2 minute read
SPOTLIGHT ON
Next Article
Transport, Rotate & Install of Vessel An example of good practice
In late 2019, Universal Cranes was contracted to transport and install a 37m long, 122T vessel during a scheduled shutdown. The lift was highly complex due to the surrounding buildings, accessibility to the install site, and size and weight distribution of the vessel. Extensive plans and lift studies were carried out to ensure this was a successful and safe lift. This project provides an excellent example of how to appropriately assess and account for a load with an offset Centre of Gravity.
Planning
The Universal Cranes engineering team determined that a Manitowoc M16000 (400T crawler crane) would be the main lift crane with assistance from a Grove GMK7450 (450T all-terrain crane) as the tailing crane. The vessel arrived at the site and was unloaded two weeks prior, to begin the fit-out for the main installation lift during the scheduled shutdown.
Specialised Rigging
As per the lift plan, specialised rigging equipment was designed and used for this project, including an assortment of soft slings, bow shackles and link plates combined with a 36.4m long lattice boom spreader bar. In addition, the rigging included a 110T capacity hydraulic cylinder, with a 1500mm stroke for fine adjustments. This allowed the vessel to be picked up level during unloading, as the vessel’s centre of gravity was 2.5m off-set from the centre of the lift points, making the lift unbalanced.
The Lift
