
6 minute read
DOWTY PROPELS ITSELF TO FUTURE SUCCESS
by Nicky
Editor
At around 1am on February 4, 2015 fi re ravaged one of Gloucestershire’s oldest and most successful manufacturing companies. It started in the roof space of the Dowty propeller factory at Staverton Airfi eld near Cheltenham, where the company’s propeller systems were made.
It took 80 fi refi ghters to battle the inferno, but the fi re destroyed almost the entire factory.
While all 29 members of staff on site at the time were evacuated and noone was seriously hurt, it could have spelled the end of Dowty’s illustrious almost 100-year history in the area. Instead, out of total devastation has come renewal.
The company, which was bought by the American conglomerate GE Aerospace in 2007, has been reborn in a new manufacturing facility at Gloucester Business Park based on the former Brockworth airfield, co-incidentally home of the Gloster Aircraft Company, where George Dowty, the eponymous founder of the company, worked before setting up his own business in 1931.
Bearing in mind that Dowty makes propellers you could say “what goes around comes around”.
Dowty Propellers is a global supplier of propeller systems and aftermarket services employing around 450 people globally, and 70 per cent of Dowty’s suppliers are UK based.
The company takes pride in its engineering excellence and advanced manufacturing techniques. It is one of only a few suppliers of type-certificated propeller systems for Part-25 aircraft in the world for civil aircraft and has more than 25,000 advanced composite blades in service with a faultless safety record.
Dowty manufactures and overhauls around 2,300 advanced composite blades every year at Brockworth, with significant presence in the military transport and civil regional sector. It provides products and services for iconic aircraft such as Lockheed Martin’s C-130J and De Havilland’s Dash 8-400 amongst others.
Dowty blades are made from composites. In fact, in 1984 Dowty designed and developed the world’s first blade manufactured from all-composite materials for the Saab 340 regional aircraft.
Starting from carbon fibre cloth, Dowty manufactures blades by applying advanced manufacturing techniques such as radial braiding, resin transfer moulding, nondestructive testing and assembly techniques to create strong, reliable and light propeller systems.
Back to that fateful night and Gaizka Bilbao, who is now Site Leader at Dowty in Gloucester. He explained how the team jumped into action immediately.
Being part of a global family
“At Dowty, and across the whole of GE Aerospace, safety is our top priority and making sure our staff were unharmed. Our emergency preparedness and evacuation procedures supported and preserved the safety of our employees.”
“That’s when being part of GE Aerospace’s global family became so important. We had support and expertise from all over the globe who joined the Dowty team in a joint effort to rebuild the business.
“Our close GE Aerospace colleagues in Bishop’s Cleeve made space available over the first weekend after the fire so that our engineers and other staff could work without interruption. Luckily our repair and overhaul services were unaffected as they were based nearby at the Metor business park at Gloucester airport, so we set up a crisis control centre there.”
Within two months, Dowty had secured a temporary factory in the Forest of Dean and invested millions of pounds in new equipment. Within nine months, blades were again rolling off its production line with no major disruption to any of its civil or military customers.
This was a stupendous achievement, because even though the new facility was temporary, the same high quality and other regulatory standards had to be met.
And that was only the start, according to Gaizka. “When we began to buy new equipment we were quoted delivery times of almost two years on some critical machinery. We couldn’t wait that long, so a team headed to Germany to negotiate.”
Other businesses helped as well, including the National Composites Centre near Bristol, which allowed Dowty to set up a manufacturing cell to make blade de-icer boots just four weeks after the fire.
For three years the company operated from five sites in county. But this could only be temporary, so Dowty looked at options for a new factory. The Brockworth project was approved in 2017. By November 2019 manufacturing had begun.
Ambition to lead in sustainable aviation
You would think that one major disaster would be enough for any manufacturer to contend with enough. And then the pandemic hit.
By this time the crisis management expertise of Dowty was honed to perfection, and Gaizka and his team swung into action once again.
“Once we entered lockdown it was very difficult to get external contractors on site, so a lot of work fell on our own amazing maintenance and facilities team completing work which would normally have been done by specialised suppliers.”
The aviation industry was hard hit by the Covid-19 pandemic, particularly on the commercial portfolio.
As we come out of the pandemic the industry is slowly recovering, now Dowty is looking to the future – and being a leader in sustainable aviation is the top priority.
