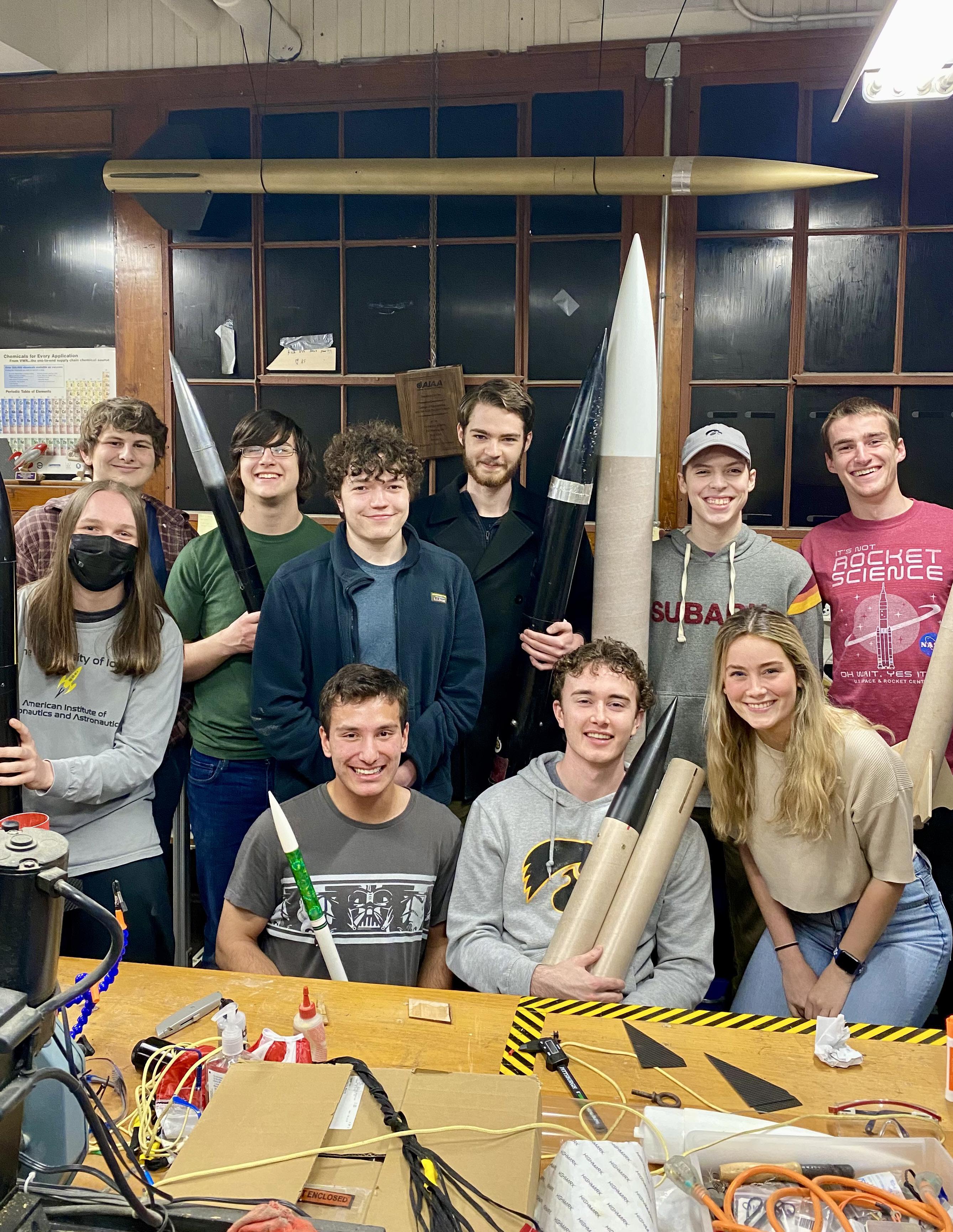
6 minute read
IOWA ROCKET CLUB
ROCKET CLUB: THE SKY IS THE LIMIT
The University of Iowa chapter of the American Institute of Aeronautics and Astronautics, AIAA or Rocket Club, for short, serves as a collaborative hub for Iowa’s aerospaceinclined students. Through its annual rocketry projects, the members of AIAA gain hands-on experience in the conceptualization, design, manufacture, and launch of high-power solid-fuel rockets. The club competes in the Midwest High-power Rocketry Competition hosted by the University of Minnesota in North Branch, MN. After a twoyear COVID-caused hiatus, the competition has resumed for the 2021-2022 school year and AIAA is hard at work on this year’s launch vehicles.
