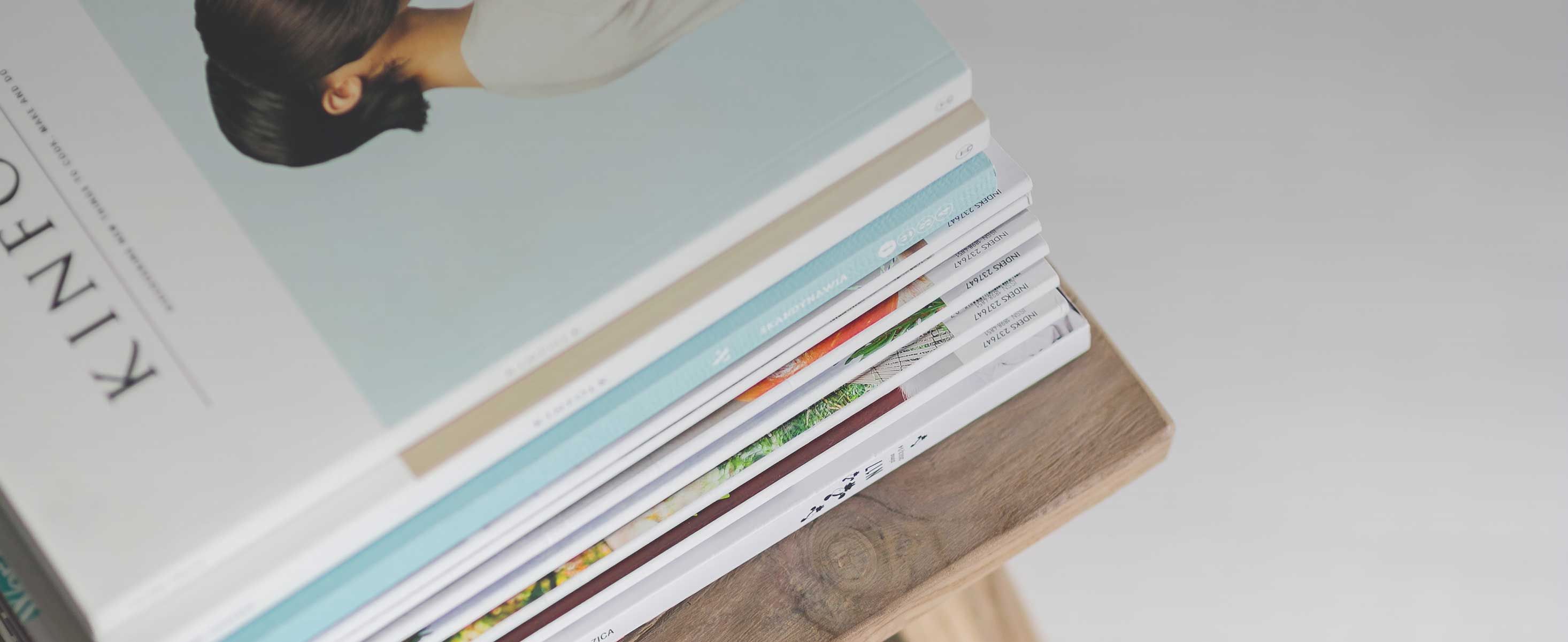
4 minute read
Increase the Number of Female Supervisors and Upgrade Apparel Jobs to Manufacturing-Related Services
shorter (as in Sri Lanka) or in countries with multiple apparel and manufacturing clusters (like Vietnam) that enable rural areas to be better connected.
A good starting point to support women’s transition to longer-horizon working trajectories is to increase the number of women in supervisory positions—and in apparel, the most realistic way to advance is to become a line leader or production supervisor. These workers also fall into the production category, but they need to have secondary or technical education and account for only a small percentage of all apparel workers. Note that, in apparel, workers are split between production (75–90 percent) and knowledge-intensive, high-skill services (10–25 percent). Within production, 70–80 percent work on the production line, and 5–10 percent are supervisors.
Advertisement
Although tasks performed in food processing, furniture production, electronic assembly, or medical supplies manufacturing are different from those in apparel manufacturing, the skills associated with supervisory work are less industry-specific and can enhance opportunities for job mobility across industries. In other words, promotions within the apparel industry will not only increase the earnings and benefits for working women in apparel but also increase their prospects of remaining in the labor market. For example, if such women interrupt their work lives to attend to childcare responsibilities, they can return to the labor market through either apparel or other manufacturing industries.
IMPLEMENT INTERNSHIPS AND SKILL-SPECIFIC TRAINING PROGRAMS
One way for women to move up to the supervisory level is through skill-specific training programs. Training ensures that workers have the necessary skills for the position, increases female participation and confidence in their abilities, and exposes men to females in leadership positions, which can also help to change male perceptions that females are less capable.
These programs should target female workers and account for the barriers they face, such as the cost of the program, lack of gender-specific facilities, and travel. To address cost concerns, the government can subsidize employers directly to incentivize them to hire and train women. For example, Saudi Arabia’s Support Women’s Jobs in Factories program subsidizes women’s salaries and training for up to six months while they receive training in computer, English, managerial, and behavioral skills (Kronfol, Nichols, and Tran 2019). Further, locating training institutes near factories in industrial areas can minimize the number and scale of transportation options that need to be developed.
In Bangladesh, a free six-week training program was offered to 80 apparel factories to promote women to supervisory roles. Before the training, both genders perceived women to be less capable than men across all skill areas needed to be a supervisor. Females also rated themselves as being weaker than existing supervisors across all areas, whereas male participants did not. After the training and after the women worked on the line as supervisors, the performance gender gap completely closed and male operators exposed to the female trainees improved their view of females as supervisors (Macchiavello et al. 2020).
Development and implementation of such programs can benefit from collaboration with experienced foreign or multinational organizations. In Bangladesh, the Gender Equality and Returns (GEAR) initiative of the Better Work program—a collaboration between the International Labour Organization (ILO) and the World Bank Group’s International Finance Corporation (IFC)—has made significant strides in advancing women’s economic potential and improving access to better jobs and opportunities. GEAR is scaling up to train 700 female operators to promote career-progression opportunities for women in the ready-made garment sector. In the first phase, GEAR trained 144 female workers, of whom 58 are now in supervisory roles. GEAR-promoted female supervisors also saw a 39 percent average increase in salary, and lines led by GEARtrained females saw an average increase of 5 percent in efficiency. The program also offers a three-day Supervisor Skills Training program (ILO and IFC 2019).
FOCUS PROGRAMS ON SUPPLYING EMPLOYABLE GRADUATES
Programs to upskill female production workers that are aligned with the evolving needs of the manufacturing industries will not only help include more women in mid-skill occupations but also support a long-run industrial upgrading strategy. Increasing education or training will not raise the number of jobs and careers available for women if labor demand is insufficient to absorb the newly educated women. Shortages and gaps between curriculum and industry are common barriers across LMICs. Workers and training programs for supervisors are often scarce in the apparel industry (Quang et al. 2020).
Vocational and short-term training can be particularly effective for filling industry skill gaps when employers and training providers work together. In Indonesia, women who attended junior vocational school instead of junior regular school were more likely to join the labor force at the end of their studies (ADB 2015). Investing in training by funding the development of relevant programs and providing benefits to factories to train workers is a key opportunity to upskill workers and increase female participation in mid-skill positions. Countries should form industry and skills councils, develop national skills development strategies, and use these programs to support female inclusion and permanence in the labor force.
When educational programs and industry priorities are aligned, greater opportunities for employment emerge. Industry-relevant skills training in emerging sectors has