
4 minute read
National Capital of High Temperature Ceramics
A unique title to crown valuable ceramic talents
If today the ceramists from Cunha are living in full ascension, this artistic recognition is due to a past of constant overcoming. The city brings together more than 100 potters, dedicated to the authorial practice produced in their own ateliers. A conglomerate of artists from different cultures, origins, languages, and thoughts that harmonize, forming one of the largest and main poles of Brazilian handmadeceramics. The first ceramists dedicated to high temperature ceramics came from Japan, Portugal and Brazil. Each with individual preferences, cultures, techniques, and languages. They settled in the city and remained, adopting Cunha as a " new homeland".
Advertisement
Cunhaisrecognizedasthelargestcenterof artistic ceramics in South America, gathering six examples of Noborigama kilns, besides having the only Smokeless kiln in the country. The diversity of influences stimulated the mixing of various techniques, mixed with different styles and ways of firing the clay and transforming it into pottery, at high or low temperature.
In Cunha, we find the largest concentration of Noborigamas in Latin America
Noborigama is a kiln typically used to fire ceramics at high temperatures. It unites two terms of Japanese origin: Nobori = ramp; and Kama=Furnace. Rule of the Japanese language: it's used as "gama" in the final word.
A primitive kiln, very well known in Japan, for the production of handmade ceramics, its origin is actually Chinese. Cunha gathers a collection of six specimens, which places the city as the leader of the largest concentration of Noborigamaskilns in Latin America, in a single city.
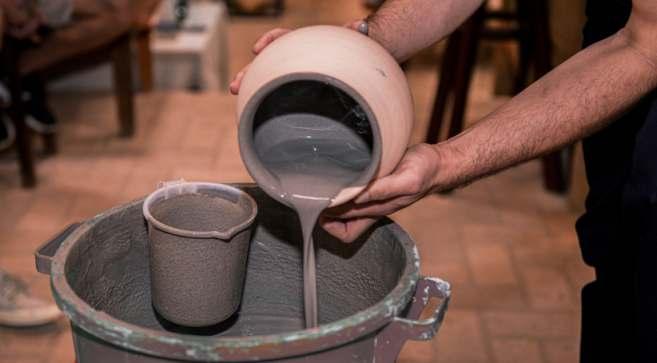
The Noborigama burning process can reach up to 1400ºC, with the use of reforested wood. It can have from 3 to 20 chambers, and is always built on a sloping terrain. The topography of the terrain is impor tant to optimize the heat distribution among the pieces organized inside the kiln.
In 2023, Cunha celebrates 48th anniversary of the Noborigama kiln in Brazil. In the city, we can find examples with 3, 4 and even 7 chambers, with differentcapacitiespercubicmeter.
Fire without Smoke?
In 2017, one of Japan's most respected masters visited Cunha. Sponsored by the ICCC master Masakazu Kusakabe built a wood oven without smoke emission, called Sasukenei Smokeless Kiln, whose operation respects Japanese ancestral techniques.
Cunha, therefore, is home to the first and only Smokeless kiln in Brazil, built with 35 thousand bricks and able to fire more than 300 ceramic pieces, depending on their size.
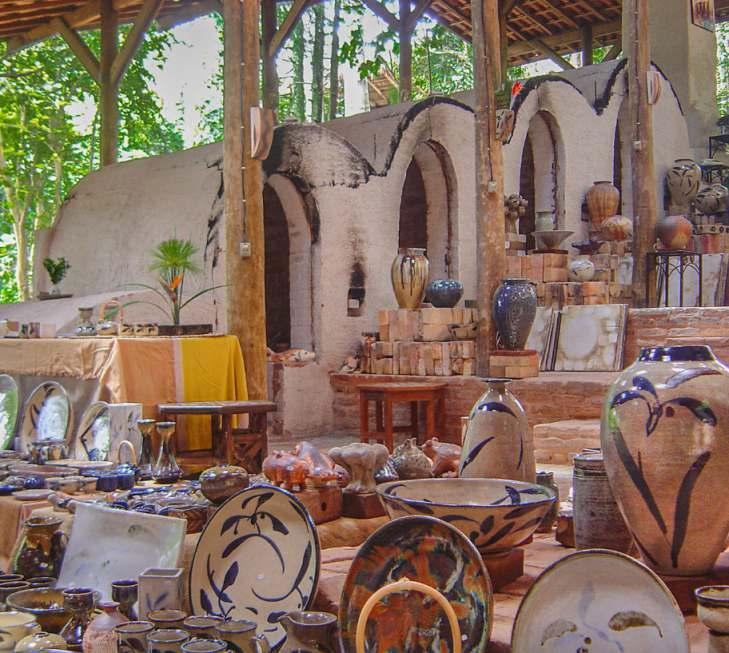
Vargem do Tanque Ceramics
An example of determination and sustainability
The artisanship of the potters, dating back to the end of the 17th century, arrived in Cunha in the 1940s, also experiencing the phases of the traditional potteries, producers of red bricks made one by one by hand.
Inspired by this tradition, the Cultural Institute of Ceramics of Cunha started in 2016 a project exclusively for rural communities, where the land ensures the livelihood of the residents. With support from private enterprise, the institution implemented a course for the community of Várzea do Tanque, with the intention of giving continuity to the conceptual and technical world, contained in the heritage ofthepottersofCunha.
