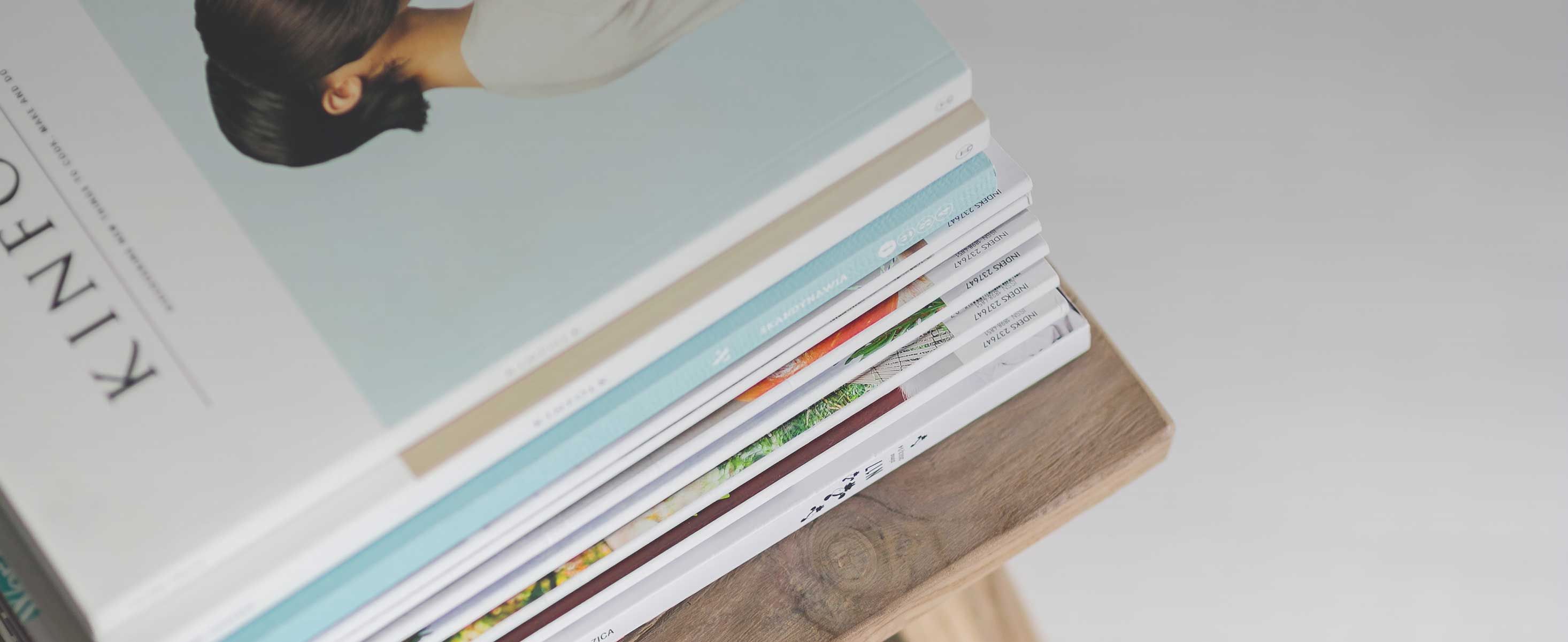
8 minute read
CREATIVITY DRIVES SUCCESS FOR DRPG APPRENTICES
Where apprentices are concerned, one of the UK’s most successful creative and events agencies, DRPG, puts its money where its mouth is.
DRPG board member Richard Hingley started his career as an apprentice 20 years ago. He’s now the group’s Creative Director.
The company’s aim is to grow and nurture a constant pipeline of people and talent for the future, and over the last two years in particular, its apprenticeship scheme has been a big part in helping to support this.
The company, based at Hartlebury near Kidderminster, currently has 10 apprentices within its workforce of around 315.
Jez Light is Head of Learning and Development at the company. His approach has been to take the prescribed apprenticeship as the base, then build a much more intensive training programme around it to produce work-ready young people within 15 months, rather than the average three years.
“When our apprentices join they are given a really robust introduction to the company,” he said. “This includes understanding our values and behaviours, and our DRPG Essentials course – 14 hour-long training sessions to give them the rounded skills they need as individuals and which will help them in the workplace.
“Some are game-led, and they are designed to be fun. The apprentices can choose which ones they want to participate in, and we follow their sessions up with e-learning to reinforce what they’ve learned.”
This is particularly important in the creative sector the apprentices have joined, where the name of the game is deadlines and meeting and exceeding client expectations. This all takes good communication skills and common sense.
“There’s no point an apprentice knowing how to code a computer or save files and spreadsheets but not being able to have a conversation with another human being,” said Jez. “We make them proud to work for us and our retention is excellent.”
