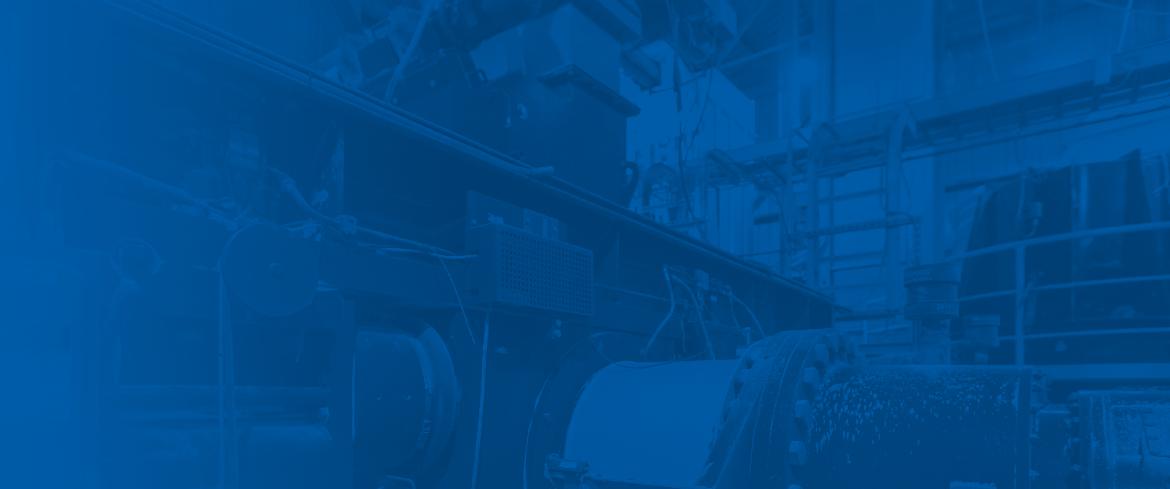
16 minute read
Weir Minerals: Engineered for endurance
Engineered for endurance
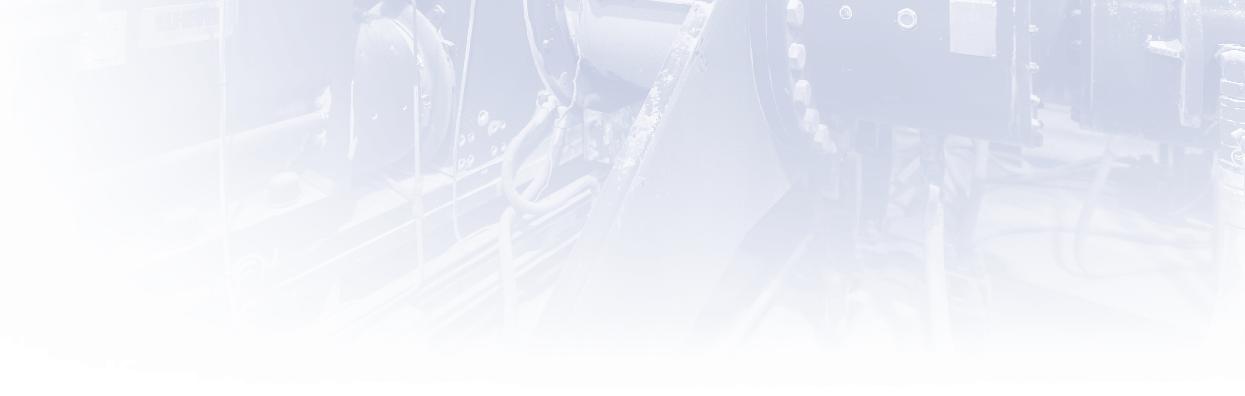
Advertisement
G & J Weir, a marine engineering company founded in Scotland in 1871 by brothers George and James, developed groundbreaking inventions such as the direct-acting feed pump for steam ships, helping support the rapid growth of transatlantic trade.