A team of teachers, all potters associated to the ICCC, moved from the center to the ruraldistrictofVargemdoTanque,toteach a basic course in low temperature pottery, based on local resources, making the projectself-sufficient.
From this initiative came a group of professionalized ceramists, organized as a cooperative, with a technically and financially sustainable production, culminating in the Vargem do Tanque Ceramics,gathering15ceramists.
In 2023, the group developed an independent project, with support from the ICCC, creating the Vargem do Tanque Ceramics Expansion Course, aiming to add to the community a contingent of 12 new ceramists, graduated in the second half of the same year. The group represents the third generation of local potters, with participations in fairs and exhibitions all overSouthAmerica.
Among the many activities of the ICCC, the incentive to research and build wood-fired kilns is one of the main activities, culminating in the formation of the Vargem do Tanque Ceramics, specialized in wood-firinginpre-Columbian kilns.
The National Capital of High Temperature Ceramics is the only national center that concentrates all the modalities of artisanal ceramics, supported by the different firings: wood, obvara, raku, electric,gas, hole, salt orpre-Columbian.
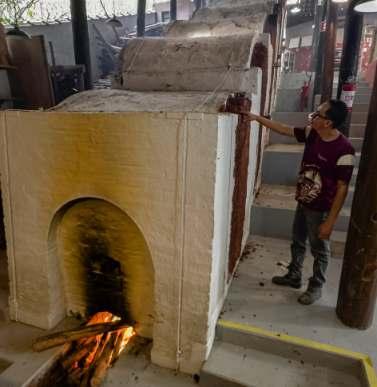
Hole burning and saggar?
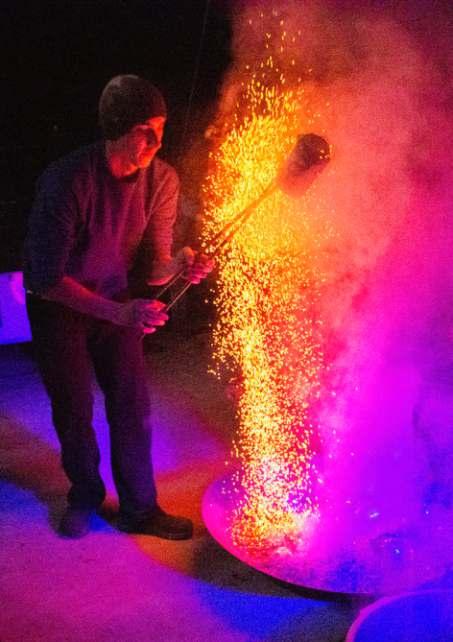
In Cunha, everything is possible when it comes to artisanal ceramics. And pit-firing consists in arranging the ceramic pieces in a pit in the ground. Over them, the potter spreadsfirewoodandorganicmaterials. It is one of the oldest firings in the history of ceramics. It reaches a maximum of 900ºC.

Saggar, or salt firing, has sharpened the creativity of the Cunhense potters, who use this adapted hole firing. Saggar is usually done in a gas kiln. However, in Cunha, an adaptation accomplishes this process in practically the same fire. The firing lasts between two to three hours, withtotalutilization-ofthefire'spotential - to print in the ceramic piece totally unexpected effects, with color nuances andsurprisingsmokyeffects.
To finalize the finishing touch, after the pieces are removed from the hole, they are carefully washed. Hours later, they receive an application of carnauba wax or beeswax, which accentuate the coloring obtainedbytheflames.
Enough with the burning?
In Cunha, there is always one more alternative
PLittle is known about the Obvara firing, which is totally unusual and provides unpredictable effects on the ceramic surface. Research indicates that it is a procedure that originated in the 12th century, in Central Europe, more precisely in Belarus and surrounding cities. In Cunha, it is usually presented to the public through events promoted by the Instituto Cultural da Cerâmica de Cunha or at ceramics festivals.
Next to the oven, a bucket is placed with a liquid mass that receives the ceramic piece. The container holds a preparation made with flour, water, granulated baking powder, and sugar. This liquid mass ferments and is used to dip the pieces one by one. With a long pair of tweezers, the piece is removed from the kiln, and immersed in this liquid, and then in water, to induce a reduction, generating different effectsintheceramic.
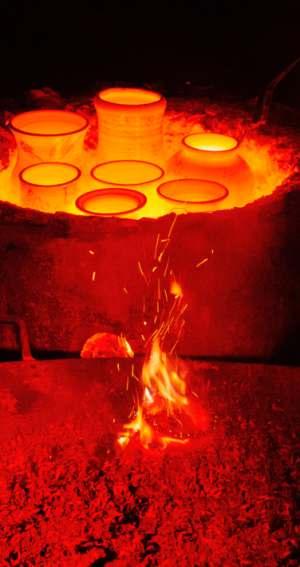
Historically, the ceramics practiced in Cunha began in the genuine Brazilian techniques of low temperature firing. Local potters have extended the traditions, maintaining the balance of technical knowledge between ceramics produced in high or low temperature firing, preserving the authenticity of h contemporarylanguage.
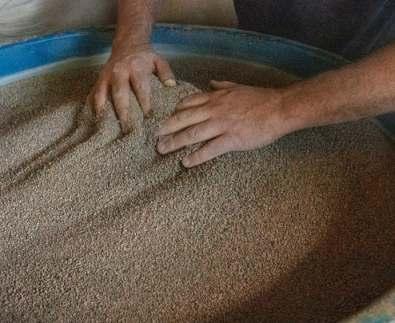