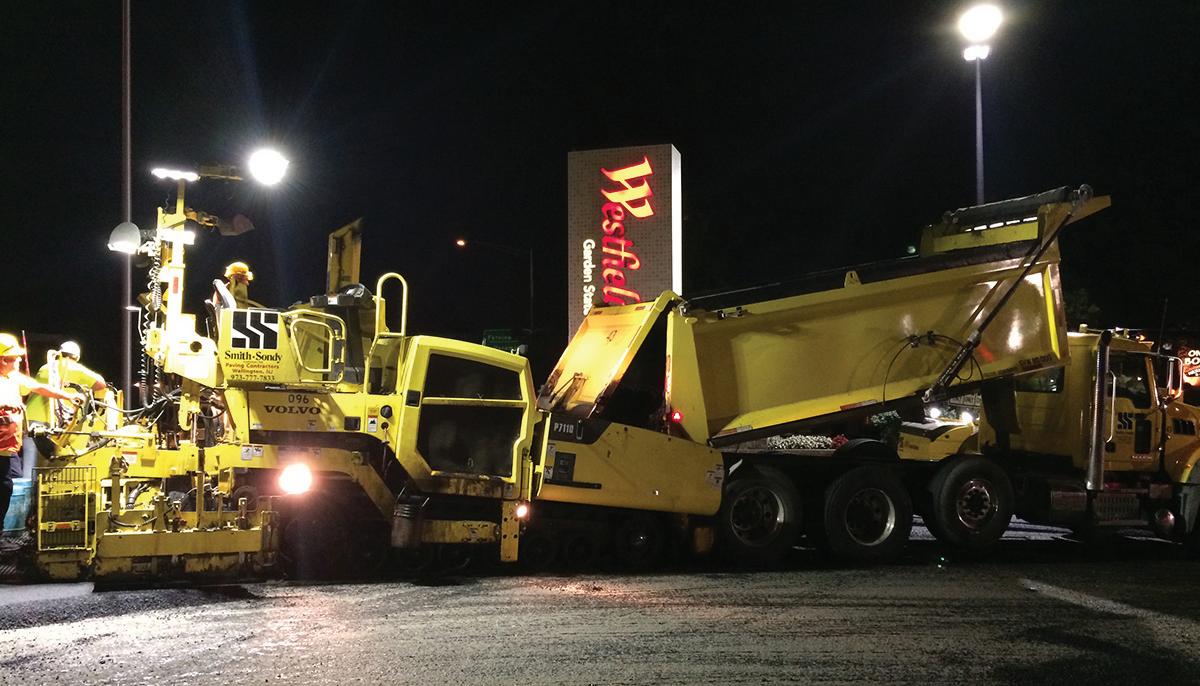
17 minute read
Smith-sondy asphalt construction co. celebrates 75 years
for it as well. When asked if I had ever built a road my response was, ‘Absolutely’ even though I had no idea what a crown was, nor did I know how to build it. I took on the challenge, learned how to run a grader, made a few mistakes, and in the end, successfully built the road. I embraced the challenge and never looked back.” Joe knew that Nick brought valuable contributions to the business. He recalls, “Nick worked here for six or seven years and then became a partner, and we’ve been together ever since. We haven’t had one argument. We both share the same work ethic and we’re excellent partners. We’ve been very fortunate.”
“That was the first time I did something really big,” Joe contin- Nick recalls that early in his career, when on a vacation with his ued. “When I started, the company was doing wife, he took away the NJ State Specificaless than $150k a year. After the first year I tion “Green Book.” He read the book as one took over, I doubled the business. I worked would a novel, and when his wife questioned nights and weekends tirelessly. My father “Each year, you take on a little him about his unusual choice of reading, joked, ‘I ran this business for 25 years and I bit more work and you get Nick responded, “I have to understand evnever stayed in the office as long as you do — why are you working at 10 o’clock at night?’ more experience; you do it erything in this book, because we’ll run into it sooner or later.” But that’s what I did. I just worked hard.” In 1975, Joe told his father he wanted to Sure enough, 40 years later, Nick’s skills and background as a professional engineer enabled the firm to take on more buy into the business. His father laughed at technical work, beginning with an $864,000 first, but ultimately gave Joe a third of the ownership. When his father passed away in -Nick Genchi site improvement contract for the Clifton City Hall. This project took the firm well 1977, Joe continued to pursue ownership of beyond its paving niche as it also included Smith-Sondy, buying out his mother in 1980 electrical installations and landscaping. That and then Joe Sondy in 1987. project acted as a springboard for more public work, and a few years later, Smith-Sondy took on their first multi-million-dolJoe’s current partner and vice president Nick Genchi joined the lar job for the State of New Jersey on Getty Avenue in Paterson. firm in 1981. His grandfather was an Italian contractor and home From there, the duo was well positioned to take on an increasing builder who worked with Joe’s uncle. Nick’s grandfather intro- amount of public work, further diversifying their portfolio and duced the two at Nick’s father’s millwork shop, and that fateful solidifying their reputation as a premier paving operation in the interaction set the stage for the following four decades of growth. state.
