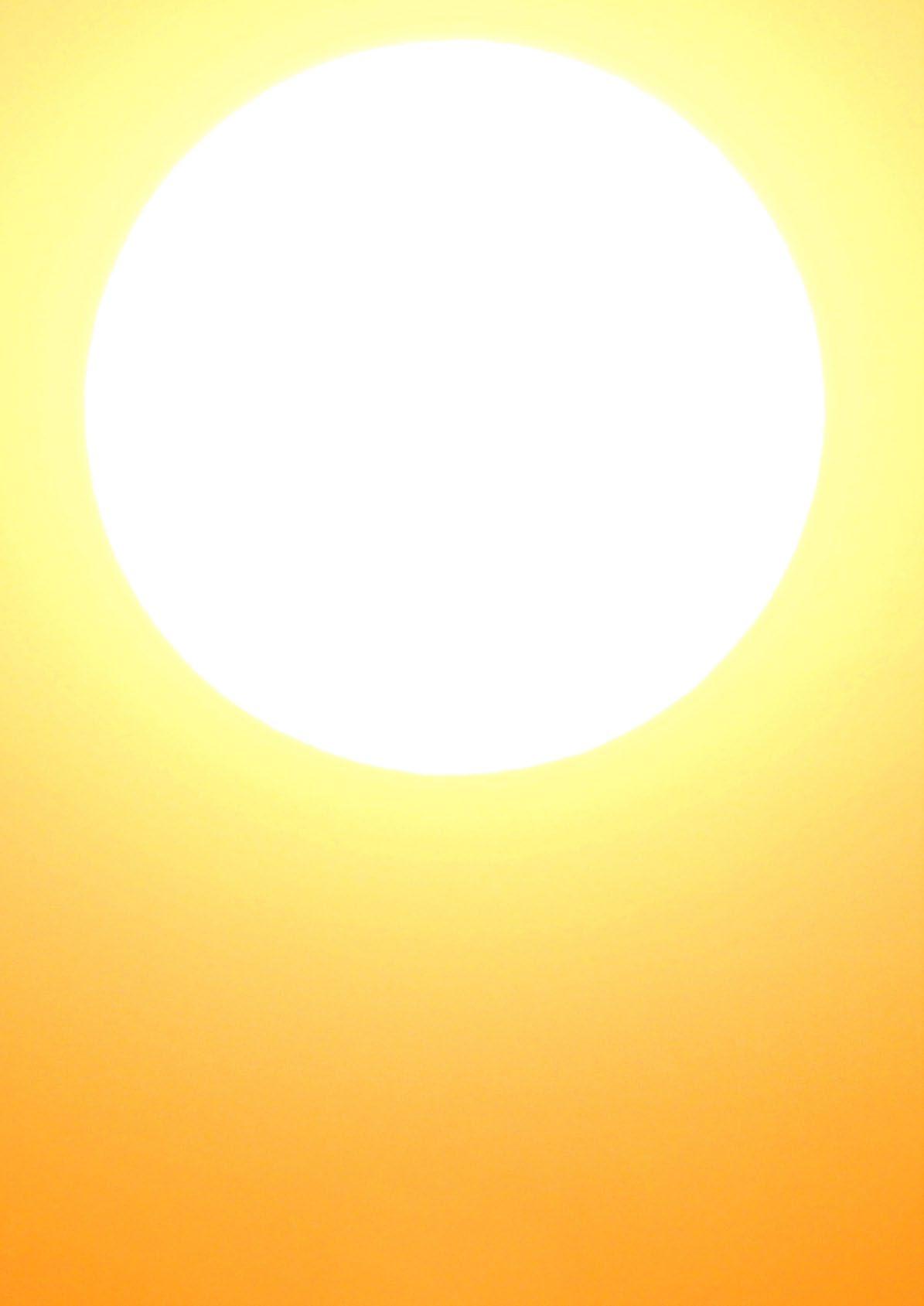
10 minute read
SOLAR, SUPPLY AND SUSTAINABILITY
SOLAR, SUPPLY AND SUSTAINABILITY
We all think of solar as a more sustainable alternative to conventional street lighting – and it is. But what about how solar streetlights are produced, the raw materials, the carbon, the supply chains, how sustainable is all this? Mark Hopkins investigates
By Mark Hopkins
In my previous article in the January 2022 edition of this journal (‘Legacysystem’, vol 87, no 1) I explained some of the points around specifying and installing solar lighting.
