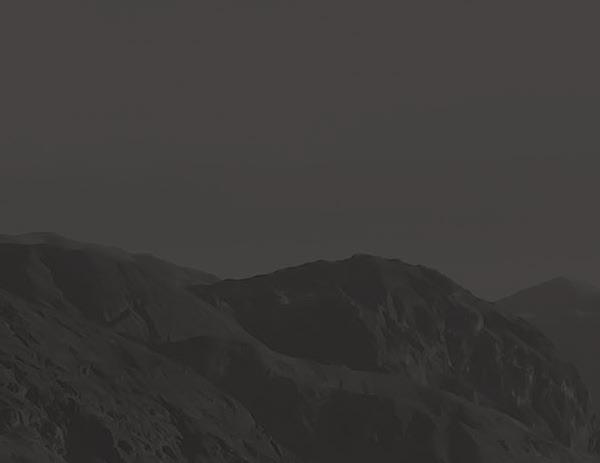

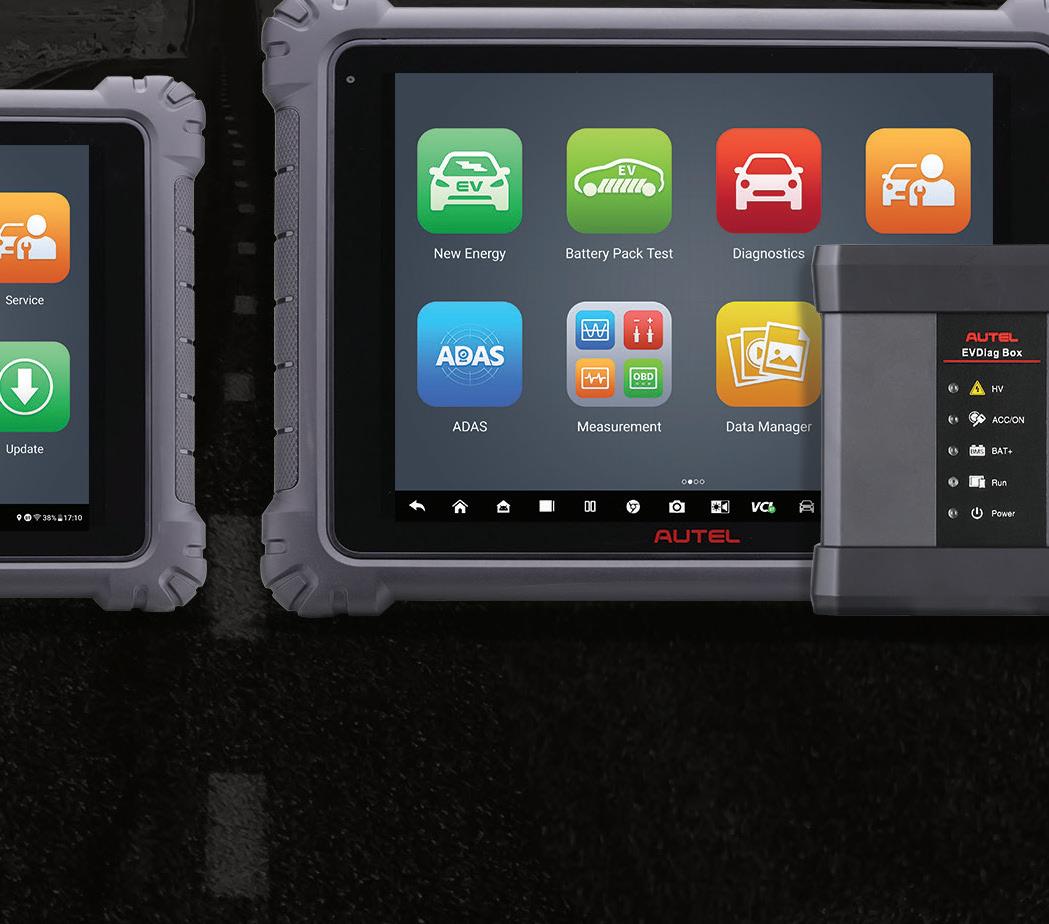

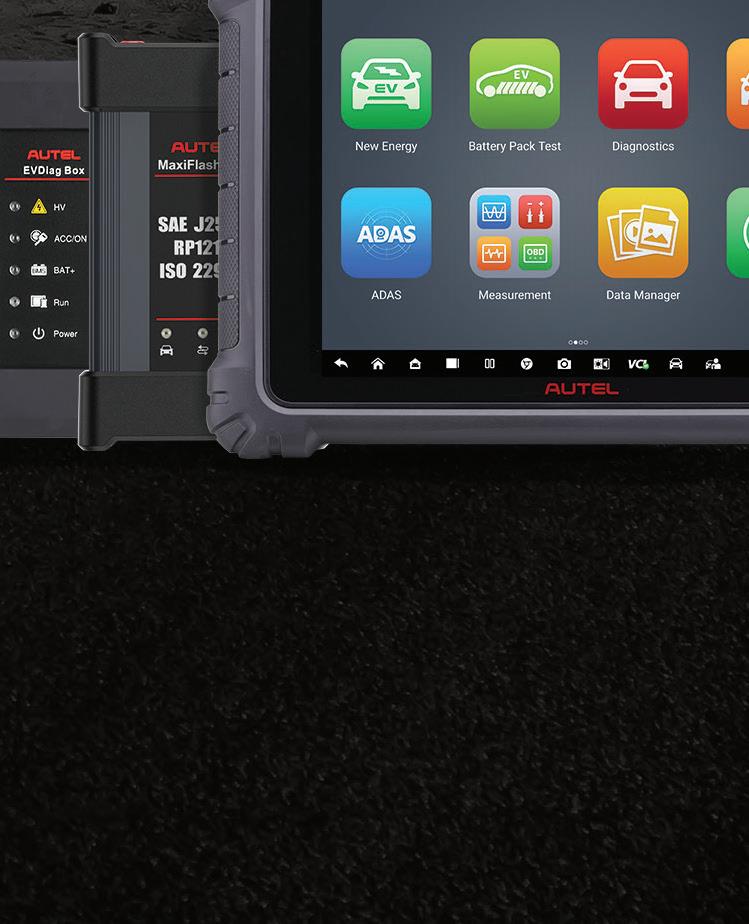

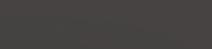



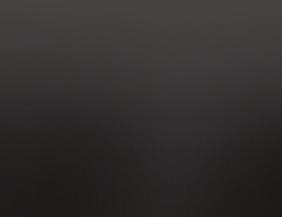


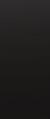


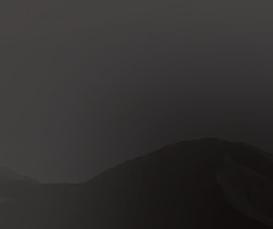

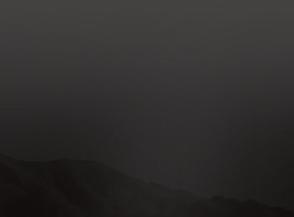

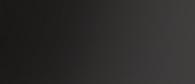

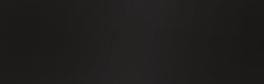



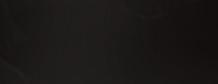

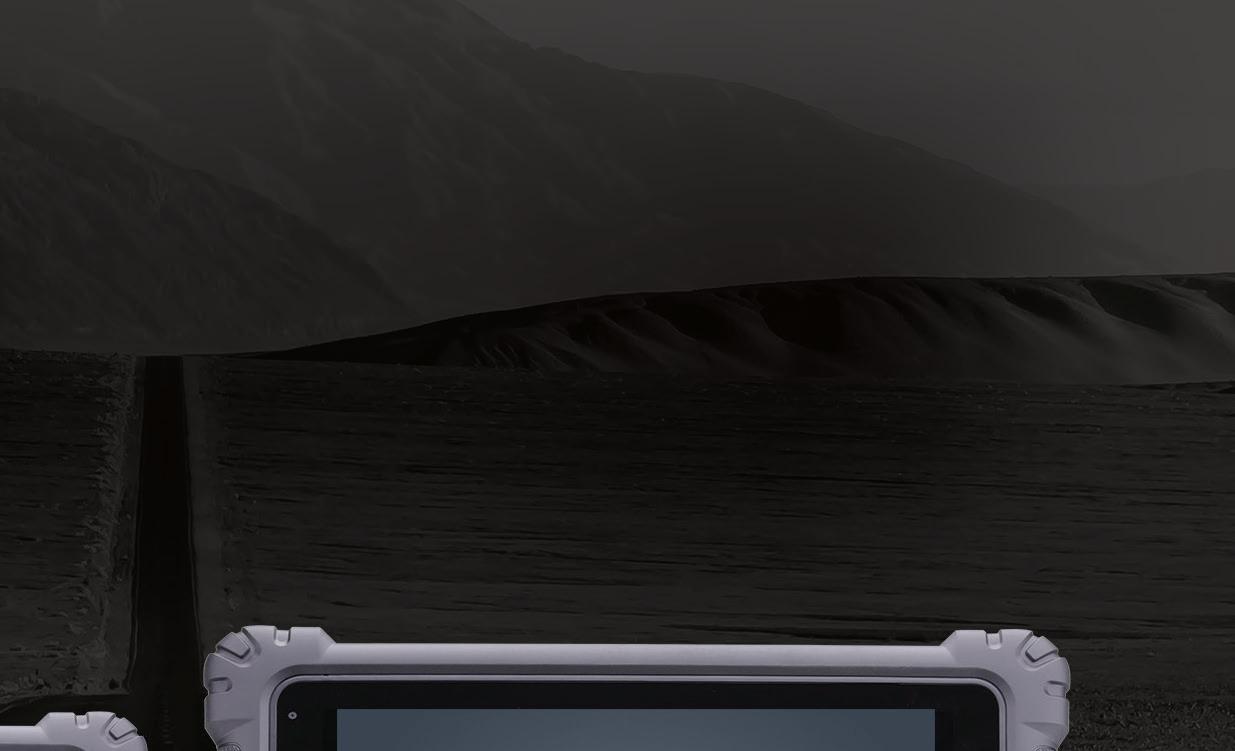
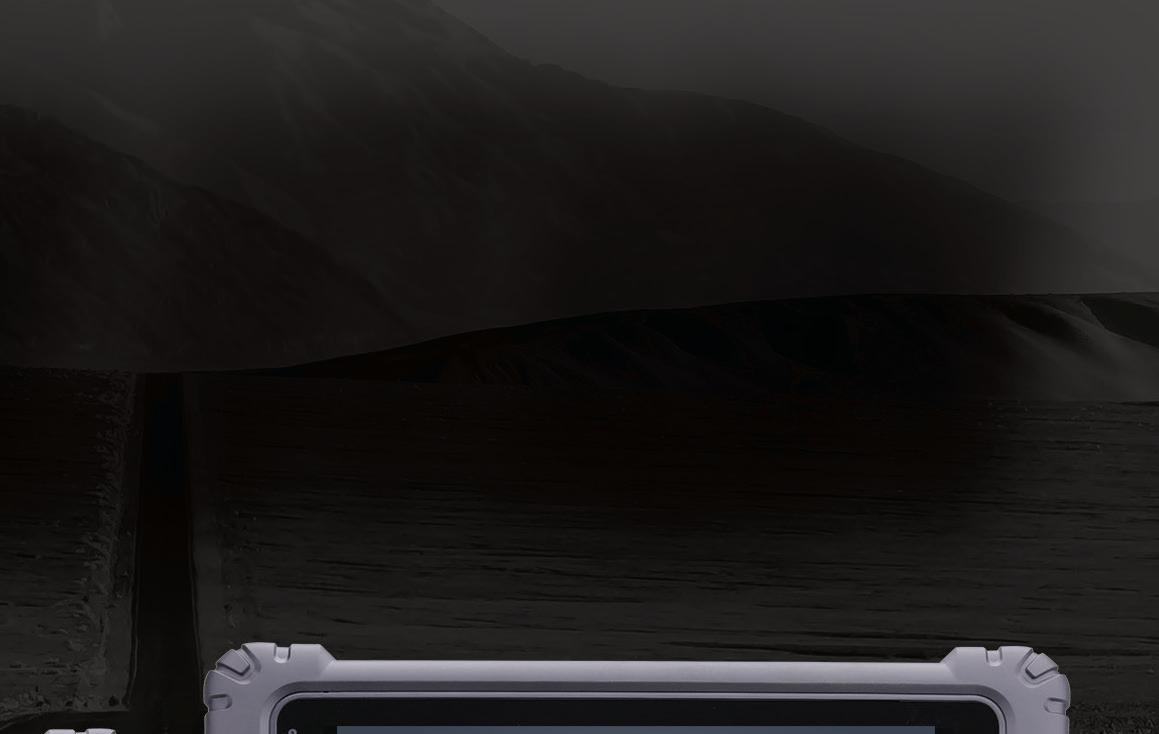




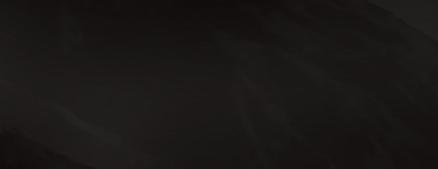
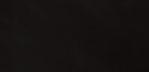
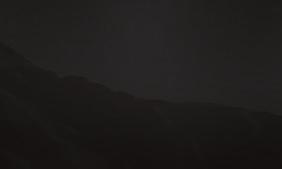
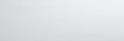
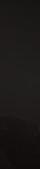



