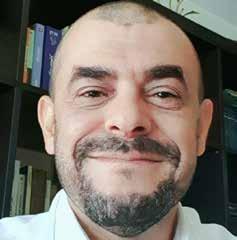
14 minute read
Façades & Skylights (Roofs) in Post-COVID World
FAÇADES & SKYLIGHTS: POST-COVID
Façades & Skylights (Roofs) in Post-COVID World
Advertisement
Ahmad Dalain
Director of Project, Taiyo Middle East LLC
About the Author:
Ahmad Dalain is the Director of Project at Taiyo Middle East LLC, a daughter company of Taiyo Kogyo Corporation Japan worldwide leader in membrane construction and innovation with unprecedented experience since 1929. With 40 companies all over the world, Taiyo is the biggest membrane contracting company in the world. Dalain is a structural engineer with a Master’s degree in structural engineering science, and with more than 22 years’ experience focused on membrane construction innovations in the Middle East and other parts of the world. He is considered one of the few most prominent experts in the field of tensile structures (PTFE, ETFE, PVC, and other innovative materials) in the Middle East with many landmark projects executed under his directions watch, the last of them was the 70m height AL WASL DOME membrane façade at EXPO2020 (The biggest projection screen in the world).
Owners, engineers, and contractors of façades and roofs envelopes shall adapt to post-COVID circumstances. This article addresses the general adaptation of all kinds of construction as construction primary activity and then it will address more focus on lightweight façades and roofs made of the membrane.
INTRODUCTION
Let’s be honest, there is a lot of information about COVID-19 crisis, we have no choice but to filter them out. Our brain typically picks things that are already primed in memory or repeated often in a kind of pattern, i.e. something recently stored in our memory.
E.g., you would recall the 2008 credit crisis or earlier one and predict when the present crisis will finish. That is pattern biased decision because it does not address other important up to date information, or in other words, you have answered health questions by answering a different question about economic recovery. Make no mistakes, COVID-19 is health crisis remember this when you make decisions, other things are symptoms & consequences which shall vanish gradually after reaching terms with health concerns.
According to all concerned entities combating the pandemic, that includes worldwide governments and non-government organizations, apart from vaccine researches, there are so far two main axioms agreed on to form a primary foundation in the post-COVID world aims to curb the virus spread into a declining curve which are the following:
Axiom1: Social distancing in all aspects of life.
Axiom2: Increase hygiene awareness and implement it strictly in all aspects
Above seems few, but they already have had an immense impact on our lives as we knew it, i.e. we went into lockdown, no offices, no meetings, almost stagnant international travel and sometimes local ones, queues grow vastly longer, consumption of hygienic gears skyrocketed.
Obviously, there is a lot to say, however, the scope of this article is to investigate the impact of those two axioms on façades/skylights (roofs) construction industry.
THE ADAPTATION ACTIONS
Straight forward, the construction industry shall adopt the following in general:

PTFE roof in Khalifa new stadium, Doha 2016
Contractors shall revise methods of construction to be shorter in duration with less dependency on manual labour work and enhance the usage of up to date technology plants and equipment. This does not mean we shall lay off manpower completely as this has by far worse impact on society, what is meant here is that part of the work which has been redundantly being done in traditional ways while the up to date technology has a faster and more feasible methods. In other words, the lesser duration of construction is going to be in line with social distancing by simply finish earlier and with a lesser gathering of manpower. Let’s keep in mind that travel restriction is seso-like (on/off) and for an unforeseen period of time.
Designers and engineers shall bear in mind as a top priority the hygiene aspect when selecting materials being used in construction, whether they are helping in easy disinfection or they are harmfully keeping the virus for a long time? The designer’s responsibility shall be extended in selecting smart materials without extra unnecessary heavier weights, abnormal long lead time of procurement, complicated fabrications, or complicated shapes that need an extensive time of coordination. The reason behind that in existing circumstances is very obvious, we shall mind social distancing in all aspects of people’s life, construction personals are no exception, and in addition to that, we shall always aim to finish in shorter durations until we reach terms with health concerns.
Owners shall mind selecting the contractors and designers who do respect the above-mentioned 1&2. In addition to that, perhaps it is making sense to boycott any company that does not respect the main two axioms as this may impact the people who work for that company and therefore ethically not acceptable, add to this, the impact on the job itself as well of contamination.
