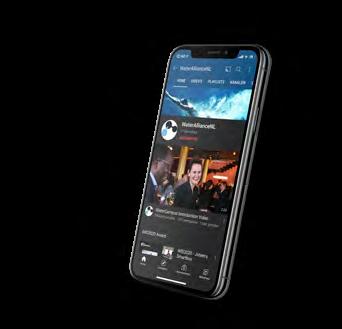
12 minute read
Short Cuts
NEWS FROM THE AROUND THE WORLD OF WATER TECHNOLOGY
WaterProof TV: Subscribe now!
Advertisement
Scan this QR code and get access to amazing content!
BERGHOF MEMBRANES AND AQUAPORIN WELCOME WAFILIN SYSTEMS IN JOINT MEMBRANE VENTURE
In order to collect testimonies to their new, jointly developed Berghof Hyperflux(TM) and Aquaporin Inside® food-ready Tubular Forward Osmosis (Food TFO) membranes and ultimately commercialize them, Berghof Membranes and Aquaporin are welcoming Wafilin Systems in a strategic alliance.
Berghof Membranes (member of Water Alliance) is a leading German manufacturer of tubular membranes for the filtration and separation of process streams and wastewater. Aquaporin is a Danish water technology company specializing in biomimetic membranes. Both companies have worked intensively in the field of tubular forward osmosis for a long time. The latest Food TFO membranes are developed to comply with food contact material regulations, thus making them suitable for use in food and beverage processing to concentrate food products at lower temperature, with less energy, and improved product quality. In order to align their technology even more successfully with market needs and commercialize their solution, Berghof Membranes and Aquaporin have decided to add Wafilin Systems (also a member of Water Alliance) to their strategic alliance. “We firmly believe that the Food TFO membrane we have developed with Aquaporin provides unique benefits, especially for the food and beverage industry”, says Berghof Membranes’ Managing Director Eric Wildeboer. “Therefore, we are happy to have Wafilin Systems onboard and look forward to strengthening our commercial efforts and making our technology even better by using the testimonials and experiences that Wafilin Systems will collect from customers.”
Wafilin Systems is a renowned membrane applications specialist that, for several years, has been successfully focusing on the food and dairy industries where forward osmosis technology is particularly beneficial.
Evaporation, which has frequently been used up until now to process food and beverage products, not only requires a great deal of energy, but also evaporates valuable aromas, flavors, and nutrients, while concentrating on forward osmosis is efficient in terms of energy and costs without compromising quality
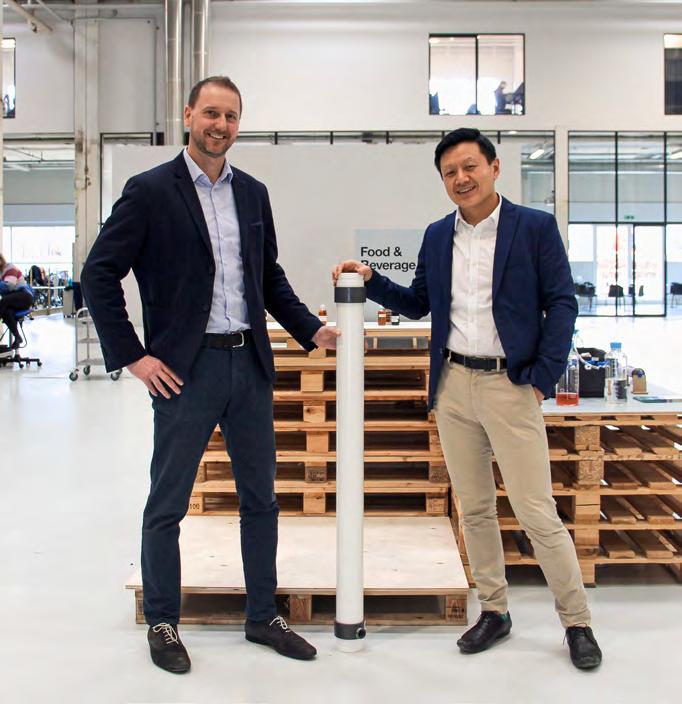
Matt Boczkowski, CEO Aquaporin and Yunfeng Li, Commercial Director F&B Aquaporin.
