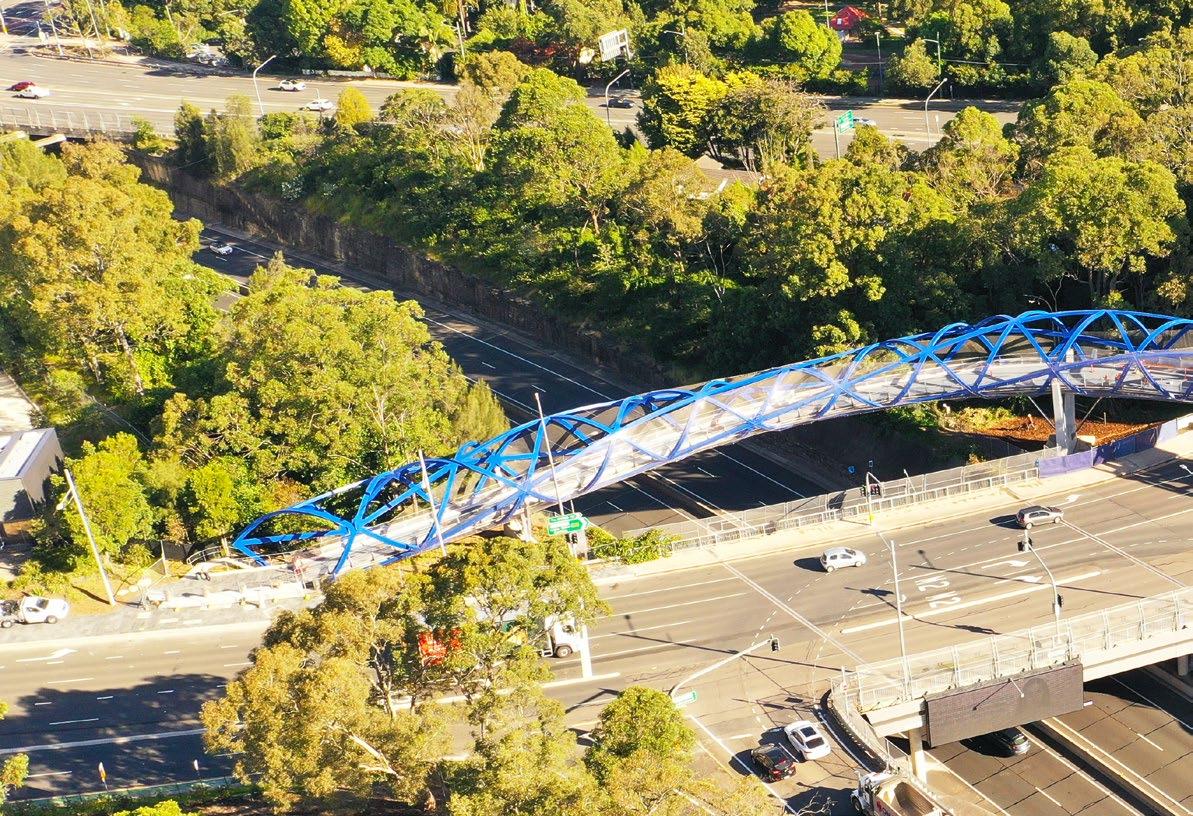
11 minute read
Australia’s First Double Helix Bridge Now Open
The $40 million Lachlan’s Line pedestrian and cycle bridge is a first of-its-kind—an organic, double helix bridge. It connects Landcom’s new Lachlan’s Line Residential Precinct on its western extremity, to the North Ryde Commercial Sector and Metro Station on its eastern extremity. Bold and bright blue, the bridge is a striking visual landmark, as well as a busy active transport connection. The bridge has transformed access to the Lachlan’s Line site, which is bounded by one of Sydney’s busiest intersections, that of the M2 Motorway and Delhi Road.
Advertisement
Commissioned by Landcom (the New South Wales Governments’ development agency), the Lachlan’s Line bridge project was delivered by a joint venture between Daracon Group and Arenco, designed and engineered by Arup and KI Studio, and fabricated by Weld Australia member, S&L Steel.
