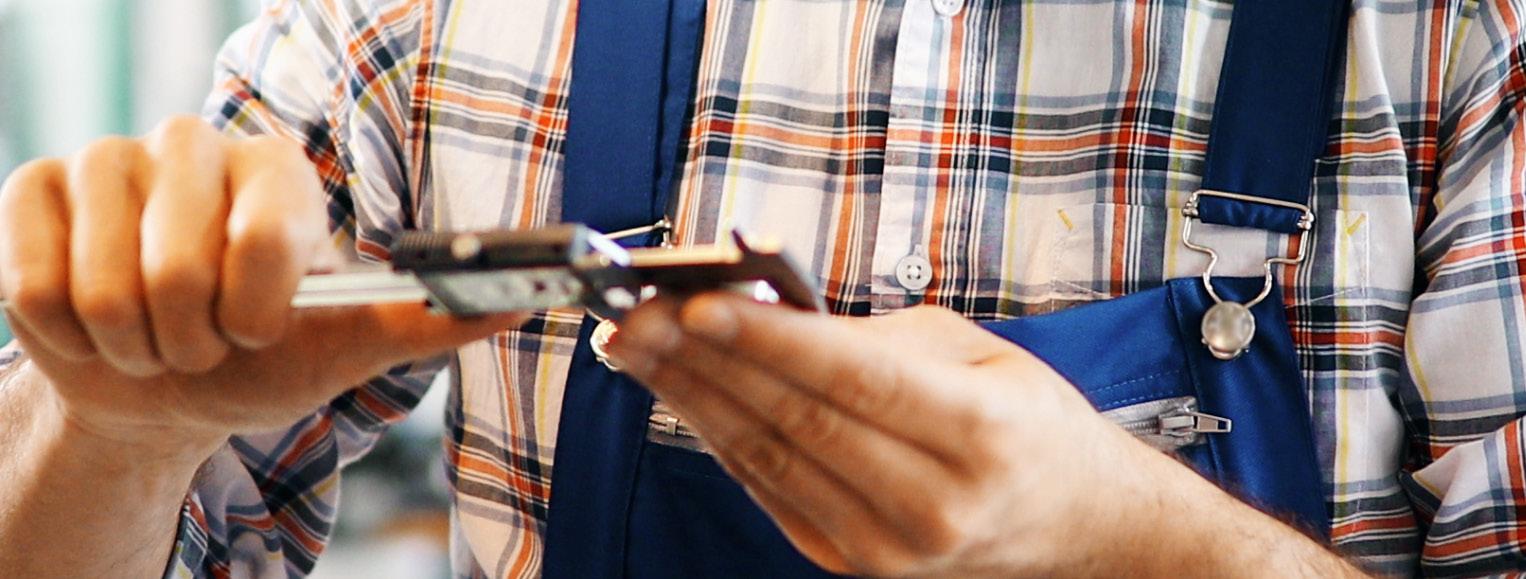
12 minute read
Reshoring to Utah: Challenges and Opportunities
Reshoring to Utah: Challenges and Opportunities
By David Beckerman, Lead Analyst, UAMMI

Reshoring has been a hot topic of late. The global COVID-19 pandemic exposed the weaknesses in global supply chains, but even before the pandemic a rise in tariffs in America on Chinese goods and increased tensions between the two countries had caused firms to reexamine the benefits and challenges of manufacturing and sourcing in China. Companies looking to reshore would like assistance with both the evaluation of opportunities and the reshoring process, but often find few such resources. To that end, the Utah Defense Manufacturing Community (UDMC), through the Utah Advanced Materials and Manufacturing Initiative (UAMMI), set out to identify and assess reshoring efforts. The goal of the research is to support Utah’s policymakers in developing a statewide reshoring program.
UDMC divided its work into four projects:
1. A benchmarking analysis that compared Utah’s reshoring efforts with those of other states and local communities around the country;
2. The second project was an economic benefit analysis that sought to compare the costs of manufacturing or sourcing in Utah with the costs of doing so overseas, particularly in China; 3. Identification of Utah companies looking to reshore;
4. Attracting non-Utah companies that seek to reshore to the U.S.
UDMC has completed the first two of these projects and gained interesting insight on Utah’s competitiveness as a reshoring destination.
The benchmarking analysis showed that Utah, although in line with its peers, could do more to proactively encourage reshoring to the state. Many people are surprised to discover that neither the Federal government nor any of the states provide financial assistance to companies that are looking to reshore. Federal support is limited to consulting and analytical support tools through the U.S. Department of Commerce. Few local entities – states, manufacturing communities states or other local organizations – have developed specific reshoring incentives. They instead treat reshoring like any inquiry for new site location or expansion. Thus, the available incentives (support for job training, new employment credits, site selection, etc.) are not specifically targeted to reshoring companies. A Google search for “Reshoring Utah” will direct you to a site run by the Reshoring Institute (an excellent organization), but not to any state or local programs.
The same is true for most states. One exception is Kansas which has a dedicated web page through its Department of Commerce. It provides case studies and highlights companies that are reshoring, but Kansas does not provide any economic incentives specifically tied to reshoring. This highlights an opportunity for Utah – UDMC has recommended that Utah develop a reshoring website and review existing economic development programs to identify strengths and weaknesses with regard to reshoring.
The second project, the economic benefit analysis, sought to identify the actual costs of manufacturing in China versus Utah based on data from Utah companies. A lack of consistent and non-proprietary data prevented a line-by-line analysis, but the researchers did confirm that basic parts, such as bushings, can cost as much as 80% less in China than in the U.S. Utah firms noted, however, the higher costs of shipping especially in the wake of the pandemic, with container costs up five times their pre-COVID levels. Lengthy delays in the supply chain have added to costs. As a result, firms want to take a look at the total costs of offshoring.