Nick graduated from Memphis State University in 1976 with a degree in Civil Engineering. He worked briefly as a consultant, but ultimately came back home to New Jersey to work for the City of Clifton and then again as a consultant in Paramus. As Nick tells it, “Joe convinced me to get into construction. We had a meeting and he told me if I worked in construction, I’d get winters off. My wife loved that point, although I don’t think we’ve really had a winter off in 40 years. I told myself that if I don’t like construction, I could always go back to consulting, but it’s been 40 years and I haven’t gotten tired of it yet.” “I did a lot of marketing with the engineers, and when Nick came on board, he helped me sustain that,” Joe recalls. “We’ve been fortunate to maintain the reputation that my father built, which has carried us into the industrial work and commercial work, and ultimately to the municipal and state work.”
Smith-Sondy is generally focused in New Jersey North of the Raritan River, and they’ve proudly worked for some of the biggest names in the industry such as Russo Development, Gale and Wentworth, and Joseph M. Sanzari, in addition to performing a considerable amount of work at Teterboro Airport for Jet Aviation, Meridian, and Signature Flight.
Nick says, “In the past, the firm concentrated on grading and paving as a subcontractor to larger construction companies, but over the years, developers would prefer to give out one contract, and that’s basically when we started building up our sitework expertise. We started to take on the crews and performed much of that work ourselves.”
Now, with about 100 employees, Smith-Sondy continues to build upon its legacy. They’re currently finishing up a State Department of Transportation project on Route 23, working on a project for Amazon in Carlstadt, and have just completed a 50,000ton paving project for Union County and a 40,000-ton project for Essex County.
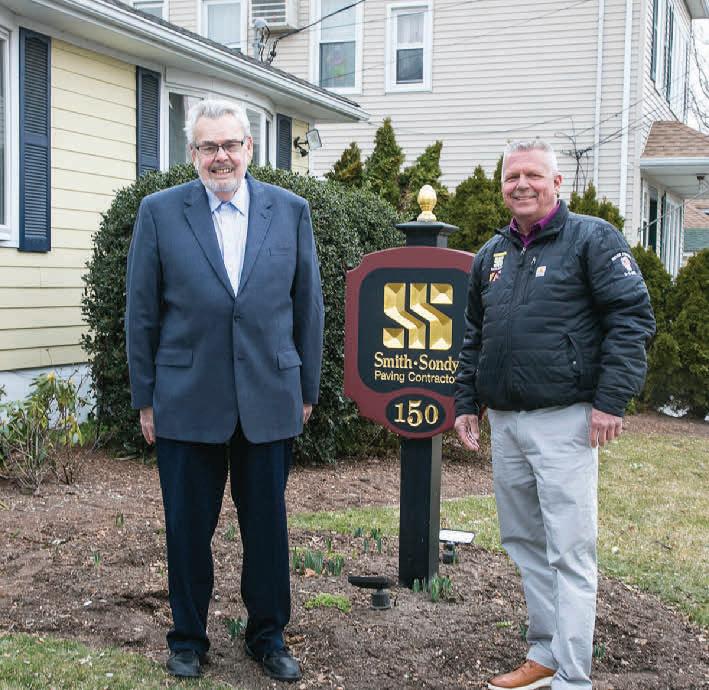
William J. Meyer and his nephew Jack Meyer together with 105 years of asphalt experience.
Nick says that, “When we started in 1981, we grossed over $1 million, and each year we’ve continued to grow. You take on a little bit more work and you get more experience; you do it more efficiently and you grow. Then sure enough, 40 years later, you’d be impressed.”
Joe attributes much of this success to his partnership with Nick, and specifically, to Nick’s eye for design. “We have an advantage,” Joe says, “because Nick and our engineers redesign a lot of the projects. One of the biggest things in the industry that we face are grades. Nobody understands grades like Nick. He is very meticulous in his work and over the years, thanks to his knowledge, we’ve continued to expand our engineering department. We currently have four engineers on staff as well as several estimators with 30-plus years of experience.”
