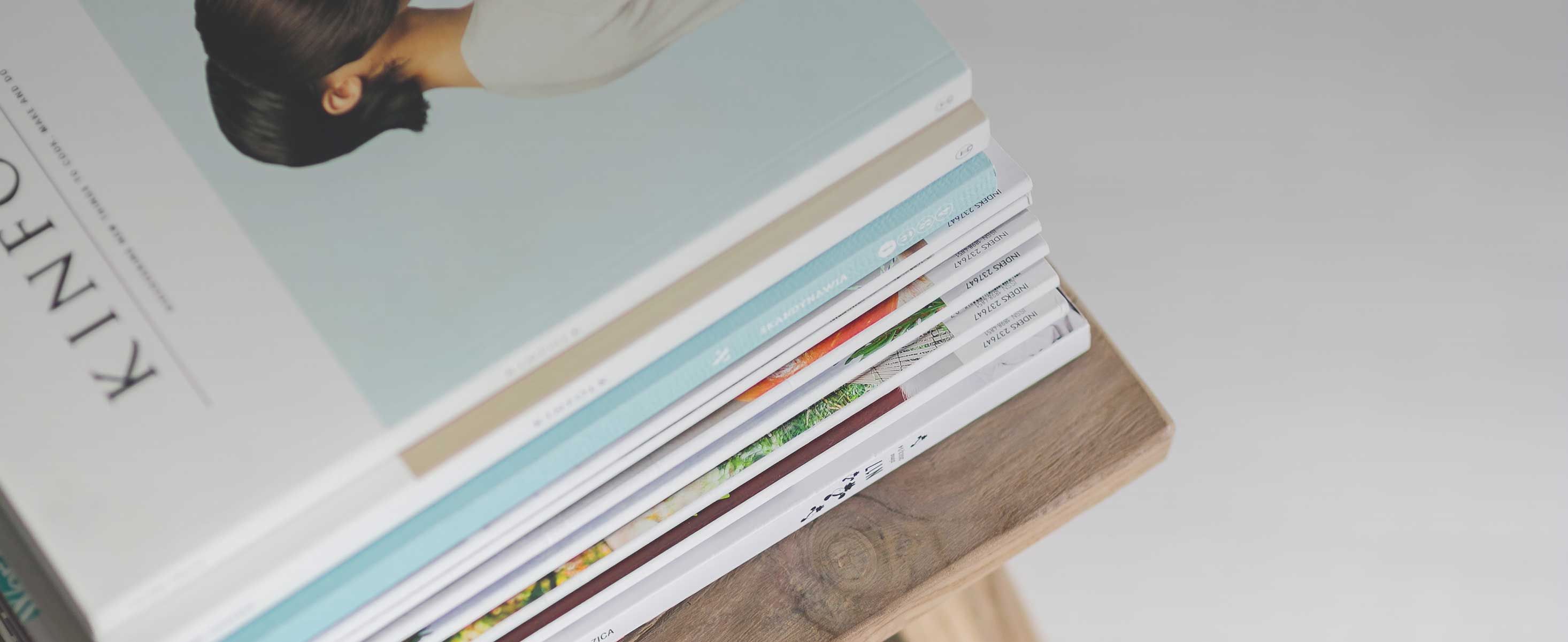
1 minute read
Root Cause Analysis of Metal Part Performance: An IMS/IAP Sample Project
From the Institute of Materials Science
One of the most common requests IAP receives is to determine the root cause of the poor performance of a product in the field. In a situation such as this, IAP typically will bring IMS technical experts and the company together to understand what information is available. To be able to determine the appropriate analyses, we often ask the company the following questions:
Advertisement
• Are the parts/materials from the same supplier?
• Are they from the same batch?
• What are the specifications supplied with the parts/materials?
Based on the answers and the type of material, we develop an approach. For example, in 2022 we were asked to identify the cause of a performance difference between two supposedly identical metallic samples, one of which was causing a significant problem for the end-use customer. The samples (shown below) were from different suppliers. They were specified to be carbon steel with an exterior hardened to a certain thickness. IAP engaged one of its metallurgy experts and we put a plan together:
• Examine the parts with optical microscopy to look for obvious defects
• Determine the overall elemental composition with SEM/ EDS
• Pot, polish, and etch the parts to examine grain structure to determine the thickness of the hardened layer
• Measure the hardness of different areas of the parts with micro-indentation
• Elemental composition from SEM/EDS showed an unusual amount of copper in one of the parts.
The Results of the characterization were as follows:
• Optical microscopy showed both materials were of good quality with no major defects.
• The normal etchant used for carbon steels did not work with the copper-containing part, and a more aggressive etchant, normally used for stainless steel was used. The microstructure of the polished parts showed the hardened outer layer of the part with copper (left) was much thinner than that of the carbon steel (right).
We were able to conclude the following from as a result of our characterization of both samples:

• The alloys of the two batches of parts were different, though they both met the criteria for the specific steel.
• Both alloys had been hardened similarly.
• The sample that was poor-performing had a notably higher Cu content.
Based on our characterization of the samples the company was able to go back to their supplier and modify the part specification to improve its performance consistency in their customer’s application environment.
IAP routinely works to resolve challenges such as this. Difficult problems such as this often require numerous techniques, and technical experts who can draw valid conclusions by putting together the different pieces of the puzzle.