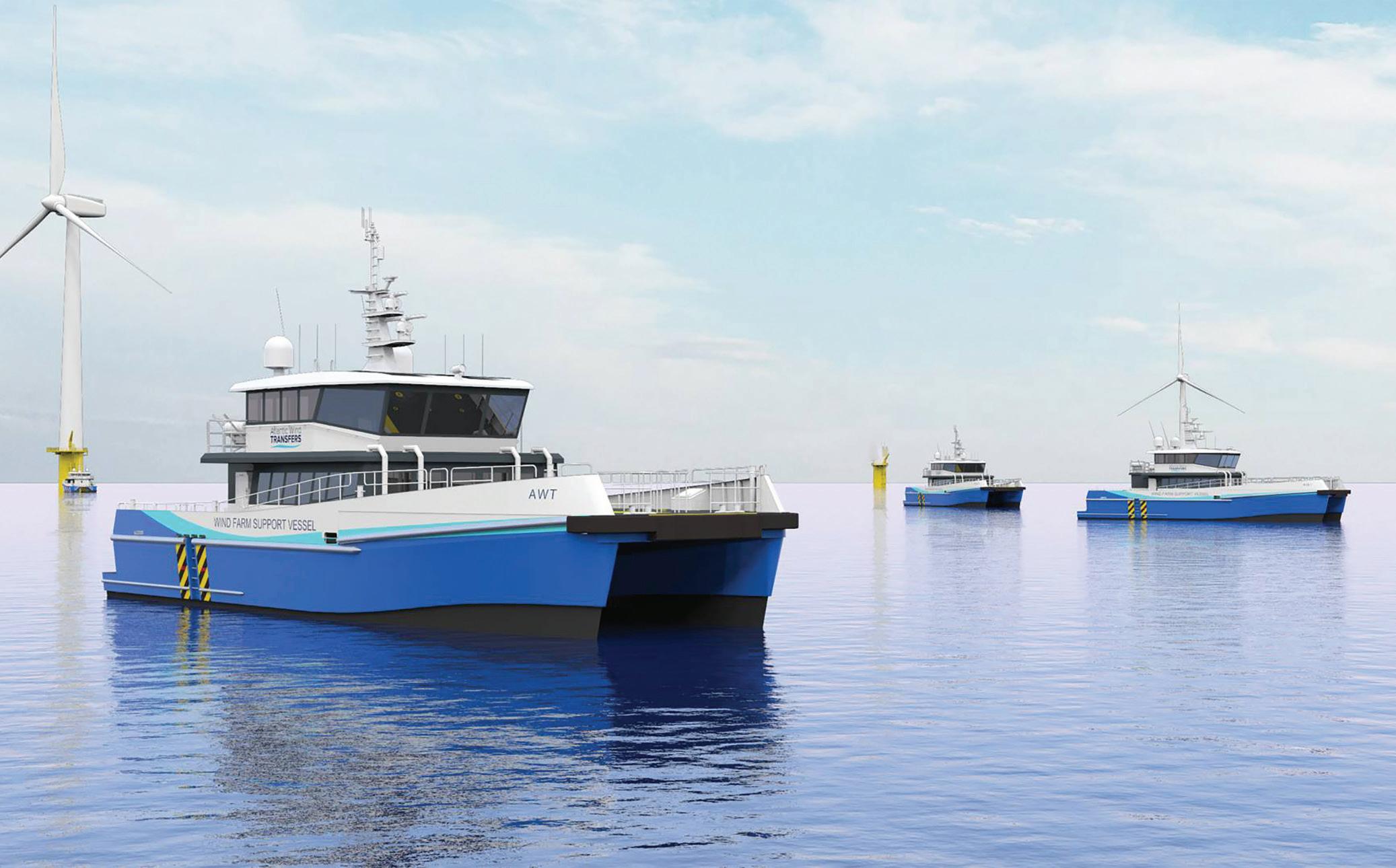
8 minute read
Mixed Forecasts
from WorkBoat April 2023
by WorkBoat
By Jim Redden, Correspondent
With some U.S. offshore wind farms facing delays or worse, shipyards engaged in the construction of crew transfer vessels (CTV) have contrasting visions on how the emerging sector will shake out over the next few years.
