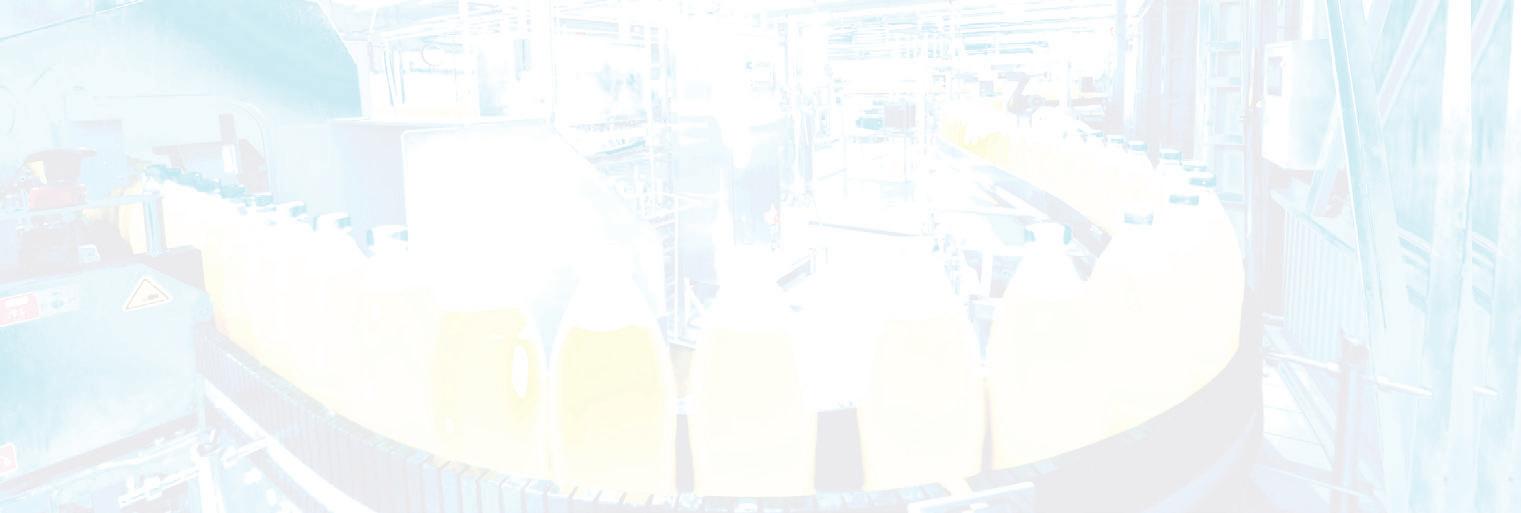
3 minute read
How to stop milk going down the drain
For a typical dairy plant with an intake of around 250 million litres of milk per year, a loss of just 1% of the raw material corresponds to literally throwing about $1.5m down the drain.
With rising inflation and environmental focus, product loss management is more important than ever in dairy plants and other fluid processing plants.
In order to minimise wasting valuable milk products, it is essential to know where in the process the leak happens. If flow rate timings or other sensors and process parameters are not set correctly, valuable liquid product could be washed out with the wastewater.
Finnish company ColloidTek (Collo) has now developed a liquid fingerprint technology that can help address this problem by detecting any type of liquid in the pipes in real time. The technology supervises all draining points in real time, monitoring all liquids in the pipes to show exactly where leakages originated.
Mikko Tielinen, Head of Sales at ColloidTek, said there are several types of traditional sensors needed to detect different types of liquids, such as whey, cream and cleaning chemicals, so optimisation systems have become complicated and expensive to manage.
“Our solution, on the other hand, offers an easy and very accurate way to detect where exactly in the process the leakage is,” Tielinen said.
“It measures the exact real-time liquid fingerprint at any desired point in the process with a single EMF-sensor. Combined with machine learning, our solution ensures that the process stays optimised and easily monitored through our cloud solution.”
Usually, product losses in the process are noticed when there is an excess of organic material in the effluent. This can also be a sign of problems in the production; however, measuring just the effluent does not tell why, and from where too much milk product is getting flushed out with the wastewater.
In order to minimise wasting valuable milk products, it is essential to know where in the process the leak happens.
“As our technology can supervise all the draining points in real time, it can keep track of the liquids in the pipes and show exactly where the leakage is,” Tielinen said. “This makes it possible to address the problem at the point of origin, saving huge amounts of milk and money.”
In addition to directly improving the profitability of a dairy plant, reducing the milk waste also lowers the cost of wastewater treatment and helps dairies to achieve their environmental goals.
“Most of the carbon dioxide generated in a dairy production originates from the stages before the milk even arrives at the dairy,” Tielinen said. “That is why it is essential to not waste valuable milk in the dairy’s processing operations. If milk-based products are lost in a dairy, a replacement amount of milk will have to be produced and transported to the dairy, which will produce even more carbon dioxide emissions.”