The study found several tools that help in this effort such as the True Cost of Ownership (TCO) Estimator developed by the Reshoring Initiative. It allows lineby-line comparisons and evaluation of what-if scenarios. The Reshoring Initiative has determined that, on average, Chinese manufacturing prices are 30% lower than U.S. prices. But when accounting for hidden costs, such as intellectual property and supply chain risks, the actual cost advantage falls to between 10 and 15%. If the U.S. manufacturer can lower its costs or raise prices, it could overcome the Chinese advantage.
Weber State University (WSU) is in the initial stages of developing an International Supply Chain Risk Assessment Model that would allow Utah companies to weigh the risk of various potential events (such as war or a pandemic) and the associated effect on revenue streams if they take corrective action or not. Users can incorporate the assessment into the TCO Estimator for enhanced analysis.
UDMC has recommended that Utah promote use of the TCO Estimator, assist WSU in the development of its tool, and identify measures to help mitigate remaining cost gaps for Utah manufacturers.
UDMC expects to make additional recommendations following the third and fourth projects of this initiative, identifying both Utah and non-Utah companies that are looking to reshore to the Beehive State.
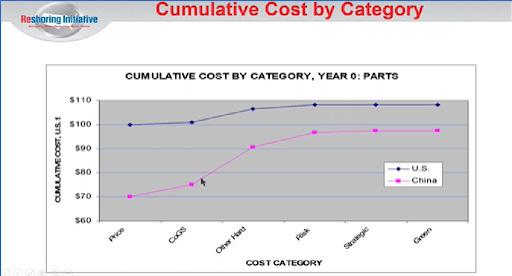
Source: The Reshoring Initiative
Click The QR Code
Links to Reshoring Reports

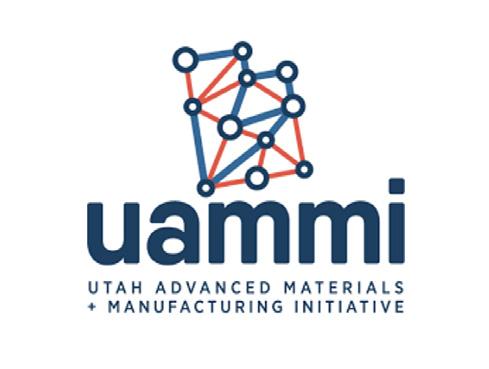
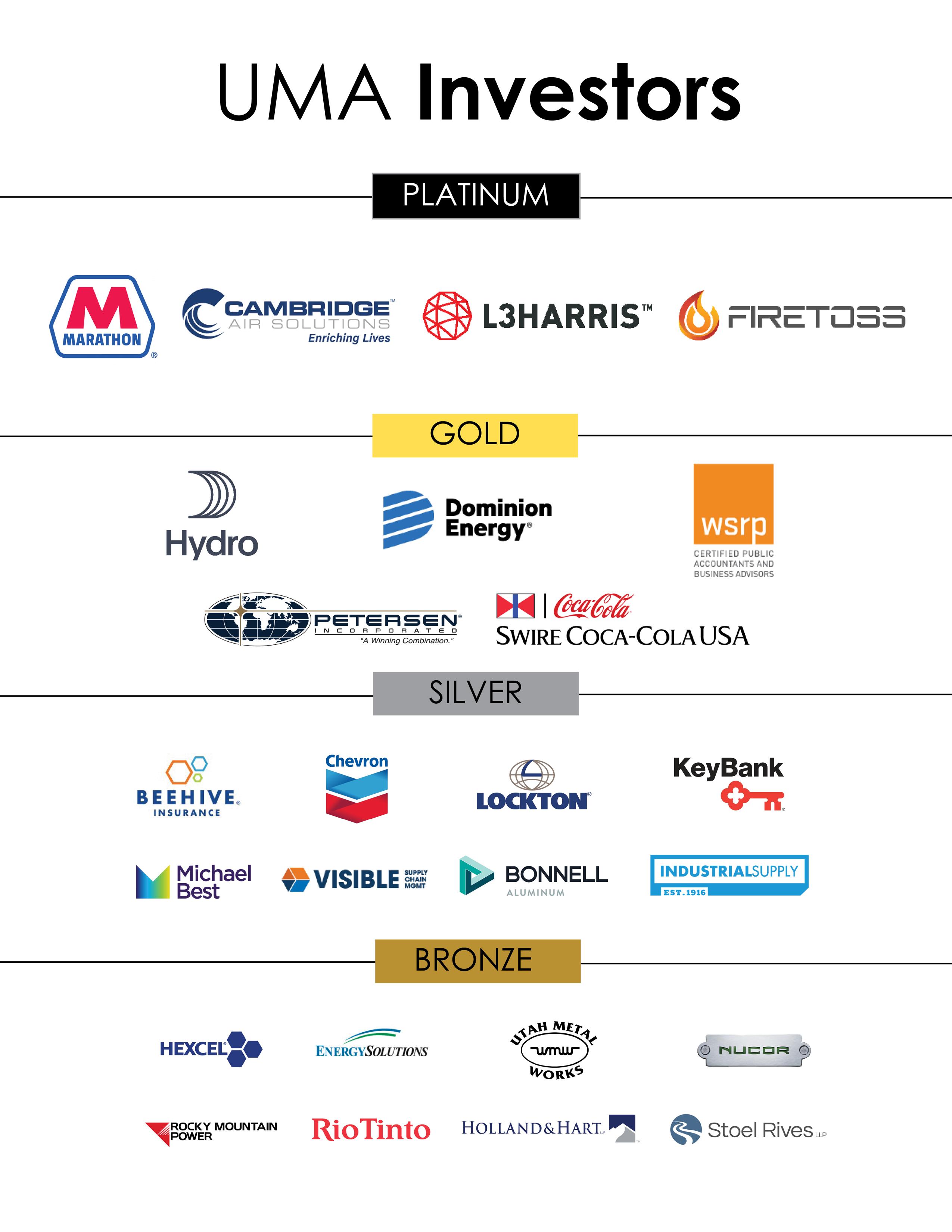
DON’T LET THE SIZE OF YOUR BUSINESS DETERMINE THE SIZE OF YOUR BENEFITS
Text the word “UMA” to 801.901.8531 We’ll send you the 2021 benefit guide
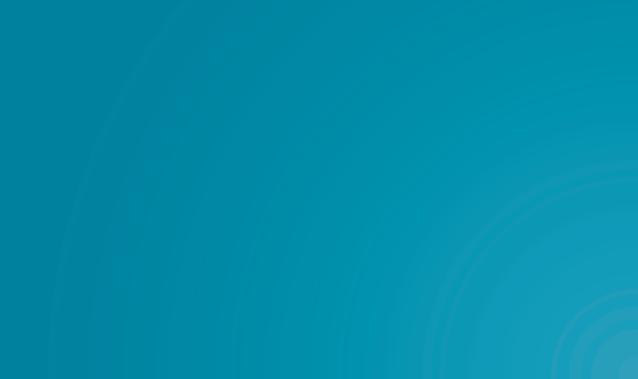
SALT LAKE CITY • OGDEN • OREM • CEDAR CITY • ST. GEORGE • REXBURG 801.685.6860 | 800.323.6303
UTAH MANUFACTURERS ASSOCIATION HEALTH PLAN
An outstanding option for Utah manufacturers! With large group plan designs offering low out of pocket maximums and broad plan choices. For more information or pricing on the Utah Manufacturers Association Health Plan, contact Beehive Insurance today.
