
10 minute read
Titanium Additive Manufacturing Evolves Incrementally To Achieve ‘Qualification’ of Global Aerospace Industry
By Bill Bihlman
Most people are familiar with the concept of 3D printing or additive manufacturing (AM) as it pertains to aerospace manufacturing. What most do not understand, however, is its level of maturity and the implications for their respective businesses. Titanium castings and smaller machined titanium parts are particularly at risk. Yet the timeline might not be as aggressive as many believe, or hope.
AM has evolved substantially since its genesis in the mid-1980s. Nearly simultaneously, Scott Crump, Chuck Hull, and Carl Deckard were experimenting with various ontologies or “modalities” of an additive process. These involved fused deposition modeling, stereolithography, and selected laser sintering, respectively. (ASTM has subsequently established the taxonomy: Material Extrusion, Vat Photopolymerization, and Powder Bed Fusion, respectively.) Initially, this new manufacturing paradigm was limited to rapid prototyping (as evidenced by the name of the largest AM conference in the United States, RAPID, established by the Society of Manufacturing Engineers in 1990).
Nowadays, AM is being used for some serialized production metal parts for aircraft and turbine engines. One of the more compelling use cases is the GE Catalyst engine. The company boasts of printing 35 percent of its gas turbine, replacing over 850 castings with only a dozen printed parts, likely using Ti-6Al4V. Perhaps even more intriguing is printing titanium-aluminide (Ti-AL) low-pressure turbine blades for the GEnx engine.
Most of the examples of AM in aerospace involve one of two modalities: powder-bed fusion (PBF) or directed-energy deposition (DED). Powder-bed fusion uses an energy source (e.g. laser) to melt a thin layer of metal powder. These particles are tiny—a fraction of the thickness of a human hair. A mechanical “recoater” spreads layerupon-layer of powder after each passing melt cycle. Parts are limited to the size of the build chamber, with dimensions often referenced in millimeters. Larger parts require thousands of layers and tens of hours to build. The benefit is that designs can include nested features or “conformal” cooling channels. In many cases, additive manufactured parts have such sophisticated geometry and features (e.g. internal lattice) that they cannot be created conventionally.
The other common modality for aerospace is directed-energy deposition. This uses either wire or powder as a feedstock. In both cases, the feedstock is fed through a nozzle and melted to form a part as the nozzle traces a pattern of the future part. The advantages of DED are the larger build envelope and higher rates of deposition. The disadvantages are the inability to: a) create complex, detailed parts compared to PBF, including “thin-wall” sections; and, b)produce high near-net shapes with smooth surfaces. Regardless of the modality, processing titanium (and aluminum) requires shielding. This usually involves gas, such as argon, to protect the melt pool from oxygen contamination.
It is believed that PBF represents at least 70 percent of the metal parts printed for aerospace, when including commercial space applications. Furthermore, it is estimated that titanium alloys represent roughly 25 percent of the total (see Figure 1). Note that titaniumpowder additive manufactured parts are also extensively used for medical applications due to its biocompatibility. In either case, the dominant titanium alloy is Ti-6Al-4V.
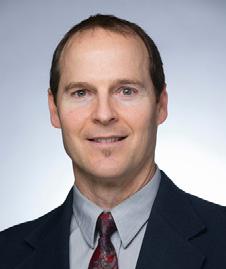
Bill Bihlman is founder of Aerolytics (website: www. aerolyticsllc.com
The global aerospace community is trying to move beyond prototyping to use AM routinely for serialized production. This requires a strong business case given higher costs often associated with high-volume printing. The return on investment calculations are confounded by the need to alter the design, compared to conventional manufacturing. Indeed, this is an emerging technology; as such, it is difficult given AM’s modest Technology Readiness Level (TRL). As a point of reference, generally speaking, metal AM is a 5 or 6 on the NASA scale of 1 to 9, with 9 being fully mature/deployable.
An important element in the maturation of metal AM for aerospace is qualification. For the most part, the Federal Aviation Administration (FAA) and their European counterpart, the European Aviation Safety Agency (EASA), are aligned with their methodology. Furthermore, this process is not a major departure from past convention, and the regulations have not changed.
Realistically, all metal forming processes need to be controlled and monitored. It could be argued that castings were the first process sensitive technique that introduced great uncertainty in terms of final mechanical properties. For this reason, the industry has accepted casting factors for most airframe structures. This can be as conservative as adding an additional 50 percent to the margin of performance (e.g. stress rupture) when creating a part. Alas, this additional metal adds unwanted weight. An alternative is a “premium casting,” which includes much tighter process controls (and higher associated costs).
Even more nuanced, though, are composite parts. These parts were commercialized in the 1980s by Airbus and then Boeing for major aircraft structures, such as the empennage. There are two important considerations: a) its mechanical properties (particularly tensile strength) can be easily manipulated to provide extraordinary anisotropy, and b) the details of the manufacturing process are essential.