SHORT CUTS
NEWS FROM THE AROUND THE WORLD OF WATER TECHNOLOGY
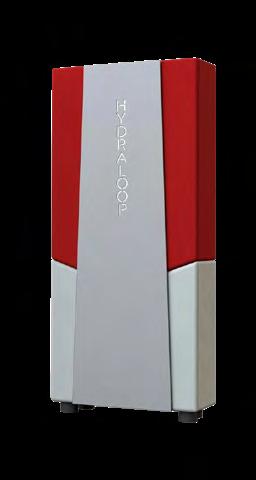
and taste. Thanks to the product quality being preserved during concentration, logistical and sustainability benefits can also be explored.
“We are pleased to welcome Wafilin Systems to our close collaboration with Berghof Membranes”, says Matt Boczkowski, Aquaporin CEO. “The goal of this expanded team is to utilize each other’s strengths to deliver a tailor-made solution to the food and beverage industry. With our solution, food and beverage manufacturers can offer innovative products while reducing their carbon footprint and optimizing transportation costs thanks to significantly reduced volumes.”
MORE NEWS ON WAFILIN SYSTEMS
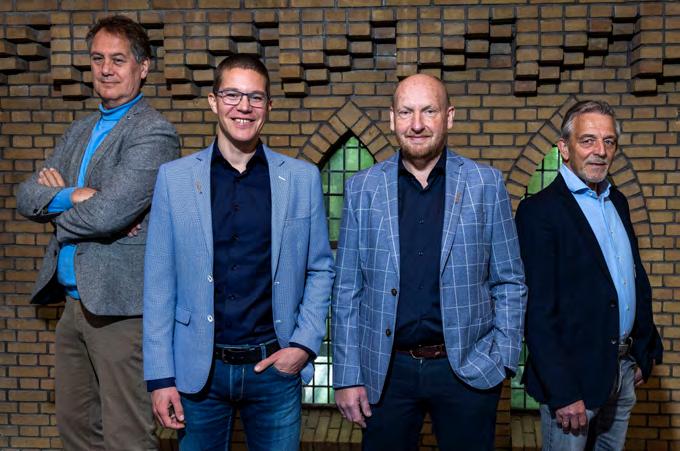
from left to right: Erwin Dirkse, Jos van Dalfsen, Henk Schonewille, Harry van Dalfsen
In April it was announced that Jos van Dalfsen, together with Henk Schonewille, will form the new Board of Directors of Wafilin Systems. Over the coming months, Harry van Dalfsen will hand-over his operational role to his son Jos and will take on an advisory role within the company. Wafilin System also welcomes Erwin Dirkse as new shareholder and, together with Harry van Dalfsen, he will take a seat on the Advisory Board. Jos van Dalfsen has been R&D Manager at Wafilin Systems since March 2018. He is looking forward to this new challenge: “Over the past couple of years, we have experienced strong development and growth. Developing unique applications that contribute to the optimization of and making the Food and Dairy industries more sustainable is incredibly inspiring. In my new role, I want to focus on continuing and rolling out our mission and strategy together with our team; that is a fantastic challenge”.
HYDRALOOP SCORES WITH CROWDFUNDING
Hydraloop, a member of the Water Alliance, is maintaining strong growth. From its headquarters at WaterCampus Leeuwarden, the company aims to make the world more sustainable with an innovative, in-house water recycling system that collects, cleans and disinfects water from showers, baths and washing machines. The water can be reused for various purposes such as flushing toilets, washing clothes and gardening. Funding for international expansion was raised through the UK platform Crowdcube. Hydraloop’s proposition struck a chord. Its initial target was 3 million euros, but it raised 4.5 million euros from 1,300 investors within just a few days. Part of the plan for international expansion is to establish factories in several countries outside Europe to assemble water-saving systems. Hydraloop focuses on numerous countries and target groups, but new construction projects in dry countries with water scarcity are of particular interest. In 2018, Hydraloop won the WIS award, Water Alliance’s innovation award. The company went on to win various international awards and frequently made international headlines.