BEEHIVEINSURANCE.COM
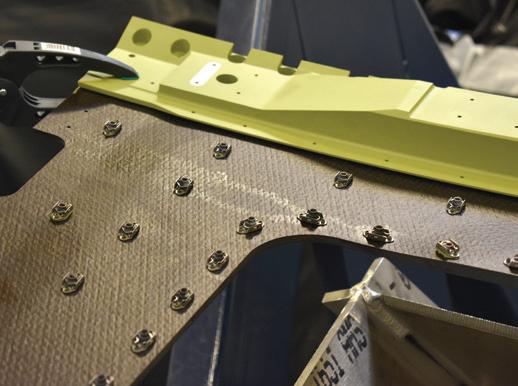
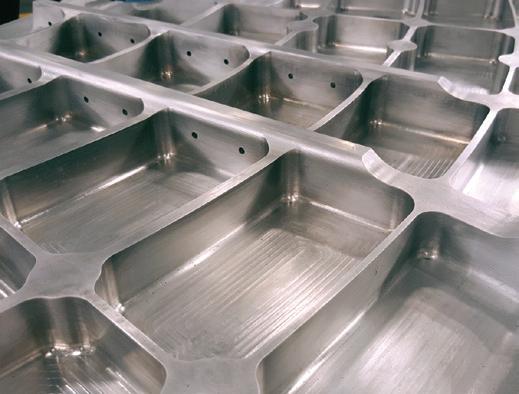
► Janicki Proprietary 5-Axis Machines ► Envelope size up to 80′ × 15′ × 6′ ► +/- 0.002″ Accuracy ► Fly-Away Parts and Assemblies ► State of the art Laser Metrology Inspection ► Production machining and specialty parts ► Design and Fabrication of Factory Integration Tooling
Serving commercial aerospace, military aircraft, and space exploration
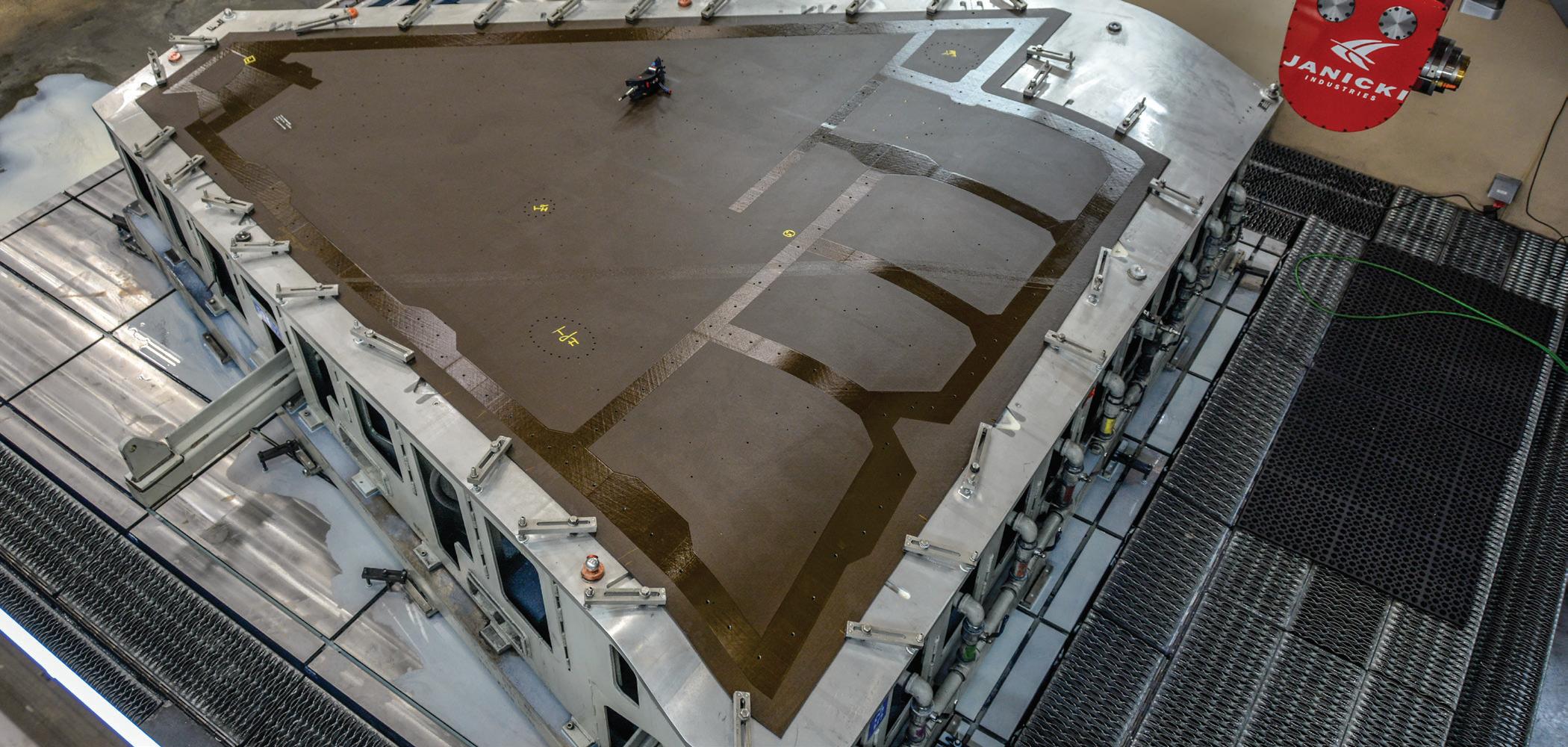
Exciting Career Opportunites
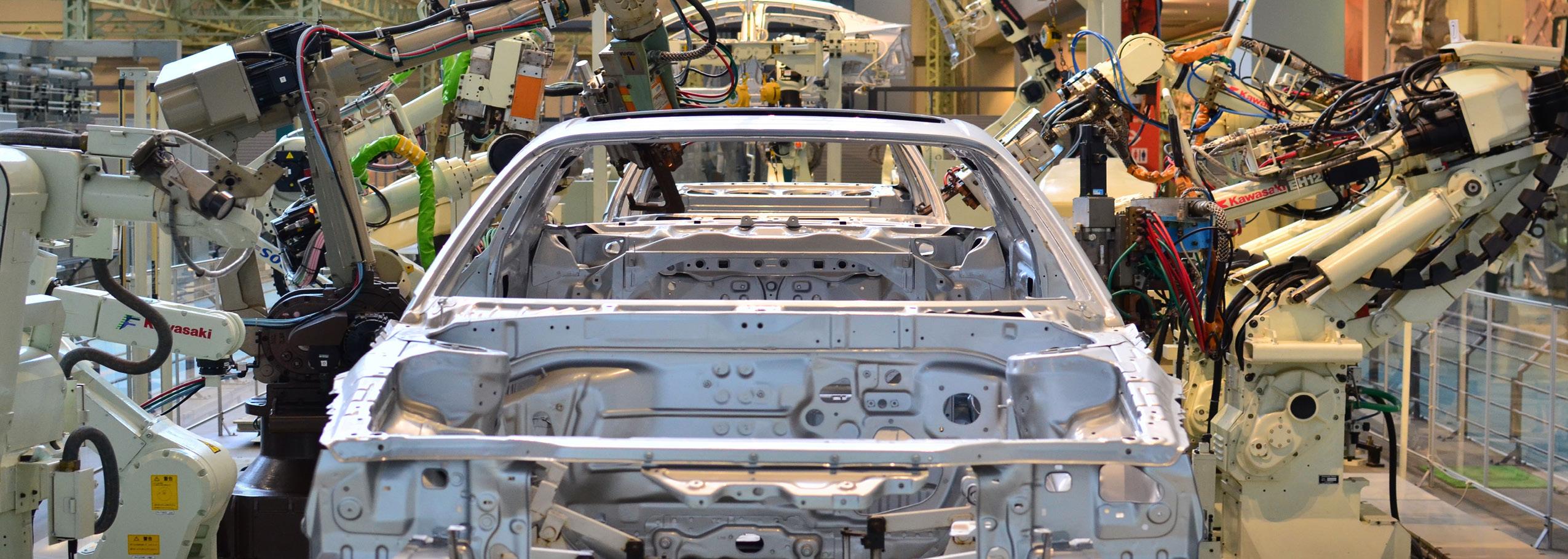
Adapting to Supply Chain Shake-Ups
With expert insight from Win Jeanfreau, Executive Director of iMpact Utah.

From bottlenecked ports in Los Angeles to labor shortages across almost every industry, the ripple effects of COVID-19’s impact on supply chains are evident and real. And unfortunately, there is no guaranteed return to business as usual anytime soon. So how can manufacturers adapt and stay competitive? Win Jeanfeau, Executive Director of iMpact Utah, offers key insights and takeaways for manufacturers looking to stabilize their supply chains and avoid disruptions in the future.
It has been said ad nauseam that the pandemic has brought about unprecedented times. But Win Jeanfeau, a successful entrepreneur who is no stranger to optimizing supply chains, points out that there is some precedent we can learn from—specifically, the 2011 Tohoku earthquake and resulting tsunami in Japan.
Much like the pandemic, the 2011 tsunami in Japan was an unforeseen disaster that not only killed thousands of people but devastated manufacturing supply chains too. Toyota, who had pioneered the just-in-time inventory (JIT) process, lost a vital chip maker in their supply chain. As a result, Toyota recognized the fragility of their JIT model. As a result, they reevaluated their supply chain philosophy, informed by this disruption. As a result of their evaluation, strategic reserves for certain elements of their supply chain were identified and upper limits increased. One of the items identified as critical and difficult to replace were chips for the computers in their automobiles. Toyota created a surplus of computer chips so they would be ready to respond should they lose such a vital component of their supply chain again.
Making JIT inventory more robust. Toyota’s preparation following the tsunami has now paid off. While most car manufacturers have had to slow or halt production due to the computer chip shortage brought on by the pandemic, Toyota has thrived. “They’re the only car manufacturer that’s been able to make cars in the last year because they had all the parts and pieces in strategic reserve,” Win says. “Nobody else did.”
