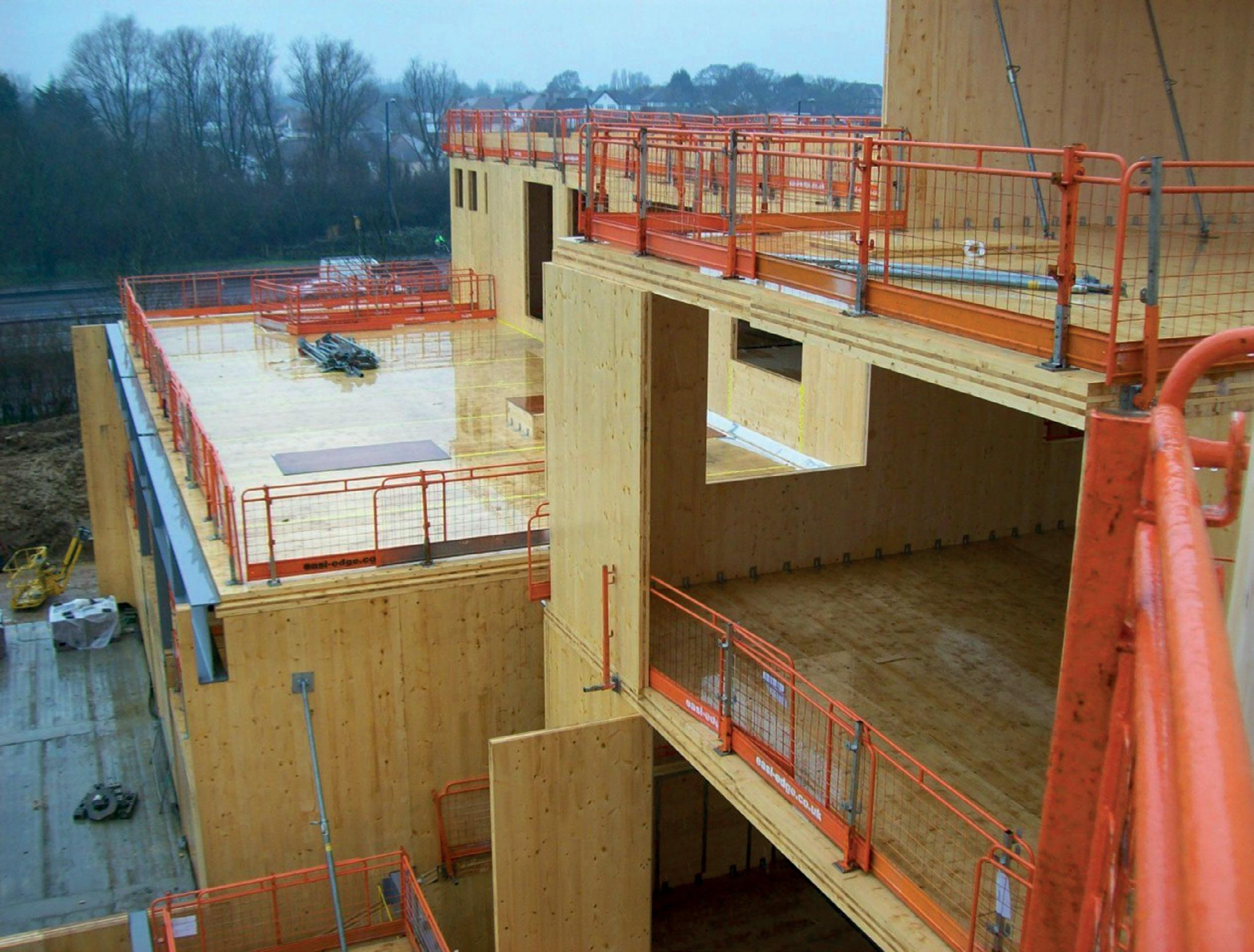
13 minute read
Weathering the Storm: Moisture Effects on CLT
Phil O’Leary, technical manager at BM TRADA, explores how moisture dynamics can affect the durability of cross laminated timber, covering the latest research from BM TRADA and Stora Enso.
Cross laminated timber (CLT) has become a popular choice for designers over the last 15 years. Spanning residential buildings to educational and commercial spaces, the market growth of CLT can be attributed to its usability in complex timber structures. Modern lightweight timber frame buildings have been used for nearly 100 years. Plus, a large proportion of the UK housing stock has timber pitched roofs, many of which are centuries old.