THE ADAPTATION ACTIONS IN FAÇADES/ SKYLIGHTS (ROOFS) MADE OF THE MEMBRANE
COVID-19 is an unfortunate situation, but ironically the lightweight membrane façades and roofs are simply ticking both axioms outstandingly! Envelopes
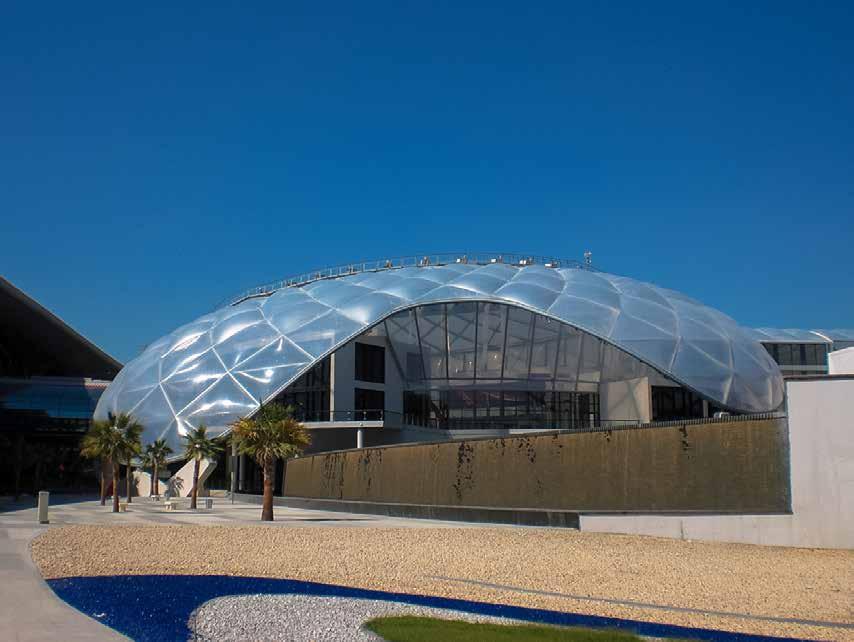
Welcome Pavilion at YASMALL (Abu-Dhabi) - First ETFE project in the Middle East
made of PTFE, PVC, and ETFE are prone to be of the highest interest in the post-COVID world as follows:
The membrane is -by large- light material, E.g. PTFE is 20 times lighter than 6mm Annealed glass, ETFE is 50 times lighter. In order to make this clicks easier in the reader’s mind, take a 45,000 sqm roof made of the membrane, under ideal situation and without hindrances of other trades, the full installation of the membrane can be done within 16 weeks on average with minimal access and lifting equipment comparing to other heavy hard envelopes. As you may notice, that is indeed lined up with the axioms.
That is said, it does not suggest that all kinds of envelopes must be changed to membrane material, there are wide kinds of functions which only hard cladding can play-in, but what is suggested here is to maximise the use of membrane envelopes as much as possible to meet nowadays circumstances in terms of reducing construction duration with minimal access & lifting equipment, as all that pours into social distancing.
Membrane hygiene comparing to other hard cladding materials is very much superior and that is due to its ability to transmit a high range of the natural light spectrum. For example, PTFE translucency varies from 9% to 40%, while ETFE transparency reaches 95%, if clear without frits. The natural light as disinfectant agent is unquestionable, yet in more details, the ETFE, for instance, can pass 95% of the entire natural light spectrum including UV that why it does not only help in maintaining a higher level of hygiene but you can cultivate green plants too. Certainly, skylights, roofs or façades made of the membrane, especially ETFE is second to none when it comes to natural light transmission and accordingly helps in areas enveloped hygiene.
The membranes can easily be coated with selfcleaning films E.g. TiO 2 (Titanium dioxide on PTFE, PVDF on PVC) that helps in easier cleaning and eventually keeps light transmittance levels as desired.
Finally, once again the two axioms sound few, but the extension of their impacts is quite huge. We cannot quarantine all impacts in one article specially that we are still on the learning curve about this pandemic.
