
7 minute read
Project updates
DC MOTOR REPAIR and OVERHAUL
WEBB ELEC REPAIRED A 100KW Leroy Somer DC motor from a steel processing company which needed a thorough overhaul and rebuild.
The motor was fully dismantled, and it was clear that although it was still running, it needed a complete overhaul to place it into good working condition.
Once degreased and stoved, the field and interpole windings were Baker tested with step voltage, surge and hi-pot to ensure the winding insulation was adequate with regard to earth protection and to ensure that there was no insulation failure between turns of wire within each coil.
The armature coils were also individually tested and re-insulated, and the commutator machined because the brushes slowly wear grooves into the copper segments, which can cause problems with the commutation when new brushes are fitted, such as sparking and overheating. The aim is to remove as little copper as possible when turning the commutator down, as this can only be machined a finite number of times before it is too small to be serviceable.
Each separate bar on the commutator is connected to several copper coils in the armature, and in between each segment is a mica insulator. The mica is harder than the copper and has to be undercut, where a small blade is run down the slot to cut down the mica below the level of the softer copper segments. It also removes any possible shorts between the segments which may be present after the machining process.
If this is not done, as the copper wears the mica will sit proud and the brushes will begin to bounce over the commutator, eventually breaking or causing sparking and serious electrical issues.
The carbon brushes are housed in the brush gear, which usually comprises four separate arms – sometimes more on larger machines. Each brush box contains a spring to maintain constant pressure on the brush while it creates a circuit on the commutator. This motor’s brush gear was cleaned, degreased and tested to ensure the insulation was fully serviceable.
After this, Webb Elec’s standard sequence of mechanical checks was carried out to ensure bearing journals and housings had not worn, along with drive shaft diameter and keyway. The armature was then dynamically balanced, the windings re-insulated, and the bearings replaced with high-quality SKF bearings. The last item was the force ventilation fan blower which was fully overhauled with a new motor fitted and the impeller balanced.
Once assembled, the motor was fitted with a new set of carbon brushes and run throughout its speed range in both directions ensuring the brushes were correctly bedded into the new commutator profile.
www.webb-elec.co.uk
PAINT SHOP FAN BREAKDOWN REPAIR
WHEN A MARKET LEADER IN PAINT shop design and manufacture experienced an untimely and frustrating paint shop fan breakdown during a crucial production run in its busy workshop, it turned to Gibbons Engineering Group for help.
The client advised that returning the fan to normal operation was urgent and that downtime must be kept to an absolute minimum, so the immediate collection of the fan from Milton Keynes was arranged.
The fan was inspected, and the motor was found to have an earth fault. The fan had seen plenty of service, resulting in a significant build-up of debris on the impeller blades.
Gibbons’ engineering team stripped the fan to its component parts, ready for repair. Whilst the special fan motor went through its in-house rewind shop for repairs, the other parts were shot blasted and coated with a hard-wearing finish ready for reassembly.
The fan was rebuilt and tested before the entire assembly was returned to the customer.
If the uniquelydesigned motor had been replaced rather than repaired, a lead time of 13 weeks would have been required, but Gibbons was able to return the plant to service within just a few days.
Engineering Services Manager, Matthew Gibbons, was delighted with the outcome: “We understand that a paint shop fan breakdown can be a very stressful and costly situation for our customer, who is naturally concerned that its production could be interrupted for weeks. Therefore, it’s always satisfying to be able to turn a repair round in such a short time and get our customer’s plant up and running.”

A global leader in coil manufacturing for over 50 years
Providing superior quality, high voltage coils with the lowest Partial Discharge levels and best Tan Delta Results in the industry. As an independent coil manufacturer we are a trusted partner to the largest OEM’s and rewind shops around the world.
E: coils@preformedwindings.com | T: +44 (0) 114 248 4391 www.preformedwindings.com
AW_PW_Half_Page_Ad.indd 1 21/05/2021 15:50

EXTEND MACHINE LIFE WITH THE N330
The N330 is our new dual channel, portable vibrometer designed to help you to identify vibration issues in the most convenient manner. The instrument is capable of both single and two-plane balancing as well as FFT, Smart Analysis, Vibrometer and Tachometer. Thus enabling you to best pursue a proactive, preventative maintenance routine to limit production downtime and extend the life of your machines. And all backed up by the most comprehensive support and parts service available in the UK.