CLT has also created exciting opportunities for low/negative carbon and sustainable buildings. However, as with all construction products, there has been a learning curve as the industry’s understanding of CLT’s strengths and weaknesses has grown. One such area where new knowledge has been uncovered is in how moisture can compromise the material’s durability.
CLT durability
Durability of construction materials and components is particularly important as more people talk about sustainability. The benefit of timber and wood-based products is that the lifespan can be almost indefinite if they remain dry. That said, timber is at risk of fungal decay if its moisture content exceeds 20% for an extended period of time. In a well-designed and constructed timber frame building or pitched roof, moisture content in service will be between 10% and 14% – well below the fungal decay threshold.
While CLT follows the same durability principles as lightweight timber structures, its thickness and the mass of timber used present additional considerations when exposed to moisture. Timber studs, joists and rafters have a relatively large surface-area-to-volume ratio and so typically dry rapidly when conditions allow. On the other hand, CLT has a much smaller surface-area-to-volume ratio and so drying rates can be substantially slower, which can affect durability greatly.
Insulation considerations
CLT external walls and roofs should always be designed as ‘warm’ construction. This means all thermal insulation is placed on the outside face of the wall or roof panel. By placing the CLT panels within the thermal envelope of the building, panels are in what should normally be a warm and dry environment – creating the ideal environment for timber to endure.
THE KING OF COMPOSITE
Don’t be fooled by a lesser product; since 1996, Trex has invented, defined, and perfected composite decking with a lineup of low-maintenance, high-performance products that fundamentally change the way we live outdoors.
Only The World’s Number One decking brand can claim all that.
Tiki Torch

One of 11 contemporary colours available.
Find out more. Call 01469 535 415, email trex@arborforestproducts.co.uk or visit www.arbordeck.co.uk
Claim your free sample pack: www.arbordeck.co.uk/samples
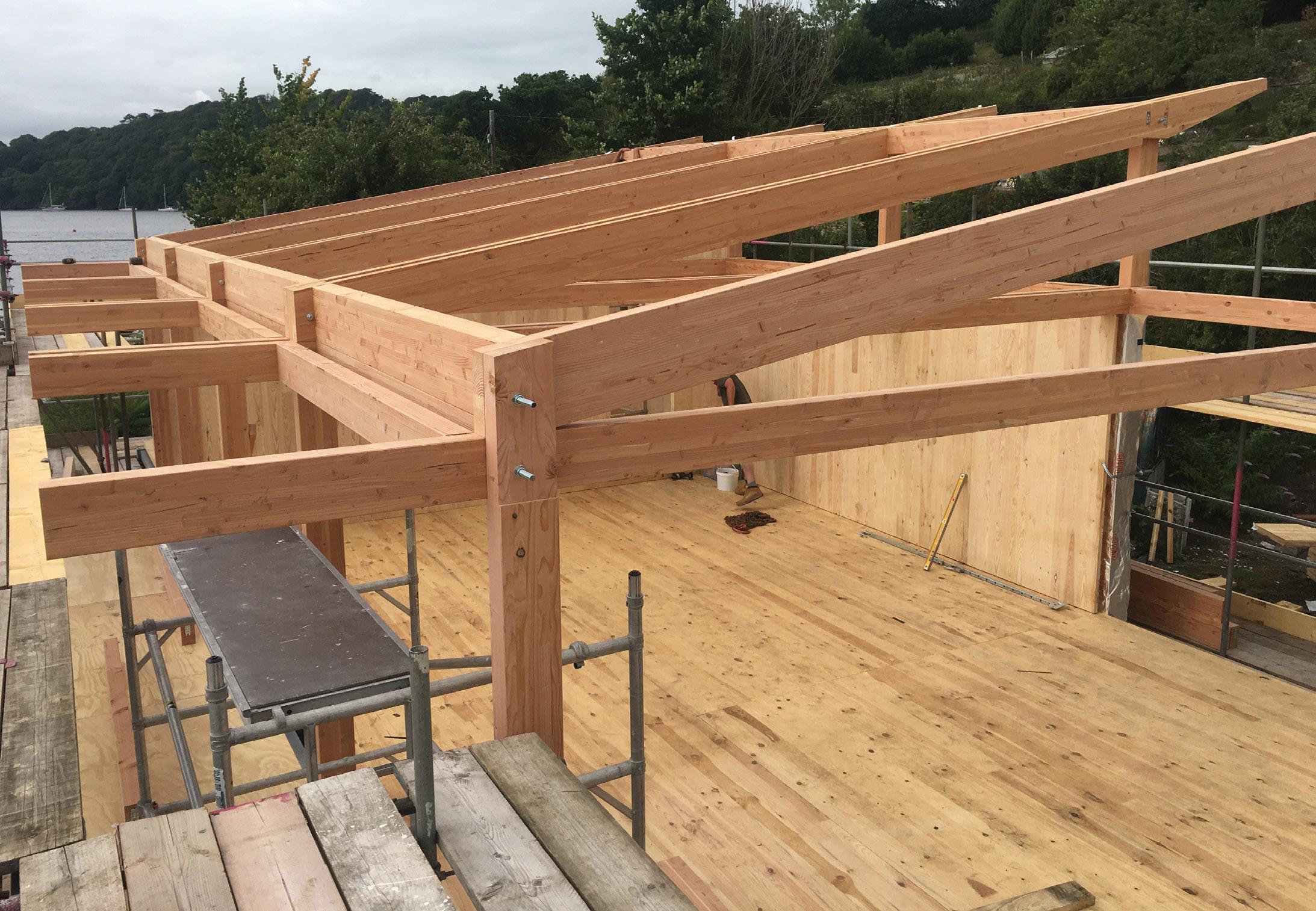
The most common insulation material placed on the outside of CLT in the UK is rigid foil-faced insulation boards (e.g. PIR/PUR/phenolic). It is installed to walls, flat roofs and pitched roofs. While these insulation materials have excellent thermal resistance and provide the required U-values, the foil facings limit drying of the CLT panels behind.
Developing understanding
Moving forward requires learning from previous experience, of which data forms a large part. For this reason, BM TRADA and Stora Enso have conducted research to better understand the moisture dynamics in CLT. The two-part project looked at both wetting risk during construction and drying rates, information which can be used to determine moisture distribution behaviour. The drying rates of five-layer, 100mm-thick CLT panels were investigated – various configurations were tested, including covering the wet outer face of panels with foil to replicate panels covered with rigid foil-faced insulation boards and/or vapour control layers. This test set-up was intended to replicate typical UK construction build-ups for warm walls as well as flat and pitched roofs.