At one end of the spectrum, St. Johns Shipbuilding, with seven aluminum CTVs either under construction or in the hopper at its Palatka, Fla. shipyard, is understandably bullish. “The market is like a freight train and it’s going to be very difficult to stop. It may slow down a little bit, but it’s not going to stop,” said Jim Cutts, who heads up the company’s CTV program.
At the other end, Peter Duclos, president of GladdingHearn Shipbuilding, Somerset, Mass., with a single CTV set for commissioning later this year, sees an inflationary cloud blocking near-term prospects. “I don’t see the market as being very encouraging at this very time,” he said. “There’s hesitancy due to inflation and that’s an understandable problem.”
For sure, project delays, at best, are likely as prominent East Coast wind developers attempt to renegotiate power purchase agreements (PPA) that were signed with states when costs were more tolerable. Four-decade high inflation rates have since put the viability of some approved wind farms into question, creating uncertainties throughout the infrastructure.
“My sense is that tenders for CTV have slowed in coming out mostly because of inflation over the last two years,” said Marcia Blount, president of Blount Boats Inc., Warren, R.I., which delivered the first U.S.-flagged CTV in 2016 and has two CTVs currently under construction. “There’s the supply chain issues in getting deliveries, but it’s mostly due to the increased costs the developers are facing.”
Duclos believes supply chain bottlenecks will ease once the economics are sorted out. “I think we have a commitment issue, resulting from the [PPA] renegotiations. I think the supply chain will fall into place when all the commitments are made, but we’re not there yet.”
Gladding-Hearn is set to deliver an 88.5' Incat Crowther CTV to Patriot Offshore Marine Services, New Bedford, Mass., this fall. The vessel will have the capacity to ferry up to 24 technicians to and from the Vineyard Wind Farm off Massachusetts, which remains on track to begin delivering power late this year.
Unlike developers, shipyards do not have the option of renegotiating boat contracts to deal with spiraling costs. “I’m shocked to see the size of the material increases and my labor rate increases, especially for ABS-certified welders. We’re under fixed price contracts so it’s getting very uncomfortable,” Blount said. “The wind farm developers are seeing their margins tightening, so they’re demanding that the vessel operators tighten, and this filters down to the shipyards. There are other types of boats to build besides CTVs, but it would be unfortunate as we are at the right place at the right time, and we understand these boats.”
St. Johns President Jeff Bukoski said aluminum prices have spiked, primarily due to the Ukrainian war and the accompanying tightness in the bauxite feedstock. “That’s a challenge for advancing medium and long-term pricing for aluminum vessels,” he said. “Machinery and equipment vendors also seem to be able to raise their prices without regard and shipyards do not have that same flexibility. We have to walk a little bit of a tightrope.”
He agreed with Blount that labor, specifically aluminum-qualified welders, ranks as a significant constraint.
“Aluminum welding is a bit of a niche even within our market and certification of those welders becomes more challenging and expensive,” he said.
Plenty Of Work
The National Renewable Energy Laboratory (NREL) estimates no less than 58 Jones Act CTVs will be required for the wind farms now permitted and in various stages of development. Cutts, for one, believes that projection is well on the conservative side.
“I think it could jump to 70 and maybe even 100 boats off the East Coast in the next 10 to 15 years. It’s huge and there’s enough work to go around for all the yards capable of building these boats,” said Cutts, who came to St. Johns from his native UK where he was heavily involved in the world’s premier offshore wind industry.
Blount said her 74-year-old familyowned shipyard is one of about 10 U.S. yards in the north and south capable of mass-producing aluminum catamarantype CTV.