EMI TWENTE EXPERT IN MEMBRANE TECHNOLOGY
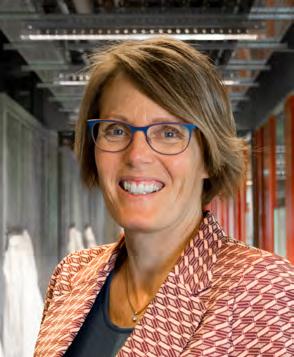
EMI Twente offers research and testing to support companies with membrane development and application-related challenges. That can help companies take a big step in the valorization process. “Membrane technology is increasingly becoming a key technology for many markets”, says business developer Heleen Sombekke. EMI Twente originated from the Membrance Science & Technology cluster at the University of Twente. ‘We bring the commercial application of an idea
Heleen Sombekke closer’
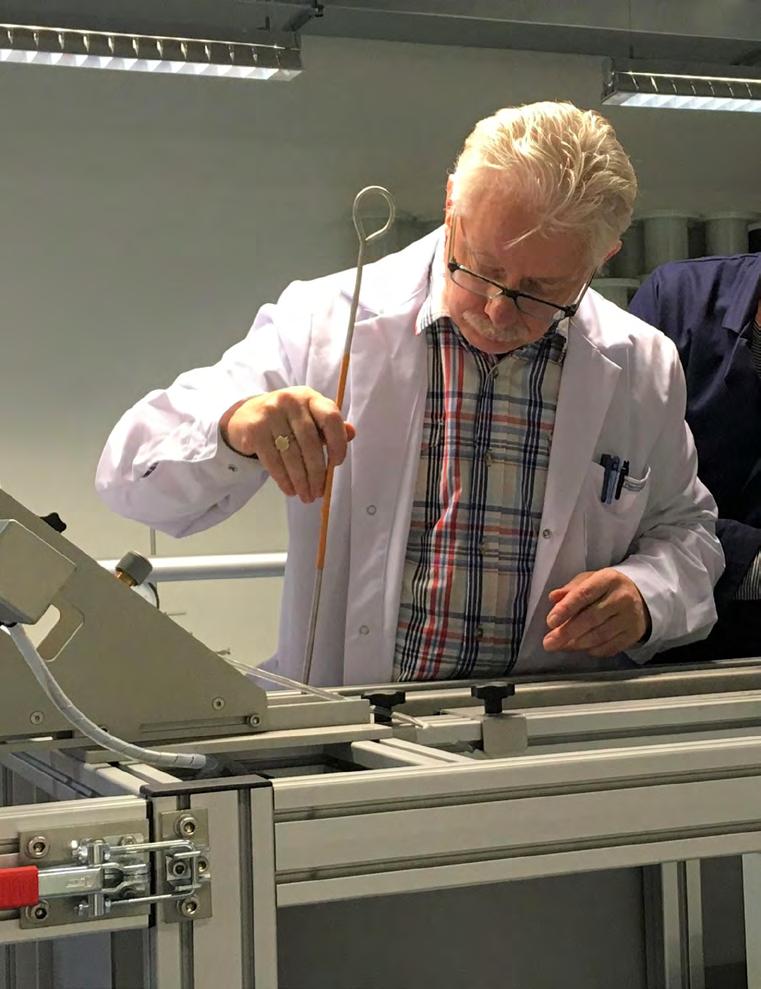
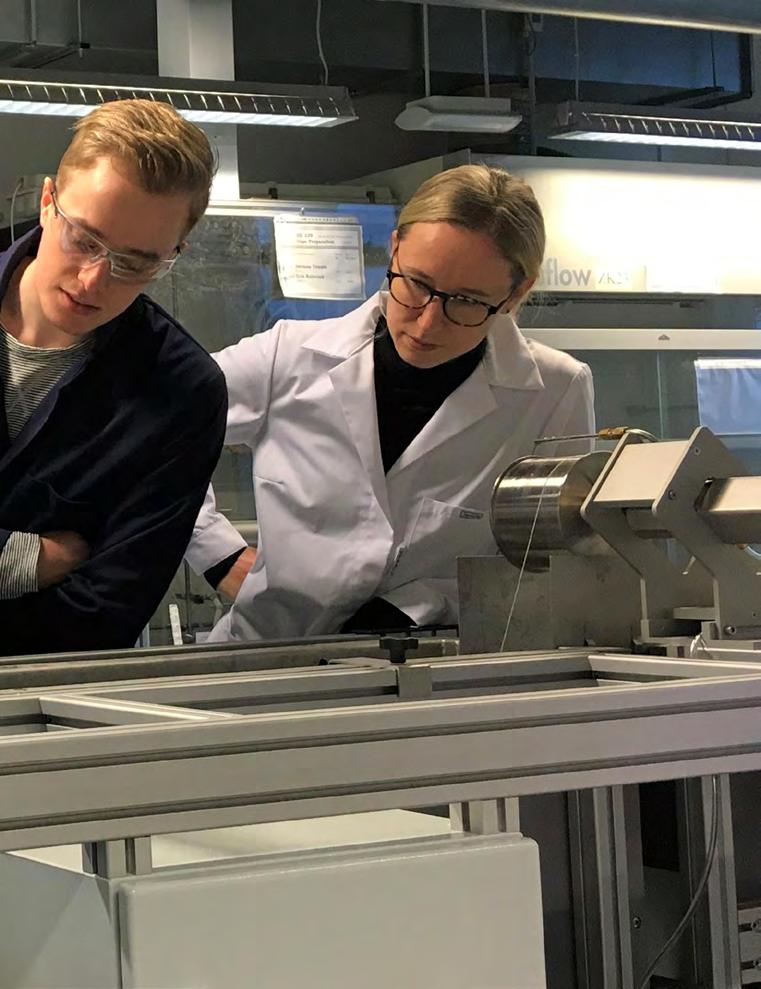
“For a university, research usually stops at Technology Readiness Level 2: research into the innovative nature of an idea and the basic principles of innovation”, says Sombekke. “We go further than that. Our activities run up to level 6, which involves the extensive testing and demonstration of a concept in an appropriate test environment. The test environment resembles an operational environment that meets industry requirements, after which companies can scale up to commercialization. “We bring the commercial application of an idea closer.” The Technology Readiness Levels Heleen Sombekke mentions were once devised by NASA to indicate the development stage of new technology. Many European and national grants use this model to indicate the phase of an innovation process for which a grant is intended.
