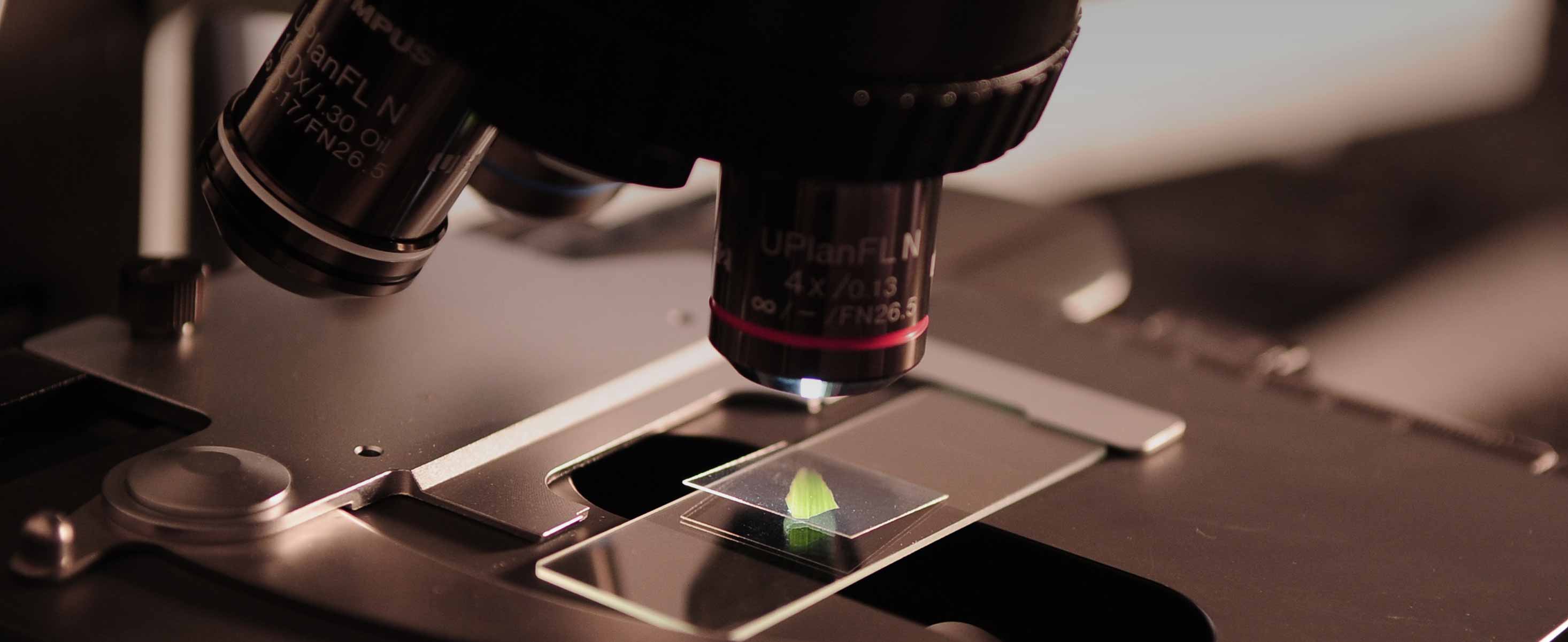
5 minute read
Servo versus closed-loop stepper motion controls
Servo motors and stepper motors both include rotors withpermanent magnets and stators withcoiled windings … so application ofvoltage to those windings prompts rotorrotation. But this is where constructionsimilarities between these motors end.
Stepper motors have 50 to 100 poles and common hybrid iterations are two-phase (bipolar) and four-phase (unipolar). In contrast, many common motors run under servo control have four to 12 poles and are three-phase units.
What’s more, drives commonly paired with stepper motors generate sine waves with constant amplitude and varied frequency to change motor speed — or drive the motor with pulse-width modulation (PWM). In contrast, servo-motor drives produce sine waves with variable frequency and amplitude for full control over speed and torque.
Regarding controls, traditional stepper motors move upon reception of some command to advance some pulses correlating to a distance but are openloop, so lack feedback to verify whether the target is reached. Servo motors also move on receipt of a controller command signal — but under closed-loop control with encoders tracking motion to inform motioncontroller corrections until target position or actuation is reached.
So with traditional stepper designs, inadequate motor torque for overcoming a load will cause skipped steps or stalling even while receiving current from the drive — for a discrepancy between commanded and actual position. One solution is to oversize the stepper motor to ensure sufficient margin between highest expected torque required (to move the load) and available motor torque. Another solution is to add an encoder for closedloop stepper operation.
Some closed-loop stepper systems include controls that compare expected position (based on the steps the motor should have taken) with actual position reached as reported by encoder feedback. Any difference between the two prompts corrective moves. Slightly more sophisticated closed-loop stepper systems continuously monitor any discrepancy between position steps and encoder feedback — and then command real-time corrections in the form of changes to drive pulse rate, current, or step angle.
Still more sophisticated closed-loop stepper systems use drives that deliver sinusoidal commutation. When rotor and stator magnetic fields are improperly aligned, digital signal processors (DSPs) leveraging encoder feedback command changes to the current into the motor — to prompt torque that’s sufficient for moving or holding the axis load. Because the controls use feedback to control torque with motorcurrent changes, this stepper control mode is sometimes called servo control. Basically, the stepper motor functions as a highpole-count servo motor — sans the noise of traditional stepper-motor operation and with smooth and precise motion. Dynamic rather than constant current input minimizes motor-heating issues … and these closedloop stepper designs also exhibit less velocity ripple than open-loop vaeriations. Read Open-loop versus closed-loop stepmotor systems at motioncontroltips.com for more on the latter.