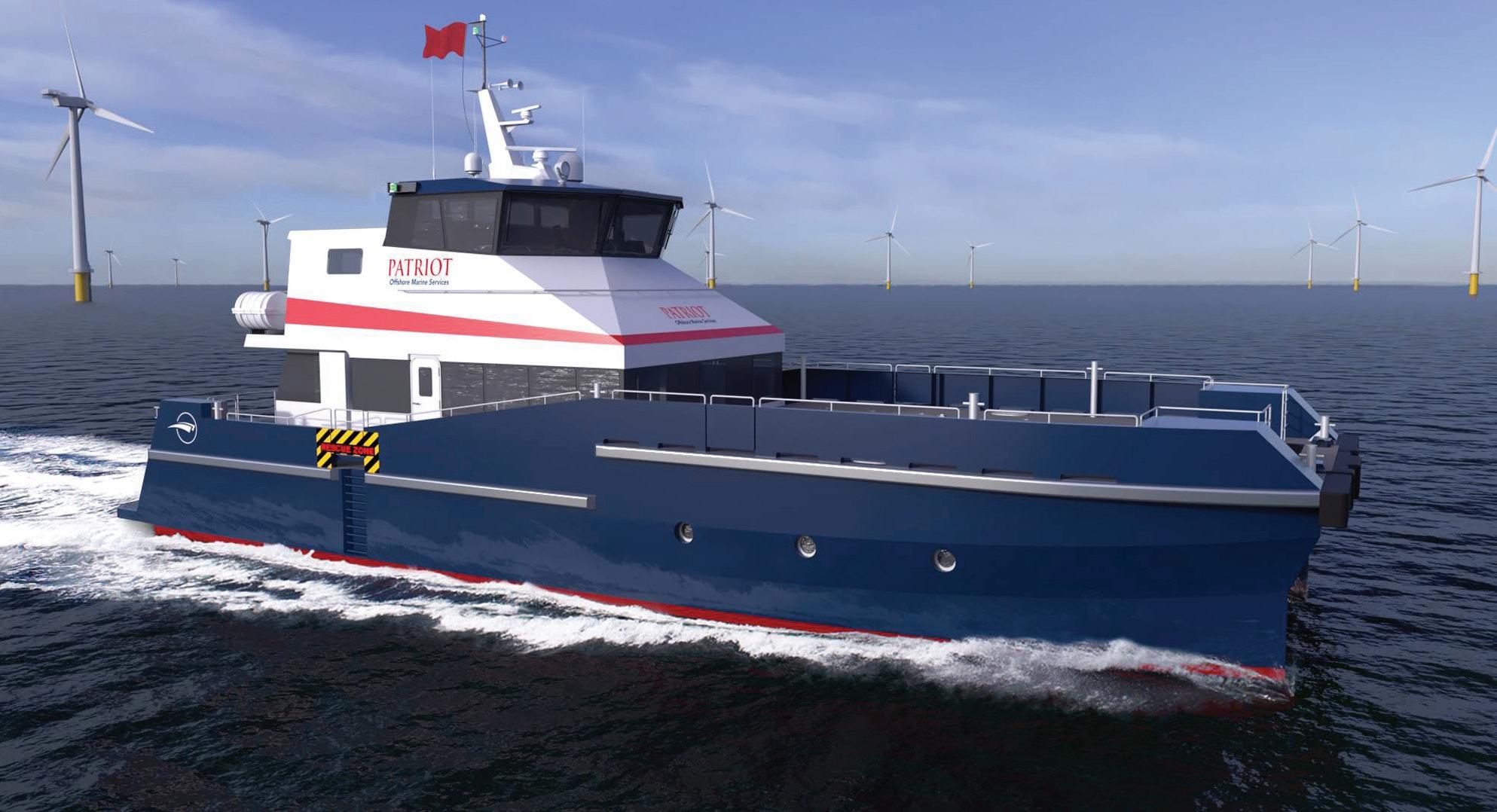
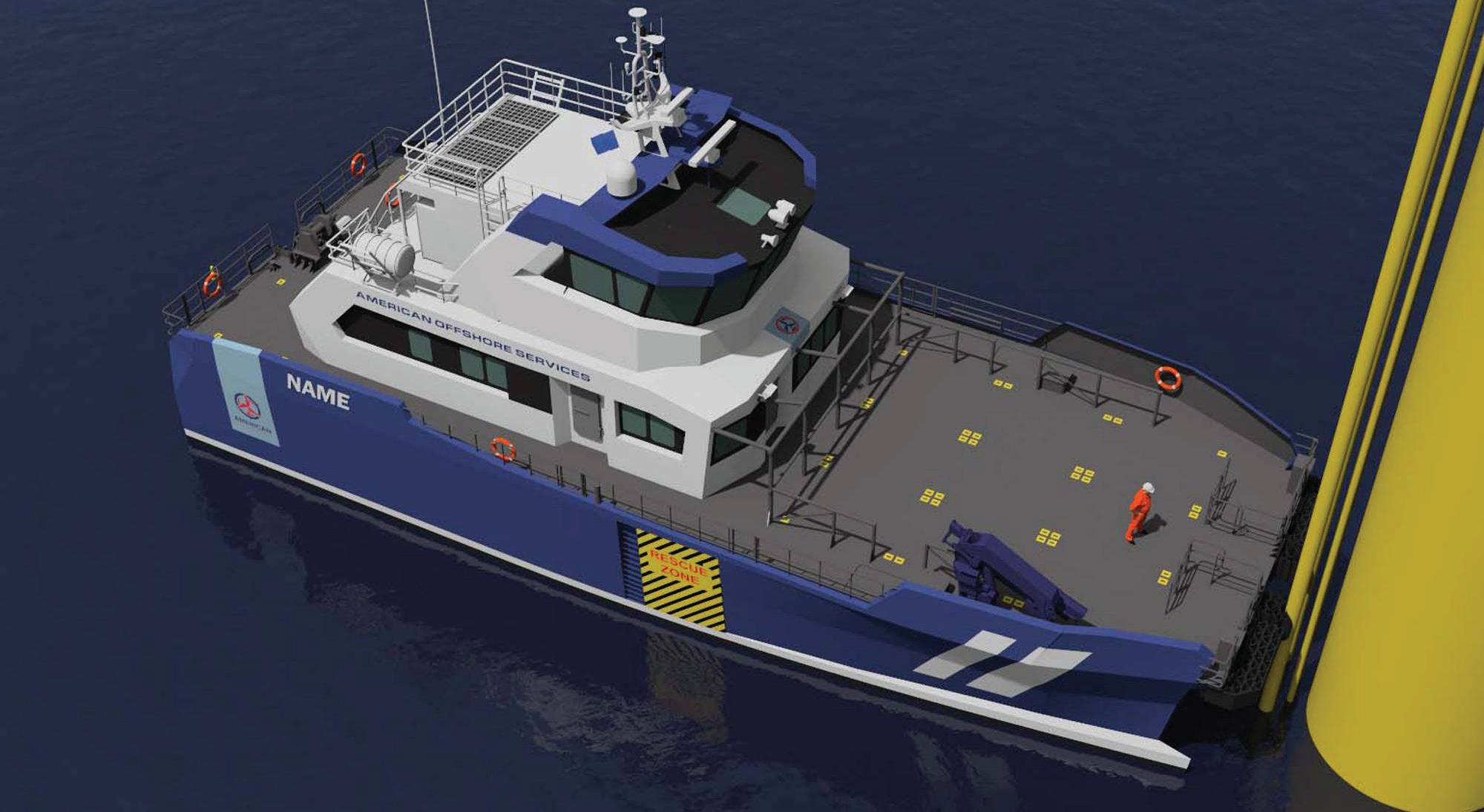
Despite the headwinds, St. Johns, which was acquired by Americraft Marine Group last year, is well un-
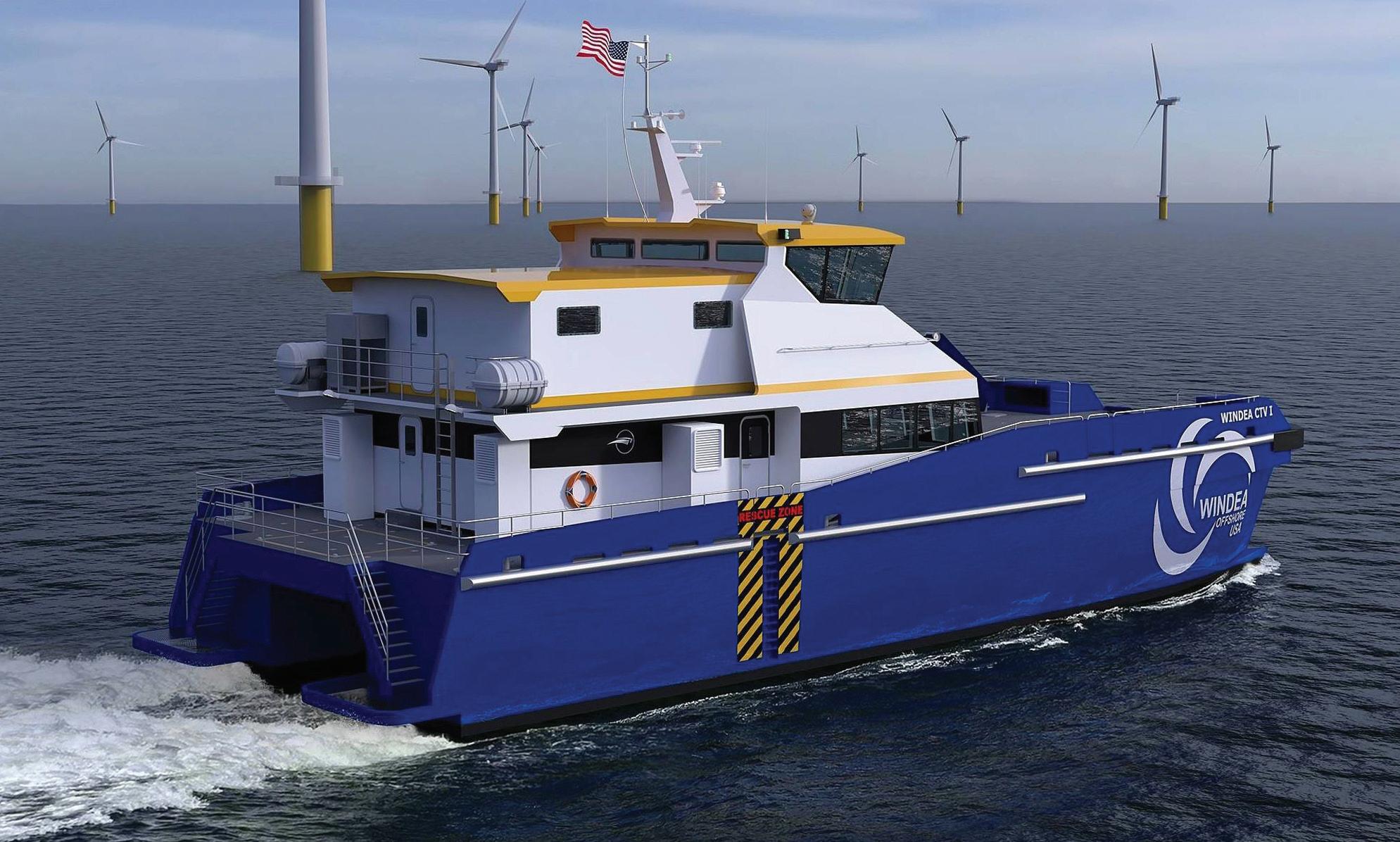
STOCKPILE OF PSV-TO-SOV CONVERSION CANDIDATES SHRINK
Asconstruction begins on the newest U.S.-flagged service operations vessel (SOVs), companies looking to get a deal on a stacked platform service vessel (PSV) suitable for conversion for offshore wind service are finding the pickings a lot slimmer “With the oil and gas industry picking up in the last 12 months, I believe there will be less and less opportunities to convert these PSVs, as they are now becoming valuable assets,” said Liviu Galatanu, managing director of Romanian naval architecture and marine engineering firm GOL Marine
Conversion made perfect sense when those vessels could be picked up for a relative song. However, as the offshore industry regains its footing after the Covid disruption, high-end PSVs once idled throughout the Gulf Coast and elsewhere are now nearly fully booked with offshore oil and gas work. According to the National Renewable Energy Laboratory (NREL), a new SOV costs upwards of $100 million or more and takes two to three years to build, while a conversion can cost half as much with a much shorter timeline.
GLO Marine has completed two PSV-to-SOV conversions, each requiring about eight months to complete. As for the actual cost differential “it’s hard to tell with today’s steel prices,” Galatanu said in an email.
Converting a PSV for offshore wind projects is far from a straightforward proposition, given the complexity of an SOV underdeck, which typically requires removal of all drilling fluid and completion brine tanks. The underdeck of an SOV has been likened to a giant warehouse, connecting to an elevator system that goes up to an articulated gangway that transfers technicians and their equipment directly to the transition piece of the wind turbine.