The Design
At 178m in overall length, the Lachlan’s Line bridge is a variable diameter helical steel truss bridge, curved in plan. As reported by This is Construction, it is the first double helix bridge in the world to have a variable diameter, which increases in size over the supports (where bending moments are higher) and narrows midspan (where moments are lower). These eye-catching curves and unique features were not designed purely for looks, but were required to meet the site constraints.
"The double helix and sinuous design was actually derived from the structural parameters, not primarily for aesthetics, as it may first appear" said Andrew Johnson (Principal and Project Director, Arup).
The bridge alignment – defined by the minimum feasible length and pier locations - dictated a sinuous structural form.
The use of curved plate fabricated box sections was also more than an aesthetic choice: it enabled each side of the section to be optimised with different plate thickness, responding to section and structural demand, which simply would not have been possible with tube sections. It also means that each of the steel plates is no thicker than required at any point, reducing steel consumption, as well as excess weight throughout the structure.
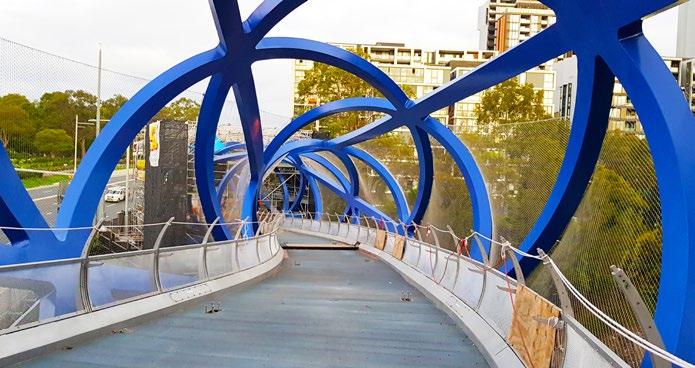
“The curved, fabricated box section construction elevates helix design and fabrication to a new level, combining sharper surfaces with fluid geometry, enabled by Arup’s digital approach through both design and delivery phases,” said Johnson.
The diameter of the bridge was adjusted to achieve greater structural depth at locations of higher demand, as opposed to increasing material use at a shallower depth. Robust materials and finishes, the use of closed structural sections and smooth connections between elements minimises maintenance and ensures long-term durability.
The Arenco Daracon Joint Venture was responsible for the novated design and construction of the new bridge. According to Phil Douch (Engineering Manager, Arenco), “We novated the design from Landcom at 85 per cent, which was undertaken by Arup for the structural works and KI Studio for the architectural features.”
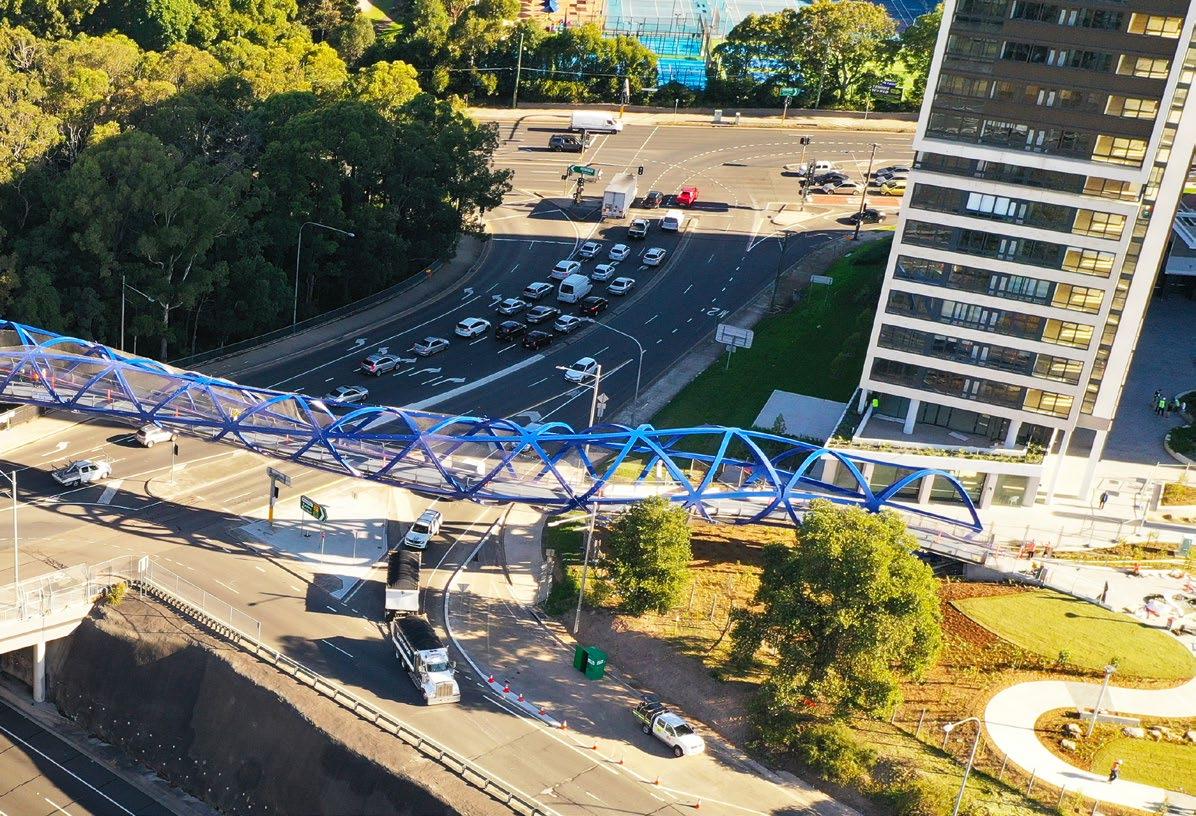
The Fabrication