Each apprentice spends around 20 per cent of their working week learning. The rest of the time all of them are working directly on events, with four working directly in the events team and the others spread out across departments supporting them.
And DRPG’s investment is working. One apprentice, Tom Smith, 23, who is working in the company’s IT department, won both Higher Level Apprentice of the Year and Worcestershire Apprentice of the Year in the county’s 2019 apprenticeship awards.
“Tom didn’t join as an apprentice but decided to follow that route when we offered it to him,” said Jez. “When he’d completed his first apprenticeship, he did a year of practical work and then decided to head back into studying and undertake a higher apprenticeship.
“It’s taken him five years to achieve but his hard work has paid off handsomely for Tom, and for the company.”
Phosters fosters training and support in Worcestershire
Last year, Kidderminster-based Phosters (FM) Ltd was named as the Worcestershire Apprenticeship Employer of the Year.
Phosters is a facility service provider offering building maintenance services across the UK and Europe.
With roots stemming back to 1918, the company is a leading provider within the industry. It has a management team with more than 100 years of collateral knowledge serving different markets and operations.
The company has been employing apprentices for around four years and has taken on 10 young people, almost all studying business administration with one accountancy apprentice.
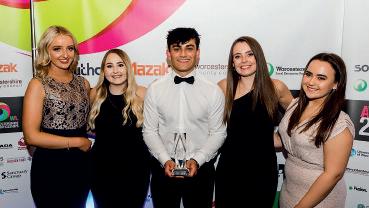
Phosters employs apprentices with their future career in mind, offering a good training programme with excellent career prospects. It sees its apprentices as future leaders and is keen to offer them as much training and support as possible.
Alexandra Kavanagh, Head of Business Support at Phosters, said: “Apprentices are excellent employees. They offer innovative ways of thinking and are very committed. Apprenticeships are quite often our first point of call when recruiting and since 2017 we have offered degree apprenticeships which has been invaluable to the company.”
Phoster’s current degree apprentice is Cameron Hamilton-Patel who is completing a chartered manager degree apprenticeship. “Cameron has
REGIONAL APPRENTICESHIP REPORT sponsored by Worcestershire Apprenticeships
become an integral member of the team and has analysed and reviewed multiple budgets leading to cost savings and improved efficiencies across the business,” said Alex. “He is a great support to the business and we are excited to see where his apprenticeship takes him.
“One of the key things we pride ourselves on is the support we offer to our apprentices, in their working life and their personal lives too. If there is anything they wish to pursue, any difficulties they are experiencing we will always offer as much support as possible. Apprentices are the future and we are invested in supporting the young people in Worcestershire.”
Want to take on an apprentice? Find out how from the Hub
The Worcestershire Apprenticeships Hub helps employers implement apprenticeships in their organisations.
The Hub makes apprenticeships easy for small and medium-sized businesses. The team gives advice on many topics, from succession planning and talent management to choosing the right provider and apprenticeship standard, accessing grants to support them to recruit and supporting registration on the apprenticeship service.
The Hub also offers an impartial referral service to the right training provider, to help businesses recruit and develop their apprentice or upskill an existing employee through an apprenticeship.
It also helps employers to encourage the growth of apprenticeship opportunities and increase the number of young people becoming apprentices in Worcestershire. The Worcestershire Apprenticeships website currently has more than 3,000 employers listing their vacancies with around 110 training providers. www.worcsapprenticeships.org.uk or phone 0300 666 3666
Eynsham-based SST Technology designs and manufactures advanced fabrications with a particular expertise in tubular components and high-performance insulation products.
Part of the Polar Technology Group, which owns a number of engineering businesses operating at the leading edge of technology, SST design systems and components, often working with its customers’ design teams. The company works with the highest performance materials such as Inconel, Titanium and stainless steel and employs advanced processes such as CNC Bending, Hydroforming, pressing and six-axis laser cutting.
The company takes on up to four apprentices at a time, most training to be engineers, although it is also putting one through an apprenticeship in finance this year.
Sharon Barrett, Head of People and Performance, said: “We train our own apprentices because it can be difficult to find enough engineers who possess the skills we need for our sector of engineering.
“We use a number of training providers, but Oxfordshire Advanced Skills gives us the benefit of being able to provide full-time training to apprentices in their first year so that when they arrive to work here in their second year, and continue their training on day-release to college, they will have a useful level of knowledge and maturity which will benefit the business as well as give them a sound skills foundation to a career in engineering.”
The new Oxfordshire Advanced Skills (OAS) Training Centre at Culham Science Centre near Abingdon, welcomed 100 young people last September to began their apprenticeships.