Accordingly, manufacturers need to quantify (and measure) a multitude of key process parameters (KPVs) involved in the cure-cycle (e.g. thermal and pressure profile of the autoclave), in addition to design details, including the orientation and number of the plies, the fiber modulus, resin chemistry, etc. Similarly, AM is process intensive, requiring a massive amount of build and pre-build information. Part pedigree is increasingly critical. As an alternative to “Point Design,” the FAA introduced a framework to help qualify material and substantiate design. This is known as the “Building-Block” approach (see Figure 2). The base of the pyramid is the “bulk material allowables” that are used as the basis for the engineering design allowables. Mechanical properties ascertained by a coupon-level testing can be extrapolated to predict the static and dynamic properties of a final part of known geometry and loading condition. Indeed, this was true for homogeneous materials such as metal. But this became vastly more complicated when fabricating process intensive materials (PIMs). The industry therefore must pivot from a list of ingredients, for instance, to the complete recipe. Clearly, the aerospace original equipment manufacturers (OEMs) are reluctant to share their trade secrets and intellectual property. As a result, other public actors are needed to help diffuse this technology, ultimately enabling the smaller organizations that comprise the majority of the supply chain.
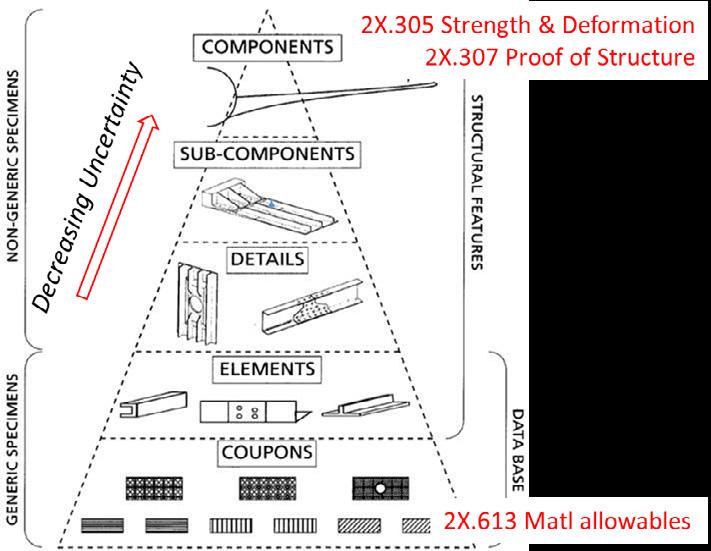
The FAA Building-block framework (Source: FAA)
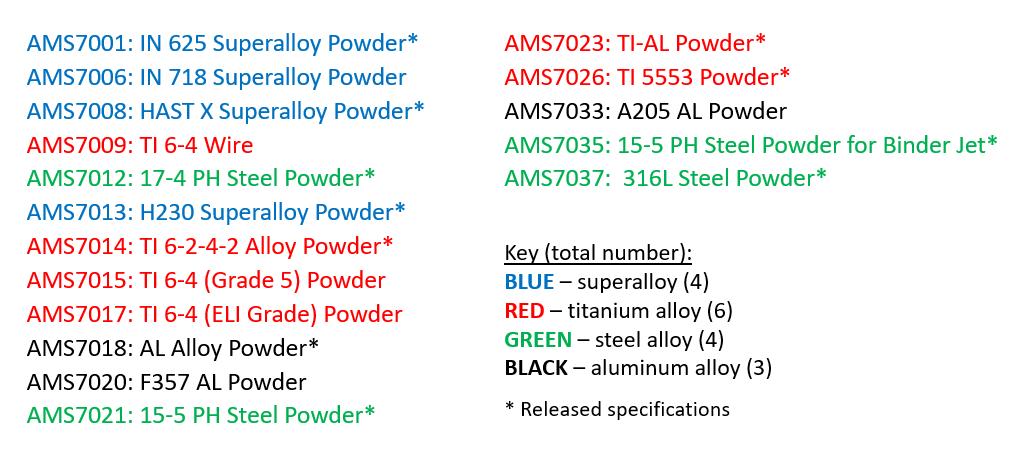
List of SAE AMS AM specifications for metal powder (Source: SAE AMS)
Arguably, the materials handbooks and standards development organizations (SDOs) play an important role in technology development. As a consequence of funding from the Pentagon and NACA/NASA – particularly during the 1950s and 1960s – the United States developed an extensive materials properties database. Much of this data migrated into military handbooks in the form of MIL-HDBK-5 (for metals) and MIL-HDBK-17 (for polymer composites). At the same time, other nations followed with their own materials research and development, particularly in Europe, due to the build-up of the Cold War. These handbooks are now known as MMPDS (Metallic Materials Properties Development and Standardization) and CMH-17 (Composite Material Handbook). Each has added additional volumes/ chapters to address the novelty of AM. Meanwhile the role of materials standards was largely enhanced.
