
11 minute read
will see three times the volume of new capacity entering the market
During the year, the company said it “increased growth, improved profitability and strengthened our competitiveness for the future”.
This was done through innovations and investments in sales and marketing that it said strengthened its market positons and brands.
The company’s online sales also increased to SEK13bn, corresponding to 10% of net sales.
Price increases and an improved product were also noted in all business areas.
The group-wide cost-savings programme was concluded at the end of 2019.
Activities to improve underperforming market positions continued and resulted in improved profitability in several markets.
In Latin America, the company strengthened its market positions and organic net sales increased 10%.
The company’s China-based subsidiary Vinda strengthened its position as market leader in tissue and launched Feminine Care with the Libresse brand.
In Asia, organic net sales rose 11%.
Additional sustainability targets for packaging were also established, with a particular focus on plastic packaging.
The company also invested in sustainable technology for alternative fibre for tissue production.
In consumer tissue, the company reported net sales of 10.6% to SEK49,904m for the January-December period.
Emerging markets accounted for 47% of net sales.Adjusted EBITDA increased 60% to SEK5,321m. This increase was mainly due to higher prices, a better mix, higher volumes, lower raw materials and energy costs, and cost saving.
In the consumer tissue business, the company has finalised some negotiations and agreed on price decreases in Europe.
The company added that the decreases are on “average low single-digits” and will have an impact in the first quarter of 2020.
Kimberly-Clark to permanently close Fullerton plant
Kimberly-Clark (K-C) has confirmed it will permanently close its Fullerton, CA, tissue plant in the first half of 2020.
The move is part of previously announced restructuring plans that will see the company closing around 10 sites and cutting 12 - 13% of its global workforce in a bid to improve costs.
The Fullerton plant was opened in 1956 and employed 330 people.
Company spokesperson Terry Balluck
Clearwater Paper appoints Arsen S. Kitch as CEO
Clearwater Paper has appointed Arsen S. Kitch - the company’s senior vice president and general manager of its consumer products division - as chief executive as of 1 April.
He succeeds Linda K. Massman, who the company said will retire from Clearwater Paper after serving in the chief executive position since January 2013.
The company also announced that Alexander Toeldte transitioned from chair to independent executive chair of the board on 1 March.
Kitch has served as senior vice president and general manager of Clearwater Paper’s consumer products business since 2018.
Prior to that, he served as vice president of finance and vice president of financial planning and analysis since joining the company in 2013.
He said: “Today, Clearwater Paper has a healthy business and a strong team focused on driving results and building on our recent momentum of solid operational results.”
Clearwater Paper manufactures quality consumer tissue, AfH tissue, parent roll tissue, bleached paperboard and pulp.
said: "We announced the closure of the Fullerton facility in January of 2018, as part of our global restructuring programme.
“These business decisions are not taken lightly, and our priority continues to be on our employees and supporting them through this transition."
Headquartered in Irving, Texas, KimberlyClark makes tissue products including Kleenex, Kotex, Cottonelle and Huggies.
Irving boosts ultra-premium capacity with TAD investment
Irving Consumer Products invests in second TAD machine following Macon start-up. The machine is planned to start-up in 2022 and will increase the company’s production of ultra-premium products to the North American market, adding 75,000tpy to Irving’s current production.
It is a repeat order of the Advantage ThruAir machine that was started up by the company 2019.
Valmet’s scope of delivery will comprise of a complete tissue production line with stock preparation equipment. The new line will include an Advantage ThruAir tissue machine including an OptiFlo II TIS headbox, ThruAir Dryers and Air system and an Advantage SoftReel reel.
It also includes mist and dust systems, automation systems, basic mill engineering and advisory services. The value of the new order is not disclosed.
Robert K. Irving, president of Irving Consumer Products, said: “The new TAD machine will help Irving Consumer Products continue to grow and deliver ultra-premium quality tissue paper products to our customers.”
Previously Valmet has delivered one ThruAir machine to Irving’s Macon, Fort Edward, Toronto site, as well as carried out major rebuilds of tissue machines TM1 and TM2 to Saint John.
Irving recently announced it is doubling capacity of ultra-premium household paper products at its Macon plant and is immediately initiating an expansion of the plant.
2019 BROUGHT RELIEF TO TISSUE’S COST ENVIRONMENT – NOW 2020 WILL SEE THREE TIMES THE VOLUME OF NEW CAPACITY ENTERING THE MARKET AFRY Management Consulting's Sanna Sosa, principal, and Soile Kilpi, director, report on emerging US trends – from M&As to asset renewals, the shift from multi-small sites to versatile mega-plants, project cost inflation, and a potential return for recovered fibre.