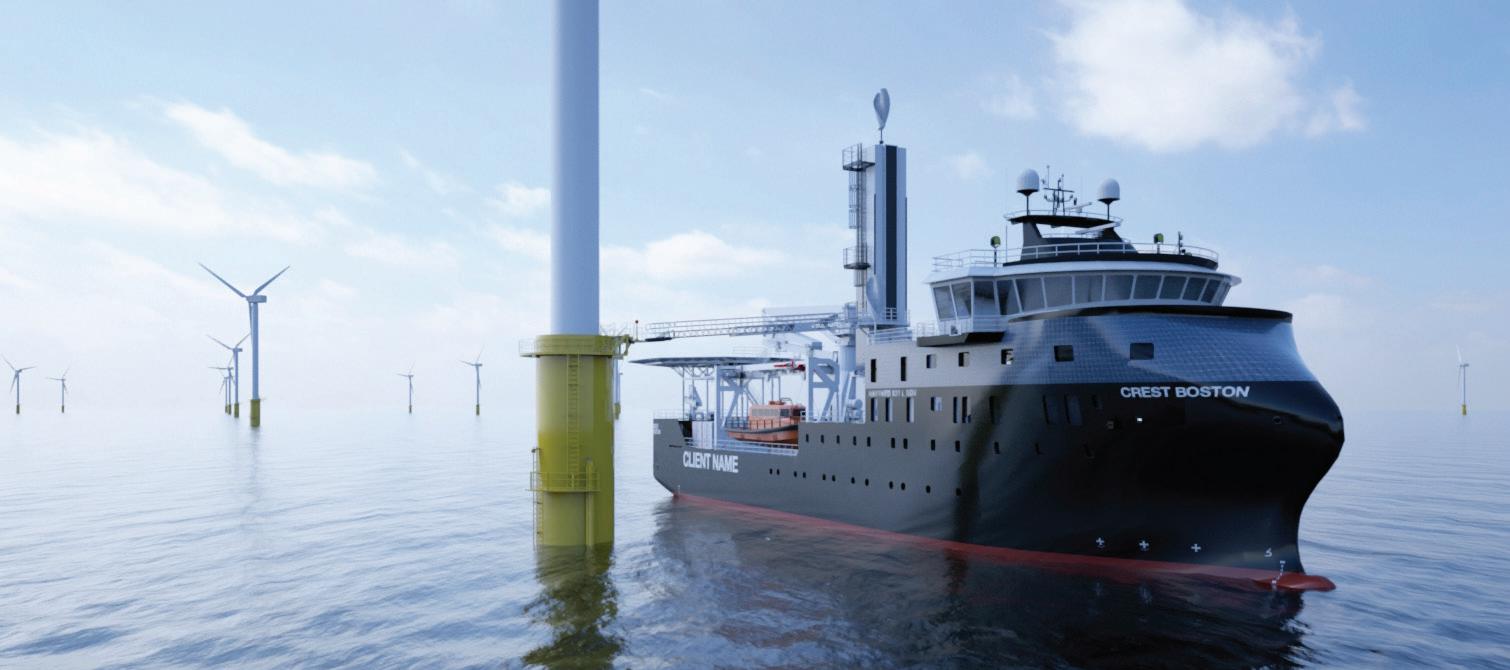
Unlike a PSV, SOV technicians are also on station for extended periods, making crew accommodations a primary design consideration. “This ‘warehouse’ is connected to an accommodation area, which for the first time in ship design history is aligned with a two- or even three-star hotel standard,” Galatanu said. “The major issues are coming from the need to accommodate a large number of technicians on board. This means adding a SPS (special purpose ship) class notation to existing PSVs which has a major impact on vessel’s stability and thus the existing arrangements and tank layout.” –
J. Redden
derway on a major expansion that includes more covered tents required for aluminum construction and an underground gas distribution system. A recently modified Maritime Administration grant is funding 50% of the expansion, which will enable the yard to produce up to eight CTVs a year.
“Generally, we’re revamping almost our entire infrastructure to support individual build slots for CTVs while still maintaining our steel line. We haven’t set an exact percentage yet, but it’s fair to say that we’ll maybe be in the 75 percent to 25 percent range of aluminum versus steel,” Bukoski said.
St Johns has two 82.8' Chartwell CTVs and two Incat Crowther 98.4' CTVs set for delivery this year to Atlantic Wind Transfer (AWT) and Windea, respectively. Windea is a U.S. joint venture of Hornblower and MidOcean Wind. Construction will begin this year on two additional AWT vessels and another CTV for an undisclosed customer.