Challenges
EMI Twente develops a wide variety of membranes—from polymeric and ceramic to hybrid membranes— for clients in various industries, including the chemical and petrochemical industry, the water sector (wastewater & drinking water), agro & food, healthcare, and energy production & storage. In addition to developing new membranes, the organization works to improve existing membranes, consultancy and application studies. “Say a company has a membrane for hydrogen electrolysis, for example, and they want to know if the membrane is suitable for other applications”, says Sombekke regarding those improvements. “We investigate whether those opportunities exist.”
According to Sombekke, there are an increasing number of application areas where membranes provide good functionality and benefits over traditional separation techniques. This includes challenges in areas such as water and energy. “Water includes the water cycle, resource recovery and energy production from wastewater. Energy challenges include energy production such as fuel cells and batteries, the electrification of the chemical industry and efficient energy use. Membranes are an excellent option for all these areas. Membranes are also often more favourable than traditional separation techniques, such as distillation, from an energy consumption point of view.”
Making a difference
The EMI Twente team consists of fifteen people. Sombekke is enthusiastic about her colleagues. “We have a fun and inspiring team comprised of various nationalities, with knowledge and experience in almost all sub-fields in membrane technology. Since EMI Twente’s inception in 1995, we have completed hundreds of assignments for a wide range of primarily industrial clients.” When asked what part of her job she enjoys most, Sombekke doesn’t miss a beat. “A client who says, ‘you really made a difference.’ That may seem logical and obvious, but make no mistake: that pat on the back, that thumbs-up, has to be earned every time. It’s about making the most of our combined ability for the customer. I also like that, in this profession, you are dealing with content-driven people and working on something that matters— something good for people and nature.”
tanning technology: fish skins as raw material for leather production
Searious innovates in tanning fish skins
A FACT: THE SKIN OF FISH SUCH AS SALMON, COD OR HADDOCK IS AN EXCELLENT RAW MATERIAL FOR SUSTAINABLE LEATHER PRODUCTION. SEARIOUS, BY ENTREPRENEUR FOLKERT FENNEMA FROM BEETGUMERMOLEN (BASED IN LEEUWARDEN), HAS DEVELOPED A TANNING TECHNOLOGY WITHOUT CHROME, BRINE OR FUNGICIDES. IN COLLABORATION WITH WATER TECHNOLOGY COMPANY CIRTEC FROM PURMEREND, HE ALSO EXTRACTS REUSABLE WATER FROM HIS WASTE STREAMS.
Fish leather is nothing new—it has been around since humans began eating fish. However, by sustainably producing fish skin as a raw material and using it for leather products, it is no longer necessary to breed exotic animals, such as snakes, to that end. Fish skin is a byproduct of fish produced for human consumption anyway. Through its collaboration with CirTec, Searious can now also recycle the water used during the production process. The collaboration has only just begun; the two parties signed an agreement during the Aqua Nederland trade show in March of this year. “It is a great use of a residual product”, Fennema said. “I use the skin of fish that are consumed anyway.