Advertisement
Although under the umbrella of the Department of Mechanical Engineering, the club is open to all majors, and members come from a wide array of educational backgrounds. Representing physics, astronomy, and five different types of engineering, club members use their combined expertise to develop aerodynamic airframes, custom-built avionics, and secure recovery systems for each rocket. While a successful launch is the ultimate goal, the knowledge and experience gained from participating in a long-term engineering project from start to finish is the most significant and persistent impact of the club’s work.
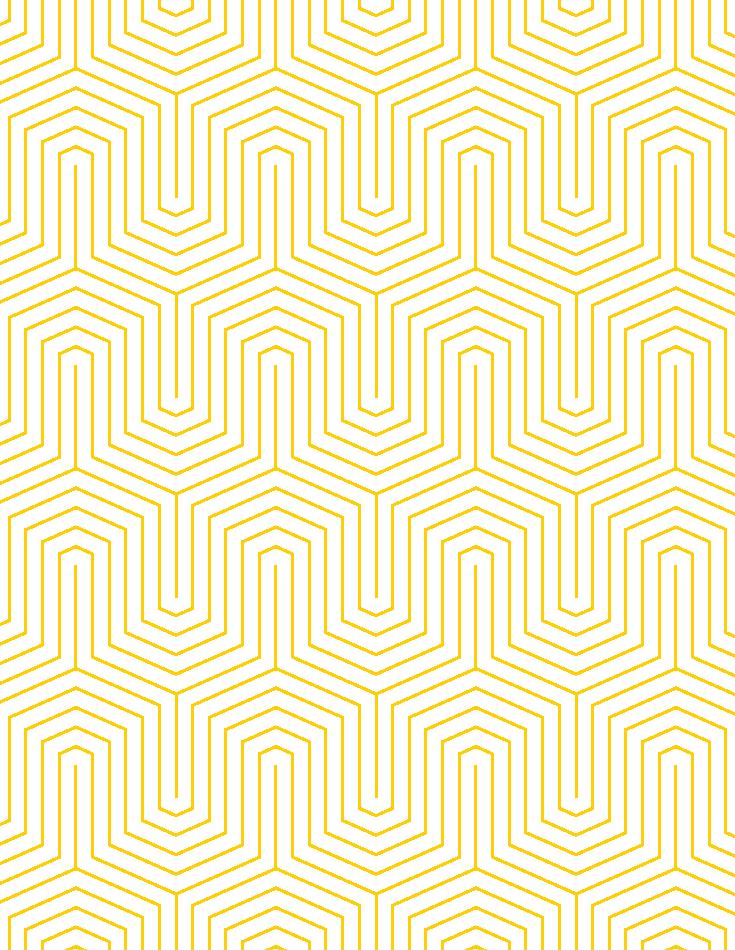
This year, the competition has challenged teams to develop a fleet of rockets technically diverse from one another. After a crash course (no pun intended) on rocket science for new members, AIAA created a set of unique and challenging problems to be consolidated into projects. Club members have been divided into three main teams, one for each group-constructed rocket. For the duration of the fall semester, each sub team identified the key design components associated with each project and conceptualized actionable technical solutions, which they have spent the spring semester building and refining.
Undertaking a unique challenge this year, the club is constructing a rocket entirely through the use of 3D printing. Named “Project Hammerhead”, the rocket will have an active flight control system, allowing for the rocket to achieve stability in a controlled fashion during flight. 3D printing a rocket allows for a great degree of flexibility in manufacturing but also creates several challenges for the team including maximum part size, thermal considerations with the propulsion motor, weight distribution, and more. To address all of these properly, the team spent several months refining the solid model of the rocket and doing a wide variety of analyses.