Blount, likewise, is looking at increasing covered capacity at its six-acre shipyard but is awaiting more clarity on the economic front. “We have approval for a 45-foot addition to our large hull shop and additions to our smaller shops where we do the prefab,” Blount said. “But I’ve got to see if it’s worth it to do the capital investment and then wait for a return. If inflation had been kept at bay, I think we all would have been fine, both the developers and the shipyards.”
Evolving Designs
Since delivering the 65' 12-passenger Atlantic Pioneer CTV to service Rhode Island’s Block Island Wind Farm seven years ago, Blount has had a ground-floor view of rapidly evolving designs. The company has two new generation U.S.specific G-class CTVs scheduled for delivery in 2024 and early 2025 to Massachusetts-based American Offshore Services (AOS), a joint venture of Sweden’s Northern Offshore Services (NOS) and SEA.O.G Offshore, Seattle. The 100' hybrid ready CTVs are designed by NOS and have capacity for 24 passengers, excluding crew.
“It’s amazing how fast these vessels have increased in size and complexity. We call them the beasts in the hull shop,” Blount said. “These are big boats and very robust with a very complicated bow section and all the bells and whistles a lot of the developers want.”
The problem is those bells and whistles can change from developer to developer, which further tightens the margins, especially on one- off projects, Duclos said. Awarding shipyards multiboat contracts with like designs would reduce costs, time, and risks, he said.
“They’re trying to standardize to a degree, but it’s a little frustrating that every developer seems to have their own idea of what the perfect boat is. The differences in what they’re asking for won’t make a lot of difference at the end of the day, when you consider the cost of building a semi-custom boat for every single contract and every single customer, said Duclos. “Then they’re splitting the boats up [between shipyards], so we’re starting from scratch to fit their designs. For the moment, we’re pretty happy with Patriot. They’re great to work with, so I’m not complaining. I’m just concerned about the future.”
That future, as Blount sees it, hinges largely on getting costs stabilized.
“There’s definitely going to be a future. There’s definitely going to be wind farms built, but I do see a lot of uncer-
Badly Needed Wtivs Heading To East Coast
Latethis year, the 472' Charybdis is expected to leave the Keppel AmFELS Brownsville, Texas, shipyard and begin work as the only Jones Act-compliant wind turbine installation vessel (WTIV) in U.S. waters, while a uniquely engineered foreign-owned installation vessel is set to follow two years later.
“Charybdis is expected to be in service ahead of the 2024 turbine installation season,” said a spokesman for Dominion Energy Inc., which ordered the vessel to install up to 180 turbines at its Coastal Virginia Offshore Wind (CVOW) project off Virginia Beach, Va. First, however, the Charybdis will deploy to New London, Conn., where it has been subchartered to Ørsted and Eversource for installation work at the Sunrise and Revolution wind farms off New York and Connecticut, respectively. Both projects are slated to go online in 2025, while construction of the CVOW project is expected to be completed by year-end 2026, the spokesman said.
The Charybdis is a start, but a far cry from what will eventually be needed to install the 2,100 wind turbines the Department of Energy (DOE) said will be required to meet the Biden administration’s objective to generate 30 gigawatts of offshore wind power by 2030. The DOE estimates that will require the delivery of up to six Jones Act-compliant WTIVs annually.
Meanwhile, Maersk Supply Service is building a wind tainty. I think if inflation can be tamed, then the cost structures can stabilize and that would help everybody.” installation vessel in Singapore destined for the East Coast. The vessel, which is slated to mobilize in 2025 under contract to the Equinor-BP joint venture to install the wind turbines for New York’s Empire Wind and Beacon Wind projects, represents a stark departure from the conventional jackup design.
The new WTIV incorporates a proprietary load transfer system that Maersk claims to be over 30% more efficient than standard installation vessels and allows the vessel to remain on location throughout the installation. “This enables the WTIV to be deployed solely for the purpose of the turbine installation. The solution is also less weather dependent, enabling installation to continue all yearround,” Maersk said in a statement.
To comply with the Jones Act, the Danish company has teamed up with Kirby Offshore Wind, Houston, to provide feeder barges and tugs. – J. Redden