Their innovations led to significant gains in efficiency and reliability, and meant Weir’s products and services were soon in demand all over the world. The company has since grown to become one of the world’s leading engineering businesses serving mining, infrastructure and, until recently, oil and gas customers in more than 50 countries. Announcing the recent sale of its oil and gas division to Caterpillar, the company said it was transforming itself into a ‘premium mining technology pure play’. This strategic decision underlines the importance of mineral resources to global economic development, while recognising the opportunities available to help miners extract and process them more efficiently and sustainably. Not long ago, miners were driven by a desire to maximise production. A number of influences have come together in recent years to change the mining mindset, however, involving criteria commonly collected under an umbrella known as ESG (environmental, social and governance). With ore grades declining and new mineral deposits also becoming harder to find, miners are feeling the pinch. Weir is particularly well placed to respond to these new drivers, as its engineers are experts in solving problems. With a tradition of innovative engineering stretching back 150 years, Weir believes it can play a crucial role in helping its mining customers make their operations safer, more efficient and more sustainable.
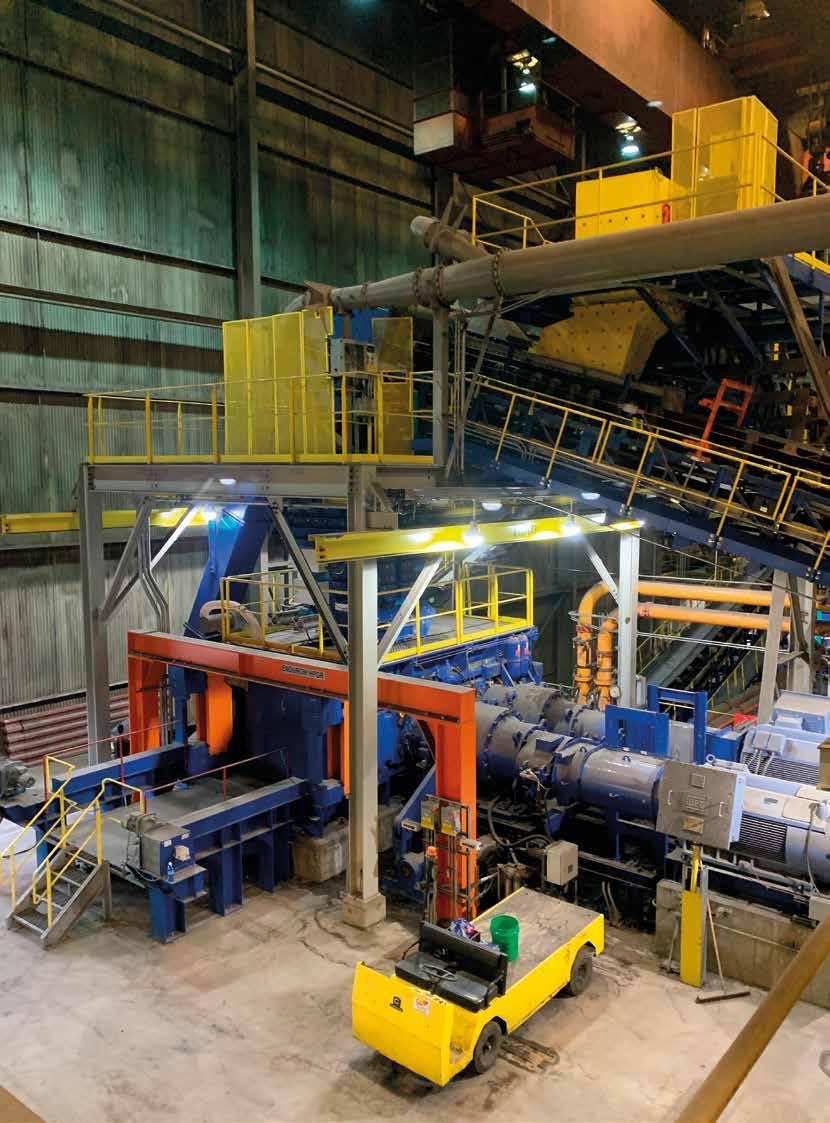
One of the many ways that Weir is addressing the new mining momentum is through its Enduron® HPGRs (High Pressure Grinding Rolls), the latest generation in crushing and grinding technology. Mining is an ancient industry and the business of breaking rocks has been fundamental to mineral recovery for centuries. In modern terminology, to break the particles up.” Crushing and grinding technologies have come a long way since early man first broke rocks by striking them with repeated blows. “Advances in technology led to mechanisation and the up to 80mm, tertiary and quaternary crushing stages can be combined into a single operation, and they can also take-over part of the ball mill grinding task. Requiring fewer process stages, the HPGR reduces overall circuit energy use, as well as grinding media consumption and wear cost.
