
4 minute read
The role of materials science in digital manufacturing
The role of materials science in
Hein Möller Materials have played a significant role throughout human history. In fact, our history has been defined by the materials that our ancestors have used in the past. The Stone Age was followed by the Bronze Age (characterised by an alloy or mixture of copper and tin), which was followed by the Iron Age.
More recently, materials have, in many cases, been the determining factor in the development of new technologies. The selection of the wrong material for a specific application has led to many failures. For example, the steel rivets that were used to join the plates of the “unsinkable” Titanic were almost as brittle as glass in the freezing waters of the Atlantic Ocean, where the ship hit an iceberg. Unfortunately, the materials scientists and metallurgical engineers at the time were unaware of this fact.
Currently we live in a period known as the Fourth Industrial Revolution (4IR). The 4IR can be described as a fusion of technologies that are blurring the lines between the physical, digital and biological worlds, collectively referred to as cyber-physical systems. In general, the 4IR is based on nine pillars: autonomous robots, simulation, system integration, the Internet of Things (IoT), cybersecurity, cloud computing, augmented reality, big data and additive manufacturing.
Materials science plays a crucial role in the advancement of the 4IR, especially in manufacturing. Digital manufacturing uses digital technology in the manufacturing process. It integrates having the necessary data at the correct place at the right time. Additive manufacturing is the industrial production name for 3D printing. It is a computer-controlled process that creates three-dimensional objects by depositing materials layer by layer. It uses computeraided design and allows for the creation of objects with precise and complex geometric shapes.
Additive manufacturing is the opposite of traditional manufacturing, which often requires machining or other techniques to remove surplus material (subtractive manufacturing). At the moment, the materials that are used for additive manufacturing are mostly based on materials that have been developed for traditional subtractive manufacturing methods.
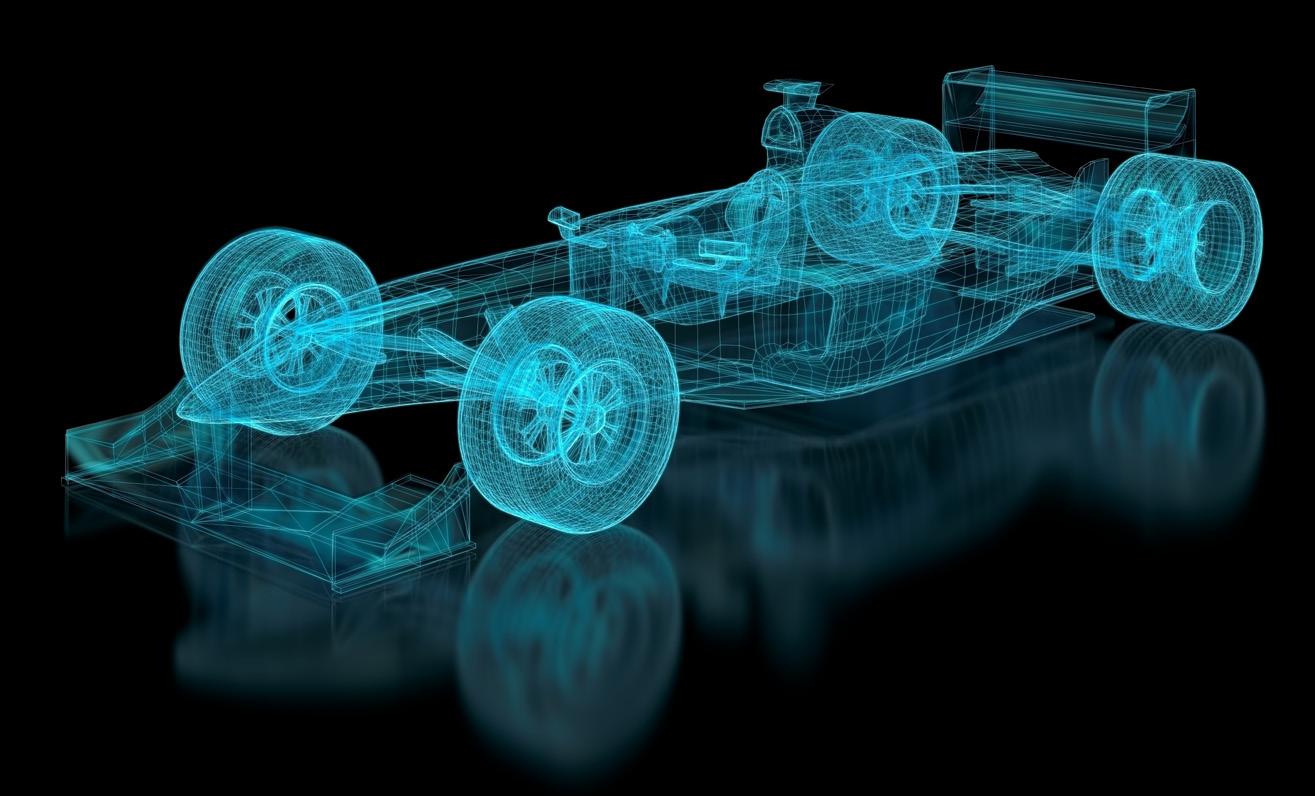
Materials have, in many cases, been the determining factor in the development of new technologies. Materials science plays a crucial role in the advancement of the 4IR, especially in manufacturing.