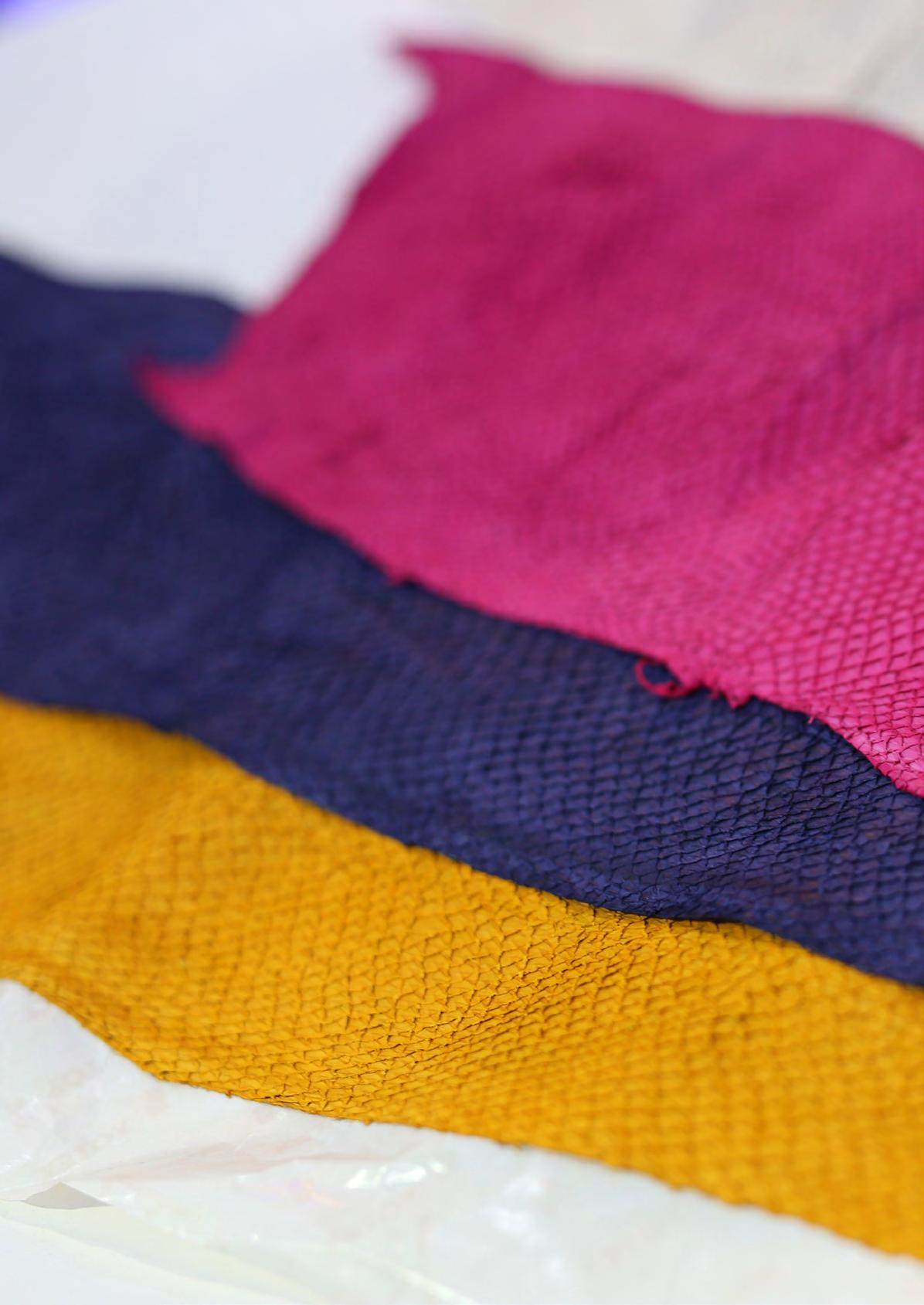
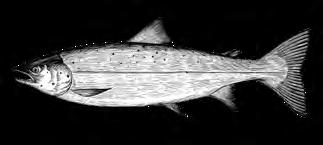
fig. a: Atlantic Salmon Tanning is a discipline in its own right. I produce leather by cleaning the skin, removing the scales, and filling it with a tannin. The result is a highly supple and strong piece of leather. That can be dyed in all sorts of colors, but I don’t do that; my products go directly to the fashion industry in Italy.” Fennema sees other benefits of his method: “I tan without using chromium, brine or fungicides, so it’s sustainable. However, I did have wastewater, and I wanted to do something with that. That is where CirTec comes in.” “I wouldn’t call it wastewater, but rather residual streams”, says Coos Wessels of CirTec. “We work with those residual streams. We extract the water from the residual stream, which can be reused at the beginning of the tanning process. It is a circular system.” There is still plenty to be done to market the idea en masse. Searious plans to build a prototype plant at its Leeuwarden location with all the process steps integrated on a representative scale this year. The project started in late 2021 and will be completed by mid-2023. The final plant will be completed shortly thereafter. Fennema: “I expect it to be widely adopted by the market within two years.” Searious BV has received grants from VIA Ontwikkelingsprojecten 2021 and the EFRO fund for the development of the prototype plant.