During testing of the covered panels, water in the wet outside face lamination was observed slowly passing through the thickness of the panels to the dry uncovered side, confirming the previously held assertion that panels could dry to the inside. However, with a starting moisture content of 35% in the wet outer lamination, it took almost 16 months for the moisture content to fall to 20%. This means drying could take years for higher moisture contents and/or thicker panels. On the flip side, uncovered panels that were able to dry directly from the wet face took approximately six weeks for a similar moisture content reduction.
Creating room to breathe
To achieve long-term durability of timber structures, a primary consideration is to provide a combination of drainage, ventilation and breathability. It is not normally an issue if timber gets wet, providing water can drain away quickly and the timber is subsequently allowed to dry. Slowing down or restricting drying though the use of high resistance insulation products and/or vapour control layers on the inner or outer faces of the panels can slow drying to an extent that the development of fungal decay may become a risk if panels are subjected to adverse conditions during construction or in service.
On the continent, CLT building systems are often paired with mineral wool or wood-fibre insulation products – these breathable insulation materials are typically beneficial to timber building systems as they allow more rapid drying of the CLT panels if they are exposed to wetting during construction or in service. The use of breathable insulation products and systems, in conjunction with good overall design detailing and a moisture management plan for the construction phase, will have a significant positive impact on the long-term durability and robustness of CLT structures.
Planning ahead
CLT will no doubt play a key part in creating greener, low carbon buildings. To do so, an understanding of how to effectively protect CLT from moisture during construction is vital. Where moisture does pose issues, appropriate remedial action must be prioritised. This should also be taken into consideration at the onset of any timber construction project, particularly when allowing sufficient drying time to prevent fungal and structural decay.
Cambridge Plans for Passivhaus
Cambridge City Council has turned to Passivhaus principles to deliver its next tranche of affordable and sustainable living.
The need for energy efficient homes has never been greater with the cost-of-living crisis and events in Ukraine continuing to push fuel bills to all-time highs. To counter this, the adoption of a Passivhaus approach using timber frame is beginning to appeal to many local authorities and housing associations to protect tenant’s surroundings and deliver low carbon homes.
With the impact of continued rising energy costs and a drive towards meeting Cambridge City Council’s objectives to be net zero carbon by 2030, Cambridge Investment Partnership (CIP) has started work to deliver its first pilot Passivhaus council homes for local residents.