comminution refers to the process through which solid materials are reduced in size through crushing, grinding and screening, before being passed through further mill circuit processes where copper, iron ore and other minerals are refined into raw commodities. In minerals processing, different combinations of crushers and mills can be deployed in the comminution process circuit, dependent, for example, on ore characteristics including rock size, hardness and moisture content. “Comminution in mining usually means crushing or grinding,” says Bjorn Dierx, global product manager for HPGRs at Weir Minerals. Crushing and grinding both break material into smaller pieces, but although most of us use these words interchangeably, they are not quite the same to an equipment manufacturer. “Crushing involves the application of sudden sharp blows,” explains Dierx, “while grinding uses consistent pressure
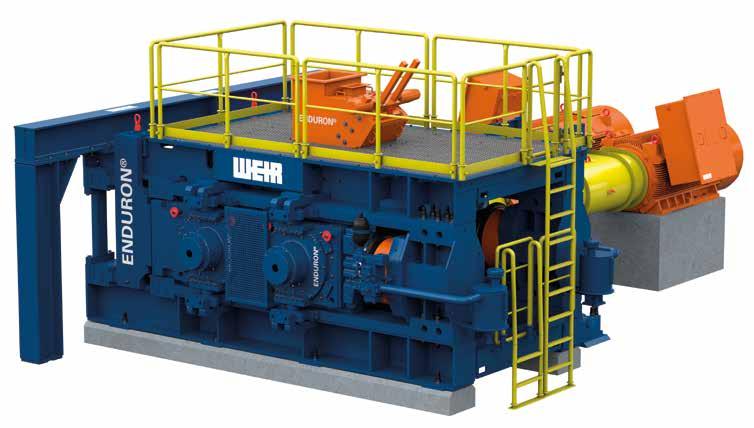
www.global.weir
introduction of steam and electricity,” explains Dierx, “so roll crushers, tube mills, hammer mills and jaw crushers became the standards for crushing and grinding equipment.” In modern times, he says, the jaw crusher became the inspiration for the cone crusher and the ball mill, but more recently still, an increased awareness of flaws in conventional methodology has stimulated a need for a new technology to streamline the transition from crushing to grinding. Weir Minerals engineers and manufactures its Enduron® HPGRs in Venlo, the Netherlands, and has supplied HPGRs for a range of applications for mine sites around the world. A comminution circuit can involve several stages, depending on the size of the original rocks and the desired size of the final particles. By using HPGRs, which can be fed with particles
Comminution is an energy-intensive process. HPGRs, often in combination with secondary cone crushers, are therefore seeing increasing acceptance in the mining industry as a replacement for the conventional SAG mill, because they offer significant benefits in energy consumption and consumable parts - as well as superior crushing performance. “The conventional blueprint for copper/gold grinding circuits using SAG and ball mill combinations,” says Dierx, “is known as an SABC circuit,” (semi-autogenous ball mill crusher). “One of our key copper/gold customers shared some figures with us from a copper project we worked on for them. These figures showed that overall circuit energy was reduced by up to 30 per cent by using HPGR, saving them around $8.4 million US dollars in a year, as well as saving 10,000 tonnes of carbon dioxide emissions. So, the savings are huge and bring a return on the