The vessel itself was large, awkwardly shaped and required installation into a location with restricted access. Step 1 of the operation involved the vessel being loaded onto a transport platform and relocated to the final lift site.
Once the vessel was in position, Step 2 involved using the 400T crawler crane rigged with a lattice spreader bar and a hydraulic cylinder. The vessel was raised horizontally for nominal clearance and rotated 180 degrees in preparation of the final lift. Step 3 then involved a 450T all terrain crane used as the tailing crane to assist the 400T crawler crane to delicately tail the vessel. Extreme care was taken during this part of the process as the lift was being operated within a restricted and tight area. The load stability was constantly monitored to ensure a safe and stable lift. Lastly, at Step 4 once the vessel was successfully tailed, it was placed into its final location with the 400T crawler crane for installation.
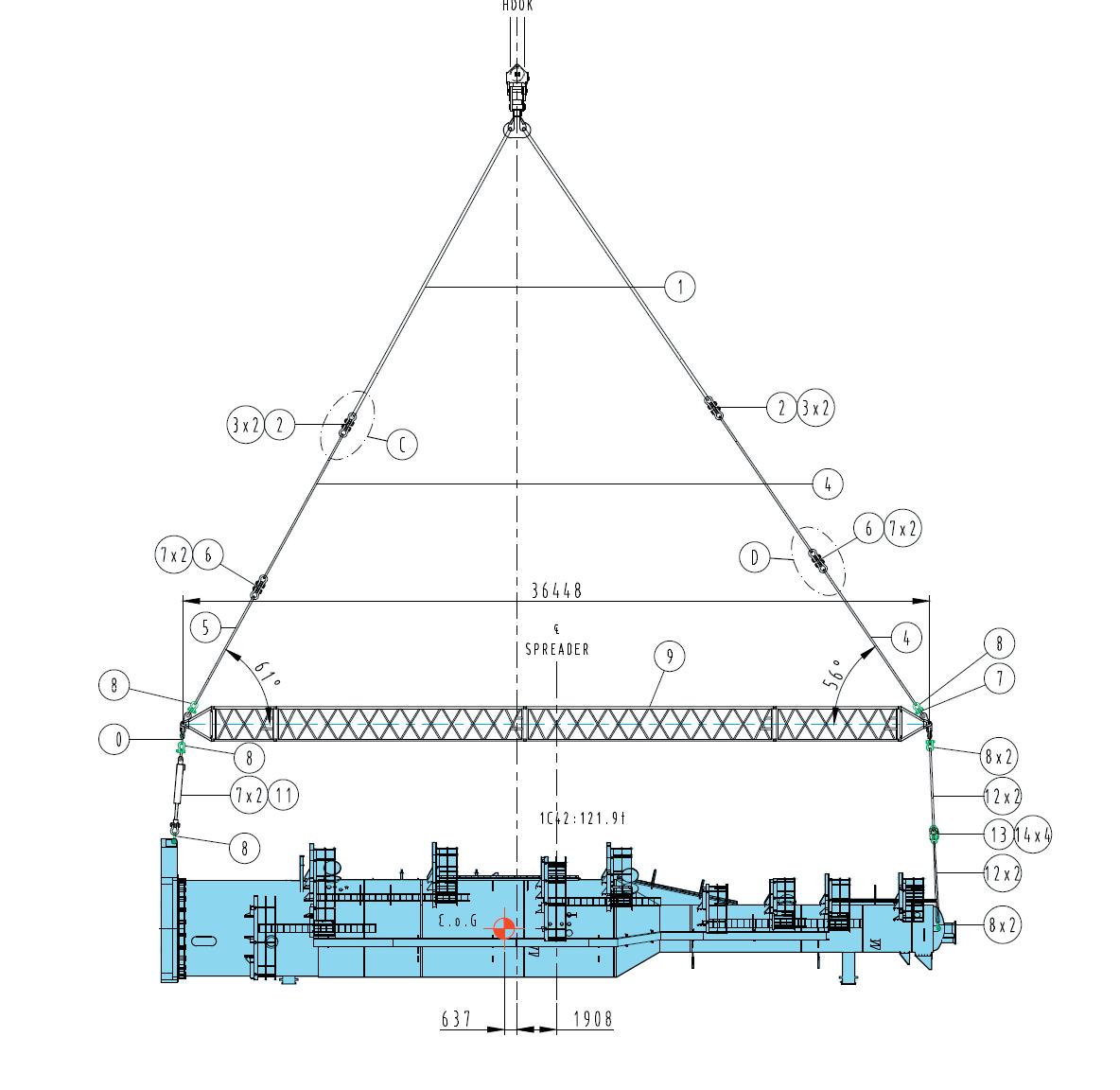
Planning Makes Perfect
With a large and complex lift such as this, the extensive planning and lift studies that were carried out were an essential piece of the puzzle in the safety and success of the job. By utilising a team of heavy lift experts, engineering programs and intricate calculations to understand and account for the load’s centre of gravity throughout the lift, rotation and tailing, Universal Cranes was well prepared for the job. Overall, the lift was a success and the vessel was installed in the planned timeframe and incident free achieving a great outcome for the client.
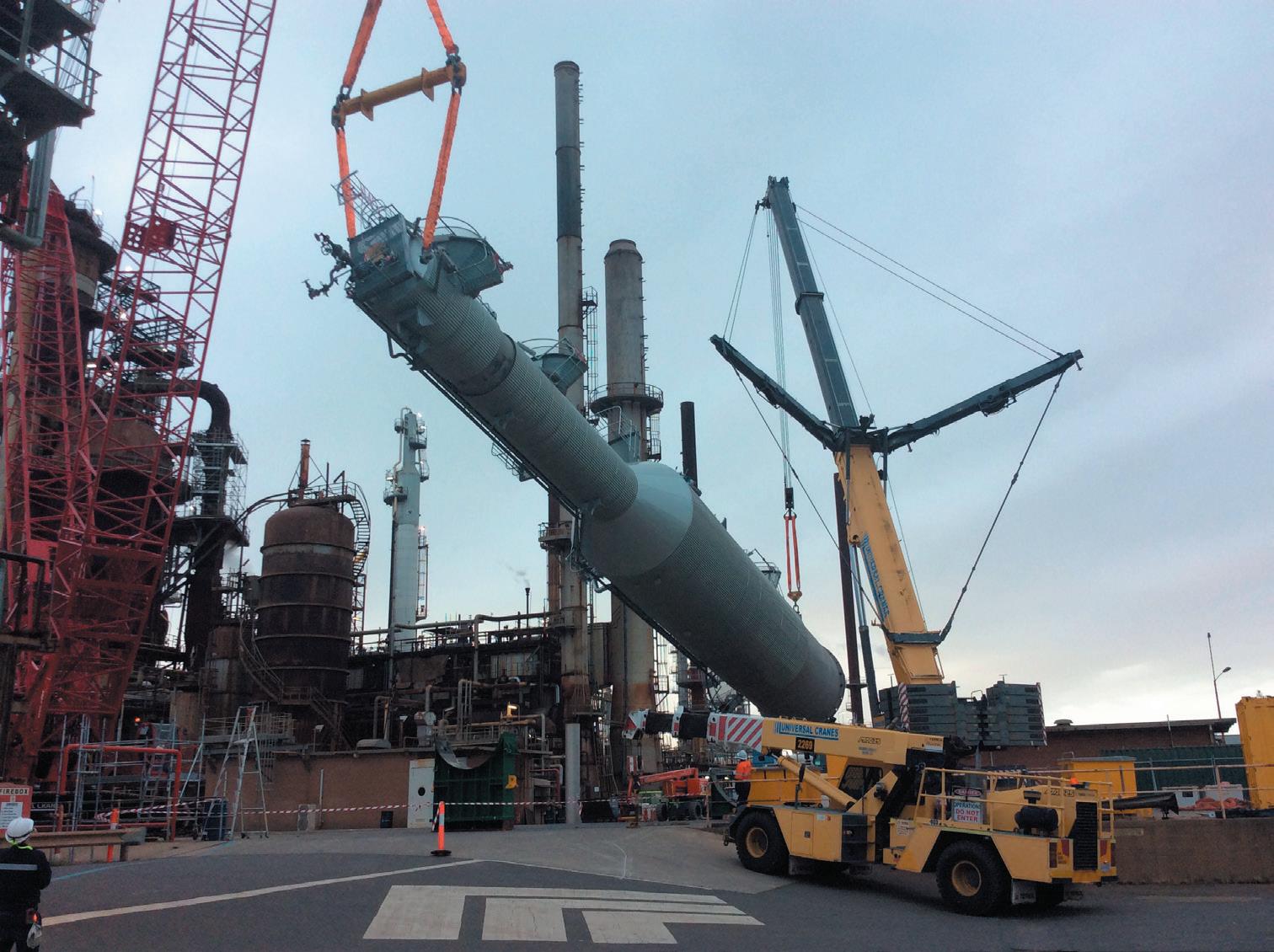
The load stability was constantly monitored to ensure a safe and stable lift.