Of all the 3,600 steel plates used to fabricate the 335 tonne structure, no two are alike – every piece of steel has a different curvature, and the helix varies 2.3m in its diameter in relation to the structural demand. Every member is unique in shape and plate thickness. This made for a complex fabrication project for Glendenning-based steel fabricator, S&L Steel.
Fabricated from 350 tonnes of locally produced structural mild steel and 170 tonnes of high grade imported Duplex 2205 stainless steel, the bridge comprises four segments, with a maximum span of 50m.
The substructure comprises reinforced concrete abutments and three piers, each in turn supported on bored reinforced concrete piles. Bridge approaches to both ends are landscaped and paved, all in keeping with the free-flowing theme of the structure.
The steel superstructure consists of 78 chord members, 160 diagonal members and 82 connecting nodes (320 members in total), creating a singular longitudinal truss arrangement. The fabrication of each member required individual cutting to size and bending of approximately 4,000 flat steel pieces prior to welding to form the individual box shaped members. Over the course of approximately 100,000 manhours, S&L Steel completed approximately 14km of welding.
According to Javier Lorenzo (Director, S&L Steel), given the unique nature of the project, it posed some challenges for S&L Steel. “Early on, our biggest worry was getting the radius of each piece correct. That was difficult for us, but we worked out a strategy that allowed us to maintain the shape of the box as we built and welded it. All the pieces had to be rolled, and sometimes during welding, pieces lose their shape. To overcome this, we had to hold down the pieces with smaller jigs.”
The Trial Assembly
Prior to the on-site erection, members for each segment were trial assembled in S&L Steel’s workshop using specially designed support jigs, tack welded in position and surveyed to verify dimensional accuracy. “We have a lot of space in our yard. In fact, I believe we have one of the largest fabrication facilities in Sydney. This affords us the ability to undertake large-scale projects such as Lachlan Bridge. For this project, we felt that the more work we could do in our workshop, the more advantages it would afford the siteworks. So, we basically replicated the entire site and bridge in our yard prior to erection. The only thing we didn’t do in our workshop was fully weld the bridge,” explained Lorenzo.