Despite its commercial success, Smith-Sondy remains a family business. Their office is still located in the house where Joe was raised, and they have an impressive history of employee retention. "Our management team “Our management team has about 300 years has about 300 years of collective expertise, and our employees are our most valuable asset,” Joe Our employees are our says. “Our people are committed and tend to -Joseph Smith stay. Most of our employees are 30-plus year employees.” He cites long-time employees like projects manager Bill Meyer and general superintendent Jack Meyer as key to the firm’s steady growth. Field managers Tony Ferreira and Jose Seixiero have been fundamental assets in the field. Former CFO Vincent Massimo served the company from 1987 until his untimely passing in 2009 and actually picked his successor, Susan Ruschke, who has served in that position since. Joe and Nick also attribute some of the company’s continued success to their dedicated subcontractors and suppliers, in addition to the valued business relationships they have developed in their long-established history.
As they look ahead, Smith-Sondy shows no signs of slowing. “Retirement is not in my genes,” Joe says. But he is optimistic for the future. “My hope is that my son, Eddie, will continue to grow what we’ve built. He has been working with us for about 15 years and is well poised to take the reins whenever I decide to slow down. I only hope he’ll be as lucky as I was to find a partner like Nick. Our partnership has been the main ingredient to Smith-Sondy’s success. There’s no doubt that the skills and knowledge that Nick brought to the business, along with his ability to negotiate and construct, have been invaluable.”
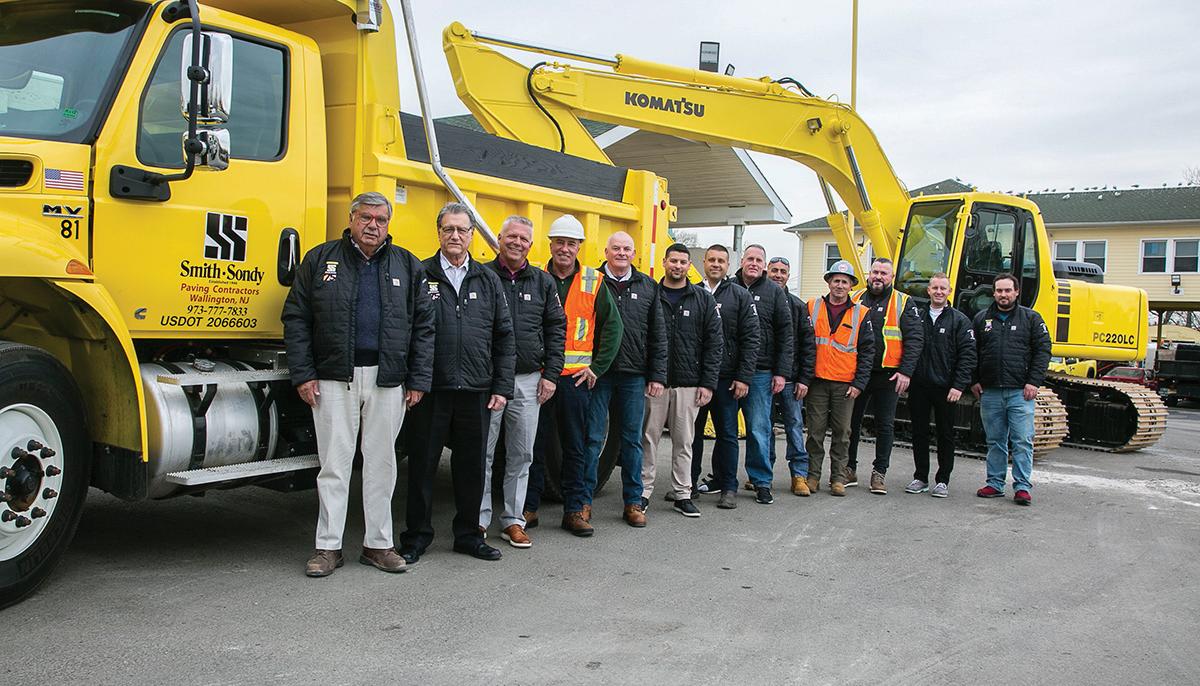
Smith-Sondy Management Team.
For three-quarters of a century, Smith-Sondy has built upon its accomplishments and expanded into a multi-million-dollar success story, all while remaining true to its foundations. Their mission of “building relationships through quality, integrity and service” has served them well and remains at the core of their business model, to this day and into the future.
Smith-Sondy has been an active member of UTCA since 1985 and has found great value in the contractor community throughout their long history. UTCA would like to congratulate Smith-Sondy Asphalt Construction Company on this impressive milestone and looks forward to celebrating their continued success.