The 12 new low carbon council homes at Fen Road, East Chesterton are the first of three sites that have been chosen by CIP for Passivhaus pilot council homes.
The development at 71-73 Fen Road sees the replacement of two existing single storey buildings, which are no longer in use and in a poor state of repair with 12 low carbon homes comprising eight two-bedroom homes, two three-bedroom homes, one three-bedroom wheelchair adapted house, and one four-bedroom wheelchair adapted home.
Cllr Gerri Bird, executive councillor for Housing at Cambridge City Council and CIP board member said: “We are now in an era of increasing living costs, which are impacting everyone, so I’m delighted that we are able to bring forward this Passivhaus pilot scheme to not only deliver the much-needed council housing in the city, but to provide homes that cut energy bills, tackle fuel poverty and are great places to live. I am especially pleased that two of these houses are wheelchair adapted for families, which is important as we look to tackle inequality and provide more fully adapted homes for disabled people.”
CIP has worked with experienced architect Pollard Thomas Edwards, The Environment Partnership and Carter Jonas to bring forward this scheme. The pilot ‘Passivhaus’ council homes will have very low energy use and heating costs and will be built using offsite timber frame systems, with thick highly insulated walls and gas free heating.
Tom Hill, regional director for Hill comments: “As a partnership we are committed to creating sustainable homes with all our new developments gas free. These new Passivhaus council homes go one step further to enable us to learn and continue to enhance our approach to sustainability which can be implemented further across all future developments. The pilot will allow us to explore the delivery of cost-efficient low carbon housing for the future in terms of up-front building costs, ongoing maintenance costs for the Council and low bills for residents.”