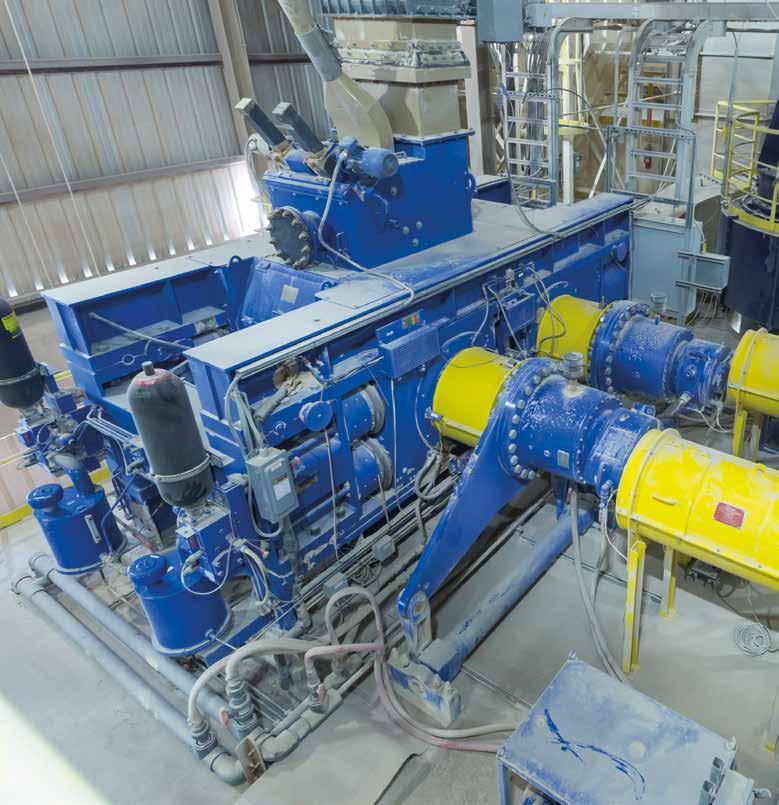
investment in the increased CAPEX in less than two years.” With their excellent throughput capacity, low maintenance requirements and energy efficiency, HPGRs are fast becoming a go-to solution for greenfield projects looking to maintain their margins, despite commodity price pressures and declining ore grades. One such is the Iron Bridge Magnetite Project, a joint venture between Fortescue Metals Group Ltd subsidiary FMG Magnetite Pty Ltd and Formosa
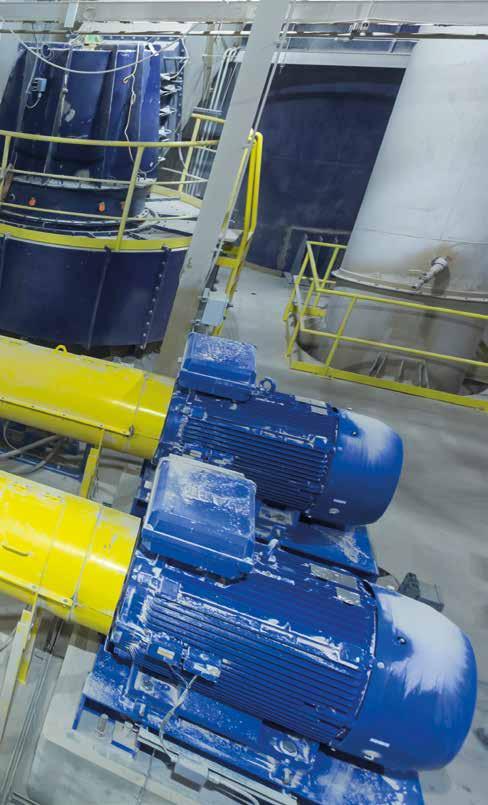
Steel IB Pty Ltd, 145km south of Port Hedland in the Pilbara region of Western Australia. In September last year Weir was awarded a £100m order to provide energy saving solutions to the project, including Enduron® High Pressure Grinding Rolls and GEHO® pumps, which together will reduce energy consumption and wet tailings waste by more than 30% compared to traditional mining technologies. Responding to the award of Weir’s largest ever mining contract, Group CEO Jon Stanton said, “Fortescue challenged us to help create one of the most energy and cost-efficient magnetite ore processing facilities in the world. Our engineers have worked relentlessly to design a solution that is truly innovative – delivering significant energy, water and cost savings. This is a great example of working in close partnership with an ambitious customer who shares our passion for using innovative engineering to make mining more productive and sustainable.” When you’re designing a comminution circuit from scratch on a greenfield site, the use of HPGRs has become a no-brainer, but it’s also becoming more of an attractive proposition in brownfield sites, too. “We definitely see interest when the existing installation is aging,” says Dierx, “or when there is a desire to increase capacity. From a financial point of view, it could also be that the energy costs of the existing site are causing losses. “It’s also the case with the older mine sites which are now processing harder rocks, that a large amount of the pebbles generated are treated as waste. In South America there are mines with massive stockpiles of pebbles which, with an efficient technology like HPGR, would become viable again to extract valuable material from. So, essentially, we can turn waste into cash for the miners.”