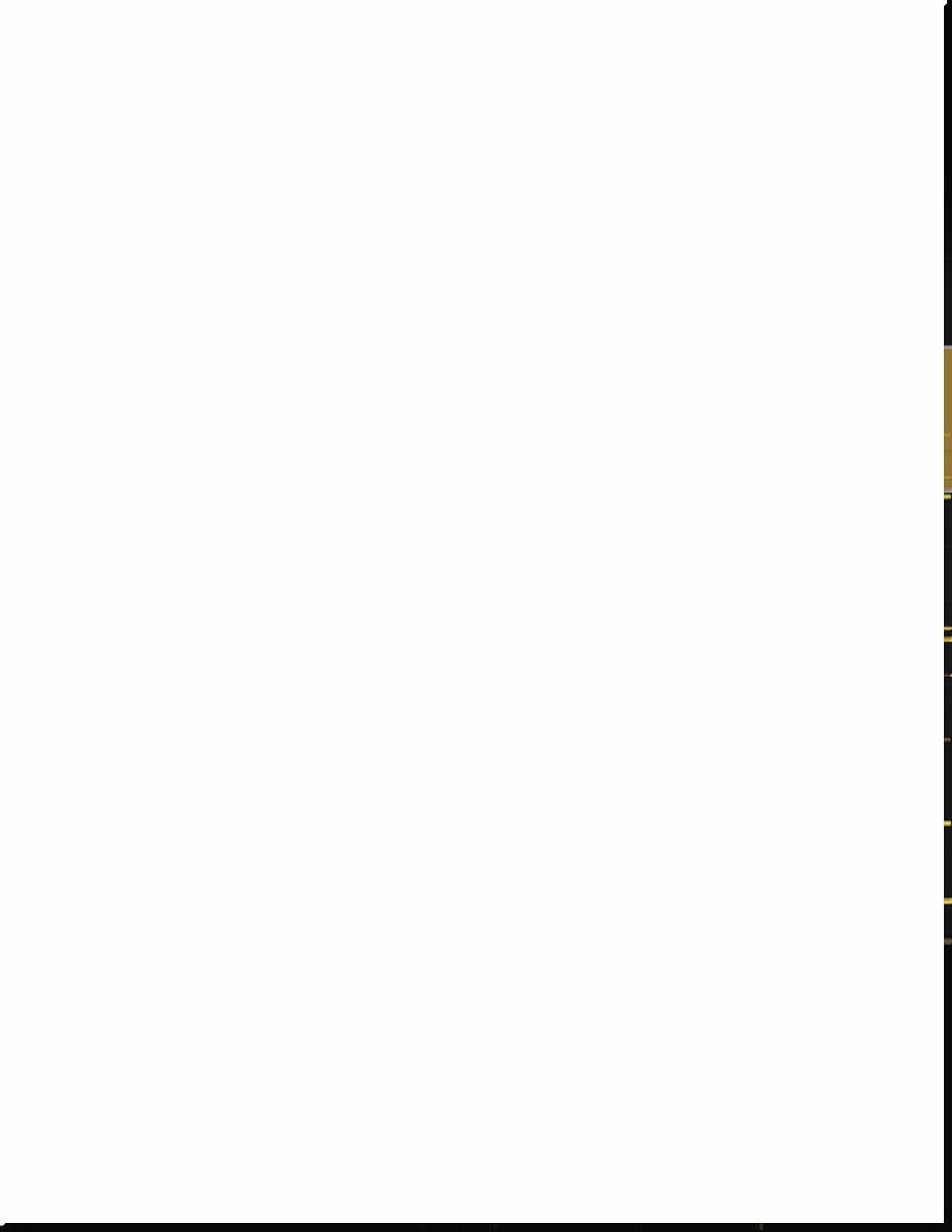




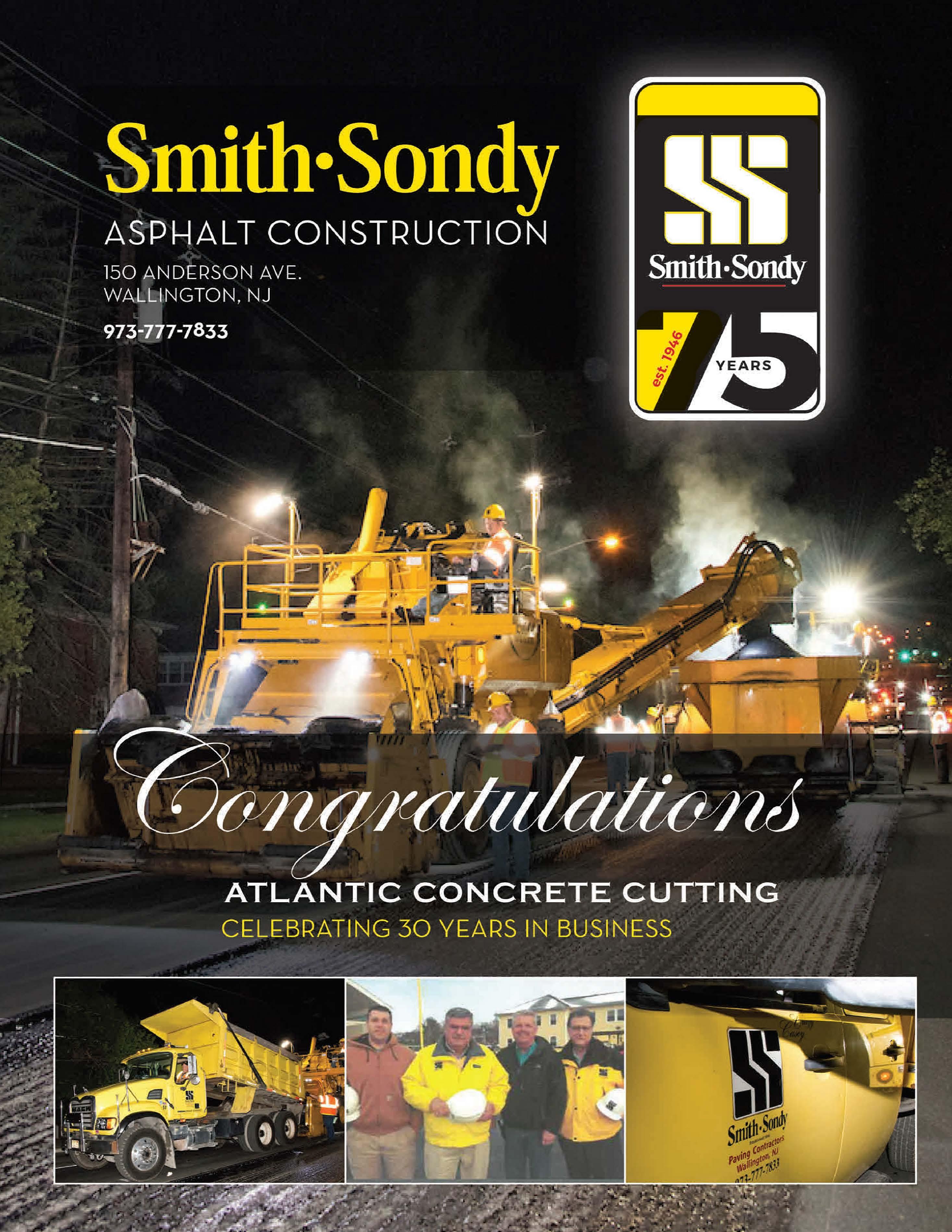


atlantic concrete cutting - building on experience in the 30th year
WBE firm reflects on their portfolio of projects while looking towards the future
There are many uncertainties in the construction industry, but after thirty years in business, Nancy Cramer knows one thing; nothing is more valuable than experience. Nancy founded Atlantic Concrete Cutting in 1991 on a shoestring budget with the goal of one day becoming a leader in both the greater New Jersey and New York construction arena and the saw-cutting industry nationally. From humble beginnings of Nancy driving trucks and completing invoicing at the kitchen table, Atlantic gradually took on more expansive projects. Nancy’s philosophy for growing her business has always been to focus on the next opportunity. With each new and challenging prospect, the firm draws on its past experiences and skills to focus its outlook for the future.
Atlantic started out in the 1990s by providing basic core-drilling and slab-sawing services. Early membership into the UTCA and the Concrete Sawing and Drilling Association (CSDA) provided access to a fantastic network of knowledgeable individuals. CSDA’s training and technical resources proved to be invaluable. Throughout the late ’90s and early 2000s, Atlantic took on more challenging projects, venturing into specialized cutting for bridge and structure demolition, as well as sawing and sealing joints in new pavements.