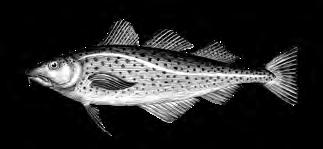
fig. b: Atlantic Cod Fish fig. c: Haddock
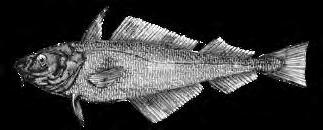
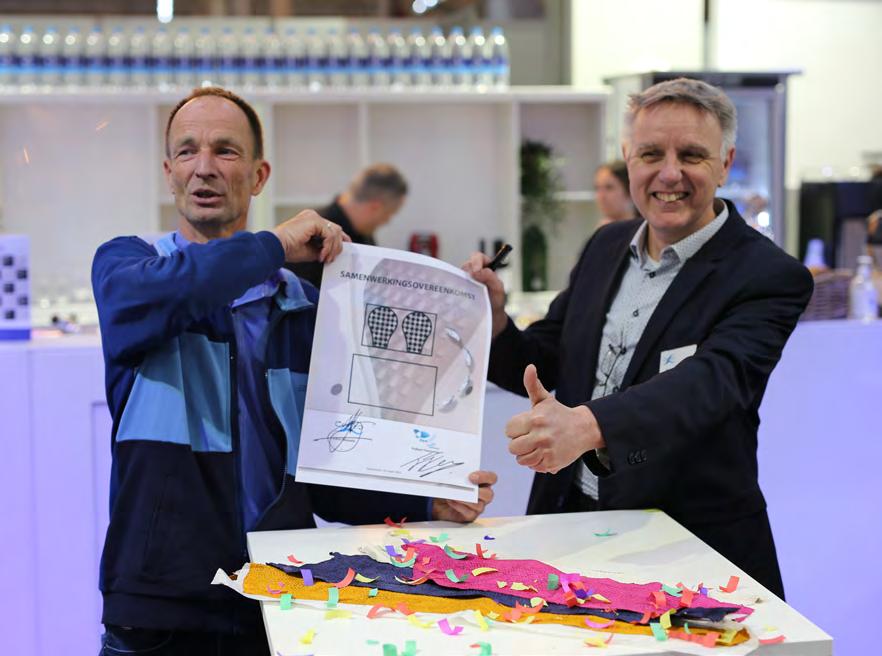

Folkert Fennema (l) and Coos Wessels with the signed collaboration agreement.
At the Asten wastewater treatment plant in the Netherlands, a pilot study has been performed with effluent polishing using a combination of nanofiltration and advanced oxidation. Water technology suppliers NX Filtration, Van Remmen UV-Technology, and Jotem Water treatment optimized the process to remove all remaining micropollutants, including medical residues, pesticides, and pathogens, at the lowest costs. The quality of the additional purified municipal wastewater meets almost all standards for drinking water, allowing for reuse in agriculture and industry.
FINAL BARRIER FOR ALL MICRO POLLUTANTS
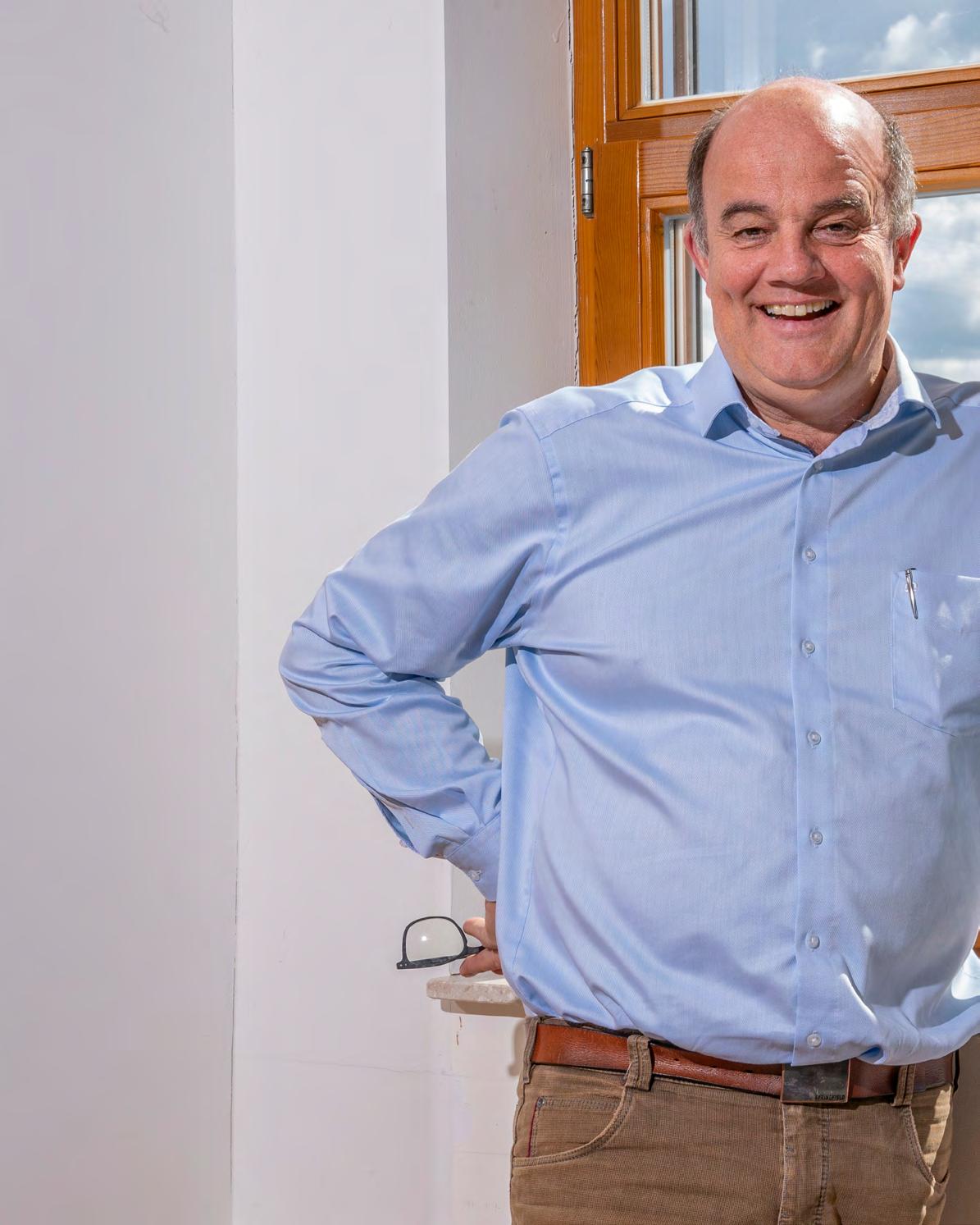
Ton Van Remmen, director of Van Remmen UVC Photo: Dennis van den Worm “The combination of hollow fibre nanofiltration and UV oxidation adds value to wastewater”, says Ton Van Remmen, director of Van Remmen UVC. “It is no longer about wastewater treatment, but rather about the production of water for agriculture and industry. We optimized the complete process so we can now supply water for less than 50 eurocent per cubic meter.” According to Van Remmen, this marks the end of an era of treating