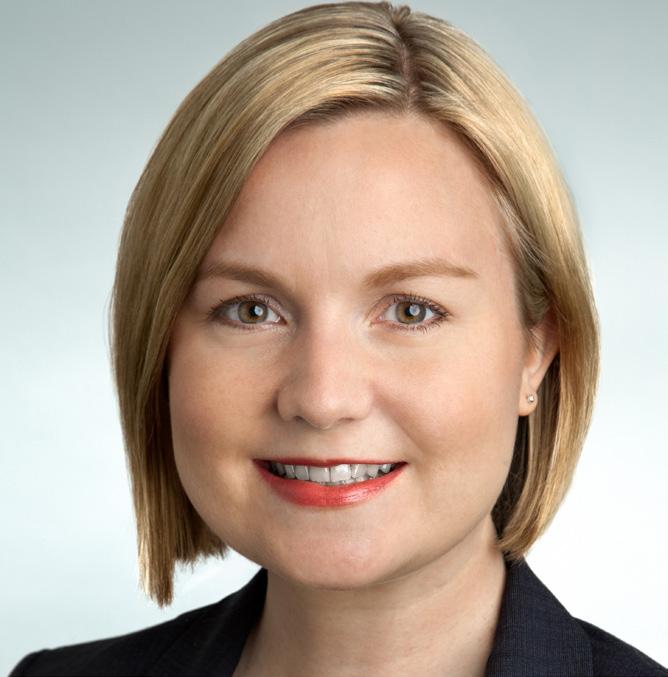
Sanna Sosa
Principal, AFRY Management Consulting
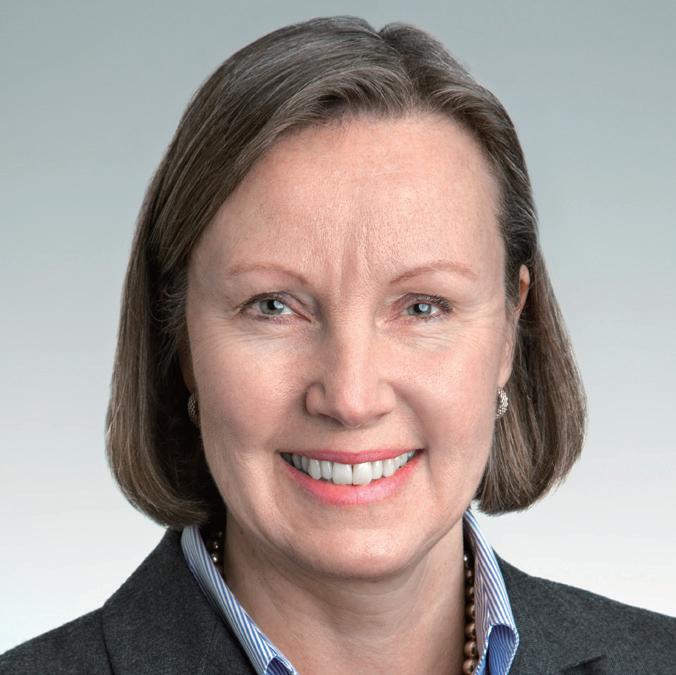
After high input costs drove tissue sector pains in 2018, 2019 was a return to a more normal operating environment for tissue manufacturers. Tissue demand was stable and producers were finally able to implement tissue product price increases by direct price changes, as well as continuing sheet count reductions, to pass through the previous year’s pulp price escalation.
Also supporting the positive tissue sector operating environment in 2019 was only modest net tissue supply growth, with a mere 115,000 short tonnes (net) of new capacity coming online from Clearwater, Irving and Georgia-Pacific (GP). However, three times the capacity additions in 2019 are expected to start hitting the market in 2020. The total 2020 new capacity growth is expected to be 365,000 short tonnes, minus exits estimated currently at around 65,000 short tonnes. In preparation for new and more efficient capacity to come on line, GP and Cascades have both closed highcost tissue manufacturing assets in 2019, while Kimberly-Clark (K-C) has slated their Fullerton, CA, mill for closure during the first half on 2020.
Soile Kilpi
Director, AFRY Management Consulting
GRAPH 1: TOP TISSUE PRODUCERS IN NORTH AMERICA
Aside from modest capacity growth, 2019 did not bring any significant changes to the industry supplier structure, as tissue manufacturing sector M&A activity remained meek. The notable exception was Cascades acquisition of Orchids Paper assets and hence consolidating the private label tissue space, and especially the growing recovered fibre-based retail private label tissue supply landscape.