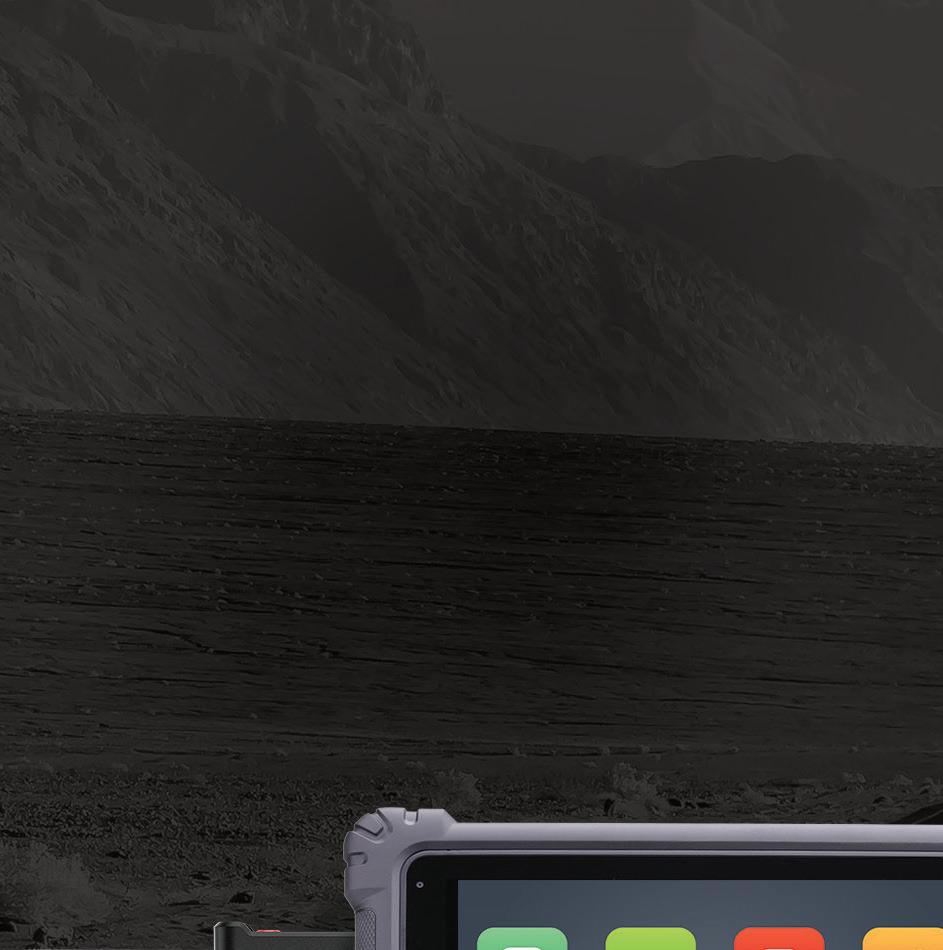


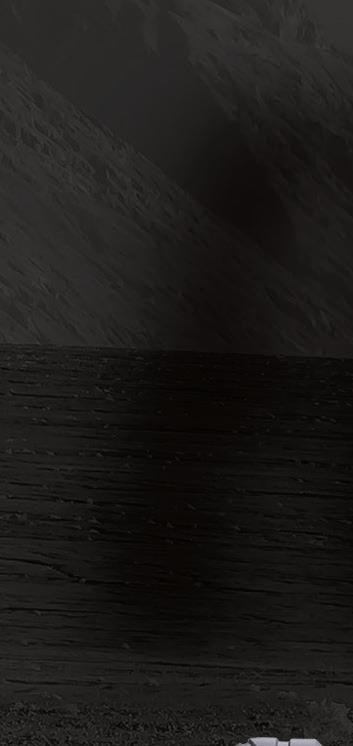
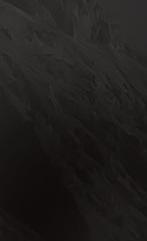




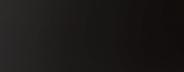
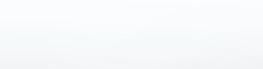
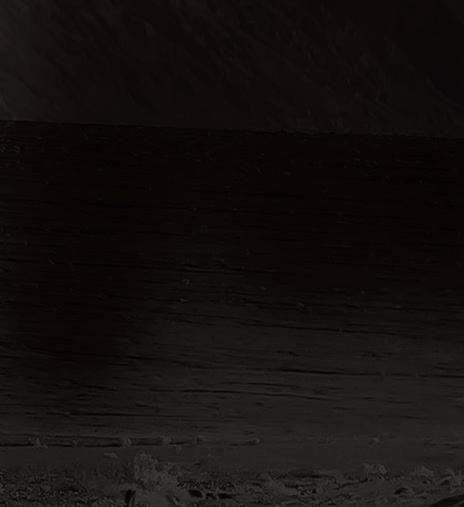
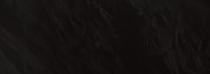
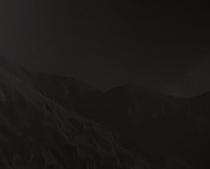
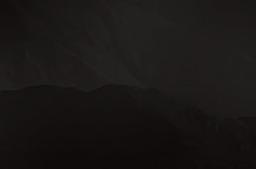



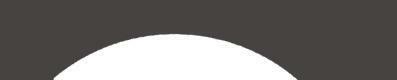
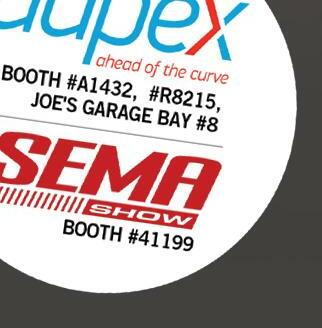

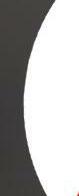
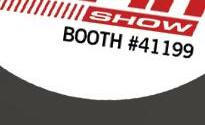


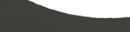



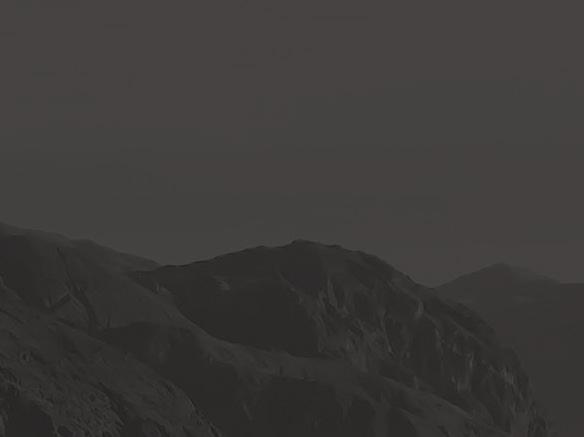

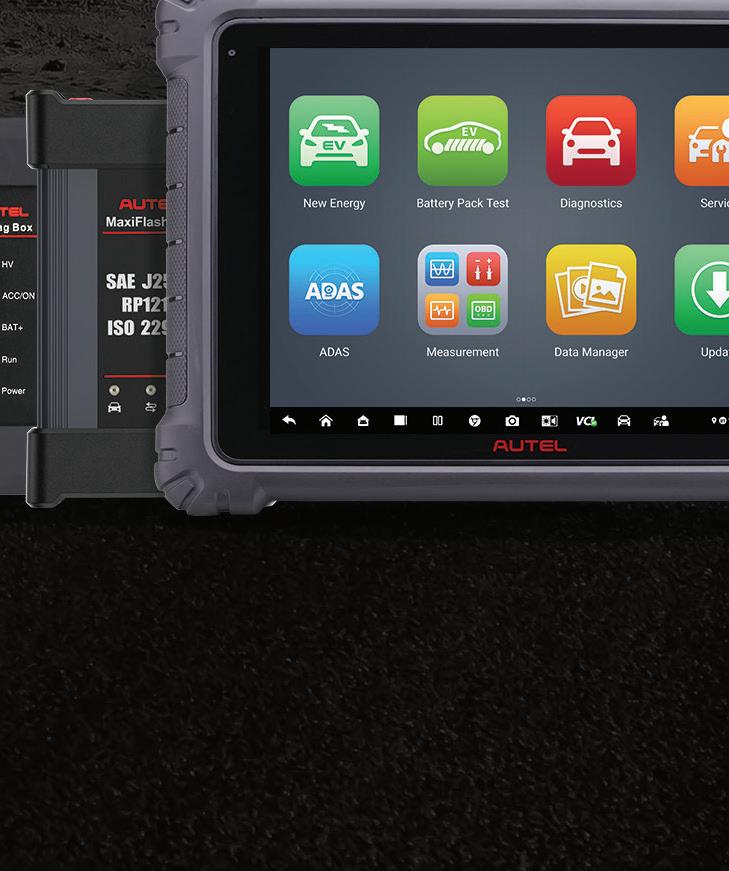
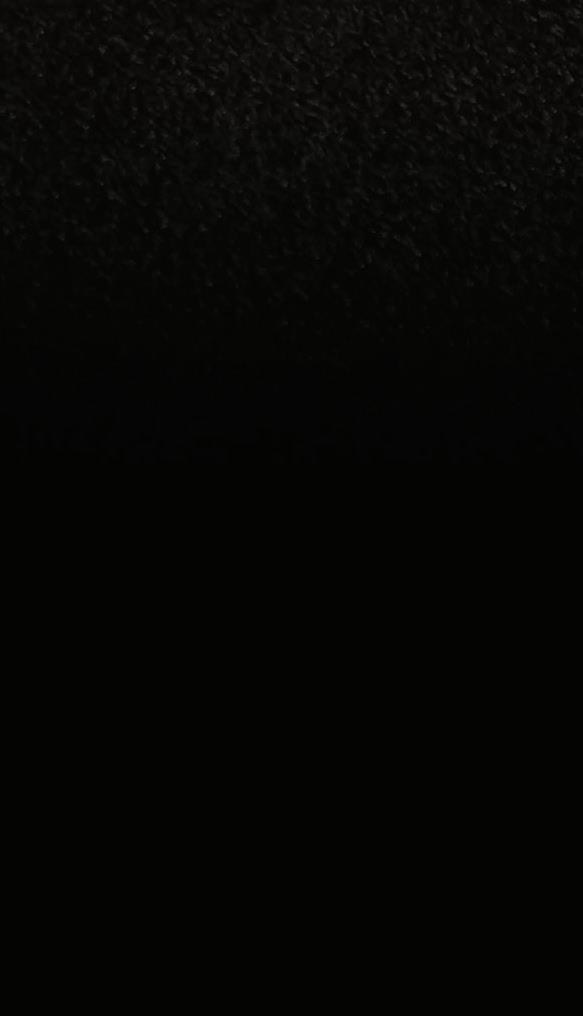
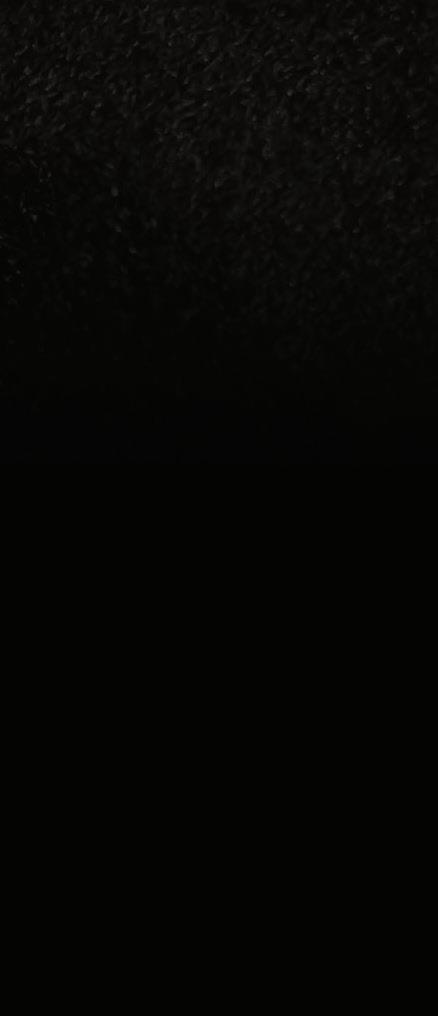
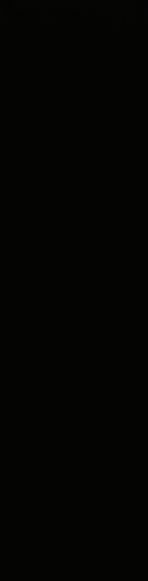
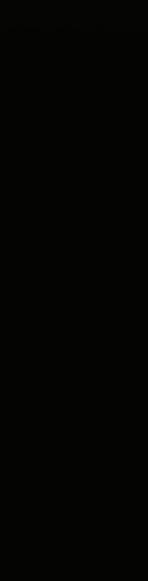
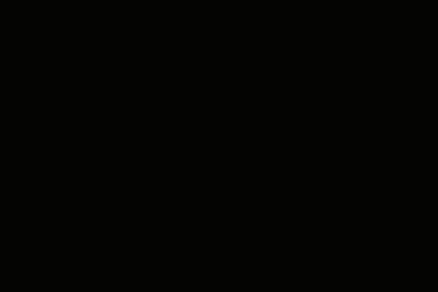
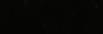

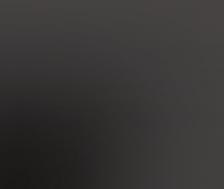
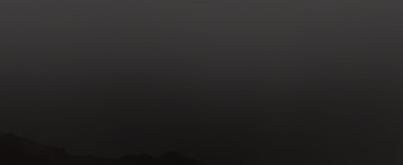






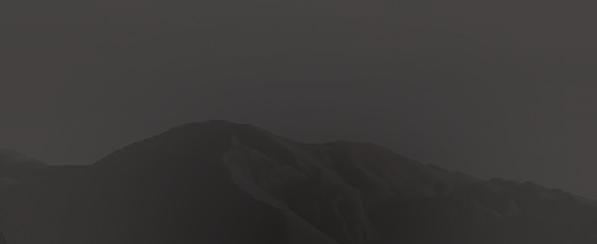
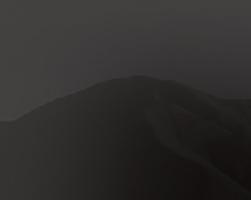