As part of the development, CIP will create a new, safe and green access for walking and cycling to the Five Trees open space, which will be preserved in its entirety, helping the local community to enjoy this space. There will also be parking spaces with electric vehicle charging points and generous provision for new cycle parking. This well positioned site will provide easy access to the city centre and other amenities for local residents.
Cambridge Investment Partnership will also be delivering Passivhaus council homes at Borrowdale and Ditton Fields. Passivhaus buildings achieve a 75% reduction in space heating requirements compared to the standard practice for UK newbuild homes. The Passivhaus standard therefore gives a robust method to help the industry achieve the 80% carbon reductions that are set as a legislative target by the UK Government.
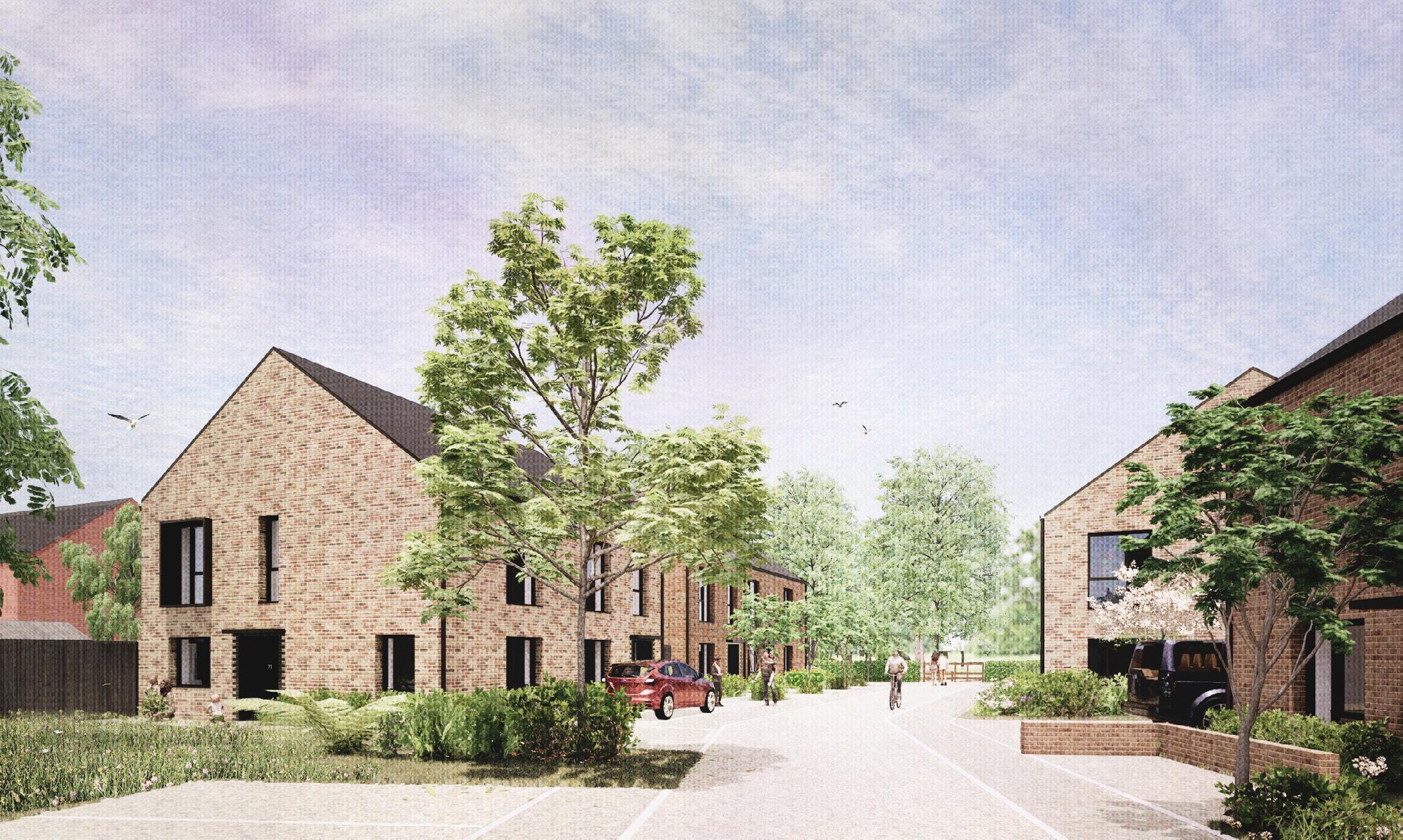
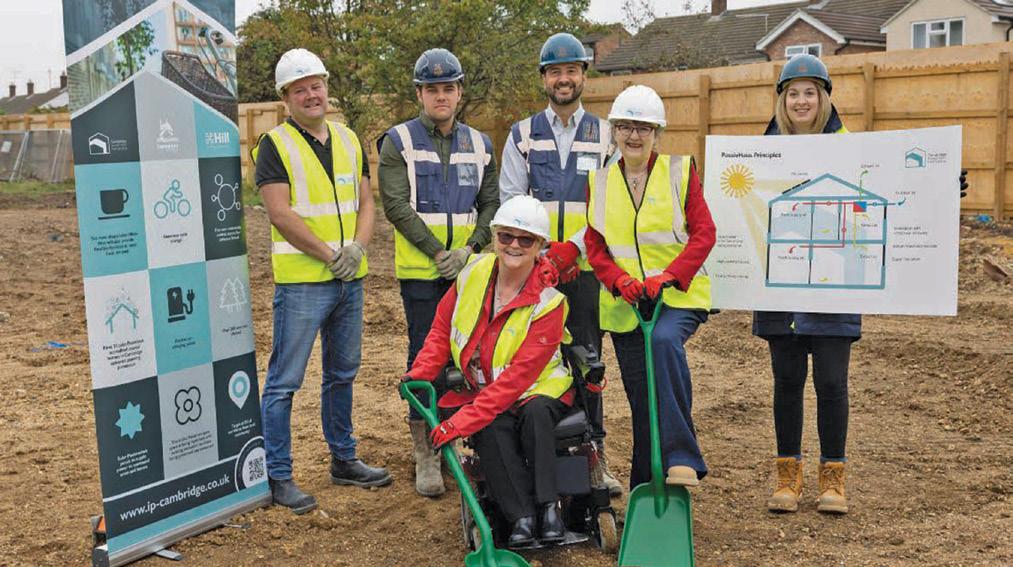
New Self-build farmhouse warms to external Wraptite® airtight solution
A new self-build farmhouse in the beautiful Scottish countryside has been fitted with the high-performing Wraptite air-barrier. The project is designed to Passivhaus standards by Architect Frances Strachan-Friar. Talla Fiodha (‘timber or wooden hall’ in Gaelic), Charleston Farm, near Errol, Perthshire, will be the new home for Frances and her husband.
From the outset, the aim was to achieve a more sustainable design and follow a different approach from the traditional timber kit. After undertaking significant research into different types of construction, the architect selected Xilonor CLT cross-laminated timber installed by Glulam Solutions Ltd., Inverurie. Frances Strachan-Friar commented on how the selection of Wraptite has benefitted the development. “The specification of the correct type of airtightness barrier was critical in achieving thermal efficiency. Wraptite was chosen because it allows the airtightness layer to be fitted to the outside of the construction. In doing so, the external application of Wraptite provides essential protection in the form of waterproofing and weatherproofing for the CLT during the build.