With expansion of Atlantic’s market area came new equipment and additional manpower. Moving into more areas of the TriState region, the firm acquired new industry contacts and joined additional professional organizations. In the mid-aughts, Atlantic undertook some of its first landmark projects; the company core drilled 14-inch tieback holes into the dry-dock walls at General Electric’s submarine plant in Groton, Connecticut. In 2009, they installed some 265,000 linear feet of neoprene joint sealant at JFK’s bay runway, which was the first of three runway rehabilitation projects Atlantic undertook for the airport. Most notably during this period, Atlantic became involved in wire sawing and wall sawing for structural demolition of the World Trade Center site in preparation for new construction. The majority of this work took place between 2007 and 2014, although Atlantic is still
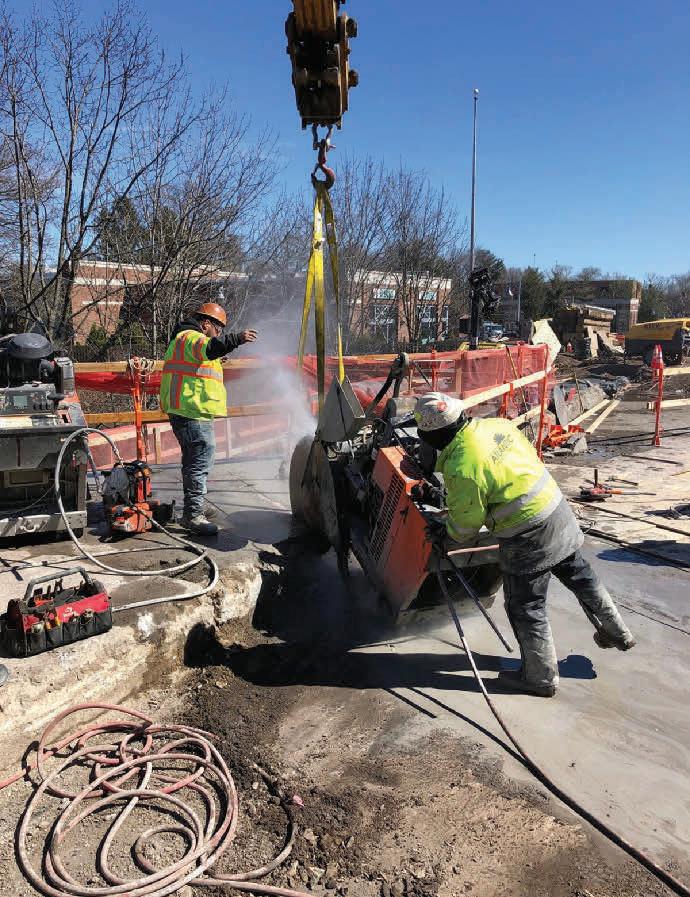
Atlantic employees cut a bridge deck into pickable pieces for IEW Group in Montclair, New Jersey.
regularly engaged in work at the World Trade Center.
Creating alternative solutions for intricate demolition problems and navigating tight schedules has set Atlantic apart from the rest, and the core of this success is the firm’s employees. Whether in the field or in the office, taking on a complicated and challenging project requires the experience and input of everyone. As an employer, Atlantic prioritizes its responsibilities and commitments to its employees and their families, providing competitive wages and salaries to skilled individuals from across the region. Since 1991, they’ve developed an extensive support network to meet the demands of their growing projects. New equipment and an expanding vehicle fleet required a well-staffed shop with trained mechanics to keep operations efficient and safe. Their administrative support staff has grown by leaps and bounds as larger contracts and growing assets required capable individuals to

The former Tappan Zee Bridge (center) showing two spans with the center portions of bridge deck sawcut by Atlantic. This was done to reduce total span weight allowing full spans to be picked by the Left-Coast-Lifter (right).
assure regulatory compliance, contract review, proper insurance coverage, and revenue collections. Michelle Morris, who joined Atlantic in 2012 as a financial controller and rose through the ranks to become CFO/COO in 2016, has been working alongside Nancy through all this growth, bringing 33 years of construction accounting experience. "Having a great team that is working together is the key to our success".
Another reason for Atlantic’s success has been diversification. The casual observer might say that concrete cutting is just concrete cutting. Not so. As the industry has matured over the years, technological advances have offered new approaches for fulfilling clients’ unique job needs. The company has a wide range of diesel-powered and electric slab saws as well as electric and hydraulic core drills. In recent years, this equipment has been supplemented and, in some cases, completely replaced with an assortment of wire saws, curb saws, dowel drills, hi-cycle wall saws, and various joint and crack sealant installation machines.
In 2017, Atlantic undertook its largest consecutively executed project to date — complete saw cutting for the demolition of the former Tappan Zee Bridge. A landmark structure in our region, the 3.2-mile-long Tappan Zee was replaced with two larger structures. The project’s final phase was the total demolition of the old bridge in a tight two-year schedule. Atlantic and its employees put their ingenuity to work to develop several methods for bisecting the 60-year-old structure into manageable pieces for disposal. The company’s crews worked long shifts in all weather conditions, wire-sawing sub-structures in and over the frigid Hudson River and operating above the active Metro North railroad. They even collaborated with an industry equipment manufacturer to design a custom road saw to cut the bridge deck into tapered pieces, which dramatically accelerated the deck-removal process.

