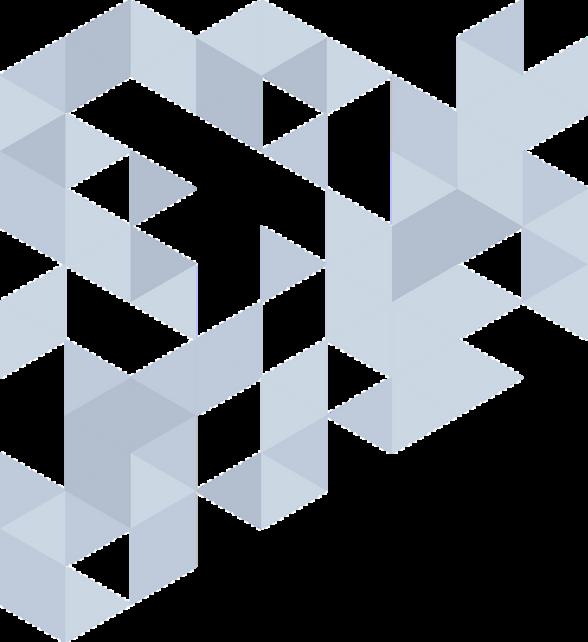
1 minute read
REDUCING PRODUCTION DOWNTIME BY IDENTIFYING CRITICAL SPARES
Vicki Hlinovsky
Business Process Lead (EAM)
Sunwater
In April/May 2022, there was a failure of a pump at Stanwell Pump Station. There are two pumps at Stanwell Pump Station, one stand by and one duty which rotate in different directions. The bearing on one pump failed, and it was sent for emergency repair in Gladstone. They needed to find bronze to fix it which was eventually sourced from another depot. They were unable to start the second pump.
Stanwell Pump Station also has two transformers - the first was out of service for some time and they couldn't swap it to the other pump as the pumps are different. We had 10 days outage, with only 4 days until Stanwell Power Station ran out of water and had to be shut down taking out power to everywhere from Rockhampton north.
We needed to identify critical spares on a region by region basis and collate the data across all of the Sunwater business to provide a risk ranked critical spares list for the business to work through purchasing or enter in to supply contracts for.
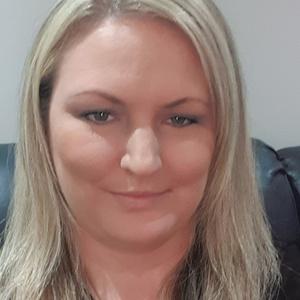
Key Learnings
Creating a logical repeatable process for determining critical spares
Gaining input from field staff to get accurate data. We assumed it would be largely a desktop exercise however this was not possible due to missing data in our system
If your spares aren't set up as Materials in your system, there is no point in doing any of it! We didn't have accurate data to analyse which made the process more difficult