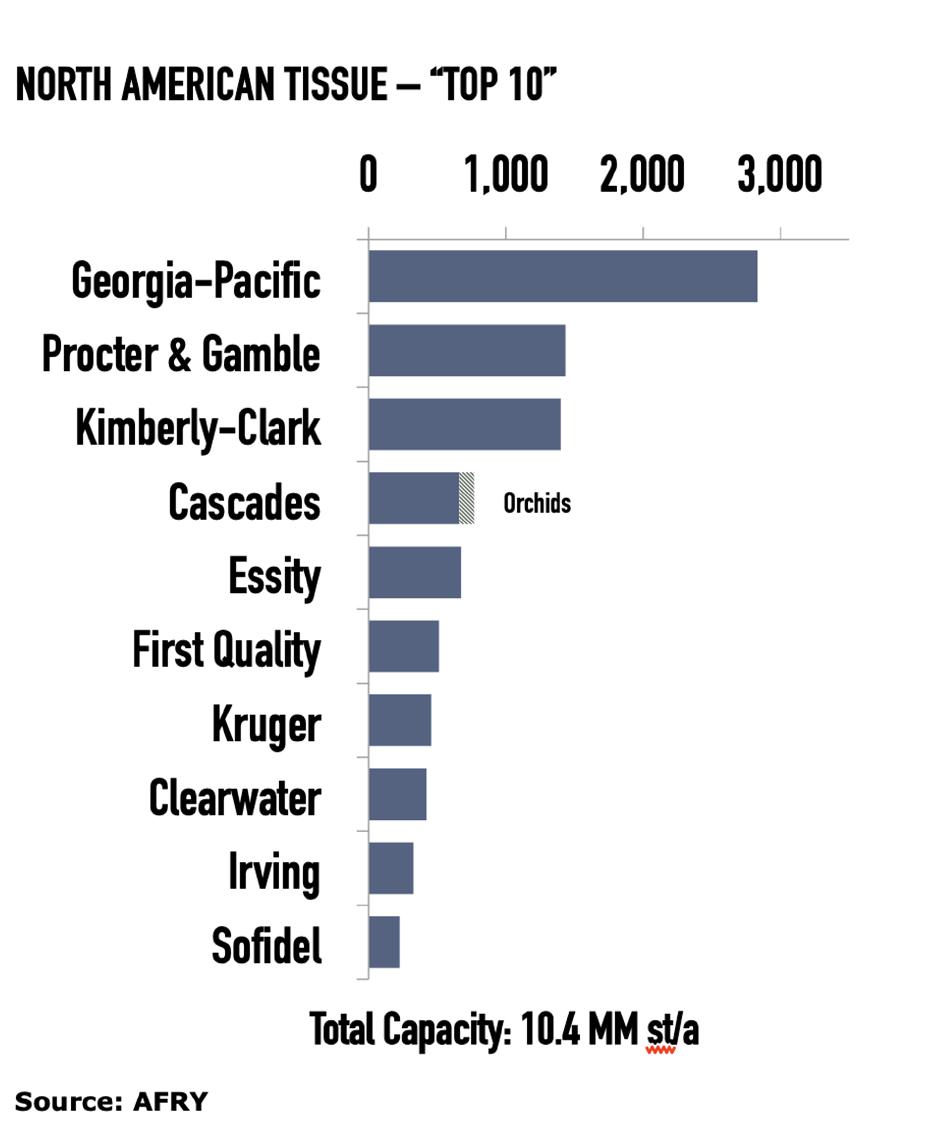
Investments in new capacity continue to be favoured over M&A
A notable characteristic of the North American tissue industry is that although there are many small and medium-size producers behind the big three producers [GRAPH 1], there has been little M&A activity over the past few years. It is very typical for industry consolidation to take place in markets with industry structure similar to the tissue sector, especially when market demand growth is only modest – which, tissue demand growth rate is at 1-2%/a. Typically, in industries with similar fundamentals, the industry leaders grow their market share via acquisitions, or the medium scale players aim to become one of the industry leaders via M&A.
Cascades acquisition of Orchids did move Cascades up one notch from the fifth largest tissue producer to the fourth largest tissue producer ahead of Essity in North America. Orchids’ acquisition price was $237m, with about five times implied acquisition multiple, which is well aligned with the typical Canadian Paper & Forest Products trading range of five-seven times, according to RBC Capital Markets. Cascades disclosed their logic for the acquisition to be “low risk strategy to modernise Cascades asset portfolio”. The Orchids business did come with two mills in Barnwell, SC, and Pryor, OK, with about 110,000st/a of premium and value quality recycled tissue capacity targeted for the retail private label market. The Orchids Paper mills had had an aggressive capital investment programme in the years leading to the acquisition. In 2015, Orchids Paper invested $39m for a 17,000 short tonnes tissue machine to replace an older, smaller one at the Pryor mill. An additional $165m was invested in a new QRT tissue machine along with converting lines and a deinked pulp line at Barnwell in 2017. However, Cascades has already announced to convert the Barnwell QRT machine to conventional tissue manufacturing technology. Capex details for the conversion were not published, but based on AFRY’s estimates, could range between $5 - $10m.