Atlantic’s management team at the last UTCA event in Atlantic City, NJ Wes Jones, Ted Nielsen, Nancy Cramer, Michelle Morris.
The Tappan Zee Bridge was an important project not only because of its size and impact on the company’s portfolio, but because the methods applied to the project have become essential to Atlantic’s work ethic going forward. Operations manager Wes Jones notes, “A large portion of our current backlog of work are projects that involve a tight and often alternate shift schedule.

Atlantic Concrete Cutting crew with Project Manager Ted Nielsen at a weekend track outage project for WMATA in Washington, DC. The ability to execute these jobs successfully really sets our team apart in our field, and the lessons learned on each project prepares us for the next.” Atlantic has been called on recently for several rapid weekend bridge-replacement jobs for the NJDOT, as well as night and weekend work for NJ Transit, the MTA, and the LIRR, and is currently working on its third large project for WMATA in the Washington, DC area.
To remain competitive and economically viable in a difficult industry, Nancy and Michelle take a hands-on approach. Nancy explains, “We always seek ways to keep our customer base and to expand into new markets. This requires ongoing training, developing an even stronger safety culture, acquiring state-of-the-art equipment, recruiting new employees who possess innovative thinking skills, recognition and advancement for our existing family of employees, and strong, aggressive leadership by our managers. This is a difficult undertaking, but one I’m confident that Atlantic can meet.”
The future is bright and full of promising opportunities for Atlantic. Its management team will continue to build on their expertise, seeking new markets, utilizing cutting-edge technologies, and providing a secure future for their employees.

Atlantic Concrete Cutting crews dice up a portion of Runway 13L-31R at JFK.



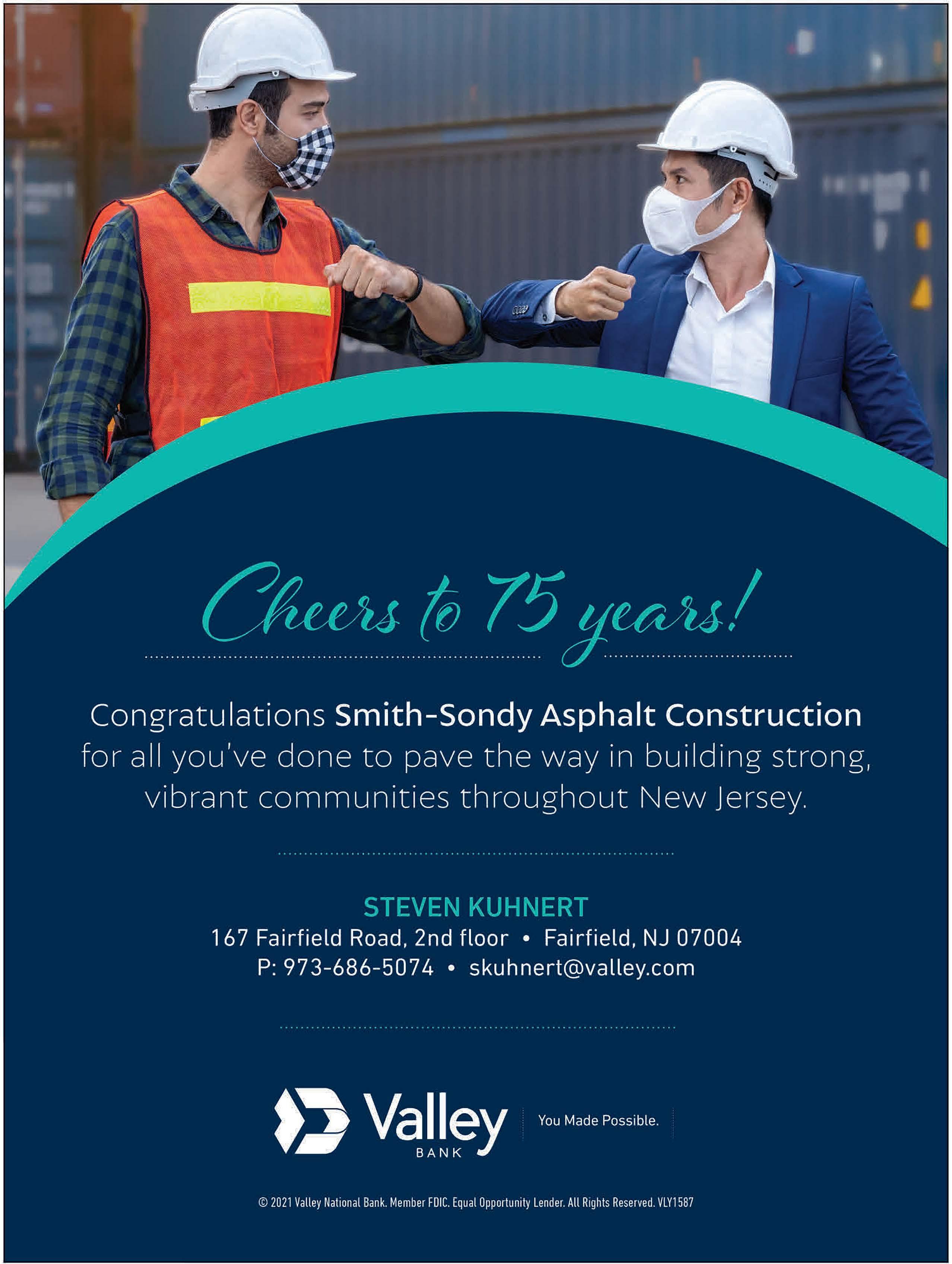



By: dan kennedy, director of environmental & utility operations
UTCA continues to work closely with Jersey Water Works (JWW), a collaborative effort started in 2015. JWW is made up of many diverse organizations and individuals who embrace the common purpose of transforming New Jersey’s inadequate water infrastructure by investing in sustainable, cost-effective solutions that provide communities with clean water and waterways; healthier, safer neighborhoods; local jobs; flood and climate resilience; and economic growth.
By serving on the Steering Committee for this effort and as a co-chair of its Asset Management and Finance Subcommittee, UTCA is positioned to assist and influence critical work conducted by this collaborative effort. Through JWW, we have generated additional support for increased funding and other priorities for the UTCA.
In addition to prioritizing funding for water infrastructure in New Jersey, it has established the following goals: waterways; and demonstrates how effective stormwater management can help mitigate the effects of climate change. Jersey WaterCheck advances the knowledge our state’s leaders need to improve New Jersey’s water infrastructure for individuals, communities, and utilities.