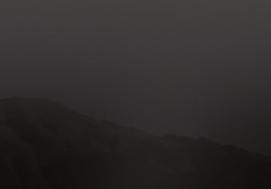

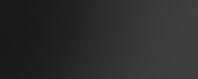

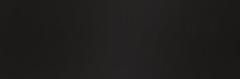

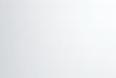


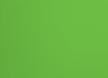
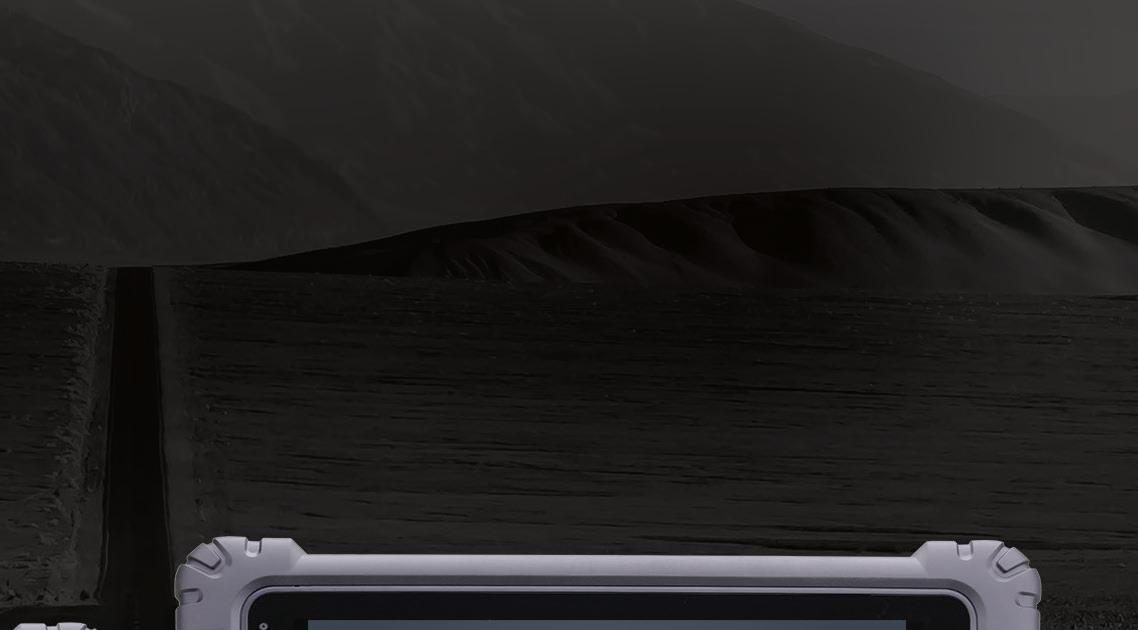

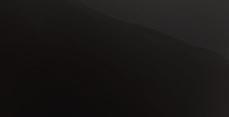



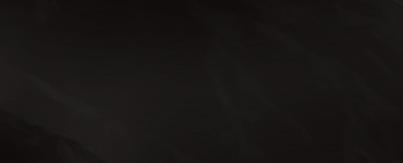
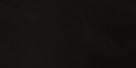

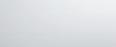

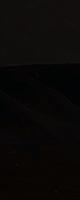


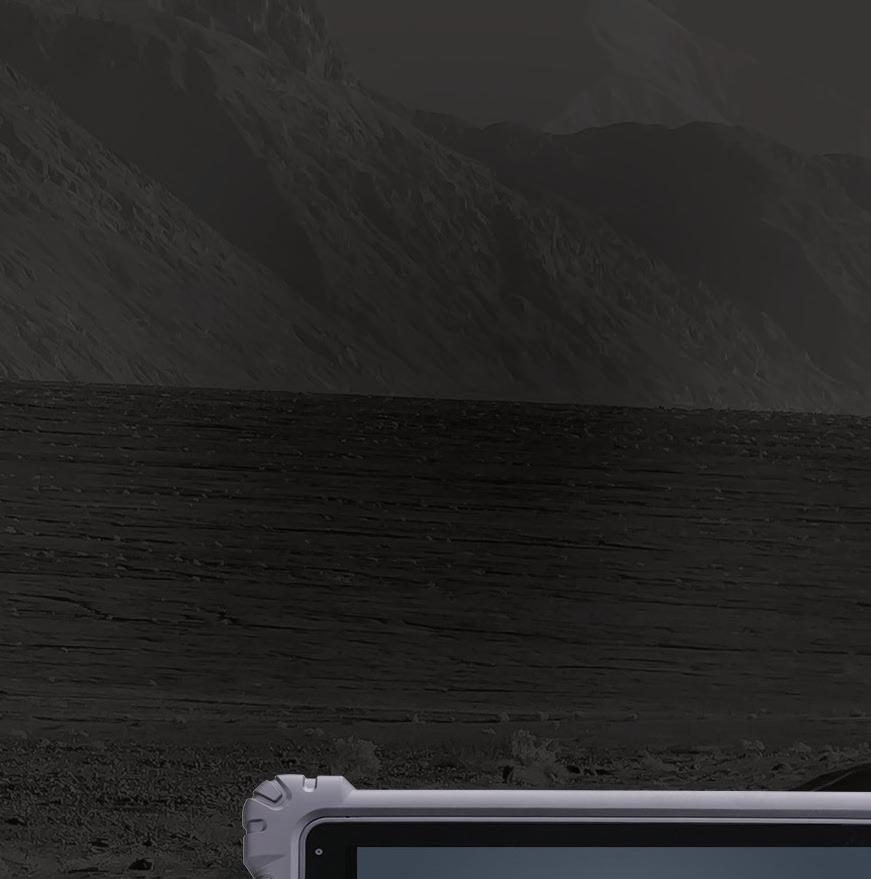



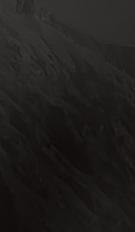
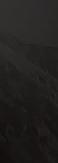
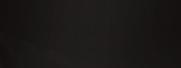


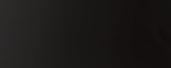
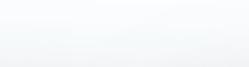
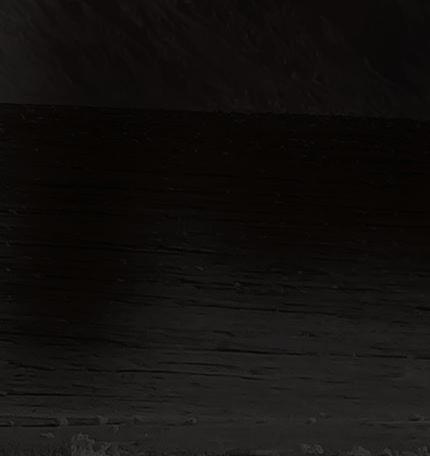

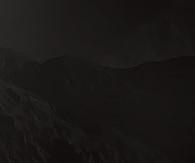
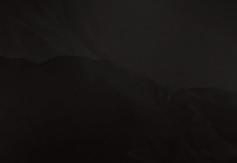


