6 minute read
NCAME Emerges as Significant Milestone
Next Article
By Michael C. Gabriele
The titanium industry remains on a quest to harness the potential of additive manufacturing. The journey has been long, but in recent years there have been significant advances in this field, with the promise that the complex technology can usher in a next generation of efficient, reliable, cost-effective commercial production capabilities. The International Titanium Association (ITA) has dedicated significant editorial coverage of this technology through its publication, TITANIUM TODAY.
The trek towards the goal of arriving at a much-anticipated “inflection point” for the technology has reached a major milestone, given the research, training and partnerships coalescing at the National Center for Additive Manufacturing Excellence (NCAME) at Auburn University, Auburn, AL.
By way of introduction, the center operates as additive manufacturing center of excellence, a collaborative effort among Auburn University, NASA, National Institute of Standards and Technology (NIST), and ASTM International, according to information posted on the group’s website (https://eng.auburn.edu/ ncame). In addition to conducting research to advance the technology, NCAME’s mission is to facilitate effective collaborations among industry, government, academia, non-profit organizations, and ASTM committees, ensuring a coordinated, global effort toward rapidly closing standards and workforce development gaps in additive manufacturing.
Nima Shamsaei, the founding director of NCAME and professor of mechanical engineering in the Samuel Ginn College of Engineering, said the program initially began to take shape in 2015 when Auburn established a partnership with the NIST, which is part of the U.S. Department of Commerce. In the fall of 2017, NCAME became NASA’s strategic academic partner and together they became the founding partners of the ASTM Additive Manufacturing Center of Excellence (AM CoE). (See the first quarter edition of TITANIUM TODAY for a feature article on AM CoE.)
NCAME has benefitted from strategic capital investments in recent years, which, collectively, have helped to transform the group into a hub for leading-edge technology. The list of investments and grants include a $18-million renovation of Auburn’s Gavin Engineering Research Laboratory; support from Auburn’s Presidential Awards for Interdisciplinary Research grant to explore additive manufacturing for medical implants; $7-million in grants from the NIST; a $4.5-million grant for the FAA; a $10-million award from NASA; and a $250,000 Concept Laser MLAB 100R metal printer from GE Aviation.
Developing additive manufacturing systems to produce parts for biomedical and aerospace are high on the list of priorities for NCAME. Shamsaei said the group focuses on powder metal and laser system in additive manufacturing. Commercially pure titanium (for medical implants), along with Ti6Al-4V, nickel-based superalloys, and aluminum alloys (for aerospace) are the materials being explored.
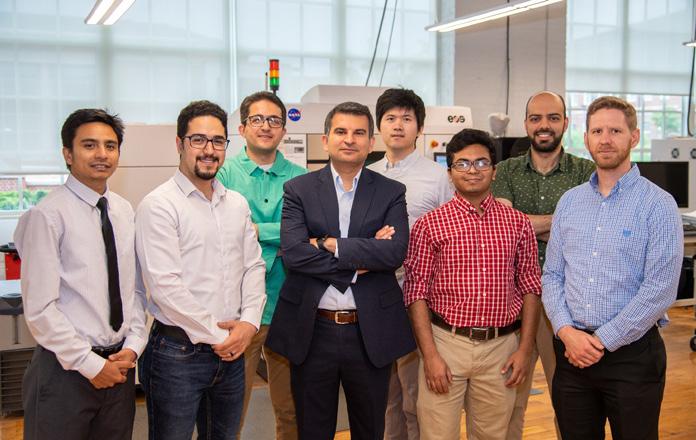
Nima Shamsaei pictured with NCAME Lab Technicians
“I envision the NCAME as a center to serve as a platform for transferring fundamental research to the applied knowledge allied with the needs of industry,” Shamsaei said. “We are working with our partners to develop commercial applications.” He stated that NCAME is working to meet the commercial production “inflection point” to establish three areas of additive manufacturing: design, processing, and material behavior. “Additive manufacturing is a challenging field. It’s unlike conventional production methods. You can’t separate those three areas. If you change the part geometry, it affects the microstructure and mechanical properties.”
He emphasized that overall activities at the Auburn center focus on training students for industry positions and publishing findings on additive manufacturing. He did outline projects. He outlined several programs underway at NCAME, such as examining fatigue behavior and defect variables, and evaluating fabrication variables to enable the production and qualification of structural aerospace components. The project is partially supported by the FAA. There’s also a project evaluating the production of patientspecific biomedical implants using additive manufacturing techniques at NCAME.
Interviewed in May 2021, Shamsaei said NASA has charged the group with a number of tasks: undertake a high level of research to advance additive manufacturing technology; become a platform for the exchange of ideas for the public and private sectors; and focus on workforce development for additive manufacturing, training technicians, designers and engineers to gain expertise in the field.