municipal wastewater to meet discharge standards. “This is about creating a new water resource that can bring relief in water stressed areas, stopping ground water depletion, and decreaseing pollution of surface water, all at the same time”, he adds.
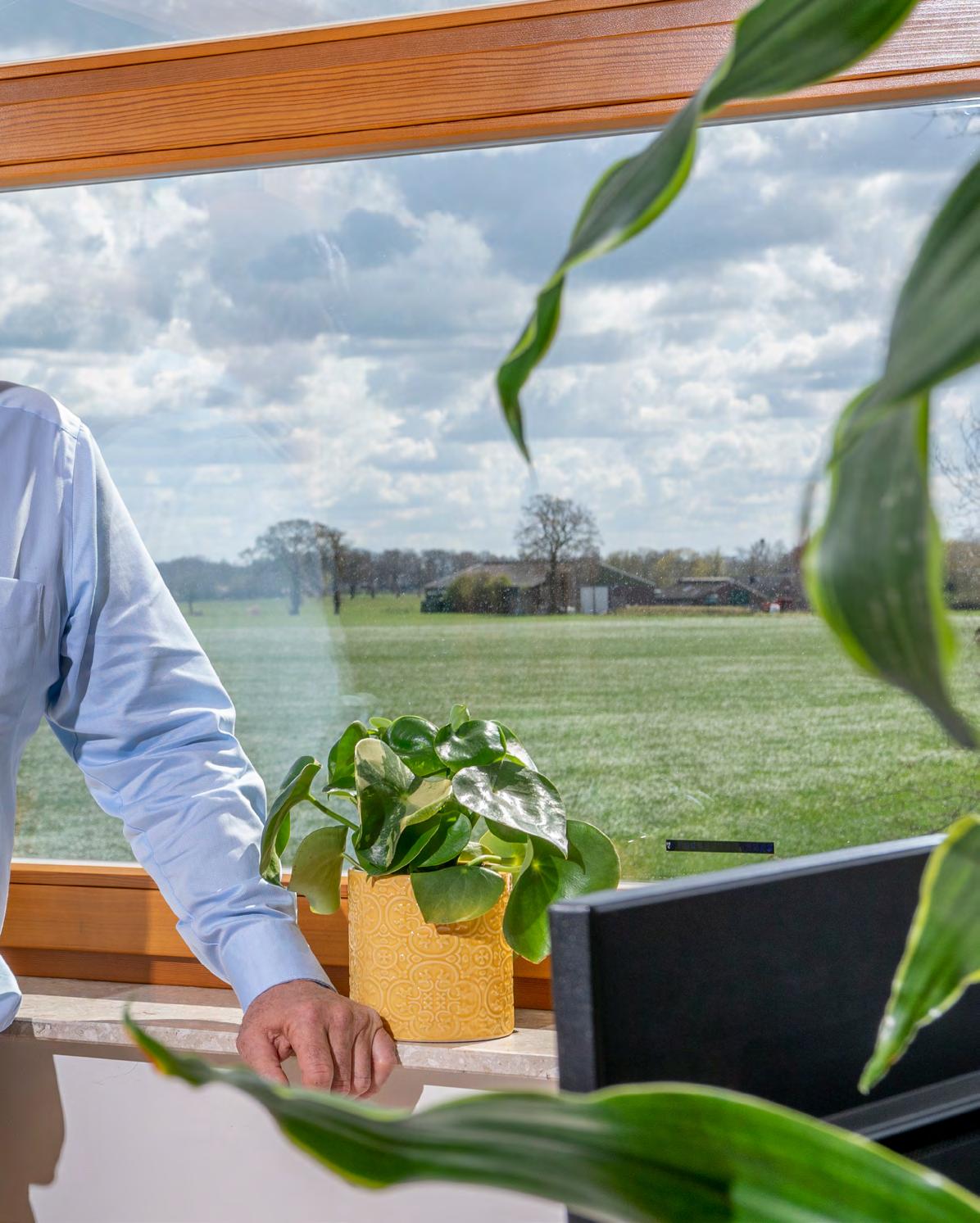
final barrier
The use of nanofiltration is particularly striking because wastewater can quickly clog the fine pores of these membranes. Supplier NX Filtration developed hollow fiber membranes that have a special nano coating on the inside that rejects almost all micropollutants, bacteria, viruses, and micro plastics. Despite the challenging conditions to treat WWTP-effluent, the nanofiltration membranes continued to perform for weeks without the need for chemical cleaning. NXF Filtration produces nanofiltration membranes with different pore sizes. These different pores sizes were used during the pilot study to optimize the treatment process. The pore size has a direct effect on the second part of the combination, the advanced oxidation using UV-C light and hydrogen peroxide. Fewer remaining pollutants from the nanofiltration resulted in a highly transparent water stream. This allowed the breakdown of any remaining substances and improved the energy efficiency of the UV-light significantly. Van Remmen, NX Filtration, and Jotem managed to optimize the treatment process using as little energy as possible. Pre-treatment with nanofiltration resulted in 75 percent less energy use for the oxidation step.
medical residues
Today, most effluent polishing at municipal water treatment plants is done with sand filtration, activated carbon, or oxidation using ozone. The main objective is generally to remove nutrients and medicine residues. Results so far show that up to 70 percent of certain medical residues can be removed this way. This new combination of nanofiltration and advanced UV-oxidation has proven to reach removal rates up to 95 percent. Additionally, it removes microplastics, heavy metals, colorants, bacteria, and PFAS. The trials at WWTP Asten will continue to verify the first results and help with finding out more about the removal of antibiotic resistant bacteria. Meanwhile, the owner of the WWTP, the regional water authority Aa en Maas, will concentrate on finding nearby industrial customers for the treated wastewater. The effluent is now discharged in a local stream whereas it can be supplied at almost drink water quality for less than 50 eurocents per cube. “We have proven the technical feasibility. Now it is up to utilities, agriculture, and industrial water users to invest in water re-use”, Van Remmen concludes.

Process control of the advanced oxidation to break down the remaining pollutants that pass the nanofiltration membranes.