View more Case Studies on our website... www.proctorgroup.com contact@proctorgroup.com +44 (0) 1250 872261
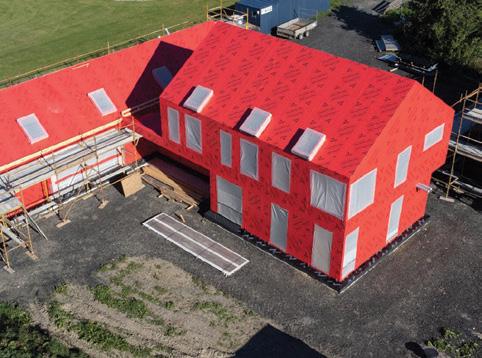
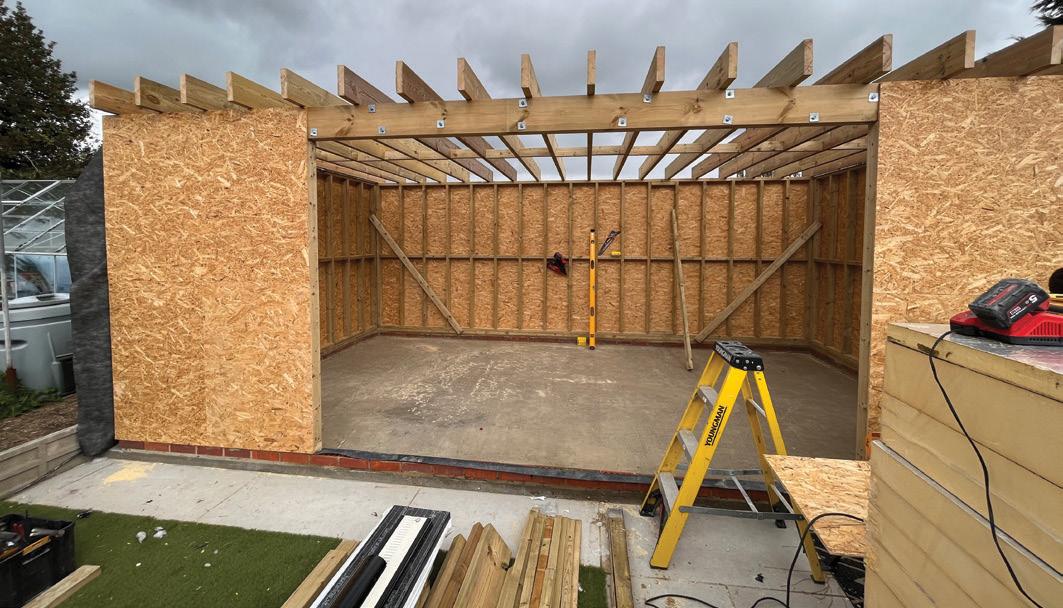
TECHNOLOGY YOU CAN RELY ON, FROM A BRAND YOU CAN TRUST
South London loft conversion specialist finds multiple uses for West Fraser’s SterlingOSB Zero
A family-run firm from Surrey, which specialises in loft conversions and the creation of bespoke garden rooms, is making extensive use of SterlingOSB Zero from panel product manufacturer, West Fraser, based on the board’s value, performance and ease of installation. MB Loft Conversions, based in Caterham, was established eight years ago by Mark Bell and undertakes contracts right across South London, Surrey, Sussex and Kent. Typically, the company completes up to a dozen loft conversions and other projects each year. Mark purchases his SterlingOSB Zero from Selhurst Timber and other builders merchants’ local to clients’ properties. While he mainly prefers to use 18mm tongue and groove boards for their strength and excellent alignment when laid, some of MB Loft Conversions’ builds also use quantities of 11mm (square edge) SterlingOSB Zero. Mark Bell commented: “There is a number of reasons why we prefer to use both West Fraser’s 8x4 and 8x2 T&G Sterling OSB Zero, apart from it being a product I’m very familiar with. We know we can rely on the quality, while the 18 mm T&G boards are like gold when it comes to doing flat roofs and make a really good deck. We also use them for the cheeks of the dormer windows, while we switch to the 11mm for internal walls. There are also many applications for SterlingOSB Zero when it comes to our garden rooms.”