While disasters like tsunamis or pandemics have revealed the fragility of bare-knuckled JIT inventory, that does not mean JIT should be completely abandoned. Instead, Win refers to pre-tsunami JIT as being version 1.0 of a lean manufacturing approach. Now, Toyota has shown us version 2.0 of JIT—one that is more robust by implementing strategic reserves and empowering manufacturers like Toyota to weather the storm.
Strategic JIT reserves are comprised of the key elements in your supply chain that are more difficult to replace in the event of a catastrophic event. Ask yourself: in the design of your product, what are those things that are challenges in your manufacturing now? Look for more than one way of designing that item. Identify if there is a substitute for that item that is more readily available without causing a declination in the quality of your product. And this leads to Win’s next bit of advice—consider sourcing that item locally.
Implementing domestic vertical integration. Another strategy for dealing with supply chain disruption is to implement, where possible, domestic vertical integration. In domestic vertical supply chains, manufacturers own it all, or at least the parts that matter most. Smaller manufacturers who can’t do that have begun to look for suppliers closer to home.
Domestic vertical integration has typically not been part of the initial calculations for manufacturers who are more inclined to pursue the shiny appeal of lowcost, overseas suppliers. But when measured by the risks to your supply chain, the true cost of relying on the panacea of Chinese suppliers is proving to be untenable. Win suggests that some manufacturers are now “realizing that a 20% increase in cost to buy domestically is probably cheaper than the time that it takes and the interruptions that can occur because I’m buying these things from China, or from Europe, or from Asia somewhere.”
In short, domestic vertical integration is about bringing your supply chain closer to home, and under more of your control, wherever you can.
Thinking ahead. If there is any silver lining to these supply chain disruptions, it is that manufacturers are learning how to make their supply chains more robust and less likely to falter in the face of catastrophe.
Implementing strategic JIT reserves and domestic vertical supply chains will inevitably lead to increased costs, and by some reports, we’re at least 3 quarters away from any kind of return to normalcy. But the challenge for manufacturers isn’t so much about how to return to normal, but rather, how to innovate and adapt. Win recommends looking towards advanced manufacturing approaches that can address supply and labor shortages. He names automation, “cobotics”, new synthetic materials, and 3D printing as the promising avenues for growth in manufacturing.
Things may seem daunting now, but remember that making decisions under stress perpetuates bad decisions. “This is a great time to go to that chi place where, rather than responding to a pandemic, you begin to think of a world beyond the pandemic,” Win advises. “The more of us that start planning for that, the more likely that future will manifest itself.”
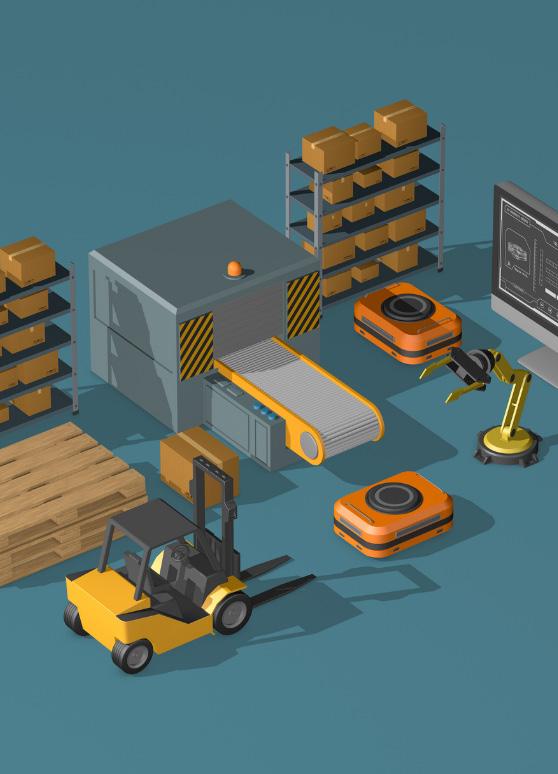
Visit impactutah.org to learn how Win Jeanfreau’s team can help your company survive, grow, and thrive.
Lockton Companies grows Salt Lake City operation
Offering deep risk management expertise to Utah manufacturers
SINCE EXPANDING INTO UTAH IN OCTOBER OF 2019, LOCKTON, THE WORLDS LARGEST PRIVATELY HELD GLOBAL INSURANCE BROKER, HAS STEADILY GROWN ITS SALT LAKE CITY-BASED OPERATION. LOCKTON’S INCREASED PRESENCE IN THE AREA HELPS MANUFACTURING COMPANIES IN ALL SECTORS ADDRESS RISKS RELATED TO THEIR BUSINESS. FROM PROPERTY/CASUALTY TO EXECUTIVE- AND HUMAN-BASED CAPITAL RISKS, LOCKTON PROVIDES CLIENTS THE TOOLS AND RESOURCES NEEDED TO MAKE THE MOST INFORMED DECISIONS.
Anthony Jensen, a 13-year insurance industry expert, leads the Salt Lake City office. Specializing in MFG, Jensen develops unique risk management strategies for all types of manufacturing clients, from food and beverage to aviation/aerospace to outdoor sports and recreation.
Jeff Bryant joined the team in March of 2020. Bryant has more than 30 years of industry experience developing comprehensive risk management programs to protect his clients’ balance sheets. He specializes in real estate, manufacturing, tech, healthcare, education, and construction.
“This team is proud to help our clients ensure risk resilience by understanding their business and industry issues. We provide the tools and guidance our clients need to avoid disruption and capital losses,” says Jensen. “At Lockton, we work hard to become an extension of our clients’ risk management teams and protect their businesses and employees as if they were our own.”