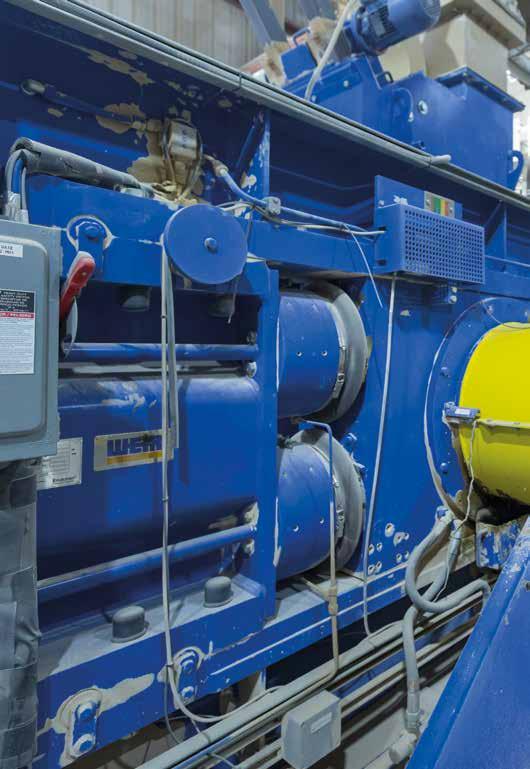
How it works
An HPGR basically consists of two counter rotating rollers, which draw the feed material from the top and into the working gap between the rollers. It sounds fairly simple, but, of course, it’s anything but. While the beauty of the Enduron® HPGR may be in its apparent simplicity, anything that works as smoothly as this is inevitably the result of a great deal of sophisticated engineering. The reason the HPGR is called a grinder, rather than a crusher, is that the ore material is not actually crushed by the working surfaces of the machine. With one roller fixed and the other floating, high-force hydraulic cylinders press against them. In the operating gap (the distance between the rolls), the particles experience extremely high pressures which exceed the compressive strength of the ore, so the material undergoes a process called inter-particle grinding. “In simple terms,” explains Dierx, “the ore is grinding itself, which gives a higher degree of efficiency compared with the cone crusher, where there is a single point of contact. “The HPGR is pressure controlled, not gap controlled, which means that the gap will be a function of the ability of the material to handle the pressure and therefore self-adjusts the gap to cater for the characteristics of the ore,” Dierx continued. This dynamic movement is called ‘skewing’. The HPGR is a flexible comminution tool which accepts a larger feed size than conventional mills but yet still produces a fine product. As the roll speed and pressure can be changed online, it can also readily adapt to changing throughputs and ore characteristics. In the last ten years, the HPGR has sparked a lot of interest and has been accepted into the market, with a growing number of new machines installed around the world. The Enduron® HPGR has been designed to eliminate problems often experienced by other HPGRs. Dynamic skewing, for example, solves a number of them. “In a perfect world,” explains Dierx, “the ore feed would be consistent, evenly distributed, with a common hardness, grade and moisture. But in the real mining world there are changing ore bodies, changing grades and uneven feed, including oversized material which can impact the operation of the machine. That’s why skewing is an essential feature
of the HPGR. The Enduron HPGRs are the only machines designed to support the roll-skew required to handle those changing conditions.” In order for particles to be crushed effectively, the pressure on the particle side of the conveyor belt, the operating gap needs to be wider at that side than
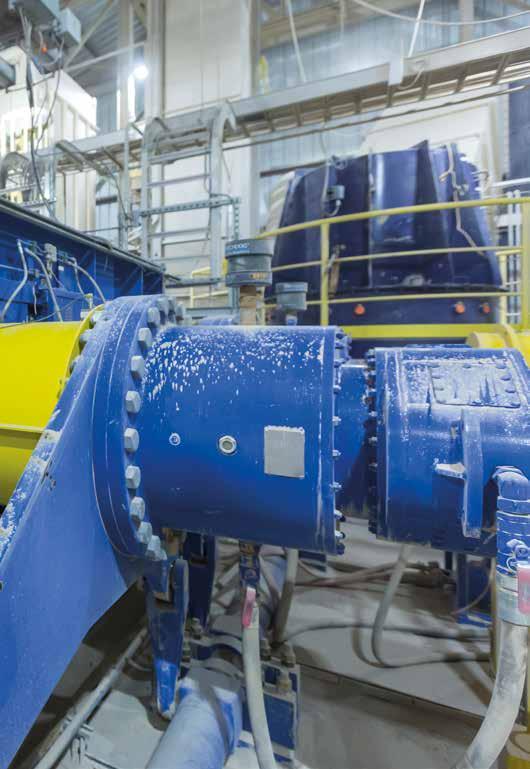
needs to exceed the compressive strength of the material. In the perfect world of even feed conditions, where the particles are spread uniformly across the width of the belt, the operating gap can be the same along its whole length and the particles will be crushed evenly. But if the rocks are loaded more on one the other, so a wedge-shaped operating gap is formed. This is referred to as the roll-skew, and it’s this that ensures a consistent grind, as all the ore particles experience the same pressure. “It’s almost impossible to eliminate feed variance and segregation completely,” says Dierx. “This has posed a critical challenge for HPGR operators in the past – but dynamic skewing, as featured in the Enduron® HPGR, maintains optimal