Standards development organizations such as SAE International have created AM working groups. The SAE AMS (Aerospace Material Specifications) AM committee was created in 2015 to address material and process (M&P) specifications, predicated upon a consensus process to ensure industry guidelines. These M&P specifications facilitate procurement by providing assurance of the physical (and chemical) properties of a raw feedstock.
Metal powder is particularly complex. Issues such as morphology (e.g. size, shape, sphericity, particle size distribution) and chemistry (e.g. oxygen, nitrogen, humidity, element vaporization) are critical considerations when building parts. For this reason, a major of the SAE AMS AM standards involved metal powder (see Figure 3). As previously discussed, titanium is highly reactive, yet widely used; it’s no surprise that it is well represented within this group.
As the prominence of PIMs grew, standards were needed to help guide the process at large, offering insight concerning certification and continued airworthiness of aviation parts. As a consequence, SAE AMS AM is developing documents that move beyond M&P. Examples include AMS7032 that considers the operation/qualification of the AM machine itself, or ARP7042, that addresses issues associated with the approval of parts within the supply chain. These types of specifications have become increasingly important as both the FAA and EASA move towards performance-based regulations.
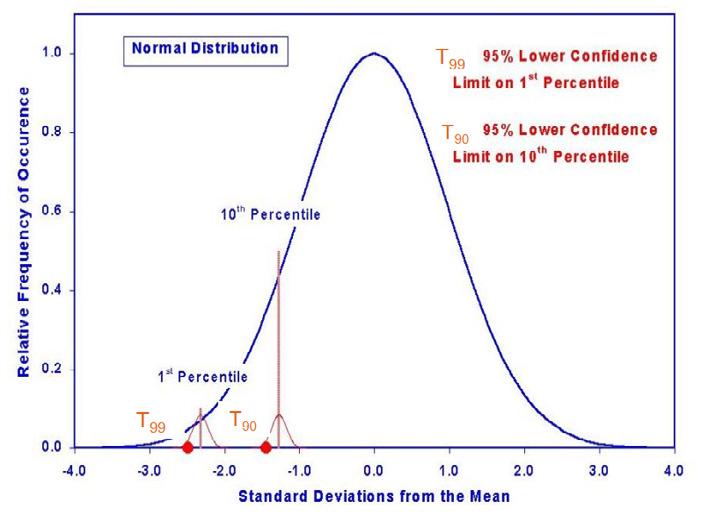
Example of material property’s distribution for the MMPDS Handbook (Source: Battelle)
What is the future state of metal AM? Clearly, the industry needs to walk before it runs, particularly for aerospace, where the likelihood of catastrophic failure is bounded by “one-in-a-billion.” For this reason, SAE and other organizations are printing and testing myriad coupons to establish bulk material characteristics for common aerospace alloys. The SAE ITC AMDC (AM Data Consortium) is developing detailed process control documents (PCDs) that can be adapted for all AM metals. The initial goal is S-basis bulk material allowables—the ultimate goal of providing C- and D-basis bulk material allowables, or T99 and T90, respectively. More forward looking, the industry will pursue more advanced AM processes, such as in-situ closed-loop process monitoring, multi-laser machines, and internal powder-reuse systems. The latter would be highly beneficial for titanium for the reasons mentioned. Ultimately, the goal is robust standards that minimize the need of Point Design, extensive testing, and 100 percent inspection of parts. One possibility would be to qualify parts based upon demonstrating a known, fixed/stable process. The first step would be to substantiate machine qualification. A “process qualification” of parts would be facilitated by a critical-part classification schema. Invoking the notion of proportionality, less critical parts would be subjected to less scrutiny. The FAA and EASA have convened a working group to address this issue. The challenge, notwithstanding, is reaching a consensus within a broad coalition of disparate stakeholders – from cabin interiors, to airframe structures, to life-limited parts (LLPs) within the turbine engine. This last category is considerably challenging, given that the fatigue behavior of AM parts is difficult and costly to quantify. In closing, AM is quickly emerging technology that shows promise for aerospace. A large proportion of additive manufactured parts involve titanium. It will challenge suppliers of titanium castings, although the actual threat is difficult to assess. At the same time, there could be opportunities for titanium printed parts to displace convention parts, including aluminum castings and extensively machined forged parts, if the business case supports new part redesign. For AM to be cost effective for newer designs, the entire artifact needs to be considered. Targeting single parts is rarely prudent for serialized production. Parts usually need to be designed with additive in mind, from the beginning. This mentality will take time. Meanwhile, the titanium industry can expect to see novel use cases for both aerostructure and turbine applications. There will be no step change. The industry will indeed continue to incrementally evolve, for the benefit and safety of the flying public. But someday, AM will be just another tool in the toolbox. (Editor’s note: Bill Bihlman is founder of Aerolytics (website: www.aerolyticsllc.com), a strategic consultancy founded in 2012 and dedicated to aerospace materials, manufacturing, and the supply chain. He started his career at Raytheon Aircraft in 1995, and is actively involved in SAE Aerospace Material Specifications. He has a BSME, MSME, and PhD in IE from Purdue University, and an MBA and MPA from Cornell University.)