With Lockton, you get something you may not be used to with insurance — creative thinking and an unmatched commitment to client success. Lockton’s team brings global resources and capabilities to Utah’s strong manufacturing community. The best and brightest are drawn to Lockton because they want to make a difference. They’re voracious doers who know how to help clients respond quickly to changing markets and offer the deep industry expertise needed to navigate these complex times.
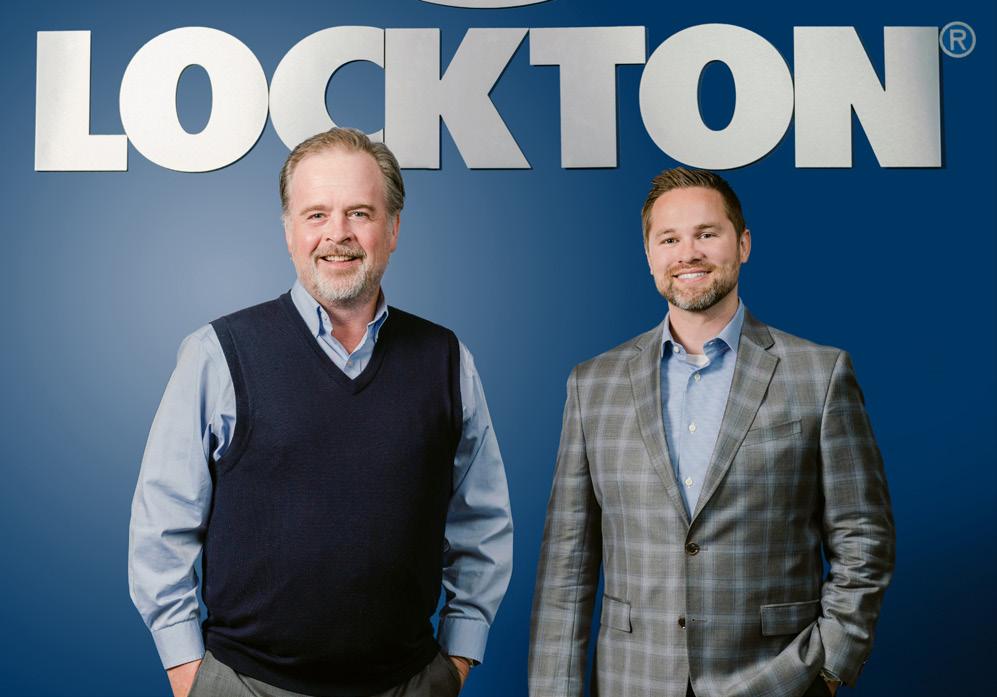
Lockton Salt Lake City
111 E. Sego Lily Dr Suite 190, Sandy, Utah 84070
anthony.jensen@lockton.com | 801.601.5366 jeff.bryant@lockton.com | 801.601.5447
Independence changes everything.
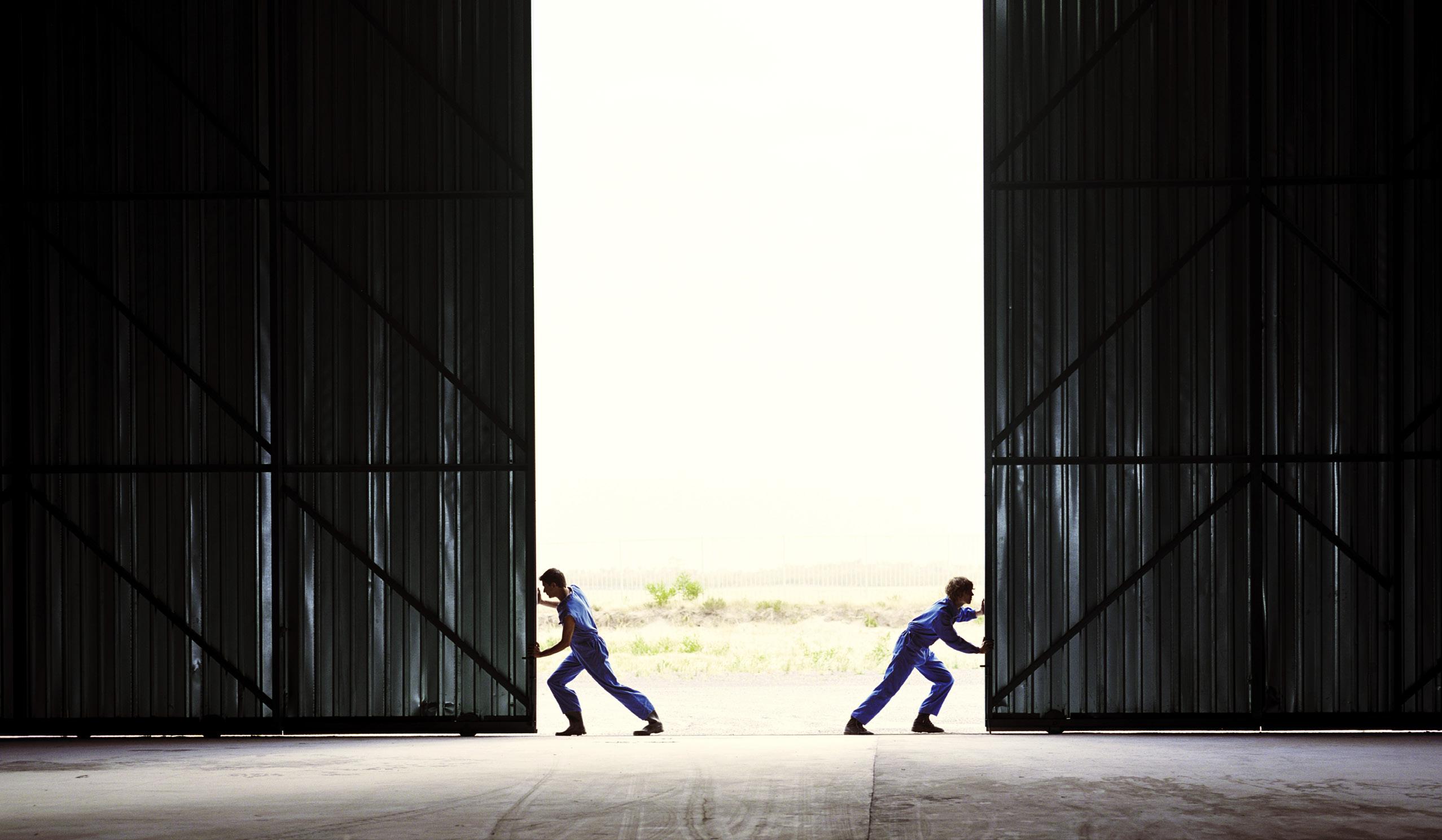
As the world’s leading independently held insurance broker, we answer to no one but our clients. Our private ownership ensures our people are empowered to focus on doing what’s right for clients. Lockton is ready to challenge whatever risks clients face — and unlock opportunities to help them move forward.
