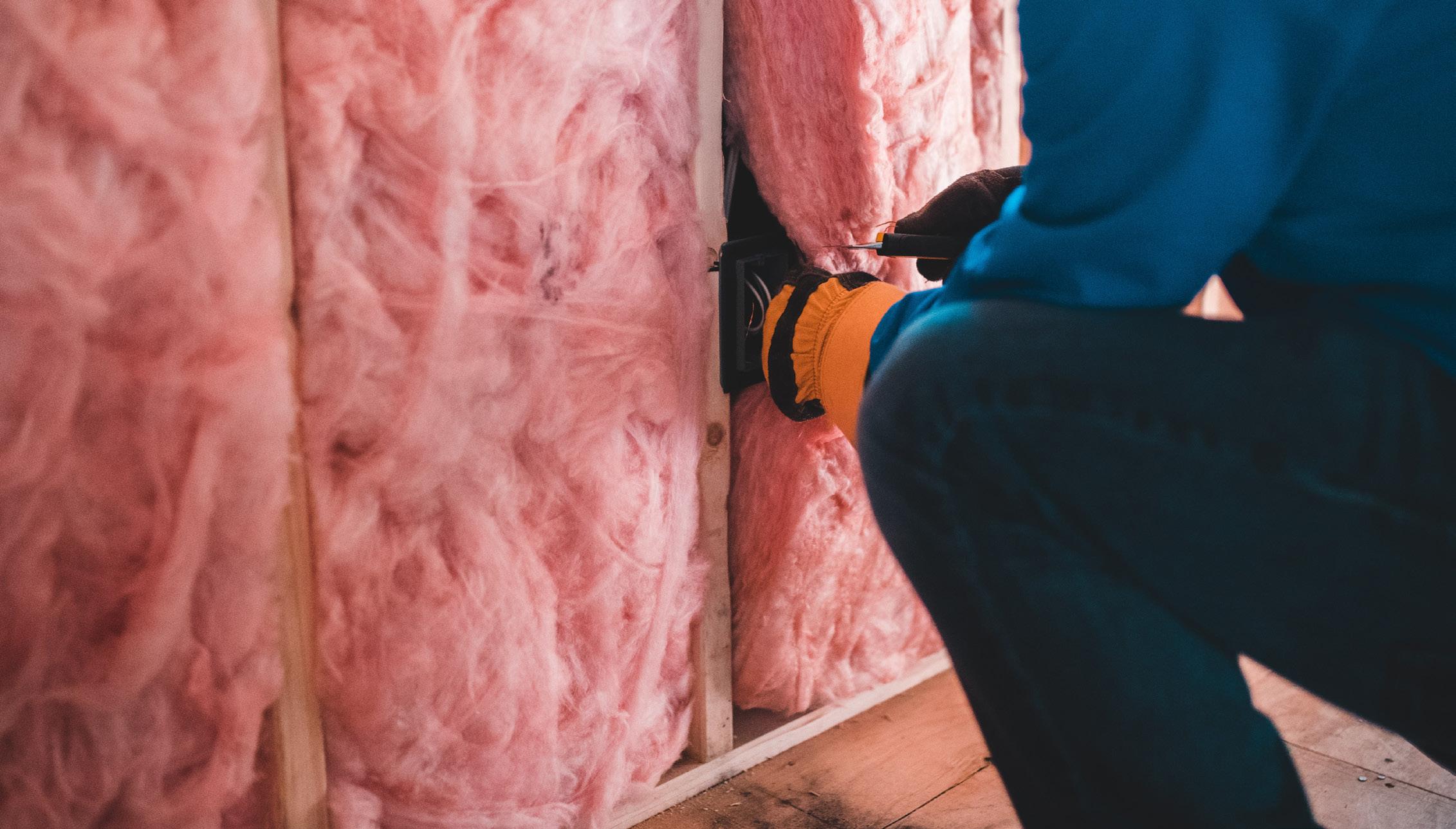
6 minute read
MATERIALS THERMAL & MOISTURE BUILDING INSULATION
In building construction, various forms of insulation are included as a means of reducing the transmission of thermal energy through walls, ceilings, and floors. In simple terms, this helps keep heated interior space warmer in the winter, and air-conditioned spaces cooler in the summer. Reducing the transmission of thermal energy not only makes spaces more comfortable, but it is also essential to controlling energy costs.
All building materials have an inherent insulating property, usually measured on a scale known as R-value, but additional materials are integrated into the building construction specifically to add insulating value to the walls, floors, and ceilings. Historically, many different materials have been used as insulation, and many of these have now been abandoned in favor of more modern and efficient materials. The type of insulation you select when designing and constructing a space will depend on your climate and the R-value you seek.
Advertisement
Blanket and Batt Insulation
By far the most common type of insulation consists of a “blanket” of rolls or batts of insulation used to fill the cavities between framing members in walls, ceilings, and floors. Batts can also be laid in a blanket across attic floors in to insulate the spaces below.
Batts and rolls consist of flexible fibers woven together in strips of varying widths and thicknesses for different applications. Most commonly, batt insulation uses fiberglass fibers, but it can also be made using mineral fibers, plastic fibers, or natural fibers such as wool or cotton.
Blanket insulation can offer R-values ranging from R-11 (for 3.5-inchthick batts) to 38 (for 12-inch-thick batts). Batt insulation is one of the most inexpensive forms of insulation, and one of the easiest to install.