To find out more about West Fraser’s products for housebuilders, call 01786 812 921 or get in touch with Dan Clarke – email Daniel.Clarke@westfraser.com or download product brochures from the housebuilder page of the West Fraser website uk.westfraser.com/housebuilders
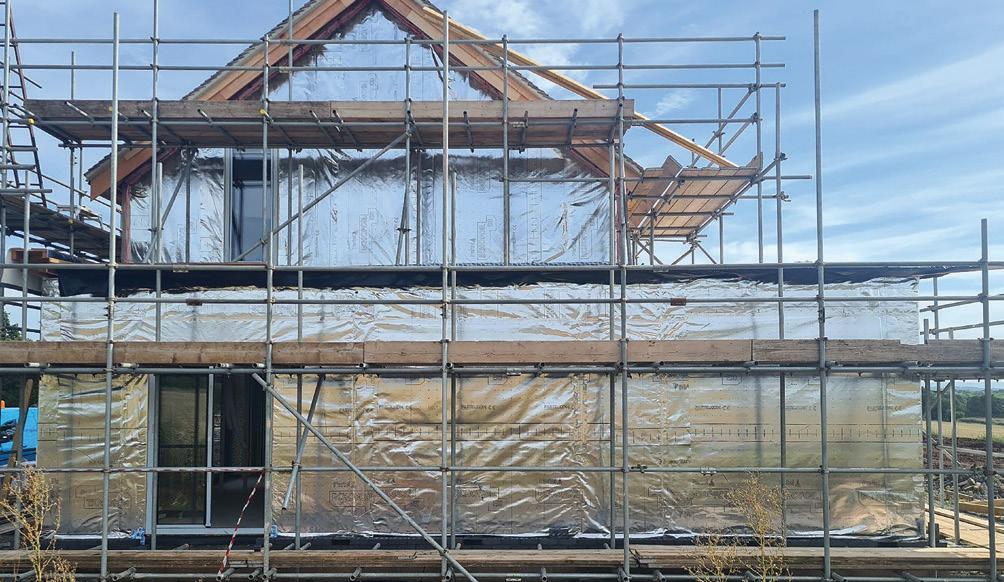
Biotecture Living hoardings transform Stonecutter Court site

Biotecture has designed and installed a green hoarding for repeat client Mace on the construction hoarding of the new Stonecutter Court development in London. Stonecutter Court, close to Fleet Street and Farringdon, is being re-developed into a flexible, user experience-driven office building. The new development, designed by Architect, TP Bennett, has strong sustainability credentials and is targeting a BREEAM Excellent rating and WELL Gold standard upon completion. International construction and consultancy company, Mace, was appointed to develop the project. As sustainability is one of the biggest drivers of the new development, greening the construction hoarding was important for both the end client and the contractor. Mace had already used the Biotecture PlantBox living hoarding at nearby Farringdon Road and so understood the benefits it can bring to a construction project. As well as showcasing the client and contractor’s green credentials, the living hoarding will improve the appearance of the construction, and help improve air quality thanks to the removal of dust, dangerous particulates and harmful pollutants from the air by the plants. This creates a healthier environment for those working on site as well as those living and working in the surrounding area. PlantBox living hoardings offer a far more sustainable choice than signage, artificial plastic greenery, or photographic panels of foliage, whilst avoiding issues with graffiti.
Biotecture is the UK’s leading living wall and living hoarding company, and this year is celebrating its 15th anniversary. To find out more about Living Hoardings, call us on +44 (0)1243 572118, email us at enquiries@biotecture.uk.com or visit our website: www.biotecture.uk.com/bioextra/living-hoardings
Partel’s high performance ECHOFOIL EXO allows timber frame Buildings to breathe
With energy prices increasing and a focus on improving the fabric of buildings through increasing legislation, the need to create energy-efficient building envelopes has never been so important. To help achieve this, Partel has developed ECHOFOIL EXO, a highperformance breather membrane designed specifically for timber frame construction. Developed by Partel, one of the market leaders in the manufacture of specialist breather membranes, ECHOFOIL EXO is a low emissivity reflective membrane designed for use in timber frame panel construction. Offering a wealth of benefits, the breather membrane improves thermal comfort and enhances airtightness in a wide range of buildings. This reflective foil membrane has one of the lowest emissivity values in the market of just ≤ 0.04 and a cavity R-Value of 0.78 m2K/W. This means it is the ideal solution to help architects and housebuilders achieve a desired low U-value. It is also highly breathable with an Sd value of 0.08m. As part of its on-going commitment to the responsible performance of buildings and sustainable production processes, Partel has published Environmental Product Declarations for five of its innovative low-carbon building envelope solutions. ECHOFOIL EXO is one of Partel’s EPD certified breather membranes. ECHOFOIL EXO is currently available in the UK, Ireland, and mainland Europe.