“We started in a similar way as all the other rockets, modeling the rocket in an open-source design suite called OpenRocket, which gave us an idea of our performance characteristics,” said Jack Sieleman, club vice president and design lead for Project Hammerhead. “After that, we started making the parts in CAD and applying the correct masses and center of gravity locations to the model to make sure our stability was acceptable.” Ensuring the theoretical stability was important, but it wouldn’t matter if the 3D printed components couldn’t stand up to the forces acting on the rocket during flight. To solve this problem, the team turned to computational fluid dynamics (CFD). Knowing the rocket’s geometry and flight speed, the team was able to use CFD to study the aerodynamic stresses on the rocket and study the airflow over the fins, which is a critical step to ensure the operational capability of the active flight control system. After determining the stresses on the rocket, the team used finite element analysis, or FEA to apply the stresses to the rocket’s components and ensure no stresses would result in failure, and that no parts would deform during flight. Iterating through this process allowed the team to refine the geometry of each part to the best possible solution to maximize the rocket’s performance.
With each rocket focusing on unique design characteristics, another rocket named “Project Sneaky” aims to reach maximum speed and altitude results through optimization of its design. Through multiple iterations and precise detailing in OpenRocket, Sneaky is predicted to reach Mach 1.4—faster than the speed of sound—and a maximum altitude of 9,343 feet. With an additional focus on aesthetics, Project Sneaky will include custom carbon fiber fins, a clear section of body tubing, and a 360-degree camera. One of the main design challenges of Project Sneaky includes keeping the rocket stable at its simulated
supersonic speed. “Once rockets reach extremely high speeds, keeping the stability higher than normal and paying attention to problems such as fin flutter and increased drag forces are imperative to a rocket’s success,” explained Geraldine Kelderhouse, the club’s Treasurer and design lead for Project Sneaky. Kelderhouse also aims to analyze the effect of surface finishes on a model rocket’s drag coefficient as a class final project and apply the results to the club.
Another challenge for Project Sneaky includes securing the 360-degree camera safely inside the clear tubing while still allowing it to be detachable. Special pieces designed in Creo by project members have been able to get through these unique challenges. “The utilization of 3D printing has also been very useful for Project Sneaky, as multiple custom pieces have been easily modeled and fitted to design complications that arise in the build process,” said Ian Silva, a team member under Project Sneaky. One of Silva’s designs includes a special interlocking piece to keep multiple sections of the rocket together without applying permanent or external attachments. He credits intermediate design classes such as Product Design and Realization taught by Phil Deierling for teaching advanced Creo modeling and FEA with emphasizing design creativity. With an open-ended rocket design challenge, the members of Project Sneaky have been able to expand their modeling experience outside of class and actively problem-solve obstacles throughout the stages of rocket building.

One of the requirements of this year’s competition is a rocket that is built from a designated kit purchased from a vendor. All teams participating in the competition must construct the same rocket. To make it interesting, though, each team must improve on the original design as much as possible, as well as provide an estimate on flight metrics such as maximum altitude, maximum velocity, and total flight time to the best of their ability. The club’s version of this kit rocket, “Project Casanova”, aims to nail these numbers as close as possible. Some of the improvements to the kit include forged eye bolts, stronger kevlar shock cords, several redundant methods of obtaining precise and accurate in-flight data, and wrapping the provided plywood fins in fiberglass. Though seemingly small and insignificant on their own, Project Casanova’s improvements aim to significantly improve the rocket over its original performance level.
In January, the club received a grant from the Iowa Space Grant Consortium (ISGC) for $4,100 to enable the club to compete in this year’s competition. These funds were used to purchase the material and equipment used to make all of these projects possible. For the grant application, as well as the competition itself, extensive documentation was written to show the design, manufacturing methods, and expected performance of each rocket.
In addition to technical projects, AIAA puts a focus on professional development as a chapter of a national-level professional organization. In the Spring 2021 semester, the club hosted the Region V Student Paper Conference, a region-wide aerospace research symposium facilitated by the national organization. In part due to participation in the club, members have been able to secure internships and post-graduation full-time positions at companies such as Collins Aerospace.
“The University of Iowa doesn’t have an aerospace engineering major,” said club President Kyle Lastine, a computer science and engineering major, “but for a group of students with diverse technical backgrounds like software, hardware, or physics to work on a project like this, I think that’s even better.” This year’s rocketry projects are nearing completion, and their launch will mark the first competition entry for the club in quite some time. In the coming years, the club hopes to reach new heights with expertise gained from participating.