SAY YES TO SAVINGS!
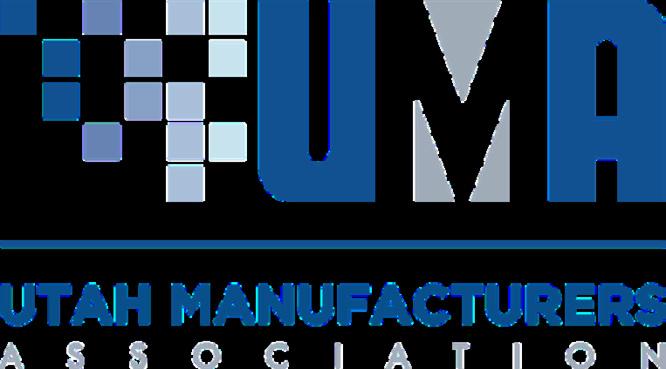
Utah Manufacturers Association Affinity Programs
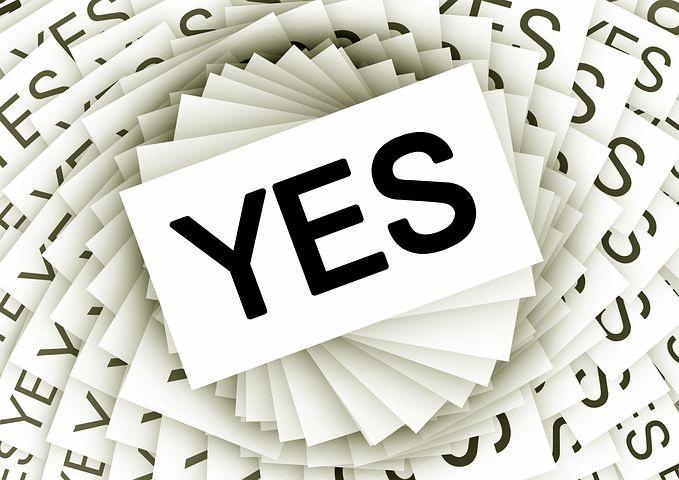
Healthy is on the horizon.

We’re committed to helping you live the healthiest lives possible.
