
2 minute read
Automation upgrades keep cheese manufacturer sharp
Edited by Mike Santora • Managing Editor
When Pacific Cheese Company realized its highly manual legacy systems were constraining throughput and making product changeovers more timeconsuming, they knew it was time for upgrades. In other cases, installing new and improved equipment on the production line — or adding additional production lines — meant that upstream and downstream systems needed upgrades to fully take advantage of potential production gains.
By standardizing on a proven and easy-to-use automation vendor, their team was able to perform all of these upgrades smoothly and cost-e ectively. Furthermore, improved technology has enabled them to deliver a superior operator experience and to add better sanitation and automatic operation capabilities, along with diagnostics to help keep production running at capacity.
Big cheese, small controls
Pacific Cheese converts and packages cheese for major retailers and foodservice customers. Most of the products are blocks and pouches of various sizes, each with specific demands for processing and labeling. Retail products might range in size from eight ounces to two pounds, while food service options could be five or operates various automated equipment to convert and package cheese in many di erent sizes and styles for major retailers and foodservice customers. Maximum uptime and flexibility are a key to success. even ten pounds. Various equipment is necessary to perform this work (Figure 1).
Although the original production lines did use a programmable logic controller (PLC) associated with a motor control center (MCC), there was also some hardwired relay logic, and the company didn’t have the software or capability to access the legacy PLC. There was no HMI to provide status and control options, and operators needed to perform many tasks manually.
The existing system frequently stopped running unexpectedly and without any alarm function, required maintenance personnel to delve into potential causes. Belt speed changes and timing adjustments, necessary for changing product sizes, also needed to be performed by maintenance personnel, often using a variable frequency drive (VFD) potentiometer. In any case, because cutting functions were mostly manual, the packaging equipment could only run as fast as these operations could proceed.
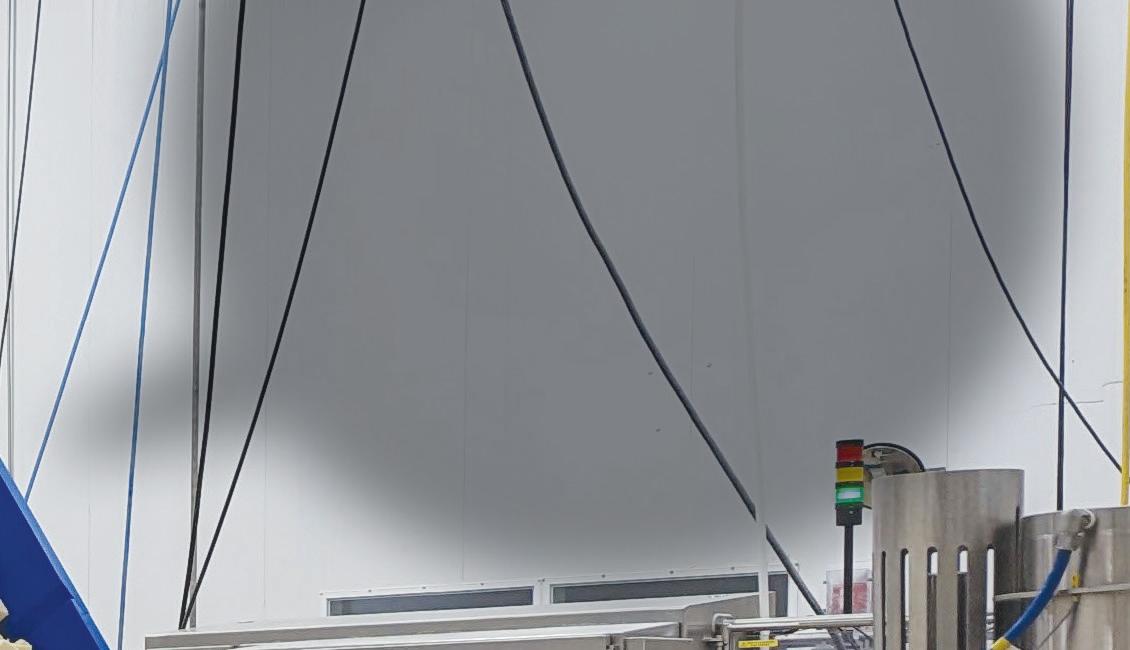
For better flexibility and performance, some changes were needed. A new high-speed cutter and flow-wrapper were part of the solution. Also, a third production line for handling larger pouches was added, which was associated conveyor belts, mixing drums, a shredder, and other equipment to be synchronized. It was clear that the new throughput and production capabilities simply could not be well served by the old controls.
Serving up new automation
Sanitation is an important aspect because Pacific Cheese typically runs two consecutive production shifts and then a third sanitation shift. The new design would need to minimize downtime because production capacity was already fully sold out.

