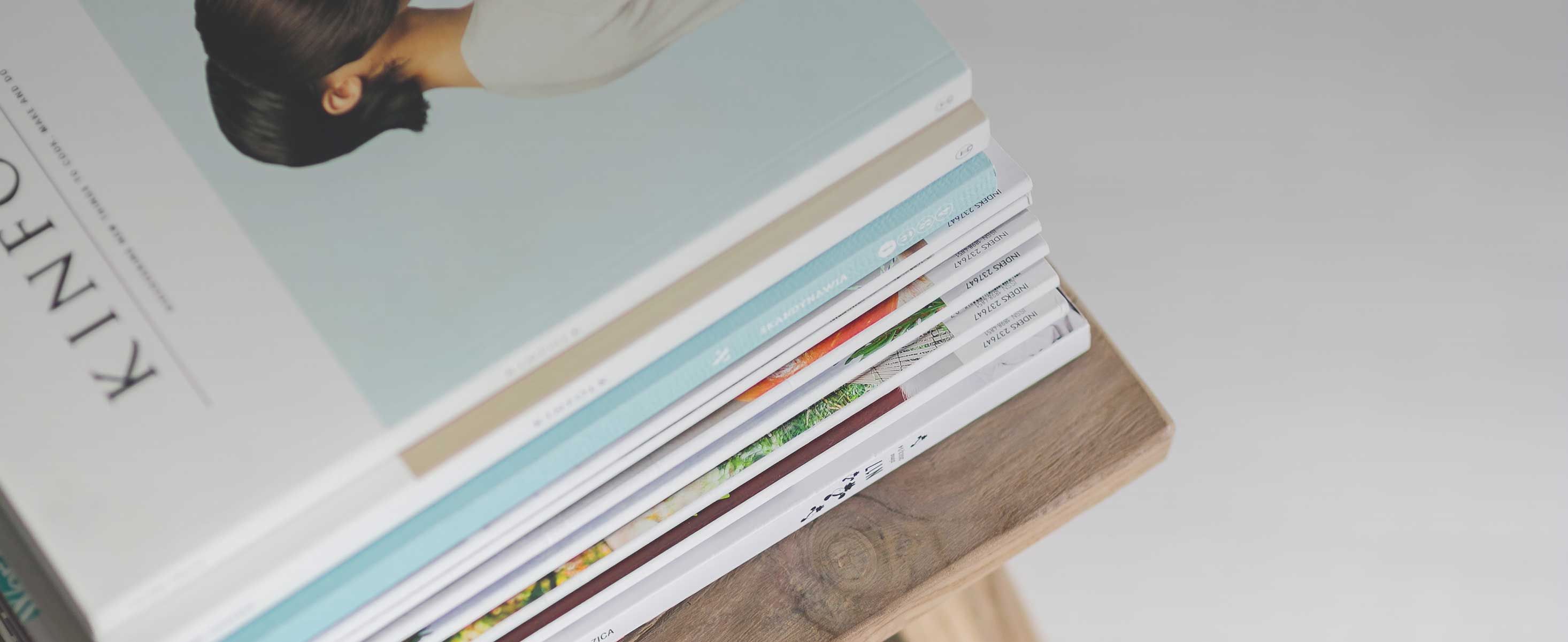
6 minute read
COVENTRY CLEANING AND HYGIENE BUSINESS RISES TO PANDEMIC CHALLENGE
It’s been an extraordinary year for Mirius. The Coventry developer and manufacturer of cleaning and hygiene products found itself at the centre of the UK’s response to the pandemic. At the same time it also received a prestigious Queen’s Award for Enterprise in International Trade.
Mirius, first established in 1963 as Coventry Chemicals, develops cleaning and hygiene products for the retail, professional and animal healthcare sectors. Last year it turned over more than £45 million, up from £32 million the previous year. At the same time, it faced its biggest challenge yet as Covid-19 rolled across the country.
The company responded by introducing a new range of anti-viral cleaning products in less than three months, investing in the machinery to produce them and doubling the workforce to meet demand.
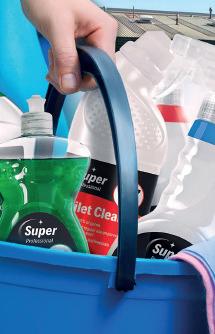
Managing Director Paul Marsh explained: “Before the pandemic hit we were already discussing what the next big healthcare challenge might be, and what we should be developing to meet it.