Q&A In this issue of Renew, Matt Fletcher, MD of Fletcher Moorland Ltd, answers questions around the correct approach to greasing electric motor bearings.
QUESTION: Should I grease the bearings on all motors at my site on a scheduled basis – such as every day, week or month?
MATT FLETCHER: Generally, bearings in electric motors do need greasing; however, just doing something because you believe it's right may have unintended consequences. Take the motor pictured here, which came into our workshop recently. The person tasked with greasing this electric motor's bearing thought they were doing the right thing. However, in this example, over-greasing has caused the bearing to fail. When my team stripped down the motor, they discovered the excess grease covering the motor internals and the windings. It's a common sight in many electric motor repair workshops, and this is not the worst we've seen.
In typical grease-lubricated electric motors, a chamber holds the bearing; the grease for the bearing is enclosed in this chamber. New grease is fed in through an external port when needed. Many motors have an exit for the old grease to escape, however, it seems that many motors don't. Grease doesn't just disappear; it has to go somewhere. If the grease isn't coming out of the front of the motor, then it's passing through the grease chamber and into the motor.
Too much grease is as bad, if not worse, than too little grease in a bearing. What happens is the grease starts to churn, and excessive heat is generated. The operator notices this and thinks the bearing needs even more grease – a vicious and destructive cycle starts, which typically ends with a failed bearing and a stopped motor.
A secondary issue can also be caused by the grease coating the motor's windings. The grease can degrade the conductors' enamel coating, which can lead to a winding insulation failure.
It may well be that the operator who did this was under production pressures to get as much life out of the motor as possible, but it was only delaying the inevitable.
There is no one-size-fits-all approach to greasing motors, but greasing every day, week or month, whether the motor needs it or not, could be a recipe for disaster. What I would recommend is that you check that your greasing program is fit for your motors and their application. In all likelihood, this will mean different timescales for different motors. Most bearing manufacturers will offer charts that calculate recommended greasing intervals based on the bearing type, size, and speed of operation.
If you are feeding grease into a motor on a regular basis. Stop to think about where the grease is going. You could be doing more harm than good without realising it.
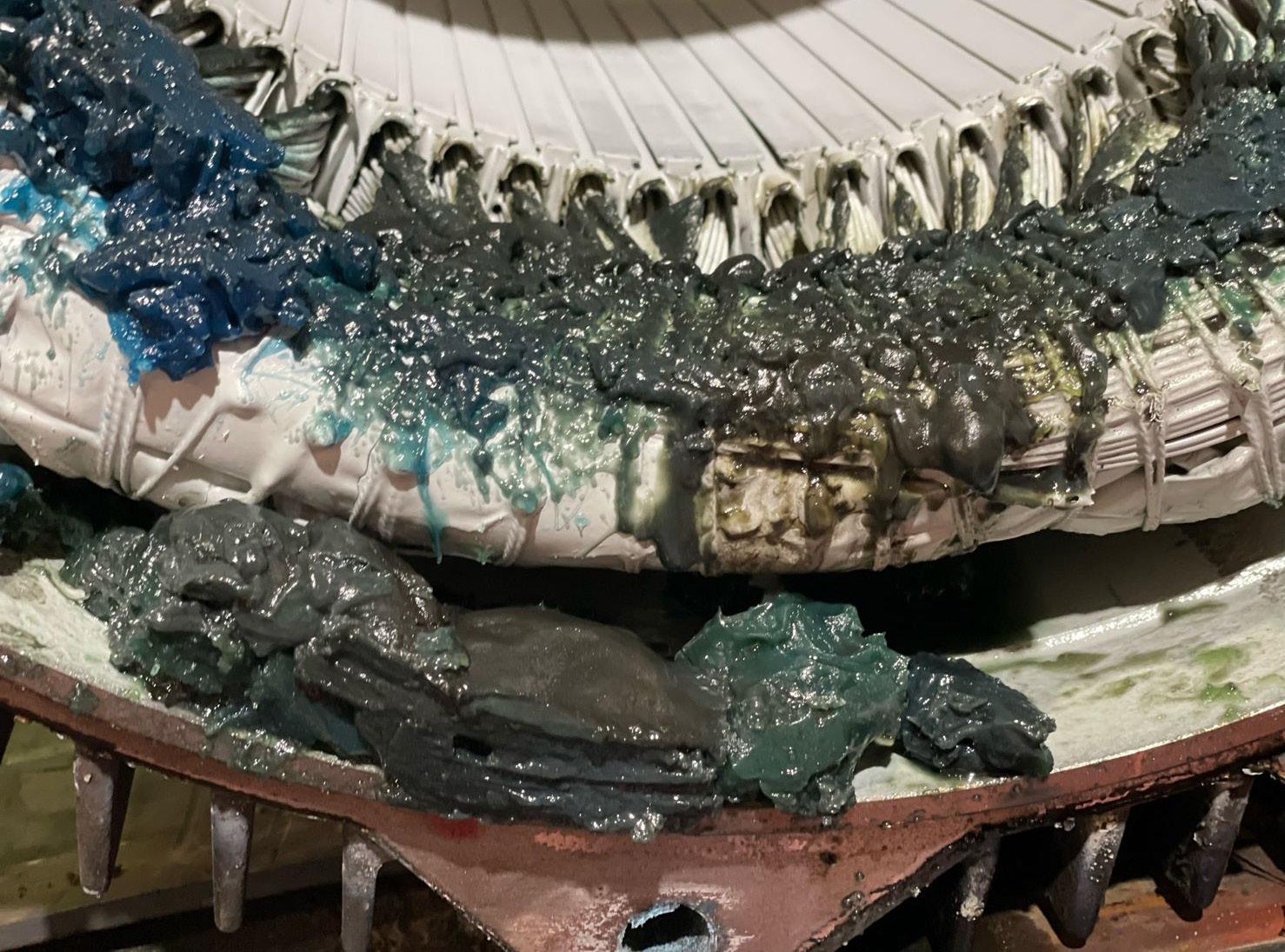
QUESTION: Do you think there could be a way to measure how much grease is in a motor? With sensors, perhaps? MATT FLETCHER: From my experience, ultrasound offers a good indication of whether a bearing has enough, too much or too little grease in it. It measures the ultrasound response to friction. From there, with a conditionbased approach, a set dosing of grease can be filled to the bearing. I don't think it's a matter of how much grease there is but 'the right amount', and that can be measured by sensors.
A lot of motors have 'sealed for life' bearings. That description is often misleading as it's the life of the bearing and lubricant that's referred to here (load and speed, of course, determine bearing life), not the life of the motor. So, there is a finite life for those bearings, typically of 2-5 years. I would much prefer to see an open bearing that can be properly lubricated, so the grease goes through the bearing completely and has an external grease relief. That way, a proper lubrication program can be followed, and the bearing can attain its design life – assuming proper fitting and alignment. TIMES-CIRCLE