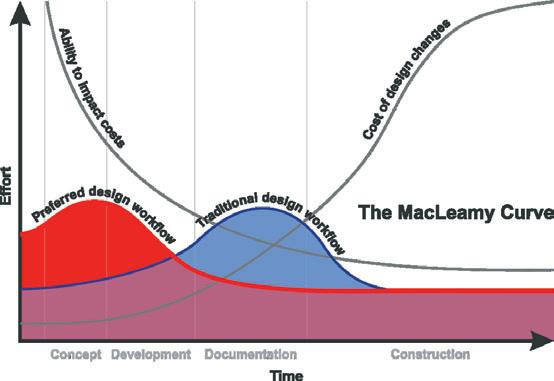
20 minute read
BIM for manufacturers
Why manufacturers have a huge part to play in Building Information Modelling.
In construction the focus is placed on the importance of the main contractor, the supply chain and design team. Very little is thought of the manufacturing supply chain in comparison or what this role can bring to a development.
The construction industry is often criticised for its lack of innovation, but it may be that we are looking in the wrong place. Recent visits to trade exhibitions, such as Ecobuild, prove that there is an abundance of innovation — if you know where to look.
Main contracting does not allow for a great deal of innovative scope. Projects are often scrutinised for overhead and profit, which does not lend itself to investment in long term innovation. On the other hand, manufacturers focus on products rather than process, which opens up for a longer term view of research and development.
It is not unusual to see new thinking and originality from construction manufacturers. The issue becomes a matter of how we get this innovation into our buildings and specified by our designers. There is a common pattern with designers reluctant to move away from their tried and tested specification, which can limit fresh thinking.
How, then, are construction product manufacturers affected by the increase in the use of building information modelling?
The construction industry has been slow to embrace technology and has tended to lag behind many other industries. However, while construction manufacturing operates within the construction sector, it is more aligned to the manufacturing industry. This means that the majority of manufacturers are already using some sort of BIM system without knowing it.
To manufacture all components and to interface with computerised machinery, products have to be developed in a digital format. Manufacturers use a wide range of software, which is often aligned to the machining process such as Autodesk Inventor. This information is produced for manufacture but can just as easily be used for design if the data within it is matched to a standard protocol.
Designers need access to this information but not all the detail. They need the geometry and some performance data but not everything. If the manufacturer can provide this information easily to the for its three-dimensional and designer the detail can be includ- geometric characteristics, its true ed in the model early, preventing value is in the joining up of inforerrors later in the workflow. mation. BIM is not about turning
Digital components can also a 2D design process into a 3D include intelligence to give the environment but about the comdesigner options and help avoid errors. For example, when speciRob Charlton plete re-thinking of how buildings are designed, procured, fying a radiator in a model, the assembled and operated. designer can only select the radi- CEO With a new workflow, the conator sizes available from that Space Architecture struction industry can develop manufacturer and if a particular one of the most sophisticated supfixing approach is required for a certain ply chains across any industry. product — such as additional feet — they All buildings are, in effect, made up of can automatically be added. components. These components are brought
In many other industries there have been together on site to produce a building. experts in the development of supply chains Access to this information digitally during and the benefits have been obvious to see. the design and prototype stage will allow
Henry Ford pioneered a supply chain that designs to be tested virtually and errors allowed him to continually improve the ironed out on a computer rather than on site. automobile. In construction our workflow is A product’s performance can be included within the digital component to allow it to be interrogated throughout its ‘‘ The industry has the opportunity life cycle. While this provides a potential opportunity for the manufacturer to market its products and ensure to have a standardised range of that they are specified earlier and components that can be managed accurately to truly maximise the benefit, the entire approach to delivering into individual supply chains buildings needs to be reconsidered. ’’ We need the construction products industry to help improve the quality, cost and performance of our buildnot set up in a way to allow this type of inte- ings. The industry is standardising its gration. Our designers are disjointed from approach to content creation and is working the contractor. The main contractor does hard to develop industry-wide protocols. have a supply chain of sorts, but this is rare- This will provide huge potential in allowing ly in digital format. The designer may have information to be interchangeable throughspecified a product and co-ordinated