“The purpose of the trial assembly was to ensure all the pieces fit together exactly. This was particularly important, given that no two pieces on the bridge are the same. If we’d craned a piece into position on-site, and then it didn’t fit, we’d have had to re-crane it the following night, causing major delays.”
Douch was equally as adamant about the importance of the trial assembly. “The trial ensured that we had all the tolerances correct. Everything was cloud point surveyed, and the segments were all joined to make sure they aligned with one another. This was all completed in the precambered state, through models. When we did the trial assembly in the workshop, we had three fully assembled units. All of these units were checked, surveyed and ticked off, before being broken down into pieces and then transported to site,” said Douch.
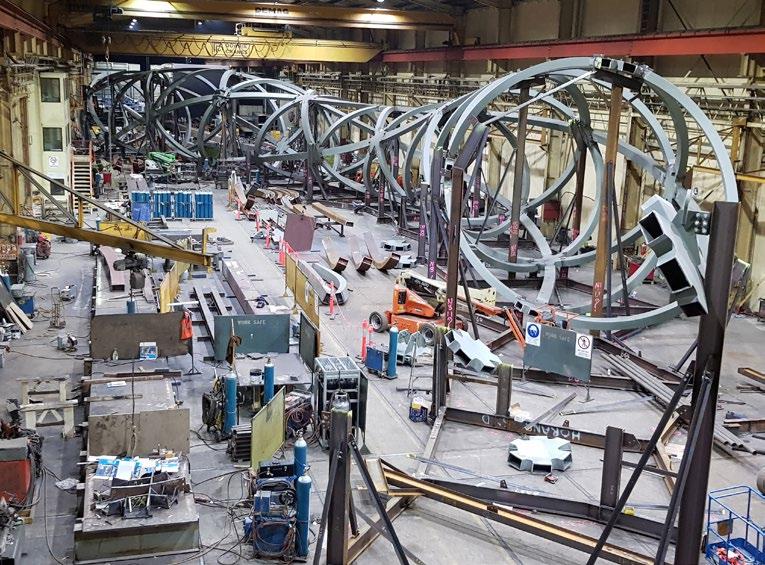
“Of all the 3,600 steel plates used to fabricate the 335 tonne structure, no two are alike – every piece of steel has a different curvature, and the helix varies 2.3m in its diameter in relation to the structural demand. Every member is unique in shape and plate thickness. This made for a complex fabrication project for Glendenning based steel fabricator, S&L Steel.”
From there, the segments were dismantled, grit blasted and painted for delivery to the purpose-built site fabrication facility. There, they were reassembled using the same support jigs that S&L Steel relied upon during the trail assembly, and then fully welded while again being surveyed for dimensional conformity.
All of the decking elements were fabricated entirely off-site, prior to delivery and fixing into each segment. Paint touch-up was completed concurrently, and tensile stainless steel mesh protective screens enveloped the external form.
As one segment was completed, S&L Steel began the adjoining segment, replicating the same process, while ensuring the splice connections between adjoining segments matched perfectly.
The Lifting Process
Arenco undertook extensive planning with the New South Wales Government’s Transport Management Centre for all four segment installations to understand and mitigate the effect each would have on the Sydney traffic network.
The key objectives were the absolute minimisation of impacts on traffic and the community. Traffic engineers prepared detailed analyses to assess projected traffic queuing and compare potential traffic detours. This process was a balance between traffic optimisation and mandatory construction aspects, including personnel safety and bridge installation complexity.
Using limited road closures, the four individual bridge segments were successfully erected into position using a single crane lift methodology. The heaviest lift was Segment Two with a gross lifting weight of 135 tonnes involving a 600 tonne crawler crane and closure of both Delhi Road and the M2 Motorway.
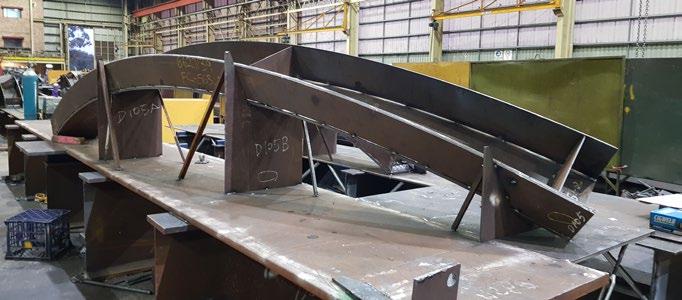
Diagonal being assembled in jig.