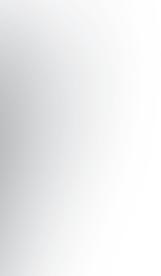

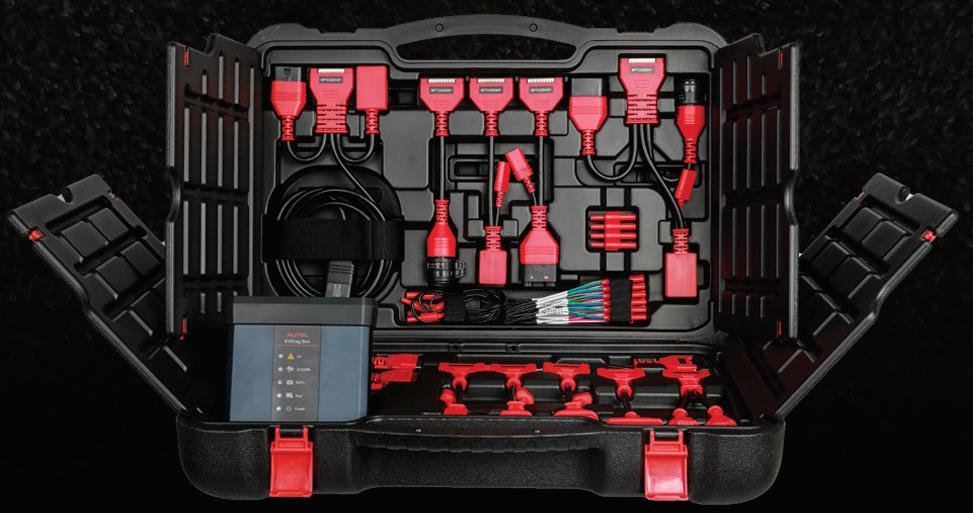

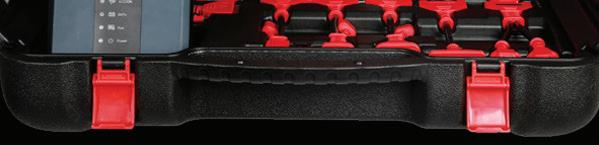







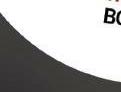





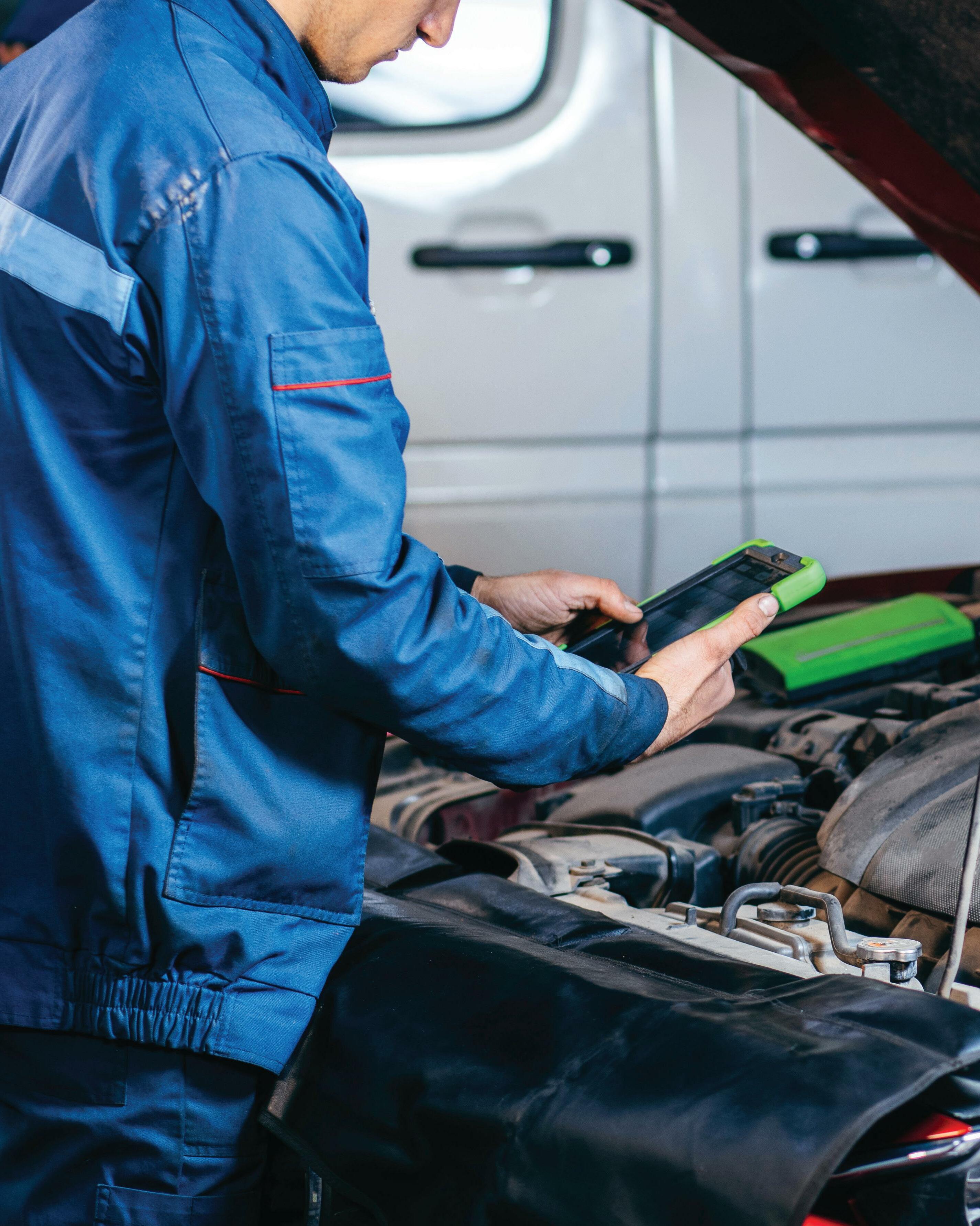

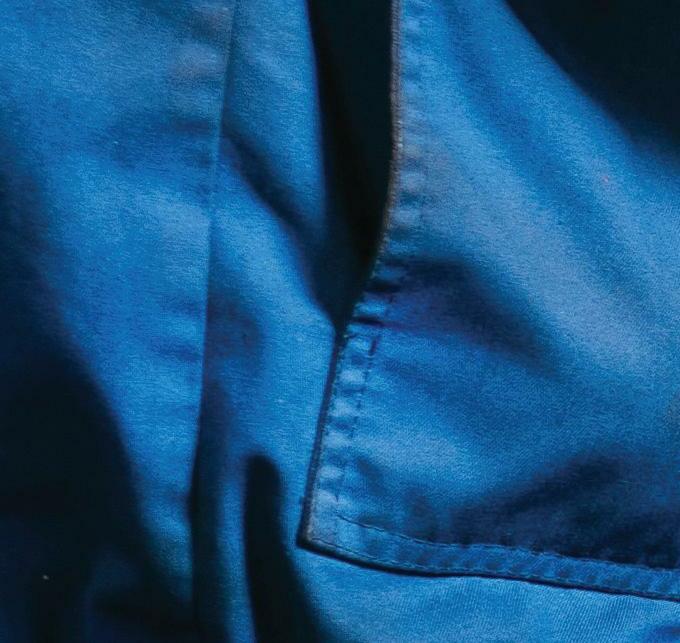
Enable Wi-Fi and Bluetooth on your Robinair NI or ROBAC1234-4 machine
ROB 80211VCI reads YMME and includes a refrigerant capacity database
ROB 80211TMP reads and tracks multiple vent temperatures for before & after service diagnosis and reporting
Compatible with ROB34288NI, ROB34788NI, ROB34788NI-H, ROB34988NI and ROBAC1234-4 machines
ROB80211TMP master kit with 2 Bluetooth temp probes
ROB80211VCI master kit with refrigerant capacity database
STRAIGHT TALK
Customers Remain calm, explain the issue and shrug off the negativity
4WD and Super Duty trucks
and Mitsubishi
STRATEGIES It’s important to establish a plan of attack
HIGH VOLTAGE LEAK CODES Understanding them, and where to look
VALUE OF THE DSO
Storage Oscilloscopes and their benefits
WHEEL BEARING TECH Isolating the issue and service tips
rundown of selected tools to consider adding to your shop’s arsenal
WE’VE ALL BEEN THERE....THE DREADED
angry customer. You know the type: the vehicle owner who thinks he or she is entitled and simply can’t be reasoned with. While the majority of your customers are likely pleasant and reasonable, there are times when you’re faced with some real winners. Here are only two examples passed on to me by shop owners and techs, with encounters that can really get your blood boiling:
“I don’t understand why you’re charging me so much. The engine was simply making a noise. I mean, how much can it cost to fi x a simple noise? I want to see the manager.” This really happened. The customer (a female, in her 40s) brought her husband’s 2002 Ford F350 RWD to a shop to have an “engine noise” fi xed. It quickly became obvious that the “noise” was due to a completely devastated left front wheel bearing, where the wheel was about to come off had the truck been driven another mile or so. The damage involved not only the wheel bearing, but the spindle (requiring a complete steering knuckle replacement). In addition, though unrelated to the wheel bearing issue, the caliper had seized up, the brake rotor was trashed and the brake hose was cracked and split.
After being given the repair estimate, the customer had what the tech referred to as a complete meltdown, screaming and throwing a child-like tantrum in the waiting room. After speaking to the actual owner (the woman’s husband), the consent was given for the repair, as the husband appeared to understand the issue. Nonetheless, the woman continued to abuse and threaten the shop staff. She got a ride home with a friend. The husband came in the next day to pick up the truck and apologized for her behavior, remarking that he hardly drives the truck and allows her to use it for her landscaping hobby. His memorable comment was “now you understand why I drink.” Enough said.
Here’s another encounter. A male customer had his beloved 1969 Camaro Z28 flat-bedded to a shop. He had just been at a local car show. Upon starting the engine and “revving it for fun,” the engine began to miss and rattle. While at the shop, he was ranting and raving and would not calm down, repeatedly screaming that “this is the worst day of my life,” even throwing his cell phone across the shop’s parking lot. The issue was simple to diagnose. A press-in rocker stud had loosened, keeping the valve closed and allowing the rocker arm to rattle around. Luckily no bent valve and no bent pushrod. The repair was handled with a screw-in rocker stud and adjusting all valves for lash. By the way, it turns out that his wife had passed away a mere month prior, but this was “the worst day” of his life.
You just can’t make this stuff up.
Dealing with difficult customers comes with the territory. While you may be tempted to raise your voice and verbally retaliate, keeping a calm demeanor is imperative. Even when the customer is out of line, let cool heads prevail. While nothing is accomplished by lowering yourself to their level, if word gets around that you “raised your voice,” word of mouth “publicity” can potentially harm your business within your market area. Remain calm, explain the issue and try your best to shrug off that one person’s negativity. Nobody said running a repair shop is easy.
MIKETurn to it any time you need the latest technical service bulletins, in-depth technical articles and the newest products. Our site also features news from suppliers and manufacturers to keep you up-to-date on what’s happening in the automotive industry.
Plus, go to our website to renew your subscription to ASP, read the digital version of each issue and sign up for a free subscription to our weekly eNewsletters!
3515 Massillon Rd., Suite 200, Uniontown, OH 44685
(330) 899-2200, fax (330) 899-2209
Website: autoserviceprofessional.com
Greg Smith / gsmith@endeavorb2b.com (330) 899-2200, Ext. 2212
Editor: Mike Mavrigian birchwdag@frontier.com
Managing Editor: Joy Kopcha jkopcha@endeavorb2b.com
Associate Editor: Madison Gehring mgehring@endeavorb2b.com
Creative Services Director: Zach Pate
Art Director: Jonathan Ricketts
Graphic Designer: Emme Osmonson
Production Manager: Karen Runion krunion@endeavorb2b.com
Je Taylor, Diagnostics & Drivability Specialist
Bill Fulton, ASE Master Tech
Craig Van Batenburg, EV Technology
Chris Chesney, Repairify
Jake Sorensen, McNeil’s Auto Care
Seth Thorson, Eurotech Automotive
Donny Seyfer, Seyfer Automotive
Bill Fulton, ASE Master Tech
Dan Thornton / dthornton@endeavorb2b.com (734) 676-9135, mobile (734) 626-4950
Bob Marinez / rmarinez@endeavorb2b.com (330) 899-2200, ext. 2217
Marianne Dyal / mdyal@endeavorb2b.com (706) 344-1388
Sean Thornton / sthornton@endeavorb2b.com (269) 499-0257
Kyle Shaw / kshaw@endeavorb2b.com (651) 846-9490
Martha Severson / mseverson@endeavorb2b.com (651) 846-9452
Chad Hjellming / chjellming@endeavorb2b.com (651) 846-9463
Vice President: Chris Messer
TECHNICIAN’SA customer came in with a 2007 Ford E-250 van with the 5.4L 2V Triton engine, complaining of rough idle and severe lack of power. No misfire codes were apparent. We checked and replaced all spark plugs (luckily the plugs had been changed once prior, so they all came out without an issue). Two were absolutely shot, so it was clear that the engine was running on only six cylinders). With new plugs in place, the engine ran fine when cold, but the miss and rough idle returned once it reached operating temperature. We did an individual check of the coil resistance (coil on plug). All checked fine when cold at 9 ohms. Once hot, one of the coils dropped rapidly from 9 ohms, resulting in the engine now running on seven cylinders. Replaced the coil, and all was good.
You may or may not run into a vehicle where stainless steel screws/bolts enter aluminum threaded holes, but if you do, here’s a tip: Never install a stainless steel bolt into aluminum dry. If the bolt/screw is tightened rapidly (generating a bit of heat in the process) or if there’s a slight burr, you run the risk of severe thread galling, making it difficult if not impossible to remove the bolt. If it’s a blind hole, apply a light coat of lube to the threads (assembly lube or dedicated thread lube). If the hole is open to water, oil or vacuum, apply Teflon pipe dope to the threads. Don’t ask how we know.
If you run into an intermittent “service engine soon” message on the instrument display on a 4WD Chevy/GMC vehicle (2015-2019), the issue could be the wiring terminals that are miss ing seals at the transfer case control module. DTCs might include C0321, C0392, C0396, C0398, C0306, C039E or C038D. Missing seals allow moisture to enter and can cause intermittent issues. If you replace the connector at the transfer case actuator due to one or more missing seals, and any corrosion is present, the transfer case actuator should also be replaced.
On Ford F-Super Duty trucks (or any engine that features a serpen tine drive belt, for that matter), pay close attention to the condition of all pulleys, especially the idler and tensioner pulleys. On a Ford F-Super Duty equipped with a 7.3L turbo diesel, as but one example, if a tensioner pulley bearing fails, the belt will fly off, leaving the driver with no water pump operation (quickly overheating the engine), and no power steering and no power brakes (since a belt driven vacuum pump provides booster operation). If an idler pulley or tensioner pulley has excess play or feels rough when turning, replace them now instead of waiting for a failure. These heavy trucks are extremely hard to stop and turn if the belt fails, creating a real driving hazard. Aside from tight access between the pulleys and the radiator shroud, replacing either of these pulleys is a fairly simple job. Seriously, if a pulley, tensioner or belt seems at all iffy, service it immediately.
Whenever servicing a cooling system, using the proper coolant (as specified by the vehicle manufac turer) is important due to specific chemistry require ments and to protect the entire cooling system from corrosion and metal contamination. But whenever you plan to introduce water (to top off or as part of a mix with concentrated coolant), the water quality really does matter. Always use distilled water, and avoid tap water. This is not new information, but in some cases people tend to overlook the importance. Minerals and/or acidic content of the water can do serious harm over time, creating rust in water jack ets and damaging water pumps and radiator cores. Just remember that all water is not created equal. Just because it “looks clear,” that doesn’t mean that it’s OK for the cooling system.
Check connector for wires missing seals. (courtesy Mitchell1) From coil plugs to water qualityModular Oil Filter Housings are becoming more common on today’s vehicles. One modular unit contains the oil filter, multiple sensors and serves as an oil cooler. Like many new OE designs, there have been problems, especially with some of the earliest versions. It is very common for the lower seals to fail causing an oil leak around the base of the housing. In some instances the housing may look okay, but it’s still a good idea to install a new housing while the vehicle is apart. A new housing, with new seals is the best way to help prevent future leaks and get your customer back on the road.
Standard® Oil Filter Housings come assembled from the factory and include everything needed for a complete and correct installation. The oil filter and cap are an exact OE-match and are already installed. All Standard® assemblies include new oil temperature and oil pressure sensors, and each includes new gaskets, seals and hardware so you won’t have to reuse any of the old, worn pieces.
It is critical to remember these are not just oil filter housings, they are also oil coolers. Vehicle manufacturers designed these housings to help keep the oil cool, meeting the strict cooling requirements of today’s engines. That is why vehicle manufacturers use high-temp
synthetic materials for oil filter housings. Standard® Oil Filter Housings are made from a high-strength, glass-filled nylon housing, maintaining the same heat dissipating properties as OE.
Other aftermarket companies have changed OE form and function, and supply metal housings. It is important to remember that metal has very different heat retention properties compared to synthetic materials. Think about the difference between touching a metal and synthetic handle on a hot pan.
Standard® Housings are vehicle specific, not universal, and designed to use the correct oil filter cataloged for the vehicle. Now, that may sound obvious, but many available housings are universal, and may not use the oil filter designed for the intended vehicle. You can imagine how much confusion that will cause when it’s time for an oil change.
Inside the Standard® box you will also find detailed installation instructions with torque specs to make installation faster and easier. Standard® Oil Filter Housings are assembled, ready for installation, feature vehicle specific filtration, and most importantly match the OE cooling characteristics; a true quality drop-in solution. To learn more visit www.StandardOFHA.com
100% New: All of the components, including the housing are new, not remanufactured
Hardware: O-rings and fasteners included for a complete repair
Gasket Set: Complete set prevents oil leaks
Standard® OFH100
Chrysler/Dodge/Jeep/Ram (2013-11)
Oil Filter: Correct, vehicle-specific oil filter keeps oil free of debris
Oil Cooler: Helps keep the oil and OE designed operating temperatures for performance and reliability
Oil Temperature Sensor: Already installed, made of high quality materials to withstand extreme conditions and tested to ensure reliability
Housing: Made of hightemp, high-strength, glassfilled nylon to dissipate heat and help cool the oil as the OE intended
Oil Pressure Sensor: Factory installed and computer calibrated to ensure accurate oil pressure readings
PERFORMING DIAGNOSTICS IS SOME THING many of us do each day, without much thought, but most seasoned technicians have a detailed diagnostic approach that they employ. They have an action plan — a diagnostic checklist — that they follow from start to finish with remarkable suc cess. Without an action plan the diagnostics of any vehicle system can be a challenge, often leading to misdiagnoses, dead ends and frustration.
The manufacturers want their technicians to do this, and they have spent a lot of time develop ing diagnostic strategies, learning courses, classes and checklists for their technicians to follow. They want technicians to be efficient and effective when diagnosing. Most of the factory-supplied diagnos tic strategies are detail oriented, step-by-step, and tailored to the manufacturer’s needs. But there is one common aspect across almost all the manufac turer-developed diagnostic strategies — the scan tool isn’t involved until a few steps into the diagnostic.
Why is this? Because manufacturers want the technician to verify the customer’s concern first. If the problem can’t be verified or confirmed, it can’t
be fixed. Sure, a scanner is likely going to be needed and used, but not at the outset of the diagnostic.
Before we dig into the checklist, I want to share a quality that I find common among the best automo tive diagnostic technicians: they rarely get stuck in a pre-diagnostic train of thought. They will attack each diagnosis with a completely clean slate.
What is pre-diagnosis? It’s the process of guess ing what the issue is, or what the fix is going to be, before even looking at the vehicle. Technicians can often be heard saying to one another, “It sounds like a bad injector. I just had one last week.” Or, “It’s a bad PCM” because it has no trouble codes. The skilled diagnostic technician will go into each repair open minded, thinking about how the system works and how best to duplicate the customer’s concern, not guessing what parts need to be replaced.
So what is the best methodical diagnostic strategy to follow?
There is no one fixed approach that will lead to a miraculous fast repair every time, but there is a common list of steps and details that make up an effective diagnostic strategy that we can adapt and use in our shops.
If you’re already ASE Certified, just go to federated5050challenge.com and enter for a chance to win every week, for fifty weeks. If you are not yet certified, visit federatedautoparts.com and click on the ASE icon to learn how to register for the ASE test. Once you’ve completed your certification, you’re eligible to enter. It’s as simple as that.
It pays to be ASE certified, both for you and for your customers. Challenge yourself today!
be neglected. We need to remember that if we cannot verify or duplicate the concern, we cannot possibly evaluate, repair or diagnose what’s wrong.
Drivability problems should involve a road test, even if it is brief, to verify the issue the customer is experiencing. When performing that road test you need to ensure that you are driving the vehicle the same way that the customer does, and this is an important, o en overlooked step.
I once took a young technician for a road test a er he was unable to duplicate a hesitation in a car. He had driven the car and the issue wasn’t obvious, but the car had returned for the complaint once already. He wanted help, so I agreed and when I drove the car, like the grandmother that owned it did, the issue was real, and the car hesitated badly. Duplicating the customer’s driving conditions is o en a key to a good drivability technician and their diagnostic strategy.