it into out the project lifecycle. the model; but it could be removed at a later Designers need to take control of specifidate because the main contractor has decid- cation again, and select and test each comed to use its own supply chain. ponent. The designers must be the custodiIn the majority of cases the reason for an of the overall building performance. change is cost. This can overlook other selec- The industry has the opportunity to tion criteria such as size or performance. have a standardised range of components The main contractor’s supply chain will that can be managed into individual suprefer to subcontractors, which in effect is ply chains. These supply chains of prodlabour-related rather than specifically in ucts will allow the ongoing specification of relation to components. These supply chains products, and the ongoing monitoring of do not innovate and are selected on service performance to enable continuous and price. They are generally unsophisticat- improvement and investment in research ed and do not invest in research and devel- and development. opment or shared learning as a rule. Manufacturers need to embrace this What does all of this have to do with the opportunity and offer components in digital use of Building Information Modelling? format to let early adopters of BIM maximise While BIM is currently best understood the potential of re-thinking our industry.
Executive guide to BIM: part 2
The second installment of this two-part guide goes into greater detail on Building Information Modelling (BIM) workflows, when a model progresses from concept to construction and facilities management. We cover the benefits and implications of adopting BIM, including changes to teams and workflows.
by Paul Woddy, White Frog
Having looked at levels of Building Information Modelling (BIM) and dimensions of information in the first part of this guide, the third factor to consider is the level of detail or level of development (LOD) contained within the model. Both terms mean the same thing and aim to clarify the expectation in terms of information granularity. These LODs are often linked to time and stage of work with a model progressing from concept through to construction and facilities management (FM).
There are two strains that have developed independently, either side of the Atlantic but have matured into near alignment. Table 1 (top page 23) compares and contrasts the two.
In table 2 (bottom page 23) the two standards diverge slightly as the purpose of the LOD is interpreted differently with the AEC terminology looking to differentiate between the geometric simplicity that is acceptable for general draughting purposes versus the complexity required to produce quality rendered images.
The majority of design work is carried out in the first three LODs where the terminology is interchangeable.
This terminology is important because it may have a major impact on the quoted price of a job and a detailed scope should go much deeper in specifying what scale and at what stage certain elements will be defined and in what dimension.
The following practical example may
The buildingSMART MacLeamy Curve promotes a workflow where the decision making process is moved further forward and lowers the cost of refining design
Part one
In part one we asked: what is BIM and is it relevant to me? We covered common terminology and principles and provided information on how and where to buy BIM software. To view this guide see AEC Magazine May / June 2013 or tinyurl.com/BIMexec1
help to clarify: For the next delivery deadline, all pipes above ##Ø will be modelled in 3D. Pipes between ##Ø and ##Ø will be shown schematically in 2D. Connections below ##Ø will not be shown.
A succession of these types of statement will clarify, without ambiguity, the extent to which the model is expected to deliver on clash detection and to what extent the final fixtures are connected by the skilled fitter on site.
Only the first part of this scope is BIM with the second part being a CAD workflow and the third being blind luck.
This is not an uncommon scenario where BIM methodology is delivered to a defined point but no further. Where traditional, manual construction methods are ultimately to be used, the advantages gained from the BIM, versus the cost of creating the model do tail off as we approach higher levels of detail.
The counter argument is that this does lead us towards a process which is open to human error. Implications of adopting BIM The buildingSMART MacLeamy Curve (pictured page 22) promotes a workflow whereby the decision making process is moved further forward and hence lowers the cost of refining design.
BIM methodology can assist in this effort by improving collaborative communication and by drawing closer parallels between the virtual concept and the built reality, thereby highlighting clashes and construction issues.