“Little did we know how relevant our discussions would quickly become.”
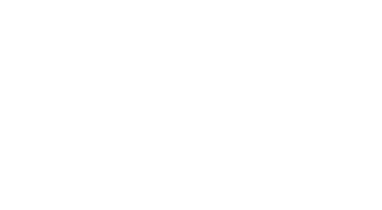
Mirius is used to dealing with pandemics. Its animal health care division is constantly developing products to help combat the spread of diseases such as avian bird flu, African swine fever and foot and mouth disease, to name a few.
“Our microbiologists are very knowledgeable,” said Paul. “In 2019, surprising as it might seem, a cleaning product range with anti-viral properties didn’t really exist, but our team predicted the need for them.”
Lots of products clean and sanitise. Bleach is the obvious one because it kills pretty much anything which comes into contact with it, but you wouldn’t want to use it in a food preparation area or, say, on fabrics or wood when it would taint or discolour the surface being cleaned.
“Coronavirus isn’t a particularly difficult virus to kill. But it does love surfaces and hangs around for a long time,” said Paul.
So Mirius’s microbiologists set about developing a product that could be used for cleaning not just sanitising. The result is Hycolin.
Hycolin antiviral surface cleaners are a range of powerful disinfectants that clean surfaces and reduce the cross contamination risk of germs and viruses.
“We launched Hycolin into the hospital sector, but consumers also wanted reassurance that there was a medicalgrade product which would clean and protect their homes from viruses,” said Paul.
In just a few months the company went from developing the first Hycolin product to selling 11 variations suitable for cleaning and sanitising all areas within a building, from toilets to kitchen areas.
“Although we knew the chemistry worked, we needed to test our products at renowned laboratories to obtain the correct certifications to prove that the Hycolin range killed enveloped viruses such as Coronavirus as well as dangerous bacteria such as MRSA and Listeria,” added Paul.
“The tests demonstrated that our claims were substantiated and that the Hycolin cleaning range is highly effective.”
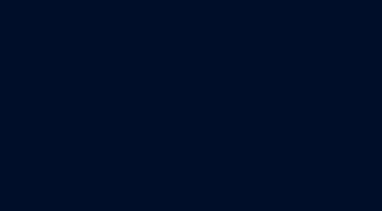
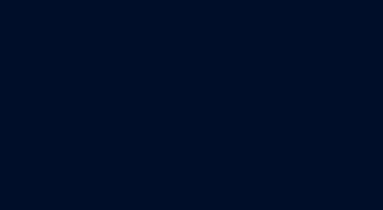
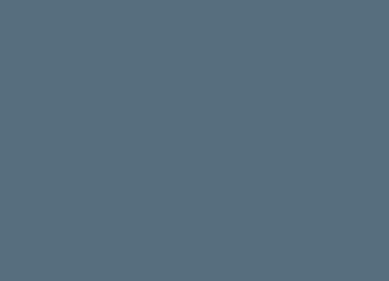
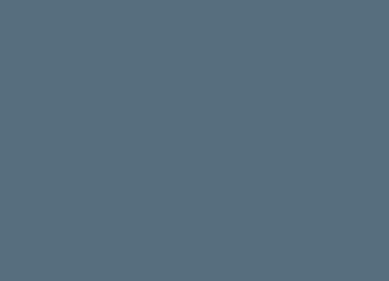
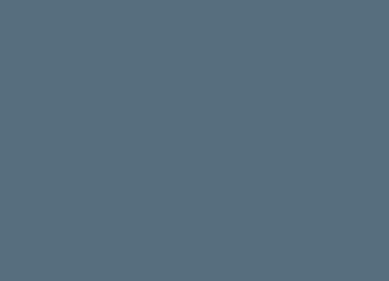
Mirius manufactures in Coventry, and during the height of the pandemic last year – like pretty much every manufacturer, it experienced key shortages (the bottle trigger heads were in very short supply at times, along with some active ingredients).
“Our success in securing supplies came down to the tenacity of our team,” said Paul.
“At times we chartered aeroplanes to bring components in so we didn’t let customers down. We even supplied components to competitors to keep them going too.”
Before the pandemic, the business ran two shifts, five days a week. By April it was three shifts a day, seven days a week.
Mirius has the capacity to produce more than one million bottles every week and now employs around 200 people, up from a 125 head count before the pandemic.
