FME, ondersteund door de provincie Zuid-Holland, de gemeente Rotterdam, PlantOne en de EFRO-subsidie. In een veilige, moderne test- en validatieomgeving kunnen (inter)nationale spelers samenwerken om technologie te ontwikkelen en implementatierijp te maken. Het fieldlab richt zich specifiek Power-to-Heat (P2H) (opwekking van proceswarmte voor de industrie met behulp van elektriciteit) en Power-to-Chemicals (P2C) (toepassing van waterstof en de omzetting van CO2 en andere broeikasgassen in bio-chemicaliën om in te zetten als ‘groene moleculen’.
Fossielvrij staal voor automotive
Ook staalproducent SSAB heeft de stap naar een duurzame staalsoort gemaakt. Recent heeft SSAB een fossielvrij staal voor de auto-industrie ontwikkeld. De producent heeft inmiddels een overeenkomst gesloten met het in de VS gevestigde Shape Corp., een vooraanstaande leverancier van lichtgewicht carrosseriestructuren, om het nieuwe fossielvrije HYBRIT staal van SSAB te testen voor gebruik in automobieltoepassingen. “De vraag naar fossielvrij staal neemt toe, wat voor SSAB een van de redenen is om de groene transitie te vervroegen met de ambitie om de kooldioxide-emissies rond 2030 grotendeels te elimineren”, zegt Martin Lindqvist, President en CEO van SSAB. De staalproducent streeft ernaar om in 2026 op commerciële schaal fossielvrij staal op de markt te brengen. SSAB werkt samen met ijzerertsproducent LKAB en energiebedrijf Vattenfall in het kader van het HYBRIT-
initiatief om een waardeketen voor fossielvrije staalproductie te ontwikkelen, waarbij de cokeskolen die traditioneel worden gebruikt voor de staalproductie op basis van ijzererts, worden vervangen door fossielvrije elektriciteit en waterstof. Dit proces elimineert vrijwel alle kooldioxide-uitstoot bij de staalproductie.
Groen hardmetaal
Naast materiaal is ook gereedschap een product dat elk metaalbewerkend bedrijf veelvoudig inzet. Ook op het gebied van gereedschappen is dus op grote schaal te verduurzamen. Gereedschapsproducent Ceratizit investeert om die reden in de verduurzaming van de hardmetaalproductie. Om de CO2voetafdruk snel drastisch te verminderen, richt het bedrijf zich in eerste instantie op drie belangrijke aspecten. Doorslaggevend is de verhoging van het gebruik van secundaire grondstoffen tot meer dan 95%. In vergelijking met primaire grondstoffen uit erts, vergt de verwerking ervan 70% minder energie en wordt de CO2-uitstoot met 40% verminderd. Een positief neveneffect is het veiligstellen van de toeleveringsketen voor grondstoffen. Een ander aandachtspunt is de stroomvoorziening. Ceratizit wil de stroomvoorziening van alle vestigingen de komende jaren omschakelen naar groene stroom uit wind-, zonne- en waterkrachtenergie. Nauw verbonden met de verandering in de stroomvoorziening is de kwestie van de waterstofvoorziening. Waterstof wordt veel gebruikt in de hardmetaalindustrie, met name voor de productie van wolfraampoeder. Tot nu toe werd waterstof voornamelijk verkregen uit aardgas door middel van stoomreforming, de zogenaamde ‘grijze’ waterstof. Voor de toekomst is Ceratizit van plan blauwe waterstof te gebruiken, die door elektrolyse met groene stroom uit water wordt gewonnen. Hiervoor zal Ceratizit samenwerken met haar bestaande leveranciers en ook zelf elektrolyse-installaties bouwen. Inmiddels heeft Ceratizit al diverse ‘groene’ producten in het assortiment zoals het groen hardmetaal en de SilverLine frees met duurzaamheidsformule.