This desire to improve can also lead into one of the most common BIM adoption pitfalls, potentially causing undue financial expense and leading to BIM software and protocols becoming unpopular among staff.
It is an incorrect assumption that in developing a design using BIM methods, all design decisions have to be made at a far earlier stage of the job than is preferable or would previously have occurred.
While the buildingSMART MacLeamy Curve diagram shows us that this can be beneficial to the overall project, it is inappropriate during the tender stage for instance, when work is carried out speculatively and with minimal effort.
It is often a symptom of the self-taught user that undue consideration of the components is applied prematurely whereas BIM software is just as capable
AEC(UK)BIM Protocols
LOD 0
LOD 1
LOD 2
AIA BIM Standard (US)
Level of development (LOD) contained within the BIM model
Description
LOD 100
LOD 200
LOD 300
A conceptual massing study where shapes and forms are explored against the client brief and design intent. At this stage, floor areas and volumes can be extracted from the 3D model and departmental flow can be rationalised
The basic form is developed using categorised components such as walls, floors, columns and equipment. These elements are generic place-holders in terms of their associated meta-data but also appearance, often with all objects made from one common material, hence the application of the term ‘White Model’
As design decisions are made, the generic place-holders are replaced with precise, manufacturer-specific objects, rich in associated information but still simple in their 3D geometry
AEC(UK)BIM Protocols
AIA BIM Standard (US)
LOD 3 N/A
Description
Simplified geometric form is adequate for most BIM tasks but when aesthetic images and rendered scenes are required, it is necessary to replace elements with more accurate objects
LOD 4 LOD 400
Objects are either swapped or additional information is appended to include fabrication and assembly information. This does not always mean that the objects get more geometrically accurate, but that information is added which is relevant to the construction process
LOD 5 LOD 500 The model is updated to reflect the As-Built nature of
the finished building of being vague and conceptual as CAD or the pencil are.
Very closely linked to this topic is the problem of over-modelling, which is not uniquely a BIM problem but is just as prevalent among CAD users. Just because software allows us to draw or model a component with accurate anatomical geometry, does not mean that it is the right thing to do.
The worst protagonists of this have and remain to be product manufacturers who provide their electronic libraries, complete with seals, washers, grommets, bolt-threads and fan-blades.
The user often does not have the time to clean and rationalise these elements and the result is too much graphical
Reference
AEC(UK) BIM standard
A working set of protocols and best practice for SMEs. Free of charge and targeted at users of specific software applications in order to use recognised terminology rather than generic vocabulary. A Revit version and Bentley version are available, with other versions in production alongside generic documents such as BIM Execution Plan Pro Forma.
BS1192:2007
A UK standard that establishes the methodology for managing production, distribution and quality of construction information, including CAD data, using a disciplined process for collaboration and a specified naming policy. Some of the techniques and protocols are dated and a review is underway.
COBie
Construction Operations Building Information Exchange is a subset of IFC (see below), designed as an exchange format for the handover of a construction project upon completion and is a large spreadsheet. It does not need a 3D model to create it but tools can automatically transfer BIM data into the COBie format.
CI/SfB
The favoured system for many architects, this element classification schema is no longer maintained and is superseded by Uniclass.
Uniclass
Developed by the Construction Industry Project Information Committee (CPIC) representing RIBA, RICS, CIBSE and others, this system replaces the CI/SfB classification and is due for a new release.
Industry Foundation Class (IFC)
A means of passing information from one BIM software platform to another. The difficulty is in the way that compliance is applied: imagine a list of one hundred bullet points and in order to comply, you must hit forty of those points. It is possible for two applications to be IFC compliant and yet completely miss each other. Future releases should tighten up the gaps.
OmniClass
A classification system for the US construction industry with a growing number of global users. The tables are made up of various other naming and numbering systems and the table for designed elements comes from UniFormat.