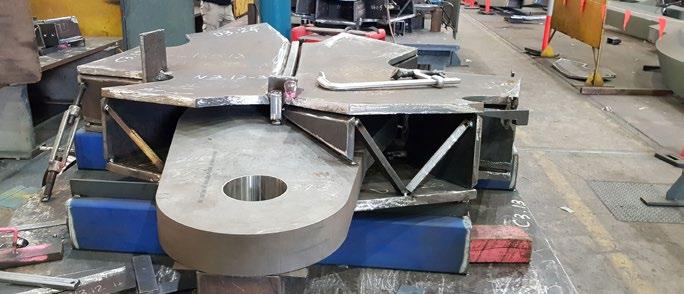
Assembley of node with pier connection.
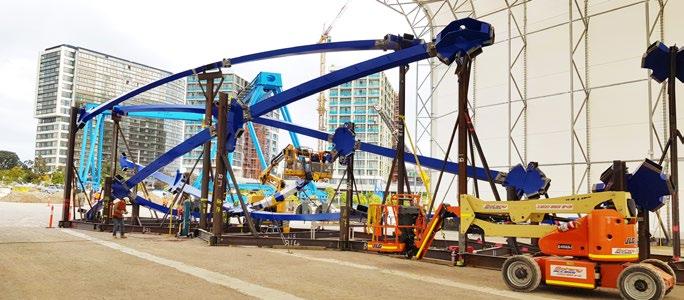
Segment assembly on-site. .

Segment One being prepared for erection. .
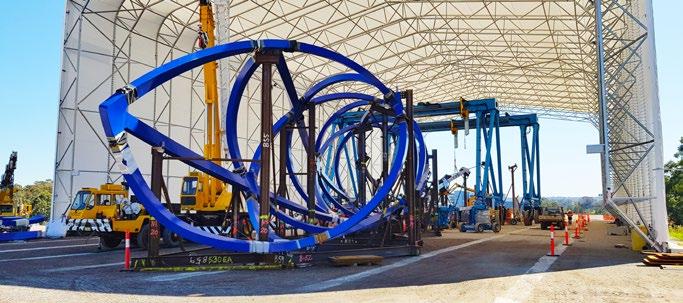
Assembly of Segments One & Two on site
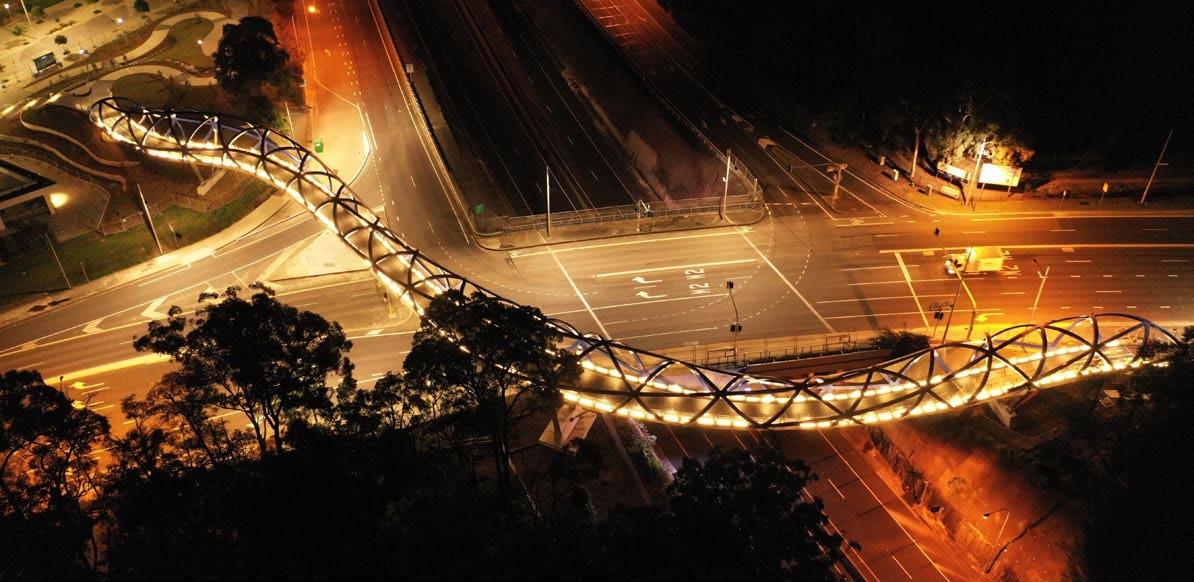
Lachlan's Line bridge will be a striking visual landmark, as well as a busy active transport connection, for years to come
According to Douch, “When Arenco took on the project, the design didn’t have any way of being lifted into place. So, in the early stages, we worked out how we were going to lift it. We agreed on four segments, each with four lifting points.”
