
6 minute read
advantage
3

1 Redundant pipework was colour-coded in the model and helped reduce the overall load on the building 2 Model geometry was directly exported to STAAD and SFRAME for structural analysis 3 During weekly client meetings, progress was monitored by reviewing the latest model using Bentley Navigator, an i-model, and progressive PDF views
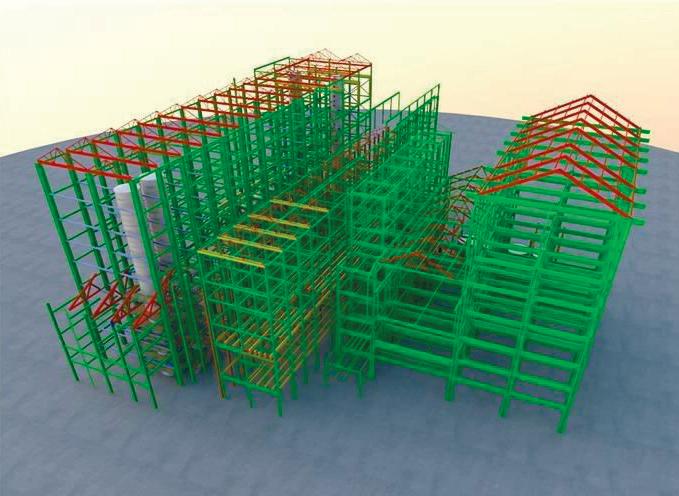
Model advantage
Multidisciplinary consultancy Stopford Projects uses 100-year-old drawings to help create an intelligent 3D model of structural inspection survey results
Built in 1873, the Winnington Works ings reflected the British Standards of 1906. i-models, and progressive PDF views for at Northwich, Cheshire, was These original plans yielded enough data for dynamic project review and analysis. Being acquired in 2006 by Tata 95 percent of the 3D model. The few 2D draw- able to easily view the 3D model helped the Chemicals, the second largest pro- ings of subsequent plant modifications com- client monitor progress, as well as visualise ducer of soda ash in the world. Tata prised the remaining 5 percent. Also, a fairly how the model would aid in maintenance Chemicals asked Stopford Projects to per- recent model of a large vessel was used. planning. At the conclusion of the project, form a full structural survey of the 6,000 m The first step was to create a custom library Stopford delivered a 12-volume survey sq wet-side soda ash plant as part of an ongo- of obsolete steel and wood member sections report, the 3D model in AutoCAD, general ing asset management and maintenance in ProSteel, as well as a catalog of obsolete arrangement drawings, and as-builts. strategy. Stopford delivered an intelligent 3D iron pipe standards in AutoPlant Piping, When remediation commenced, the 3D model created in Bentley’s ProSteel to map Bentley’s piping design and modelling soft- model was modified to reflect current ascorroded components throughout the plant. ware. Structural elements were produced built conditions. Colour-coding facilitated
The $1.5 million Tata Chemicals project using the ProSteel shape files. Custom pipe prioritisation of projects, with safety issues launched in April 2011. Stopford had com- specifications were produced using modified highlighted such as spurious loads, restrictpleted the survey by September 2011, and ductile iron catalogs. General arrangement ed access areas, and unsafe stairways. was awarded follow-on remediation works. drawings were generated directly from the
Bentley’s structural steel detailing and fab- model, using ProSteel workframes clipping Maintenance and safety rication software ProSteel was critical to suc- planes to produce plans and elevations. Stopford produced an adaptable tool for Tata cess because Stopford based its winning bid Column and beam annotations are read Chemicals to use in maintenance planning on fast completion. Although Tata Chemicals directly from the model database. and personnel training. The model revealed did not initially specify an intelligent 3D places that were not readily visible in photomodel as the required deliverable, Stopford Colour coding graphs or drawings, such as areas encased persuaded the client to reconsider by demon- The general arrangement drawings had in scaffolding. Plant safety was improved strating ProSteel’s features — including numerous sectional views of each floor, and through an awareness of escape routes. All model production speed, automatic updat- each structural element was given a unique stairways were brought up to modern staning, and model exporting to AutoCAD. tag number. The 3D model included 13 pri- dards as a result of the inspections. mary structural steel models, 15 secondary Tata Chemicals can maintain the 3D Component survey structure models, 13 piping and equipment model in ProSteel or convert it to AutoCAD The survey team had to start from scratch at models, and all 102 staircases in the com- solids and/or ACIS bodies. In addition, the Winnington Works. The wetside soda ash plant is a 10-storey steel-framed building on a Subsequent to ‘‘ the successful survey ability to interface with other software such as Staad.Pro and Bentley AutoPipe will help to T-shaped area with overall dimensions of 90 x 75 m. The project, Stopford was awarded five jumpstart future projects that require data for structural analstructure is a mix of 19th-cen- follow-on projects in the wet-side ysis, isometric generation, and tury timber, early 20th-century columns, beams, and bracbuilding and used the intelligent 3D other functions. Estimating the cost to duplicate or expand ing, and 1950s-era steelwork. model extensively facilities is made easier with The supporting structure is now a structural steel shell clad in corrugated steel panels. Structural plex. In total, more than 10,000 structural ’’ access to an intelligent 3D model. For example, the 3D model of the Winnington Works wet-side connections are mainly riveting, with sec- elements were modelled in ProSteel, and soda ash plant could be used to estimate the tions riveted to form composite members. 2,500 metric tons of iron pipe were mod- cost of future steelwork by extracting the The building has remained virtually elled in AutoPlant Piping. data for the steel components and calculatunchanged since its last major expansion in Stopford took the general arrangement ing the total weight. 1950. Over time, the constant wet, alkaline drawings to the site and used the tag numatmosphere has degraded the materials. bers on the reports and photographs to Counting the cost
Stopford did the structural inspection inspect the as-built structure. Degraded sec- Using Bentley software allowed the project and reviewed the major equipment and tions were mapped to create a visual repre- team to achieve their schedule for modelling pipework that impinged on the structure. sentation to develop maintenance plans. An the plant. The firm had priced the job at oneThe survey team inspected 5,750 individual up-to-date, colour-coded inspection model third less than some of the other bidders structural elements and prepared documen- was produced, and 3D PDFs were generated based on the anticipated ease and speed to tation, with every element photographed, for client review. Various colours indicated model. This was the main reason Stopford assessed, numbered, and recorded on draw- areas with no defects, minor defects, major was awarded the project, according to David ings. All secondary steelwork was inspect- defects, and severe defects. Coupe, piping department manager. ed, including platforms, walkways, concrete Subsequent to the successful survey projfloors, and other load-bearing elements. Inspection results ect, Stopford was awarded five follow-on
The results of the survey were evaluated During the on-site inspection, ProSteel projects in the wet-side building and used for corrosion levels on individual compo- made it easy to keep the 3D model up to the intelligent 3D model extensively. These nents, so that Tata Chemicals could plan date. A change in the size of a structural sec- projects included a lateral load study associremediation work. tion, for example, automatically adjusted all ated with re-cladding the building, stairway the connecting elements to the modified replacements to bring stairs up to current 3D model size, and the respective general arrangement standards, removal of a concrete floor and Stopford began building a basic model based drawings were simultaneously updated. replacement with steelwork, and inspection on 671 archived drawings, including as- At the weekly progress meetings, of the utilities building. builts dating back to 1908. The earliest draw- Stopford used Bentley Navigator, Bentley ■ bentley.com