UniFormat
The dominant system in North America and those parts of the world where the US has influence, such as the Middle East.
AIA BIM Protocols E202
Focuses on the processes surrounding BIM use and collaboration between the various stakeholders rather than the internal standardisation of BIM software use. It is very similar to the BIM Execution Plan mentioned in the AEC (UK) documentation set and the Penn State version as well. information going into a drawing or model.
BIM should be the technology that removes this problem but it is also the technology that accentuates it. It has the potential to eliminate it because associated metadata can provide specifics on a chosen element without the need for graphical recognition — rather than model the hinges of a door, the properties of a simple generic component can advise that Furniture set A is applied as per specification, for example.
Unfortunately, bad practice and overenthusiastic users tend to get carried away, enjoying the ability to recreate a component as a virtual work-of-art. This is repeatedly evident by reviewing the copious online repositories for BIM content where proud modellers are willing to share their creations in return for plaudits and followers.
The problem is that such extremes are not scalable, nor do they necessarily add to the delivery or the value of the finished product. Standards and protocols Various international standards will be bandied around and may be referred to on different projects. A brief explanation is provided on the most relevant of those (box out, left).
All of the standards mentioned, left, are industry-wide protocols with many more coming up for consideration in each of the different disciplines, such as transfer protocols specific to environmental assessment of buildings and structural analysis of structures.
There are too many to list in this exploratory article but further information is available in this series of training modules. Team and workflow changes There are many areas of working practice that are touched by the BIM ethos if properly embraced.
That is not to say that complete turmoil will ensue on the first day of use, and BIM methodology can be eased into a practice and allowed to prove its merits before spreading its wings, but in order to take full advantage, old processes and workflows may need to be re-assessed.
A few such examples are highlighted here.
In the traditional drawing office, a pyramidal structure would see a lead designer at the pinnacle and a tier of tracers at the base with various grades in between. Often the lead designers would have a hands-off approach to drawing production work.
BIM encourages, and in many cases insists that operators understand what is being modelled because the elements are not arbitrary lines to which meaning is assigned by a skilled overseer; they are intelligent objects with properties and inherent characteristics specific to the category of component.
As such the more building-savvy the user — the more efficient they are at modelling and manipulating information in a BIM environment.
Particular skills will naturally emerge and talents for specific tasks will surface among the users. Some will take to content creation while others will gravitate towards schedules, detailing or model management.
Over time the team will settle into a new, more horizontal structure as these skills develop.
Another area that can lead to frustration in the office is the timeline for producing deliverables. Again looking at a traditional environment, a twelve week programme with a requirement for 200 drawings should see somewhere in the region of 150 drawings at or near completion by the nine week stage. Management and the client can see the progress and gauge whether deadlines will be met.
In a BIM scenario however an inexperienced team may not have a single drawing prepared by the same milestone, but they have a fantastic model filled with metadata and resplendent with fabulous views which are compiled at the eleventh hour to deliver the job. This can only lead to stress that can easily be avoided.
Most BIM tools allow the drawing sheets to be created, named and views allocated, even if those views are largely empty or under development.
As the model progresses, so do the drawing sheets, so the boss can see what is going on. Fees and deliverables It is imperative that the implications of BIM are considered when preparing fee proposals and agreeing terms with clients and contractors. By this we do not imply that it is more expensive to deliver a project when BIM methodology is utilised, nor is it as simple as saying that the reverse is true.