In this article, I want to look in greater depth into the bigger picture of what makes solar lighting a sustainable solution and what the environmental and ethical impacts are throughout the product life.
If we are to make an actual impact to reduce carbon emissions and to install new products that meet these criteria, then the whole life cycle must be taken into consideration. ‘From cradle to grave’ is a philosophy that underpins many decisions we make today, and making this part of an ongoing specification will be the only way a positive outcome is achieved.
To put this article into perspective, and taking street lighting as the main subject, then the pole, the luminaire, and any control electronics, will be assumed to be common components of both solar and mains installations, leaving the solar panel and battery to be considered in detail.
That is not to conclude that there are no impacts from the pole, luminaire, and controller, but they remain a fixed contribution.
I am going to take you on a journey from the source of the materials and their processing, through to the manufacturing of the components and assembly, then installation, and finally the decommissioning at their end of life.
THE ROLE OF SILICON PV
Silicon PV (photovoltaic) is of course the primary source for solar panel manufacturing. As the world’s eighth most common element, you may be forgiven in thinking silicon is a low-cost material to use.
However, the silicon required in photovoltaics and semiconductors needs to be of almost perfect purity and this requires some complex and energy-intensive processes.
The journey starts with extraction of the quartz, which creates damage to the environment from mining operations. This is followed by conversion to the polycrystalline form of silicon, which is achieved through a reaction with hydrochloric acid and hydrogen.
This produces silicon tetrachloride, a colourless but volatile gas that turns to a corrosive substance when in contact with water.
But, as a gas, it is easier to handle and, through vapour deposition, can be converted to pure silicon.
For every tonne of polysilicon produced, four tonnes of silicon tetrachloride is produced. Clean technologies to scrub this waste are employed by the West, but outdated process are recorded in some Eastern countries, which are sources of pollution.
To turn this polysilicon into wafers, it is heated in a furnace to just below 1500°C and from this furnace a single crystal is grown either by seed growth from the surface or through the gradual cooling from the bottom to maintain a single grain boundary. This produces a uniform ingot of monocrystalline silicon.
This ingot is then sliced into very thin wafers using diamond-coated wire saws. There are other innovative methods to produce wafers from the molten polysilicon, including using vacuum deposition. This prevents waste from the cutting process.
The type of semiconductor produced is now achieved by doping with Boron for ‘P-type’ cells and Phosphorus for ‘N-type’ cells.
Further processes to texture the silicon surface, acid cleaning, additional doping to increase conductivity, etching and edge isolation, and finally anti-reflective coating deposition completes the wafer production.
It is now ready to have the copper busbars soldered in place to build into a solar panel. All these processes use various amounts of energy, but the scale of production is such that to produce 1.0m² of cells it uses up to 250kWhr, and as a guide for the UK a 1.0m² panel will produce up to 100kWhrs per year.
So, it will take between 2.5 and four years to pay back this energy. And, with solar panels lasting 25years, this is a serious net gain for the zero-carbon goal.
There are more than 350 companies in the world that take these silicon wafers and manufacture solar panels. But the primary companies in this market are again based in China, with Germany, Japan, South Korea, USA all having home-based companies. This is shown in figure 1 opposite.
The facts and figures surrounding the production process for solar PV are centred on China. As the world’s main producer, it has at an estimated 90% of the world’s production and include both tiers 2 and 3 of the supply chain [1]
The current production in China is estimated to rise from 295GW at the end of 2022 to a staggering 536GW by the end of this year. With more than 80% of this capacity exported, the dominance of a single supply chain source cannot be underestimated.