pressure across the entire feed.” As well as uneven ore feed, tramp metal such as steel balls from ball mills can also enter the operating gap, which can cause substantial damage to the roller surface. The risk of damage is significantly reduced with a skewable HPGR. There are other HPGRs on the market, but the Enduron® HPGR is the only one capable of delivering dynamic skewing reliably, because of its innovative bearing arrangement. In an Enduron® HPGR the bearings stay aligned with the shaft when it skews, as the bearing housings are designed to skew with the shaft. “We see a lot of bearing failures with competitors’ machines,” says Dierx. “It’s a global problem with HPGRs, but our design mitigates that issue. It’s one of the great strengths of the Enduron HPGR. “Some competitor HPGRs are prone to bearing wear because the shaft skews within the bearing itself, which introduces a very high load in the bearing and results in unreliable shafts. These bearings have lead times over 52 weeks. There’s a huge global shortage of large engineered bearings so for our customers it’s very important that the machine has high availability and they don’t need to keep expensive stock on site. Our unique bearing design ensures that.”
Another value-add built into the Enduron HPGR is the design of the lateral walls. These retain the ore particles to ensure they are kept in the operating gap. The lateral wall is the sealing plate, which, combined with the tyres, are the main wear components of an HPGR. “The Enduron HPGR’s lateral walls have a spring-loaded design,” explains Dierx, “which adjusts their position relative to the tyres, a particularly important factor with a skewable design philosophy. This assures a tight seal, where others have a static design with a larger distance between the tyre and the lateral walls. “We use a patented tyre technology, which works in conjunction with the lateral walls,” he continues, “bringing another high value-add to the machine.” The multi-faced integrated locking system features tungsten carbide studs, embedded into the base material of the tyre, permanently securing the edge stud. Edging can be problematic with poor feed presentation and maintenance practices, but the Enduron® HPGR’s edging studs remain in place where others might become dislodged. Still on the subject of edges, HPGRs are subject to a so-called ‘edge effect’ at the end of the roller, which gives a lower grind as a result of the lower pressure there. The length of the edge effect area is related to the operating gap between the rolls, which is a function of the diameter of the roll. The bearing design of an Enduron® HPGR facilitates a compact roller design, keeping the roll diameter as small as possible but with wider rolls. The Enduron® tyre’s Length (L) to Diameter (D) ratio therefore delivers a higher grinding efficiency at a single pass, as the edge effect is diminished with wider rolls. “The L/D ratio can also have a big impact on a circuit’s CAPEX,” points out Dierx. “Longer rolls can be fed with a wider hopper, which reduces the height of the hopper, which in turn reduces the height of the building which houses the HPGR, and that is directly reflected in lower structural costs. Furthermore, a lower HPGR building reduces the length of the conveyors, and that impacts on the plant’s footprint, which means a big reduction in investment as well.”