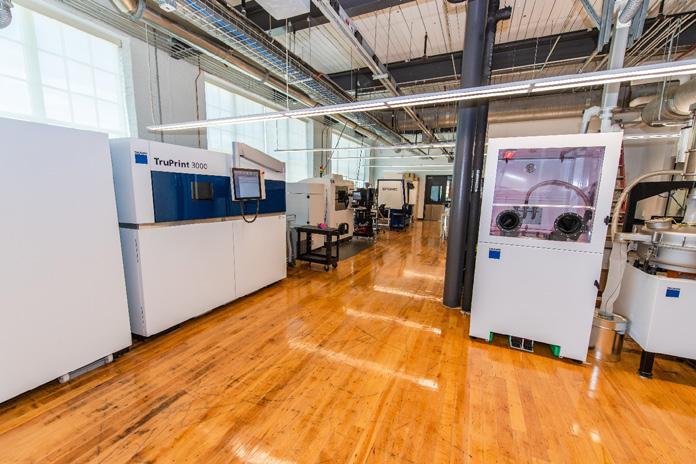
Auburn’s Gavin Engineering Research Laboratory
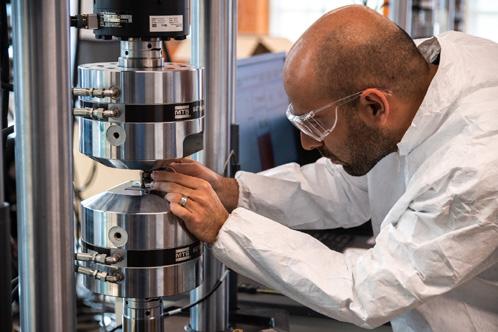
Testing Fatigue Behavior
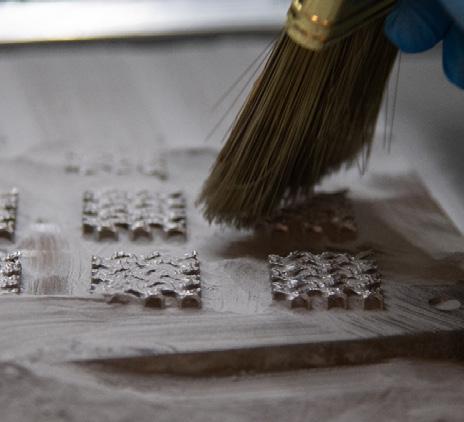
Additive Manufacturing Process
The list of production equipment being utilized by NCAME features: three EOS M290 Direct Metal Laser Sintering Systems; a Trumpf TruPrint 3000 Laser Metal Fusion system; a Renishaw AM250 Metal Additive Manufacturing System; a Coherent CREATOR; a OPTOMEC LENS 3D Additive Machine Tool; 10 MTS Uniaxial and Multiaxial Fatigue Testing Machines; a Zeiss Crossbeam 550 Scanning Electron Microscope; a KEYENCE VHX-6000 microscope; a FT4 Powder Rheometer; and other equipment to thoroughly characterized additive manufactured materials and parts. The center is also heavily involved in computational activities in modeling and simulating the additive manufacturing process and the performance of the products in an attempt to reduce the time and cost of experimentation.
Shamsaei is the Philpott-WestPoint Stevens distinguished professor in the Department of Mechanical Engineering at Auburn University, and the founding director of NCAME. He’s published over 200 peer-reviewed journal articles and conference proceedings as well as more than 60 technical presentations, including invited talks or keynote/plenary speeches in the areas of fatigue, fracture, mechanics of materials, and additive manufacturing part qualification and certification.
There have been other significant steps on this journey, accelerating the drive towards defining additive manufacturing as a full-fledged commercial process for the titanium industry and beyond. Separately, as mentioned above, ASTM’s Global Additive Manufacturing Program has established a “Center of Excellence” to accelerate the standardization and industrialization of additive manufacturing technology, a strategic field of interest for the titanium industry. ASTM and the NCAME maintain an alliance.
The ASTM’s mission is to provide education and workforce development offerings to support the adoption of additive manufacturing technology. One of the goals is to identify gaps in the additive manufacturing standards, and then to fund targeted research and development projects to close the gaps and accelerate standards. ASTM and its founding partners (NASA, Auburn University, the Manufacturing Technology Center of England, and Edison Welding Institute [EWI]) established the program in 2018.
Interviewed earlier this year, Dr. Martin White, who heads the center of excellence programs for Europe, said ASTM and its partners launched the effort “to accelerate the closing of gaps in standards for additive manufacturing, and to provide critical training and workforce development offerings to facilitate the broad adoption of this technology in multiple industries. The ‘normal’ pace of development of standards does not keep up with the rapidly progressing world of additive manufacturing, and we cannot wait for standards to be ‘reactive’ to information and data from industry.”
Art Kracke, president of AAK Consulting LLC, Charlotte, NC, an executive who has been in the titanium industry for nearly four decades, is one observer who has tracked the methodical march towards additive manufacturing’s inflection point. In recent interviews, Kracke has explained that additive manufacturing represents a suite of technologies and production methods, not just one process.
“The design flexibility of additive manufacturing can open doors to new global markets for titanium,” he said. “Given the promise of additive manufacturing, key factors are beginning to emerge, such as improved techniques to produce the titanium powder to upgrade its consistency and characteristics, the ability to engineer unique alloy combinations, and new generations of additive manufacturing equipment for part production.”
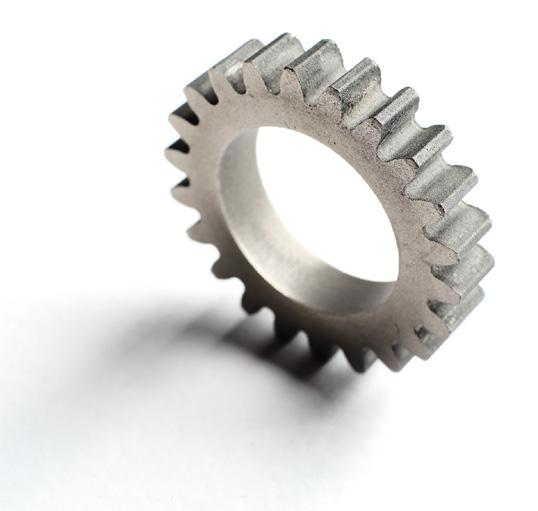
Additive Manufactured Parts