OAS offers training for the Level 3 Engineering Technician Apprenticeship Standard. This qualification has been designed by employers to give the technical and practical knowledge required to work in the engineering sector. The OAS is also introducing training in BTEC Level 4 Higher National Certificate in Engineering with degree apprenticeships in the planning for September 2020.
The training centre, which is being run by the Manufacturing Technology Centre (MTC) will make a significant contribution to developing the next generation of engineers to support the future skills needs of businesses across Oxfordshire, the Thames Valley and the surrounding area – one of the UK’s high-tech hotspots.
David Martin, Director of Oxfordshire Advanced Skills Centre, said: “The OAS is an employerled skills hub providing high quality training contextualised by being delivered in the workplace. Based as we are at one of the most exciting science and technology hubs in the UK, we have created something very special that has the potential to impact careers and business performance for decades to come.” sponsored by Oxfordshire Advanced Skills
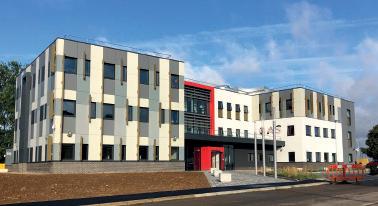
The new 3,800 sq metre training centre at The UK Atomic Energy Authority at Culham incorporates some of the country’s most advanced equipment on which the apprentices are learning.
It will provide more than 160 apprentices a year with the technical skills Oxfordshire and the Thames Valley’s economies need, and a springboard for future career success.
Training at the new facility is being delivered by MTC Apprenticeships, replicating the industry-leading tuition provided at the Advanced Manufacturing Training Centre (AMTC) on the MTC campus at Ansty Park, Coventry. The AMTC has a reputation for equipping apprentices not only with core engineering skills but also the latest advanced manufacturing techniques.
More than 20 of Oxfordshire’s most exciting science and technology companies are currently placing their apprentices with Oxford Advanced Skills.
Working for Reaction Engines is out of this world
Reaction Engines, based at Culham Science Centre, is currently putting three apprentices through their training at Oxford Advanced Skills Centre. One electrical apprentice is in his first year of full-time training while a second year mechanical apprentice is completing his BTEC certificate and a fourth year mechanical apprentice is completing his HNC.
Reaction Engines offers an Advanced Level 3 Apprenticeship Scheme to ensure its apprentices have cutting-edge engineering and science disciplines.
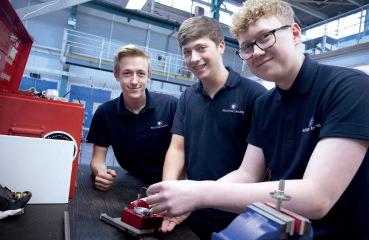
Nothing less will do for those who want to build a career with one of the UK’s most exciting companies which is developing the technologies needed for a new class of innovative hypersonic propulsion system it has named the Synergetic Air-Breathing Rocket Engine (SABRE).
Reaction Engines propose to take on at least one apprentice a year, with applications opening for the 2020 intake.
Apprenticeship Scheme Manager, Barry Coulling, said: “Our apprenticeship programme nurtures the skills our workforce will need in the future. Having such a new and well-equipped apprenticeship training centre on site is of huge benefit to us.
“The collaboration between the OAS and Reaction Engines will benefit us and our apprentices as they train to build their careers in engineering and aerospace with a future-focused business.”
Lisa Rudzki, Reaction Engine’s Head of HR, said: “An apprenticeship at Reaction Engines offers the best of both worlds. Each individual gains a recognised qualification while getting valuable work experience by learning on the job.
“We are delighted to offer schemes that take outstanding young people and train them in academic and real work environments developing them into our next generation of designers, technicians and engineers.”
Apprentices fly high at Oxford Space Systems
Oxford Space Systems is an award-winning space technology business based at Harwell which is pioneering the development of a new generation of deployable antennas and structures that are lighter, less complex and lower cost than those in current commercial demand.
Chief Operating Officer, Mat Rowe, is passionate about the value of apprenticeships. He was an UK Atomic
Energy Authority apprentice, as was David Martin the new Director of the Oxfordshire Advanced Skills Centre.
Mat also sits on a trailblazer space technology apprenticeship group, which is working on setting standards for a pioneering new space apprenticeship to be rolled out soon.
“We launched Oxford Space Systems in 2014 and took on our first apprentices in
2016. It’s unusual for an SME to take on apprentices at such an early stage but I felt it was essential as there is such a vacuum of engineering talent since apprenticeships petered out in the 1990s.
Mat welcomed the opening of Oxfordshire Advanced Skills. “We need smart, bright technicians to work in our facility and build spacecraft hardware alongside our really experienced team who work here full-time,” he said.