Looking, briefly, at life-cycle analysis, notably the CO² emissions from transport the CO²/kWatt hr and assuming a 30-year life cycle, what you get is as follows:
• Solar life-cycle analysis. This encompasses raw material extraction, polycrystalline production, wafer manufacture, module assembly. Here, you are looking at 45-73 grams of CO²e/kW.
• Solar shipping. It’s common to have 8,000 miles with an expected 30-year life expectancy. This gives you 15 grams of CO²e/kW.
The end of life and recycling of PV has yet to find stable economic viability, primarily because of economies of scale. This will change as the original installations reach their end of life, with the potential to recycle over 90% of the material. This will in part be driven by the supply chain, as materials such as silver become scarce and more expensive.
The science behind the two main battery chemistries for PV is well documented and, with the advent of some new innovative environmentally friendly solutions, the outlook is very positive.
Figure 1. This shows the split in terms of primary producers, and what they tend to specialise in
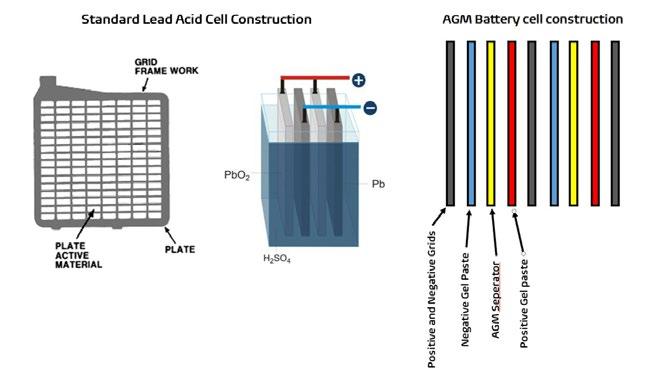
Figure 2. This illustrates the different construction processes behind lead acid cell and AGM battery cell construction
BATTERY STORAGE SOLUTIONS FOR PV
Of the many battery chemistries to choose from, two types stand out for use with solar-powered street lighting. the first and original one is lead/acid chemistry, the second Lithium-Ion. They are very different in many ways and both have positive and negative features.
Lead acid batteries have of course been the mainstay for automotive applications since before the Model T Ford and are manufactured in such volumes as to be relatively low cost.
Lithium-Ion is the newcomer, with only 32 years application history courtesy of the Sony Corporation in 1991.
The manufacturing process behind lead acid batteries starts with either recycled lead or mined lead. Again, the main world supply of lead originates in China, with over 85% of the mined lead going into battery manufacturing.
However, the lead acid battery industry has been recycling its output for many years and it is estimated that between 60% and 80% of a lead acid battery is currently manufactured from recycled material. This makes them significantly more environmentally friendly than the plastics industry, which at best only manages a 30% recycled rate for specific plastics and, some, no better than 1%.
However, it is worth noting that many of the recycling operations are conducted in countries where environmental pollution has yet to be controlled.
The latest lead acid technology uses carbon or graphene as a coating on the anode to prevent sulphurisation of the lead. This has significantly increased the performance of the technology to rival that of Lithium-Ion in terms of life cycle and charge characteristics, with the added benefit of still being easy to recycle.
Lithium-Ion refers to a broad spectrum of technologies, all of which are defined by the transfer of lithium ions between the electrodes during charging and discharging.
Li-Ion cells do not contain metallic lithium, but the ions are inserted into the structure of other materials. For the cathode, these can be metal oxide materials made from cobalt, nickel, and manganese. For the anode, it will be lithium titanate, silicon and now graphene.
The difference in manufacturing complexity between the two different battery technologies cannot be understated. However, following the huge investment by many countries into Lithium-Ion battery production, the technology has a long run ahead.
In terms of the overall environmental impact between the two technologies, the cost per kWatt Hr for lead acid is approximately 50% greater than that for lithium. However, there is a wide disparity between the different texts on the subject, ranging from 39-200 Kg CO²e/kWhr for Lithium-Ion to 250 Kg CO²e/kWhr for lead acid.
