
1 minute read
The Robot Report
Results
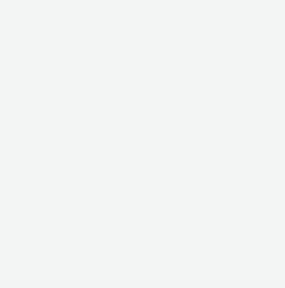
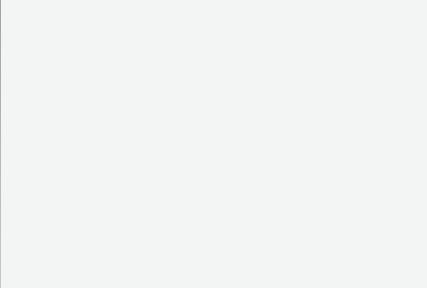
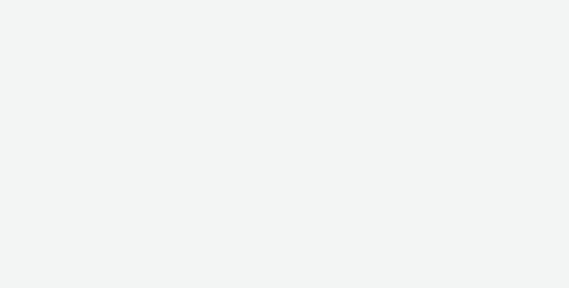
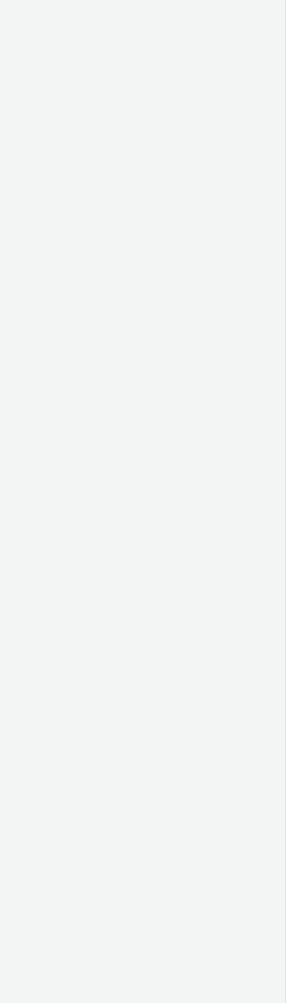
The employees at FMO Surface were enthusiastic about the new colleague right away.
“Thanks to the safety features, collaboration with people in a single workspace is possible,” said KUKA sales engineer Robert Korte.
In the past, this type of quality control for DMCs was much more time-consuming. “When checking for completeness, we had to scan each part individually,” said Hertz. For this, an employee had to take the components out of the tray and subsequently put them back again. Today, with the LBR iisy, this task is performed much faster and more precisely.
FMO said the LBR iisy cobot could also provide valuable services in pad printing in the near future. Furthermore, the company hopes to make use of the larger versions of the LBR iisy with their payload capacities of 11 and 15 kilograms.
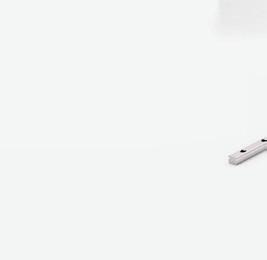
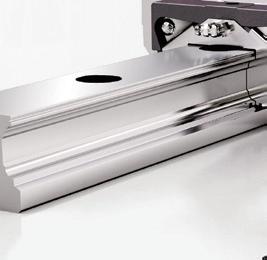

FMO Surface has also collaborated with KUKA on using a KR CYBERTECH nano (KR 10 R1420) robot arm for palletizing and to tend a laser system. Two years later, FMO Surface added another industrial robot om the KR CYBERTECH series to turn over, measure and laser plastic parts to be finished.
“Particularly in view of the shortage of skilled workers, automation plays an important role for a medium-sized company like ours,” said FMO Surface. RR
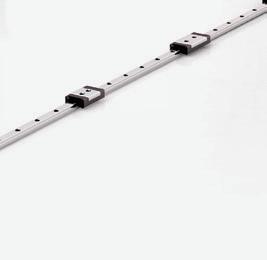
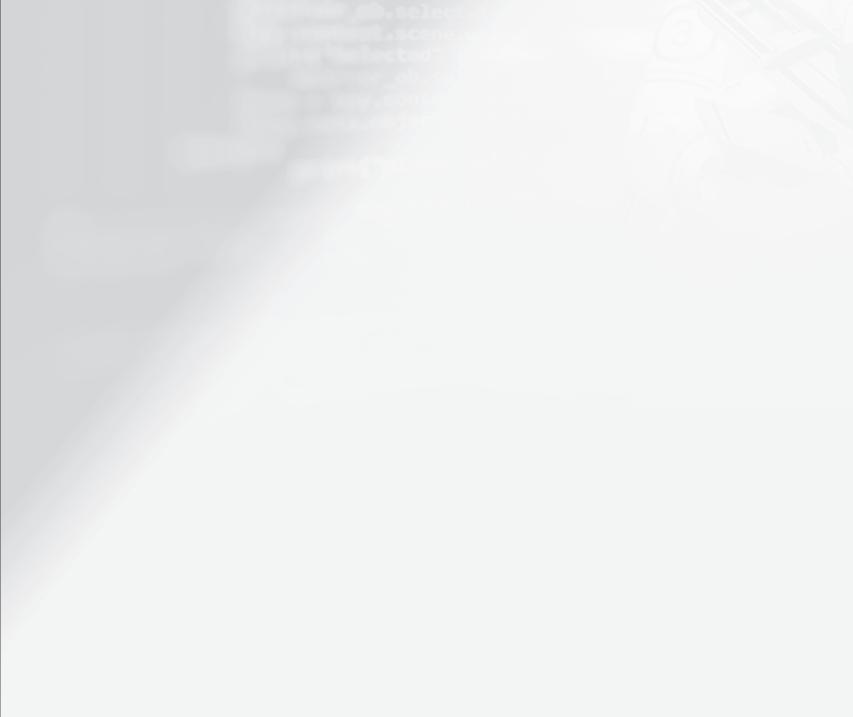

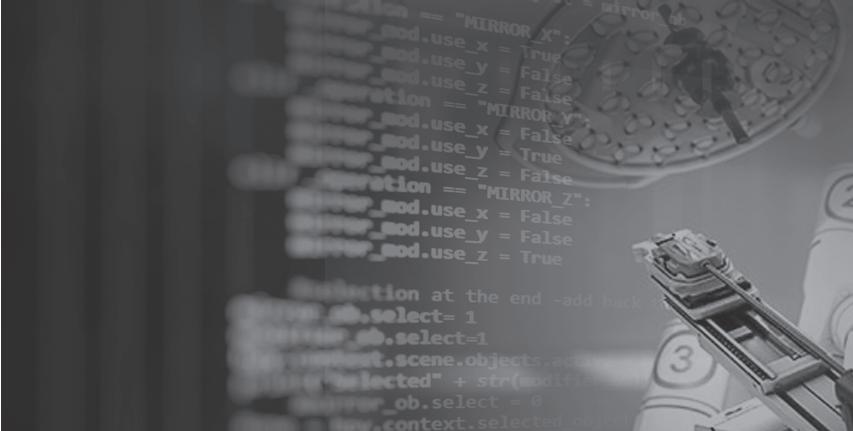