Basics must be checked. This cannot be stressed enough when it comes to following the diagnostic checklist. There are so many simple things that can
1. Interview the customer — Ask lots of questions
2. Verify the concern — Road test
3. Inspect the system
a. Basics and visual inspection first
b. Check customer history, earlier repairs
c. Understand how the system is to properly function
4. Begin the diagnostics and system analysis
a. Symptoms, full system scans for DTCs
b. Follow the manufacturer’s system verification or self-tests
c. Check for bulletins, recalls
5. Follow the DTC or symptom diagnostics charts
6. Find the issue or cause of the concern and repair it
7. Validate that the repair is complete and successful
We need to start off by gathering as much information as possible. And that gathering of information will start with the customer interview. This is not o en an easy thing to do, especially when a vehicle is le at the shop overnight with a small note about the issue.
Questions should be asked about when the issue happens, how o en it happens, and what the driver was doing when it happened. For example, are they passing? Accelerating from a stop? The questions can be many, but the answers may point in a specific direction that could be a clue. Was the service engine soon (SES) light flashing? These all can be clues to an issue.
The second step in a diagnostic is to verify and understand the customer’s concern. This is a fundamental step, but it is important and can’t
cause an issue and they are o en overlooked right at the start of a diagnostic. Not checking the basics can o en lead to false or inaccurate diagnostics, conceal the actual issue, or make the diagnostic harder than it needs to be. The ba ery voltage and the charging system function are critical. Low or poor ba ery voltage can affect so many things, especially on today’s heavily networked and electrically loaded vehicles. Other basics o en overlooked are the type and amount of engine oil and low cooling systems. Low or improper engine oil can easily translate into variable valve timing issues, DTCs and drivability concerns. Low coolant levels can cause indicator lights on the dash, air conditioning issues, overheating and DTC issues, even though the expansion tank is full.
We will all have our di erences and ideas on how we approach a diagnostic, but these are the most common diagnostic steps I have found that work the best.Using the scanner and checking for codes should be done, but it shouldn’t always be the rst thing that is done during a diagnostic. This shows the scanner results of a Nissan with issues. Always perform a full module scan and record all the codes. (all photos by author) A good visual inspection can often reveal the issue, just by opening the hood and looking. This Ford Mustang no-start was customer induced. Checking the basics found the issue.
When you accept American Express® Cards, you have access to benefits, signage and materials to help your business thrive.
Social media posts and posters to help promote your business.
Discounted Offers from our Partners Save on services to help you with marketing, finances, and more.
Free Signage Supplies for your business to welcome your clients. Scan the QR code or visit americanexpress.com/signage
For more information on resources for your business, visit americanexpress.com/business-solutions
Another area that we need to pay particular atten tion to at the start of a diagnostic is the inspection for aftermarket components and earlier repairs. After market components and systems can cause issues, from no-starts, battery draws and drivability problems to systems that won’t communicate. Checking the basics at the start of the diagnostic can save a lot of time and frustration and often expose the cause of many concerns.
Getting all the information from the customer the first time is imperative. Here is an example. The cus tomer’s concern on their 2016 Ford F-150 pickup is that the air conditioning stops blowing cold at times. The technician is following their diagnostic checklist and trying to verify the concern. The technician per forms the visual and basic inspection, with no issues found. The air conditioning works fine on startup, and it continues to function properly on the road test. Returning to the shop, the scanner is installed and shows no related codes. The air conditioning gauge set is installed, and the pressures and functionality are confirmed and ok.
The issue can’t be duplicated, so the technician heads to the office to discuss the findings: the system is working properly.
The customer is contacted, and more information is gathered about the issue. The customer explains that the issue only happens when towing a large travel trailer up a steep grade.
This information would have been far more useful at the beginning because what the customer is expe riencing is normal. The truck’s engine management will shut off the air conditioning compressor to sup ply more power to climb the grade. A better customer interview would have saved the technician a lot of time looking at something that is fully functional
The issue is verified, but there are no trouble codes. A 2019 GMC Sierra pickup is dropped off, this time with a detailed note indicating the climate control dis play in the vehicle will show the message “Climate Off,” but the climate control system in the truck still is fully functional. The message will go away if they change a climate setting.
The customer even included a photo from their phone that shows this error message. The technician assigned to the truck sees the message displayed on the center stack during a road test, and it goes away when the fan speed is changed; the issue has been verified.
Returning to the shop, a scanner is installed, but there are no codes displayed as current or history in any modules that pertain to the condition that will aid in the diagnostic of this climate control issue.
But the technician has confirmed the issue does exist, since the error message was displayed. So the technician moves along in the diagnostic strategy and investigates if there are any technical service bulletins (TSBs), manufacturer bulletins, or recalls that could cause or relate to the issue.
Logging into the shop’s information system, the technician discovers the TSB No. 19-NA-189, which says the following: “Radio displays CLIMATE OFF message or HVAC popup displays different settings.” Reading the TSB, the information says that the customer complaint may be that the center stack will display the message “Climate Off,” but still be functional and that message will disappear when a climate setting is changed. The noted repair procedure is to reprogram the radio mod ule (A11) and the serial data gateway module (K56) to fix a software anomaly.
This TSB is addressing the situation that this truck is experiencing. The customer was advised that a mod ule reprogramming update would be needed to repair
This dash warning was the reason the customer brought in the vehicle, but the warning would not show up until the vehicle was road tested, and road testing is an important step in the diagnostic checklist. (all photos by author)
the issue. The customer agreed to the update, the pro cedure was performed, and the concern was no longer present. The diagnostic was successful, and the vehicle was repaired.
The goal of any successful diagnostic procedure or checklist is to use an established plan of attack, which will guide us through each phase of the diagnostic situ ation, from verification to repair.
Yes, there will be different diagnostic patterns that we will follow for different situations. Diagnosing a grinding transfer case will have different steps from diagnosing a coolant leak or a flashing check engine light. But the steps will be similar in each case. The first step in all diagnos tics is verifying the concern. And the last step should always be to verify that the repair has fixed the issue. How we get from verifying to repairing will be different, but the use of a methodical step-by-step approach, while pay ing particular attention to basics and not pre-diagnosing, is the best method.
Jeff Taylor boasts a 30-plus-year career in the automotive industry as a fully licensed professional lead technician. Jeff works for the CARS Training Network Inc. in Oshawa, Ontario, Canada. He is also heavily involved in government focus groups, serves as an accomplished technical writer, and he has competed in international diagnostic competitions as well as providing his expertise as an automotive technical instructor for a major aftermarket parts retailer
Another example of a broken ground strap on a 2016 GMC G van that caused a no-start and caused CAN communications issues.ACDC IS BACK WITH MORE DIAGNOS TIC HELP when working on high voltage systems. High voltage (HV) is isolated from the chassis for good reasons. When any high voltage part has a connection to the chassis, that could spell trouble, depending on how much current the connec tion can carry. The engineers have cleverly designed circuits and strategies that can determine a “lack of isolation” and report that to your scan tool and set a warning light. How does that detection system work? (Note we use ASE L3 terminology as much as we can. If you are not L3 certified, ACDC can help you.)
When faced with a code for a high voltage leak to chassis ground, here is what you need to remem ber. When the HEV-PHEV-EV (ACDC calls them EMVs, which is all-encompassing and stands for electrified motor vehicles) is in “Power On” mode (Fig. 1), most OEMs will check the battery pack for a HV leak to the chassis. We called this a Type “A”, sometimes known as an “Active Loss of Isolation” (LOI) Detection System.” Once the HV battery has passed an HV leak test, the contactors will close in a certain sequence and the high voltage parts will be powered on in a precise order, unless there are other codes preventing a “READY” light (Fig. 2).
Another detection system, called Type “B,” or a “Passive LOI Detection System” is also used. This system is fast to react. As HV components, cables and more come on line, if there is a short to chas sis ground the contactors will open instantly, the HV capacitors will discharge and codes will set and “lock” out the driver’s ability to “READY” the EMV.
These codes should be treated with utmost care as something is wrong with the HV safety system.
This “active test” is done before the contactors are closed. When in “Power On” mode most of the time the HV bat tery isn’t connected to any other HV part. We know of three exceptions: the older Honda IMA systems, the Renault Zoe EV early model, and newer Ford HEVs as the HV battery is connected to the HV system in “Power On” mode. So make sure you’re always protected from high voltage when working with an EMV brand you’re not familiar with. There are no “rules” an OEM must follow, so be careful!
Once the EMV has been set to “Power On,” a 12-volt circuit (Fig. 3) in the “HV battery ECU” will look for a leak in the high voltage battery by comparing two sections of the HV battery for “leakage.” Just like EVAP separates the EVAP system into two sections and then looks for decay with pressure or vacuum to locate a leak, the HV battery ECU uses that thinking. (Fig. 1 shows a simple version of type A detection.)
This circuit can monitor for an HV leak by placing a “voltage divider” between the Posi tive and Negative posts of the HV battery. That effectively divides the pack in half. If you had a 200-volt pack and measured at the halfway point of the cells arranged in series, you would have 100-volts at each measurement point. Upon restarting the EMV, comparing the two readings, assuming they were the same, one would know that the pack was not compromised. With learned memory, any small changes over time would be accepted as normal and the battery would pass an “HV Leak Test.” Then the contactors would cycle through their closing and testing phase. If the HV battery split voltage readings showed a larger than expected variation between the two sides, a determination could be made that the HV battery has a leak to the chassis. The contac tors would not close, so no READY light. A code would be set. (This is a simplified explanation.) You could replace the entire battery pack or you may be able to remove the HV pack, open it up and closely examine it for something that may cause that code. Some packs can be inspected while still in the EMV.
Fig. 5: Here’s an analogy. Consider a double-headed drum. If you pound on one end of the drum, the opposite end will vibrate at the same frequency. When AC current is applied to the low voltage side of capacitor A, an AC sine wave is sent onto the high voltage DC cable.
Fig. 3: Once the EMV has been set to “Power On,” a 12-volt circuit in the HV battery ECU will look for a leak in the high voltage battery by comparing two sections of the HV battery for leakage.
Fig. 4: This Type B circuit diagram shows an “AC source” that sends the alternating current to capacitor A and chassis ground.
Once the HV battery is connected to the rest of the HV system, another high voltage detection circuit in the ECU takes over. Look at the Type “B” circuit dia gram (Fig. 4). It has an “AC source” (No. 5) that sends alternating current to “Capacitor A” (No. 3) and chas sis ground (No. 7). The interesting thing about the use of capacitor “A” (usually a DC device) is that it can transfer the AC current through the capacitor with out having the high voltage connect to the low voltage of the sensing circuit. Think about a double-headed drum (Fig. 5), like a “Mridangam” from Eastern India. If you pound one end of the drum, the opposite end will vibrate at the same frequency. When the AC current is applied to the low voltage side of Capaci tor “A”, an AC sine wave is sent onto the high voltage DC cable (No. 10). That sine wave has an amplitude and a frequency. The frequency never changes, but the amplitude will if there is connection to the chas sis. A very small circuit (No. 9) makes an extremely low current connection back to the detection circuit to compare amplitude levels. Those electrical engi neers are clever. Depending on how big the leak is (the height of the amplitude), the system can either
turn on a warning light and set a code, put the EMV into limp in mode, or if the amplitude is too low, the contactors open and the high voltage is turned off. The EMV will not READY up until that HV leak is fixed.
One more fact to consider: when any high voltage component is mounted in the vehicle, it is always bolted securely to the chassis in more than one place. This is to ensure that a person will not become the ground path if a component has a high voltage leak to the chassis.
EVs with a bo om-mounted HV battery pack (Fig. 6) are sealed so if driving through standing water, water will not enter the pack. Some plug-in hybrids and most hybrids do not seal the HV pack as they are in the trunk or under a rear seat. Experience has taught us to look for these signs, mostly on hybrids:
• Animal chewing on cables and wiring
• Water in the pack from a leaky hatch seal
• A customer who spilled a liquid
• Overheated NiMH cell leaking electrolyte
• Dirt and debris in pack plus a dirty blower motor
• Someone who tried to “fix” it before There is more to learn about the construction and function of the many new components in EMVs entering service bays. Stay tuned for the next installment about tools and equipment you will need to service them.
Craig Van Batenburg is the lead trainer and CEO of ACDC, a hybrid and plug-in technician training company based in Worcester, Mass. ACDC started hybrid training in early 2000. ACDC owns a eet of 16 EMVs, from the most popular models to current EVs. Recently, ACDC has expanded to 5,000 square feet and added a battery lab. Class info is available at www.FIXEV.com or call 508 826 4546. Contact Craig at Craig@ xhybrid.com.
DURING MY FIVE PLUS DECADES of being in the automotive service and repair industry I have learned that diagnosing an engine performance problem, drivability problem or electrical problem is not an exact science.
GM teaches a thing called Strategy Based Diag nostics while Ford has their pin point charts. Some manufacturers supply us with the conditions to set a code such as what the PCM needed to see to set the code and what the conditions were to set the code.
I have always favored symptom-based diagnostics, where once we have identified the symptom we focus our testing on a specific area. All of these things have a certain amount of merit but the truth is the techni cian working on the car is basically alone.