“All the lifts were completed over weekends and at nights to minimise the amount of time roads were closed,” said Douch.
Segment Two, which was largest segment weighing in at 110 tonnes, was erected on 28 December to capitalise on the quieter traffic over the Christmas and New Year period. Even then, Arenco worked to ensure that the M2 was closed for as short a period of time as possible.
“During the lift of Segment Two— which was the largest segment— the M2 was only closed while the segment was slewed over the motorway. Throughout the set up and pack up of the crane, the motorway remained operational. We originally planned to close the M2 for 40 hours, but only needed to close it for 15 hours in the end,” said Douch.
The Erection S&L Steel was heavily involved in the erection process. “Our job was to transport each segment approximately 300m from the site shed to the site. The segments were gigantic to be travelling along a road – it was quite an impressive sight. On most jobs, we would have transported the segments from our factory in Rooty Hill to the construction site but it simply wasn’t possible for this project,” said Lorenzo.
“The segments had an 8m radius, which meant they were too large to transport along the M7 Motorway— they would have knocked out all the overhead bridges. That’s why the decision was made early on to build a workshop on-site, so we could finish the job over there.”
Each segment was lifted out of an assembly jig at the on-site factory, and onto transport frames. “The transport frames suspended the segments, almost like a mini crane lift itself. Then the segments were transported into position to be lifted by the crane,” said Lorenzo.
As Douch explains, the lifts themselves were no mean feat. “When we lifted the segments, because of their unusual shape, we used a synchronised lifting system. This was a bit like a hydraulic jack at the end of each segment. We were then able to rotate the segments as we picked them up from the transporter—tilting them from the horizontal position to match the grade of the bridge.”
“A lot of the segments had to be lifted higher or lower than the last to suit the site constrains. For instance, Segment Two clashed with Pier Two, so it was lifted in higher at one end and then rotated into place,” said Douch.
Lorenzo explained further. “When Segment Two was craned into position, because of the shape of the structure, it forced the end of Segment One to point up into the air. The segment didn’t rest in its final position—it flexed. The crane had to be fitted with hydraulics so that segments could be manipulated while in mid-air—twisted and tilted so that the two connecting plates of the pieces fitted exactly,” said Lorenzo.
Once each segment was erected, it was bolted onto the adjacent segment, and sat on a pier as a temporary support. It was only then that the crane could be released, all the joints welded, and the bolted sections cut off, so that the segment was fully self-supporting.