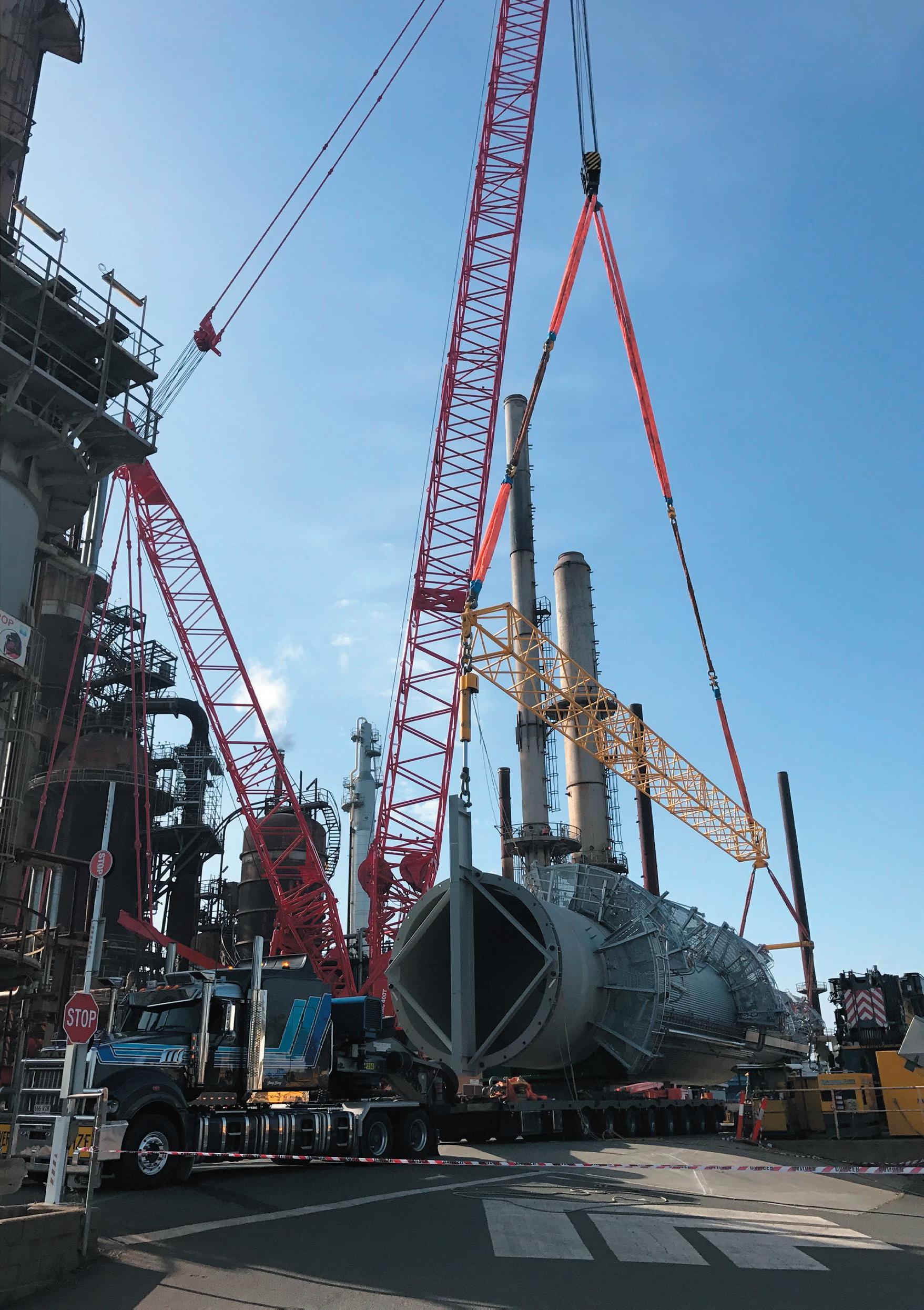