I would like to compare the technician to a base ball pitcher. A pitcher is on the mound and he is all alone. It is he who has to decide what pitch to throw and to what location. He gets the signal from the catcher and it is he who must decide what pitch to throw and to what location. He may even shake off the catcher’s sign. Yes, he has the defense to back him up.
We as automotive technicians are like the major league pitchers. Some of us are very good with a good winning record. Having said that, not one of us has always batted 1000%.
All of us technicians have had our share of butt whippings just like a major league pitcher who has suffered the loss. We have our support in technical
training, technical articles we have read and our past hands-on experiences, and we take advantage of sources such as YouTube and our technical informa tion systems like Mitchell On Demand, All Data and Identifix. We may even have a coworker who can help give advice. Even so, we are like that major league pitcher on the mound. We are basically all alone. It is the technician who makes the call as to what test equipment to use and what to test.
We all know of the diagnostic value of our scan tools and are also aware of the limitations of the scan tool. In cases of a misfire code the misfire could be caused by a secondary ignition failure such as worn spark plugs of a defective coil or secondary lead. Based on the all-time high in odometer readings of vehicles that are currently on the road today, the problem may be compression related such as cylin der blow by, leaking intake or exhaust valves, wiped cam lobes, lean or rich density misfires or a retarded cam timing issue. To dynamically pinpoint the cause of a misfire for example, the Digital Storage Oscil loscope (DSO) offers us the ability to find the cause of the misfire. In addition, the DSO gives us the abil ity to view and analyze PCM inputs and output PCM drive signals as well as bus circuit signals — all of this done dynamically with the DSO. On my travels across the country teaching automotive technology, I find that roughly 10% of the techs attending have a DSO and use it.
I also know several shops that have purchased a premium scan tool that includes a DSO and a
See the complete picture before and after repairs.
Easily identify and complete calibrations in-house.
Get instant access to our team of 400+ certified technicians.
Find out what asTech can do for you at asTech.com
multimeter which are never used. Before we begin our digital waveform analysis lets take a look at Fig. 1 of a standard DSO screen. The vertical scale has 10 major divisions and will represent voltage. The horizontal scale represents time. We can monitor voltage changes over time. There are 10 major divi sions on the horizontal scale. Each major division on the vertical and horizontal scale includes five minor divisions.
More importantly we can determine the integrity of the waveform. One of the most important func tions of a DSO is the ability to view a secondary or primary ignition event to determine the cause of a misfire. One well known automotive instructor has stated that “there is more diagnostic value from a primary or secondary ignition waveform than any other waveform on any other automotive application. In an earlier article titled the Anatomy of Wave form, which can be found in the August 2021 edition of Automotive Service Professional, we provided much detail on analyzing primary and secondary ignition events.
In this article we will briefly touch on primary and secondary ignition events when using a DSO. First let’s discuss the secondary KV probes needed when using a DSO. See the two examples in Fig. 2 and Fig. 3.These probes have an attenuation factor of 1000 to 1. What this means is that if the voltage per division setting is 1 volt per division, the attenuation now becomes 1Kv per division. Fig. 3 is known as a COP (coil on plug) wand. This wand was designed to inductively pick up a secondary event from a COP unit by simply laying the probe to the top of a COP unit. Some modern COP coils are so heavily potted that the magnetic field is too weak to pick up with these probes. On the heavily potted COP units a sec ondary lead can be used between the COP unit and the spark plug and then clamp the universal second ary probe around the lead. However, many of the COP coils will emit a strong enough magnetic to dis play a secondary event when using the COP wand. This probe works as well by laying it next to a sec ondary lead on distributorless ignition systems. It is important to remember that secondary firing events on COP systems are negative firing events so the invert function must be used on the DSO. On distrib utorless ignition systems, half of the firing events
Fig. 1: Example of a standard DSO screen. The vertical scale has 10 major divisions that represent voltage. The horizontal scale represents time. (all photos by author)
Fig. 2: Universal KV probes have an attenuation factor of 1000 to 1. If the division setting is 1 volt per division, the attenuation now becomes 1Kv per division.
At Cool Boss, we focus on innovations that deliver incredible comfort and value. Every one of our COOLBREEZE™ and COOLBLAST™ evaporative coolers use tap water to instantly chill areas at a fraction of the cost of traditional air-cooling methods. Just plug them into a standard wall outlet, fill them with water, and instantly lower the surrounding temperature by as much as 26 degrees. It’s that simple!
Learn more at COOLBOSS.COM or call 1-855-2BE-COOL
are negative events while the other firing events are positive firing events, where we would turn off the invert function. On distributor equipped engines, all secondary firing events are of the negative polarity so the invert function must be used. If you are scope checking the primary side of the ignition system the invert function must be turned off since these are positive firing events. Let’s look at a good example from a DSO in Fig. 4. The time base is set at 1 mil lisecond per division with the voltage per division at 1Kv. When viewing a secondary firing event the most important portion is the spark at idle and no load condition. The minimum spark duration period should not go below 1 millisecond during an idle and no load condition. Once the mechanical condition is verified, I never chase a misfire symptom with worn original spark plugs with an odometer reading that shows a six-digit reading. There is an exception on the multi-fired coils on late model Ford engines where the PCM will fire the coils as many as three times when RPM is below 1,000 RPM. Above 1,000 RPM the Ford systems will revert back to a single fir ing event. The first three spark duration periods will measure about 0.5 milliseconds. When adding up all three events the spark duration period will add up to more than 1.5 milliseconds. Then with a light power brake condition, the duration period drastically shortens up and the spark line bends upward. This is the indication of a lean condition. Again we gave much more info and detail in our previous article titled The Anatomy of a Waveform.
When using a DSO there are five cardinal rules that must be known and used to obtain a good stable DSO waveform. See Fig. 5. Some DSOs are equipped with various presets which basically will get you in the ballpark but may not be the best seat in the house, which means you may well have to change some of the voltage, time and trigger level settings. Some DSOs have an auto sync function whereas the scope will sample the incoming signal and pre-con figure the time and voltage per division settings. The same results are predictable. The first consideration is to determine the scope trace mode. The auto selec tion is the most popular in that a trace will be on the screen without even being connected to a circuit. The second choice is normal, meaning that the DSO will not display a trace on the screen until a specific
Fig. 4: Scope checking the ignition secondary side. The time base is set at 1 millisecond per division with voltage per division at 1 Kv. The minimum spark duration period should not go below 1 millisecond during idle and no-load.
Fig. 5: Follow these five cardinal rules to obtain a good and stable DSO waveform.
trigger level is seen by the DSO. This scope trace mode is commonly used to detect a signal drop out. If the trigger level is not seen by the DSO then the miss ing event can be easily seen. The third choice is the most critical in the trigger level and trigger source. If a waveform is not seen or is unstable on the hori zontal scale, then the trigger level or trigger point is not seen by the DSO. In addition, the proper trigger source must be selected. For example let’s say you are doing a single trace with channel one, then the trig ger source for channel one must be selected. When doing a dual trace, triple trace, or a four trace you must select which channel is to be used for the trig ger source. The fourth setting is known as the trigger slope. The two choices are either positive or negative, or rising or falling. If you are scope checking a device that is ground-side controlled by the PCM, then the negative slope would be the best selection. When you are viewing a secondary waveform for example, the rising slope would be the best choice.
The fifth consideration is the probe selection. The standard DSO leads have an input impedance of 1 to 1. This means that 1 volt per division represents 1 volt per division on the vertical scale. In cases where it may be necessary to scope check a primary event, then a 10 to 1 probe would be needed. The reason being is that the maximum voltage per division is 10 volts on many DSOs and there are 10 divisions on the vertical scale then a maximum voltage display would be 100 volts. A primary ignition event varies between 250 volts to 350 volts depending on the system. Without using a 10 to 1 adapter the internal circuitry of the DSO could be damaged. Some scopes actually use a 20 to 1 attenua tion probe. With a 10 to 1 probe this means that if the voltage per division is set at 5 volts per division we sim ply multiply this value times 10 which now becomes 50 volts per division. This primary ignition check is very popular on the Ford and Chrysler systems where the primary drivers are in the PCM. We would simply back probe the negative coil terminal to obtain a pri mary ignition waveform. We noted in our previous article that a primary ignition waveform gives us the same diagnostic value as that of a secondary waveform. These two waveforms will literally mirror each other. See Fig. 6. When using a DSO to scope check the sec ondary circuit, a 1,000 to 1 probe would be needed. In addition, when scope checking the primary or sec ondary side of the ignition system always use the peak detect mode of the DSO.
Let’s take a look at a common hall effect crank sen sor that generates a 5V/0V toggle in Fig. 7. On the Snap-On scopes the time base icon represents the total horizontal time on the screen. Notice in Fig. 7 the total time on the screen indicates 50 milliseconds. With 10 divisions on the horizontal screen each division repre sents 5 milliseconds. We suspected a faulty hall effect CKP sensor was causing a jerk and buck symptom. Notice Fig. 7. The waveform looks flawless even though the symptom is consistent. The peak detect mode is on. Now let’s take a look at Fig. 8. We increased the time on the screen to 500 milliseconds or 50 milliseconds per division. Since we are still in the peak detect mode we increased the time base to increase our chances of seeing the signal drop out as indicated in Fig. 8. Some DSOs have a zoom function where we can automatically zoom in on the signal. The DSO simply decreases the voltage per division and decreases the time base. This
Fig. 6: Primary ignition waveform provides that same diagnostic value as a secondary. These two waveforms will mirror each other. When using a DSO to scope the secondary circuit, a 1000 to 1 probe is needed.
is sort of a magnifying effect. In addition, on the SnapOn scopes the voltage icon represents the total voltage on the vertical scale instead of a voltage per division. For example, if the Snap-On scope screen indicated 20 volts it represents 2 volts per division.
Let’s take a look at a common digital type signal from a magneto resistive type crank sensor found on
Fig. 7: A common hall effect crank sensor can generate a 5V/0V toggle. Here the total time on the screen indicates 50 milliseconds. A faulty CKP sensor may be causing a jerk/buck concern.
Glitch Detected
Fig. 8: While in peak detect mode, we increased the time base to increase chances of seeing the signal drop out.
Chrysler COP (PRI./SEC.)Heavy-duty pliers used to remove and install the large internal retaining ring in transmission cases.
26" handles provide the leverage needed to compress large retaining rings.
For use on GM 5L40, 5L50, 6L45, 6L50, 6L80, and 6L90 transmissions.
Straight .120" diameter interchangeable tips.
many GM engines. The symptoms include an intermit tent good crank and no start along with an intermittent jerk and buck symptom. The PCM has set a crank sensor code. Two separate replacements of the CKP sensor did not solve the problem. We tapped into the CKP signal wire and obtained the waveform in Fig. 9. Notice the scope settings are at 5 volts per division at a 20 millisecond per division time base. Notice the trig ger level is set at 3 volts on the rising or positive slope. This sensor generates a good 8 volt to 0 volt toggle. You can easily identify this bad signal in Fig. 9. A redun dant sensor signal circuit was installed and verified the problem was gone.
Let’s look at a linear type signal from a TPS in Fig. 10. The symptoms included loss of cruise control func tion along with a surge type symptom. During a KOER TPS sweep test notice the signal dropout in Fig. 10. If your scope is equipped with the single sweep mode the single sweep mode can be used. Using the single sweep test the DSO will begin drawing a trace when a trigger level is met and then freezes the waveform.
Whenever you are trying to detect a signal dropout or glitch you should always use the peak detect mode of the scope. This function puts the scope in the maxi mum sampling rate. Without the peak detect mode, signal dropouts or glitches may not be seen by the DSO. On the typical DSOs the sampling rate is propor tional to the time base. The sampling rate increases as the time per division is decreased to a faster time per division. So as the time per division is increased the sampling rate decreases. This is why the peak detect mode is so important. In my opinion the minimum peak detect mode should be a minimum of 10 mega hertz. That means the signal is sampled 10,000,000 times a second. Some modern day scopes greatly exceed that sampling rate. Back in the ‘80s there were a lot of arguments about the live analog scopes versus the digital DSO, whereas some techs argued that the live analog scopes gave you a better chance of catch ing a glitch. I simply don’t agree with that in light of the fact that the human eyeball updates at best four times per second. Another point I would make is that with the conventional analog scope you cannot record or freeze a waveform to analyze it. So it looks like the digital DSO is here to stay.
Signal tracing the oxygen sensor with a DSO can yield a lot of information. Let’s look at a good zirconium
Fig. 9: Example of a waveform when tapped into the CKP signal wire. This sensor generates a 8V to 0V toggle. You can easily identify this as a bad signal.
Fig. 10: Example of a linear type signal from a TPS. Symptoms included a loss of cruise control along with a surge. During a KOER TPS sweep test, notice the signal drop out.
Fig. 11: Example of a good zirconium O2 sensor signal. Notice the uniform rich to lean shifts with a clean waveform.
Fig. 11
oxygen sensor signal in Fig. 11. Notice the uniform rich to lean shifts and lean to rich shifts with a clean wave form. Now let’s look at an oxygen sensor from a vehicle with a rough choppy idle condition in Fig. 12. Notice the vast amount of hash on the oxygen sensor signal. The likely cause here is a lean density misfire. This
TPS Signal DropoutCentric® brakes are designed, manufactured, and tested to exacting standards to meet the demands of today’s vehicles. Engineered to match or exceed OE effectiveness, Centric aftermarket brake pads feel and function just like the original equipment.
sensor can be easily graphed out when using the scan tool but the vast amount of hash will not be seen.