Looing beyond fossil fuels – but you’ll always need a propeller
“Sustainability is a generational challenge for us and for the world,” said Gaizka. “It’s also a deeply personal one for me as my nine-year-old daughter will be living through the decisions we make.
“Flying allows us to connect people and transport goods. It helps the world. But how we do that in a sustainable way using new technology is the key challenge.”
Flying sustainably will require new technologies away from fossil fuels.
Such technologies are likely to enter the regional sector first and there are many new propulsion options, such as fully-electric, hydrogen power, hybrid, sustainable aviation fuels.
There is one common constant in all these options - a propeller is needed to thrust an aircraft through the air. Dowty is well positioned to lead the race in sustainable aviation.
“We are looking at technologies which will help reduce noise and weight while improving efficiency,” said Gaizka. “We are also working towards reducing our own carbon footprint.” Dowty powers its plants with renewable energy and is improving the efficiency of its manufacturing operations as well as investigating re-use and recycle options for its materials.”
£20m project drives manufacturing change
To do that the company continues to invest in research and development.
Last year Dowty completed a fouryear Digital Propulsion research and development programme, called DigiProp, in collaboration with three of seven of the UK’s High Value Manufacturing Catapult centres. This was an ambitious £20 million project, part funded by the UK government, that sought to innovate every aspect of the design, manufacture and testing of its propeller systems.
Dowty is also looking to remove waste from its operations. Its new manufacturing facility in Brockworth is flexible and fully prepared for the future to enable machine connectivity to optimise its utilisation and carbon footprint.
Dowty’s key asset is its people, and developing this talent is an important investment for the company, It runs a very successful apprenticeship programme that gives students the skills and professional training they need to build a successful career in the aviation industry, and their apprentices have won regional awards.
Dowty welcomes around 15 undergraduate students every year as part of its internship programme where they get a feel for industry and participate in key sustainability projects in the company.
“We are involving the next generation with our own teams,” said Gaizka. “The new generation have a different way of thinking, and are passionate about the future, so a combination of their viewpoint and knowledge alongside the experience we hold in our teams can be a powerful force for positive change.”
You can take the man out of Spain…
Gaizka Bilbao, 44, was born in Bilbao, Spain. His father was an engineer, working at one point for an automotive multinational company in central Spain. When he took his young son to see what he did, Gaizka knew he wanted to be an engineer designing cars.
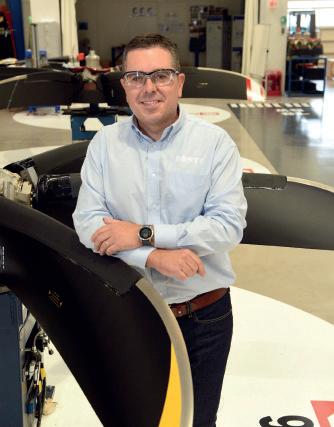
As he grew up, he was in the right region of Spain. The Basque country had previously been home to some of Spain’s biggest industries, including tool manufacturing and mining. When these industries began to decline, new sectors began to establish themselves, such as aerospace manufacturing alongside automotive.
Gaizka moved to the UK and completed a degree at Bath University, including a year in industry at Rolls Royce, Filton near Bristol. After his degree he joined GE Aerospace and hasn’t looked back.
“I began my career following my technical degree in an engineering role which gave me deep domain expertise in our products.
“Being so close to manufacturing operations attracted me towards process improvement and Lean Six Sigma activities. Working with teams to improve processes was a great segway into the operations arena where my heart lies. GE offers incredible training opportunities.”
That included two years working in Cincinnati, USA for GE as a Program Manager for Boeing before returning to the UK, first to work for GE in Hamble,
Hampshire before joining Dowty in 2015, just months before the fateful fire.
“I have been exposed to different disciplines throughout my career, from technical to commercial roles, but my heart is in manufacturing and the supply chain,” said Gaizka. “I love being close to the product, the people making it and the customers we serve.
“Manufacturing is about helping people in a tangible way and making lives better. During the pandemic we supported air forces across the world which played a key role in the transport of people, medical equipment and vaccines.
Our field service network is vast and supports our customers across the globe. It made us all incredibly proud to recognise the part we were playing”.