PTFE roof at King Abdullah Sports City (Saudi Arabia)
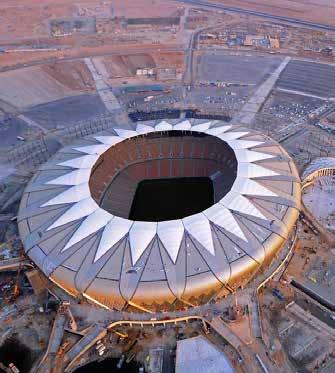
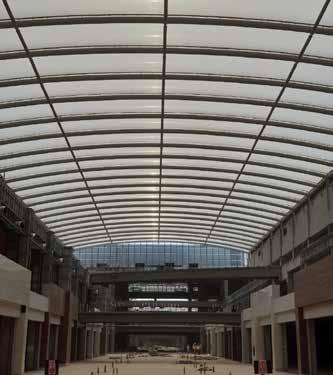
Saudi Arabia Cordoba Mall (Riyadh)- First ETFE skylight
THERMAL TRANSMITTANCE (U-VALUE)
The Real Value of U-Value
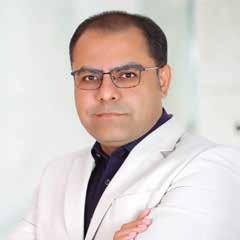
Ashhad Iqbal
General Manager, Knauf Insulation
About the Author:
Ashhad Iqbal is a seasoned professional with an innovative focus on strategy, sales, and marketing of building materials. He has acquired experience through general management and commercial roles for some of the industry-leading companies, covering the Middle East and South Asia. He has conducted complex transformation programs, managed multicultural teams, and ramped-up a successful business. Currently working with Knauf Insulation and focusing on changing the way the market perceives the various products, bringing innovative solutions that demonstrate optimum results.
THE PRICE OF UNDER-PERFORMANCE
The European Commission launched legal action against seven nations, including the U.K. in December, for failing to properly police emissionscheating exposed by the “dieselgate” scandal. In this scandal, car manufacturer Volkswagen (VW) admitted to falsely declare the fuel efficiency and emissions levels of millions of cars between 2009 and 2015. Shortly after news of the violation broke in October 2015, shares in VW plummeted 20%, with a further drop of 17% two days later. VW has since agreed to spend up to $16.5 billion in connection with the scandal, and in November 2016, they unveiled plans to cut 30,000 jobs by 2020 as the repercussions take hold. Although the scandal occurred in the automotive industry and not the construction industry, it raised concerns as to the potential implications of real performance not matching that of designed performance.
SO, WHAT ABOUT OUR BUILDINGS?
Delivering near-zero energy buildings that perform as expected in reality and not simply in design is essential to the entire building industry, from energy efficiency improvements to policy implementation. However, studies carried out by Knauf Insulation in conjunction with leading universities and industry bodies point out that there is often a significant gap between the real performance of our buildings and their designed performance.
THEN WHERE BUILDING DESIGNERS AND SPECIFIERS START IN GETTING THE DESIGN AS ACCURATE AS POSSIBLE?
Arguably the first thing to do is to ensure that the designed energy performance of a building is calculated using the correct methodologies and to the relevant standards. And that starts with the
Delivering near-zero energy buildings that perform as expected in reality and not simply in design is essential to the entire building industry
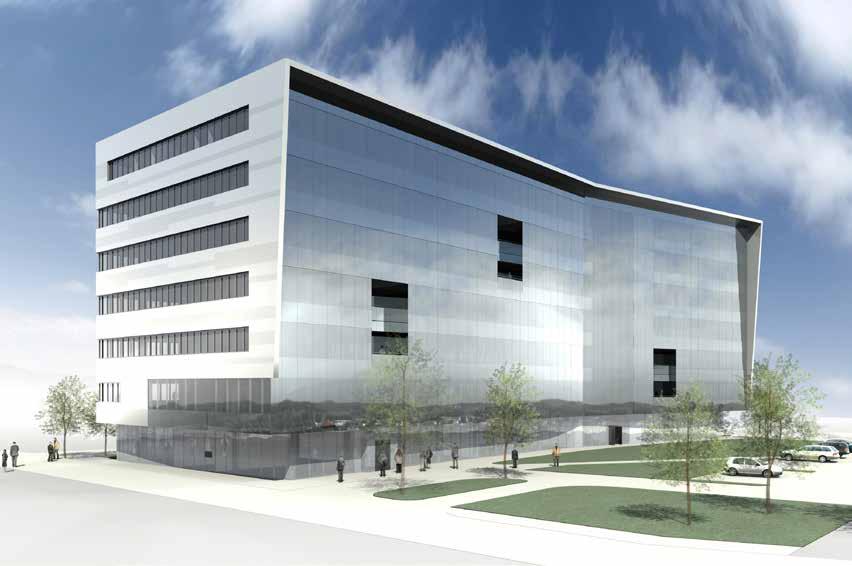
U-values of the building fabric. Standards and regulations in the listed locations and regions were considered for each baseline insulation specification. For Dubai - there is Dubai Green Building Code; for Abu Dhabi - it is Abu Dhabi International Energy Code; for Doha - Karamah Regulations; for Riyadh - the draft Saudi Arabian Standard, SASO and where applicable, ASHRAE Energy Standard 90.1-2013 (for all buildings except low-rise residential buildings) and ASHRAE Energy Standard 90.2-2007 (for low-rise residential buildings); and for Muscat - ASHRAE Energy Standards 90.1 and 90.2 were considered as no local standards are in place..