The alternator on today’s engines is a major player. Alternators generate A/C voltages that must be rectified by the rectifier bridge and diodes inside the alternator into D/C voltages. PCMs can only identify D/C voltages. An alternator with a failed diode will create unwanted A/C voltages into the PCM and circuits. This usually creates a laundry list of DTCs along with severe engine performance issues. The DSO can easily detect a failed diode inside the alternator. We simply clamp the positive DSO lead to the feed wire of the alternator. I know that many of the alternators are buried and not easy to access. You could probe into the feed wire as close to the alternator as possible. Checking for A/C at the battery will not work since the battery acts as a big shock absorber.
Let’s take a look at this test in Fig. 13. The scope is A/C coupled which blocks out the D/C voltages. I like to teach that negative A/C voltage over 400 millivolts could spell problems. Notice that the ground tick mark is located in the middle of the screen. A/C voltages below this tick mark are of negative
polarity. The scope is set at a 10 millisecond screen time or 1 millisecond per division. On the vertical scale above and below the ground tick mark is 50 millivolts. Since this is the Snap-On unit, each division represents 5 millivolt. Notice that the maximum A/C negative voltage is 9 millivolt.
Most scopes have a function known as a low pass filter which helps block out unwanted electrical noise. For example, when scope checking a TPS sweep with the engine running, the scope leads could inductively pick up the magnetic fields from a secondary lead. If you are scoping out a signal whereas the trace has a lot of hash, the low pass filter could be used
Fig. 12: Example of an oxygen sensor from a vehicle with a rough choppy idle. A lean density mis re is the likely cause.
Fig. 13: Here the scope is A/C coupled which blocks out the D/C voltages. Negative A/C voltages over 400 millivolts can spell trouble. Notice that the ground tick mark is located in the middle of the screen. A/C voltages below this tick mark are of negative polarity.
to clean up the trace. Another example may include signal tracing the oxygen sensor where you may need to use the low pass filter function. There are premium scope leads that are heavily shielded to prevent unwanted electrical noise that can be picked up inductively by the scope.
A Honda Odyssey came into the shop with a high idle complaint. The idle would not go below 1,200 RPM. Normally we would all suspect a major vacuum leak. Smoke checking the intake system indicated no vacuum leaks. Blocking off the IAC air passage did not lower the idle RPM. There were no DTCs from the PCM. The TPS was checked and proved to be functional. With a DSO we decided to check the PCM drive signal to the IAC solenoid. See Fig. 14. This solenoid is ground-side controlled by the PCM. The on time is where the voltage is pulled to ground. The waveform tells us that the PCM is in control of the IAC control solenoid. There were no PCM codes. When doing
Fig. 14: Using a DSO, we check the PCM drive signal to the IAC solenoid. This solenoid is groundside controlled by the PCM. The waveform tells us that the PCM is in control of the IAC solenoid. There were no codes, but when we did a bus circuit sweep test, a traction control code showed a loss of communication with the PCM. When we performed a wiggle test at the ABS connector, the RPM came down.
a bus circuit sweep test, we discovered a traction con trol code stating loss of communication with the PCM. When doing a wiggle test at the ABS header connector the RPM came down. After doing a park to drive shift the RPM came down to a steady 600 RPM. We cleaned the male and female terminals to correct the connection problem. I can’t explain the strategy that Honda used to create this high RPM problem when the PCM loses com munication to the ABS module. The RPM increase was caused by the PCM advancing the spark timing.
On today’s modern day vehicles several modules communicate data to each other such as fuel level, engine speed, engine load, throttle angle, vehicle speed, brake input, A/C request and many more. A corrupted bus network can create a host of problems including lack of communication to the scan tool and loss of com munication between modules. It is likely to have a host of U series codes on the scan tool if you can even com municate with the network. A DSO would be the prime tool to determine if the network is corrupted. There are several different types of bus circuits but all are of the digital type signals.
First let’s dive into the GM class 2 network in Fig. 15. This is a single wire network that can be signal traced at pin two of the DLC.
Notice the good 7 volt 0 volt toggle. A Chevy Silverado came in with an intermittent loss of the electronic throttle control with a P1518 code. In addition, the radio would turn off and the door locks would cycle. Since all of these components are controlled on the class two net work, the car finally acted up with our scope connected to pin two of the DLC. Notice the corrupted signal in Fig. 16. The PCM would shut off the throttle and set the ETC code. On the early GM truck lines a TAC module is used to communicate with the PCM on a 2 wire UART (universal asynchronous receiver) type bus circuit. The TPS and APP sensors report their position to the TAC module. The TAC module then communicates this data to the PCM on the UART network. The PCM then sends the throttle command to the TAC module and the TAC module driver sends the command to the TAC motor. The TAC module then communicates their position to the PCM on the two-wire UART network. The TAC mod ule drives the TAC motor by commands from the PCM. See a good UART signal from this vehicle in Fig. 17. With the radio turning off and the door locks cycling we know that these functions are controlled on the class two
Fig. 15: Example of a GM class 2 network. A single wire network can be signal traced at pin 2 of the DLC. Notice the good 7V to 0V toggle.
Fig. 16: Example of a corrupted signal on a Chevy Silverado. The PCM would shut off the throttle and set an ETC code.
Fig. 17: The TAC module drives the TAC motor by commands from the PCM. Here we see a good UART signal. The voltage spike seen in Fig 16 was from the TAC module’s bad ground and the voltage spike was back feeding from the UART network into the PCM and corrupting the class 2 network.
network. The voltage spike seen in Fig. 16 was from the TAC module’s bad ground and the voltage spike was back feeding from the UART network into the PCM and corrupting the class two network. A poor TAC module ground was found on the back side of the intake manifold. Another example of a corrupted class two network was from a Cadillac Deville with an intermittent no crank condition. A bus circuit sweep test showed a laundry list of U series codes. Because of that we suspected a corrupted class two circuit. Using a DSO, we probed terminal two of the DLC during KOEO conditions. The 7 volts 0-volt toggle looked nor mal in Fig. 18. Now during a cranking attempt notice the DSO trace came well above ground in Fig. 19. This tells us there has to be a ground problem somewhere. Voltage dropping the starter ground circuit showed nearly battery voltage. The ground cable between the block and body was defective. Remember on these cars, the battery is under the rear seat.
The most common bus circuit on today’s mod ern day vehicles is a two-wire high speed network known as CAN. On all CAN compliant vehicles the CAN high terminal reports data to pin six of the DLC, while the CAN low data reports data to pin 14 of the DLC. See Fig. 20. The top trace is CAN high
Fig. 19: During a cranking attempt, notice the DSO trace came well above ground, which indicates a ground problem.
and the digital toggles begin at a 2.5 voltage level and at that level the circuit is at rest. When the voltage jumps to 3.5 volts it means that a module is communicating. Pin 14 CAN low data is the bottom waveform; 2.5 volts is at rest. When the voltage jumps down to 1.5 volts it represents data and that a module is communicating. If these
Fig. 18: Using a DSO we probed terminal 2 of the DLC during KOEO conditions. The 7V to 0V toggle looked normal. Notice the slight voltage shift above ground during KOEO.
2001 CADILLAC DEVILLE GOOD CLASS 2 BUS SIGNAL DURING KOEO 2001 CADILLAC DEVILLE (class 2 bus circuit indicating bad ground)signals are corrupted we would need to monitor the waveform as we unplug one module at a time to see if the waveform is corrected.
In our future articles we hope to include current ramping by using the low and high inductive amp probes interfaced with the DSO and another article covering the use of a vacuum and pressure transducers interfaced with the DSO.
You may be thinking of investing in a DSO or if you already have one you may be motivated enough to start using it and going through the buttonology learning curve much like you did on your scan tool or cell phone. The question is that if you look in the rear view mirror of your past experiences in diagnosing drivability issues, were there any cases where you could have done, may have done or should have done testing with a DSO to locate the problem quicker and more efficiently? I can assure you that in the future you will see a need to use a DSO.
The industry is be er because of your commitment.
Bill Fulton is the author of Mitchell 1’s Advanced Engine Performance Diagnostics and Advanced Engine Diagnostics manuals. He is also the author of several lab scope and drivability manuals such as Ford, Toyota, GM and Chrysler OBD-I and OBD-II systems, fuel system testing, and many other training manuals in addition to his own 101 Lab Scope Testing Tips. He is a certi ed Master Technician with more than 30 years of training and R&D experience. He was rated in the top three nationally on Motor Service magazine’s Top Technical Trainer Award and has instructed for Mitchell 1, Precision Tune, OTC, O’Reilly Auto Parts, BWD, JD Byrider, Snap-on Vetronix and Standard Ignition programs. You may have also seen Fulton in many Lightning Bolt Training videos and DVDs and read his articles in many auto service magazines. He owns and operates Ohio Automotive Technology, which is an automotive repair and research development center and where the images for this article were produced.
Fig. 20: CAN high terminal reports data to pin 6 of the DLC and CAN low data reports data to pin 14. The top trace is CAN high and the digital toggles begin at a 2.5 voltage level, and at that level the circuit is at rest. When voltage jumps to 3.5V, it means that a module is communicating.
NLESS YOU HAVE JUST STARTED IN the automotive field in the last few weeks, you likely have faced this work order. A customer is concerned about exhaust noise.
You get in the vehicle and start the road test. The exhaust is quiet, but the familiar hum or growl of a wheel bearing is oh so familiar. You return to the shop and alert the front desk service adviser that the cus tomer has a bad wheel bearing and the exhaust on the vehicle is just fine.
Identifying the noises of a bad wheel bearing is often the easiest part of the failed wheel bearing pro cess. Identifying and isolating which wheel bearing is causing the noise can often be the difficult part.
A wheel bearing is considered a low maintenance part of the vehicle today, unlike when the rear-wheeldrive vehicle was still prevalent. It was considered a regular maintenance item, and manufacturers like GM recommended that the wheel bearings be cleaned and repacked every 15,000 miles.
But with the change to front wheel drive as the norm, those serviceable front wheel bearings quickly faded away and the advent of the hub or press fit wheel bearing became the norm.
Just because a wheel bearing is considered a low maintenance part doesn’t mean that it will last forever. They do have a lifespan and they do fail and need to be replaced. Wheel bearings are a vital part of the opera tion of a vehicle and are considered a critical safety component. After all, they are carrying the weight of the vehicle, allowing for steering, braking and suspen sion movement.
The wheel bearings that are in use today are perma nently lubricated, hermetically sealed and either the steel (ball) bearing or the tapered bearing type. They are carefully assembled to allow the wheel to rotate smoothly, quietly and for a substantial amount of time.
1. A road test and a visual inspection found this bad wheel bearing, and yes, they drove it to the shop.
Today’s sealed wheel bearings don’t require any ser vice in their lifespan, and that lifetime is expected to be about 100,000 miles or more. But they do and can fail.
Before we talk about how to diagnose a failed or failing wheel bearing, it is good to understand why a wheel bearing fails.
2.Not all noises are going to indicate a bad wheel bearing. They may be isolated to one wheel or corner of the vehicle, but again the visual inspection will typically show the actual problem like this bad CV shaft.
Potholes, rough roads, overloading, unbalanced tires, accidents, improper bearing installation/ replacement, radical car modification and other things can cause wheel bearing failure. But the breakdown of lifetime wheel lubrication/grease is the most common cause of wheel bearing failure.
They are most often caused by the failure of the lubrication that is sealed inside the bearing assembly.
Water and debris can eventually get past the seals that are designed to keep this stuff out and permeate into the permanent grease responsible for lubricating the bearing surfaces.
Once the grease that is protecting the precision roll ing surfaces becomes contaminated it will be displaced,
3.The ABS encoder ring has rusted and separated from this wheel bearing, resulting in an ABS code. The fix is to install a new wheel bearing assembly.
4.When replacing a wheel bearing or wheel bearing assembly, changing all the needed parts such as torque to yield fasteners is a must.
and metal-to-metal or metal-to-debris con tact can occur creating yet more debris.
As this debris starts to accumulate the bearing assembly will begin to encounter more and more friction. This excess friction can allow for changes in rotational direction or geometry (wobbling), creating noises, steering wheel movement, Anti-Lock Brak ing (ABS) issues and in a rare, worst-case scenario — catastrophic failure.
Noise is the most common complaint of the metal-to-metal contact of a failed wheel bearing. The customer may not even notice the noise at first because it may gradually get louder, and the cus tomer has become acquainted with the noise. But wheel bearing noises are com mon, and that noise can be used to help diagnose where it is coming from.
Even though noise is the largest com plaint that a failed wheel bearing will create, ABS faults are also common. The ABS sensor magnetic encoder ring can be incorporated into the outer seal of the bearing assembly. Some of these encoder rings are integrated into the seal; others are bonded to the seal and over time can corrode, separate, crack and fall off. This will result in an ABS code being set and the only way to repair the issue is to install a new wheel bearing assembly.
Because most of the wheel bearings and hub assemblies that we see today are sealed, we need to rely on other methods for diagnostics and the noise of a wheel bearing can help.
If we are performing a road test to diag nose a wheel bearing noise, the cyclical growling, humming noise will generally become louder the faster we travel. It may get louder or quieter or even disappear as we pitch or change the direction the vehi cle while driving. This happens because of the weight transfer to the wheels as the vehicle rotates around its center of gravity. You don’t need to be driving fast to perform this check, but fast enough to
apply a good load equally to both sides of the vehicle as we pitch back and forth.
When performing this type of wheel bearing diagnostic we want to listen to where the noise gets the loudest. Is the noise louder on the left or the right only when the weight is pitched to that side? That usually indicates the wheel
bearing concern is on the side the weight has shifted to. But be aware that this test may show a wheel bearing that gets louder when the weight is off it because the dam age to the bearing’s rotating surface may be on the top of the bearing assembly, and the pitching is pulling up in that direction augmenting the noise.