“Fortescue challenged us to help create one of the most energy and cost-efficient magnetite ore processing facilities in the world. This is a great example of working in close partnership with an ambitious customer who shares our passion for using innovative engineering to make mining more productive and sustainable”
Weir continues to work on technology development, too. “Wear life improvement is another big value-add for our customers,” says Dierx, “and here we are focusing on improving the roller surfaces, so the wear life can remain
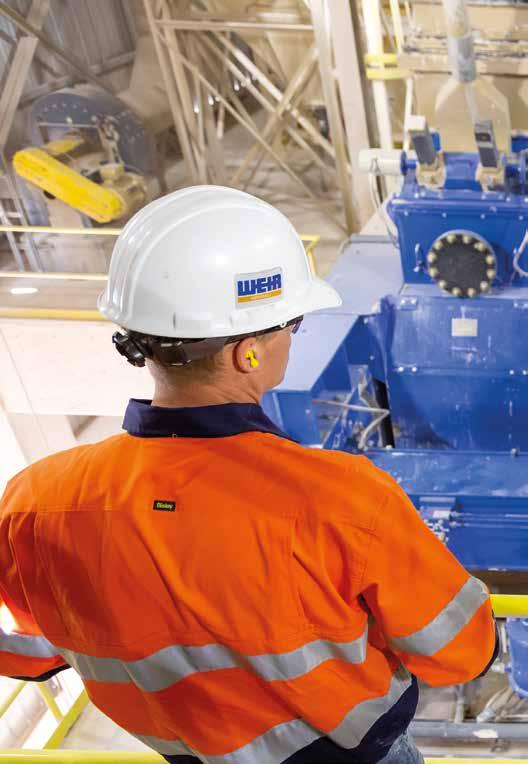
high in the face of increasing ore hardness. “The Covid-19 pandemic has also created a need to support customers remotely, so we’ve developed digital systems which enable remote monitoring of all our HPGRs. And we are working on an automatic tyre wear management system so we can monitor the condition of the tyres without stopping the machine. So, the remote support will help with optimisation and also predictive maintenance.” Another advantage of the Enduron® HPGR is its high degree of availability – 95 per cent is not uncommon. Its unique design enables the rollers to be replaced quickly, reducing downtime and releasing personnel and lifting
tools during a planned shutdown. As there is no need to disassemble the feed chute and hopper to exchange rollers, the tyres can also be replaced within a 24-hour shutdown.