The big difference comes in the origin of the different materials used in Lithium-Ion battery construction.
The world’s supply of lithium is held between five countries. Yet the manufacturing processes are distributed throughout the globe, making it a difficult technology to establish an accurate carbon footprint.
Currently only around 6% of Lithium-Ion batteries are recycled because of the complexity and commercial viability of doing this. For lead acid the future recycling capacity is guaranteed, with a new UK plant to come online soon in Birmingham, to recycle up to 15,000 metric tons per year.
The technology is a clean process and will make a marked contribution to the move towards COP26 compliance. This same company aims to recycle Lithium-Ion batteries on a clean commercial scale in the future.
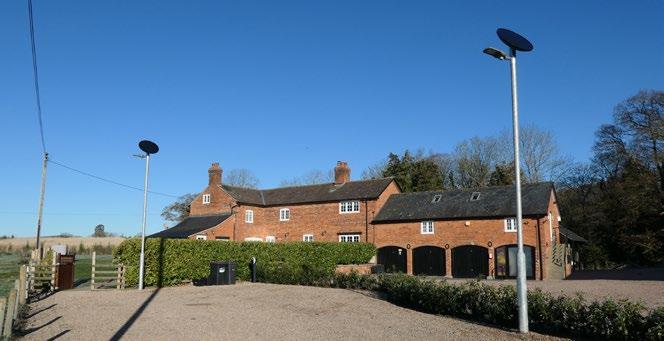
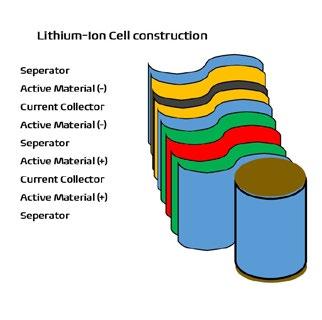
Figure 3. A breakdown of Lithium-Ion cell construction

Figure 4. The key geographic locations for lithium production

Figure 5. A breakdown of National Grid supply, taken late afternoon on 30.01.23
CONCLUSIONS
In conclusion, to answer the original questions: is solar sustainable economically viable, environmentally, and morally sound?
The United Nations’ definition of sustainability is: ‘meeting the needs of the present without compromising the ability of future generations to meet their own needs’ [2]
The rapid advances made in technology in a lifetime now see environmental legacies coming round faster than in previous generations, and our actions today may have to be explained and justified within our professional lifetime. This is something our forefathers were seldom worried about.
Having said that, these figures hopefully speak for themselves. For a simple solar streetlight with a 100W PV Panel and a 25Ahr battery and a 12-watt luminaire. For, Solar PV you are looking at 43.47 kg CO².
For a Li-Ion battery, it is 11.7-60kg CO²e. For a Pb (lead acid) battery, it is 75kg CO²e. The equivalent Grid supply over the same period is 296Kg CO²e, as shown in figure 5 below (with the figure taken at the end of January).
This article is not addressing the serious moral issues regarding the way local communities are treated in the production cycles described. But, as our world continues to have open communications, I am hopeful these issues will eventually be included in the purchasing decisions – and in certain areas they already are.
Last year, the UK produced 3.9% of its energy from solar. So, although a very positive contribution to the National Grid, more than two-thirds (67%) was still generated from non-renewable resources.
While, it is clear, there is still therefore a way to go, I am optimistic that the integration of solar lighting into the equation will continue to make a positive contribution to our drive towards both energy autonomy and sustainability.
Mark Hopkins is joint managing director of OG2 Lighting
[1] For those unfamiliar with supply chain tiers, broadly, tier 1 suppliers will be direct suppliers of a product. Tier 2 suppliers will be subcontractors for tier 1. Tier 3 will be suppliers or subcontractors for tier 2. [2] The United Nations, ‘Sustainability’, https:// www.un.org/en/academic-impact/sustainability