Drive solutions for beverage bottling
Automatic bottling and conveyer systems in beverage and liquid food production set high requirements for energy efficiency, operational reliability, washdown capability and corrosion protection. NORD Drivesystems can provide suitable hygienic solutions for bottling and conveyor technology in beverage lines.
Drive systems used in automatic bottling systems for the beverage industry must reconcile various requirements. The DuoDrive geared motor integrates an IE5+ synchronous motor into the housing of a single-stage helical gear unit, with a system efficiency of up to 92%. The constant motor torque over a wide speed range allows for consistent version reduction and reduction of operating costs. Together with the plug-and-play commissioning, this is designed to reduce total cost of ownership. It contains an unventilated, washdown design with smooth surfaces to meet hygiene requirements and ensure cleaning.
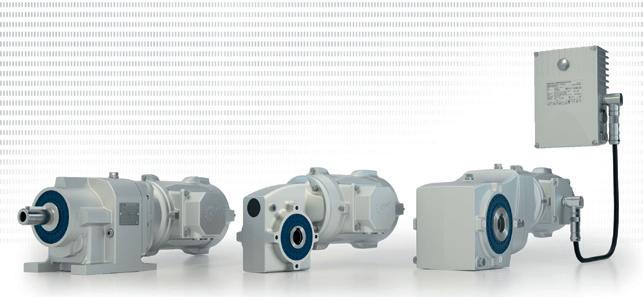
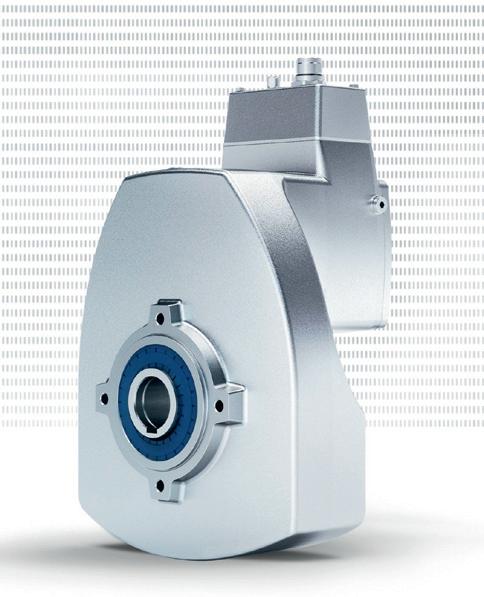
Beverage bottling is an area where the demand for decentralised drive technology is on the rise. NORDAC ON/ON+ covers power ranges up to 2.2 kW and is characterised by an integrated Ethernet interface (Profinet, EtherNET IP and EtherCAT can be set per parameter), full plug-in capability and a compact design. Decentralised inverters are ideally suited for integration into bottling and conveyor systems and can save space as well as the extensive motor cable wiring required for centralised frequency inverters.
The nsd tupH surface treatment provides a good anti-corrosion treatment for drive components in washdown-optimised cast aluminium housings for the beverage industry. The surface treatment is available for DuoDrive, NORDAC ON/ON+ and most NORD modular drive systems made from aluminium. Using a special method, the surface is made corrosion-resistant and harder, and is claimed to make aluminium behave like stainless steel with regard to corrosion protection. It is not a coating, but a surface treatment which creates a protective layer that bonds to the substrate material. The drives are made to be easy to clean and largely resistant to acids and alkalis. It is possible to use high-pressure cleaners or apply aggressive media.
NORD Drivesystems (Aust) Pty Ltd www.nord.com
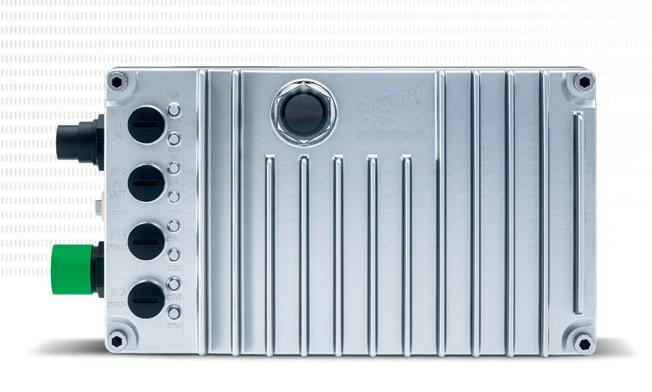
Packaging coatings
AkzoNobel Packaging Coatings has revealed its next-generation product portfolio to distinguish its new BPA-Ni and NexGen coatings from its legacy products.

The move will support the transition away from coatings based on legacy technologies like epoxy and vinyl, towards technologies that comply with incoming regulations by the European Food Safety Authority (EFSA), FDA and other regulatory bodies. Beverage coatings will become Accelshield and Accelstyle for internal and external coatings respectively. Both will feature products that remove various materials such as BPA and other bisphenols, phenolics, PFAS, formaldehyde and Styrene. Similarly, food packaging coatings will become Securshield and Securstyle for internal and external coatings respectively.
AkzoNobel Pty Limited www.akzonobel.com