“Our workforce has been absolutely fantastic,” said Paul. “They adapted to different shift systems so we always had capable people who knew exactly what they were doing in terms of making, packing and transporting.”
Now, as the world adapts to life postCovid, Mirius is building on its work of the last 12 months.
“We’re talking to our customers, including supermarkets and professional users, to further improve our products,” said Paul. “We are also being approached by innovative small businesses which have some really exciting cleaning chemistries. We are helping them develop their ideas and bring them to market.”
The cleaning sector has suffered from inertia for the last decade or more. That’s changing with new technologies being developed as people better recognise the importance of hygiene, cleaning and the training of staff.
“People are now open to new products, procedures and ideas. It’s become a very dynamic marketplace,” added Paul.
Mirius is also constantly working to improve its sustainability and ecocredentials. It has developed the Mireco plant-based range of cleaning products, as well as working with leading supermarkets to develop their own eco ranges.
Mirius uses r-Pet recycled plastic in its trigger spray bottles, and is accredited to the RSPO certification in its use of Responsibly Sourced Palm Oil.
In April, the company won a Queen’s Award for Enterprise in International Trade. Mirius sells around the world, particularly into the key markets of Ireland and across Scandinavia. Its animal health care products are sold across the Far East, and in the USA it sells through an American pharmaceutical company.
There are many more overseas opportunities, particularly in mainland Europe, said Paul, and across Australia and New Zealand.
Domestically, the company continues to concentrate on product development and increasing brand awareness.
“We gained a lot of customers during the pandemic,” said Paul “Our sales team was glued to the phones, and we were tenaciously sourcing raw materials in order to not let anyone down. We want to build on that by further penetrating current markets and opening up new territories overseas.”
When Steve Lindsey discovered that air compressors absorb a staggering 10 per cent of the world’s energy, and no one had succeeded in making them more efficient for 100 years, he decided to do it himself.
His invention, the Blade Compressor, was a completely new and patented geometry for a machine that is at the core of many industries. It leaks less, uses less energy and is more reliable than traditional machines of this type.
And with the global air compressor market expected to exceed $37 billion by 2022, driven by additional demand from the food & beverage and pharmaceutical sectors, it seemed ideal to launch a new product into a sector ready to embrace potentially costsaving technology.
In 2019, Lontra, the company he set up in 2004 to design, manufacture and sell the compressor, opened a purpose-built advanced manufacturing centre in Napton, in rural Warwickshire.
And last year, the advanced engineering technology company began production of the blade compressor on a new assembly line in Tyseley, Birmingham.
Lontra has secured significant partnerships with major US distributor networks to ensure it can secure a major market presence in North America.
Steve, CEO of Lontra said: “Beginning production of our first machines for export was a pivotal moment in Lontra’s growth trajectory.
“It is fast growth manufacturing firms such as ours that reflect the sector’s strength to thrive post pandemic. Manufacturing and exports create a strong bedrock for the economy, supporting local jobs and highlighting our world-class skills that make us competitive on a global scale.”
Sales of Lontra’s LP2 product are forecast to boost the company’s value to nearly £600 million by 2024. Following refinements to the original design, the company says its compressor is now up to 34 per cent more efficient than competitors.
Queen’s Award for high-tech engineering company recognises international sales
A Warwick-based high-tech engineering company has received its second Queen’s Award for Enterprise. 3P Innovation’s latest accolade for International Trade follows on from it’s first Queen’s Award for Innovation last year.
3P Innovation designs, manufactures and supports top-quality production equipment and machinery, from lab-scale to commercial scale.
3P says it is one of a limited number of companies globally which can design and manufacture such sophisticated and heavily regulated automation.
Its latest Queen’s Award builds on last year’s success for 3P. Shortly after launching a national visor initiative, which saw the manufacturer donate more than 40,000 visors to frontline staff, the company was awarded with a UK Business Hero stamp by the British Chambers of Commerce.
The firm ended the year on a high note after announcing a transition to employee ownership.
3P’s founder and Managing Director, Tom Bailey, said: “In a year that has been challenging for everyone, the team at 3P innovation have worked harder than ever to achieve remarkable international growth.”
“This has provided us with further security and stability in an ever-changing market affected by Covid, and it’s great to see that UK innovation and international growth within the manufacturing sector are being recognised by the Queen’s Awards.”