The PL6100 from SOLAR provides an ideal stable power supply mode to maintain vehicle system voltage during reflashing events:
• Continuous power up to 100A (no time limit)
• Selectable target voltage from 13.1-14.9V
• Minimal voltage ripple (<100mV)
• Rapid Load Response Technology
• Extra-long 13’ cable reach
• Includes charging capability (60/40/10A)
• Requires 20A outlet
Charge mode compatible with a wide variety of battery types:
To learn more, visit our website at cloreautomotive.com or call 800.328.2921
We need to pay particular a ention to noises that don’t change when we pitch the vehicle. The cause may not be a failed wheel bearing, but bad tires, bad drivesha hanger bearings and front CV axle sha support bearings can o en be misdiagnosed as a bad wheel bearing. Other noises such as rear wheel drive differential noises may only occur during deceleration.
Another common issue that will occur with a failed wheel bearing, especially on 4WD pickup trucks, is that an extra steering input will be needed when turning a corner or on a long sweeping curve. These wheel bearing failures typically do not make any noise, don’t cause a vibration or any other driver concerns. But when the driver starts a turn, when the weight of the vehicle shi s, extra steering input will be needed to keep the vehicle aimed in the direction that the driver wants to go. This will happen because the wheel bearing is now allowing excess lateral, axial or angular movement and changing the front-end geometry of the truck.
Once we have identified and verified
that we have a failed wheel bearing concern from the road test (we may or may not have an idea which bearing has failed), we can begin the on-hoist diagnostic.
Once the vehicle is safely raised off the ground we can begin a visual wiggle test inspection of the wheel bearing assembly. We will be looking for any excessive movement in any of the wheel bearing assemblies. Grab the wheel at the top and bo om or at 10 o’clock and 4 o’clock, which is my go-to position for wheel bearing inspection. I have found that not being at the 12 o’clock and 6 o’clock positions will show more wheel bearing excessive play than the typical top and bo om location.
We are not expecting any movement or play. If there is movement that is likely the bad bearing especially if it is accompanying the road test noise location.
When using this wiggle test, the extra steering effort 4WD truck front hub/wheel bearing usually shows extreme movement.
Don’t forget to inspect the rear wheel while performing this test as they can fail even though there typically isn’t as
Visit our website for a complete, internet-based catalog designed exclusively for the Professional.
much weight on the rear wheel bearings as the front assemblies.
If we still haven’t identified the noise-causing culprit at this point, or we have a good idea what bearing is failing but want to ensure we are chang ing the correct one, I like to use the electronic stethoscope or chassis ear method to verify which bearing has failed.
The use of an electronic ear will allow for the placement of sensors on each of the hubs/knuckle assemblies. I will then road test the vehicle at a speed that produces the wheel bearing noise or pitch the vehicle to get the bearing to emit the growling noise that the electronic stethoscope will pick up and send back to the headphones. I will switch from one transmitter to the next to isolate what corner of the vehicle the noise is coming from. I will often get a coworker to ride with me so they can listen while I get the vehicle to make the noise. Using the electronic stethoscope has saved a lot of time and the replacement of tough to diagnose wheel bearings over the years.
Once we have made the decision on which wheel bearing has failed, we can start on the replacement. Wheel bearing or hub replacement may require the use of some special tools, especially if the wheel bearing is a press fit into the hub or knuckle. The use of a hub tamer kit will make this type of bear ing replacement substantially easier. Don’t forget to pay attention to detail when doing these types of bearing replacements. Make sure that the retainer ring groove is clean, a new retainer ring is used, and
My old ChassisEar set has been a huge help in locating a bad wheel bearing on many vehicles. I haven’t replaced the wired with the wireless kits that are available today.
that the assembly is installed squarely with a small amount of lube to aid in the installation.
With most wheel bearings being a complete hub assembly, the replacement of a hub is often quite straightforward, provided you don’t live in the rust belt. Some aftermarket bearing companies will now sell the complete knuckle assembly to speed and ease the wheel bearing replacement and ensure that all the parts that should be changed are changed.
The final step to completing either the press-in bearing type or the hub assembly type wheel bearing replacement is the careful torquing of the axle nut to the prescribed torque. One of the greatest causes of premature wheel bearing failure following its replacement is the improper torquing of the axle nut.
The axle nut torque will preload the wheel bear ing. If the axle nut is under torqued it will allow too much movement causing irregular loading and excessive bearing wear. And if the axle nut is over torqued it will produce unnecessary load causing the bearing to overheat.
The hub tamer kit that I have has saved a lot of time, aggravation and damaged components, when changing a pressed in wheel bearing assembly.
It can’t be stressed enough to stay away from holding the impact gun on the nut and guessing how tight the axle nut is. Using the proper torque wrench to ensure the replacement is done correctly will give the same service life as the original.
Jeff Taylor boasts a 30-plus-year career in the automotive industry as a fully licensed professional lead technician. Jeff works for the CARS Training Network Inc. in Oshawa, Ontario, Canada. He is also heavily involved in government focus groups, serves as an accomplished technical writer, and he has competed in international diagnostic competitions as well as providing his expertise as an automotive technical instructor for a major aftermarket parts retailer.
A rundown of selected tools to consider adding to your shop’s arsenal
EVERY NOW AND THEN WE LIKE TO BRING YOU UP TO speed with regard to new tools and equipment that have recently hit the market and should be of interest in terms of capabilities and features.
The Continental Autodiagnos Pro Automotive Diagnostic Sys tem has been designed and built by developers who build diag nostic tools for Original Equipment Manufacturers, and it uses the same OEM scan tool development platform. Continental’s
scan tool is continuously enhanced to help streamline ve hicle diagnosis and repair. In addition to domestic applica tions, the tool covers leading European makes, including recently added coverage for 1.5 million Volkswagen, Audi and Mercedes-Benz vehicles in the United States and Can ada, as well as a wide range of Asian and domestic makes.
The Autodiagnos Pro Automotive Diagnostic System — which can utilize an existing laptop, tablet or other compli ant PC — is offered on a subscription-based model so there is no large, up-front investment.
On the TPMS side, Continental offers two dedicated TPMS tools: Autodiagnos TPMS SE, which allows techni cians to focus on TPMS service and Autodiagnos TPMS D which provides both diagnostic and service capabilities. An optional tread depth gauge can be coupled with the TPMS D tool to support tire, front-end and suspension sales. Both tools use Continental specific software to streamline TPMS service and diagnostics.
Autodiagnos TPMS D reads and diagnoses 100% of OE TPMS sensors and 20 aftermarket TPMS brands. The Au todiagnos SE works with 100% of OE sensors and sensors from Continental’s Redi Sensor and Schrader’s EZ-Sensor. “Both tools can easily perform relearns on 98.6% of all do mestic, European, and Asian TPMS-compliant vehicles,” say Continental officials.
Milwaukee Tool offers a new cordless electric random orbital polisher, the M18 Fuel15mm. The polisher provides an operating speed range from 2,650 to 5,100 rpm, and an eight-position speed dial for easy speed selection. The polisher is designed with user convenience in mind, with low vibration, low noise and an extended length for superior operating balance.
Matco Tools offers its Maximus 4.0 scan tool. The new diagnostic tool provides a viewer-friendly 13.3-inch screen, CAN FD, a battery analyzer mode, a four-channel scope and FCA security gateway access. A Bluetooth battery tester allows quick battery diagnosis/condition/issue identification. Also available is Tech 2 remote diagnosis that allows the technician to consult directly with experts remotely when dealing with difficult and complex diagnostic issues.
BendPak has released the new MDS-6EXT mid-rise vehicle lift. While the dual-scissor pneumatic system is applicable to a wide variety of vehicles, the extended lift is ideal for servicing electric vehicles that may feature lift points that exist on the outer edges of the vehicle underbody. The lift is also configurable to accept vehicles that have very low ground clearance and/or that are equipped with very wide tires. Load capacity is rated at 6,000 pounds. The lift is designed for either above-ground or floor-flush placement.
Florida Pneumatic has released a new Aircat 115-degree angle die grinder, the Aircat 115. The tool features 0.6HP and a maximum speed of 18,000 rpm. The 115-degree angle provides an ergonomically improved working angle, and the quick-change spindle lock provides easy bit changes. It’s a great alternative to straight or 90-degree versions.
both spot lighting and flood lighting selection in low, medium and high illumination levels. If the charge drops, the light can continue to operate while plugged in and recharging. The BearTrap can be used as a stand-alone, hung with the built-in stowable hook or it will clamp to a variety of surfaces. A magnetic base is also featured for secure mounting to a steel surface. It is ideal for underhood, under-car or under-dash lighting.
Launch Tech USA offers its new pro-level Millennium MAX diagnostic system. The tablet features a seven-inch touchscreen and supports full diagnostic capabilities. Features include automatic VIN identification and supports for CAN FD and Do1P protocols. Software updates are easy via Wi-Fi
Continental delivers the exact replacement blower motor you’ll need to restore original cooling performance. Built with unsurpassed quality and reliability for OE vehicle-specific fit and performance, every motor features true OE connections and mounting flanges for easy and for trouble free install. No flying leads or wire splicing. All wheels included.
Streamlight announces its newest addition, the cordless/rechargeable BearTrap MultiFunction work light. Offering bright, worker-friendly illumination, the light features
The Mastercool Dual EVAP/High Pressure diagnostic smoke machine takes smoke detection to the next level. The versatile smoke machine with a truck adapter accessory kit handles smoke detection for EVAP issues, turbocharger systems, intake systems and even heavyduty truck smoke testing. The tool features an internal compressor, allowing mobile testing when shop air is not available, but still allows the use of shop air (or inert gas) if needed.
Autel offers its newly released Intelligent ADAS system for ADAS calibration and wheel alignment applications. The ADAS IA900WA offers a single system that combines ADAS calibration capabilities with wheel alignment function in one space-saving package. The alignment system software covers 1996 and later domestic and import applications, providing a 24-inch touchscreen for user convenience. Six high-res tracking cameras automatically monitor on-lift vehicle height and robotic frame movement allows alignment accuracy readings to 0.02-degrees. Combining ADAS service and alignment service into one package is especially useful when shop floor space is at a premium.
cover and locate the hose connecting the intake manifold to the crankcase.
Disconnect the hose from the intake manifold side and clean o any residue with a cloth. Blow into the hose. If there is some air resistance, the check valve is operating correctly. If there is no resistance, the PCV valve should be replaced.
If fuel trim values improve and move closer to zero, valve replacement is recommended. If values do not improve, re-install the original valve.
Use of the GFF is permitted at this point.
Here are tips to diagnose crankcase breather issues with 2008-2013 Volkswagen Passat sedans. You may nd rough running, engine noise and MIL on with DTCs P0300, P0301, P0302, P0303, P0304, P2279, P1297, P1093 or P2187 stored in the ECM.
P0300 random/multiple cylinder mis re detected
P0301.......... cylinder 1 mis re detected
P0302 cylinder 2 mis re detected
P0303 cylinder 3 mis re detected
P0304......... cylinder 4 mis re detected
P2279 intake air system leak
P1297 charger throttle connection, drop in pressure
P1093 bank 1 fuel measuring system 2 malfunction
P2187 .......... system too lean at idle, bank 1
A faulty PCV valve will allow pressurized intake air back into the valve cover/ crankcase. This pressurized air can blow out of several openings. The oil ll cap, air lter and dipstick should rst be checked for evidence of oil blow out.
With the engine o , remove the engine
With the engine running, disconnect the hose from the valve cover. Plug the hose and check idle quality. If idle quality improves, replace the PCV valve. With the engine running, remove the dipstick. If idle quality improves, replace the PCV valve. Remove the oil ll cap. Place a sti piece of paper over the opening. The paper should be sucked against the hole within a few seconds if the PCV valve is operating correctly.
The best way to ensure the functionality of the system is to look at fuel trim readings in MVB32. If faults pertaining to the PCV valve are found, do not erase the faults. Proceed with the following steps prior to following the GFF test plan to avoid erasing fuel trim readings.
Using VAS tester, read current fuel trim level in MVB 32 eld one (idle fuel trim) and two (part throttle). Normal values are 0 +/- 3 in both elds.
Replace the original valve with a knowngood test part.
Make sure no additional loads such as A/C and heated seats are turned on during the test.
If the noise goes away or the engine is no longer running rough, PCV valve replacement is recommended.
Using VAS tester, run basic settings 32 for at least ve minutes.
While running basic settings 32 for ve minutes, we can monitor elds one and two for fuel trim readings.
This bulletin applies to 2015-2017 Mitsubishi Outlander Sport vehicles. The check engine light may be on and a shift shock may occur when shifting from neutral to drive and neutral to reverse, due to a fail-safe function.
As a result, DTC P1740 will be stored during the solenoid valve monitoring operation.
Replace the CVT-ECU with a new counter-measure part to change the setting of the solenoid valve voltage monitoring circuit.
Visit autoserviceprofessional.com/TSB for additional service bulletins.
Information courtesy of Mitchell 1Aftermarket Auto Parts Alliance Inc. 21
Aftermarket Auto Parts
www.myplace4parts.com
IBC www.hawaiigetaway2023.com
American Express 13 www.americanexpress.com/business-solutions
asTech 25 www.astech.com
Autel 5,
Centric
Clore
www.autel.com
33 www.centricparts.com
41 www.cloreautomotive.com
Continental 47 www.continentalaftermarket.com
Continental
Cool Boss,
Federated Auto
www.redi-sensor.com
27 www.coolboss.com
11 www.federated5050challenge.com
Lang Tools 31 www.langtools.com
Launch Tech
www.launchtechusa.com
noble6 34 www.noble6.com
O’Reilly
OTC
42-43 www.firstcallonline.com
OBC www.otctools.com
OTOFIX 37 www.otofixtech.us
ProMAXX
www.promaxxtool.com
Raybestos 7 www.raybestos.com
Robinair IFC www.robinair.com
Schrader
Sellars
SEMA
www.schradertpms.com
www.shoptowels.work
www.semashow.com
www.frogtape.com/performance
www.standardOFHA.com
www.texausa.com
and stands tested
handle
Engineers
protect
(LDJ Models Only)
2-ton aluminum jack
3-ton jack
3.5-ton jack
5-ton jack
5-ton jack with air/hydraulic assist
10-ton jack
10-ton jack with air-assist
20-ton jack
22-ton under axle jack with air/hydraulic assist
27.5-ton under axle jack
2-Ton capacity aluminum jack stands, pair 3-Ton capacity jack stands, pair 4-ton capacity jack stands, pair 6-Ton capacity jack stands, pair 12-ton capacity jack stands, pair
22-Ton capacity jack stands, pair
22-Ton capacity jack stands, pair