UTCA and others are working to build institutional and financial capacity in all water systems and to gain support from the federal and state government to overcome decades of underinvestment. We believe that when residents and businesses are educated on the condition of their underground and unseen water infrastructure issues, they will be willing to invest more to modernize these assets and elect representatives at all levels of government who are willing to address these issues head on.

Bringing Water System Data to your Fingertips
UTCA is helping to promote Jersey WaterCheck, a new online resource created by JWW that can be accessed by heading to www.njwatercheck.com.
UTCA contributed to the development of this new tool with the goal of helping bring the status of drinking water and wastewater systems to the light of day. The urgency of the water-infrastructure problem in many (not all) of New Jersey’s older cities and towns cannot be overstated. We hope this new tool can help identify and celebrate those water systems that are succeeding and expose those that are underachieving. This is expected to encourage continued success (for well-run systems) and more aggressive actions to bring failing systems into compliance.
This new website is intended to make it easier for all to learn more about how their local water systems are faring in terms of regulatory compliance, investment, and transparency. Jersey WaterCheck helps New Jerseyans understand our drinking water and wastewater systems; shows how improved water infrastructure can enhance the health of our communities, rivers, and
Benchmarking and Checking in on Water Systems

This tool has two main features. The first is the “Benchmark Hub,” which helps utility managers and state leaders dive into the factors that contribute to the need for water infrastructure investment. Here you will find the details, measures, reports, results, and data that JWW has gathered for every water and wastewater system in the state. It should be noted that JWW is partnering with the NJDEP, and their staff should be credited with bringing historically buried regulatory data to the public eye. Do you want to know how many drinking water systems met primary drinking water standards? Do you want to know how much money has been received by the federal government that is used to provide project funding support? Jersey WaterCheck can provide responses to these questions and many more metrics-based measures.
Jersey WaterCheck includes 55 metrics, which are measures of specific conditions. Most of them show information about water and wastewater systems. Data for metrics come from four primary sources: 1) publicly available information provided by government agencies such as New Jersey Department of Environmental Protection (NJDEP) and Delaware River Basin Commission; 2) self-reported survey data from utilities and municipalities; 3) data and information gathered from utility websites; and 4) information from a statewide public opinion survey.
The second feature is the “System Finder,” which gives users a