CHOOSING BETWEEN CLOSED- LOOP STEPPERS AND SERVOS
Stepper motors under closed-loop control are a small but growing percentage of stepper applications — increasingly common where load on an axis may vary and even in machine designs involving advanced multi-axis coordination.
Where appropriate for the application, it’s not uncommon for closed-loop stepper systems to be 25% less expensive than comparable servo motor solutions … and with common NEMA dimensions for simple integration. Closed-loop stepper motors are typically most suitable for applications in which:
• Position loss is unacceptable
• The axis needs high torque at relatively low rpm
• The design has a simple architecture or particularly tight cost constraints
In these situations, closed-loop stepper systems excel with relatively high torque output — for acceleration and top speed that can be twice as fast as that from comparable open-loop arrangements. Such capabilities can be useful in machines that must quickly index or pick workpieces for sufficient throughput.
But where are closed-loop stepper motors unsuitable — and true servo motors a better solution? Well, consider the speedtorque curves of these motors. Steppers typically generate higher continuous torque at low rpm than comparable servo motors. Servo motors on the other hand can output exceptionally high intermittent peak torques at low rpm — as well as peak and continuous torques over wider ranges of rpm. Here are some questions to ask about these and other parameters:
What are the speed requirements? Typical steppers excel on axes that run slower than about 800 rpm. Above that, core losses and the effect of time constants cause stepper-motor torque to wane. (For more information on this, search Why is the electrical time constant important for stepper motors? on motioncontroltips.com.) Torqueproducing current through a stepper motor has a certain rise time, and a given voltage may only get limited speed increase. But in many cases from about 30 rpm to stall or when holding loads, step motors output more torque than servo motors of comparable size.
Of course, servo motor torque doesn’t fall off until several thousand rpm. That helps servo motors excel where repeatability and resolution requirements are especially stringent … to outperform certain closed-loop stepper systems on high-speed axes, machine designs needing high torque at high speed, and (as we’ll detail) systems that handle dramatically variable loads. One footnote: Servo motors are known for their ability to run at high speeds, but certain specialty controllers allow some motors (especially those with direct-drive construction) to work at speeds down to one revolution per second.
Note that some axes to run between about 800 and 2,700 rpm or so may be able to use either motor technology. Here, continuous and peak torque requirements often indicate which may be more suitable.
What are the torque requirements? Servo motor systems output high torque on demand, even over wide speed ranges. So servo motors may be more suitable where closed-loop stepper designs are incapable of peaking torque enough to get sufficiently quick acceleration … or on particularly dynamic axes. Plus servo motors come in wider torque ranges than most comparable stepper-motor options … and some servo drives today even include software to simplify or automatically execute system tuning and compensation tasks.
That said, many of today’s stepper motors have power ratings surpassing those of legacy variations thanks to advances in construction featuring stronger magnets and smaller airgaps. High torque lets stepper systems deliver accurate and stiff low-speed motion sans gearing. Larger rotors on otherwise equivalent geometries and frame sizes also make for more torque density. One caveat is that rotor inertia affects acceleration … though some stepper designs can see 20:1 rotor-to-load inertia ratios ... and more modest acceleration requirements, advanced closed-loop controls, and microstepping allow ratios to 100:1 or greater.
What is the required accuracy? Some manufacturers differentiate applications suitable for closed-loop steppers from those requiring full servo motor control with measures of rigidity requirements. A linearmotion axis with cantilevered (overhung) load or employing a belt drive is likely to accept closed-loop stepper operation. An axis that employs bearings, linear slides, and a ballscrew for maximum stiffness and minimal deflection may be one particularly reliant on rigidity for accuracy to machine, scan, or assemble delicate workpieces … and one requiring a servo motor.
Does the axis require a lot of position holding? Closed-loop stepper motors excel on point-to-point positioning and on axes that must hold in place. That’s because a stepper motor at rest can hold load absolutely still, with none of the hunting some servo-motor systems exhibit. Where efficiency is a key concern, sometimes axes are even setup to use stepper-motor detent torque to hold loads sans power input.
Will the axis see a lot of disturbances and load variability? Servo motors tend to be most suitable where high throughput or bandwidth for disturbance correction are top design objectives. Such responsiveness depends in part on the system’s inertial arrangement. Many stepper motors require a load-to-motor inertia ratio below 30:1. (Read Why use a gearbox with a stepper motor? at motioncontroltips.com for more on stepper-motor inertia.) Traditional geared servo motors often have loadto-motor inertia ratios below 10:1 for sufficient responsiveness and acceleration capabilities. But advanced servo systems with high-resolution encoder feedback and stiffness (with no sources of lost motion) allow higher ratios for top efficiency as well as responsiveness.
Visit motioncontroltips.com/ stepper-motor-servomotor for more on this topic.
What resolution does the axis require? We cover the relationship between stepper-motor mode and resolution at the motioncontroltips.com stepper-motor library. One rule of thumb is that when a design needs positioning resolution better than a couple hundred steps per revolution, stepper motor systems (especially five-phase variations and those that microstep) can work if employed with encoders — which have resolutions to a thousand steps per revolution or better. In contrast, servo motor resolution is (at least in theory) infinite … though encoder resolution is a factor. Of course, encoders 28-bit and beyond allow millions of counts per motor revolution.
Might direct-drive servo motors be suitable? Further blurring the lines between motor-construction types are direct-drive servo motors with high pole counts that work without gearing or intermediate mechanical components. These are suitable for axes (often with high inertia) needing slower operation — generally though not always below about 1,200 rpm. Systems with these motors can see 300:1 and higher rotor-to-load inertia ratios for maximum responsiveness and performance … with high-resolution feedback as well as system stiffness maintained by specialty materials in the drivetrain, upsized bearings, and (in the case of frameless direct-drive servo motors) integration right into the machine frame.