Foam Board Insulation
Polystyrene or polyurethane foam boards provide superior insulating R-values for relatively little thickness. They can be used for nearly any part of a building and are especially effective for insulating exterior wall sheathing, interior sheathing for basement walls, and in special applications such as attic hatches or air gaps where floor joists meet foundations. They offer a good way to insulate the spaces between roof rafters in unvented attics.
When used on interior wall applications, foam panels must be covered with half-inch-thick gypsum board panels or another approved building material.
Foam board provides excellent thermal resistance, as much as twice that for other materials of the same thickness. They can easily be trimmed to size for various applications.
Liquid Foam
Liquid foam insulation consists of cementitious or polyurethane materials that are sprayed, injected, or poured into walls or under floors, where it then hardens into an excellent insulating material. It is ideal for irregularly shaped areas and around obstructions, or it can be used to add insulation over existing finished areas. It is a good option for insulating existing walls, as it can be injected into them without removing the wall surfaces.
Liquid foam may allow you to achieve higher R-values than with traditional batt insulation, and it has the advantage of being able to fill the smallest holes to reduce air gaps around pipes, door and window frames, and plumbing and electrical lines.
Spray foam is available in many forms. It can be applied professionally to large areas by contractors using specialized machines or applied to small air gaps using simple spray cans available at home improvement centers.
Loose-Fill Insulation
Loose-fill and blown-in insulation, usually consisting of cellulose, fiberglass, or mineral wool, can be blown or poured into the joist cavities on attic floors or in the joist cavities of walls.
R-values vary depending on material and loose fill insulation has a tendency to settle over time, reducing its R-value. But it is relatively inexpensive and is considered a “green” option since these materials are created from recycled waste materials. Cellulose insulation is made mostly from recycled newsprint, most fiberglass insulation is made from 40 to 60 percent recycled glass, and mineral wool contains about 75 percent recycled material.
Concrete Block Insulation
Concrete and concrete block walls can be insulated in a number of ways.
Concrete block can be insulated by applying rigid foam board to either the outside of the walls (on new construction) or the interior walls (on existing homes).
An additional method of insulating concrete blocks involves the use of blocks consisting of autoclaved aerated concrete (AAC) or autoclaved cellular concrete (ACC). These materials contain about 80 percent air by volume and have about 10 times the insulating value of traditional concrete blocks. Precast ACC blocks use fly ash instead of the high-silica sand used in AAC blocks. Autoclaved blocks easily absorb moisture, so they must be protected from water, but they are lightweight and easy to install.
In poured concrete foundations, beads of polystyrene foam can also be incorporated into the concrete mix to increase their R-value. This method can increase the R-value 10-fold over standard poured concrete.
Radiant Barriers and Reflective Insulation
While most insulations work by resisting conductive and convective heat flow, reflective insulation works by actually reflecting back radiant heat.
These insulations incorporate a radiant material—usually shiny aluminum foil—applied to a layer of traditional insulation that also has some form of backing—kraft paper, plastic film, or cardboard. It is most commonly used in attics to reduce summer heat gain and to lower cooling costs. It is one of the best types of insulation for preventing downward heat flow.
Reflective insulation forms a radiant barrier that lessens heat transfer from roofs down into an attic space. It must face an air space in order to be effective. They are most effective in hot climates, where they can lower cooling costs by 5 to 10 percent. However, in cooler climates, traditional thermal insulation is a better choice.
Rigid Fiberboard Insulation
Rigid fiberboard made from either fiberglass or mineral wool is normally used in places that will be affected by high temperatures such as the ductwork for HVAC systems. One of the advantages of this type of insulation is that it can be preinstalled on ductwork at shops or custom-fabricated at the job sites. The panels come in a range of thicknesses, from 1 to 2.5 inches. Both faced and unfaced boards are available.
Fiberboard insulation is usually installed by HVAC contractors, who apply it to exterior duct surfaces with a system of pins or clips. When unfaced boards are used, the outer surfaces are finished with an insulating cement or canvas. With faced boards, the joints between panels are sealed with tape or mastic.
Structural Insulated Panels (SIPs)
An entirely different method of insulating a building can be achieved with the use of structural insulated panels (SIPs) instead of traditional stud framing. SIPs are large prefabricated panels that include a 4- to 8-inch thick foam board insulating material (usually polystyrene or polyisocyanurate) sandwiched between strong facing materials, such as oriented strand board (OSB). A SIP-constructed building can be as much as 12 to 14 percent more energy efficient than a traditional “stick-frame” home. A SIP building will also be more airtight and quieter.
SIPs are not an option for insulating existing buildings but can be considered when planning a new building or major addition. In addition to offering excellent insulating value, SIPs are structurally stronger and more stable than traditional framing.
Insulating Concrete Forms (ICFs)
Insulating concrete forms (ICFs) are prefabricated forms for poured concrete walls that remain as part of the wall assembly. The system consists of foam boards or interlocking foam insulation blocks joined together with plastic ties. When concrete is poured into the foams, the resulting walls achieve an insulating value of about R-20.
ICFs can be used for foundation construction alone in buildings with basements, or they can form the above-ground walls as well. Structures built from ICFs still resemble traditional framed structures.
Installing an ICF system is a highly specialized skill that requires an experienced contractor. Especially critical is making sure the walls are insect- and waterproof. Juan Rodriguez