www.global.weir
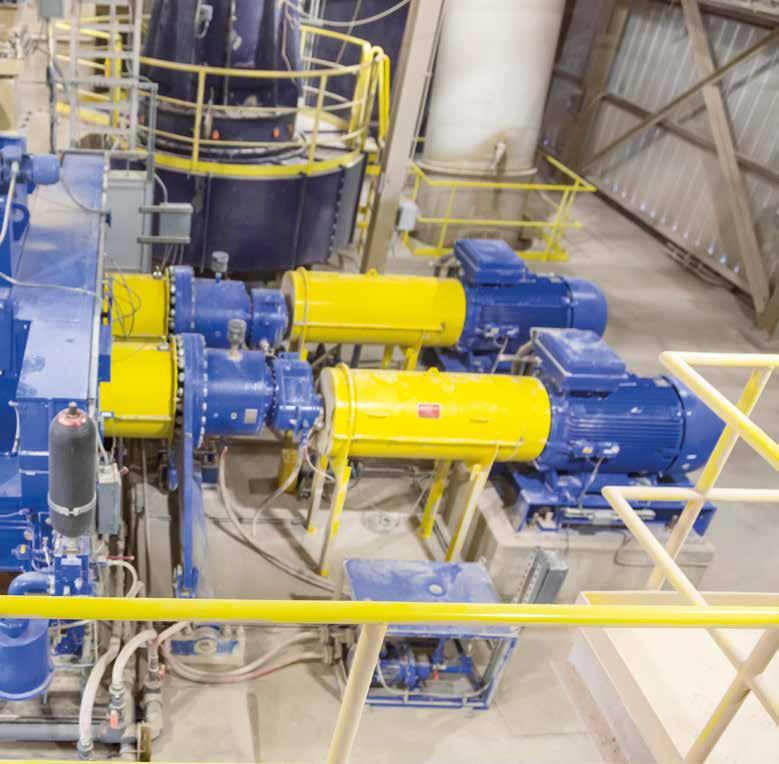
As crushing and grinding machinery are energy-intensive, optimising efficiency can save a lot of money. In a conventional SAG mill, oversized feed wastes energy because some of the material is recycled continuously through the machine. Being pressure controlled, rather than gap controlled, gives the Enduron® HPGR several advantages over conventional machinery. Interparticle grinding increases efficiency, as pressure is transferred to the particle via multiple directions. By applying the right pressure for the specific material, final product size can be determined by controlling the pressure. The HPGR therefore streamlines the transition between crushing and grinding by accepting a larger feed size than a ball mill and producing finer sized particles than a cone crusher. The unique control philosophy of the Enduron® HPGR, facilitated by the bearing design, transfers the energy equally to all ore particles across the width of the tyre, creating self-adjusting metal rolls, and ensures that the ore is kept in the operating gap at all times, even during roll-skew. The optimised roller surface technology derives from over 25 years of operational experience. Thanks to their premium tungsten carbide studs, Enduron® HPGR tyres last longer than the competition. Optimised for load bearing and promoting an autogenous layer to absorb wear, the Enduron® HPGRs come with a guarantee of a specified minimum life. Combined with the unique bearing assembly that reduces the risk of failure and the wear reduction associated with skewing, the Enduron® HPGR is expertly engineered for endurance. “The market drivers for HPGRs are very compelling,” concludes Dierx. “Ore grades are declining, ore is harder and can be more difficult to liberate. Energy is a huge cost for the mining industry but all miners are now under huge pressure to reduce their carbon footprint as well. And then, ore scarcity means that new mines tend to be located in increasingly arid areas, so water is at a premium or not available at all. “Against this backdrop HPGR brings essential benefits,” he continues. “It doesn’t need additional water for fine grinding, as we saw in Iron Bridge. This also leads to substantial reduction in wet tailings. So, the cost of ownership compared to a SAG circuit is greatly reduced, driven by high uptime and relatively long wear life. And, of course, the massive energy savings.”
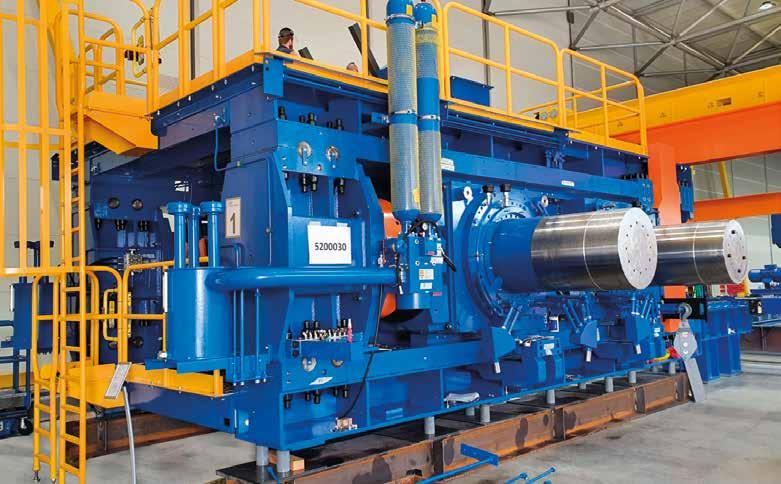