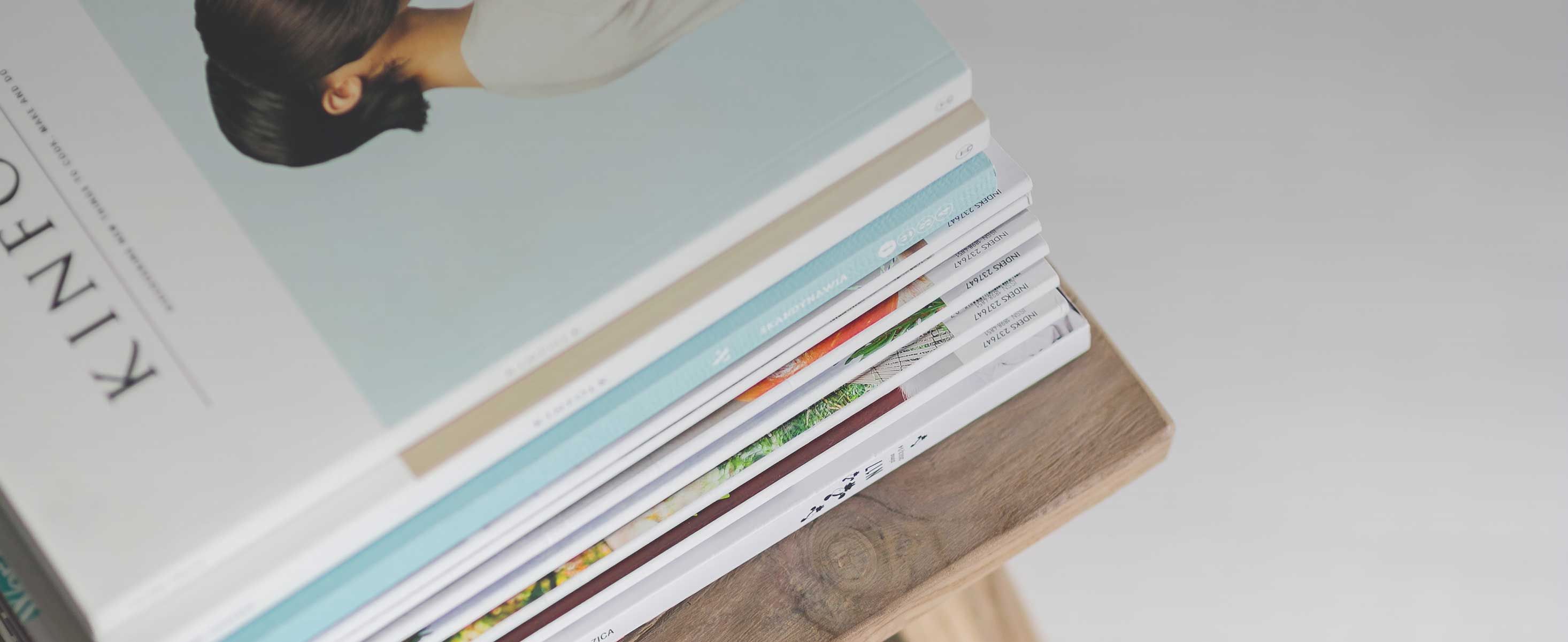
3 minute read
for Profit =
from 2023 July Current
by The Current
Hazard
Continued from page 11 including Hazmat team members located around our network,” Robynn Tysver, UP Railroad Manager II Communications, said in an email.
Advertisement
Both rail lines operate through Spokane Valley, with BNSF officials telling city officials approximately 70 – 80 trains pass through the area daily on their line, amounting to more than 90,000 cars of hazmat material per year of which 40,000 is oil.
Both railways provide much of the same features when it comes to safety measures. Both use trackside detectors — more than 4,000 for BNSF and over 7,000 for UP — to detect problems that occur with train wheels, sensors that use sound, vibration, temperature and other factors to find and analyze faults.
BNSF and UP crews also perform frequent visual inspections of their network for problems with rails, ties and other features — including inspections of rails, bridges and tunnels after a major weather event. Teams use a variety of equipment, including specialized rail cars, and both BNSF and UP operate unmanned track geometry cars which can survey sections of track 24/7.
“The urgent items are relayed to our field teams for repairs,” Tysver with UP said. “The rest of the data is used to drive our longer team maintenance planning.”
Both BNSF and UP upload all of this data to a central traffic command center that operates 24/7/365. The real-time data is communicated to work and maintenance crews, dispatchers and train crews, also in real time.
Train crews with BNSF — UP crews have a similar system — utilize a system called “Positive Train Control.” PTC uses trackside information, an “Onboard Locomotive System” that records and analyzes train conditions, a “Back Office Server” that communicates mandatory movement directives from the operations center to individual trains and GPS to “constantly calculate a warning and braking distance based on the train’s speed, speed limits, signals, switch positions, grade and work zones” via an onboard computer.
“These efforts, coupled with the use of specialized rail cars to carry hazmat, mobile apps to equip first responders with critical safety information, and a software system to determine the safest rail routes all help ensure that more than 99.99% of all hazmat moved by rail reaches its destination without a release caused by a train accident,” Kent with BNSF said.
And while trains also don’t come with Material Safety Data Sheets, there is a way to identify the type and amount of hazardous chemical content in the various cars through an app called AskRail.com. This app is available to and used by many first responders, including SVFD.
Training and resourcefulness
Even with safety features in place and working, hazmat accidents happen. Responding to these incidents not only requires specific equipment but specialized training.
Both Kent with BNSF and Tysver with UP said their companies provide thousands of hours of training to their employees and to first responders who request it. Bond with SVFD said they have utilized some of this training, along with training provided by other agencies.
More is needed, however, and the department has recently taken steps to upgrade that; breaking ground in May on a new $8.8 million, 13,000plus square foot training building on Barker Road. The facility will provide state-of-the-art classrooms and facilities — including a two-story residential house layout inside — to meet this need, which Bond said right now amounts to about 50 firefighters per day needing some additional training.
Even with training, each hazmat incident is unique. In the case of the Inland Paper Mill fire, firefighters were battling a powder that ignited when it came into contact with water — producing an exothermic reaction.
Firefighters initially applied water on the powder to extinguish the fire, but when the water was removed, the exothermic reaction returned, generating intense heat. Compounding this, there was “thousands of pounds of the stuff,” Bond said, combined with outside temperatures that were unseasonably warm.
Bond said they inquired about CO2 capabilities onsite, but found this was limited to small, hand-held units. Foam was ruled out as its main component is water.
Eventually, Bond said they settled on an approach of applying “copious amounts of water, thousands of gallons a minute” on the material to allow cooling to take place and limit the reaction. The process took two days to complete.
While some reports surfaced of a possible evacuation of nearby businesses and residences, Bond said this was not the case, and the evacuation was only for mill employees. As they would do with other hazmat accidents, Department of Ecology officials used modeling software to determine if any plume of hazardous gas or chemicals was possible, and if so, its nature and which direction it might travel.
If an incident where a general public evacuation is needed, Bond said these models are used to determine the best possible routes of escape, which would be implemented by local law enforcement agencies.
As more and more hazardous materials are transported and utilized, the more resources and training will be needed by first responders to deal with accidents. Bond said SVFD is continuing to work on these resources, including coordination with other agencies to minimize as much risk as is possible.