Their team initially gained experience with AutomationDirect products at one site for a single project, with excellent results.

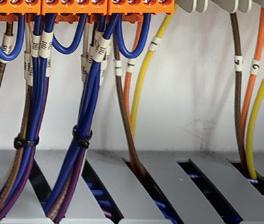
Pacific Cheese has generally standardized on the Productivity1000 stackable micro PLC, which provides all of the control, data storage, I/O, and communications capabilities they need in a compact form factor, which retrofitted easily into available cabinets (Figure 2).
Combined with a C-more HMI, it can now provide a new level of functionality in its plant. Many times, the company was able to repurpose the existing MCC and integrate it with the new controls, resulting in significant savings during installation and commissioning.
Automation upgrade yields many benefits
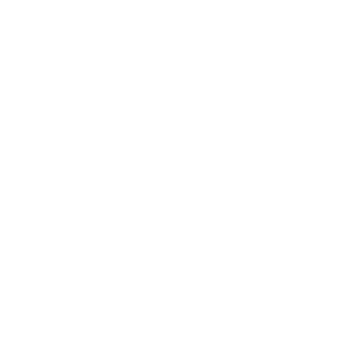


The baseline for the new automation upgrade was to supersede existing functionality, but the team went far beyond this initial goal. For the production lines mentioned earlier, one PLC was used to control and orchestrate all three production lines. Normally, the lines run completely in automatic. However, if a line is stopped, operators can now manually command equipment using the HMI to stage a line for operation (Figure 3). There are clear HMI messages such as “Waiting for Scale” and “Scale Override.”The amps consumed by the shredder are displayed so operators can monitor and fine-tune operation, and some equipment uses the amp readings so the PLC can feed the proper amount of ingredients in a controlled manner.

A new sanitation mode runs the line slowly for 90 minutes with an extendable countdown timer, giving the crew good access to the equipment
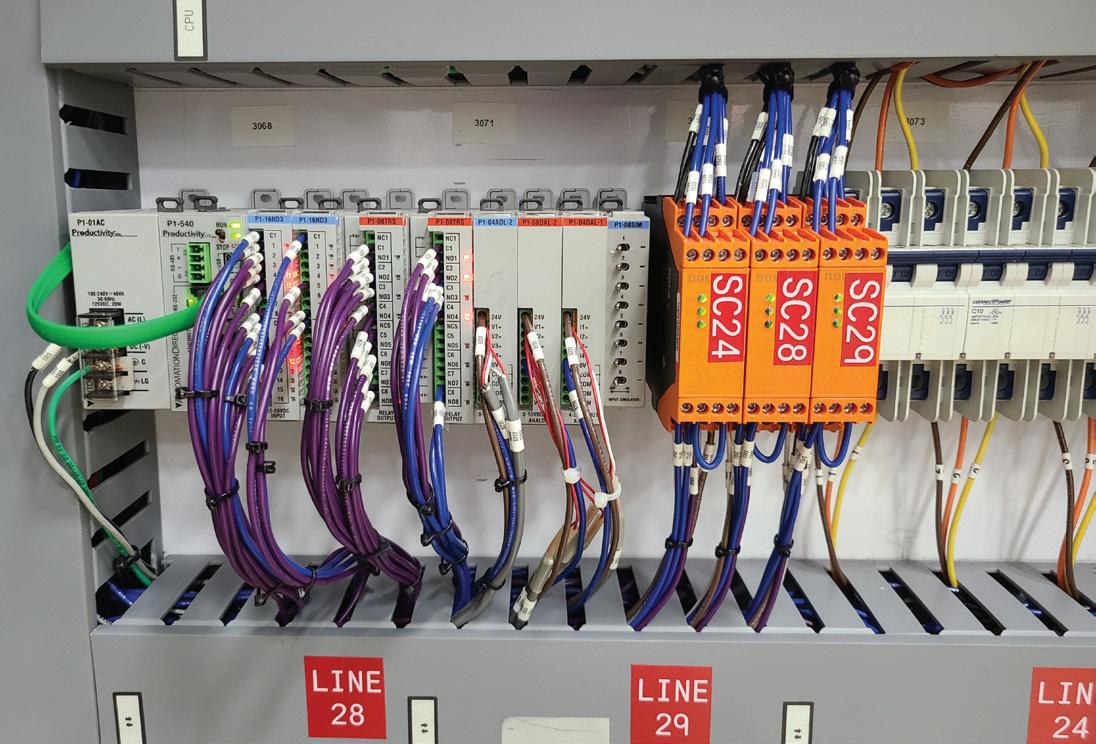