Often the increase in efficiency and hence the reduction in time and costs of preparing deliverables is offset by the
increase in expectation and potential market which will come under intense influencing proposals without signifiadditional services, which may be naive- scrutiny in the future. cant cost implications. ly promised for no additional fee. Those BIM is not about a single piece of As far as the insurance industry is conseeking work and agreeing terms at the software, nor even a specific type of soft- cerned, BIM adoption has made them top of a company need a good under- ware, but a means of interacting with nervous to say the least. The current constanding of the various costs and efforts data from many perspectives and objec- sensus seems to be that BIM is a free-forinvolved in preparing a particular set of tives, and hence the exchange formats are all and that the only way to protect themdata by those at the coal-face. ultimately more important than the soft- selves is to ring-fence BIM activity and
This is nothing new, but the upheaval ware used in any one part of the building effectively treat it as a means to an end in of new technology and the clamour for life-cycle. the production of drawings, with the available work has seen a few companies Formats such as IFC are hopefully sharing of models prohibited. over-promise and strip out all profits going to step in and fill the gaps that cur- This is due in no small part to the lack from a job. rently exist and allow stakeholders to of common standards and mandated pro-
There are new roles emerging within pass information freely around the tocols by which they can gauge the capathe industry that will need to be filled, design, construction and maintenance bility of a company or the requirements and hence opportunities to offer new ser- teams without large amounts being lost of a project, and hence assess the inhervices and grow additional revenue along the way. ent risks. It is something that the whole streams. Someone within a project team industry has to work to overcome and as will need to take on BIM leadership and Contract and insurance standards are defined and gain accepco-ordination. Do you want that role and Much has to change in order to allow tance in the future, we will see the emerthe associated fee and responsibility? BIM methodology to reach full potential gence of professional accreditation and
Who owns the qualifications which model? This is can then be mandated always an interesting question because unless it If you only take one ‘‘ statement from this guide, let it by underwriters and sought as a mark of quality. is stated in the be that the most important part of BIM is the ‘I’ in contract documentation, the the middle. Information is king. In the BIM The final word BIM is a mind-set, not BIM data is sim- methodology, data is collated, modelled, manipulated a software applicaply a means to an and managed, but always with an understanding of tion, and adopting end in preparing the drawings that the object to which the data relates BIM methods can require an overhaul of you are obliged to deliver. If the client or contractor ’’ the design process, team structure and even business practhen asks the architect for a copy of the and for the entire industry to properly tices in order to achieve the full potential model for clash detection, review or even embrace the new way of working and col- of the technology. FM, should he expect to get it for free? laborating. This is not going to happen overnight,
Many would argue that if I paid for Various initiatives aimed at proving as much because the industry will your time in preparing the information, the effectiveness of IPD contracts need to adapt as it is because of the then I can expect to have it in the original (Integrated Project Delivery) or similar internal upheaval and cost, but the format that it was prepared in. are both available and underway and potentials are an exciting area of develWhichever side of the fence you sit on, it these new contract documents should opment with new revenue streams, addiis much better all round if this is clarified ease the adoption of BIM by eliminating tional services, increased efficiency and at a contractual level and not fought over some of the risks surrounding litigation, a wider involvement in the whole buildat the back end. but this mitigation of risk is not the only ing lifecycle.
Protecting embedded intellectual prop- contract-related change that we will It is not so new as to be an untested erty is a topic that logically leads on from probably see in the near future. technology, but it is new enough not to be the model ownership. One example of an area that will have able to see the ultimate potential yet.
If a lot of time is spent developing a to change radically if we are ever to rea- ■ whitefrog.co data-rich and efficient library of compo- lise the collaborative advantages of worknents, and a model containing such ele- ing in a fully co-ordinated 3D model is ments can easily be mined for elements, the terms of contract for building servic- White Frogs seen in Asia this will inevitably lead to these elements es consultants and designers. falling into the hands of competitors and Recent years have seen a steady decline The White Frog team office in India. In has opened addition to an there is very little you can do about that. in their involvement, often to nothing providing products and services to This should not be used as a reason not more than schematic design and plant- the Asian market, the New Delhi to build libraries but should be consid- room layout. office will be adding to its range of ered when defining the specification of such efforts. Even this small amount has been done at a relatively advanced stage of the electronic books and training materials interactive for BIM.
Data format is also an aspect of the design process, leaving little room for