WHY U-VALUES ARE USED?
The use of U-values allows for the comparison of different buildups for applications, so the insulating properties of a solid wall could be compared to that of a cavity wall, for example, or allow the comparison of two different types of insulation in different thicknesses. U-values are the basic building blocks on which the thermal performance of a building and its associated energy usage is established. A well-insulated building fabric is a key factor in enabling new buildings to deliver their specified energy efficiency.
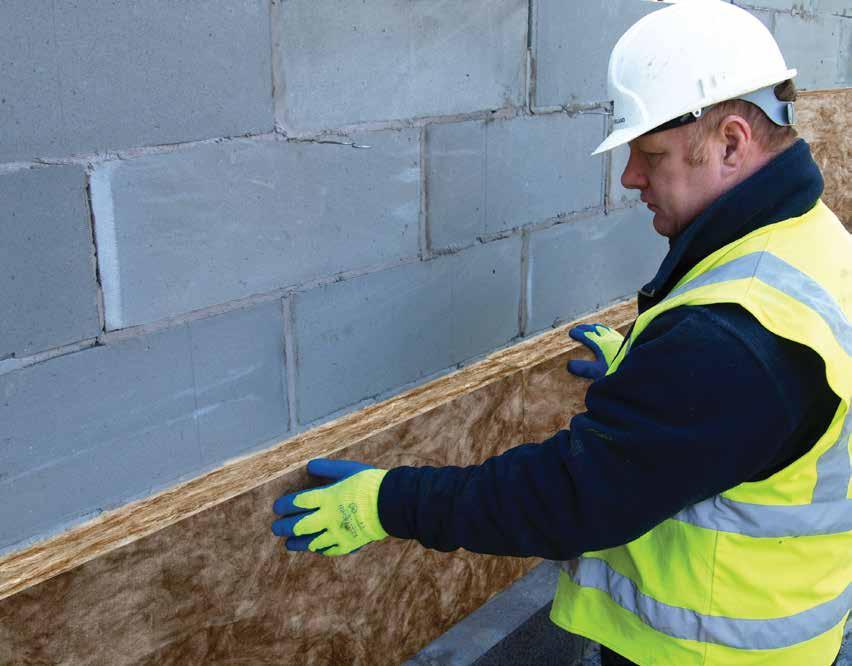
It is the most accurate way of measuring the insulating properties of the application or material and building regulations/standards specify U-values which have to be achieved when building or refurbishing a building. For example, when building in Dubai, a roof in a villa has a recommended best starting point of a U-value of 0.30W/m 2 .K Without knowing the U-value of a wall or a floor or roof, you will not know how energyefficient the whole building will be.
Before you start any building work, you should calculate the U-value as part of the design process to make sure that it meets or is lower than that of the specifications by building regulations/ standards.
For that reason, anyone compiling SAP or SBEM calculations need to be confident that the U-values they are relying on to establish building fabric performance is accurate and correct. It is simple to think that all U-value calculations are created equally and that it can be taken for granted and
they are indeed correct and accurate. However, that may not always be the case. It is crucial to ensure that a U-value provided to a specifier or building designer has been consistently and correctly calculated by a technically competent person employing the correct methodology.
HOW U-VALUES ARE CALCULATED?
To calculate the U-value, you have to start with the R-value or resistivity of the elements that make up the building element that you are trying to calculate the U-value for. The R-value refers to a material’s ability to resist heat transfer at a certain thickness - the higher the R-value the better the insulation material you are looking for.
In its simplest form, a U-value is calculated by establishing the thermal resistance of each layer in the construction element and adding them together to provide a total resistance (TR) value. The U-value is calculated from the reciprocal of the combined resistances of the materials in the element, including any airspaces and surface resistance values.
Taking a standard timber frame wall as an example: TR=Rse + Ra + Rb + Rc + Rd + Re + Rf + Rg + Rsi
• Rse is the external surface resistance
• Rsi is the internal surface resistance
This method of calculating U-values, however, does not allow for non-uniformities that exist in real constructions and therefore will not enable a realistic model to be calculated.