The University of Iowa doesn’t have an Aerospace Engineering major, but for a group of students with diverse technical backgrounds like software, hardware, or physics to work on a project like this, I think that’s even better.
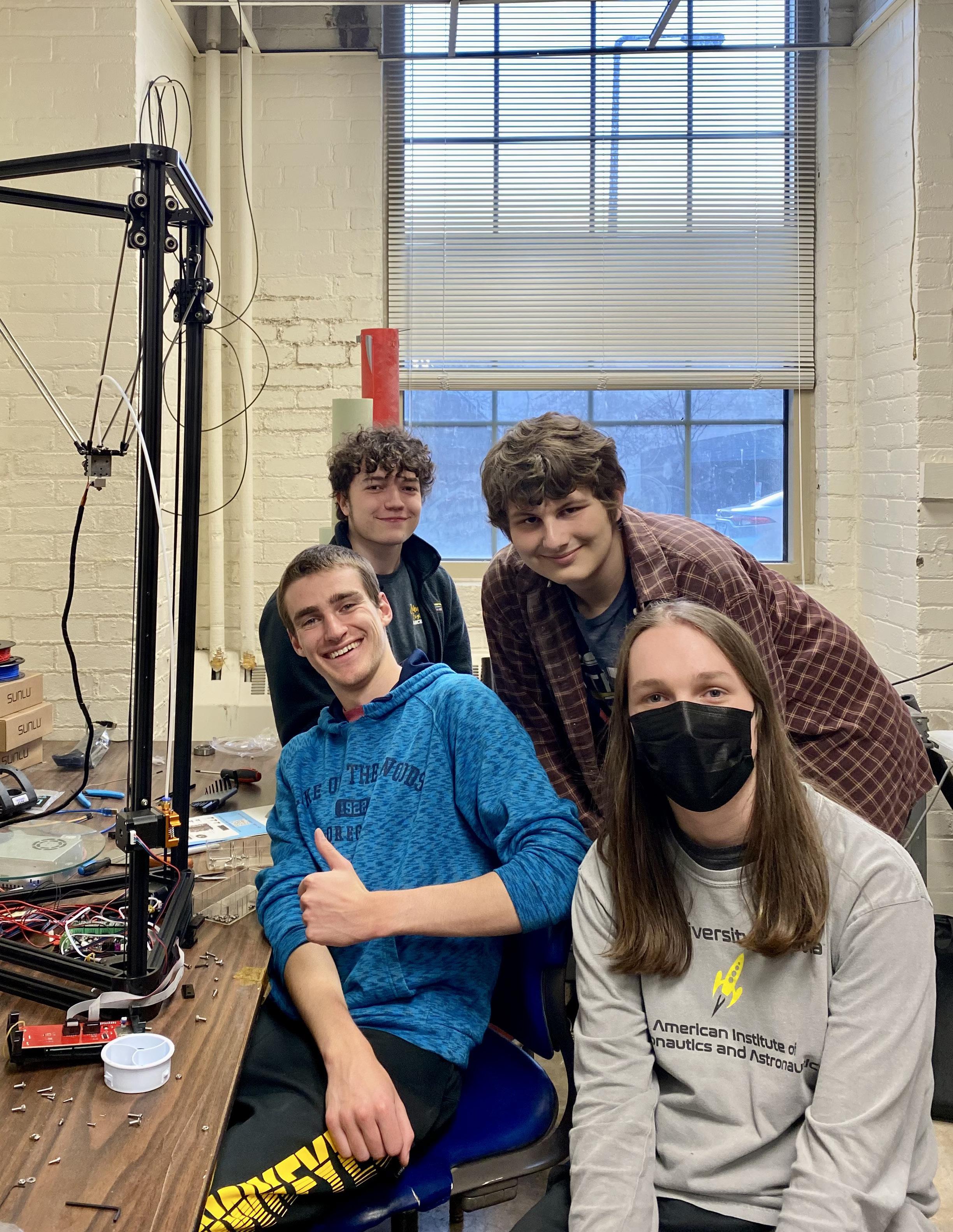