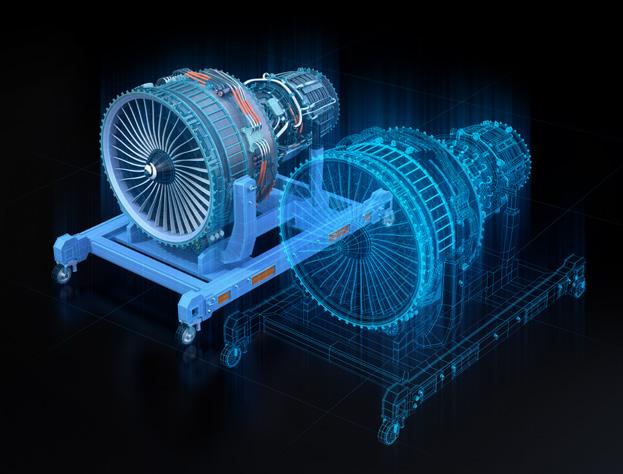
These materials are not necessarily the best choices for additive manufacturing, and it is up to materials scientists and metallurgical engineers to develop new materials that are best suited to the demands of digital manufacturing. Such new materials can create exciting new opportunities to develop products with properties that could otherwise not be achieved.
An example of such a new material is Scalmalloy ® , an aluminium-magnesium-scandium powder alloy that was specifically designed for metal additive manufacturing. The alloy was developed by the German-based company APWorks and Airbus for aerospace applications. In July 2020, the governing body of Formula 1 ® added Scalmalloy ® as an officially approved additive manufacturing material for use in the international racing car championship. According to the Swedish metal additive manufacturing company Freemelt ® , “the metal 3D printing revolution is a materials game”.

Its 3D printer has specifically been designed to make materials that are not yet known to mankind.
The development of new materials is not limited to metals and alloys. Materials scientists are also conducting research on developing new polymer, ceramic and composite materials. For example, Markforged ® , a 3D printer manufacturer, has recently announced the availability of a new flame-retardant composite material. The Onyx FR composite material is nylon with chopped carbon fibres. The main property of this material is its selfextinguishing capabilities, allowing it to prevent itself from burning. This sets it apart from traditional 3D printing thermoplastics and opens up more applications for 3D printing across automotive, aerospace and defence industries because it meets higher fire safety standards.
Greg Satell, who was named by the International Data Group (IDG) as one of the ten digital transformation influencers to follow today, wrote an opinion piece in December 2018 explaining why materials science may be the most important technology of the next decade. Traditionally, developing new materials has been a timeconsuming and expensive process. To find the desired material properties, materials scientists and metallurgical engineers would sometimes have to test many materials one by one. Now, powerful simulation techniques, as well as sophisticated machine learning algorithms, are being used to develop new materials much more rapidly, and assist with possibilities that had never been considered before. Companies who are working in this field include Questek ® and Alloyed ® .
It is therefore clear that materials science is a technology that will shape the future of humankind. It will influence the progress of digital manufacturing and will be a necessity for the 4IR. Materials scientists and metallurgical engineers have a crucial role to play and are ensured of exciting and relevant careers.
References
Satell, G., 2018. Materials science may be the most important technology of the next decade: Here’s why. www.inc.com/greg-satell/ materials-science-may-be-most-importanttechnology-of-next-decade-heres-why.html.