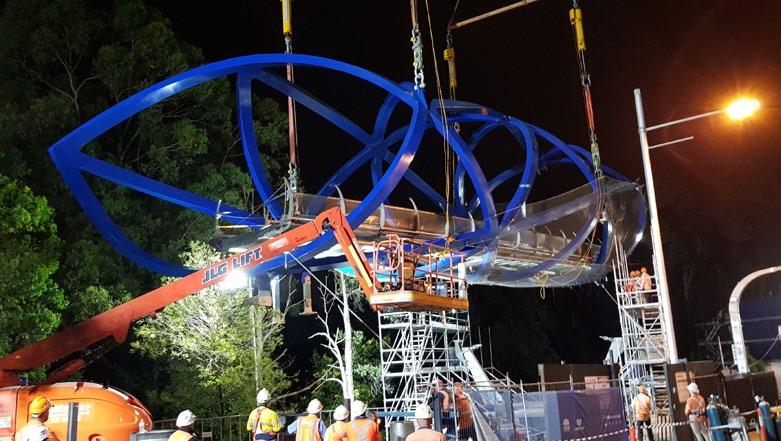
Erection of Segment One takes place
The Outcome
The end result is a truly remarkable feat: bold and bright blue, Lachlan’s Line bridge will be a striking visual landmark, as well as a busy active transport connection, for years to come. As such, it is little wonder that the project stakeholders were so keen to be involved.
Lorenzo’s enthusiasm and excitement was clear. “You just have to look at the design—the first reaction is always ‘wow’. We knew it was going to be hard work, but now that the bridge is finished, it’s clear that it is an iconic project. People are going to wonder how we managed to build it for years to come.”
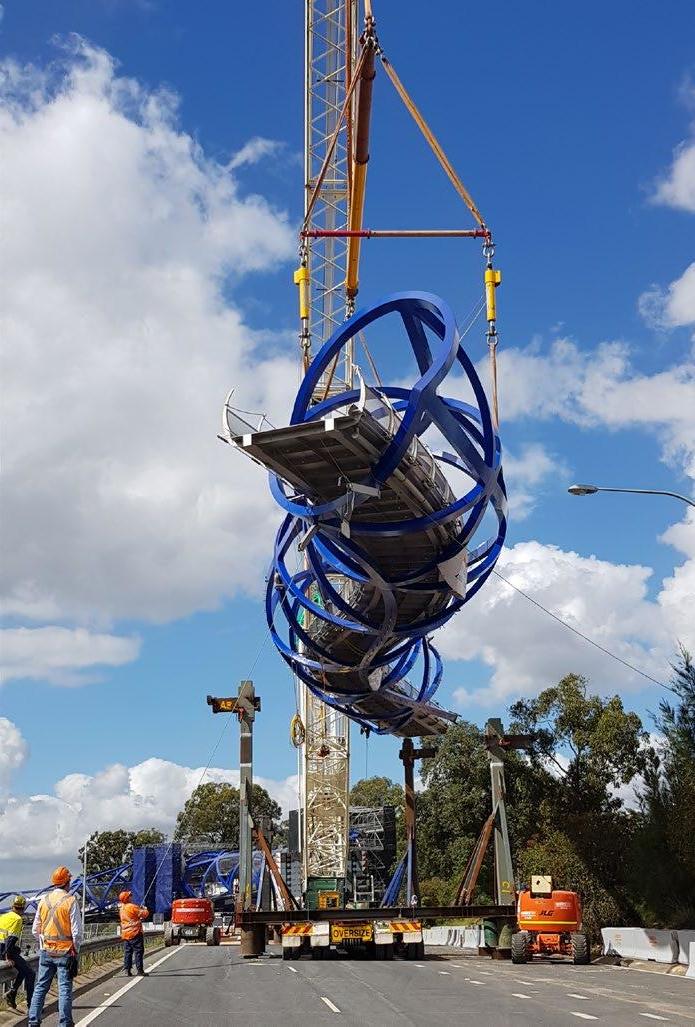
Segment Four is lifted out of the transport frames
“As soon as I saw the design, I went looking for projects and bridges that are similar. There’s a similar bridge in Singapore, but when you look at it in detail, the Lachlan’s Line bridge is considerably more difficult. The bridge in Singapore is constructed using rolled members—we had to fabricate physical boxes.”
“There are other helix bridges all around the world, but Lachlan’s Line is snake shaped – it’s like a worm, where it gets fatter and skinnier. There is simply no other bridge in the world like it,” said Lorenzo.