In addition to modern assets, the acquisition will eliminate tissue outsourcing contracts Cascades has had in place and will optimise the company’s operations footprint. Closures of Waterford, NY, and Kingman, AZ, converting plants have been announced.
Another new merger in the industry is Marcal, which is coming up from a devastating fire at their Soundview, NJ, plant, merging with a Pennsylvanian converter Nittany. The merger creates an integrated recovered fibre based Awayfrom-Home tissue product supplier, but, again will not change the overall all tissue industry structure or supplier landscape.
Asset renewal programmes by the leading players
Rather than marching the path of mergers and acquisitions, the tissue sector’s leading players have focused on asset renewal. The reasons for their favouring of new build capacity over M&A include that the top three companies already dominate two thirds of the retail tissue market, and hence there just aren’t many tissue brands to buy. Nor are there many manufacturing assets that would complement their product portfolios, especially on the retail tissue side.
GP continues to be the largest tissue manufacturer in North America, with capacity as large as the number two, P&G, and number three, K-C, combined. After some time on the sidelines, GP has been actively renewing its tissue mill assets over the past year or so. In 2019, it brought on line a $400m investment at Palatka, FL, on a new TAD machine and converting operations to expand its premium private label towel and branded retail towel capacity. At the same time, GP was rationalising its production platform and in conjunction with a closure of bleached board manufacturing at Crossett, AR, one of the mill’s older and smaller tissue machines was also closed. At its other Southern US mill in Pennington, AL, the company is investing $120m in a new tissue machine and roll storage building. The new line is expected to replace two older machines at the site late this year.
After K-C announced a massive workforce reduction - cutting 13% of its workers and closing down ten plants company-wide in 2018 - similar to GP the company is now back on track of renewing its assets on multiple fronts. There is a $100m investment in Mobile, AL, towards tissue machine replacement to improve efficiency and quality. The mill has capabilities to process both virgin and recycled fibres and has received significant capital improvement projects over the recent years. And that is not all. K-C has $235m capital improvement plans at Beech Island, SC, and Jenks, OK, manufacturing complexes. The capital programme includes expansion of the Jenks mill and installation of a new tissue machine and converting operations to manufacture facial and bath tissue products, and is expected to be completed in 2020. Similarly to GP, to balance its capacity footprint K-C announced the closure of its two tissue machines at Fullerton, CA, removing 67,000 short tonnes of capacity.
All of the top three tissue manufacturers are investing. In early 2019, Procter & Gamble (P&G) committed to its plan to expand operations at its Box Elder, UT, plant, which was originally built in 2011. The $310m announcement will create 221 jobs in Utah. Across its businesses, P&G has been shifting its manufacturing strategy from many small plants to versatile mega-plants. Growth of Box Elder seems to align with the strategy.
Mid-market movers and shakers continue to bring private label-focused capacity on line
In addition to the asset renewal projects by the leading players, the mid-size tissue manufacturers continue to bring private label focused new tissue capacity online [FIGURE 1]. However, running large scale tissue capacity growth projects on time and budget has proven to have its challenges.
Clearwater Paper completed its Shelby, NC, expansion project during the first half of 2019. The Shelby expansion is now successfully running, but had challenges with a tight construction labour market and building material cost inflation causing the project to cost $80m more than the $340m budget originally estimated at the beginning of the project in 2017.
Irving Tissue’s state-of-the-art Greenfield tissue production plant in Macon, GA, was inaugurated in late 2019, and similar to the Shelby project, the announced project cost of $470m appears to be about $70m higher than the original estimates provided in 2018. But, the potential construction budget increase did not cause Irving Tissue to slow down its US South premium quality tissue growth plan. The company confirmed an additional $400m expansion project to add another TAD tissue machine by 2022.
In 2020, both First Quality Tissue and Sofidel are on schedule to bring on line the final additions to both companies’ so far announced North American growth plans. First Quality Tissue’s footprint will soon consist of seven high quality, TAD, private label-focused tissue machines with total capacity of close to half a million tonnes at two mill sites in Anderson, SC, and Lock Haven, PA.
Sofidel’s North American platform will expand to six tissue machines with 370,000