For more information visit www.partel.co.uk or contact the Partel team on 02037 401918 to discuss requirements for your next project.

Choose life, Choose wood
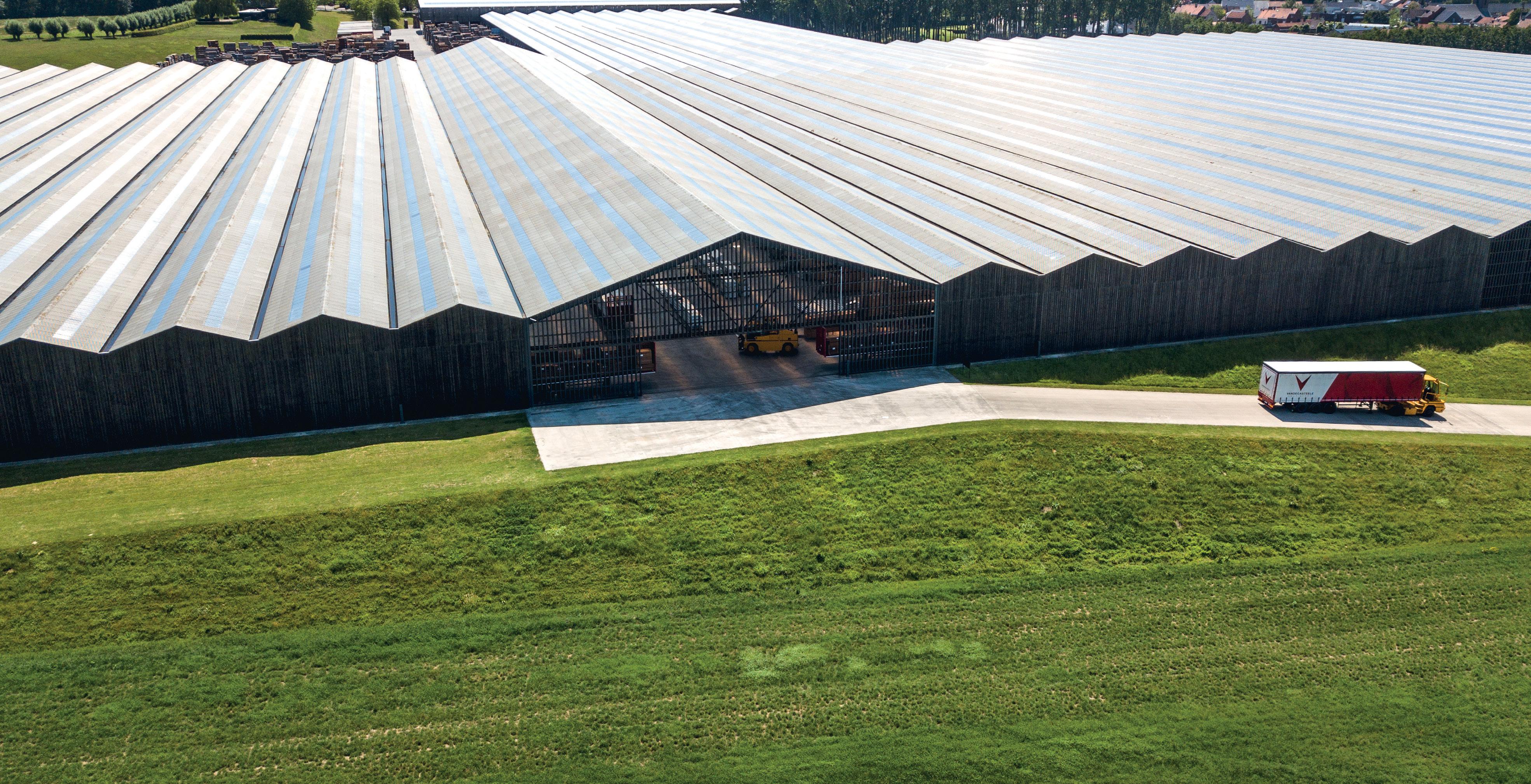