These non-uniformities require factors to include an allowance for the effect of repeating thermal bridges, (e.g. timber studs in timber frame construction, mortar joints in a lightweight and aircrete masonry, or metal rails and clips in twin metal skin constructions), fasteners that penetrate the construction, and the possibility of the imperfection of fit that might allow air movement around insulation layers.
These methods are defined by international standards such as BS EN ISO 6946 (‘Building components and building elements – Thermal resistance and thermal transmittance – calculation method’), and BR443: 2006 (Conventions for U-value calculations).
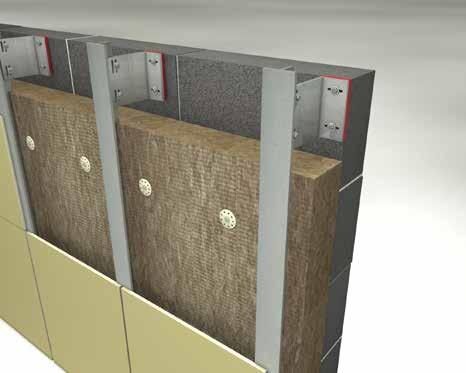
The accurate calculation of U-values is a fundamental building block in the development of whole-building energy models and building regulations submissions
This is the basic formula, and by using this you could work out the U-value for a particular application. However, there are also other factors that need to be taken into account, including thermal bridging factors of fixings or stud work.
When the combined U-value method is applied to the calculation of the U-value of this construction, it becomes 0.26W/m 2 K as opposed to 0.20W/m 2 K if the effect of the timber studs is ignored. In this calculation, the proportion of insulation replaced by timber is 15%.
This proportion is identified as the default timber fraction in BR443, and a level 1 air gap correction has been applied as per guidance given in BR 443:2006 and BS EN ISO 6946:2007 as the insulation layer is penetrated by timber studs. Air gap correction levels are adjusted according to the number of insulation layers, their continuity of contact at butted edge joints in the insulation, and the level of contact with the construction. Mineral wool insulation by way of its nature can be cut such that it fits “snugly” in-between studs and makes good contact with the construction.
A FUNDAMENTAL BUILDING BLOCK
Clearly, the accurate calculation of U-value requires detailed knowledge of product characteristics, calculation methodologies & standards, and construction techniques. The accurate calculation of U-values is a fundamental building block in the development of whole-building energy models and building regulations submissions.
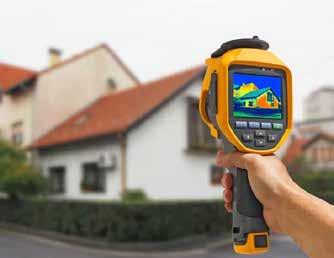
Thermal leak detection U-VALUE & CONDENSATION CALCULATION COMPETENCY SCHEME
This ever-increasing importance of consistent and correctly compiled U-value calculations was recognised by the British Board of Agrèment and the Thermal Insulation Manufacturers and Suppliers Association (TIMSA) in 2010 leading to the creation of an industry-leading U-value and Condensation Calculation Competency Scheme.
The primary purpose of the scheme is to promote and assist accurate, objective, and consistent calculation of U-values and condensation calculations within the construction industry. Membership of the U-value Calculation Competency Scheme provides specifiers and building designers with confidence that the calculations supplied to them are accurately and consistently modelled and is in-line with all the relevant industry standards.
ACHIEVING COMPETENCY STATUS
In order to achieve competency status, a company must have demonstrated appropriate technical competency and have in place a wide range of procedural controls to ensure that the U-value and condensation calculations they supply are accurate and consistent and that there is a clear and comprehensive audit trail in place.
HOW DO SPECIFIERS AND BUILDING DESIGNERS ENSURE THE U-VALUE THEY HAVE BEEN PROVIDED IS ACCURATE?
Recent research suggests that the first port of call for a U-value calculation is to use an online U-value calculator. However, to be assured that the calculations supplied are accurately and consistently modelled in-line with all the relevant industry standards, specifiers and building designers should request that the U-values they are provided with, are calculated by a member of the BBA/TIMSA U-value Calculation Competency Scheme. This gives the designer a reassurance that the calculation is provided after taking into account all non-uniformities and factors which may affect the thermal transmittance of the building element in question. Yes, there is still a long way to go in order to ensure that the real performance of the building matches the designed performance, but using a U-value in which the designer has confidence that can often be the starting point for giving a better chance of the success.