PRSRT STD US POSTAGE PAID SALT LAKE CITY, UT PERMIT NO. 508


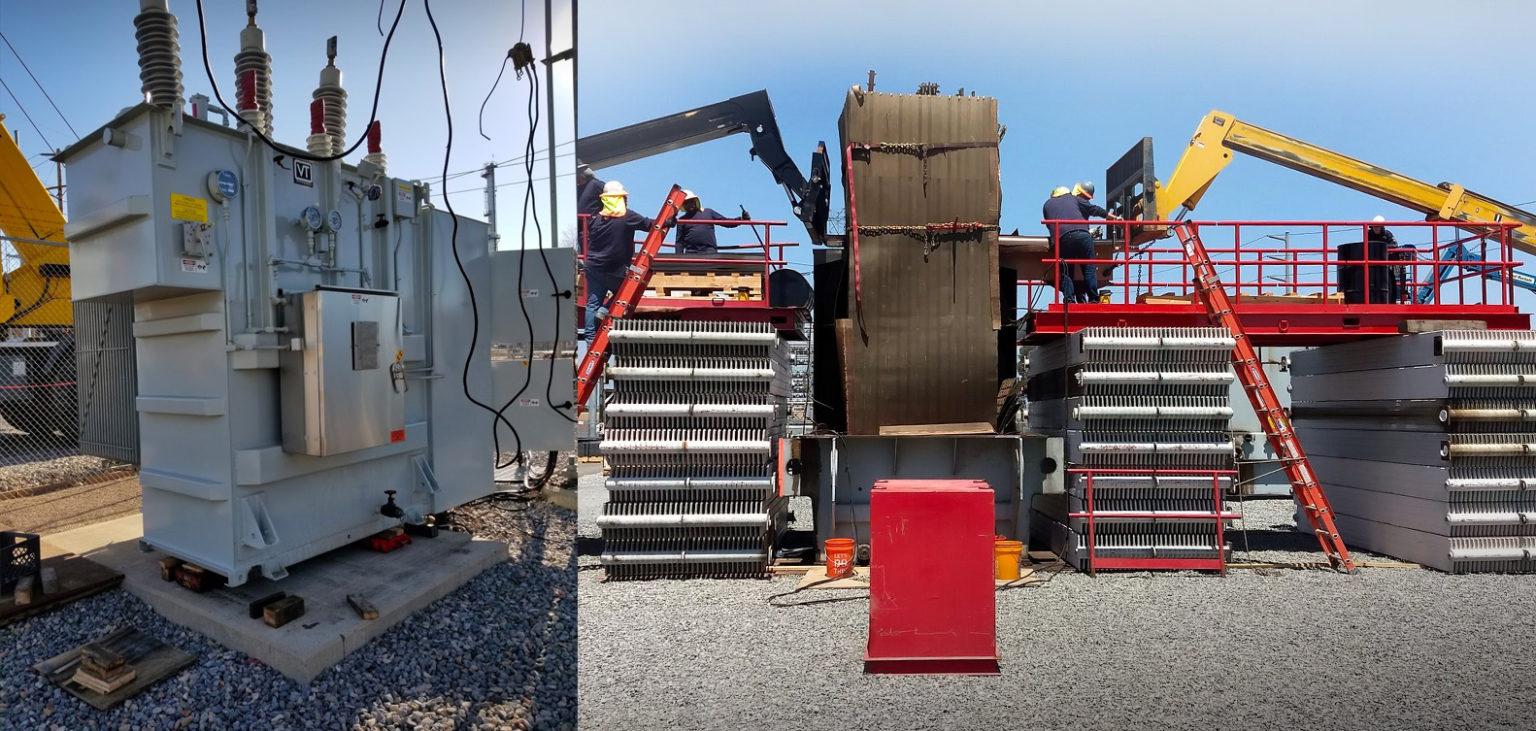
Intermountain Rigging and Heavyhaul
Contact IRH Today! 800-334-2409 irhusa.com
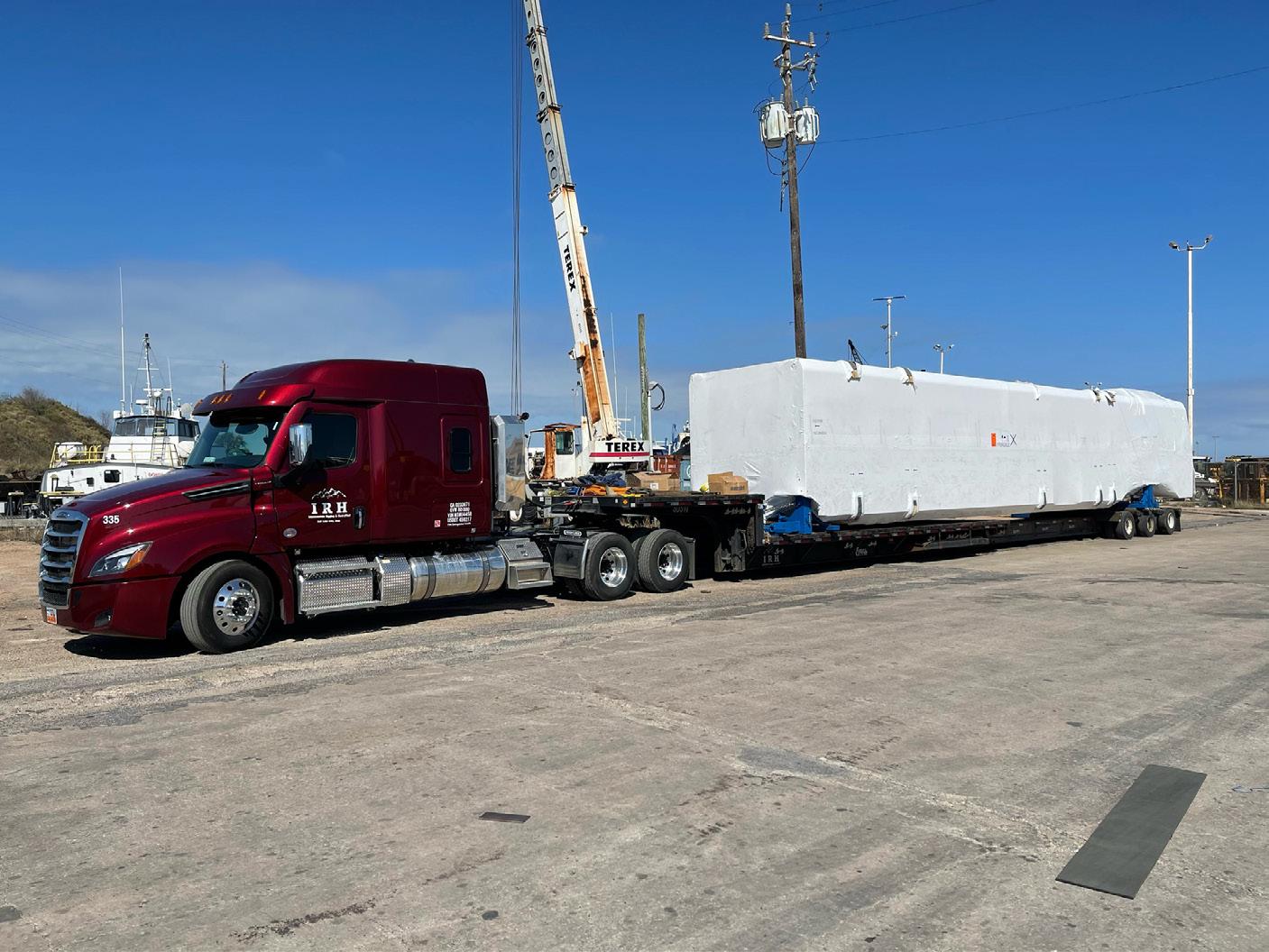
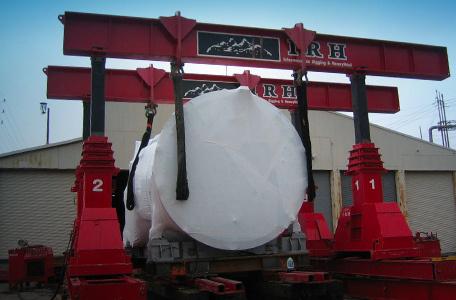
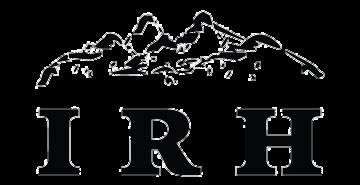